精编完整版年产780万件汤盘的天然气隧道窑窑炉毕业论文说明书Word格式文档下载.docx
《精编完整版年产780万件汤盘的天然气隧道窑窑炉毕业论文说明书Word格式文档下载.docx》由会员分享,可在线阅读,更多相关《精编完整版年产780万件汤盘的天然气隧道窑窑炉毕业论文说明书Word格式文档下载.docx(25页珍藏版)》请在冰豆网上搜索。
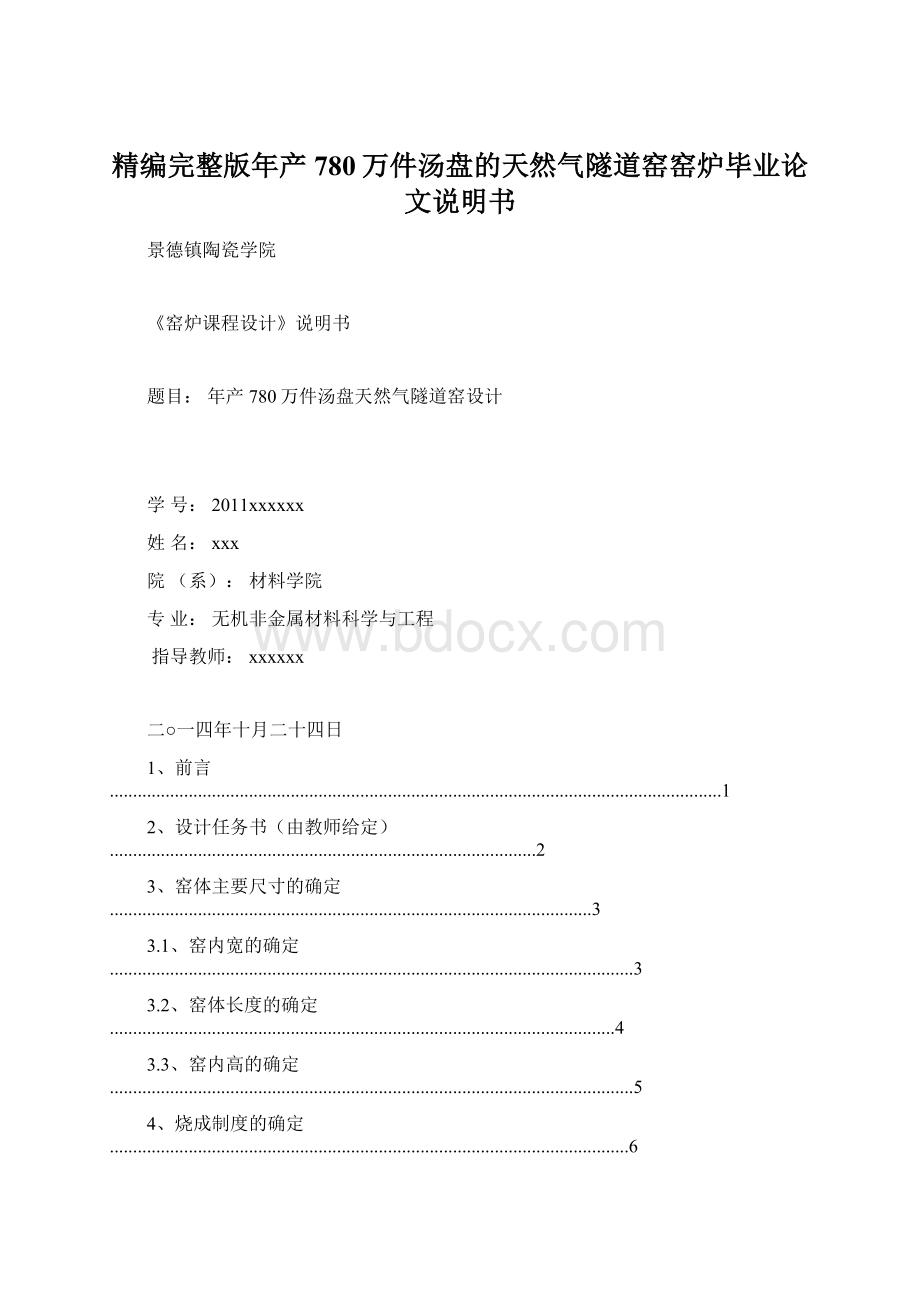
5.5、窑体附属结构................................................................................................................8
5.5.1、事故处理孔................................................................................................................8
5.5.2、测温测压孔及观察孔................................................................................................9
5.5.3、膨胀缝........................................................................................................................9
5.5.4、挡墙............................................................................................................................9
5.6、窑体加固钢架结构形式...............................................................................................9
6、燃料燃烧计算................................................................................................................10
6.1、空气量.........................................................................................................................10
6.2、烟气量.........................................................................................................................10
6.3、燃烧温度.....................................................................................................................10
7、窑体材料及厚度的确定................................................................................................12
8、热平衡计算....................................................................................................................14
8.1、预热带及烧成带热平衡计算.....................................................................................14
8.1.1、热平衡计算基准及范围..........................................................................................14
8.1.2、热平衡框图..............................................................................................................14
8.1.3、热收入项目..............................................................................................................15
8.1.4、热支出项目..............................................................................................................16
8.1.5、列出热平衡方程式...................................................................................................21
8.1.6、列出预热带烧成带热平衡表...................................................................................22
8.2、冷却带热平衡..............................................................................................................23
8.2.1热平衡计算基准及范围..............................................................................................23
8.2.2热平衡框图..................................................................................................................23
8.2.3热收入项目.................................................................................................................23
8.2.4热支出项目................................................................................................................24
8.2.5列出热平衡方程式....................................................................................................26
8.2.6列出预热带烧成带热平衡表....................................................................................27
9、烧嘴的选用...................................................................................................................28
9.1、每个烧嘴所需的燃烧能力........................................................................................28
9.2、每个烧嘴所需的油(气)压....................................................................................28
9.3、烧嘴的选用................................................................................................................28
10、参考文献.....................................................................................................................29
1前言
陶瓷工业窑炉是陶瓷工业生产中最重要的工艺设备之一,对陶瓷产品的产量、质量以及成本起着关键性的作用。
它把原料的化学能转变成热能或直接把电能转变成热能,以满足制品焙烧时所需要的温度,在期间完成一系列的物理化学变化,赋予制品各种宝贵的特性。
因此,在选择窑炉时,为了满足陶瓷制品的工艺要求,应充分了解窑炉类型及其优缺点,考察一些与已投入生产的陶瓷厂,然后结合本厂实际情况和必要的技术论证,方可定之。
判断一个窑炉好坏的标准,通常由以下几个方面来评价:
满足被烧成制品的热工制度要求,能够焙烧出符合质量要求的陶瓷制品。
烧窑操作要灵活,方便,适应性强,能够满足市场多变的要求。
经济性要高。
包括热效率要高,单位产品的综合能源消耗要少,炉龄要长。
容易实现机械化,自动化操作,劳动生产率高。
劳动条件好,劳动强度小,环境污染小。
以上几点,其中能否满足所烧制品的热工制度要求,是衡量陶瓷窑炉性能好坏的重要技术指标。
实际生产中,往往是力求使制品被烧使窑内温差尽量减少,它是提高产品合格率的关键所在。
隧道窑是耐火材料、陶瓷和建筑材料工业中最常见的连续式烧成设备。
其主体为一条类似铁路隧道的长通道。
通道两侧用耐火材料和保温材料砌成窑墙,上面为由耐火材料和保温材料砌筑的窑顶,下部为由沿窑内轨道移动的窑车构成的窑底。
隧道窑的最大特点是产量高,正常运转时烧成条件稳定,并且在窑外装车,劳动条件好,操作易于实现自动化,机械化.隧道要的另一特点是它逆流传热,能利用烟气来预热坯体,使废气排出的温度只在200°
C左右,又能利用产品冷却放热来加热空气使出炉产品的温度仅在80°
C左右,且为连续性窑,窑墙,窑顶温度不变,不积热,所以它的耗热很低,特别适合大批量生产陶瓷,耐火材料制品,具有广阔的应用前景.
2设计任务书
通过对专业知识的学习,本学期第4-6周为窑炉课程设计。
本文设计产品为直径9
英寸、质量0.4kg的汤盘的隧道窑,年产量为780万件,以天然气为燃料进行烧成,最
高烧成温度是1318℃,烧成周期为19h,年工作日时间为330天,入窑水分为〈3%,产
品合格率为95%,夏季室外温度为40℃。
2.1原始数据
产品规格:
9英寸(直径228.6mm),0.4kg块
9英寸汤盘坯料组成(%)
SiO2
Al2O3
CaO
MgO
Fe2O3
K2O+Na2O
I.L
69.20
19.96
0.87
0.49
0.88
3.12
5.48
烧成周期:
19小时
气氛:
常温-1050℃氧化气氛
入窑水分:
〈3%
产品合格率:
95%
工作日:
300天
夏季最高气温:
40oC
最高烧成温度:
1320oC
燃料
天然气
CO
H2
CH4
C2H4
H2S
CO2
N2
O2
Qnet(MJNm3)
0.2
95.6
3.5
0.3
0.1
41.58
3窑体主要尺寸的确定
3.1窑内宽的确定
3.1.1窑车棚板和支柱的选用
为减少窑内热量损失,提高热利用率,根据原始数据所给的清洁燃料液化气,直接用明焰裸烧,并结合装载制品10汤盘的重量大小,选定全耐火纤维不承重型结构窑车:
棚板、支柱均为碳化硅材料,以降低蓄散热损失,考虑到全窑最高烧成温度为13180C,选用碳化硅材料选用50%,体积密度2.2gcm3,最高使用温度14000C,导热系数计算式5.23+1.28×
10-3t。
棚板规格:
长×
宽×
高:
480×
480×
10(mm)
棚板质量=480×
10×
10-6×
2.2==5.07kg
支柱规格:
50×
50×
100(mm)
支柱质量=50×
100×
2.2=0.55kg
3.1.2窑车尺寸的确定
汤盘的规格
直径228.6×
40mm,400g。
制品码装方法
每块棚板装四个汤盘,棚板左右间距10mm,距窑车边缘15mm,每层中,横6竖4摆放,每层用24块棚板,35个支柱。
如图:
图3.1装码方式
窑车尺寸
棚板间距10mm,棚板边缘与窑车台面间距15mm,故窑车的尺寸
宽=6×
棚板规格480+间距10×
5+2×
边缘距离15=2930mm
长=4×
3+2×
边缘距离15=1950mm
3.1.3窑内宽的确定
隧道窑内宽是指窑内两侧墙间的距离,包括制品有效装载宽度与制品和两边窑墙的间距。
窑车与窑墙的间隙尺寸一般为25~30mm,本设计中取用30mm,则预热带与冷却带窑内宽:
B1=2930+30×
2=2990mm
3.2窑体长度的确定
3.2.1窑长尺寸
窑车每层装载制品数为4×
6×
4=96件,共8层,故每车装载制品数为96×
8=768件,
装窑密度g=每车装载件数车长=7681.95m=393.84件m
55.02m
G—生产任务,件年;
L—窑长,m;
—烧成时间,=55.021.95=28.2辆,取整数28辆,此时窑长=29×
1.95m=
56.55m。
该窑采用钢架结构,全窑不设进车和出车室,故全窑长取56.55m,分为29个标准节,每节长2000mm,所以窑炉全长5800mm。
3.2.2全窑各带长的确定
有烧成时间可知,各个段时间为6、5、8小时,据此预热带9节,烧成带7节,冷却带12节
各段长度及所占比例
预热带9节9×
2=18m,占总长1856=32.1%
烧成带7节7×
2=14m,占总长1656=25.0%
冷却带12节12×
2=24m,占总长2456=42.9%~
各个温度段对应长度下表
表3.1温度段对应长度
温度(0C)
烧成阶段
长度(m)
节数
20~300
预热带
10m
1~5
300~600
6m
6~10
950~1318
烧成带
14m
11~17
1318~800
冷却带(急冷带)
8m
18~21
800~400
冷却带(缓冷带)
4
22~23
400~200
冷却带(快冷带)
6
24~26
200~80
冷却带(尾冷带)
27~28
3.3窑内高的确定
为避免烧嘴喷出的高速火焰直接冲刷到局部制品上,影响火焰流动,造成较大温差,窑车台面与垫板间、上部制品与窑顶内表面之间都设有火焰通道,其高度(大于或等于烧嘴砖尺寸):
棚板下部通道取230mm,上部火焰通道取240mm。
因此,窑内高初定为:
火焰通道470+制品码装高度480mm+窑车台面距棚板200=1150mm。
通用砖厚取65mm,需要115065=17.6块,取18块,故
砖高=mm,灰缝=mm,内高=1170+36=1206mm此处确定预热带和缓冷段、快冷段的内高1206mm,烧成带和急冷段加两块通用砖65×
2+2×
2=134mm,故烧成带和急冷段的内高1206+134=1340mm
4烧成制度的确定
4.1温度制度的确定
根据制品的化学组成、形状、尺寸、线收缩率及其他一些性能要求,制订烧成制度如下:
表3-1温度制度
温度(0C)
时间(h)
烧成气氛
升(降)温速率(0Ch)
2.0
氧化气氛
140
150
2.5
180
1.5
还原气氛
100
中性气氛
60
1.0
烧成带(高火保温)
260
4.0
160
4.2烧成曲线图
图3-2烧成温度曲线
5工作系统的确定
5.1排烟系统
上述已算得预热带共22节,其中1~9节为排烟段,第一节前半节两侧墙及窑顶设置一道封闭气幕,气慕风由冷却带抽来的热空气提供。
后半节上部和下部各设1对排烟口(尺寸由第十一部分算得180×
100mm,为砌筑的方便高度取3×
67=201mm,排烟量可通过过桥转来控制),目的是使窑头气流压力自平衡,以减少窑外冷空气进入窑体。
第二节到第七节每节在窑车台面棚板通道处各设2对排烟口,位置正对。
另外,为方便调节预热带温度,尽量减少上下温差,在第9~13节上部设置喷风管,每节设3根(尺寸67),一侧2根另一侧1根,反复交替,两侧墙的喷风管成交错布置,这样有利于调节该段温度制度,也能有效搅拌预热带断面气流,达到减小预热带上下温差的目的。
在第14~22节下部设置高速调温烧嘴(即上风下嘴结构),同时烧嘴的正对面是观火孔(尺寸67),每节设3只高速调温烧嘴,同一侧上下对应位置上设2根喷风管和2只烧嘴,对侧上下对应位置设1根喷风管和1只烧嘴,高速调温烧嘴喷出的热烟气与喷风管喷出风在窑内断面上形成气流循环,使窑内气流实现激烈的搅动,促进上下温度场的均匀,而且加快了窑内的对流传热,缩短烧成时间。
5.2燃烧系统
第23节到42节为烧成带,第23、24节与预热带一样,仅在下部设置3只烧嘴,而从第25节开始,每节上下均匀布有高速烧嘴,上部设置2只,下部设置3只,上下与两侧墙均呈交替布置,这样有利于烧成带温度制度的调节。
5.3冷却系统
冷却带按照烧成工艺分成三段:
第43~49节为急冷段。
该段采用喷入急冷风直接冷却方式,除急冷首节(第43节)只在后半节设冷风喷口(尺寸67)(上设4个,下设3个)外,其余每节上部设5对冷风喷管,下部设4对冷风喷管,上下喷管交错设置。
第50~58节为缓冷段。
第51~58节的侧墙设置两段间冷壁,每两节作一段,顶部设有不锈钢间冷风箱,间冷壁及冷风箱均设有调节闸板,可根据需要调节抽热风量。
第59~68节为快冷段。
为加强出窑前的快速冷却,在该段第60~66节布置冷风喷管,直接鼓入冷风,每节6对——上部3对、下部3对,交错排布.
5.4传动系统
隧道窑对辊子材料要求十分严格,它要求制辊子材料热胀系数小而均匀,高温抗氧化性能好,荷重软化温度高,蠕变性小,热稳定性和高温耐久性好,硬度大,抗污能力强。
5.4.1辊子的选择
常用辊子有金属辊和陶瓷辊两种。
为节约费用,不同的温度区段一般选用不同材质的辊子。
本设计在选用如下:
中温段(40℃~400℃和400℃~80℃)
耐热不锈钢管φ40*3000(mm)
高温段(400~1180℃和1180~400℃)
碳化硅辊棒φ40*3000(mm)
5.4.2辊子