培养基模拟灌装方案文档格式.docx
《培养基模拟灌装方案文档格式.docx》由会员分享,可在线阅读,更多相关《培养基模拟灌装方案文档格式.docx(82页珍藏版)》请在冰豆网上搜索。
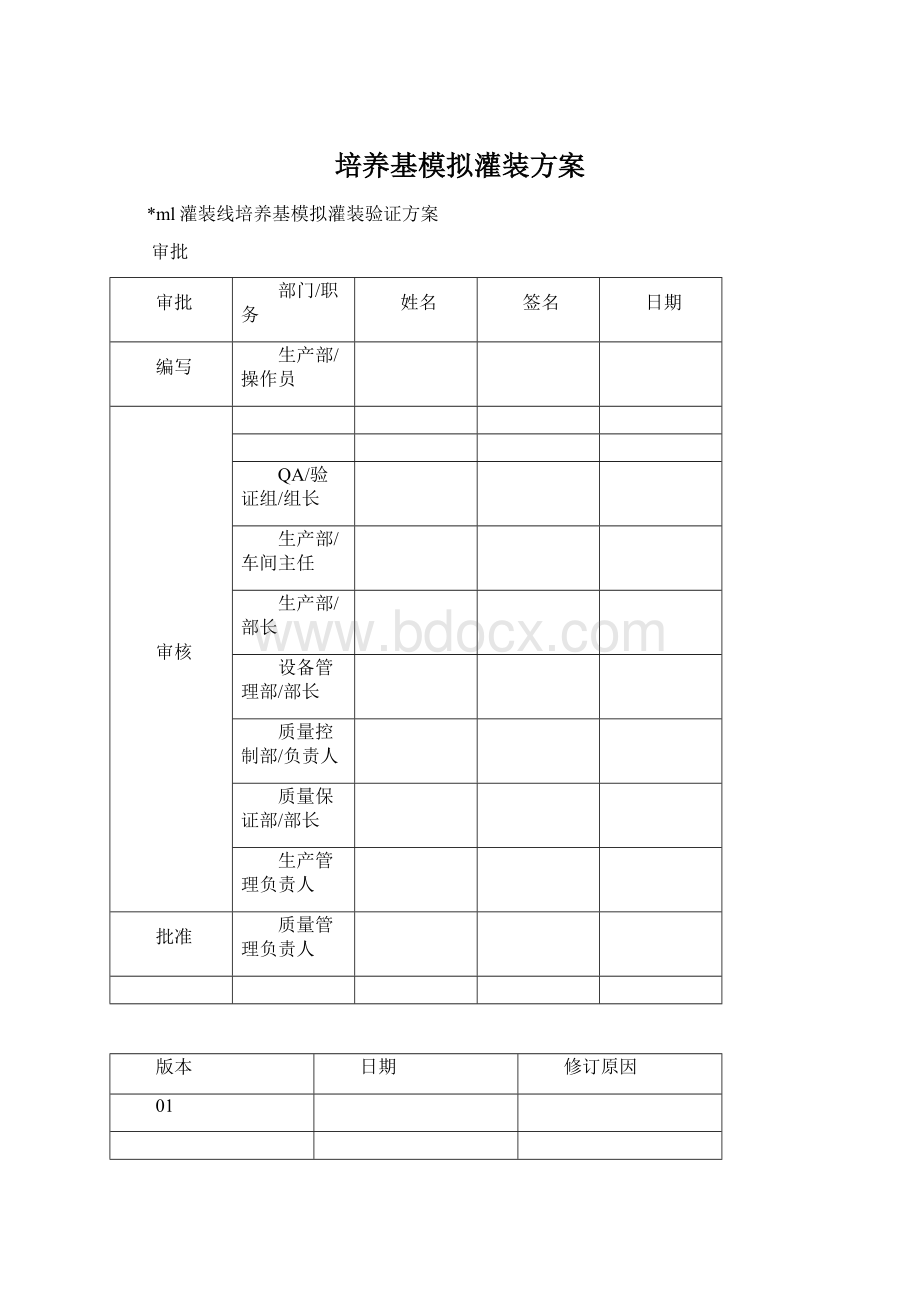
✓模拟灌装过程中涉及到的生产工艺包括:
产品的配制、存储和除菌过滤,西林瓶的清洗灭菌、免洗胶塞灭菌、分装器具组装、除菌过滤、无菌灌装、压塞、轧盖的全过程。
✓生产所用物料的转移,包括半成品的转移及灭菌后包材、器具等的转移。
4.职责
4.1.生产部职责
✓方案编写
✓报告编写
✓方案的执行
4.2.质量保证部职责
✓审核方案
✓保证在执行前所有的先决条件得到满足
✓方案监督执行
✓审核报告
4.3.质量控制部职责
✓检测各项指标是否合格
4.4.设备部、物资管理部门各职责
✓对方案中的相关项目进行协助确认
4.5.质量管理负责人职责
✓批准方案
✓批准报告
5.法规和指南
为编写本方案,参考了以下法规和指南:
5.1.法规
✓国家食品药品监督管理总局(CFDA),中国,药品生产质量管理规范(2010年修订),2011年03月
5.2.指南
✓EudraLex第四卷欧盟药品生产质量管理规范指南医药产品人用及兽用,2008年11月
✓美国食品药品监督管理局,美国,美国FDA行业指南—无菌工艺所生产的无菌药品—现行药品生产质量管理规范,2004年9月29日
✓国家药典委员会,中国,中国药典(ChP)2015年版
✓美国药典委员会,美国,美国药典(USP)第34版,2011年
✓欧洲药品质量管理局,欧洲药典(EP)第7版,2011年
✓PIC/SPI007-5无菌工艺验证
✓无菌灌装产品的工艺模拟,PDA技术报告22,2011年版
✓无菌工艺模拟试验指南(无菌制剂)
6.参考文件
为编写本方案,参考了以下文件:
文件名称
文件编号
7.生产工艺描述
7.1.工艺流程图
7.2.模拟灌装验证流程图
模拟灌装过程流程图
7.3.模拟生产工艺过程描
7.3.1模拟产品生产规模:
产品批量
批号
M2
7.3.2生产制度
灌装工艺每批次由1个班次执行。
具体的工艺操作过程如下。
7.3.3生产前检查
在生产前检查环境卫生、设备、公共系统、上批次文件及物料和分装用具。
7.3.4操作前检查
包括分装指令的接收和半成品交接确认,生产状态标识的检查。
7.3.5生产操作
包括灌装间1操作人员的进入、分装器具组装前环境监测、分装器具的组装、制品除菌过滤、灌装和加塞操作。
7.3.6轧盖
制品灌装加塞后经水平传送带传至轧盖间1轧盖输瓶网带,然后开始进行制品轧盖,将刚开始轧盖的制品抽样进行检查,检查合格后正式开始制品轧盖。
7.4.基本原理
培养基模拟灌装试验将使用TSB培养基进行模拟灌装及培养,综合考虑生产线上所有潜在的污染风险因素,模拟无菌工艺生产过程,确认TSB培养基是否在工艺过程中被污染。
它将模拟无菌工艺生产的操作,并考虑最差情况的模拟,对无菌操作进行挑战。
模拟过程中的环境监测的数据也将作为工艺评估的有用信息。
无菌工艺模拟主要关注的是工艺、人员、设备和器具。
7.5.工艺:
无菌容器具及培养基的转运;
✓C/D级环境中包装材料的清洗灭菌及A级洁净区保护下影响无菌状态的工艺和操作;
✓设备、无菌器具、包材的清洗和灭菌;
✓设备的无菌连接,如灌装机部件灭菌后的装配,灌装针头的连接等;
✓除菌过滤后药液接收;
✓半成品的灌装、加塞过程;
✓加塞后产品的转移;
✓轧盖
7.6.人员:
所有参与无菌工艺过程的人员:
✓生产线各个岗位上的操作人员,包括西林瓶清洗灭菌、胶塞及铝盖清洗灭菌、无菌过滤、灌装、轧盖等;
✓质保人员;
✓维修人员。
7.7.设备和器具:
✓与物料直接接触的工艺设备,如灌装机;
✓其他工艺设备:
包括洗瓶机、灭菌隧道、轧盖机、湿热灭菌柜等;
✓环境控制设备,包括RABS、层流罩、传递窗;
✓监测系统与仪器,包括尘埃粒子测试仪、浮游菌取样仪等;
✓辅助器具,包括物料传递桶,取样器具等。
7.8.运行频次和周期
培养基模拟灌装试验的首次验证,每班次应当连续进行三次合格试验。
空气净化系统、设备、生产工艺及人员重大变更后,应当重复进行培养基模拟灌装试验。
正常生产期间培养基模拟灌装试验应当按照每条生产线每班次每半年进行一次,每次至少一批。
本次为培养基模拟灌装试验每半年进行一次的验证,每班次应当进行1次合格试验,即完成1批验证。
综合以上信息,模拟灌装方案安排如下:
模拟规格
参与班次
批次信息
所有班次
1批
******
每批次工艺模拟时间应涵盖总工艺时间,本次计划模拟灌装时间8小时左右。
在灌装过程中除完成各项干预和最差条件模拟外,其余时间应采用以设备低速运转的方法/停机进行时间的等待。
7.9.运行数量
本次模拟灌装批量约为20000瓶/次,灌装量3ml/瓶进行模拟,旨在使培养基充分的与生产用的器具、设备充分接触,从而全面检查生产工艺的无菌保证水平。
7.10.模拟物料和培养基
7ml灌装线是将产品在无菌保证的条件下进行灌装的过程,主要工艺步骤包括西林瓶的清洗灭菌、免洗胶塞灭菌、无菌过滤、无菌灌装加塞、轧盖等。
根据PIC/SPI007-5《无菌工艺验证》的建议,无菌工艺模拟所需的培养基需要能支持大范围的微生物生长,也就是能支持诸如枯草芽孢杆菌、金黄色葡萄球菌、白色念珠菌、黑曲霉和芽孢梭菌等大范围的微生物生长;
胰蛋白胨大豆肉汤培养基(TSB)不仅适合于需氧菌的生长,而且适合真菌生长。
因此,本次模拟灌装采用TSB培养基作为模拟物料,并进行培养。
用TSB培养基模拟物料在灌装机中的灌装过程,然后进行压塞,轧盖等。
在工艺模拟过程中,需要对配制好的培养基和灭菌后的培养基进行无菌和促生长能力测试,以确认工艺模拟使用的培养基适合微生物的生长。
7.11.密闭和开放系统
本工艺中包含在“密闭”和“开放”系统下的两种操作。
有无菌物料暴露的“开放”环节采用A级送风保护。
对开放系统下的操作判定为高风险,每次都要在验证中进行确认;
对密闭系统下的操作判定为低风险,可以在验证过程中进行监控即可。
序号
项目名称
密闭/开放
当前控制方法
风险级别
1.
西林瓶的清洗
开放
D级环境
低
2.
铝塑盖清洗
C级环境
3.
隧道灭菌
A级保护
高
4.
免洗胶塞灭菌
密闭
5.
铝塑盖灭菌
6.
灭菌后胶塞转运和添加
7.
灭菌后铝塑盖转运和添加
C级到A级保护
8.
无菌管道连接
9.
除菌过滤器的连接
10.
陶瓷泵安装
11.
过塞板安装
12.
压塞盘安装
13.
胶塞料斗安装
14.
胶塞缓冲斗安装
15.
分液器连接
16.
硅胶管及灌装针头连接
17.
100L缓冲罐的连接
18.
铝盖缓冲斗
19.
除菌过滤
20.
灌装、加塞过程
RABS内
21.
轧盖过程
7.12.风险评估
需要对培养基模拟灌装试验风险分析时确认的危害进行全面的审查以保证能够确定出所有的潜在风险并对其进行评估。
采用故障模式和影响分析(FMEA)的风险工具来进行风险评估,见下表风险评估矩阵。
在本方案中风险评估的表达将使用定性描述,如“高”、“中”、“低”。
一个风险的判定依靠风险优先性来定义。
严重性(S)
严重性是衡量危害可能后果的一个指标。
在此阶段需要对失效的可能后果进行评估。
对失效可能造成的影响进行描述(即使没有失效发生的大的可能性)。
下面表格是对分级的说明。
对于每个确认的风险均要确定严重性。
严重性
描述
高(H)
预计会对产品质量产生显着的影响(不符合质量标准)。
中(M)
预计会对产品质量产生较小的影响(不符合质量标准)。
低(L)
预计会对产品质量无影响或很微小的影响(质量在标准之内)。
注:
当潜在关键工艺参数的严重性被评估为“H”时,该工艺参数被自动升级为关键工艺参数。
可能性(P)
发生的可能性是列出可能发生的原因及产生所描述的失效模式的可能性。
在现有或类似的设计/过程历史数据可用来评估可能性。
了解失效发生的可能性,帮助选择适宜的控制方法对所确定的风险进行控制。
描述失效发生的可能性(依据失效来源的描述)。
下表列出对于每种确认原因的可能性分级。
可能性
发生可能性高。
以往经验表明已经发生过,或者明确知道会发生的,具有较窄的操作范围的。
根据知识判断可能会发生的。
操作范围接近于设定范围,或参数范围比较宽,参数本身比较容易控制。
异常情况下才会偏离范围。
没有发生过,且根据知识判断发生概率微小的。
操作范围远比设定范围窄,或参数范围比较宽,紧急情况下才会偏离设计空间。
风险级别评价
将把严重性和可能性合在一起来评价风险级别。
将采用如下方法来确定风险级别:
可能性低
可能性中
可能性高
严重性高
风险级别2
风险级别1
严重性中
风险级别3
严重性低
可检测性(D)
可检测性是基于确定的过程控制/检查将产生原因在失效前预防或消除的可能性。
了解失效的可检测性也可以帮助选择适宜的控制方法对所确定的风险进行控制。
失效可以通过自控系统自动检测,或是通过手动方法进行检测。
描述失效的可检测性。
下表列出对于每种可检测性的分级。
可检测性
失效能通过设备控制及报警自动发现,并能自动采取恢复措施。
失效很容易被操作人员或通过报警方式发现。
失效不太可能被操作人员或设备控制系统发现。
7.13.工艺风险分析
在生产工艺过程中的很多步骤中会有一些操作对非最终灭菌产品的无菌水平存在关键的影响,通过以下的分析,确定在培养基模拟灌装过程中所需采取的模拟手段和工艺。
基于《人免疫球蛋白工艺风险评估报告》需要进行无菌工艺模拟验证,工艺的工序或关键控制点在下表中列出。
工序
可能出现的情况
对无菌性影响的风险分析
关键性
风险控制措施
西林瓶的清洗灭菌
西林瓶的清洗、灭菌不合格
直接影响产品无菌性
关键的
洗瓶机和灭菌隧道的PQ已完成
免洗胶塞灭菌
胶塞灭菌不合格
胶塞灭菌后检查打包所用呼吸袋边上的灭菌指示带是否变色
湿热灭菌柜的PQ已完成
过滤器完整性检测不合格
制定SOP,每次在过滤完成后检测完整性
检测过滤后培养基的无菌性
灌装工序
操作人员应完成培训,并考评合格
在模拟灌装试验中模拟过程操作
分装器具的组装
只有经培训且考核合格的人员才能进行组装操作
灭菌后胶塞的转运和添加
灌装过程的人员干预
工器具灭菌不合格
灭菌指示带变色
灌装机内部操作环境不符合A级环境
确认灌装机PQ已完成
实时动态环境监测
在模拟灌装试验中进行灌装操作
灌装总时间过长
增加总产品的暴露时间
模拟灌装挑战产品最长暴露时间
灌装过程停机
增加物料在设备中的保留或暴露时间
定期进行维护保养
在模拟灌装过程中设备进行维修
轧盖工序
轧盖不严密
影响包装密封性,导致产品被污染
在模拟灌装过程中模拟轧盖过程
7.14.模拟项目
模拟灌装过程
以考察物料暴露最长时间和最大灌装速度的最大操作难度下工艺的无菌保证;
灌装机各分装器具经灭菌后的无菌组装
如设备部件组装、灌装针头的连接等;
模拟最多进入灌装间的人数
包括现场操作人员(4人)、维修人员(1人)、现场QA人员(1人)等,但是同时在灌装间的总人数不超过5人;
人员干预
模拟人员干预项目
(灌装过程中)
次数/时间
(轧盖过程中)
开RABS门次数
8次
9次
调整灌装针头
3次/班次/批
灌装过程中更换沉降菌碟
2次/班次/批
卡瓶
卡盖
倒瓶
调整装量
5次/班次/批
更换沉降菌碟
灌装过程中卡塞
注:
模拟灌装过程中有人员干预的情况下灌装的培养基要用记号笔做好标记单独培养
模拟人员活动
模拟人员活动
手消毒
20-30分钟进行一次
模拟灌装人员中途休息
1次/人/批
更换手套
至少每隔一小时更换一双手套,但在操作过程中手套被污染,应立即进行更换、消毒
模拟设备故障,灌装机灌装过程中停机,维修人员模拟维修
1次/班次/批/10min
接打车间内线电话
不做规定
加胶塞
9次/班次/批
写记录
加铝盖
10次/班次/批
模拟最差条件
(1)胶塞、灌装机部件、器具灭菌后放至相应SOP规定的最长时间前(48h)使用。
(2)使用的物品应放至相应SOP最长的保留时间前使用,如洁净工作服(72h)等。
(3)本次模拟灌装共1个批次,每一批次的模拟灌装将模拟部分的最差条件,具体见下表:
(本方案中“Y”代表可以达到规定要求,“N/A”代表不适用)
最差条件
模拟参数
7ml西林瓶
批号M2
1
模拟灌装过程的工艺速度
前10000瓶:
220瓶/分钟,后10000瓶:
180瓶/分钟
Y
2
灌装机分装器具灭菌后的无菌组装
1次
3
模拟最多进入灌装间的人数,同时在灌装间的总人数
5人
4
人员干预最大次数
按照本方案条执行
5
6
模拟人员中途休息
7
胶塞、灌装机部件、器具灭菌后放置至相应SOP规定的最长时间前使用
48h
8
使用的物品应放置至相应SOP规定最长的保留时间前使用,如洁净工作服
72h
9
模拟设备故障,灌装过程中停机
10min
10
模拟正常停机
60min
7.15.灌装体积
计算7ml的瓶高,选择培养基体积时,应保证满足瓶容量1/3~1/2,目前选定的3ml的灌装体积。
7.16.模拟培养基灌装样品的培养和检查
模拟培养基灌装样品应按照相关规定由QC进行培养和检查、监督工作,程序如下:
灌装后的西林瓶应进行目测,将所有轧盖不完整、裂瓶等已知可能导致后续微生物污染的产品剔除,剔除的产品应计数。
在进入培养前应充分震摇,以保证培养基能够充分接触到西林瓶和胶塞的内表面,先在±
℃正置培养7天,培养完毕后进行目视检查,应无微生物生长;
低温培养完毕后,若无微生物生长,转移至±
℃倒置培养7天,培养完毕后进行目视检查;
应无微生物生长。
在最终检测时如果发现有产品染菌,应启动偏差调查,偏差调查至少应注明发现染菌的产品的发生时间,并应当进行菌种鉴别,至少鉴定到属,如果有可能则鉴定到种。
7.17.人员
各岗位操作人员和参加验证的人员数目列表:
工序名称
每班人数
西林瓶的清洗、灭菌岗位
灌装物品准备
灌装、加塞
轧盖
清洗/灭菌操作员
洁净服处理操作员
消毒液配制/清洁操作员
维修人员
质保人员
7.18.工艺模拟
本次验证使用3g/100ml胰蛋白胨大豆肉汤培养基(TSB)模拟7ml制品的无菌灌装过程,按照方案描述进行模拟灌装,将无菌TSB培养基按照3ml/瓶,灌入西林瓶,然后进行加塞,轧盖。
按照批量为20000瓶,TSB培养基装量为3ml/瓶,过程损耗及取样为5000ml,因此TSB原料为1950g/批。
在配制罐中,配制3g/100mlTSB培养基,培养基在除菌间除菌过滤后进入灌装间1,将100L缓冲罐与分液器进液口连接、分液器的出液口与陶瓷泵进液口连接、陶瓷泵出液口与灌装针头连接。
胶塞经过灭菌之后,模拟灭菌后的胶塞向灌装机胶塞料斗转运和添加的过程。
西林瓶在完成洗瓶机清洗,灭菌隧道灭菌后经传送带传送至灌装机,灌装机装量自动调节和控制,将TSB培养基装入西林瓶中,经过液体灌装器灌装3g/100mlTSB培养基,经过加塞后,转移至轧盖机进行轧盖。
本次验证活动共进行一批模拟灌装试验,前10000瓶采用220瓶分钟的最快速度灌装,后10000瓶采用180瓶/分钟速度灌装,模拟试验包含日常生产可能的灌装速度范围,分别考察灌装线在相应灌装速度时可能的操作难度和可能的最长暴露时间,从而考察灌装线灌装工艺的无菌保证水平。
培养基模拟灌装执行过程中详细的操作步骤,包括生产操作的模拟,设备的清洗、灭菌,分别按各个生产岗位的工艺操作SOP及设备/仪器操作SOP进行,以尽可能的模拟日常生产的实际情况,考察生产车间7ml灌装线的无菌保证能力。
在本方案中只对主要操作过程和控制参数进行描述。
在培养结束后,取25瓶灌有TSB的产品,进行促生长能力检测,以保证TSB在使用后仍有合格的促生长能力。
7.19.取样计划
本次验证过程中的取样计划如下:
测试项目
合格标准
取样量
取样时间
无菌
应无菌
5瓶/次X3(前中后)
灌装完成
200ml
经过最终除菌滤器后取样
轧盖完成
培养基促生长能力
应符合2015版《中国药典》四部1011无菌检查法,各试验菌均生长良好。
指导原则进行测试,应符合规定
25瓶
样品培养14天完成后。
7.20.培养基灌装产品的处理
培养基模拟灌装过程中使用的所有的培养基(包括染菌的和未染菌的),经处理后送医疗废弃物处理中心进行销毁。
7.21.培养基模拟灌装清洁确认
设备的清洁结构、取样位置及测试项目描述
为确定培养基模拟灌装完成后、培养基在与其接触的设备部件上可能的残存情况,根据清洁风险分析方法在清洗完成后对相关设备进行清洁确认,需进行清洁确认的设备部件、取样位置及清洁测试项目明细及如下表:
设备名称
设备编号
取样点
取样方法
100L缓冲罐
N/A
罐盖
在清洁验证过程中进行擦拭取样、淋洗水取样
目视检查
擦拭:
活性成分残留
淋洗水:
电导率
罐体内壁
进液口
出液口
+μm除菌过滤器(滤壳)
过滤器内壁
分液器
分液器外表面
分液器内壁
连接硅胶软管
软管内壁
灌装针头
陶瓷泵