机械四大传动的分析及研究Word文档格式.docx
《机械四大传动的分析及研究Word文档格式.docx》由会员分享,可在线阅读,更多相关《机械四大传动的分析及研究Word文档格式.docx(35页珍藏版)》请在冰豆网上搜索。
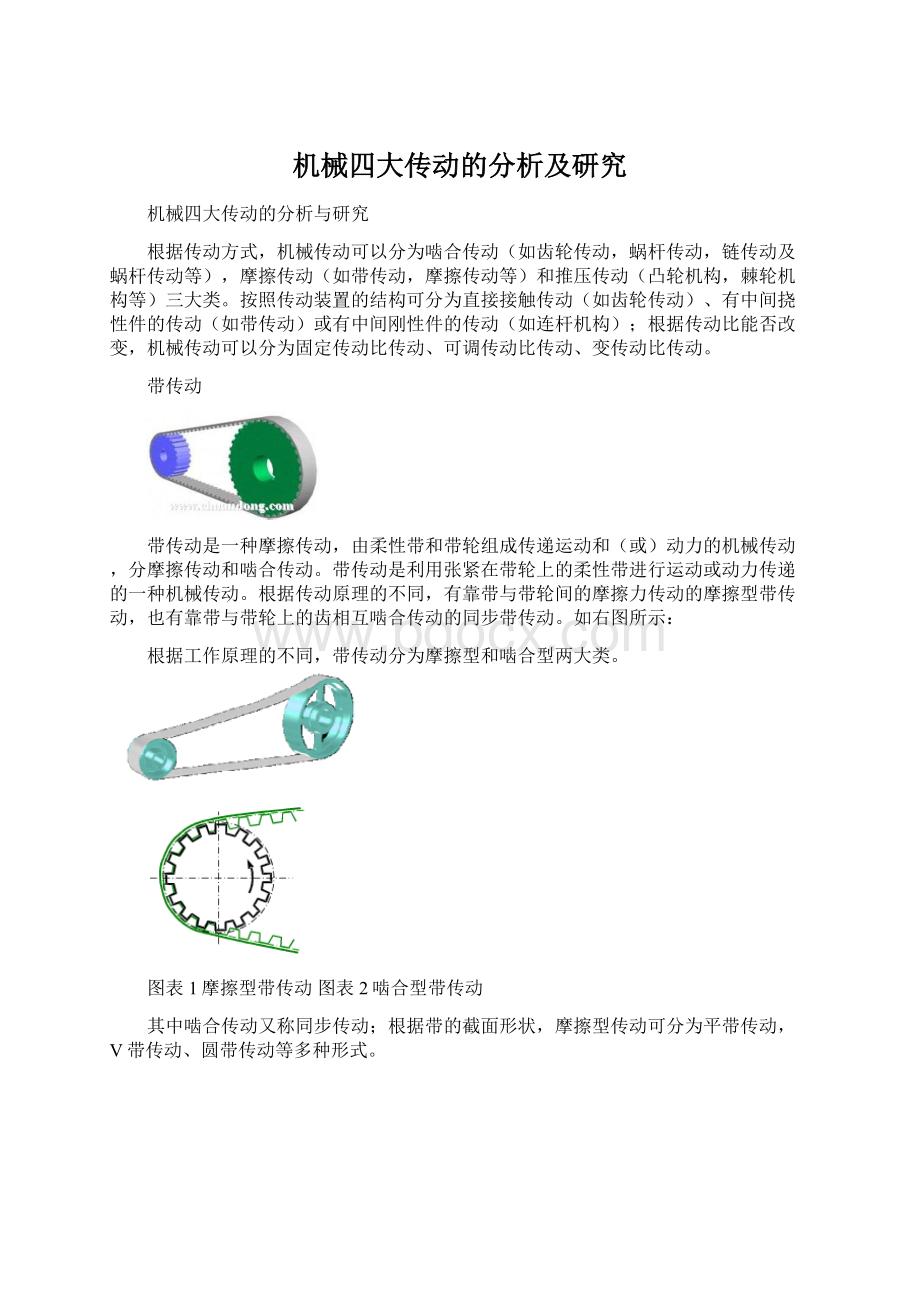
因此,在不打滑前提下,保证带具有一定的疲劳强度和寿命是V带传动工作能力的设计计算准则。
单根V带既不打滑,又保证一定疲劳寿命时所能传递的额定功率P为
2V带传动设计步骤和传动参数选择
1.选择V带型号
V带有普通V带、窄V带、宽V带、大楔角V带等多种类型,其中普通V带应用最广,窄V带的使用也日见广泛。
普通V带由顶胶、抗拉体(承载层)、底胶和包布组成,如图11.9所示。
抗拉体由帘布或线绳组成,是承受负载拉力的主体。
其上下的顶胶和底胶分别承受弯曲时的拉伸和压缩变形。
线绳结构普通V带具有柔韧性好的特点,适用于带轮直径较小,转速较高的场合。
图11.9
V带都制成无接头的环形。
各种型号带的基准长度见图11.10。
图11.10V带的基准长度Ld
带的型号可根据计算功率PC和小带轮转速n1选取,普通V带见图11.11,PC=KAP(11.12)
式中KA--工作情况系数,见表11.3;
P--名义传动功率(kW)。
当工况位于两种型号相邻区域时,可分别选取这两种型号进行计算,最后进行分析比较,选用较好者。
2.确定带轮基准直径
在V带轮上,与所配用V带的节面宽度bp相对应的带轮直径称为基准直径dd,带轮基准直径系列见表11.4。
带轮愈小,传动尺寸结构越紧凑,但带的弯曲应力愈大,带容易疲劳断裂。
为避免产生过大的弯曲应力,对各种型号的V带都规定了最小带轮基准直径ddmin.
图11.13
⑶实际中心距
7.确定带的初拉力
初拉力的大小是保证带传动正常工作的重要因素。
初拉力过小,摩擦力小,容易打滑;
初拉力过大,带的寿命低,轴和轴承受力大。
推荐单根V带张紧后的初拉力F0为
图11.14
圆带传动的截面是圆形,其柔韧性较好,适用带轮较好的场合;
但承载能力较低故只用于轻装置中。
啮合型带传动一般也称为同步带传动。
它通过传动带内表面上等距分布的横向齿和带轮上的相应齿槽的啮合来传递运动。
与摩擦型带传动比较,同步带传动的带轮和传动带之间没有相对滑动,能够保证严格的传动比。
但同步带传动对中心距及其尺寸稳定性要求较高。
同步带传动具有带传动、链传动和齿轮传动的优点。
同步带传动由于带与带轮是靠啮合传递运动和动力,故带与带轮之间无相对滑动,能保证准确的传动比。
同步带通常以钢丝绳或玻璃纤维绳为抗拉体,氯丁橡胶或聚氨酯为基体,这种带薄而且轻,故可用于较高速度。
传动时的线速度可达50m/s,传动比可达10,效率可达98%。
传动噪声比带传动、链传动和齿轮传动小,耐磨性好,不需油润滑,寿命比摩擦带长。
其主要缺点是制造和安装精度要求较高,中心距要求较严格。
所以同步带广泛应用于要求传动比准确的中、小功率传动中。
链传动
链传动是通过链条将具有特殊齿形的主动链轮的运动和动力传递到具有特殊齿形的从动链轮的一种传动方式。
链传动是啮合传动,平均传动比是准确的。
它是利用链与链轮轮齿的啮合来传递动力和运动的机械传动。
1.链条
链条长度以链节数来表示。
链节数最好取为偶数,以便链条联成环形时正好是外链板与内链板相接,接头处可用弹簧夹或开口销锁紧。
若链节数为奇数时,则需采用过渡链节。
在链条受拉时,过渡链节还要承受附加的弯曲载荷,通常应避免采用。
齿形链由许多冲压而成的齿形链板用铰链联接而成,为避免啮合时掉链,链条应有导向板(分为内导式和外导式)。
齿形链板的两侧是直边,工作时链板侧边与链轮齿廓相啮合。
铰链可做成滑动副或滚动副,滚柱式可减少摩擦和磨损,效果较轴瓦式好。
与滚子链相比,齿形链运转平稳、噪声小、承受冲击载荷的能力高;
但结构复杂、价格较贵、也较重,所以它的应用没有滚子链那样广泛。
齿形链多用于高速(链速可达40m/s)或运动精度要求较高的传动。
国家标准仅规定了滚子链链轮齿槽的齿面圆弧半径、齿沟圆弧半径和齿沟角的最大和最小值(详见GB1244-85)。
符合上述要求的端面齿形曲线有多种。
最常用的齿形是“三圆弧一直线”。
2.链轮
链轮轴面齿形两侧呈圆弧状,以便于链节进入和退出啮合。
齿形用标准刀加工时,在链轮工作图上不必绘制端面齿形,但须绘出链轮轴面齿形,以便车削链轮毛坏。
轴面齿形的具体尺寸见有关设计手册。
链轮齿应有足够的接触强度和耐磨性,故齿面多经热处理。
小链轮的啮合次数比大链轮多,所受冲击力也大,故所用材料一般应优于大链轮。
常用的链轮材料有碳素钢(如Q235、Q275、45、ZG310-570等)、灰铸铁(如HT200)等。
重要的链轮可采用合金钢。
小直径链轮可制成实心式;
中等直径的链轮可制成孔板式;
直径较大的链轮可设计成组合式,若轮齿因磨损而失效,可更换齿圈。
链轮轮毂部分的尺寸可参考带轮。
链传动-类型
链传动-设计
链传动设计
1.失效形式
链传动的失效形式主要有以下几种:
(1)链板疲劳破坏 链在松边拉力和紧边拉力的反复作用下,经过一定的循环次数,链板会发生疲劳破坏。
正常润滑条件下,链板疲劳强度是限定链传动承载能力的主要因素。
(2)滚子、套筒的冲击疲劳破坏 链传动的啮入冲击首先由滚子和套筒承受。
在反复多次的冲击下,经过一定循环次数,滚子、套筒可能会发生冲击疲劳破坏。
这种失效形式多发生于中、高速闭式链传动中。
(3)销轴与套筒的胶合 润滑不当或速度过高时,销轴和套筒的工作表面会发生胶合。
胶合限定了链传动的极限转速。
(4)链条铰链磨损 铰链磨损后链节变长,容易引起跳齿或脱链。
开式传动、环境条件恶劣或润滑密封不良时,极易引起铰链磨损,从而急剧降低链条的使用寿命。
(5)过载拉断 这种拉断常发生于低速重载的传动中。
在一定的使用寿命下,从一种失效形式出发,可得出一个极限功率表达式。
为了清楚,常用线图表示。
为在正常润滑条件下,对应各种失效形式的极限功率曲线。
图中阴影部分为实际上使用的区域。
若润滑密封不良及工况恶劣时,磨损将很严重,其极限功率会大幅度下降。
2.功率曲线图
采用推荐的润滑方式时,各型号A系列滚子链所能传递的功率。
若润滑不良或不采用推荐的润滑方式时,应将图中值降低;
当链速v≤1.5m/s时,降低到50%;
当1.5m/s<v≤7m/s时,降低到25%;
当v>7m/s而又润滑不当时,传动不可靠。
张紧装置时,应将计算的中心距减小2~5mm使链条有小的初垂度。
2.
额定功率确定方法
试验条件:
两链轮安装在同一个水平面上,单列链水平布置、载荷平稳、工作环境正常、按推荐的润滑方式润滑、使用寿命15000h;
链因磨损而引起链节距的相对伸长量
对于的低速链传动,链的主
要失效形式是过载拉断,应
进行静强度校核。
静强度安
全系数应满足下列要求
滚子链传动的设计步骤和主要参数的确定
设计滚子链时的原始数据为:
传动的功率、小链轮和大链轮的转速(或传动比)、原动机种类、载荷性质以及传动用途等。
•设计步骤:
1.选择链轮齿数z1、z2
小链轮齿数对链传动的平稳性和使用寿命有较大的影响,链轮齿数不宜过多或过少。
过少时将:
1)增加传动的不均匀性和动载荷;
2)增加链节间的相对转角,从而增大功率消耗;
3)增加铰链承压面间的压强(因齿数少时,链轮直径小,链的工作拉力将增加),从而加速铰链磨损等;
4)增加链传动的圆周力,从而加速了链条和链轮的损坏。
由于链节数应选用偶数,所以链轮齿数最好选质
数或不能整除链节数的数。
并优先选取17、19、
21、23、25、38、57、76、95、114。
2.确定传动比i
3.确定计算功率
4.确定链节距:
在承载能力足够条件下,应选取较小节距的单排链,高速重载时,可选用小节距的多排链。
一般,载荷大、中心距小、传动比大时,选小节距多排链;
速度不太高、中心距大、传动比小时选大节距单排链。
5.确定中心距和链长
6.链速和链轮的极限转速
链速的提高受到动载荷的限制,所以一般最好不超过12m/s。
如果链和链轮的制造质量很高,链节距较小,链轮齿数较多,安装精度很高,以及采用合金钢制造的链,则链速也允许超过20m/s-30m/s。
•
链轮的最佳转速和极限转速。
7.计算链传动作用在轴上的力FQ
齿型链传动设计
齿轮传动
齿轮传动是利用两齿轮的轮齿相互啮合传递动力和运动的机械传动。
按齿轮轴线的相对位置分平行轴圆柱齿轮传动、相交轴圆锥齿轮传动和交错轴螺旋齿轮传动。
齿轮传动是指用主、从动轮轮齿直接、传递运动和动力的装置。
在所有的机械传动中,齿轮传动应用最广,可用来传递相对位置不远的两轴之间的运动和动力。
设计准则
针对齿轮五种失效形式,应分别确立相应的设计准则。
但是对于齿面磨损、塑性变形等,由于尚未建立起广为工程实际使用而且行之有效的计算方法及设计数据,所以目前设计齿轮传动时,通常只按保证齿根弯曲疲劳强度及保证齿面接触疲劳强度两准则进行计算
1、闭式齿轮传动
2、开式齿轮传动
减少噪音方法
为了避免减速机不能通过出厂测试,原因之一是减速机存在间歇性高噪声;
用ND6型精密声级计测试,低噪声减速机为72.3Db(A),达到了出厂要求;
而高噪声减速机为82.5dB(A),达不到出厂要求。
经过反复测试、分析和改进试验,得出的结论是必须对生产的各个环节进行综合治理,才能有效降低齿轮传动的噪声。
1.控制齿轮的精度:
齿轮精度的基本要求:
经实践验证,齿轮精度必须控制在GB10995-887~8级,线速度高于20m/s齿轮,齿距极限偏差、齿圈径向跳动公差、齿向公差一定要稳定达到7级精度。
在达到7级精度齿轮的情况下,齿部要倒棱,要严防齿根凸台。
2.控制原材料的质量:
高质量原材料是生产高质量产品的前提条件,该公司用量最大的材料40Cr和45钢制造齿轮。
无论通过何种途径,原材料到厂后都要经过严格的化学成分检验、晶粒度测定、纯洁度评定。
其目的是及时调整热处理变形,提高齿形加工中的质量。
3.防止热处理变形:
齿坯在粗加工后成精锻件,进行正火或调质处理,以达到:
⑴软化钢件以便进行切削加工;
⑵消除残余应力;
(3)细化晶粒,改善组织以提高钢的机械性能;
⑷为最终能处理作好组织上的准备。
应注意的是,在正火或调质处理中,一定要保持炉膛温度均匀,以及采用工位器具,使工件均匀地加热及冷却,严禁堆放在一起。
需钻孔减轻重量的齿轮,应将钻孔序安排在热处理后进行。
齿轮的最终热处理采用使零件变形较小的齿面高频淬火;
高频淬火后得到的齿面具有高的强度、硬度、耐磨性和疲劳极限,而心部仍保持足够的塑性和韧性。
为减少变形。
齿面高频淬火应采用较低的淬火温度和较短的加热时间、均匀加热、缓慢冷却。
4.保证齿坯的精度:
齿轮孔的尺寸的精度要求在孔的偏差值的中间差左右分布,定在±
0.003~±
0.005mm;
如果超差而又在孔的设计要求范围内,必须分类,分别转入切齿工序。
齿坯的端面跳动及径向跳动为6级,定在0.01~0.02mm范围内。
5.切齿加工措施:
对外购的齿轮刀具必须进行检验,必须达到AA级要求。
齿轮刀具刃磨后必须对刀具前刃面径向性、容屑槽的相邻周节差、容屑槽周节的最大累积误差、刀齿前面与内孔轴线平行度进行检验。
在不影响齿轮强度的前提下,提高齿顶高系数,增加0.05~0.1m,,改善刀具齿顶高系数,避免齿轮传动齿根干涉。
M=1~2的齿轮采用齿顶修圆滚刀,修圆量R=0.1~0.15m。
消除齿顶毛刺,改善齿轮传动时齿顶干涉。
切齿设备每年要进行一次精度检查,达不到要求的必须进行维修。
操作者亦要经常进行自检,特别是在机床主轴径向间隙控制在0.01mm以下,刀轴径跳0.005mm以下,刀轴窜动0.008mm以下。
刀具的安装精度:
刀具径向跳动控制在0.003mm以下,端面跳动0.004mm以下。
切齿工装精度,心轴外径与工件孔的间隙,保证在0.001~0.004mm以内。
心轴上的螺纹必须在丙顶类定位下,由螺纹床进行磨削:
垂直度≦0.003mm,径跳≦0.005mm。
螺母必须保证内螺纹与基准面一次装夹车成,垫圈的平行度≦0.003mm。
6.文明生产:
齿轮传动噪声有30%以上的原因来自毛刺、磕碰伤。
有的工厂在齿轮箱装配前,去除毛刺及磕碰伤,是一种被动的做法。
⑴齿轮轴类零件,滚齿后齿部立即套上专用的塑料保护套后转入下道工序,并带着专用的塑料保护套入库和发货。
⑵进行珩齿工艺,降低齿面粗糙度,去除毛刺,并防止磕碰伤,能有效地降低齿轮传动噪声。
7.采取其它材料及热处理、表面处理方式:
⑴ 可利用粉末冶金成型技术,齿轮成型后齿部高频淬火。
⑵ 采用墨铸铁,齿轮切削加工后,再进行软氮化处理。
⑶ 采用40Cr材料,齿轮切削功工后,采用软氮化处理或齿部镀铜处理。
综合所述,要根治齿轮传动噪声,齿轮材料及热处理是要本,齿坯精度是保证,齿轮精度是关键,文明生产是基础。
加工方法
1.磨齿:
IT6~IT4→IT3,Ra:
0.8~0.2μm原理:
成形法和展成法。
⑴成形法磨齿IT6~IT5,Ra:
0.8~0.4μm,用成形砂轮磨削,生
产率较高,加工精度较低,应用较少。
⑵展成法磨齿
锥面砂轮磨齿:
砂轮截面齿形为假想齿条的齿形,工件向右滚动,利用砂轮右侧面磨削第1齿槽的右侧面,从根部磨至顶部;
然后工件向左滚动,以砂轮左侧面磨削第l齿槽的左侧面,也从根部磨至顶部,当第l齿槽两侧面全部磨削完毕时,砂轮自动退离工件,工件作分度转动,然后再向右滚动,磨削第2齿槽,这样反复循环,直至磨完全部轮齿。
2.研齿:
IT7~IT6,Ra:
1.6~0.2μm设备:
研齿机。
研具:
精密的铸铁齿轮。
研磨剂:
磨粒:
220#~240#,活性润滑油特点:
与珩齿相同,只能降低表面粗糙度,不能提高齿形精度。
平行轴线研磨法:
1.过程:
研磨轮与被研齿轮的轴线平行,研磨时被研齿轮带动研磨轮作无侧隙的自由啮合运动,被研齿轮还作轴向往复运动,研磨轮被轻微制动。
经一段时间后,研磨轮和被研磨轮作反向旋转,使齿的两个侧面被均匀研磨。
2.特点:
由于齿面的滑动速度不均匀,研磨量也不均匀,在齿顶及齿根部分的滑动速度大,研磨量也大。
蜗杆传动
蜗杆传动是在空间交错的两轴间传递运动和动力的一种传动,两轴线间的夹角可为任意值,常用的为90°
。
蜗杆传动用于在交错轴间传递运动和动力。
蜗杆传动简介
蜗杆传动由蜗杆和涡轮组成,一般蜗杆为主动件。
蜗杆和螺纹一样有右旋和左旋之分
,分别称为右旋蜗杆和左旋蜗杆。
蜗杆上只有一条螺旋线的称为单头蜗杆,即蜗杆转一周,涡轮转过一齿,若蜗杆上有两条螺旋线,就称为双头蜗杆,即蜗杆转一周,涡轮转过两个齿。
圆柱蜗杆传动简介
圆柱蜗杆传动是蜗杆分度曲面为圆柱面的蜗杆传动。
其中常用的有阿基米德圆柱蜗杆传动和圆弧齿圆柱蜗杆传动。
①阿基米德蜗杆的端面齿廓为阿基米德螺旋线,其轴面齿廓为直线。
阿基米德蜗杆可以在车床上用梯形车刀加工,所以制造简单,但难以磨削,故精度不高。
在阿基米德圆柱蜗杆传动中,蜗杆与蜗轮齿面的接触线与相对滑动速度之间的夹角很小,不易形成润滑油膜,故承载能力较低。
②弧齿圆柱蜗杆传动是一种蜗杆轴面(或法面)齿廓为凹圆弧和蜗轮齿廓为凸圆弧的蜗杆传动。
在这种传动中,接触线与相对滑动速度之间的夹角较大,故易于形成润滑油膜,而且凸凹齿廓相啮合,接触线上齿廓当量曲率半径较大,接触应力较低,因而其承载能力和效率均较其他圆柱蜗杆传动为高。
蜗杆和蜗轮结构
一般蜗杆与轴制成一体,称为蜗杆轴。
蜗轮的结构型式可分为
3种形式。
①整体式:
用于铸铁和直径很小的青铜蜗轮。
②齿圈压配式:
轮毂为铸铁或铸钢,轮缘为青铜。
③螺栓联接式:
轮缘和轮毂采用铰制孔,用螺栓联接,这种结构装拆方便。
蜗杆传动应用
蜗杆传动常用于两轴交错、传动比较大、传递功率不太大或间歇工作的场合。
当要求传递较大功率时,为提高传动效率,常取Z1=2~4。
此外,由于当γ1较小时传动具有自锁性,故常用在卷扬机等起重机械中,起安全保护作用。
它还广泛应用在机床、汽车、仪器、冶金机械及其它机器或设备中,其原因是因为使用轮轴运动可以减少力的消耗,从而大力推广。
蜗杆传动设计
这种传动由于具有结构紧凑、传动比大、传动平稳以及在一定的条件下具有可靠的自锁性等优点,它广泛应用在机床、汽车、仪器、起重运输机械、冶金机械及其它机器或设备中。
蜗轮蜗杆的形成
蜗杆蜗轮传动是由交错轴斜齿圆柱齿轮传动演变而来的。
小齿轮的轮齿分度圆柱面上缠绕一周以上,这样的小齿轮外形像一根螺杆,称为蜗杆。
大齿轮称为蜗轮。
为了改善啮合状况,将蜗轮分度圆柱面的母线改为圆弧形,使之将蜗杆部分地包住,并用与蜗杆形状和参数相同的滚刀范成加工蜗轮,这样齿廓间为线接触,可传递较大的动力。
蜗杆蜗轮传动的特征:
其一,它是一种特殊的交错轴斜齿轮传动,交错角为∑=90°
,z1很少,一般z1=1~4;
其二,它具有螺旋传动的某些特点,蜗杆相当于螺杆,蜗轮相当于螺母,蜗轮部分地包容蜗杆。
8.1.2蜗杆传动的类型
按蜗杆形状的不同可分:
1.圆柱蜗杆传动-普通圆柱蜗杆(阿基米德蜗杆、渐开线蜗杆、法向直廓蜗杆、锥面包络蜗杆)和圆弧蜗杆
2.环面蜗杆传动
3.锥蜗杆传动
蜗杆传动由蜗杆相对于蜗轮的位置不同分为上置蜗杆和下置蜗杆传动。
普通圆柱蜗杆传动的基本参数及其选择
1.基本参数:
(1)模数m和压力角α:
在中间平面中,为保证蜗杆蜗轮传动的正确啮合,蜗杆的轴向模数ma1和压力角αa1应分别相等于蜗轮的法面模数mt2和压力角αt2,即
ma1=mt2=m αa1=αt2
蜗杆轴向压力角与法向压力角的关系为:
tgαa=tgαn/cosγ
式中:
γ-导程角。
(2)蜗杆的分度圆直径d1和直径系数q
为了保证蜗杆与蜗轮的正确啮合,要用与蜗杆尺寸相同的蜗杆滚刀来加工蜗轮。
由于相同的模数,可以有许多不同的蜗杆直径,这样就造成要配备很多的蜗轮滚刀,以适应不同的蜗杆直径。
显然,这样很不经济。
为了减少蜗轮滚刀的个数和便于滚刀的标准化,就对每一标准的模数规定了一定数量的蜗杆分度圆直径d1,而把及分度圆直径和模数的比称为蜗杆直径系数q,即:
q=d1/m
常用的标准模数m和蜗杆分度圆直径d1及直径系数q,见匹配表。
(3)蜗杆头数z1和蜗轮齿数z2
蜗杆头数可根据要求的传动比和效率来选择,一般取z1=1-10,推荐z1=1,2,4,6。
选择的原则是:
当要求传动比较大,或要求传递大的转矩时,则z1取小值;
要求传动自锁时取z1=1;
要求具有高的传动效率,或高速传动时,则z1取较大值。
蜗轮齿数的多少,影响运转的平稳性,并受到两个限制:
最少齿数应避免发生根切与干涉,理论上应使z2min≥17,但z2<26时,啮合区显著减小,影响平稳性,而在z2≥30时,则可始终保持有两对齿以上啮合,因之通常规定z2>28。
另一方面z2也不能过多,当z2>80时(对于动力传动),蜗轮直径将增大过多,在结构上相应就须增大蜗杆两支承点间的跨距,影响蜗杆轴的刚度和啮合精度;
对一定直径的蜗轮,如z2取得过多,模数m就减小甚多,将影响轮齿的弯曲强度;
故对于动力传动,常用的范围为z2≈28-70。
对于传递运动的传动,z2可达200、300,甚至可到1000。
z1和z2的推荐值见下表
i=z2/z1
z1
z2
≈5
6
29—31
7—15
4
29—61
14—30
2
29—82
1
(4)导程角γ
蜗杆的形成原理与螺旋相同,所以蜗杆轴向齿距pa与蜗杆导程pz的关系为pz=z1pa由下图可知:
tanγ=pz/πd1=z1pa/πd1=z1m/d1=z1/q
导程角γ的范围为3.5°
一33°
导程角的大小与效率有关。
导程角大时,效率高,通常γ=15°
-30°
并多采用多头蜗杆。
但导程角过大,蜗杆车削困难。
导程角小时,效率低,但可以自锁,通常γ=3.5°
一4.5°
(5)传动比I
传动比 i=n主动1/n从动2
蜗杆为主动的减速运动中
i=n1/n2=z2/z1=u
n1-蜗杆转速;
n2-蜗轮转速。
减速运动的动力蜗杆传动,通常取5≤u≤70,优先采用15≤u≤50;
增速传动5≤u≤15。
普通圆柱蜗杆基本尺寸和参数及其与蜗轮参数的匹配表。
8.2.2蜗杆传动变位的特点
蜗杆传动变位
变位蜗杆传动根据使用场合的不同,可在下述两种变位方式中选取一种。
1)变位前后,蜗轮的齿数不变(z2'
=