六西格玛Word文档格式.docx
《六西格玛Word文档格式.docx》由会员分享,可在线阅读,更多相关《六西格玛Word文档格式.docx(13页珍藏版)》请在冰豆网上搜索。
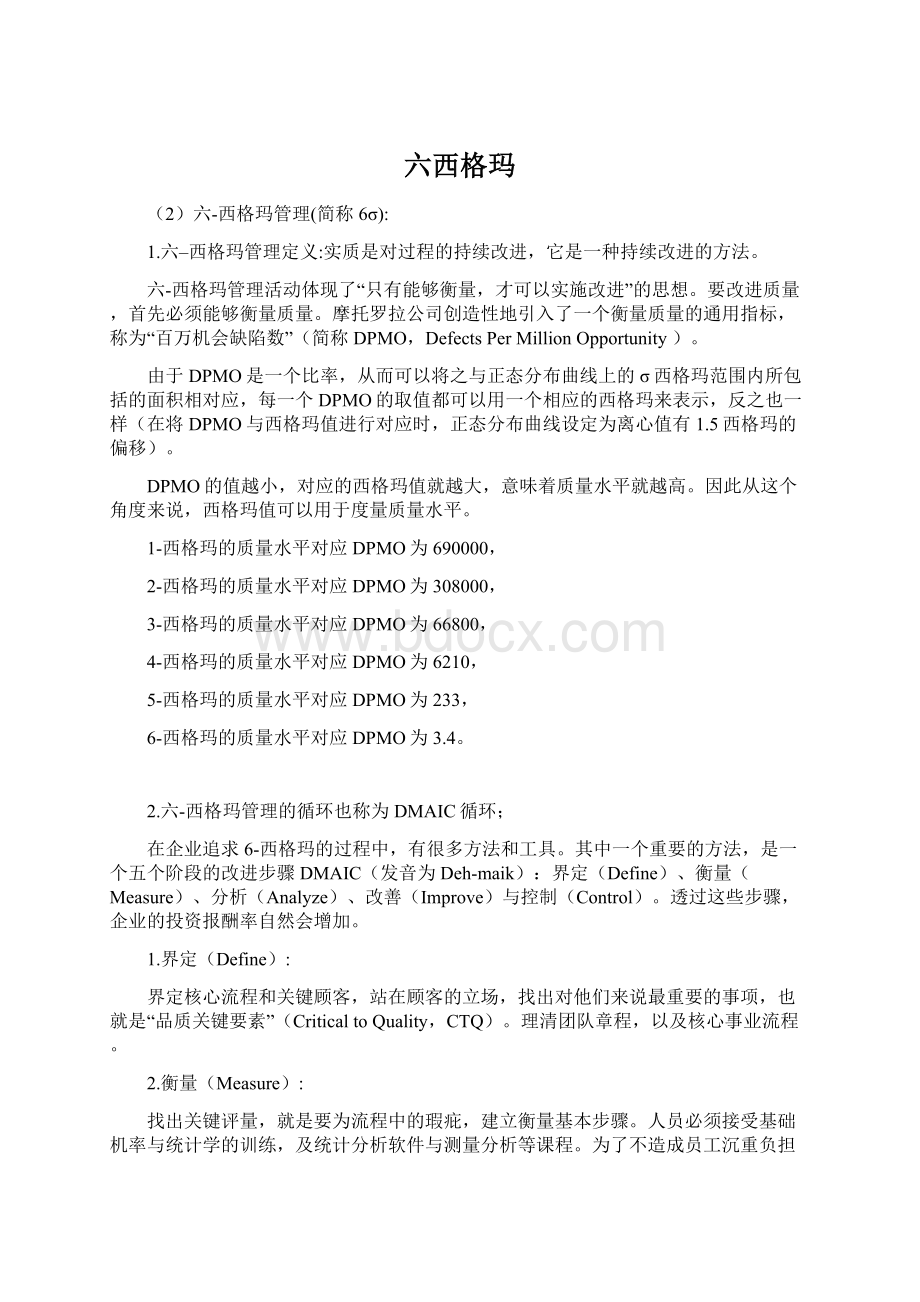
探究误差发生的根本原因。
运用统计分析,检测影响结果的潜在变量,找出瑕疪发生的最重要根源。
所运用的工具包含许多统计分析工具。
4.改善(Improve):
找出最佳解决方案,然后拟定行动计划,确实执行。
这个步骤需不断测试,看看改善方案是否真能发挥效用,减少错误。
5.控制(Control):
确保所做的改善能够持续下去。
衡量不能中断,才能避免错误再度发生。
在过去许多流程改善方案里,往往忽略了控制的观念;
而在六个标准偏差中,控制是它能长期改善品质与成本的关键。
如果成功推动,6-西格玛所带来的,将是改变企业惯性,让员工能够不断问问题,并寻求更好的解决方案,让企业常处于向上爬升的斜率上。
3.六-西格玛支持技术:
1.度量技术:
DPMO(百万机会缺陷数)的计算方法。
过程能力(CPK/PPK)分析技术(包括长/短期过程能力分析)。
2.基本技术:
(新、老七种工具)。
3.高级技术:
SPC:
统计过程控制技术,度量、分析、改进和监控过程的波动。
DOE:
优化设计技术,通过DOE,改进过程设计,使过程能力达到最优。
FMEA:
风险分析技术,辅助确定改进项目,制定改进目标。
QFD:
顾客需求分析技术,辅助将顾客需求正确地转换为内部工作要求。
防错:
从根本上防止错误发生的方法。
4.软技术:
领导力,提高团队工作效率,员工能力与授权,沟通与反馈。
统计过程管理(简称SPCStatisticsProcessControl)
1.什么是控制图?
控制图是对过程质量加以测定、记录从而进行控制管理的一种用科学方法设计的图。
2.控制图的应用:
控制图中包括三条线:
1.上控制线UCL)2.中心线(CL)3.下控制线(LCL)
区别:
4.上公差线(USL)5.下公差线(LSL)用于直方图中。
3.形状和位置公差
形状公差的符号:
直线度,平面度,圆度,圆柱度,线轮廓度,面轮廓度。
位置公差的符号:
平行度,垂直度,倾斜度,对称度,同轴度,位置度,园跳度,全跳度。
4.控制图建立的步骤:
1.选择质量特性2.决定管制图之种类3.决定样本大小,抽样频率和抽样方式4.收集数据5.计算管制参数(上,下管制界线等)6.持续收集数据,利用管制图监视制造过程。
5.控制图选择的方法;
X控制图主要用于观察正态分布的均值的变化,R控制图主要用于观察正态分布分散或变异情况的变化,而X-R控制图则将二者联合运用,用于观察正态分布的变化。
6.控制图的种类:
数据:
是能够客观地反映事实的资料和数字数据的质量特性
1.计量值:
可以用量具、仪表等进行测量而得出的连续性数值,可以出现小数。
计量型数据的控制图:
XBar-R图(均值-极差图)
(注:
均值X=各样本的平均值,极差R=各样本中最大值-最小值)。
XBar-S图(均值-标准偏差图)
标准偏差S^2=1/(n-1)*[(a1-x)^2+(a2-x)^2+(a3-x)^2+……(an-x)^2],各偏差(an-x)平方的平均数。
方差s^2的算术平方根即为标准偏差s)
极差、方差和标准偏差的区别与联系:
极差R、方差S^2和标准偏差S都是用来衡量(或描述)一组数据偏离平均数的大小(即波动大小)的指标,常用来比较两组数据的波动情况。
2.计数值:
不能用量具,仪表来度量的非连续性的正整数值。
计数型数据的控制图:
P控制图用于控制对象为不合格品率或合格品率等计数质量指标的场合,用P图时应选重要的项目作为判断不合格品的依据;
它用于控不合格品率、交货延迟率、缺勤率、差错率等。
N-P控制图用于控制对象为不合格品数的场合。
设N为样本,P为不合格品率,则N-P为合格品数。
C控制图用于控制一部机器,一个部件,一定长度,一定面积或任何一定的单位中所出现的不合格数目。
焊接不良数/误记数/错误数/疵点/故障次数。
U控制图当上述一定的单位,也即N保持不变时可以应用C控制图,而当N有变化时则应换算为平均每项单位的不合格数后再使用U控制图。
7.控制图八种异常图例:
有很多信号规则适用于所有的控制图(Bar图和R图),最常见的有以下八种:
规则1:
1个点在控制线以外(1点外)。
规则2:
连续9点在中心线一侧(9单侧)。
规则3:
连续6点递增上升或递减下降(6递增减)。
规则4:
连续14个相邻点上下交替(14交替)。
规则5:
连续3个点有2个点落在中心线一侧B区以外(2/3B外)。
规则6:
连续5个点有4个点落在中心线一侧C区以外(4/5C外)。
规则7:
连续15个点在C区中心线上下(15C上下)。
规则8:
连续8个点在中心线两侧,但无1个点在C区中(8缺1C)。
8.控制图的异常判断:
控制图可以区分出普遍原因变差和特殊原因变差。
1.特殊原因变差要求立即采取措施。
2.减少普遍原因变差需要改变产品或过程的设计。
9.改正错误的措施:
1.试图通过持续调整过程参数来固定住普通原因变差,称为过渡调整,结果会导致更大的过程变差造成客户满意度下降。
2.试图通过改变设计来减少特殊原因变差可能解决不了问题,会造成时间和金钱的浪费。
控制图可以给我们提供出了哪种类型的变差的线索,供我们采取相应的措施。
直方图使用:
(一)直方图是频数直方图,就是将数据按其顺序分成若干间隔相等的组,以组距为底边,以落入各组的频数为高的若干长方形排列的图。
直方图法是从总体中随机抽取样本,将从样本中获得的数据进行整理,根据这些数据找出质量运动规律,预测工序质量好坏,估算工序不合格品率的一种常用工具。
主要用途:
显示波动的形态;
直观地显示过程质量状况;
帮助寻找可以改进的项目。
(二)直方图的特点
直方图是是用一系列宽度相等,高度不等的长方形表示数据的图。
长方形的宽度表示数据范围的间隔。
长方形的高度表示在给定间隔内的数据的数目。
变化的高度形态表示数据的分布情况。
主要标注:
TU规格上限:
TL规格下限:
M规格中心:
X实际分布中心:
N总数:
S标准偏差。
(三)直方图的作用
1、显示波形的形态
直方图的尺寸分布服从正态分布的形态
计算平均值X:
计算标准偏差S:
2、直观的传达有关过程的信息
通过计算可准确地得到平均值和标准偏差,但不直观。
通过绘制直方图并对其形态的研究,就能直观的掌握过程的情况。
3、决定在何处集中力量进行改进。
(四)直方图的应用步骤
1、收集数据
作直方图的数据一般应大于50个。
2、计算数据的极差R
在原始数据中找出最大值xmax和最小值xmin,计算二者差值,即极差。
3、确定分组的组数和组距
一批数据究竟分多少组,通常根据数据的多少而定,可参考下表
直方图数据分组数表
数据个数
分组数k
50-100
5-10
100-250
7-12
250以上
10-20
组数去除极差,即得直方图每组的宽度,即组距h
4、确定各组界限值
为避免数据落在组界上,组界值的末尾数应取测量值单位的1/2。
例如,测量单位为0.1mm,组界的末尾数应取0.1/2=0.05mm。
分组界限应能把最大值和最小值包括在内。
在决定组界限时,可先从第一组起。
第一组的上界限值就是第二组的下界限值,第二组的下界限值加上组距,就是第二组的上界限值,也是第三组的下界限值,以此类推,可定出各组的组界。
为了计算的需要,往往要决定各组的中心值。
每组上下界限相加除以2,所得数据即为组中值。
组中值为各组数据的代表值。
5、编制频数分布表
将测得的原始数据分别归入相应组中,统计各组数据个数,即频数fi,填好各组频数后,检查总数是否与数据总数相符,避免重复或遗漏。
6、画直方图
按数据值比例画横坐标,横坐标表示质量特性;
按频数值比例画纵坐标,纵坐标为频数(或频率)。
在横轴上标明各组组界,以组距为底,频数为高画出一系列的直方柱,每个直方柱的宽度都是相等的。
直方图画好后,要在直方图上应标注出公差范围(T)、样本大小(n)、样本平均值(X)、样本标准偏差值(s)和X实际分布中心的位置等。
(五)做直方图应注意的问题
直方图的原始数据表,为计算方便,可以简化处理;
数据同时加上或减去一个数,其σ不变。
则要进行还原,即减去或加上同一个数。
数据同时乘以或除以同一个数,其σ和也要随之扩大或缩小同样倍数,因而,将来的σ和要还原计算。
数据最好处理成整数。
处理后的数据表如果出现“0”或“负数”,都不影响其作图和分析。
样本容量n≥50,通常取100,生产量小不宜用;
计算组距(h),取测量单位的整数倍;
确定分组界限,关键是计算第一组下限;
各组频数根据频数分布表中各组的频数记号统计;
频数记号应按数据表的顺序逐个数据“对号入座”进入相应的组;
做出直方图后,应在图上标出n,x、s三个数
标出四条线:
TU规格上限,TL规格下限,M规格中心,X实际分布中心。
计算过程能力指数,稳态可用控制图进行控制。
(六)直方图的定量表示
直方图定量表示的主要特征值是平均值X和标准偏差S。
平均值:
表示数据的分布中心位置,它与标准的中心M越靠近越好。
标准偏差s表示数据的分散程度。
它越小,数据分散程度越小,加工精度越好;
它越大,数据分散程度也越大,加工精度也越差。
直方图形状所反映的现象:
(a)对称型。
这是正常的形状。
(b1)左偏向型。
当缺陷数近于0,使下限受到控制的情况下,会出现此型。
(b2)右偏向型。
与情况(b1)正好相反,当缺陷接近于极限值等原因使上限受到控制的情况下,会出现此型。
(c)双峰型。
存在两种不同分布时多出现这种情况。
例如:
将两批不同来源的产品混在一起检测时。
(d)孤岛型。
说明工序条件发生过异变。
在原料一时发生变化或短期内由不熟练工人替班加工或测量。
(e)平顶型。
当生产过程有某种因素在发生缓慢变化时多有出现。
工具发生磨损、操作者疲劳或环境发生了缓慢变化。
(f)锯齿型。
通常是测量方法或读数有问题,也可能是数据太少,分组的组数太多导致。
失效模式及后果分析(简称FMEAFailureModeandEffectAnalysis)
(1)失效模式及后果分析(FMEA)的三种介绍:
1.系统FMEA-SFMEA
用来在早期构思系统阶段,分析系统与子系统。
分析重点:
由系统缺陷所引起的与系统功能相联系的潜在失效模式。
2.设计FMEA-DFMEA
用来在产品交付生产前分析产品。
由设计缺陷引起的产品潜在失效模式。
3.过程FMEA–PFMEA
用来分析制造与装配过程。
由制造或装配过程缺陷引起的潜在产品失效模式。
(2)FMEA(潜在故障及原因分析)目的
1.鉴定潜在失效模式与评定其后果(影响)的严重程度。
2.确定关键特性与重要特性。
3.对潜在的系统与过程缺陷进行排序。
4.帮助工程师集中力量以排除对产品与过程的担心。
5.帮助防止问题发生。
6.持续改进。
(3)FMEA(潜在故障及原因分析)步骤
1.系统/产品/过程分析。
2.功能分析。
3.风险评估。
4.量化风险。
5.优化措施。
(4)FMEA(潜在故障及原因分析)控制方法
控制失效模式或失效原因,可采用或现时正采用的:
1.检测。
2.分析。
3.评审的手段。
4.技术。
5.方案。
(5)FMEA(潜在故障及原因分析)量化风险
1.严重度(Severity)
对失效模式发生时引致的后果的严重程度的评估。
2.频度(发生度)(Occurrence)
某一特定失效原因/机制出现可能性。
3.不易探测度(难检度)(Detection)
控制方法可探测潜在失效模式/原因的能力的评估。
风险顺序数RPN(RiskPriorityNumber):
RPN=S*O*D(严重度x发生度x难检度)。
优化设计技术(简称DOE)
是一系列实验及分析方法集,通过有目的地改变一个系统的输入来观察输出的改变情况
(1)DOE的目的
1.确定哪些x对y的影响最大;
2.确定应把有影响的x设定在什么水平,以使y达到或尽可能靠近希望值;
3.确定应把有影响的x设定在什么水平,以使y的分散度(或方差)尽可能减小;
4.确定应把有影响的x设定在什么水平,以使不可控x(噪音因子)对y的影响尽可能减小。
(2)DOE的基本术语
1.响应变量:
所关注的可测量的输出结果,如良率、强度等,常用y表示;
2.因子:
可控的变量,通过有意的变动,可确定其对响应变量的影响,如温度、时间等,常用x表示;
3.重复:
指在不重新组合实验设定的情况下,连续进行实验并收集数据;
4.复制:
意谓每个数据值在重新设定测试组合之后收集;
5.随机化:
适当安排实验次序,使每个实验被选出的机会都相等;
6.全因子实验:
组合所有因子和每个因子水平的实验;
7.部分因子实验:
如果没有全部资源和时间时采用的一种只运行全因子试验中的部分组合的实验;
8.主效果:
一个因子在多种水平下的变化导致输出变量的平均变化;
9.交互作用:
改变其他因子的不同水平是,一个因子水平的主要效果有所改变,在这种情况下因子间具有的作用;
10.中心点:
检查一个两水平因子试验的主效果在两个水平之间是否是线性的;
11.区组:
无法控制的变量称之为分区化变量,在一个分区变量的某个标准上进行的实验称为一个分区;
12.P值:
检查一个因子说效果是否显著的概率值;
13.曲率:
检查中心点是否显著的值;
14.失拟:
检查简化模型过程是否合适(失拟表示被剔除的项是显著的活模型所包含的项中有不显著的);
15.残差分析:
检查分析结果是否可用,从正态、随机角度分析;
R-Sq、R-Sq(预测)、R-Sq(调整):
检查模型准确性,三个数值应尽量接近
系数:
y=f(x)中各x的系数,决定方程式的系数,为模型优化做准备;
16.响应优化器:
基于y=f(x)进行望大、望小、望目的对x的预测。