60T锅炉氧化镁法技术方案60吨文档格式.docx
《60T锅炉氧化镁法技术方案60吨文档格式.docx》由会员分享,可在线阅读,更多相关《60T锅炉氧化镁法技术方案60吨文档格式.docx(16页珍藏版)》请在冰豆网上搜索。
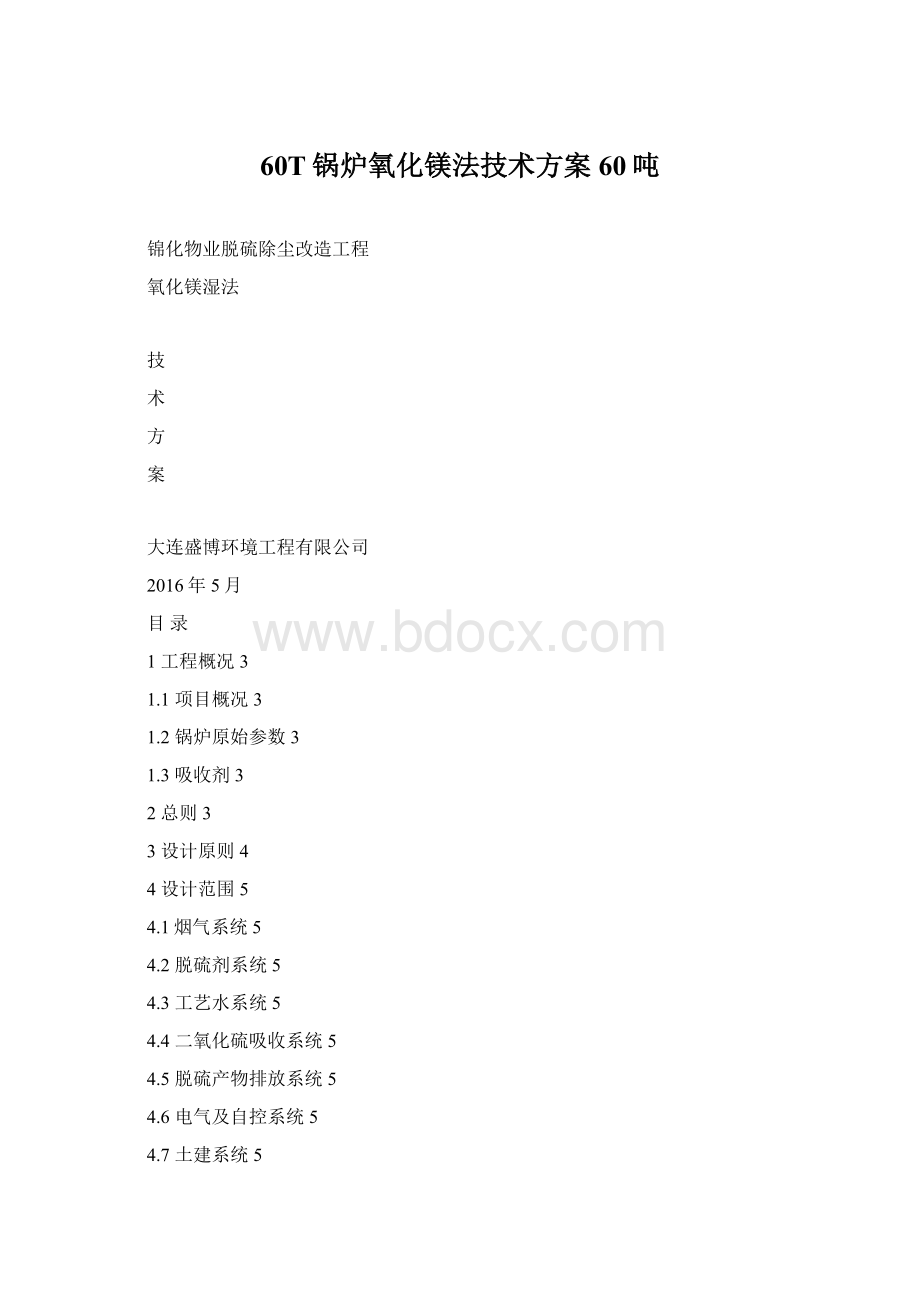
脱硫工艺采用氧化镁湿法烟气脱硫技术,二机一塔,共1套脱硫除尘系统。
除尘工艺采用布袋除尘器,因该项目为改造项目,原引风机为变频风机,风量能满足要求,压头最大可调到3115Pa,克服整套脱硫除尘阻力,无法满足要求。
故可通过更换电机,提高电机转速,基本满足脱硫系统的工况要求。
用来克服脱硫除尘装置和烟道的阻力,在保证脱硫系统稳定运行的同时,也确保了脱硫系统不影响供热锅炉主机的生产。
本脱硫除尘工艺保证不超过《锅炉大气污染物排放标准》GB13271-2014的要求。
实现SO2年减排量80吨。
本装置脱硫率可以达到98%,出口烟气SO2浓度≤300mg/Nm3,烟尘浓度≤50mg/Nm3。
1.2锅炉原始参数
1.2.160T吨热水锅炉烟气参数
项目
类别
参数
锅炉
蒸发量
20+60t/h
数量
各1台(20t/h为备用)
燃煤
产地
(设计煤种)
燃煤量
10.29t/h
应用基含硫量
0.50%
应用基灰份
18%
烟气参数(额定负荷)
烟气流量
150000m3/h
烟气温度
130℃
SO2排放浓度
1180mg/Nm3
1.3吸收剂
吸收剂制浆方式采用外购MgO粉末,在混合池内加入恒温热水进行熟化,制成浆液。
混合池为混凝土结构,作业一个班次能满足脱硫系统24小时使用。
熟化好的氢氧化镁溶液打入氢氧化镁储罐。
2总则
2.1本技术条件适用于20t/h+60t/h(20t/h做为备用)供热锅炉尾部烟气脱硫除尘系统配套的主辅系统及其设备。
它提出了该系统的功能、设计、结构、性能、土建、安装和试验等方面的技术要求;
2.2本方案提出的为最低限度的技术要求,并未对一切技术细节作出规定。
也未充分引述有关的标准和规范的条文;
2.3脱硫工艺采用成熟的氧化镁脱硫技术。
脱硫系统的设计脱硫效率应满足当前国家排放标准要求,并考虑满足今后10~15年内不断趋于严格的SO2排放标准。
供方保证提供符合国家标准和需方要求的优质产品及其相应的服务,对国家有关安全、环保、劳卫、消防等强制性标准保证满足国家有关要求;
2.4本技术条件所使用的标准如遇与需方所执行的标准发生矛盾时,按较高标准执行;
2.5脱硫工程的设计结合现场的场地条件,力求使流程和布置紧凑、合理。
2.6本工程采用氧化镁湿法脱硫方式。
供方采用该技术对整个脱硫系统进行设计;
包括整个脱硫系统正常运行所必需具备的工艺系统、设备选择、采购、运输、制造及安装等的设计、施工、调试、试验及检查、试运行、考核验收、培训和最终交付投产等;
2.7供方对供货范围中的烟气脱硫系统成套系统内设备(含辅助系统与设备)负有全责;
2.8供方保证满足需方提出的自备供热锅炉尾部的脱硫岛设计参数;
3设计原则
3.1适应煤种变化,用户可根据煤种含硫量的高低,通过调整脱硫剂的使用量,达到最佳的脱硫效果;
3.2脱硫系统在锅炉工况(50~110%)变化的条件下能够正常工作,确保烟气治理系统的安全、稳定运行;
3.3采用氢氧化镁法脱硫工艺,脱硫效率可达≥98%,SO2排放浓度≤200mg/Nm3,水分≤75mg/Nm3;
3.4脱硫工程的设计应结合现场的场地条件,力求使流程和布置紧凑、合理。
采用1台20t/h,1台60t/h锅炉两炉一塔的配置方式;
3.5脱硫系统设置100%烟气旁路,保证脱硫装置在任何情况下不影响供热机组的安全运行,脱硫系统设有可靠的保护系统,以避免因系统的故障引起脱硫塔内装置的损坏;
3.6反应后的浆液经排浆泵排入本热力站现有冲灰水系统。
脱硫后的净烟气从烟囱排放。
3.7脱硫系统控制采用DCS系统。
采用烟气在线自动监测系统,对脱硫后的烟气二氧化硫含量进行连续实时监控(由需方自行负责);
3.8脱硫工艺应尽可能节约能源和水源,尽可能降低脱硫系统的投资与运行费用;
3.9脱硫塔采用喷淋空塔,整套脱硫系统阻力小于<
1200Pa;
3.10在设备及管道运行中溢流、冲洗和清扫过程中产生的废水(例如:
氧化镁浆液或副产品浆液系统设备与管道等)收集在脱硫装置的事故坑内,然后送至吸收塔系统中重复利用,不直接排放;
3.11选用质量可靠、能耗低的机电设备及性能优异、价格适宜的专用设备,尽可能降低系统的运行费用;
3.12脱硫后没有二次污染,保持原有清洁干净的厂貌。
4设计范围
4.1烟气系统
烟气系统从除尘器烟气出口至烟囱水平烟道入口。
主要包括烟道、旁路、挡板门、密封系统。
4.2脱硫剂系统
脱硫剂系统从氧化镁混合池入口至氢氧化镁储罐出口。
4.3工艺水系统
工艺水系统从工艺水箱入口法兰外一米以内为界。
4.4二氧化硫吸收系统
二氧化硫吸收系统从吸收塔烟气入口至吸收塔烟气出口。
4.5脱硫产物排放系统
脱硫产物处理系统从吸收塔排浆泵出口口至冲灰沟。
4.6布袋除尘系统
布袋除尘器系统从锅炉出口烟道至引风机入口。
4.7电气及自控系统
4.8土建系统
脱硫系统范围内所有设备基础及土建由供方设计,由需方负责施工。
5规范和标准
5.1供方的系统功能设计、结构、性能、制造、建筑、供货、安装、调试、试运行等采用以下所列的国家最新版本标准。
5.2环境保护、劳动卫生和消防设计采用中华人民共和国标准。
5.3供方在设计、制造、建筑、安装、调试、试运行中执行的初步标准清单附后,若在合同执行过程中有新的标准颁布按新的标准执行。
5.4脱硫系统及其配套辅机设计、制造、检验原则上采用中国现行规范和标准,但凡按引进技术设计制造的设备,均按引进技术相应的标准及规范进行设计、制造、安装、施工、检验。
若供方使用的规范及标准与本技术规范所用标准发生矛盾时,按较高标准执行。
设计标准
GB13271-2014《锅炉大气污染物排放标准》
DL/T5196-2004《火力发电厂烟气脱硫设计技术规程》
DL5000-2000《火力发电厂设计技术规程》
GB4053.4-93 《固定式工业钢平台》
GB50054-95 《低压配电设计规范》
NDGJ5-88《火力发电厂水工设计技术规定》
设备标准
GB/T8163-1999《流体输送用无缝钢管》
GB10889-89《泵的振动测量与评价方法》
GB2649-89《焊接接头机械性能试验取样办法》
GB3214-91《水泵流量测定方法》
GB50229-96《火力发电厂与变电所设计防火规范》
GB8162-1999《结构用无缝钢管尺寸外形重量及允许偏差》
GB912-89《普通碳素结构钢和低合金结构钢薄板技术条件》
GB50055-93《通用用电设备配电设计规范》
JB/T4735-1997《钢制焊接常压容器》
验收标准
GB50235-97《工业金属管道工程施工及验收规范》
GB50268-1997《给水排水管道工程施工及验收规范》
GB50205-95《钢结构工程施工及验收规范》
6技术方案
6.1方案介绍
本工艺是针对大连锦化物业20t/h+60t/h(20t/h锅炉作为备用)供热锅炉进行烟气脱硫除尘,带有大量粉尘和二氧化硫的烟气从锅炉出口烟道排出,然后进入布袋除尘器,经除尘器脱下的粉煤灰通过除尘器下的卸灰阀经加湿机加湿后由推车统一外排至渣场,脱尘后的含硫烟气经引风机增压后,进入脱硫塔进行脱硫。
脱硫采用氧化镁湿法脱硫工艺。
现将脱硫工艺流程叙述如下:
来自投料口的氧化镁粉自混和池顶部的投料口加入与来自工艺水管网的工艺水、来自厂区管网的热水在混和池内混合熟化,熟化浆液流至储存池,利用储存罐中的供浆泵将脱硫浆液送往吸收塔;
脱硫浆液进入吸收塔后,经塔外循环泵循环,送入喷嘴进行喷淋,与从下而上的烟气进行逆向接触,充分进行化学反应,生成MgSO3。
再鼓入空气氧化MgSO3,使之生成MgSO4。
反应后的浆液经排浆泵排入锅炉厂现有冲灰水系统,直接做为冲灰水使用。
脱硫后的净烟气从吸收塔上方的烟道排至烟囱。
6.2工艺原理
氢氧化镁法脱硫工艺采用Mg(OH)2吸收烟气中的SO2,得到含结晶水的以亚硫酸镁为主的产物,通过曝气氧化系统将亚硫酸镁氧化成硫酸镁固体,经过初步沉淀后通过排污泵排放。
主要发生的化学反应如下:
(1)制浆:
MgO+H2O→Mg(OH)2(浆液)
Mg(OH)2→Mg2++2OH—
(2)吸收:
Mg(OH)2+SO2+5H2O→MgSO3·
6H2O↓
MgSO3+SO2+H2O→Mg(HSO3)2↓
Mg(HSO3)2+Mg(OH)2+10H2O→2MgSO3·
(3)强制氧化:
MgSO3+1/2O2+7H2O→MgSO4·
7H2O↓
Mg(HSO3)2+1/2O2+6H2O→MgSO4·
7H2O↓+SO2
6.3系统介绍
氢氧化镁法脱硫除尘工艺主要由烟气系统、除尘系统、吸收剂系统、工艺水系统、二氧化硫吸收系统、脱硫产物排放系统和电气自动控制系统。
6.3.1除尘系统
本套除尘系统每台锅炉设置一台布袋除尘器,除尘器的除尘效率满足烟气出口含尘浓度≤50mg/Nm3。
除尘系统阻力为≤1500Pa,除尘采用低压脉冲喷吹清灰。
滤袋使用寿命不小于2年,袋长采用6米滤袋,滤袋材质为PPS+PTFE。
6.3.2烟气系统
本项目中,供热锅炉烟气经布袋除尘器除尘后进入引风机、通过引风机送入脱硫塔内。
脱硫除尘后的锅炉烟气由脱硫系统出口挡板门进入出口净烟道,最终由烟囱排入大气。
锅炉正常运行时,其脱硫系统亦同时运行,只在特殊情况及故障情况时允许脱硫系统被旁通,此时锅炉在无脱硫装置的情况下(烟气通过旁通烟道)运行。
正常运行时,无论脱硫装置处于何种工况下运行都不会对供热机组产生影响。
吸收塔低负荷运行时,可按吸收塔特性停运一层喷嘴。
脱硫系统投运时,系统的进、出口挡板门打开,通往烟囱的旁通烟道挡板门关闭。
在锅炉启动过程中或脱硫系统解列、需要检修时,脱硫系统进、出口挡板门关闭,旁通烟道挡板门打开,机组烟气经引风机和旁通烟道直接进入烟囱排出。
本系统中烟道挡板门采用优质百叶窗双层密封挡板门。
脱硫塔出口配置一台出口烟气挡板门。
挡板门配置完善的密封风系统。
烟道留有适当的取样接口、试验接口和人孔
6.3.3吸收剂系统
脱硫剂系统包括脱硫剂存储及浆液制备和浆液输送三部分。
(1)脱硫剂存储
脱硫剂采用氧化镁。
袋装脱硫剂(纯度为85%的氧化镁)由市场采购,采用50kg编织袋装,纯度≥85%,储存的吸收剂可供本锅炉脱硫装置使用10天。
(2)浆液制备
氧化镁直接倒入混合池内。
混合池采用采用混凝土结构,混合池内将氧化镁和热水按一定比例搅拌配置成一定浓度的浆液。
锅炉余热废水,接管引入浆液制备系统,热水流量根据管道上的流量计显示通过调节阀门开度进行调节。
熟化后的氢氧化镁溶液通过输送管道送入氢氧化镁储罐。
氢氧化镁储罐采用钢结构,内部设置必要的防腐涂层。
考虑到储罐内介质性质及存储时间,在罐内设置搅拌器,以防止氢氧化镁沉淀。
同时设置液位开关,对罐内液位进行监控。
控制信号进入脱硫DCS控制系统内。
(3)浆液输送
储存在氢氧化镁储罐内的浆液通过碱液泵送至脱硫塔内。
碱液泵设置三台,两用一备。
碱液的量按镁硫比通过碱液泵出口调节阀进行调节。
碱液的量通过智能电磁流量计显示,并将信号送入脱硫DCS控制系统。
6.3.4工艺水系统
工艺水主要包括两部分,一部分是消化制浆耗水,主要来之锅炉冷却水;
另一部分是除雾器冲洗及脱硫塔补充水,主要来至厂区供水管网。
工艺水设置一台水箱,存储冷水。
水箱采用钢结构,材质为普通碳钢。
箱内设置液位计对箱内水位进行监控。
除雾器冲洗水采用三台泵,其中两用一备。
通过冲洗水量调节脱硫系统总流量。
氧化镁熟化用水采用锅炉冷却水。
熟化用水水量通过智能电磁流量计进行监控,同时流量信号送入脱硫DCS控制系统。
6.3.5二氧化硫吸收系统
二氧化硫吸收系统是烟气脱硫系统的核心,主要包括吸收塔、喷嘴、除雾器和浆液循环泵等设备。
在吸收塔内,烟气中的SO2被脱硫剂浆液洗涤并与浆液中的Mg(OH)2发生反应,最终生成亚硫酸镁晶体,循环泵将反应液反复送入吸收塔,以提高吸收反应的效率。
达到一定浓度的亚硫酸镁浆液由废液排出泵送入冲灰水系统中(副产品也可处理浓缩脱水,外销做复合肥)。
在吸收塔的上部设有除雾器,以除去脱硫后烟气带出的细小液滴,使烟气在含液滴量低于75mg/Nm3下排出。
本脱硫工程配置一座逆流式喷淋吸收塔。
二炉一塔。
吸收塔布置在引风机之后,正压运行。
当脱硫系统解列或出现事故停机需要检修时,吸收塔内的吸收浆液由吸收塔低排污阀排出,存入地坑中,以备再次启动之用。
(1)吸收塔
空塔喷淋吸收塔主体为圆柱形塔、碳钢衬玻璃磷片,吸收塔底部为浆液池,上部分为喷淋层和除雾器两部分。
塔体内配置有多个高效喷嘴及高效除雾装置,浆液在吸收塔内通过高效雾化喷嘴雾化,形成良好的气液接触反应界面,烟气进入塔内之后,在塔内匀速上升,与雾状喷液进行全面高效混合接触,脱除SO2等酸性气体。
带雾点的烟气上升至高效除雾装置时,通过除雾装置的作用,气液进行接触二次吸收并同时得到有效分离,从而避免烟气夹带雾沫,最大限度地减少烟气带水现象。
吸收塔塔体材料采用钢衬玻璃鳞片,直径3.2米,塔高18m。
。
在脱硫塔的进、出口烟道上设置挡板门和旁路系统,以保证当脱硫系统检修停运或事故时不影响锅炉的连续、安全、稳定运行;
所有的烟气挡板门易于操作,在最大压差的作用下具有较好的严密性。
烟道系统地走向做到经济合理简洁、减小管道系统阻力并便于挡板门的操作和检修。
烟道和支架结构采用钢结构,外表面防锈油漆。
1.1.1废水处理系统
由于本期脱硫副产物较少,按抛弃处理,吸收塔排放的浆液由浆液排放泵排入到灰渣缓冲池,进入该厂现有冲灰水系统中或(由肥料厂家来直接回收,制作复合肥)。
1.1.1排放系统
本工艺需充一个事故浆液坑,以便于吸收塔检修或事故状态下,塔内浆液由浆液排放泵排空至事故坑中。
检修完成或故障排除后,坑内的浆液由泵送回到吸收塔中,节约了吸收剂并防止了浆液外排时对环境造成污染。
另外通过排水沟收集循环泵、浆液排放泵停运冲洗时的浆液和设备密封水,并可由吸收塔排水坑泵打到吸收塔,达到循环利用、节约用水。
(2)喷淋层
脱硫塔采用喷淋空塔;
脱硫塔内部喷淋系统由分配管网和喷嘴组成。
喷淋系统合理分布要求的喷淋量,使烟气流向均匀,并确保脱硫液与烟气充分接触和反应。
(3)除雾器
采用折流板除雾器,材质为增强阻燃聚丙烯(PP)。
在脱硫塔上部设置两层除雾器,有效地捕集脱硫后烟气中携带的液滴,保证100%工况脱硫经除雾器后烟气液滴浓度小于75mg/Nm3;
在除雾器上设置有冲洗装置,定时、定压冲洗。
(4)循环泵
一套脱硫系统配备3台脱硫循环泵。
每个喷淋层单泵控制。
以便根据锅炉负荷分别控制循环浆液量。
循环泵可变频调节,系统可根据锅炉负荷、煤含硫量、烟气出口SO2浓度、烟气温度进行调节,得到系统最优化的运行参数,做到节能运行。
循环泵采用引进技术材料和引进技术生产的耐磨耐腐蚀全金属卧式离心泵。
密封形式采用机械密封。
(5)设备阻力
脱硫系统阻力为1700Pa,如果现有引风机压力满足,可利用现有引风机的余压。
在脱硫装置运行时关闭旁路挡板门,打开脱硫进口挡板门,脱硫出口挡板门,在脱硫装置停运时,打开旁路挡板门,切换到原有系统,不影响锅炉的正常运行。
6.3.5电气自动控制系统
我方提供的低压柜采用先进的GCK柜型,功率较大的电机设置低压电动机保护装置。
设置就地控制箱,就地控制箱必须有起停开关、指示灯、转换开关、电流表等。
电机的防护等级至少为室外IP54。
电缆通道结合现场情况采用电缆沟和架空桥架,桥架采用渡锌电缆桥架。
脱硫控制系统采用重要参数自动调节,使脱硫电气系统能独立运行,又能与其他系统相兼容。
系统具有中等自动控制水平,系统所采用电气元器件均为国内外知名品牌,保证系统可靠性。
控制系统监控的主要内容有以下几点:
工艺运行状态的监测,主要采集与处理现场测量仪表的信号。
根据工艺对控制系统的要求,通过调节回路进行自动调控,使脱硫系统运行在正常的工况状态下。
控制电气设备运行工况,对马达控制中心(MCC)的开关量和模拟量信号进行采集处理,判断设备的运行状态。
通过通信网络连接到主控室DCS主控系统,进行规约转换,完成对锅炉负压的监控。
据工艺设计要求和现场实际条件,对系统进行连锁操作控制,保证系统安全运行。
完成温度、压力、流量、液位等参数的显示与报警。
6.4技术特点
6.4.1吸收剂为粉状,到厂后直接熟化成脱硫浆液,而不需进行破碎、磨粉等工序,且其用量仅相当于石灰石的40%,因而脱硫剂制备系统大大简化。
6.4.2由于镁基溶液的碱性比钙基高数百倍,吸收反应所需水量(即液/气比值)仅为钙基脱硫的1/3-1/6,而且吸收反应强度更高,脱硫效率可达到99%,其吸收塔的高度显著低于石灰石脱硫塔,其循环液量也大大减小,电耗不到石灰石/石膏法工艺的一半。
6.4.3镁基脱硫的副产品不易粘结、结垢,因而避免了石灰石脱硫过程中常发生的结垢、堵塞等运行困难。
6.4.4对煤种变化的适应性强。
无论是含硫量大于3%的高硫煤,还是含硫量低于1%的低硫煤,镁基湿法脱硫工艺都能适应。
当锅炉煤种变化时,可以通过调节镁硫比、液气比和pH值等手段以保证达到系统设计的脱硫率;
6.4.5脱硫副产品(MgSO3和MgSO4)具有更高的利用价值.MgSO3可以进一步用来生产硫酸并将MgO再生还原,MgSO4用于镁肥,在美、日、德等国都有成功的工业化生产实绩。
7设计参数一览表
序号
单位
脱硫系统
备注
1
锅炉负荷
t/h
60+20
20t/h的做为备用
2
10.29
3
含硫量
%
0.5
4
烟气量
m3/h
150000
5
排烟温度
℃
140
6
标况烟气量
Nm3/h
99300
7
年脱去二氧化硫流量
t/a
80
8
入口二氧化硫浓度
mg/Nm3
1180
10
要求二氧化硫排放浓度
≤300
11
二氧化硫去除量
kg/h
52.8
12
吸收剂耗量
40.38
纯度85%
吸收剂费用
元/h
20.2
500元/吨
13
产渣量
379
干态
14
塔径
m
3.2
15
系统阻力
Pa
≤1500
16
系统耗电量
Kw·
h
120
电费
69.6
0.58元/度
17
工艺水耗量
水费
1.0元/吨
18
设备及布袋维修费
万元/a
18.23
运行费用
224
万元/年
34.0
1520h/a计
7供货范围
7.1供货范围
本工程供货范围为除尘器入口接入至脱硫后净烟气吸再到原烟道(含进、出口和旁路挡板门、非金属膨胀节)的全套脱硫除尘装置,包括设计、制造、安装、调试、(168小时)试运行(供方提供土建设计以及桩基的设计,由需方负责土建施工以及桩基的处理),调试、试运行期间的水、电、和脱硫剂等消耗材料由需方负责。
包括所有电缆及电缆桥架等系统的材料及安装。
接口界限:
除尘系统:
入口:
从现有除尘器入口烟道口开始。
出口:
到引风机入口烟道接口。
副产品:
以粉尘加湿搅拌机出口为界;
烟气
从汇合原烟道上烟气入口开始,含脱硫入口烟道挡板门及旁边路挡板门。
到原烟囱净烟气出口,含出口烟道挡板门。
以制出副产品出口为界;
氧化镁粉
进口:
氧化镁粉仓进口管接口(以内)。
工艺水:
工艺水箱接入口(法兰)外一米(以内)为界。
工艺废水
废水排放泵出口。
压缩空气
由供方负责
电气(电源):
以需方低压开关柜出线端子为界;
其他以设备接入口(法兰)外一米(以内)为界。
控制系统
脱硫除尘系统范围内控制设备。
包括提供脱硫除尘系统控制信号与主控室主控制系统接口。
8安全生产、环境保护、消防及节能
8.1安全生产
本装置在制作安装过程中,严格遵照OHSAS18001:
2001职业安全健康管理体系要求,执行安全生产管理制度与安全工程措施:
(1)执行国家有关安全生产和劳动保护的法规,建立安全生产责任制,加强规范化管理,进行安全交底、安全教育和安全宣传,严格执行安全技术方案。
(2)现场铺设施工电缆和电器应遵守全国通用的规则和标准。
(3)采取一切适当预防措施保证所有工作场所安全可靠,在进行施工平面图设计时充分考虑安全、防火、防爆、防污染等因素,做到各种设施布局合理。
使整个工作场所不存在可能危及工人安全与健康的危险。
此外,在制作安装期及运行管理期,为了保证安全生产,使职工自觉遵守安全生产中的各项章程,具体内容如下:
①根据施工现场编制和执行各种有安全生产管理制度以及安全责任制;
②对全体职工进行安全教育培训,事故和偶发事件的分析;
③制定安全工作操作规程;
④成立项目部安全委员会;
⑤制定应急预案;
⑥定期经常对所有职工作医疗检查;
⑦颁发和使用安全防护用品如安全帽、鞋、工作服等。
8.2环境保护
烟气脱硫工程本身是治理环境污染的基础设施,但由于污染物相对集中,在处理过程中若不加妥善处理,会对环境产生不良影响。
本公司严格遵照ISO14001:
1996环境管理体系要求,在工程中对现场环境因素及施工人员环境保护意识加强管理,确保工程不造成二次污染。
本工程环境保护包括两个方面,即在工程建设过程中和建成投产之后。
(1)工程建设中的环境保护
在工程建设过程中,施工机械引发的噪声、输送建材对交通产生的影响、施工过程中产生的污染等,这些影响应采取适当的措施予以解决:
①合理规划施工活动,以保证对社会最小干扰;
②选择适当的路线运送材料和设备;
③设置警告讯号,道路封闭时按需进行交通管理,以保证正常进行和减少交通障碍;
④尽量减少大面积埋管、开挖沟槽等,并在施工场地设置标志,防止无关人员进入;
⑤限制场地施工范围,能满足工程需要即可;
⑥所有车辆和设备