机械专业中文翻译注塑模设计.docx
《机械专业中文翻译注塑模设计.docx》由会员分享,可在线阅读,更多相关《机械专业中文翻译注塑模设计.docx(20页珍藏版)》请在冰豆网上搜索。
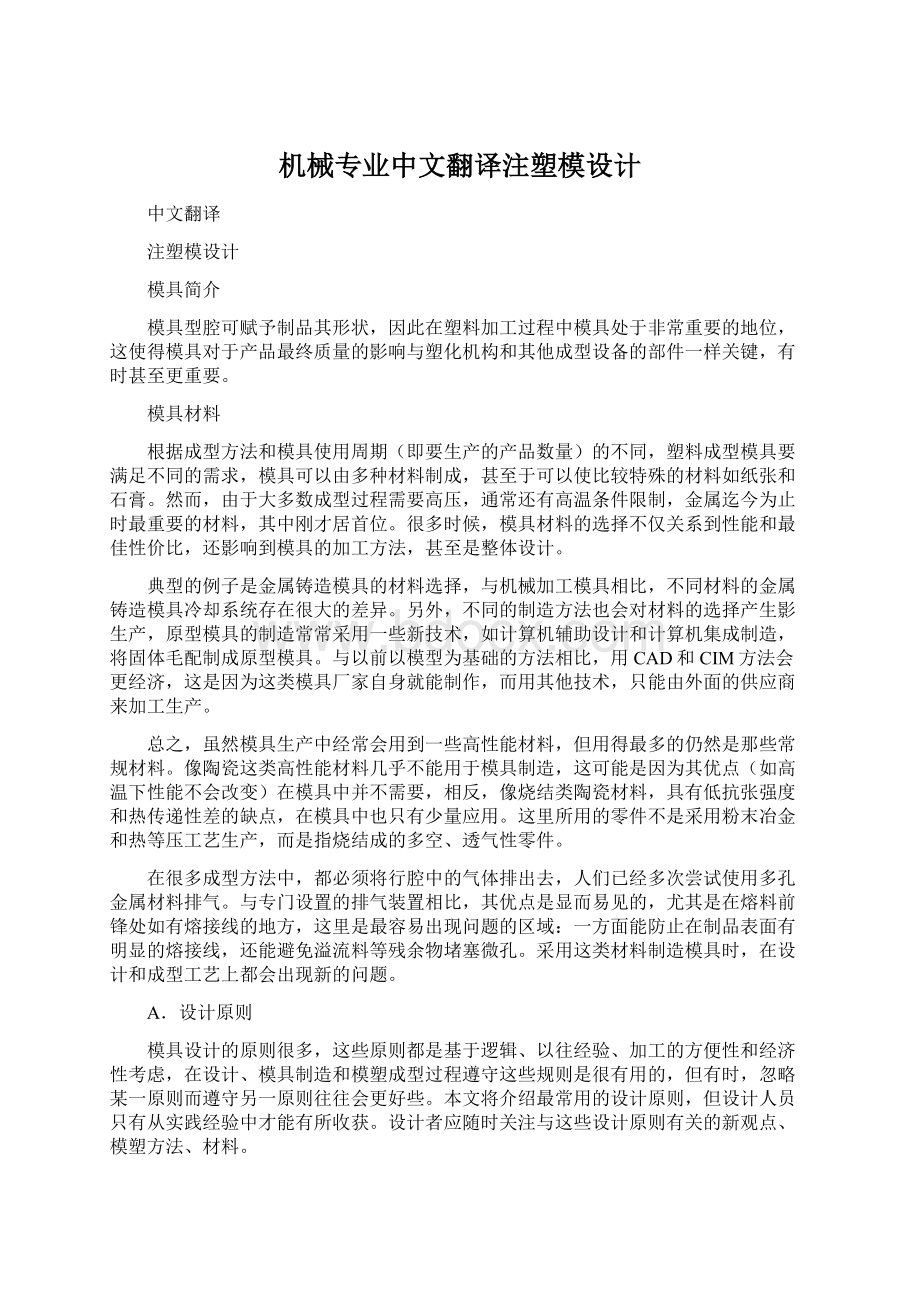
机械专业中文翻译注塑模设计
中文翻译
注塑模设计
模具简介
模具型腔可赋予制品其形状,因此在塑料加工过程中模具处于非常重要的地位,这使得模具对于产品最终质量的影响与塑化机构和其他成型设备的部件一样关键,有时甚至更重要。
模具材料
根据成型方法和模具使用周期(即要生产的产品数量)的不同,塑料成型模具要满足不同的需求,模具可以由多种材料制成,甚至于可以使比较特殊的材料如纸张和石膏。
然而,由于大多数成型过程需要高压,通常还有高温条件限制,金属迄今为止时最重要的材料,其中刚才居首位。
很多时候,模具材料的选择不仅关系到性能和最佳性价比,还影响到模具的加工方法,甚至是整体设计。
典型的例子是金属铸造模具的材料选择,与机械加工模具相比,不同材料的金属铸造模具冷却系统存在很大的差异。
另外,不同的制造方法也会对材料的选择产生影生产,原型模具的制造常常采用一些新技术,如计算机辅助设计和计算机集成制造,将固体毛配制成原型模具。
与以前以模型为基础的方法相比,用CAD和CIM方法会更经济,这是因为这类模具厂家自身就能制作,而用其他技术,只能由外面的供应商来加工生产。
总之,虽然模具生产中经常会用到一些高性能材料,但用得最多的仍然是那些常规材料。
像陶瓷这类高性能材料几乎不能用于模具制造,这可能是因为其优点(如高温下性能不会改变)在模具中并不需要,相反,像烧结类陶瓷材料,具有低抗张强度和热传递性差的缺点,在模具中也只有少量应用。
这里所用的零件不是采用粉末冶金和热等压工艺生产,而是指烧结成的多空、透气性零件。
在很多成型方法中,都必须将行腔中的气体排出去,人们已经多次尝试使用多孔金属材料排气。
与专门设置的排气装置相比,其优点是显而易见的,尤其是在熔料前锋处如有熔接线的地方,这里是最容易出现问题的区域:
一方面能防止在制品表面有明显的熔接线,还能避免溢流料等残余物堵塞微孔。
采用这类材料制造模具时,在设计和成型工艺上都会出现新的问题。
A.设计原则
模具设计的原则很多,这些原则都是基于逻辑、以往经验、加工的方便性和经济性考虑,在设计、模具制造和模塑成型过程遵守这些规则是很有用的,但有时,忽略某一原则而遵守另一原则往往会更好些。
本文将介绍最常用的设计原则,但设计人员只有从实践经验中才能有所收获。
设计者应随时关注与这些设计原则有关的新观点、模塑方法、材料。
B.模具基础
1.模腔
模腔指的是通过机加工在模具材料内部挖出的空间,以供模塑材料,即塑料填充,并获取该空间形状得到需要的制品。
模具的历史几乎与人类文明一样悠久,通过在沙型这类的模具中注入液体金属如铁、青铜,生产出工具、武器、钟、塑像和厨房用具,如今在铸造厂仍使用这类模具,为了取出固化后的制品,需要将模具打碎,因此这种模具只能用一次,我们一直在寻求可以反复使用的永久模具,现在可以用坚固耐用的材料如钢材、软质铝及其他合金材料生产模具,当生产量不是很大、模具寿命要求不是很高时,甚至可以用某些塑料制品模具。
注塑生产时,熔料以高压注入型腔,因此就需要模具足够结实以抵御变形。
2.型腔数量
多数模具,尤其生产大型制品的模具多为单腔模,但是大批量生产时的模具,会有两个或更多型腔,这纯粹是出于经济考虑。
注射多型腔的时间并不比单腔模多,例如四腔模注射一个产品的时间大约仅是单腔模的1/4,而产量却与型腔数成正比。
多腔模比单腔模贵,并不是说要贵四倍,但需要带有大模板和锁模能力的注塑机,而且该例所需总的塑料量是单腔模的四倍,需要有较大的注射装置,较大设备的单位成本要比用小型模具的设备高。
目前多型腔模大多选择2、4、6、8、12、16、24、32、48、64、96、128这样的数字。
选择这些数字(偶数)的原因是为了方便在长方形区域内布置型腔,这样有利于设计、定尺寸以方便加工制造,也有利于围绕机器中心对称分布型腔,这种对称分布对保证每个型腔分配到相同的锁模力非常重要。
也可以在圆形范围内设置较少量的型腔数,甚至于是3,5,7,9这样的奇数,还可用任意型腔数排布,但要注意围绕注塑机中心线投影面积对称分布。
3.型腔形状及收缩
型腔形状实际上是塑件形状的“反”形状。
尺寸需要家上塑料的收缩量。
型腔形状可以用切削设备或电火花、化学腐蚀及任何新型加工方法进行加工和制造,如电镀工艺,也可以将铜或锌基合金浇铸到具有制品形状的石膏模或硬塑料模如环氧树脂中,再机加工成规定形状。
型腔可以直接在模板上切挖出来,也可做成嵌件攘入模板中。
C.型腔和型芯
通常模具的凹部叫型腔,与之相配的凸起部分叫型芯。
大多塑料制品是杯状的,这并不是它们看起来像水杯,而是有内外两面,其外部由型腔成型,内部由型芯制得。
另一种是平板状制品,模具没有明显的凸起,型腔有时看起来像镜面,这类制品有塑料小刀、游戏筹码、圆片状制品如唱片,产品外表看起来很简单,但注塑成型时却有很多严重问题出现。
通常将型腔设置在注塑一侧的半模上,而将型芯设置在动模一侧。
这样放的原因是所有注塑机在动模侧都设置有顶出机构,而且制品通常易于收缩并包覆在型芯上,随后被顶出。
绝大多数注塑机在注射侧不安置顶出机构。
聚合物成型过程
聚合物成型加工是将固体(有时是液体状)粉末、粒状、珠粒等形状的树脂转变成具有一定形状、尺寸和性能的固体塑料制品,通常包括:
挤出、模塑、压延、涂布、热成型等。
为了实现上述目标,成型过程通常包括一下步骤:
国体物料输送、压缩、加热、熔融、混合、成型、冷却、固化、修饰。
很显然,这些操作不一定顺序完成,其中有一些是同时进行的。
为了赋予塑料材料规定的几何形状和尺寸,需要通过成型加工来完成。
还要综合考虑黏弹性形变和若传递,他们和溶体的固化有关。
成型加工包括下述两种方式:
二维成型如口模成型、压延和涂布;三维成型。
二维成型既包括连续稳定的操作也包括间歇式操作,连续式如薄膜和片材挤出、线缆包裹、纸张和片材涂布、压延、纤维纺丝、管材和异型材基础等,间歇式操作如挤出吹塑成型。
通常,模塑成型是间歇式的,所以工作条件有时会不稳定。
热成型、真空成型及其他类似方法常可以被看作是对已有的二次加工,例如在吹塑成型中,就包括预成型(型胚的生成)和二次成型(型胚的吹胀)两部分。
成型过程中既有同步的液体流动和热传递,也有交错的流动和热传递。
在二维成型过程中,一般成型后再接着固化,而在三维成型时,固化和成型往往在模具内同时进行。
根据材料的性质、设备和成型条件,结合流动面的情况(自由与否),流动通常包括剪切、拉伸及压缩流动(国内一般将流动形式只分为剪切和拉伸流动)。
聚合物流动和固化时的热力学-机械性能决定了制品的微观结构变化如形态、结晶度和取向分布等,制品的最终性能与期微观结构密切相关。
因此,只有了解树脂性能、设备、操作条件、热力学-力学性能、微观结构和制品最终性能之间的相互作用,才能更好的实现生产过程和制品的质量控制。
已经运用数学模型和计算机模拟来研究它们之间的相互作用,鉴于CAD/CAM/CAE系统在塑料成型中应用越来越广泛,此种研究思路也越来越重要。
注塑成型
将粒状、粉末及液体塑料转变为制品有很多种方法,塑料材料处于可模塑状态并可适用于多种成型方法。
大多数情况下,热塑性材料可以用某些方法成型,而热固性材料需要用其他方法。
这是因为热塑性材料加热后会软化,冷却前可被重塑,而热固性材料在加工前未聚合,成型过程中会发生化学反应,这种反应通常是在热、催化剂或压力的作用下完成的,在进行塑料加工研究和应用时,了解这一点尤为重要。
注塑成型是迄今为止用得最多的一中热塑性材料的成型方法,同时也是历史悠久的一种方法,目前占到塑料成型总量的30%。
由于原料可惜此一步成型,注塑方法适于大批量和一步自动成型复杂几何形状的塑料制品,大多数情况下不需要后续加工。
典型制品有玩具、汽车配件、家庭用具和电子产品。
由于注塑成型时有很多相互关联的变量,这种方法是相当复杂的。
成功的注塑生产不仅有赖于设备参数的正确设置,还在于要消除每次注射时的泼动,这种泼动是由液压系统、料筒温度及材料黏度变化引起的。
提高每次注射时设备参数的稳定性,可得到公差小、次品率低和质量高的产品。
任何成型加工最根本的目标都是:
提高产品质量,缩短成型周期,采用重复性和自动化程度高的循环过程。
模具人员在生产过程中总是想尽办法降低或消除不合格。
用注塑法生产那些精度要求很高的化学产品,或者附加值很高的产品如电器外壳,降低次品率的好处很大。
典型的注塑成型过程由五个阶段组成:
1.注射与充模;
2.补料或压缩;
3.保压;
4.冷却;
5.顶出制品。
注塑概况
工艺
注射成型是一个塑料在压力下进入一个空腔中成为理想形状的的循环过程。
塑造,是通过冷却(热塑性塑料)或由一个化学反应(热固性)来实现的。
这是一个为大规模生产具有优良尺寸精度的复合塑料零部件最常见和最灵活方式。
它需要极少或根本没有整理或装配作业。
除了热塑性塑料和热固性,这个进程现在通过用聚合物粘结剂被扩展到象纤维,陶器,金属粉末这样的材料。
应用
按重量计算大约所有塑料加工的32%是通过注塑成型机器的。
历史上,注入成型的主要里程碑包括往复移动螺丝机器和各种新的替代过程,和应用电脑仿真,以及设计和制造的塑料零部件的发明。
注射机的发展
从19世纪70年代初注入成型机器问世以来它已经经历了显著的修改和改进。
尤其是往复移动螺杆机器的发明使热塑性塑料注塑成型过程的多功能性和生产力得到了彻底改革。
往复移动螺杆的好处
除在机器控制方面和机器起动功能上有明显改进外,注塑成型机器的一个主要发展是从一个活塞机器到一个往复移动螺丝杆的变化。
虽然活塞机本身简单,它的普及受到限制归咎与它仅仅通过纯传导的缓慢的加热速度。
往复移动螺杆用它旋转的运动能使材料塑化更迅速而均匀,如图1中所示使可塑材料。
另外,它能把这个熔融的聚合物注入在一个向前的方向,就像一个活塞。
注塑成型过程的发展
注塑成型过程开始只与热塑性塑料聚合物一起使用在活性材料方面的发展,在塑造设备方面的改进,并且由于特殊工业的需要已经把工艺的用途扩展到超出了他原先的范围
供选择的注塑工艺
在过去二十年期间发展注射模塑已经被做出许多尝试,随着特殊设计发展道具生产零件的工序可用作替换过程,从传统的注射模塑中派生而来的应用策划新时代,它有更多自由设计和特殊结构上特征通过这些努力产生了许多类型,包括:
级进注射(夹心)成型
易熔芯注塑成型
气体辅助注塑成型
压缩注塑成型
层状(微)注射
交替供料的注塑成型
低压注入成型
推拉注塑成型
反应注塑成型
结构泡沫注塑成型
薄壁件成型
计算机模拟注塑成型过程
由于他们的扩展性和希望性,电脑仿真也已经扩展超出早期的"外行-扁平物"现在,复杂程序在过程期间模仿填充后行为,反作用动力学和两材料的不同性质或者二维的使用。
仿真部分提供关于使用C-类型产品的信息在设计题目有中间几例子,其给你怎样能使用CAE工具改进你的部分和塑造设计和使处理状况最优化配上插图。
级进注射(夹心)成型
总体上说
级进注塑成型是通过两种不同的材料连续的和或同时地由同一浇口注射完成的。
材料层板和凝固。
这工艺生产零件,其随着在层皮材料之间把型芯材料嵌入有一层积的结构中.这项创新过程为用最优性能的每一种材料或修改模的一部分属性提供了固有的灵活性。
图1四个阶段的级进注塑成型(a)短球的皮合物融化(显示在里深绿色)注入进那些模型(b)核心聚合物的注射熔化,直到型腔被差不多填补如(c)中所示皮聚合物再次被注入,以便把离开的这个核心聚合物从浇注系统中清除出去
熔心注射成型
熔芯工艺在单个产品中,空的部分用复杂内部结构的易熔(丢失,可溶)如下图。
这个工艺在塑造核芯内部完成,核芯将自身融化或者化学消失,留下它的外部结构作为塑料部分的内部形状。
图1。
易熔(失芯,熔芯)核心注射成型
气体辅助注塑成型
气体辅助工艺
气体辅助注塑成型过程的是树脂聚合物熔体欠料进入模腔。
压缩气体,然后注入的聚合物核心部分帮助填满模具。
这个