过程装备与控制工程毕业论文Word下载.docx
《过程装备与控制工程毕业论文Word下载.docx》由会员分享,可在线阅读,更多相关《过程装备与控制工程毕业论文Word下载.docx(47页珍藏版)》请在冰豆网上搜索。
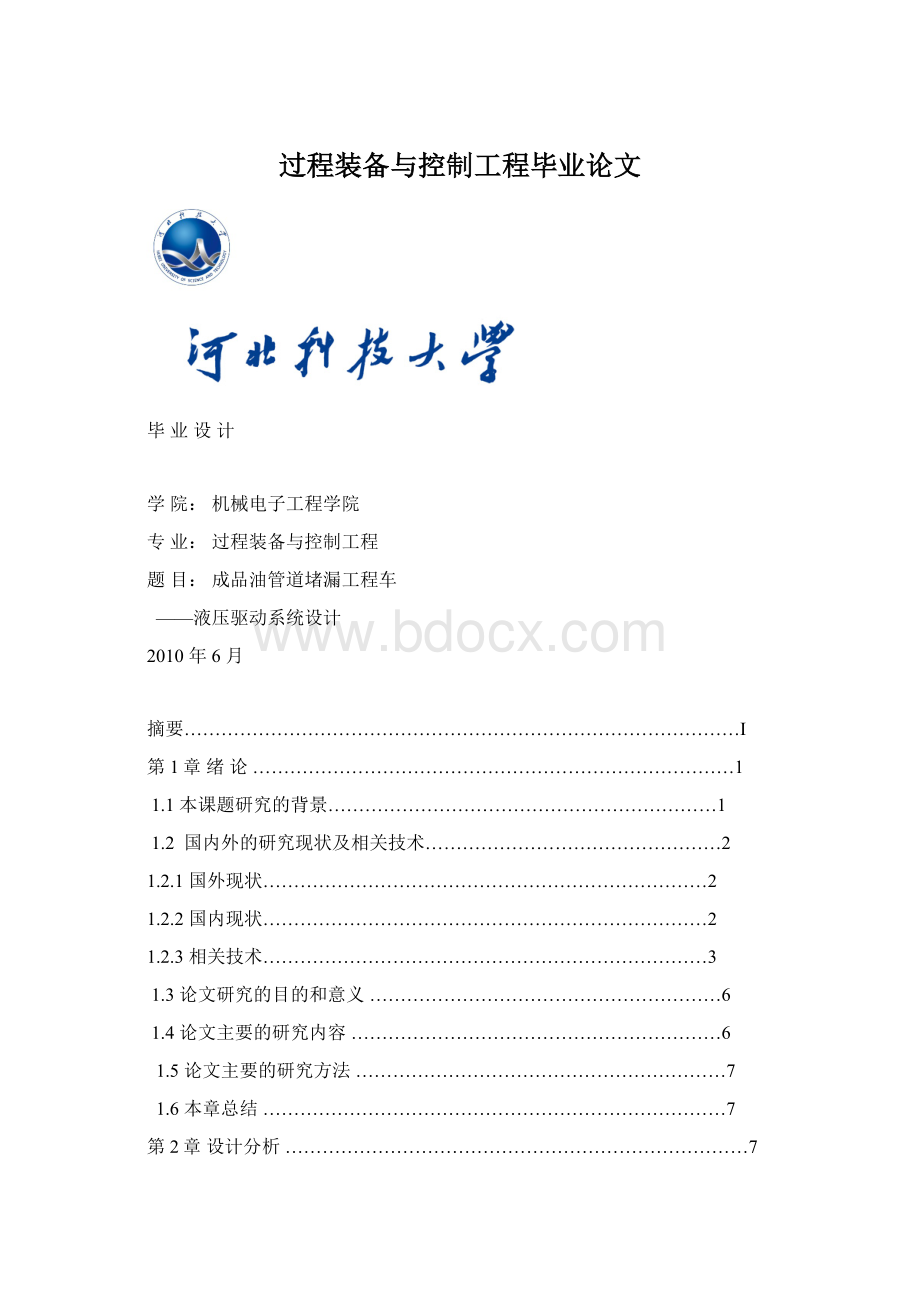
3.1液压系统的基本回路……………………………………………………11
3.1.1限压回路………………………………………………………………11
3.1.2缓冲回路………………………………………………………………11
3.1.3节流回路………………………………………………………………13
3.1.4行走限速回路…………………………………………………………14
3.1.5闭锁回路………………………………………………………………15
3.1.6再生回路………………………………………………………………15
3.2工程车液压系统的原理图…………………………………………………15
3.3本章总结……………………………………………………………………16
第4章工程功能的实现……………………………………………………………17
4.1直线行走……………………………………………………………………17
4.2行走工程中转弯……………………………………………………………17
4.3绕履带转弯…………………………………………………………………17
4.4绕装置中心转弯……………………………………………………………17
4.5装置失速控制………………………………………………………………18
4.6补油回路……………………………………………………………………18
4.7高低两速切换回路…………………………………………………………18
4.8爬坡角度限制回路…………………………………………………………18
4.9找管定位……………………………………………………………………18
4.10本章总结……………………………………………………………………19
第5章主要元件的参数计算及其选型……………………………………………19
5.1选择行走马达………………………………………………………………19
5.2选择液压泵…………………………………………………………………19
5.2.1液压泵工作压力的确定…………………………………………………20
5.2.2确定液压泵的流量………………………………………………………20
5.2.3选择液压泵的规格………………………………………………………21
5.3选择液压控制阀……………………………………………………………22
5.4选择发动机…………………………………………………………………24
5.5本章小结……………………………………………………………………25
第6章液压辅助元件的选择与计算………………………………………………25
6.1油箱的计算与结构………………………………………………………25
6.1.1油箱有效容积的计算…………………………………………………25
6.1.2油箱的结构……………………………………………………………26
6.2管道的计算与选择………………………………………………………27
6.2.1吸油管道的计算………………………………………………………27
6.2.2回油管道的计算………………………………………………………28
6.2.3油管的选材……………………………………………………………29
6.2.4液压管路的连接方法…………………………………………………29
6.3过滤器的选用………………………………………………………………30
6.4液压系统温度的计算和冷却器的选用……………………………………31
6.4.1液压系统温度的计算…………………………………………………31
6.4.2冷却器的选用…………………………………………………………34
6.5加热器的选用………………………………………………………………35
6.6本章总结……………………………………………………………………35
第7章液压系统性能验算………………………………………………………36
7.1液压系统压力损失…………………………………………………………36
7.1.1沿程压力损失……………………………………………………………36
7.1.2局部压力损失……………………………………………………………36
7.2液压系统发热温升计算……………………………………………………37
7.2.1液压系统发热功率计算…………………………………………………37
7.2.2液压系统散热功率计算…………………………………………………39
7.3液压系统邮箱大小的验算……………………………………………………41
7.4冷却器所需冷却面积的验算…………………………………………………41
7.5本章的总结……………………………………………………………………42
第8章液压装置的结构设计………………………………………………………42
8.1液压装置的结构……………………………………………………………42
8.2液压泵站的类型及其组件的选择…………………………………………42
8.2.1液压泵类型的选择………………………………………………………42
8.2.2液压元件的配置形式……………………………………………………42
8.3本章总结……………………………………………………………………43
第9章装置防爆……………………………………………………………………43
9.1电气控制方面………………………………………………………………43
9.2静电放电控制方面…………………………………………………………44
9.3机械系统方面………………………………………………………………44
9.4本章总结……………………………………………………………………45
结论…………………………………………………………………………………46
参考文献……………………………………………………………………………48
致谢…………………………………………………………………………………50
第1章绪论
1.1本课题的研究背景
当今社会,能源问题日益告急,然而新能源尚未大规模开发,在相当长的一段时期之内,石油能源仍将在人类的生产生活中占据着霸主地位。
世界各国仍不断地进行着石油开采和石油炼制方面的研究。
在石油工业高度发展的同时,石油以及成品油的运输也成为现实中一个重要问题:
伴随着地下管道大面积铺设,于此带来大大小小的安全隐患,不发分子进行打孔盗油,从中来谋取利益。
再加上自然天气和地理因素的影响,输油管道会发生腐蚀,导致发生泄露、油喷现象。
现象发生后易造成二次灾难,产生更大的损失。
输油管道泄漏事故一旦发生,其堵漏工作便成为管道抢修的重要环节。
同时堵漏方法及堵漏时间的长短直接关系到泄漏发生的经济损失,财产安全,环境污染等。
在国内国外的石油运输业中,输油管道占有重要地位。
因输油管道相比于其它运输方式具有众多的优点:
可承受多种外力的作用,包括本身的重量、流体作用在管端的推力、风雪载荷、土壤压力、热胀冷缩引起的热应力、振动载荷和地震灾害等,同时也降低了成本,提高了输油效率。
因此,管道输油在石油以及成品油运输中得到非常广泛的应用。
它的建成以及对其不断的维护与检修对国家经济增长、国防安全、综合国力的增强,都具有重要意义。
然而就目前来看,输油管道运行条件苛刻,油品易燃易爆,管道腐蚀破裂常常引起连锁事故。
因腐蚀导致的原油泄漏、停工停产、人身伤亡及环境污染给相关企业带来了巨大的损失,同时各种人为管道破坏、违章占压管道、违章施工作也是造成管道泄漏事故的重要原因。
输油管道泄漏事故严重危害着国家和人民群众的生命财产安全。
堵漏作为管道抢修的关键步骤,其技术的发展直接关系到泄漏事故发生后所造成的危害程度。
然而目前在国内,泄漏孔的封堵主要是靠人工安装夹具和补块。
其作业的危险性高,并且操作时要求管道降低管道压力,在低点修补时还需要排出高点管道中大量的油品,从而增加了整个抢修的时间,同时,也会引起油品泄漏量的增加,加大了发生重大事故的可能性。
我们在堵漏技术和堵漏设备上的不完善,促成了管道抢修这一急需研究和解决的重要课题。
因此成品油管道堵漏工程车,即成为这一重要研究课题的初步尝试。
1.2国内外的研究现状及相关技术[1]
本论文所设计的堵漏工程车是以某小型液压挖掘机为模型而改造设计的,所以液压挖掘机国内外的研究现状及相关技术间接的影响该工程车的研究现状及技术。
纵观挖掘机发展史,在技术上大致经历了三次飞跃,第一次是柴油机的出现,使挖掘机有了较理想的动力装置;
第二次是液压技术的广泛应用,使挖掘机的传动方式更趋合理;
第三次是控制技术的广泛应用,使液压挖掘机的控制系统日益完善,并向着自动化、智能化方向发展。
1.2.1国外现状
工业发达国家的挖掘机生产较早,法国、美国、德国、俄罗斯、日本是小型单斗液压挖掘机的主要生产国家,从20世纪80年代开始生产特大型挖掘机。
例如,美国马利昂公司生产的斗容量50-100m3挖掘机;
B-E(布比赛鲁斯-伊利)公司生产的斗容量107m3的挖掘机,是世界上目前最大的挖掘机。
自20世纪90年代以来,国外工程机械进入了一个新的发展时期,在广泛应用新技术的同时,不断涌现出新结构和新产品。
继完成提高整机可靠性任务之后,技术发展的重点在于增加产品的电子信息技术含量和智能化程度,努力完善产品的标准化、系列化和通用化,改善驾驶人员的工作条件,向节能、环保方向发展。
目前,国外的遥控挖掘机多以纯遥控为主,未发现手动、遥控并用型挖掘机,设备的利用率低,都属于概念型样机,价格较高。
所以国外的抢险工程车基本上就是以纯遥控为主的,而且技术先进,动作灵敏、准确。
1.2.2国内现状
早在1954年我国就开始生产机械式挖掘机,当时的抚顺机器厂(抚顺挖掘机厂前身)引进了前苏联的机械式挖掘机。
由于国家经济建设的需要,后又发展10余家厂生产,到1966年12年间全国共生产了机械式挖掘机3000余台。
在80年代初引进德国系列液压挖掘机制造技术,浙江大学的冯培恩教授开始率先着手研究挖掘机机电一体化技术,首先实现挖掘机器人作业过称的分级规划和局部自主控制。
后引进日本小松制作所的PC系列挖掘机制造技术,使我国挖掘机的技术上升到一个新水平。
在我国由于挖掘机的发展滞后,故以挖掘机为基础的抢险工程车研究的起步较晚,总体发展水平也落后于西方发达国家,特别是在成品油堵漏工程车方面的研究还没有起步。
抢险工程车是在各种危
图1.1无线遥控工程车
险及恶劣环境下从事危险作业、抢险救灾、垃圾清理和化学灾害处理等工作,其要求人员远离事故现场,所以就要开发遥控的抢险工程车,本论文设计的堵漏工程车也不例外。
1.2.3相关技术[2]
1.2.3.1遥控技术
本堵漏工程车由于在管道堵漏时,其泄露环境危险,易燃易爆,所以要求设计成遥控工程车,如图1.2。
工程车辆上的所有执行装置全部采用电信号控制,在遥控操作时,操作者虽然从驾驶室中解脱了出来,但仍需要像常规操作那样控制各关节点。
无线遥控液压工程车系统,由控制台发射、接收部分和车上接收、发射部分组成。
控制台包括图像及声音接收器,为处理输入信号所需要的译码装置、控制装置和编码装置。
机器上接收器接收发射台发出的控制信号,并将信号转换为驱动比例电磁铁和控制摄像机所需
的信号。
发射器则将电视图像信号通过天线发送到远方的操作员。
在工程车上装有摄像头,操纵人员可以根据摄像头中视野来控制工程车的动作。
1.2.3.2液压控制技术
本堵漏工程车以挖掘机为基础,其模型如图1.3所示,采用三组液压缸,工作装置具有三个自由度,铲斗可实现有限的平面转动,加上液压马达驱动回转运动,使铲斗
大到有限空间,再通过行走马达驱动行走(移位),使挖掘空间可沿水平方向得到间歇地扩大,从而满足挖掘作业的要求。
液压挖掘机传动示意图由柴油机驱动液压泵,操纵分配阀,将高压油送给个液压执行元件(液压缸与液压马达)驱动相应的机构进行工作。
液压挖掘机采用连杆机构原理,各部分的运动通过液压缸的伸缩来实现。
挖掘作业时,接通回转马达,转动转台,使工作装置转到挖掘位置,同时操纵动臂缸小腔进油使液压缸回缩;
动臂下降至铲斗触底后在操纵斗杆缸或铲斗缸,液压缸大腔进油而伸长,使铲斗进行挖掘装载工作。
在实际挖掘作业中,由于土质情况、挖掘面条件及挖掘液压系统的不同,三种液压缸在挖掘循环中的动作配合可以是多样的、随机的。
总之,液压挖掘机是由多学科、多系统组成的有机整体,只有在系统层面上的各系统、各学科协同优化才能获得挖掘机整机的最佳性能。
1.2.3.3电液比例控制技术[3]
电液比例控制阀简称比例阀,其结构特点是由比例电磁铁与液压控制阀两部分组成。
相当于在普通液压控制阀上装上比例电磁铁以代替原有的手调控制部分。
电磁铁接收输入的电信号,连续地或按比例地转换成力或位移。
液压控制阀受电磁铁输出的力或位移控制,连续地或按比例的压力和流量。
比例阀实现连续控制的核心是采用了比例电磁铁,电磁铁是一种通电后使铁磁物质产生电磁吸力,把电能转换成机械能的电器元件。
比例电磁铁的工作原理见图1.4所示。
图1.2液压挖掘机传动示意图
当线圈2通电后,磁轭1和衔铁3中都产生磁通,产生电磁吸力,将衔铁吸向轭铁。
衔铁上受的电磁力和阀上的或电磁铁上的弹簧力平衡,电磁铁输出位移。
当衔铁3运动时,间隙δ保持恒值并无变化,所以比例电磁铁的吸力F和δ无关,其静特性见图1.5所示。
图中静坐标是比例电磁铁的吸力F,横坐标是衔铁的行程S。
图1.3比例型电磁铁原理图1.4比例型电磁铁的静特性
1—磁轭;
2—线圈;
3衔铁;
4—导磁套;
Ⅰ—吸合区;
Ⅱ—工作行程区;
5—调整弹簧;
6—调整螺钉;
7—推杆;
Ⅲ—空行程区;
8—限位片;
9—工作气隙;
10—隔磁环;
δ—间隙;
由图可得出以下结论:
(1)在S很小,或S很大时,力F随行程S而变化,不宜作为工作区段。
(2)在S大约为1.5mm左右的中间区段,曲线大体上呈水平的平行线,这个区段的曲线可作为工作区段曲线。
一般来说,比例电磁铁的有效工作行程小于开关型电磁铁的有效工作行程。
(3)比例电磁铁的吸力在有效行程内和线圈中的电流成正比。
(4)比例电磁铁的吸力在有效行程内和衔铁位置无关。
由于比例阀实现了用经过放大器放大的电信号对液体压力、流量和流向的控制,构成自动控制系统,即可开环控制,也可闭环控制;
因其能连续地、按比例地对压力和流量进行控制,控制方便且可避免压力和流量有级切换时的冲击;
抗污染性能优于伺服阀,制造比伺服阀简单,价格低于伺服阀,但高于普通液压阀;
一个比例阀可兼有几个普通液压阀的功能,可简化回路,减少阀的数量,提高可靠性。
随着耐高压直流比例电磁铁的产生,电液比例阀的优越性得到了进一步发展。
耐高压直流比例电磁铁除了具有一般电液比例阀的优点,还具有较大的功率重量比,可以输出较大的位移和力,不仅可用来推动比例先导阀,还可以直接驱动主阀。
由于它的导套具有足够的耐压强度,所以比例电磁铁可承受35Mpa静压力。
1.3论文研究的目的与意义
在我国,输油管道多埋于地下,泄漏发生时,其产生的高压喷射冲出地面,在泄漏周围环境中形成大范围的喷射油液雾化,造成极度危险的环境空间。
同时由于管道埋于地下,具体的泄漏点无法确定,根本无法进行人工手动或机械自动安装卡具。
本课题根据我国成品油管道泄漏发生的这一实际情况,进行了“履带行走式油管堵漏工程车—液压驱动系统”的设计。
目的是使该工程车完成在较高的压力下对φ508mm成品油输油管道泄漏的堵漏工作。
该工程车应用后,可以远程遥控进行管道漏点的找管定位,对漏油进行简单回收,减少成油品的泄漏量或者是损失量,有效控制喷射油液雾化,降低次生灾害发生的可能性,减少泄漏对环境的污染,为后续维护抢修人员实施抢修提供更安全的工作环境。
1.4论文主要的研究内容
成品油管道堵漏工程车是履带式液压挖掘机与液压、自动控制技术及无线遥控相结合的产物。
用图1.5进行表示。
图1.5工程车的控制
本课题设计了“成品油管道堵漏工程车——液压驱动系统”,以完成成品油管道泄漏的堵漏工作。
成品油管道堵漏工程车由工作装置,回转机构及行走机构三部分组成,其中工作装置包括大臂杆,小臂杆,收油罩杆,行走机构包括左右行走马达和后支撑机构,上述所有机构的动作均由液压驱动。
本说明书详细阐述了“成品油管道堵漏工程车——液压驱动系统”的设计过程。
包括液压系统设计的分析,液压原理图的制定,各个液压元件的选择计算,液压装置的结构设计以及液压系统的性能验算。
液压驱动系统的设计是该工程车辆设计的关键环节之一,采用液压驱动有诸多优点:
在同等体积下,液压装置比电气装置产生出更多的动力;
液压装置工作比较平稳,可方便在大范围内实现无极调速。
低速大扭矩马达的最低稳定速度为1r/min。
液压传动易于实现自动化;
液压装置易于实现过载保护;
由于液压元件已实现标准化,系列化和通用化,液压系统的设计,制造,使用和推广都比较方便。
1.5论文研究的主要方法
以某液压挖掘机的液压系统为基础,按照液压系统设计步骤设计出堵漏工程车的合适液压系统。
其基本思路是:
(1)讨论所设计工程车所满足的基本要求,即技术要求和功能要求
(2)参照挖掘机的液压系统原理图,初定都漏工程车的液压原理图(3)分析初定的原理图,讨论所选的液压系统能否满足要求(4)选择并计算基本的液压元件和液压辅助元件(5)验证所选的液压元件是否满足设计要求(6)得出结论。
1.6本章总结
本章阐述了该论文研究的背景、目的、意义及内容,简要说明了改造设计成该工程车的原型—液压挖掘机的国内外发展现状和技术水平,最后对本论文的主要研究方法及思路做了一个概括的说明,也就是在液压系统的设计步骤基础上,对后面的设计方案提供指导。
第2章设计分析
2.1工程车的设计要求
按照堵漏工程车的工作装置、回转装置、行走装置及其它装置的工作及传动需要,把各种液压泵、液压马达、液压阀等液压元件用液压油管有顺序有规律地连接在一起就可以组成一个堵漏工程车的液压系统。
在工作的过程中,液压系统是用油液作为自己的工作过程中介质、然后利用液压泵把发动机送出的机械能转变为液压油的液压能来传递,然后通过液压缸和液压马达等各种执行元件再把液压油的液压能转变为各种机械能,这样就可以实现堵漏工程车所需要的各种动作[4]。
堵漏工程车在预工作时,动作比较复杂,主要机构需要经常启动、制动、换向,冲击和振动非常频繁,温度和环境变化大,因此该工程车液压系统应满足如下要求。
2.1.1技术要求
成品油管道堵漏工程车以某小型液压挖掘机为模型,虽然很多技术要求与挖掘机相同,但是它拥有自己的技术要求来满足工程的需要:
表2.1成品油管道堵漏工程车主要技术参数
项目名称
单位
数值
输油管直径
毫米
φ508
最大输油压力
兆帕
10
维抢工作允许压力
≤3
最大工作压力
20
最大流量
升/分钟
60
输入功率
千瓦
22
最大承载力
千牛顿
22.2
最大行走速度
公里/小时
2
最大爬坡角度
度
25
整车重量
吨
≤5
吊臂可承载载荷
15
车架可实现回转角度
360
2.1.2功能要求
本工程车以液压挖掘机为模型,拥有自己特殊的工作装置,因此,具有与挖掘机不同的功能要求[4]:
2.1.2.1行走功能
(1)直线行走功能
在装置不需要转弯时,要求能进行直线行走。
(2)装置转弯功能
考虑到装置在行走过程中,由于道路原因需要转弯,需设计行走中转弯功能;
当装置在行走过程中由于道路原因,或找管定位过程中,需要装置拐急弯时,需设计绕履带转弯的功能;
当装置接近泄漏油喷射口,需要就地调整装置的方位角度时,有时需要绕装置中心就地旋转。
需设计绕履带中心旋转的功能。
(3)爬坡行走功能
因为装置的使用环境包括山路,有上下坡道,要求爬坡角度为25º
。
装置行走部分采用履带式结构,动力由液压系统提供,左右履带分别由两台低速大扭矩马达驱动。
通过分别控制两台液压马达液压油的流量,可实现此功能。
(4)装置失速控制功能
考虑到装置在行走过程中有上下坡的要求,当装置下坡时,由于重力作用有可能造成失速,因此在液压系统中需设计了失速控制。
(5)高低两速切换功能
考虑到充分利用系统的功率,应设计高低速自动切换功能。
当装置在平地或下坡行走时,装置需要的驱动功率小,使装置实现高速行走;
当装置上坡时,装置需要大功率驱动,低速行走。
(6)装置行走刹车功能
装置要求能够上下坡道,在堵漏工作进行时,要求装置必须能够可靠的制动,车体确保严格不动,保证后续工作准确可靠的进行。
在动力系统、传动系统、执行系统出现故障时,更要求有可靠的刹车装置,否则装置会翻下山去,造成无法挽回的损失。
当液压系统停止供油,或由于故障液压系统不能供油时,液压马达自动刹车,保证装置安全。
2.1.2.2找管定位功能
装置行走过程中,用遥控摄像头远程监控路面情况和管道位置情况。
人工远程控制该装置行走到漏油油管附近后,装置停止行走并刹车制动。
通过遥控摄像头监控,通过液压系统,控制大臂体、小臂和收油器三个运动部件的转动,实现泄漏控制和漏油回收部件的定位。
2.1.2.3喷射控制和漏油回收功能
利用流体喷射形成的动能把流体导流到指定位置。
采用内锥形小锥角大导油管结构,减少油流喷射入收油器中在导流方向的运动能量损失。
收油器下端设有回收檐,减少反射回来的油流的速度和泄漏油的雾化,降低收油