精品云南雄业水泥4465MW余热发电项目可研报告Word文档下载推荐.docx
《精品云南雄业水泥4465MW余热发电项目可研报告Word文档下载推荐.docx》由会员分享,可在线阅读,更多相关《精品云南雄业水泥4465MW余热发电项目可研报告Word文档下载推荐.docx(27页珍藏版)》请在冰豆网上搜索。
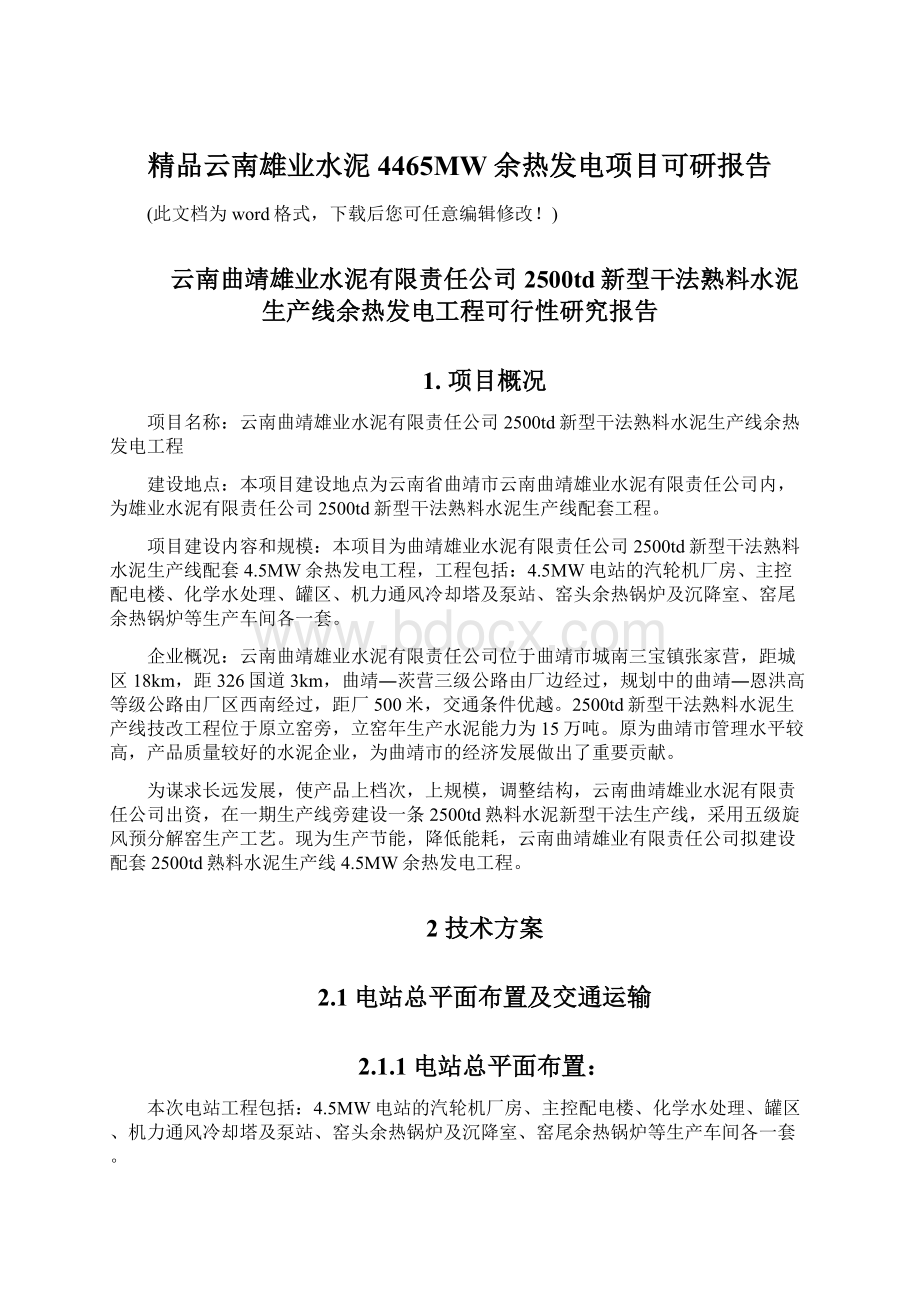
2
建、构筑物占地面积
1090
3
建筑系数
%
26.1
4
绿化系数
28.3
5
绿化面积
1189
2.2热力系统及装机方案
2.2.1热力系统及装机方案设计前提
根据2500td水泥生产线的废气情况,热力系统及装机方案应考虑下述前提条件:
1)充分利用2500td水泥生产线窑头熟料冷却机及窑尾预热器废气余热。
为充分利用窑头熟料冷却机废气余热,提高窑头余热锅炉的烟气温度,使之产生与窑尾余热锅炉相同参数的过热蒸汽,因此对窑头熟料冷却机进行改造,取用其中段废气余热。
根据公司提供的数据水泥生产线废气可利用的余热量为:
a.经过技术改造后实际2500td水泥生产线窑头熟料冷却机中部废气余热为105000m3h(标况)-350℃~206℃。
具有约3303×
104kJh的热量
b.窑尾预热器废气余热为173000m3h(标况)-330℃~206℃(排出的废气考虑用于生料烘干该温度值由水泥工艺确定),具有约3478×
104kJh的热量。
2)本工程实施后电站不应向电网返送电;
3)本纯余热电站的建设及生产运行应不影响水泥生产系统的生产运行;
4)本纯余热电站的系统及设备应以成熟可靠、技术先进、节省投资、提高效益为原则,并考虑目前国内余热发电设备实际技术水平。
5)烟气通过余热锅炉沉降下来的窑灰应回收并用于水泥生产以达到资源综合利用及环境保护的目的。
2.2.2热力系统方案及装机容量
根据目前国内纯余热发电技术及装备现状,结合水泥窑生产线余热资源情况,并根据本工程项目建议书确定的装机规模,本工程装机方案采用纯低温余热发电技术。
综合考虑目前水泥生产线窑头、窑尾的余热资源分布情况和水泥窑的运行状况,在充分利用余热的前提下,以“稳定、可靠、技术先进、不影响水泥生产”为原则,确定热力系统及装机方案如下:
本系统主机包括两台余热锅炉及一套凝汽式汽轮发电机组,装机容量为4.5MW。
在水泥窑窑头熟料冷却机中部的废气出口与窑头废气袋收尘器间设余热锅炉一台,即AQC炉。
保留冷却机原有烟道作为AQC炉低温段的排风烟道,当AQC炉故障检修时,水泥烧成系统可以继续运行,不影响水泥线的正常生产。
AQC炉一段生产8.09~1.35MPa-330℃的过热蒸汽,AQC炉二段生产2.1MPa-110℃的高温热水。
在窑尾预热器废气出口与窑尾高温风机间设余热锅炉一台,即SP炉。
SP炉废气设旁通烟道,当SP炉故障检修时,水泥烧成系统生产可以继续进行而不受任何影响。
SP炉生产1.25MPa~1.35MPa-310℃的过热蒸汽。
与两台余热锅炉配套,设置一台4.5MW凝汽式汽轮发电机组。
AQC炉一段、SP炉生产的蒸汽共同作为汽轮机的主进汽推动汽轮机作功,AQC炉二段生产的高温热水作为AQC炉一段、SP炉的给水,
2.2.3AQC余热锅炉
窑头熟料冷却机中间出口废气参数:
105000m3h(标况)-360℃。
此部分废气全部进入AQC余热锅炉用于发电。
AQC炉出口废气温度为100℃。
AQC炉受热面分为两段:
第一段—蒸汽Ⅰ段,生产8.09th-1.35MPa-330℃的过热蒸汽。
第二段—热水段,生产22th-2.1MPa-110℃热水用于加热汽轮机凝结水,提高AQC蒸汽段及SP锅炉的给水温度。
2.2.4SP余热锅炉
目前水泥窑尾预热器出口烟气进入高温风机后再进入生料磨,用于烘干。
同时需要进行增湿减温,造成能源浪费。
窑尾预热器出口废气参数:
173000m3h(标况)-330~206℃。
SP炉出口废气参数:
189000m3h(标况)-225℃。
SP炉出口烟气经高温风机后再进入生料磨,用于烘干。
SP炉受热面为一段:
蒸汽段,生产12.56th-1.35MPa-310℃的过热蒸汽。
2.2.5热力系统
根据热力计算及主机配置情况确定热力系统如下:
汽轮机凝结水经凝结水泵送入真空除氧器,再经给水泵为窑头熟料冷却机AQC余热锅炉热水段提供给水,热水段的出水作为AQC锅炉蒸汽Ⅰ段及SP锅炉的给水。
AQC余热锅炉蒸汽I段生产的1.35MPa的过热蒸汽与SP余热锅炉生产的同参数的过热蒸汽汇合后进入汽轮机用于发电。
汽轮机做功后的乏汽通过冷凝器冷凝成水,经凝结水泵送入真空除氧器,从而形成完整的热力循环系统。
上述方案的配置,可以使电站运行方式灵活、可靠,能很好地与水泥生产配合。
具体为:
①窑头熟料冷却机余热锅炉采用两段受热面,最大限度地利用了窑头熟料冷却机废气余热。
窑头余热锅炉I段为蒸汽锅炉,生产1.35MPa-330℃的蒸汽,作为汽轮机主蒸汽,窑头余热锅炉II段为热水锅炉生产110℃的热水,作为窑头余热锅炉蒸汽段及窑尾余热锅炉的给水。
②窑尾预热器余热锅炉均采用一段受热面,保证了电站运行安全并充分保证水泥生产线烘干用废气余热。
窑尾余热锅炉为蒸汽锅炉,当水泥窑窑尾废气温度波动时,相应的窑尾余热锅炉的产汽量也随之发生变化。
窑尾余热锅炉生产的蒸汽与窑头余热锅炉蒸汽段生产的蒸汽一起进入汽轮发电机发电。
③为了保证电站事故不影响水泥窑生产,余热锅炉均设有旁通废气管道,一旦余热锅炉或电站发生事故时,可以将余热锅炉从水泥生产系统中解列,不影响水泥生产的正常运行。
④余热锅炉均采用膜式受热面立式锅炉,解决余热锅炉漏风、磨损、堵灰等问题并减少占地面积,提高余热回收率。
⑤除氧器均采用真空常温水除氧方式,有效的保证了除氧效果。
⑥由于窑头废气粉尘粒度较大,在窑头余热锅炉废气入口采用设置沉降室,使废气中较大颗粒沉降下来,以减轻熟料颗粒对窑头余热锅炉的冲刷磨损。
以上各项措施已经在众多工程中应用,并取得了较好的效果,因此该技术是成熟、可靠的。
2.2.6主要设备
根据热力系统选择及国内余热锅炉和低参数汽轮机的生产和使用情况,确定主、辅机设备如下:
设备名称及型号
数量
主要技术参数、性能、指标
4.5MW凝汽式汽轮机
型号:
额定功率:
4.5MW
额定转速:
5600rmin
主汽门前压力:
1.25MP
主汽门前温度:
360℃
排汽压力:
0.008MPa
4.5MW发电机
4.5MW
3000rmin
出线电压:
10500V
窑尾余热锅炉
入口废气量:
173000m3h(标况)
入口废气温度:
330℃
入口废气含尘浓度:
<
65gm3(标况)
出口废气温度:
225℃
产汽量:
12.56th-1.35MPa-310℃
给水参数:
16.65th-110℃
锅炉总漏风:
≤5%
布置方式:
露天
窑头余热锅炉
105000m3h(标况)
360℃
30gm3(标况)
100℃
锅炉I段(蒸汽)
蒸汽参数:
8.09th-1.35MPa-330℃
给水温度:
5.13th-110℃
II段出水参数:
21.48th-185℃
40℃
除氧器及水箱
工作压力:
0.0926MPa
工作温度:
45℃
除氧水量:
20m3
6
锅炉给水泵
(每个系统各两台)
流量:
15~30t
2.2.7电站技术经济指标:
电站年运行:
7200h
装机容量:
平均发电功率:
4.081MW
站用电率:
8%
年发电量:
2938×
104kW·
h
年供电量:
2702×
年少购电量:
2852×
h(5.27%线损)
2.3主厂房布置
主厂房包括汽轮发电机房、除氧间、中控室、高、低压配电室等。
化学水处理、循环水冷却塔及循环水泵房等车间。
主厂房占地23.4×
22.5=526.5m2,双层厂房。
汽机为岛式布置,运行层为7.500平面,气轮发电机布置在7.5.000平面上,±
0.000平面布置有给水泵、凝结水泵、油泵等;
除氧器及水箱布置在汽轮发电机房5.000平面。
2.4辅助设施
AQC余热锅炉布置在窑头厂房与窑头电收尘器的空余场地上,占地面积6.8×
8.4m2,锅炉主体布置于8.000平面上,连续排污扩容器及加药装置布置在车间周围空余场地上。
SP余热锅炉布置在窑尾厂房的空余场地上,锅炉主体布置在14.000平面上,占地面积12×
9m2,连续排污扩容器及取样装置等均布置在±
0.000平面上。
2.5电站室外管线
室外汽水管线主要有:
来自AQC及SP余热锅炉的主蒸汽管道;
由汽机房去AQC余热锅炉的给水管道以及由AQC炉至SP余热锅炉的给水管道。
管道敷设方式:
管道采用架空敷设,并尽量利用厂区现有的建筑物或构筑物做管道的支吊架以减少占地面积和节省投资。
管道保温及油漆:
管道保温采用岩棉管壳和岩棉板,管道按照设计规范和规定设计。
2.6炉灰处理
2.6.1工艺流程
本工程为纯低温余热发电,当水泥生产线窑头及窑尾废气经余热锅炉换热后,沉降下来的炉灰产量经计算为:
窑头余热锅炉平均1.08th
窑尾余热锅炉平均2.80th
该两部分炉灰均回用于水泥生产,设计中考虑采用螺旋输送机,分别将炉灰就近送回水泥生产系统。
主要设备
备注
螺旋输送机
能力:
56m3h
刚性叶轮给料机
规格:
φ300×
300
输送量:
23m3h
2.3水泥生产工艺系统与余热电站的关系
2.3.1水泥生产工艺与余热电站有着十分密切的关系,水泥生产系统的运行直接影响到余热电站的生产。
水泥生产系统的正常运行是保证余热电站安全、稳定生产的前提。
余热电站的建设能使现有水泥生产系统的运行更加完善、更加节能、更有利于环境保护。
余热电站属于公司的一个车间,除余热电站必备的设备、车间及人员外不需另设辅助设施,如机修、环保等机构。
2.3.2由于余热锅炉的设置,对水泥生产中窑头、窑尾的废气系统各增加了部分阻力,经计算,分别为800Pa和600Pa。
对风机阻力和漏风的增加,经过对窑头、窑尾高温风机的校核计算,结果均在允许的工作范围内,原系统的风机能够满足余热锅炉后的系统要求,可以不对风机进行改造。
2.3.3由于余热锅炉设置于水泥生产最主要的管道上,一旦发生事故(如锅炉爆管、粉尘堵塞等)将影响水泥生产的正常运行。
为防止这种情况发生,余热锅炉废气管道及发电系统汽水管道均考虑了应急处理措施。
2.3.4窑头余热锅炉
窑头余热锅炉废气入口采用沉降室降尘处理,以减轻熟料颗粒对锅炉的冲刷磨损,即便如此,为了避免影响正常的水泥生产,对窑头余热锅炉也采取了如下措施:
措施1:
设旁通废气管道,一旦锅炉发生事故,启用旁通废气管道。
措施2:
发电系统汽水管路考虑了将窑头余热锅炉从发电系统中解列出来的措施。
2.3.5窑尾余热锅炉
措施2:
发电系统汽水管路考虑了将窑尾余热锅炉从发电系统中解列出来的措施。
2.4循环冷却水系统
本工程是利用公司2500td水泥生产线的窑头、窑尾余热建设一套装机容量为4.5MW的纯低温余热电站。
2.4.1设计依据
2.4.2设计范围
电站生产设备冷却水系统,冷却水系统中建、构筑物设施的设计。
设备冷却用水量
凝汽器冷却水量:
1610m³
³
h)
冷油器冷却水量:
80m³
空冷器冷却水量:
100m³
锅炉给水泵冷却水量:
2m³
本工程设备冷循环却水量为:
2032m³
2.4.3设备冷却水系统方案
本工程设备冷却用水拟采用循环系统,循环冷却水系统包括循环冷却水泵、冷却构筑物、循环水池及循环水管网。
该系统运行时,循环冷却水泵自循环水池抽水送至各生产车间供生产设备冷却用水,冷却过设备的水(循环回水)利用循环水泵的余压送至冷却构筑物,冷却后的水流至循环水池,供循环水泵继续循环使用。
为确保该系统良好、稳定的运行,系统中设置了旁滤和加药装置。
本工程循环冷却水泵拟采用2台双吸离心水泵,其设置在冷却构筑物附近。
根据本工程所在地区气象条件和本工程的冷却用水量、建设场地的特点,循环冷却水构筑物拟采用2台逆流式机械通风冷却塔。
2.4.4系统损失水量与补充水量
余热发电总用水量:
49008m3d,循环用水量:
48768m3d,循环回水量:
47784m3d,循环补充水:
984m3d,(含逆流式机械通风冷却塔的蒸发、风吹、渗漏等损失、循环冷却水系统排污量、系统总损失水量),直接循环使用率可达到98%,纯水制备用水量:
240m3d。
余热发电每天实际需补充水量:
1224m3d。
2.5接入系统及电量平衡
2.5.1电站接入系统
拟建的4.5MW纯低温余热电站采用10kV单母线接线方式。
发电机组由电站10kV母线经单回电缆线路与总降10kV母线连接。
4.5MW纯低温余热电站与现有电力系统实现并网运行,运行方式为并网电量不上网。
在电站侧的发电机联络线开关和发电机出口开关处设置并网同期点。
在不改变总降原有供电及运行方式的前提下,发电机发出的电量将全部用于全厂负荷。
因此本接入系统方案,从现行的条件和技术要求来讲,对本电站工程是可行的。
2.5.2电量平衡
公司拥有的2500td新型干法生产线总用电负荷约为18000kW,预计全厂年用电量约5037×
104kWh。
该余热电站建成后,电站年总供电量约为2702×
通过电站运行调整公司用电系统功率因数并使现有供配电系统损耗减少,公司再向电网减少购电量约150×
即公司年向电网少购的总电量约为2852×
104kWh,因此在公司各生产线及电站正常运行情况下,全厂供电自给率可达50%以上,从而大大减少了公司购电成本,提高了公司的整体经济效益。
电站的运行以并网电量不上网、自发自用为原则,当各生产线因计划检修、故障停运或生产调整造成额定发电量大于全厂生产用电负荷时,电站可采取压负荷运行,以避免向电网系统返送电。
3电气及自动化
3.1编制范围
编制范围包括以下几个主要方面
1)电站的电气主结线,电站接入系统;
2)站用电配电,站用辅机控制;
3)热工自动化及计算机控制系统;
4)电站室外动力及照明配电线路;
5)车间照明、防雷及接地设计。
3.2编制依据
公司提供的设计基础资料。
3.3电气
3.3.1站用电配电
1.电压等级
发电机出线电压:
10.5kV
站用高压配电电压:
10kV
站用低压配电电压:
0.4kV
站用辅机电压:
0.38kV
站用照明电压:
380V220V
操作电压:
交流或直流:
220V
检修照明电压:
36V12V
2.站用电负荷及站用电率
站用电总装机容量:
4500kW
站用电计算负荷:
330kVA
电站年发电量:
2938×
104kWh
电站年自用电量:
236×
电站年供电量:
2702×
水泥厂年向电网少购电量:
2852×
104kWh(5.27%线损)
站用电率:
~8%
3.3.2站用变压器选择
根据站用电负荷计算结果,同时考虑电站运行的经济、可靠性,资源综合利用电站站用变压器选择二台10.5kV0.4kV,400kVA变压器。
两台变压器按互为暗备用的方式配设。
正常工作时,每台变压器的负荷率为41.25%。
当一台变压器因故障或检修退出运行时,另一台变压器的负荷率为82.5%。
3.3.3直流系统
直流系统的负荷(包括正常工作负荷和事故负荷),考虑投资、维护以及管理等费用,设计选用铅酸免维护蓄电池直流成套装置一套。
3.3.4主要电气设备选型
1)10kV高压配电设备选用金属铠装全封闭中置移开式高压开关柜;
2)400V站用低压配电设备选用抽屉式低压配电屏;
3)继电保护屏选用PK-10标准屏;
4)控制屏选用KG系列仪表控制屏,控制台为由DCS系统配套的电脑工作台;
5)静止可控硅励磁装置随发电机配套。
3.3.5过电压保护和电力装置的接地
1)根据气象资料公司所在地属于中雷区,对高于15m的建筑物(如汽轮机房等)按三类防雷建筑物保护设计;
2)发电机母线及发电机中性点均设有电站专用避雷器;
3)电力装置的接地。
高压系统为接地保护,低压系统为接零保护,接地系统为TN-S系统。
在汽轮发电机房、化学水处理、发电机出线小间、高低压配电室及电站中央控制室等场所均设置接地装置。
并通过电缆沟及电缆桥架上的接地干线,将各处的接地装置连接起来,形成电站的接地网络。
3.3.6站用电设备的控制
根据纯低温余热电站的技术特点,将采用机电炉集中的单元控制方式。
电站10kV母线设备,汽轮发电机、余热锅炉及其它站用辅机将在电站中央控制室进行集中控制。
但化学水处理将设独立的控制盘集中控制。
3.3.7电气照明
(1)正常照明:
电站的正常照明电源引自站用电屏,电源为三相四线制,电压为380220V。
主要车间照明一律采用均匀照明和局部照明相结合,均匀照明为主,局部照明为辅。
(2)事故照明:
电站内设有事故照明屏,当厂用交流电源消失后,事故照明屏自动将直流系统提供的直流电源投入。
根据电站内不同岗位的重要性,在重要岗位及车间设有事故照明灯,以满足可靠性和安全的要求。
(3)安全照明:
锅炉等金属体设备内检修采用安全照明电压12VAC。
照明灯具接至局部照明变压器220V36-24-12V二次侧,灯具采用手提安全灯。
4热工自动化
4.1编制原则及控制方案
为了使纯低温余热电站处于最佳运行状态,节约能源,提高劳动生产率,本工程拟采用技术先进、性能可靠的集散型计算机控制系统(简称DCS系统)对各车间(除化学水处理车间外)进行分散控制、集中管理。
4.2控制设备及一次仪表选型
为保证整个控制系统的先进性和可靠性,拟选用DCS系统实现对过程参数的采集、监视、报警与控制。
对于关键性的检测和控制元件选用进口设备或国内引进技术生产的优质产品。
选用的一次仪表设备有:
(1)智能化系列压力差压变送器;
(2)温度检测仪表元件;
(3)锅炉汽包水位等电视监视系统。
4.3系统配置及功能
设置于电站的计算机系统(DCS)由现场级及中央控制级组成。
计算机系统配置详见F11-计算机系统配置方案图。
(1)现场级
根据电站的特点,在位于汽轮机房运转层的电站中央控制室内设置IO模件机柜,采集所有来自现场的开关量和模拟量信号并输出驱动信号。
现场级完成电动机顺序逻辑控制、工艺过程参数的检测与监控,以及PID串级、多变量复杂控制等。
(2)中央监控级
中央监控级设1个工程师工作站和2个监控操作站,分别由监控管理计算机、CRT和打印机等组成。
监控操作站的功能包括:
1)具有动态参数的热力系统及工艺流程图显示;
2)电动机开停操作和运行状态显示;
3)棒形图显示;
4)历史趋势曲线的显示;
5)调节回路的详细显示及参数修正;
6)报警状态的显示;
7)报警状态及运行报告的打印等。
4.4应用软件
用于电站的DCS系统应用软件是实现现场级和中央监控级功能的重要文件。
应用软件包括逻辑控制软件和过程控制软件。
(1)逻辑控制软件
对电站所有电动机、电动阀,根据CRT显示的热力系统图,通过键盘操作,完成组启、组停、紧停复位、逻辑联锁等控制。
(2)过程控制软件
为保证整个电站运行工况的稳定,共设有4个自动调节控制回路。
4.5系统特点
本系统是一个控制功能分散控制、集中监视和管理的控制系统,电站中控室取消了常规模拟仪表盘和模拟流程图,代之以大屏幕彩色图形显示器,更便于运行人员监视与操作,同时大大缩小了中控制室的建筑面积。
此外系统中还采用了面向过程的语言,硬件均为模块化,使整个系统的操作与维护更加简便。
为防止数据丢失和电源干扰,系统采用不间断电源(UPS)供电,保证了运行的可靠性。
4.6自控线路和接地
一次检测元件、变送器至现场站之间的连接导线及直流信号线均选用对屏+总屏的计算机专用屏蔽电缆,热电偶至IO模件柜的连接导线选用补偿导线。
开关量信号线选用交联控制电缆,DCS控制系统各设备之间的连接电缆随设备成套供货。
电缆线路均敷设在电缆沟或带顶盖的电缆桥架内,并尽可能与电力电缆分开敷设。
当由于条件所限信号电缆与动力电缆同架敷设时,必须用分隔板隔开。
引出电缆沟或电缆桥架后导线须穿钢管暗配或明配。
接地系统