电子制造业IQC各工序稽核检查表副本Word文档下载推荐.docx
《电子制造业IQC各工序稽核检查表副本Word文档下载推荐.docx》由会员分享,可在线阅读,更多相关《电子制造业IQC各工序稽核检查表副本Word文档下载推荐.docx(19页珍藏版)》请在冰豆网上搜索。
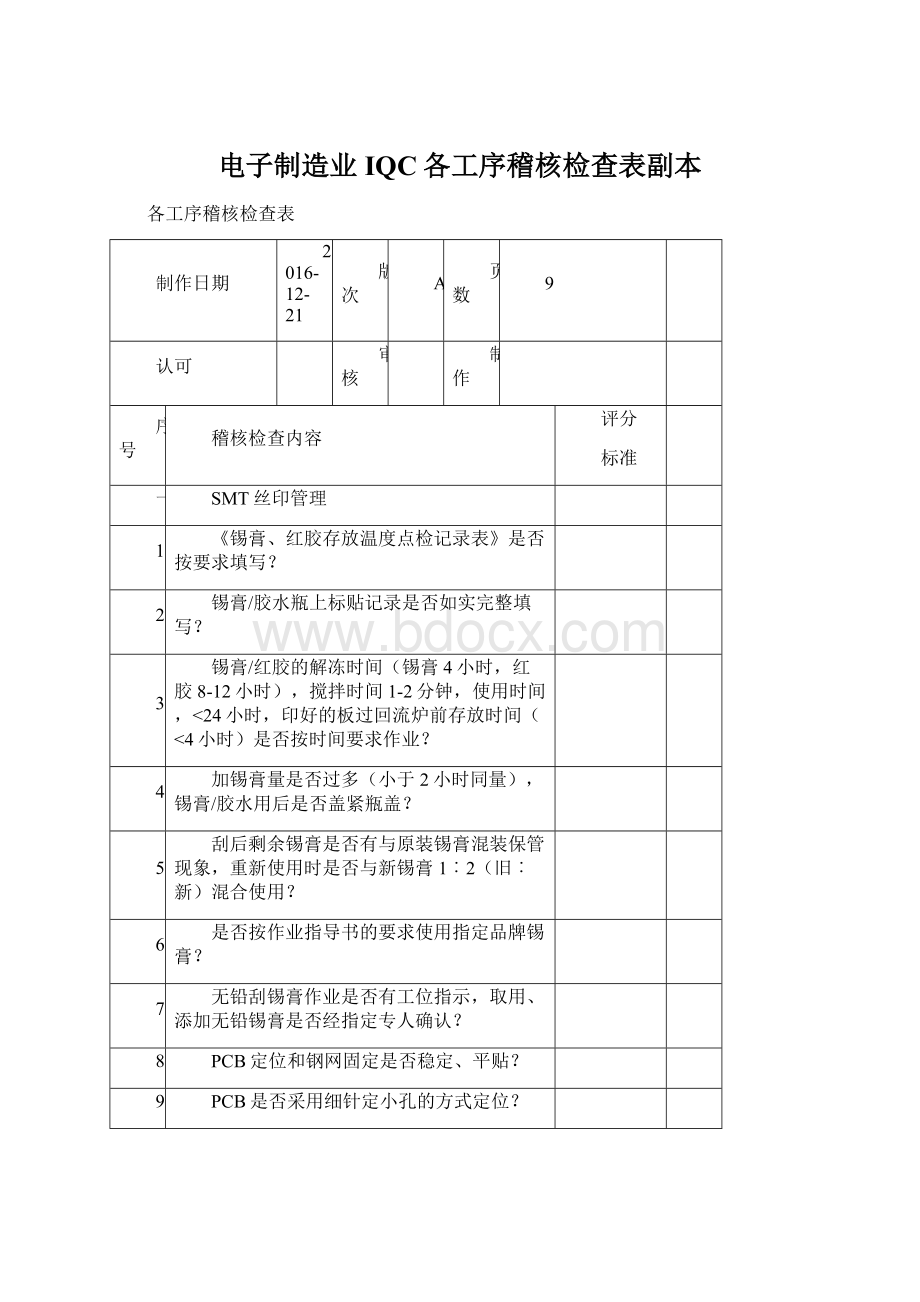
是否按作业指导书要求加厚和封钢网?
11
是否按时清洗钢网、刮刀、搅刀?
丝印台、工作台是否有保持干净、整洁,无任何锡膏残留?
12
是否在PCB放入前按规定要求用不脱毛的碎布擦拭钢网(≤3PCS擦一次)?
13
作业员是否对完成品进行100%自检?
14
刮锡膏/胶水的完成品是否平放,待打板是否超过规定数量和遵循“先刮先用”的原则?
15
胶水板是否慢速刮且刮刀与钢网成45°
角度?
16
不良品是否经IPQC或组长确认后用无水酒精清洗?
清洗后是否再次经IPQC检查确认后使用?
17
底面有零件的板卡在印刷时是否确认顶针没有顶住零件的现象?
18
钢网是否按作业指导书要求定时清洗,刮锡膏间隔12小时,刮红胶间隔4小时,是否填写“钢网清洗记录表”记录。
19
20
二
SMT换料作业
《SMT上料记录表》是否如实、即时和正确的填写?
散料是否经IPQC检查OK后开机打件?
操作员相互对料动作是否在开机打件前进行?
备用物料是否按站位号对应摆放于料架小车上?
同一时间是否只取一个供料器换料?
“0805”及以下的电阻、电容类零件否保留样品?
IC、BGA等极性元件在开机前是否确认方向?
同时在作业指导书中是否对极性的辨别做特别说明?
换料时取下的空料盘是否经IPQC确认?
操作员是否定时检查板卡的品质状况并追踪改善?
品质出现异常时,操作员是否反馈给技术员解决?
故障供料器是否标故障,撕掉PASS标后送修,使用中的供料器是否有PASS标贴?
操作员是否正确填写“SMT生产进度表”,有异常的停机现象是否即时的报告和记录?
用大量的料是否预先装好料待用,换料动作是否按顺序“取出供料器备用供料器装
料放入站位拆出原供料器料盘”进行作业,以节省机器停机时间?
三
手贴作业
手贴物料是否标示规格、型号、位置,IC是否标示丝印,备用料是否也有规格、型号标示?
是否按极性方向排列,无堆料现象?
手贴散料放置是否使用防静电盒或防静电盘?
台面物品的摆放或拿放板的方式是否有造成抹件的现象?
对抛料、抹件和漏料板是否有自行修复没有按流程修复的现象?
零件脚是否偏出焊盘、抹锡膏或连锡膏的现象?
堆板是否按“先进先出”的原则处理?
零件脚变形的器件是否专人整形OK后使用?
零件贴装后是否有下压零件动作?
手贴零件下有焊盘是否确认焊盘上无锡膏后再贴?
是否互检前工位零件的极性方向和偏位,互检是否记入《个人作业不良记录表》中?
小料加料时是否使用完毕后再加,是否有通知IPQC确认?
交接班时物料是否交接清楚并记录?
四
炉前送板
机种更换时是否有确认回流炉参数设置是否与机种符合?
炉前是否有IPQC确认的样板参照检查?
送板过炉是否有锡纸重叠或铝纸残缺的现象?
PCB是否有锡纸重叠过炉的现象?
板厚小于1.6mm的大板是否垫板作业并用双手端放在回流焊网带上,以免PCB变形造成IC移位?
五
炉后捡板
炉否检查IC连焊和不熔锡现象,并有相应的记录?
是否清洁排骨架后放板?
放板是否有卡零件的现象?
贴标签是否有作业指示,是否经IPQC首件确认后才批量贴?
作业区是否放置未正在使用的标签?
不良品过高是否反馈给组长和技术员?
六
SMT补件作业
是否经培训合格的专职人员作业?
补件前阻容类零件是否有量测?
补件元件旁是否有打颜色标记点,是否有责任人标示和位置指示,以区分责任人和指示补件位置?
是否经品质部IPQC进行零件规格、型号的确认?
补件OK板是否保留黄箭头标签指示已补零件?
元件是否有分类、区分、标示、补件的料盒内是否存在混料现象?
无丝印且无法测量的元件是否直接在料盘上取料修补?
是否有补件记录?
IPQC检查确认后是否有签名?
七
生产和物料控制
《订单确认表》是否以看板或其它方式和会各相关人员?
领料员是否领料与BOM不符或有疑问物料?
领料时是否核对料号和规格?
散料领用是否已有明确标示、签名,无法量测且丝印不能与BOM对应的散料(如三极管)是否有IQC签名确认?
裁剪的物料是否有保留原装料盘或标签以便查验?
来料上线前是否标示客户名称、机种?
散装物料是否有接带的现象?
物料和生产是否按批号、客户、型号区分管理?
物料、半成品的领用、交接是否有记录,PCB是否配发放,是否如实填写记录,并填写批号、批量、客户、型号?
机器的分配及安排计划是否用看板显示?
客户烧录软件是否有《软件流程单》,领料单上是否注明校验码?
作业前相关的作业指示是否追踪到位?
《转线通知单》是否即时发放?
转线前所有物料及准备工作是否到位?
打“X”PCB是否分类区分清楚数量后下线?
新产品上线是否填写《样板制作确认表》交工程部跟线并制作首件?
须区分的板是否以“下线条”的方式通知后工序?
清尾欠料板是否有专人跟踪并区分、标示、隔离?
BGA(如客户、工艺有特殊要求的零件和PCB)是否按要求进行烘烤作业?
IC是否按要求保管于防潮柜中)
欠料是否即时(1小工作日内)报仓库领料?
贵重物料或产品是否有下班前盘点,专人负责并有效保管?
制程各站是否按时填写看板显示生产状况?
21
各站是否制订标准产能,转线时间是否在规定时间内?
22
每日生产例会是否召开并有记录?
生产计划、产能、品质目标的达成及物料异常是否每日追踪并检讨?
23
24
八
平面焊
是否有私自调整烙铁温度的现象,烙铁温度是否在规定范围?
是否有叠板、堆板、推板的现象,台面是否干净整洁?
双面零件板下线是否有加珍珠棉保护?
是否有敲烙铁头现象?
海棉水份是否适当,使用烙铁前是否保持烙铁嘴干净?
拖IC前是否有加助焊剂,三下拖不干净是否再加助焊剂,是否沿IC脚方向拖焊?
后加IC作业否所有IC脚拖焊2次或以上?
相似板是否有同时下线现象?
后加零件业是否有通知IPQC进行首件检查确认?
撞件、漏件、错位和反向是否贴黄箭头标签指示?
九
零件加工
不同加工方式的元件是否预先做好区分?
同一型号、规格,相同加工方式的元件是否单独集中后再加工?
同一工作区内是否存在两种或两种以上规格的加工或待加工元件?
剪脚作业是否挡飞脚的措施?
脚直径在0.6MM以上的元件,整形时是否按作业指导书上的要求操作,避免使脚的根部受力,损坏元件?
不同客户、不同机种的物料是否区分放置?
机器剪脚零件脚长是否在规定范围内,每种型号是否有试插检查?
加工完毕品是否保留原装标示标贴?
十
插件
分板作业是否用分板机分板,如特殊板不能分板机作业,是否有用治具按要求作业?
外观相同或相似零件是否编排于不同工位?
物料盒、待处理零件盒是否有标示?
待插物料是否有明确的工位区分(如:
划线或放置于固定盒内)?
是否实施互检,《个人作业不良记录》中是否有记录互检不良?
开线、转线、换料、加料和捡起零件是否核对其正确性再用?
组长或物料员在转线时是否对各工位使用的物料进行核对?
贴胶纸是否有垫防静电垫或防静电海棉,是否用非金属物切割胶纸?
是否有挂伤板卡的现象?
插件员工是否双手交替作业?
插件工位区域内是否有散落零件?
流水线上PCB放置是否因空位造成作业员等板的现象?
流水线速度与作业速度是否一致?
掉件的板卡是否贴上标记重新下线,零件规格是否经确认后插入PCB?
套模是否面向下放置,使用前是否检查和清理杂物后才使用?
套模是否定时(2天)或定量(使用400次)用酒精浸泡清洗?
手推插件线作业员之间是否保持以不碰手的最小距离?
十一
波峰焊
波峰焊参数设置是否与《波峰焊参数设定记录表》相符合?
波峰焊是否保养计划实施,并如实记录在《设备日常保养记录表》中?
《波峰焊每月参数记录表》是否按时检查,如实填写?
锡炉表面是否保持一层液态的抗氧化油?
锡面高度是否控制在±
5mm内,助焊剂用量是否过多?
波峰在过窄板时是否有加波峰挡板以减少锡氧化?
下班前是否将剩余锡条加完?
是否有元件脚过长,刮到波峰,甚至造成PCB停顿的现象?
波峰操作员是否每半小时内检查一次炉后产品的焊接品质状况?
异常情况是否及时处理并报告异常的处理结果?
因过炉造成的PCB变形是否在1︰100(变形尺寸︰板长度)的要求内?
炉后是否有连锡、SMT红胶元件空焊、DIP元件未上锡造成空焊和掉件等现象?
外露出PCB边缘的元件(如:
插座、开关等)是否有防护和防助剂喷雾措施?
无铅锡条的添加是否有专人确认和记录,是否有无铅作业标示?
十二
补焊
波峰焊出是否有PCB跌落现象,手工接板是否托住PCB从大零件拿取,是否有PCB受力变形的现象?
波峰后第一工位是否有检查炉后异常情况?
掉件、溢锡板是否贴黄色箭头标签交专人处理,处理完后是否单独送检?
补件修板人员是否经培训合格后指定的专人作业,修补后是否作颜色责任标记位置?
是否修补有记录?
小锡炉温度和浸锡时间是否符合规定?
是否有私自调整烙铁温度的现象,烙铁温度是否符合要求?
剪脚作业是否有防“飞脚”措施,零件脚是否飞出防护罩?
防护罩内是否放有其它半成品?
剪钳是否有定时检查刀刃记录?
评分标准
零件剪脚方法、动作是否正确,是否有剪伤锡点,剪完后是否有检查其脚长?
烙铁海绵是否定时清洁并保持适量水分,烙铁头是否干净?
后加元件是否标示位置、规格,是否通知IPQC进行首件检查?
流水线上不同工位的放板方向和位置是否有规定区分,保持整齐和间隔均匀、适当?
下班时传送带线上是否有留板现象?
双面有SMT零件的板是否加海绵保护后才下线?
十三
测试
作业指导书上的测试步骤和方法是否与实际操作一致,有无漏测现象?
作业员是否有规定相应的代号,测试OK后的板卡是否在标签规定位置签上作业员代号?
所有板卡是否按要求摆放?
FLASH拷贝和升级是否完全按软件管理规定执行?
良品、不良品是否分区域摆放,且有明确的标识?
仪器、仪表是否在校验有效内?
不良品标识单是否填写完整及清楚?
故障卡是否立即挂在测出的不良品上后再进行其它板的测试?
所有报表每小时是否按时记录,测试出的不良现象是否立即记录?
出现功能不稳定现象的板卡是否经过反复确认OK后才下线,如多次出现是否报告技术员分析原因?
维修OK板是否按正常流程操作?
FLASH拷贝和升级软件是否进行功能测试以确认其软件的正确性?
软件拷贝记录是否填写完整?
碟片是否读碟面朝上放置,是否有重叠的现象?
贵重的专用测试碟是否每班有专人进行使用状况的确认?
如怀疑会烧机芯的板,不可拿到其它工装测试,是否单独交维修分析并记录?
测试OK板在流水线上是否按统一方向和位置放置?
为避免机芯烧坏,测试排线的使用、检查、修复、更换是否按规定进行?
十四
包装
包装时检查周转箱、包材是否干净、是否有水分?
周转箱外部残留的标签是否清除干净?
包装时检查测试OK的板是否有贴PASS标签?
记号是否正确?
新产品散包的包装方式是否经品质主管和工程人员确认?
散包时层与层之间是否有隔板,板与板之间是否有撞件可能?
板卡上的易损零件(如显示屏、轻触开关)包装时是否采取保护措施?
彩包时,附件是否以“箱”为单位数好后再包?
以避免漏装?
每层、每箱装满后是否有确认数量?
相似的板是否有同时下线的现象?
是否作特别区分?
包材、包装OK板、QA待验板、QAPASS板、待返工板是否按区域整齐摆放?
堆放高度是否符合规定?
外箱标示的填写是否符合要求?
包装OK板是否即时填写“送检单”送QA抽检?
贵重产品是否有滞留在生产线未即时入库的现象?
未满箱的尾数板有无滞留生产线未作管制或未即时入库的现象?
没有满箱的尾数出货是否采取填充或其它防护措施?
十五
品质控制
(一)
QC
检查的区域和内容是否明确?
有无示意图和作业指导书?
是否有IPQC确认的样板作为检查依据?
是否有明确的品质标准?
是否了解和熟悉?
不良品过高或出现异常时是否及时反馈组长或IPQC?
每日是否对QA不良板、电性维修不良板进行分析改善?
是否有责任人记录并作为考核成绩的重要依据?
是否建立机种履历(或病历)记录?
机种上线是否查阅履历记录?
有工程变更的板卡是否相关各站重点检查区分?
是否有IPQC确认的样板?
QC代码是否有记录存档?
检查PASS的板是否作检查人区分标记或标代码以便追朔?
对特殊流程的板卡(如补件板)是否按要求内容检查确认?
是否使用放大镜检查SMT料件?
补焊线对套模过炉的板是否再检查SMT零件焊点?
(二)
IPQC
是否理解熟悉程序文件,共通作业指导书和检验规范的含义和内容?
是否按文件要求稽核检查?
首件核对是否按时按要求执行?
转线和后加零件是否对线上物料及标示检查?
是否提供首件OK板给QC作为检查样板?
新产品首件核对后2小时内是否由另外一名IPQC再核对一次SMT物料?
样板上是否有时间和签名?
SMT站位物料核对是否核对物料实物规格、站位、料盘和空料盘标示与站位表一致以后才在换料记录上签名?
对料前是否确认对料的相关文件资料是否齐全,并且是最新有效版本?
(相关文件资料有:
BOM、工程变更单、代用单、订单确认表、转线流程单、软件流程单,客户样板)
未变更BOM单或未完成的工程变更单是否与BOM单附一起保存,以避免遗漏?
对特殊岗位的作业员是否对其进行资格检查确认?
每日是否如实测量烙铁、小锡炉温度并记录?
静电环检测和使用有无监督执行?
回流炉后抽检是否制作管制图?
异常问题是否追踪解决?
是否按时如实填写IPQC检查记录?
对异常问题是否追踪责任人改善并签名确认?
对有疑问的事项是否询问相关部门责任人明确后执行?
十六
现象共同部分
5S
5S的检查内容、检查频率和评比标准是否有文件规定?
5S的责任区域和作业要求是否有文件规定?
相关责任人是否明确自己的责任范围和要求?
5S作业和检查是否按规定执行?
检查结果是否有看板公布?
5S未达要求的责任人是否有相应的改善措施、改善措施是否有效?
文件控制
现场使用的文件是否经指定责任人审批、认可?
现场文件是否为最新有效版本、旧版本是否完全回收或作废处理?
受控文件是否有盖“受控”印章?
现场文件是否妥善保管?
作业内容是否有相应的作业指示或经认可的样板?
“工程变更通知单”、“订单确认表”上的作业要求是否通过有效的方式知会作业现场?
(三)
静电防护
SMT机房作业员是否穿戴防静电工作服、鞋、帽?
所有人员是否戴静电手套或防静电环接触产品和零件?
静电环测试和工作台面接地检查是否每日进行?
记录是否完整?
地线、防静电台面、防静电服和防静电胶箱是否定期测试?
SMT物料、产品是否使用防静电材料箱(盒)放置?
(四)
物品的标示及放置
产品和物料是否有明确的标示?
不同状态的物品是否有明确的区分或区域放置?
作业现场是否有不明确状态的物品存在?
SMT炉前异常堆板是否有标示开始堆放的时间?
物品堆放是否整齐?
堆放高度是否超过规定高度?
箱内物品是否有压住现象?
排骨架放板方式是否有经IPQC确认?
是否有卡住零件的现象?
作业中是否有推板、叠板、甩板现象?
工位堆板是否超过规定数量?
(五)
不良品处理
发现不良品是否立即标示和记录?
不良品是否有专用的胶箱、排骨架、零件盒放置?
是否有颜色的区分(红色)?
不良品是否有指定不良品区域或车架区分放置并标示?
良品、不良品是否隔离放置?
有无同放一处的现象(如同一车架、同一区域、同一箱)?
不良品是否即时知会相关责任人?
QC、维修报表相关责任人是否每2小时签名确认并追踪改善?
作业不良品是否有个人作业不良记录?
是否作为考核的重要依据?
特殊不良品(如少件、错件、坏件、反向、IC移位、板面上锡)是否有贴黄色标签标示(插件线不良品除外)?
是否指定专人修复并经培训合格上岗?
修复后是否单独送检?
不良率超标是否有相应的改善措施和记录?
电性不良品维修是否按流程进行?
维修记录是否准确完整?
测试PASS板,有外观不良经烙铁修复后是否经QC检查后再测试?
(六)
报表的填写
作业现场所使用的各类报表记录是否按时如实填写和签名?
是否按要求归档保管?
各工序生产看板是否按要求填写?
(七)
工作纪律
工衣工帽是否穿戴整齐整洁?
衣扣、袖扣是否扣上?
是否有串岗、聊天的现象?
是否提前五分钟进入工作岗位做好作业准备?
是否上班前十分钟开始早训(会)?
下班是否集合后排队离开工作现场?
是否有擅自离岗现象?
交接班时,物料和作业要求是否交接清楚并有首件确认后离岗?