SBR工艺及各种改进工艺的特点非常全Word文档下载推荐.docx
《SBR工艺及各种改进工艺的特点非常全Word文档下载推荐.docx》由会员分享,可在线阅读,更多相关《SBR工艺及各种改进工艺的特点非常全Word文档下载推荐.docx(12页珍藏版)》请在冰豆网上搜索。
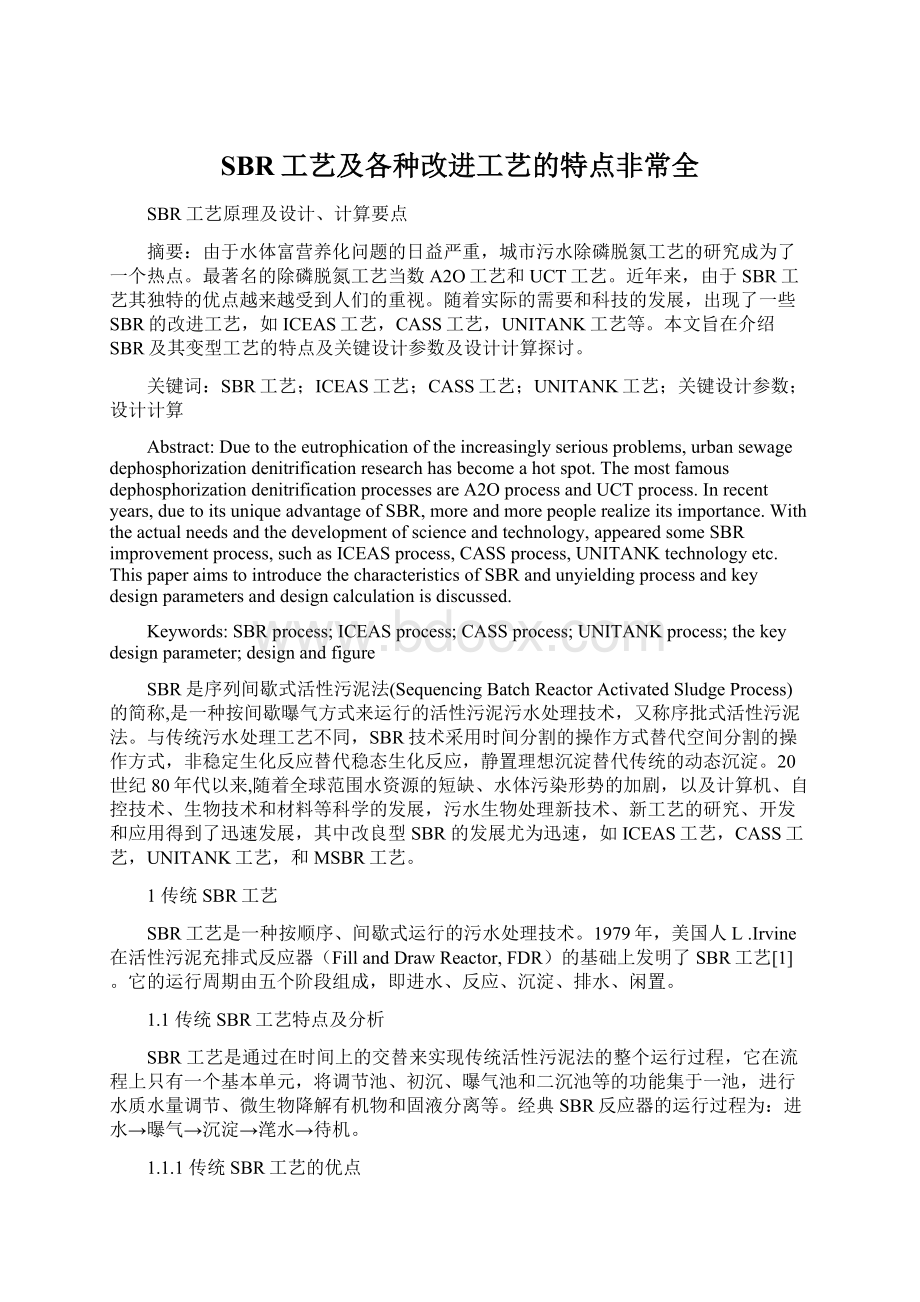
1979年,美国人L.Irvine在活性污泥充排式反应器(FillandDrawReactor,FDR)的基础上发明了SBR工艺[1]。
它的运行周期由五个阶段组成,即进水、反应、沉淀、排水、闲置。
1.1传统SBR工艺特点及分析
SBR工艺是通过在时间上的交替来实现传统活性污泥法的整个运行过程,它在流程上只有一个基本单元,将调节池、初沉、曝气池和二沉池等的功能集于一池,进行水质水量调节、微生物降解有机物和固液分离等。
经典SBR反应器的运行过程为:
进水→曝气→沉淀→滗水→待机。
1.1.1传统SBR工艺的优点
(1)理想的推流过程使生化反应推动力增大,效率提高,池内厌氧、好氧处于交替状态,净化效果好。
(2)运行效果稳定,污水在理想的静止状态下沉淀,需要时间短、效率高,出水水质好。
(3)耐冲击负荷,池内有滞留的处理水,对污水有稀释、缓冲作用,有效抵抗水量和有机污物的冲击。
(4)工艺过程中的各工序可根据水质、水量进行调整,运行灵活。
(5)处理设备少,构造简单,便于操作和维护管理。
(6)反应池内存在DO、BOD5浓度梯度,有效控制活性污泥膨胀。
(7)SBR法系统本身也适合于组合式构造方法,利于废水处理厂的扩建和改造。
(8)脱氮除磷,适当控制运行方式,实现好氧、缺氧、厌氧状态交替,具有良好的脱氮除磷效果。
(9)工艺流程简单、造价低。
主体设备只有一个序批式间歇反应器,无二沉池、污泥回流系统,调节池、初沉池也可省略,布置紧凑、占地面积省。
1.1.2传统SBR工艺的缺点
(1)连续进水时,对于单一SBR反应器需要较大的调节池。
(2)对于多个SBR反应器,其进水和排水的阀门切换频繁。
(3)无法达到大型污水处理项目之连续进水、出水的要求。
(4)设备的闲置率较高。
(5)污水提升水头损失较大。
(6)如果需要后续处理,则需要较大容积的调节池。
1.1.3传统SBR工艺的适用范围[4]
(1)中小城镇生活污水和厂矿企业的工业废水,尤其是间歇排放和流量变化较大的地方。
(2)需要较高出水水质的地方,不但要去除有机物,还要求出水中除磷脱氮,防止河湖富营养化。
(3)水资源紧缺的地方,SBR系统可在生物处理后进行物化处理,不需要增加设施,便于水的回收利用。
(4)用地紧张的地方。
(5)对已建连续流污水处理厂的改造等。
(6)非常适合处理小水量,间歇排放的工业废水与分散点源污染的治理。
1.2传统SBR工艺的设计要点及主要参数
由于SBR工艺是合建式,一个池子既要满足生化反应要求,又要实现沉淀分离功能,因此其计算比一般活性污泥工艺更为复杂。
目前的SBR设计方法主要有污泥负荷法、模型法和泥龄法。
污泥负荷法主要针对有机物的去除,难以适应脱氮的要求。
传统的模型法由于涉及到了大量的化学计量参数,而这些参数的测量复杂、取值随水质多变,应用比较困难。
而污泥龄法则没有对系统中的碳源和需要回流的硝态氮进行核算,往往不能对有限的碳源进行充分利用。
这几种方法各有优劣,在实践中应该根据实际情况采用合适的方法。
随着污水脱氮要求的日益严格,精确的设计计算是非常必要的,我国也在这方面不断的努力、探索。
SBR工艺的设计计算涉及几十个参数,这些参数可以分为三类[2]:
(1)外部条件参数,包括水量、水质等,是设计计算的先决条件;
(2)选定参数,包括运行周期参数等,需由设计人事先选定;
(3)计算参数,需要通过计算才能得出,其中最关键的是反应池总泥量和反应池的总体积。
下面列出了几个重要的设计参数及设计要点。
1.2.1运行周期的确定
SBR的运行周期由充水时间、反应时间、沉淀时间、排水排泥时间和闲置时间来确定。
充水时间应有一个最优值。
如上所述,充水时间应根据具体的水质及运行过程中所采用的曝气方式来确定。
当采用限量曝气方式及进水中污染物的浓度较高时,充水时间应适当取长一些;
当采用非限量曝气方式及进水中污染物的浓度较低时,充水时间可适当取短一些。
充水时间一般取1~4h。
反应时间是确定SBR反应器容积的一个非常主要的工艺设计参数,其数值的确定同样取决于运行过程中污水的性质、反应器中污泥的浓度及曝气方式等因素。
对于生活污水类易处理废水,反应时间可以取短一些,反之对含有难降解物质或有毒物质的废水,反应时间可适当取长一些。
一般在2~8h。
沉淀排水时间一般按2~4h设计。
闲置时间一般按2h设计。
周期数=24/周期时间。
1.2.2反应池容积的确定
假设每个系列的污水量为q,则在每个周期进入各反应池的污水量为q/n·
N。
各反应池的容积为:
1/m*V=q/n*N
V为各反应池的容量;
1/m为排出比;
N为周期数(周期/d);
N为每一系列的反应池数量;
Q为每一系列的污水进水量(设计最大日污水量)(m3/d)。
关于池容的计算,现在有很多的方法,实际操作时要根据实际情况来计算。
以下例举几种现行的方法[5]:
(1)负荷法
该法与连续式曝气池容的设计相仿。
已知SBR反应池的容积负荷或污泥负荷、进水量及进水中BOD5浓度,即可由下式迅速求得SBR池容:
容积负荷法:
V=nQ0C0/Nv
Vmin=[SVI×
MLSS/106]×
V
污泥负荷法:
Vmin=nQ0C0×
SVI/Ns
V=Vmin+Q0
(2)曝气时间内的负荷法
鉴于SBR法属间歇曝气,一个周期内有效曝气时间为ta,则一日内总曝气时间为nta,以此建立如下计算式:
V=nQ0C0tc/Nv×
ta
V=24QC0/nta×
MLSS×
NS
(3)动力学设计法
由于SBR的运行操作方式不同,其有效容积的计算也不尽相同。
根据动力学原理演算,SBR反应池容计算公式可分为下列三种情况:
限制曝气:
V=NQ(C0-Ce)tf/[MLSS×
Ns×
ta]
非限制曝气:
V=nQ(C0-Ce)tf/[MLSS×
Ns(ta+tf)]
半限制曝气:
V=nQ(C0-Ce)tf/[LSS×
Ns(ta+tf-t0)]
反应池的形式为完全混合型,反应池十分紧凑,占地很少。
形状以矩形为准,池宽与池长之比大约为1∶1~1:
2。
反应池的数量,考虑清洗和检修等情况,原则上设2个以上。
在规模较小或投产初期污水量较小时,也可建一个池。
1.2.3曝气系统
序批式活性污泥法中,曝气装置的能力应是在规定的曝气时间内能供给的需氧量,在设计中,高负荷运行时每单位进水BOD为0.5~1.5kgO2/kgBOD5,低负荷运行时为1.5~2.5kgO2/KgBOD5。
在序批式活性污泥法中,由于在同一反应池内进行活性污泥的曝气和沉淀,曝气装置必须是不易堵塞的,同时考虑反应池的搅拌性能。
常用的曝气系统有气液混合喷射式、机械搅拌式、穿孔曝气管、微孔曝气器,一般选射流曝气,因其在不曝气时尚有混合作用,同时避免堵塞。
1.2.4确定设计水量
SBR工艺通常污泥龄比较长,有很强的抗冲击负荷的能力,因此在计算污泥龄的时可按照最高日流量而不是最高日最高时流量计算。
当采用延时曝气时,污泥龄更长,缓冲能力更好,可安平均日流量设计计算。
1.2.5池水深
与分建式活性污泥工艺反应池不同,SBR反应池水深将影响池容的大小,这是因为SBR反应池还要满足二沉池的功能。
按照规定水深一般4~6m,一般可取中间值5m左右。
1.2.6安全高度
安全高度是SBR反应池特有的参数,它相当于分建式活性污泥工艺二沉池的清水层的深度,其作用是将污泥层和出水溢流堰分隔开,以免污泥被带入出水中影响水质。
安全高度多0.1m,意味着安全水深多占0.1m,与总池深相比只占几十分之一,对池容和工程投资影响不大。
1.2.7污泥负荷与需氧量的关系
需氧量=a*Q(Sa-Se)+b*V*Xv
式中a为活性污泥微生物对有机污染物氧化分解过程的需氧率,即活性污泥微生物每代谢1KgBOD所需要的氧量;
b为活性污泥微生物通过内源代谢的自身氧化过程的需氧率,即1Kg活性污泥每天自身氧化所需要的氧量;
Xv为混合液中挥发性悬浮固体量(MLVSS),Kg/m³
;
V为反应器的有效容积,m³
Q为每日处理污水量,m³
/d;
Sa为经预处理后4进入曝气池污水含有的有机污染物的浓度,Kg/m³
Se为经生化处理后4处理水中残留的有机污染物的浓度,Kg/m³
。
1.2.8混合液污泥浓度
反应池内混合液污泥浓度的控制应从供氧的经济性与可能性、活性污泥的絮凝沉淀性能以及剩余污泥处理造价等方面综合考虑。
一般SBR池的活性污泥浓度Nw控制在2.5Kg/m³
~4.0Kg/m³
范围内。
污泥指数SVI值大时Nw值取下限,反之取上限。
1.2.9计算污泥的产率系数
污泥的产率系数通过以下公式计算:
Y为污泥的产率系数,kgSS/kgBOD5;
K为修正系数,K=0.9~0.95;
Sj为进水悬浮物固体浓度,mg/L;
Lj为进水BOD5,mg/L。
2.ICEAS工艺
间歇循环延时曝气活性污泥法工艺,即ICEAS工艺在20世纪80年代中期随着新型SBR活性污泥法的出现,被广泛应用于处理生活污水。
2.1ICEAS工艺原理分析
ICEAS工艺运用连续进水和周期性排水原理,生物氧化作用,硝化和反硝化作用,除磷,固液分离等均在一个反应池中进行。
ICEAS工艺由反应、沉淀和滗水3个阶段组成,其反应器由进水端的预反应区和主反应区组成,运行方式为连续进水(沉淀期和排水期仍保持进水),间歇排水,没有明显的反应阶段和闲置阶段。
但其在工艺改进的同时也丧失了传统SBR工艺的优点,仅仅保留了其结构特征。
与传统SBR工艺相比,ICEAS工艺具有以下特点:
(1)ICEAS的沉淀会受到进水扰动,破坏了其成为理想沉淀的条件。
为了减少进水带来的扰动,一般将池子设计成长方形,使出水近似于平流沉淀池。
(2)由于连续进水,ICEAS丧失了经典SBR的理想推流和对难降解物质去除率高的优点,而且不能控制污泥膨胀的发生,所以需要设置选择区。
(3)连续进水不用进水阀门之间切换,控制简单,从而可应用于较大型的污水厂。
图一ICEAS工艺流程及反应装置图
2.2ICEAS工艺设计要点及主要参数[7]
ICEAS工艺是活性污泥法的一种型式,其基本原理与活性污泥法A/O脱氮工艺等相同,原则上可按传统SBR的公式设计计算。
2.2.1曝气时间与曝气量
(1)预反应区曝气量的确定
ICEAS反应器和传统的SBR反应器相比,最大的特点是进水端增加了一个预反应区,把ICEAS反应器分为两个反应区:
预反应区和主反应区。
主反应区是污水的主要反应区域,预反应区兼具生物选择器的作用,使活性污泥在选择器中处于高负荷的快速基质积累阶段,有利于絮凝性细菌的生长,使ICEAS同样保持SBR不易发生污泥膨胀的优点。
试验发现,生物选择区采用限制性曝气可以取得较好的实验结果,一般控制生物选择区DO<
0.5mg/L。
这样,一方面可使部分难降解的有机物在缺氧状态下转化为易降解的物质,提高污染物的去除率;
另一方面可有效防止污泥膨胀。
据有关资料介绍:
在缺氧条件下(有硝态氮,没有溶解氧),菌胶团细菌可以利用硝酸盐作为最终电子受体,实现有机物的吸收、储存和降解利用,而丝状菌则缺乏这种能力。
从而在选择器中菌胶团细菌占优势,抑制了丝状菌生长。
所以在预反应区曝气采用穿孔管曝气,并限制DO<
预反应区曝气时间和主反应区的曝气时间一致。
(2)主反应区曝气时间与曝气量
要得到最优的曝气时间和曝气量,必须首先研究有机物的去除与曝气过程的关系,即研究有机物的降解规律。
试验需采用连续进水,滗水结束后再开始曝气的方式。
随着曝气时间的延长,DO在45min内迅速增长为有机物的氧化降解提供了足够的溶解氧,有机物也在此期间内大量降解,此后的降解速度降低。
由于在曝气充氧阶段,不仅有机物要降解,消化细菌还要把有机氮转化为氨氮,继而转化为亚硝酸氮和硝酸盐氮,除磷菌也要大量的“吸磷”,所以要继续曝气。
根据研究资料显示,在曝气60min后,由COD、DO变化规律可得出,COD的降解幅度已很小,曲线趋于平稳。
单纯从降解有机物的角度看,曝气时间可以缩短,但由于脱氮除磷的需要,要相应的延长曝气时间。
氨氮的降解不同于有机物,它的降解速度低于有机物,所需反应时间要长,氨氮需要在曝气120~150min左右出水才能达到排放标准(8mg/L以下)。
从以上两个方面考虑,为使硝化反应进行得更彻底,以氨氮出水指标低于8mg/L为基准,最优曝气时间不低于150min。
最优曝气量的确定要根据去除有机物、氨氮的指标来控制。
曝气量的控制是以DO浓度来体现的。
对于一般的生活污水而言,去除有机物的DO浓度,在2h曝气时间里,DO浓度达到并保持在2mg/L左右,有机物的去除就可以达到要求。
去除氨氮的DO浓度,曝气45min时达到2.0mg/l以上,60min达到3.0mg/L左右,并一直保持到曝气结束,氨氮的去除效果好,出水浓度低于8.0mg/L。
为了保证氨氮的出水效果,反应装置中DO浓度应在曝气60min时达到3mg/L左右,并一直保持到曝气结束。
2.2.2沉淀时间和排水时间
对于ICEAS处理系统来说,由于是在装置中进行,沉淀时间的确定显得更为重要。
沉淀时间过短,水中悬浮物过高,影响出水水质;
另外,系统要具有脱氮除磷功能,就必须保证系统中厌氧和好氧的交替进行,因为ICEAS在前期只有曝气阶段,没有提供单独的厌氧阶段,所以在沉淀时间的确定上,要相应的延长沉淀时间,使反应器中的污泥层能够出现缺氧和厌氧的时段,为反硝化和除磷菌的释磷提供条件,实验表明,沉淀15min之后,污泥进入厌氧阶段。
若沉淀时间太长,释磷菌释放的磷将穿过污泥层,重新回到污水中,降低除磷效果。
实验结果还表明经过20min的沉淀,就基本完成了沉淀过程;
沉淀30min后,水中的SS浓度基本不再进一步降低了,泥水界面变化也很小。
在不同的工况运行时,即使曝气时间不一样,重复上述试验,都得到了基本相同的结果。
所以在沉淀30min后,开始排泥,这主要是为了排除含磷高的污泥,达到除磷的目的。
排泥在30min内结束。
鉴于以上考虑,最优沉淀时间定为1h。
此时,泥水已经完全分离,并且污泥层已经进入厌氧阶段,实现了好氧和厌氧的交替。
由于ICEAS反应器为连续进水,因此在排水时为了保证水质,不能瞬时排水,而是用滗水器将沉淀后的上清液一层层较均匀地从ICEAS反应器内滗走,确保出水水质。
排水时间为1h。
作为一种改良型的SBR,ICEAS工艺由于其连续进水,运行操作的复杂性低的特点,故适用于较大规模的污水处理。
3.CASS工艺
3.1CASS工艺特点及原理分析
CASS工艺是在ICEAS工艺的基础上开发出来的。
CASS池分为三个反应区:
生物选择器、缺氧区、好氧区。
生物选择器是设置在CASS前端的小容积区,通常在厌氧或兼氧条件下运行,其基本功能是防止产生污泥膨胀,同时还具有促进磷的进一步释放和强化反硝化的作用,另外,难降解的大分子物质在这个区内易发生水解作用,这对提高有机物的去除率具有一定的促进作用。
主反应区是去除有机底物的主场所,运行过程中常通过控制主反应区的曝气强度使反应区内主体溶液处于好氧状态,完成降解有机物的全过程。
CASS工艺有很多优点:
(1)CASS工艺与ICEAS工艺相类似,它通过设置选择器、预反应区和污泥回流等措施控制了污泥膨胀、增大了有机物的去除率并起到了脱氮除磷的作用,同时通过多个反应器的组合创造了静止沉淀的条件。
CASS工艺在沉淀阶段不进水以保证污泥沉降无水力干扰,可以保证系统有良好的分离作用。
(2)无污泥回流设备和沉淀池内的刮泥设备,节省了投资与电耗。
(3)CASS工艺流程简单,可大大减少设备管理和维修的工作量。
3.2CASS工艺设计要点及主要参数
CASS设计中应注意的问题:
(1)水量平衡
工业废水和生活污水的排放通常是不均匀的,如何充分发挥CASS反应池的作用,与选择的设计流量关系很大。
如果设计流量不合适,进水高峰时水位会超过上限,而进水量小时反应池容积又不能充分利用。
当水量波动较大时,应考虑设置调节池。
(2)控制方式的选择
一般情况下,CASS工艺采用自动控制和手动操作两种方式。
后者便于手动调试和自控系统故障时使用,前者为日常运行使用。
(3)曝气方式的选择
间断曝气容易造成污泥堵塞微孔,因此在选择曝气头时要尽量选择不堵塞的曝气形式,这一点与SBR工艺相同。
(4)排水方式的选择
CASS工艺的排水要求与SBR相同。
目前,常用的设备为旋转式撇水机,其优点是排水均匀、排水量可调节、对底部污泥干扰小、能防止水面漂浮物随水排出。
(5)需要注意的其他问题
漂渣和沉渣的排除方法;
排水比的确定;
雨季对反应池内水位的影响及控制;
排泥时机及泥龄控制;
反应池的长宽比;
间断排水与后续处理构筑物的高程及水量匹配问题。
CASS工艺是活性污泥法的一种型式,其基本原理与活性污泥法A/O脱氮工艺等相同,原则上可按传统SBR的公式设计计算。
3.2.1CASS池容积
与传统SBR反应池容积算法相似。
不过CASS池中间设一道隔墙将池体分割为预反应区和主反应区两部分,靠进水端、容积为CASS池总容积的10%左右的预反应区为吸附兼氧区,另一部分为主反应区,预反应区长度按照0.16~0.25m来设计。
3.2.2污泥龄[6]
硝化所需好氧污泥龄:
θSN=(1/μ)*1.103(15-T)*fs
式中θSN为为硝化所需最低好氧污泥龄,当T=13℃时,θSN=8d,μ为硝化菌的比增长速率。
T=15℃时,μ=0.47d,fs为安全系数,一般取2.5~3.0;
T为污水温度,℃。
3.2.3剩余污泥量
系统剩余污泥量:
Sp=Q*BOD5*[YH-(0.9*bH*YH*fT.H)/(1/θSR+bH*fTH)]+Yss*Q*(SSi-SSe)
式中SSi、SSe分别为反应池进、出水的悬浮固体浓度,mg/L。
YH为异养微生物的增殖率,取0.5~0.6Yss为不能水解的悬浮固体率,Yss=0.5~0.6。
fT.H为温度修正系数bH为异养微生物的内源呼吸速率,(自身氧化率),bH=0.08d-1。
通过对CASS工艺较为全面的实验探讨及对SBR和CASS工艺实验结果进行分析比较后,在处理城市污水时推荐使用的工程设计参数见下表:
CASS工艺适用于有脱氮除磷要求的城市污水及某些工业废水的处理,有其自身独特的优势。
在废水水质日益复杂的今天CASS作为一种具有竞争力的工艺有着广阔的发展前景。
目前该工艺在我国应用的技术关键主要是提高自动控制装置的可靠性及运行和操作管理人员的素质。
随着国内环保产业的迅速发展以及科学研究的不断深入,CASS工艺将在理论和生产应用中实现较大的突破。
4UNITANK工艺
UNITANK工艺是1987年INTERBREW与KULeuven基于三沟式氧化沟结构提出的一种活性污泥法污水处理新技术。
4.1UNITANK工艺特点及原理分析
UNITANK的通用形式是采用三个池子的标准系统[8],这三个池子通过共壁上的开孔实现水力连接,无需用泵输送。
每个池中都装有曝气系统(可以是表曝也可以是鼓风曝气),同时边缘的两个池子都装有溢流堰用于排水,既可以用作反应区也可以用作沉淀池。
每个池子都可以进水,剩余污泥从边缘两个作沉淀池的池子排出。
与传统活性污泥法一样,UNITANK系统是连续运行的,但是其单个池子是按一定周期运行的。
UNITANK系统可在恒定水位下连续运行,此时从整个系统来看它已经不属于SBR,而与交替运转的三沟式氧化沟非常相似,更接近于传统的活性污泥法,这是该工艺最为显著的一个特点;
UNITANK系统也可在恒水位下交替运行,出水采用固定堰而不是滗水器,在任一时刻总有一个池子作为沉淀池,这个沉淀池相当于平流式沉淀池,所以在设计上需要满足平流沉淀池的功能,这是UNITANK的第二个特点;
标准的UNITANK系统是由三个正方形池所组成,弥补了单个反应器完全混合的不足,这是其第三个特点。
但是相对于传统活性污泥法,UNITANK工艺仍是一种尚处于发展和完善阶段的技术,缺乏科学的设计依据和方法以及成熟的运行管理经验,UNITANK在现阶段的发展过程中,主要存在以下方面的问题[9]:
(1)无专门的厌氧区,磷去除效果不理想;