石油相关产品Word文件下载.docx
《石油相关产品Word文件下载.docx》由会员分享,可在线阅读,更多相关《石油相关产品Word文件下载.docx(34页珍藏版)》请在冰豆网上搜索。
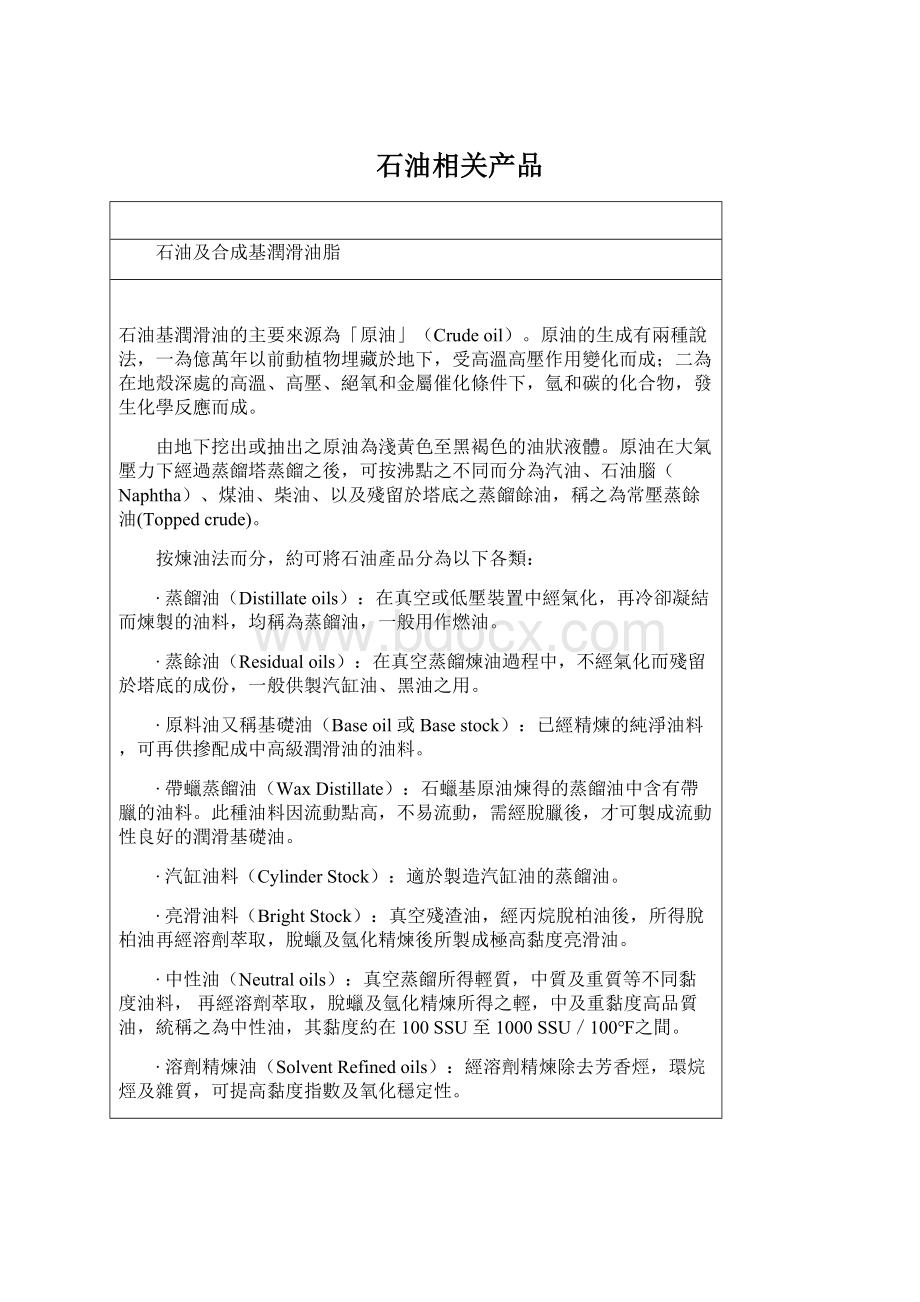
經過濾後所得顏色較淺的油。
∙深色油(Darkoils):
呈黑色的蒸餾油。
∙純礦油(Straightmineraloil):
不含任何添加劑的機油。
其中常壓蒸餘油經過真空蒸餾、脫瀝青、溶劑萃取精煉、脫蠟、及加氫精煉後,即成各種不同品質及黏度的基礎油(Baseoil)。
再以基礎油為原料,加入添加劑並摻配一定的黏度,即成為潤滑油。
(二)原油的種類
由於原油產地的不同,在外觀和性質有很大的不同,但其組成元素幾乎都是一樣的。
其中有83-87%的碳成分、11-14%的氫成分、其餘的則包含有氧、氮、硫及一些金屬,如鎳、釩等。
就潤滑用油立場而言,原油可按其化學組成分為下列數種:
∙石蠟基原油(Paraffinicbasecrude),以石蠟基之碳氫化合物為主、含蠟多、流動點高,經精煉後可製成高品質潤滑油。
∙環烷基或柏油基原油(NaphthenicorAsphalticbasecrude),以環烷基之碳氫化合物為主、含蠟少、流動點低,經精煉後可製成冷凍機油,環烷基型橡膠軟化油及變壓器油,此種原油來源漸少。
∙混合基原油(Mixedbasecrude),含有以上1、2兩項之成份,既含蠟、亦含瀝青,來源最多,精煉後可得高黏度指數之高品質潤滑油。
∙芳香基原油(Aromaticbasecrude),含芳香基較明顯。
具高度未飽和環狀碳氫化合物,反應性強,有高溶解度,高溫易氧化,黏度指數低。
(三)原油煉製成基礎油的程序
基礎油的製程有兩種方式,一種是分離(separation),另一種是轉化(conversion)。
利用分離的方式製造的基礎油稱之為傳統基礎油,而以轉化的方式所製得的油則稱為非傳統油。
真空蒸餾所得的真空蒸餾油(Vacuumdistillates),經過這兩種方式的製程與精煉後,製造出石油基潤滑油的基礎油。
基礎油的製造過程包含有五個步驟:
1)蒸餾
2)脫瀝青
3)溶劑萃取或氫化精煉以改善黏度指數與品質
4)溶劑或觸媒作用脫蠟以改善低溫特性
5)黏土或加氫精製加工以改善色澤,,穩定性等
所謂傳統的分離煉製就是以溶劑萃取、溶劑脫蠟、最終再以加氫精製加工,目前約有三分之二的石蠟基礎油是以這種方式生產。
較新的非傳統轉化煉製是以氫氣在溫度、壓力、與觸媒的作用下,產生化學反應去除不需要的物質;
非傳統的全氫處理過程(All-hydrogenprocessing)包括氫裂解、觸媒作用脫蠟、與加氫精製。
圖表1顯示傳統與非傳統基礎油煉製的兩種過程示意圖。
圖表1
基礎油煉製過程示意圖,
分離製程(上)與轉換過程(下)
1.
真空蒸餾
(VacuumDistillation)
原油先在常壓蒸餾下將較輕的油料取出,塔底殘餘油在溫度約達700°
F(371°
C)時將可能產生熱裂解,所以在常壓蒸餾後,將塔底殘餘油引進真空蒸餾塔內。
這些較重的殘油進料,在低壓(10mm汞柱)或真空下,沸點降低所以蒸餾不會引起熱裂解的發生。
真空蒸餾主要控制的性質有油的黏度、閃火點、及殘碳量。
通常四至五種真空餾份,按其沸點之高低分為重柴油餾份(Heavydieselfraction)、輕質餾份(Lightfraction),中質餾份(Mediumfraction),及重質餾份(Heavyfraction)等四種餾份及殘留於塔底的真空蒸餘油(Vacuumtar)或稱為真空殘渣油(Vacuumresidue)即可滿足潤滑油製造的需求。
供真空蒸餾或供製造潤滑油的原料,均為常壓蒸餾所得的蒸餘油,特稱為「潤滑油進料油」簡稱為「進料油」(LubeoilfeedstockorFeedstock)。
如以環烷基原油(或稱柏油基原油)為原料,真空蒸餾的各餾份中不含蠟份,或所含蠟份甚少,經精煉後即可得低流動點及較低黏度指數油料,可供冷凍機械潤滑之用。
如以石蠟基或混合基原油為原料時,各真空蒸餾餾份均含有蠟份,流動點高,且黏度指數亦高,須再經溶劑萃取及脫蠟除去蠟份後,才可得低流動點及較高黏度指數油料。
此種石蠟基原油精煉所得基礎油可攙配成高品質潤滑油,供車輛及工業機械潤滑之用。
因此由真空蒸餾所得的蒸餾油及真空殘渣油都可作為煉製潤滑基礎油的進料油,其中真空殘渣油需進一步丙烷脫瀝青得到脫瀝青油,然後將所得蒸餾油及脫瀝青油再度精煉,便可製成不同黏度之輕、中、重質的中性油及高黏度亮滑油。
其品質及產率深受原油特性及煉製條件影響。
同時大部份潤滑基礎油均從石臘基原油煉製而成。
在傳統溶劑煉製的製程下,基礎油的黏度是由蒸餾出的餾份的黏度所決定;
但在氫裂解的製程下,最終的基礎油黏度是與真空餾份的黏度是無關的,因為氫裂解的過程下,新的分子已產生。
2.
脫瀝青
(De-asphalting)
真空蒸餾的塔底殘留油,仍保有潤滑基礎油可用黏度非常高的碳氫化合物,但蒸餾已無法將殘留在內的瀝青分離,所以採用了溶劑萃取的方式脫去瀝青。
常用之溶劑有丙烷、戊烷及丁烷。
其中以「丙烷脫瀝青法」(Propanedeasphalting)最為有效。
脫除瀝青後之真空殘渣油,稱為「脫瀝青油」(Deasphaltoil,簡稱DAO)去除瀝青後的殘餘油主要是包含有飽和烴和芳香烴,再經溶劑萃取芳香烴後,作為高黏度的基礎油使用,通常稱為亮滑油(brightstocks),其黏度在100°
C可超過
45cst。
另一種脫瀝青與萃取芳香烴一併進行的過程稱為是雙溶劑(Duo-Sol)精練過程。
這個過程一方面脫除瀝青,一方面萃取芳香烴後成為潤滑基礎油的進料。
丙烷用於脫除瀝青,酚或甲酚(cresylcacid)則用於萃取進料。
3.
基礎油的精煉過程
(LubeRefiningProces)
以酸、溶劑與氫化精煉是幾種用於煉製基礎油所使用的過程,用以去除芳香烴與其他不需要的成分,來改善黏度指數和基礎油的品質。
A.
酸精煉
(AcidRefining)
用酸來精煉真空蒸餾油已經不常用了,因為酸殘留物很難處理,所以現在大都已被溶劑萃取的方式所取代。
有一些顏色非常輕的白油煉製或使用過的舊潤滑油的再製回收仍然使用酸精煉的方式。
經與硫酸處理後,芳香烴的含量減少,使得黏度指數提高。
酸精煉需複雜的中和與後續的吸附處理,以消除酸殘餘物質。
B.
溶劑萃取
(SolventExtraction)
真空蒸餾油及脫瀝青油,因油中仍含有多量對潤滑有害之不安定之成份,不僅使油料黏度指數偏低,而且氧化穩定性低。
如高分子成份、芳香族成份、聚環烷基成份(Polynaphthenes)、聚環基成份(Polycylics),或其他雜環等有害之成份,均須充份去除。
以提高油料黏度指數及安定性。
此一過程稱為「精煉」(Refining)。
普遍使用「溶劑精煉方法」(SolventRefiningProcess)精煉潤滑油。
以本法煉製時,必須選用一種對潤滑油中所含不安定之成份,如上述芳香族成份等,具有特別之溶解性,而對高品質或高黏度指數之石蠟基潤滑油具有極微之溶解者。
如此經溶劑處理之後,油中所含之芳香基等不良成份大都為溶劑所萃取而除去,品質因而大為提高。
相較於酸精煉以化學反應的方式將芳香烴含量減低,溶劑萃取是以物理反應分離方式將芳香烴萃取出來,取出芳香烴的基礎油通常稱為中性油(solventneutrals–SN)。
另一部份是溶劑與芳香烴的溶合物,將溶劑蒸發後則得到大部分的芳香烴油。
其實溶劑溶合物中,視原油的不同,除芳香烴外,也可能有高達30%-50%的石蠟基油在內。
目前常用之溶劑,有下列各種:
●
糠醛(Furfural)--有效溶化油中所含對潤滑有礙之各種雜質,而且其比重小,表面張力高,容易與萃取之油料分離,以利回收。
酚(Phenol)--效果亦佳,但須加入少許水份,以增加溶劑之選擇溶解力。
唯有腐蝕性,操作應小心並做好設備防蝕。
丙烷與甲酚(PropaneandCresylicAcid)混合溶劑--多用於黏度極高之油料,如汽缸油等。
以本法為溶劑者,又稱為「雙溶劑精煉法」(Duo-SolRefiningProcess)。
二氧化硫及苯--在高壓下,以液體二氧化硫和苯作溶劑,其精煉效力亦高,但須高壓而且二氧化硫具腐蝕性,為其缺點。
以本溶劑精煉者,又稱為Edeleann法。
●∙N-Methyl-Pyrollidone(NMP):
此種溶劑具有高度溶解力,穩定性高,操作費用低且毒性低及所產生萃餘油顏色低等優點,是最近發展出來萃取溶劑。
常用為萃取之溶劑以糠醛、酚及N-Methyl-Pyrollidone(NMP)使用最為普遍,但因酚具有腐蝕性,使用漸少。
過去也以二氧化硫來使用,現今已非常少用,僅少部分的環烷基油的精煉使用它。
最近一些使用糠醛或酚的煉油廠已改用NMP,因為NMP是無毒、且具高溶解度、使用量低、省能源;
如設立新廠其硬體投資較省、操作費用低。
如果真空蒸餾油的芳香烴或環烷基烴含量越高,則溶劑萃取的執行度越高,因而溶劑溶合物的量也越多,相對的基礎油的產量將越少。
萃取物的量的多寡將影響傳統溶劑精煉的成本。
溶劑萃取後的基礎油可提高VI值,熱與氧化穩定性也可以提高,一般標準溶劑萃取精煉要求基礎油的VI值需達到95,所以溶劑萃取的執行度將配合這樣的要求。
基本法則是VI值欲提高一個點數,溶劑溶合物的量要多增1%。
有些煉油廠僅精煉達VI值70或
80再以VI改善劑提昇VI,因此可減低15%-20%的萃取成本,但缺點是其氧化穩定性較低,也可能含較高的硫含量或芳香烴量;
以溶劑萃取法的經濟考量,真空蒸餾油的最低限定值須VI值50。
必須注意的是往後的溶劑脫蠟需再取走約20%的基礎油的量,這也是為什麼在傳統溶劑萃取的製程下平均需10桶原油的量,才製成1桶潤滑基礎油的原因。
C.
加氫反應與氫裂解精煉過程
(HydrogenationandHydrocrackingProcess)
傳統的溶劑精煉法是以物理反應的分離方式去除真空蒸餾油內不需要的物質,而加氫反應與氫裂解法是以氫氣改變礦物油的分子結構的。
不穩定的極性分子包含硫、氧、氮等與氫結合後被移除而變得穩定,氫裂解是加氫反應過程中最嚴苛的執行方式。
嚴苛的加氫反應在高溫、高壓與觸媒的作用下使芳香烴轉化成飽和的環烷基烴與石蠟基烴。
在約400°
C與3000psi氫氣下,碳與碳的鍵裂開而將較大的分子分裂成較小的分子。
除了芳香烴將飽和外,環烷基的環也會打開。
氫裂解通常以製成
95-105VI的基礎油為目標,更嚴苛的執行度可使VI增加至115以上,但產量會顯著減少。
如以高蠟含量的石蠟基油為原料,
可達更高的VI值(>
130)。
利用這些過程,潤滑基礎油的特性比起溶劑分離精煉法更容易設計與訂製。
由於氫裂解過程大都將較大,較重的分子分解成較小、較輕的分子,所以氫裂解油的黏度都較低(80-500SUS,ISOVG22-100),也因此氫裂解油不單獨適用於很多重工業與引擎機油使用,除非它與溶劑煉製油或與增稠添加劑混合以增加它的黏度使用。
氫裂解的另一項優點是對於原油品質良窳的依賴度將降低。
溶劑精煉的經濟效益取決於最終基礎油的生產量,而氫裂解卻可彌補原油的品質而有較高的產量,因此氫裂解製程特色有:
1.它可取代傳統製程之溶劑萃取;
2.它可使用低品質原油作進料;
3.除去大部份含硫及含氮及含氧成份;
4.可生產低芳香烴,顏色淺,高黏度指數之較高品質基礎油;
5.操作費用低及產率高。
可以預見的是,將來的潤滑基礎油的煉製將會朝向加氫反應與氫裂解法來生產而逐漸取代傳統溶劑精煉的方式。
氫裂解法與傳統的溶劑精煉比較有下列的優點:
1/
有較高的潤滑基礎油的產量:
轉化欲移除的物質成潤滑油。
2/
生產進料較有彈性:
允許較劣質與便宜的原油來生產基礎油。
3/
有較高品質的基礎油:
可生產品質要求較高的的基礎油,如GroupII,III油。
4.
基礎油的脫蠟過程(LubeDewaxingProcess)
真空塔底的脫瀝青油與真空蒸餾油經過精煉後,蠟含量仍然存在油中,這些蠟必須加以去除,使基礎油得到必要的低溫性質。
溶劑脫蠟、觸媒作用的脫蠟是目前使用的方式。
溶劑脫蠟(SolventDewaxing)
長鍵,高熔點的蠟將影響潤滑油的低溫流動性並提高流動點,因為在低溫下蠟開始結晶,使油變得渾濁且黏度增高。
油中所含之蠟份,有結晶形蠟(Crystallinewax)與非晶型之微晶蠟(Microcrystallinewax)兩種。
前者通稱為「石蠟」(Paraffinwax),多存在於真空蒸餾油等餾份中;
後者則多留於真空殘渣油中,且視製品之軟硬,分別稱為凡士林(Vaseline或Petrolatum)或Cersin,或微晶蠟等。
溶劑脫蠟過程包含三個步驟:
晶化、過濾與溶劑回收,是較複雜且操作費用較高過程的。
將石蠟油先與溶劑混合,稀釋後再降溫以使蠟結晶,然後將蠟過濾分離是傳統的脫蠟法。
常用的溶劑是MEK(methylethylketone)或丙烷(Propane),可將流動點降低至
–12°
C,如欲更低則可採用一些歐洲廠採用的Di-Me
(dichloroethane-dichloromethanemixtures)
溶劑脫蠟。
觸媒脫蠟或氫化脫蠟過程(CatalyticDewaxingorHydrodewaxing)
傳統的基礎油的煉製過程中最複雜的莫過於溶劑脫蠟。
除了操作成本高外,對於流動點降低的侷限也是它的缺點。
現今已發展出將無支鍵的長鍵、短鍵,或支鍵少的石蠟基烴,在加氫反應(氫裂解)與觸媒作用下,使蠟的長鍵斷裂成較輕的物質,或形成支鏈異構化(isomerization)的無蠟、異構石蠟基的潤滑油分子,以此改善潤滑油的低溫特性。
它較具成本效益,是溶劑脫蠟的有效取代方式。
在1979年美孚公司首先提出美孚潤滑油脫蠟過程(MobilLubeDeWaxingProcess–MLDW),不同於溶劑脫蠟以物理分離蠟晶子,MLDW主要是將蠟在觸媒作用與加氫反應下,將蠟分裂成較小的石蠟基油與量大較輕的燃油副產品。
MLDW的產能由於產生較多的輕質副產品,所以基礎油的產能較差。
此後因觸媒的發展,使得更嚴厲的氫異構化過程能夠完成(MobilSelectiveDeWaxing–MSDW),故能得到高產能的無蠟的異構石蠟基油。
異構化除蠟過程(isodewaxing)可以使流動點降至
–45°
C,但需注意的是,如果此過程將流動點降得太低(視操作條件與觸媒),也會損失VI值的。
現今的觸媒脫蠟技術已可生產具低流動點與高VI油,並有高產能的目標。
5.
加氫精製加工過程(LubeoilFinishingProcess)
今日,加氫精製加工過程(Hydrofinishorhydrorefining)是溶劑萃取與脫蠟過程後最後一道加工製程。
過去使用費用較高的酸處理,與以活性白土或酸性白土(ActiveorAcidClay)吸除油中所含極微量之雜質,使油脫色。
此即稱為「白土過濾」(ClayFiltering)。
唯因處理後廢白土處理不易,所以白土處理法現在很少使用,而以加氫處理來取代。
加氫精製加工是一種比較輕微的加氫反應(hydrogenation),處理用以改善潤滑油的色澤、氣味,並移除表面活性物質,以加強消泡及解乳化能力。
這個過程並不會如其他較嚴苛的加氫反應會使芳香烴飽和,或使碳與碳的鍵斷裂,通常也不具有除硫份的能力;
但如超過100bar的壓力下所進行的較嚴厲的氫化處理,則具相當的除硫份與解芳香烴化能力。
在製造冷凍機油、變壓器油、渦輪油、白油時,有時也額外的以漂白黏土作黏吸處理,進一步濾過與去色。
6.
混合式潤滑油煉製過程(HybridLubeOilProcessing)
將傳統的溶劑精煉、與嚴苛的氫化處理、及氫裂解合併一起的過程,稱之為混合式煉製過程。
欲製造較高VI(>
105)與較低硫份的油在溶劑精練後,則以中度嚴苛的加氫處理,取代傳統的溶劑脫蠟(如渦輪油的製造);
如仍使用傳統的溶劑煉製過程,產量損失大,且硫份也無法完全去除(僅達約80%)。
混合式煉製可以保持較高的產能,真空蒸餾油先經過溶劑精煉後,再加以氫處理。
另一種混合式煉製的應用是將糠醛先低度萃取後,在較小型的反應爐,生產較低度氫裂解加工的裂化油;
較少量的氫氣消耗搭配現有的溶劑煉製設備,可提供品質尚優,生產經濟效益較佳的油。
7.
蠟異構化過程(axIsomerization)
七十年代初VHVI油已可經由蠟煉製,而蠟是由溶劑脫蠟而得。
長鍵的正石蠟基或支鍵少的石蠟基,在觸媒作用下氫裂解過程與異構化轉化成異構體後,可製得具良好的低溫特性與高VI油。
將蠟異構化是製造超高VI(>
140)基礎油的過程,這個過程的次序是先經過氫裂解後,再續以氫異構反應。
由於進料的蠟已是無芳香基與無環烷基的原料,所以觸媒作用可以極佳化的轉化這些石蠟物質,過程中產能損失較大,但可以生產出高品質價格較高的裂解油(ShellXHVI,MobilMWI,ExxonExxyn)。
圖表2
顯示經由氫裂解與蠟異構化,包括溶劑脫蠟的過程製造XHVI油。
製造極高VI基礎油過程示意圖
8.
氫開始(Hystart)
較劣質的真空餾份在尚未溶劑萃取前可先以氫化處理以提昇它的品質,這個過程稱之為氫開始(Hy-startingorHystart)。
9.
全氫過程或路徑(
All-HydrogenProcessorRoute)
基礎油的生產過程中以氫裂解,觸媒反應無溶劑脫蠟,加氫精製加工的過程稱之為全氫過程或路徑,視氫裂解的執行嚴峻度可製得HVI油與VHVI油。
10.
不同氫化處理基礎油與溶劑精煉油之比較
基礎油類型
(Basestocktype)
加氫精製(Hydrofinished)
加氫處理(HydrotreatedVHQ)
加氫裂解(HydrocrackedHDC,VHVIorXHQ)
溶劑精煉
(Solvent-refined)
氫化執行度
低
中度
高
-
氫化處理目的
飽和烯烴與芳香烴,移除硫與氮
飽和烯烴與芳香烴,移除硫與氮,打開環狀結構
進料
經溶劑精煉
真空蒸餾:
HDC與VHVI;
真空蒸餾,粗蠟:
XHQ
性質檢驗
與進料微小改變
較低芳香烴,硫與氮
極低芳香烴,硫與氮
黏度指數(VI)
90-105
105+
95–105(HDC)
115–130(VHVI)
130+(XHQ)
ISO黏度範圍
22-460
22–100
22–100(HDC/VHVI)
22–46(XHQ)
改善性能元素
改善色澤,解乳化性、消泡性
改善氧化穩定性
氧化穩定性大幅提昇
溶解性
極優
良好
(四)潤滑基礎油
原油經常壓、真空減壓蒸餾所得潤滑油餾份,經溶劑精製,溶劑脫臘及白土或加氫精製而成潤滑基礎油。
潤滑基礎油之成份,以碳與氫之化合物(HydrocarbonCompounds)之混合物為主,約佔99%以上,其餘為硫、氮、氧等之化合物。
黏度低者,其分子量約在250以上,高黏度者,其分子量超過1,000。
由於原油中碳與氫化合物分子結構形成之不同,而分有:
石蠟基油(Paraffinicbaseoils或Paraffinicoils)
環烷基油(Naphthenicbaseoils或Naphthenicoils)
芳香基油(Aromaticbaseoils或Aromaticoils)
混合基油(Mixedbaseoils)
如與環烷基及芳香基油比較,石蠟基油之比重較小,流動點與閃火點均較高,且有最佳之抗氧化特性,經久耐用;
其黏度受溫度之改變亦較小,即黏度指數較高,故作潤滑基礎油用者,以石蠟基油為最佳。
如以SAE30號之石蠟基與環烷基油為例,可比較如圖表3。
早期以美國賓州(Pennsylvania)所產之原油屬石蠟基油,經過簡單提煉,即可製成品質良好之潤滑油。
過去都認為賓州原油煉製之潤滑油為最佳。
如今,由於煉油技術之不斷進步,且新油源相繼開發,可由任何一種原油煉成高黏度指數之石蠟基潤滑油,且其品質更駕賓州潤滑油之上。
圖表3.石蠟基與環烷基油之比較
SAE30
性狀
石蠟基
環烷基油
黏度
SSU/210℉
61
SSU/100℉
460
650
cSt/210℉
10.5
cSt/100℉
99.3
140
比重,Sp.Gr.60/60℉
0.886
0.905
閃火點,℉
490
430
流動點,℉
+5
-30
黏度指數
96
20
抗氧化性
1,500
1,000
揮發性
較小
較大
環烷基油之特點為流動點特低,主供冷凍機等需要低流動點機件之潤滑。
在國際上基礎油買賣,除指明為何種基礎成分(如石臘基或環烷基)外,主要是以粘度作為分類,其分類編號表列如圖表4。
在台灣煉製潤滑基礎油的公司只有中殼潤滑油股份有限公司一家,這家公司是由中國石油與殼牌公司合資的公司,煉廠在高雄市郊,生產的基礎油除供台灣地區自用外,也有部分外銷各地,產品的編號及規格簡述如圖表6。
中國大陸