整理锻造部分习题总结铸造工艺习题部分含答案Word下载.docx
《整理锻造部分习题总结铸造工艺习题部分含答案Word下载.docx》由会员分享,可在线阅读,更多相关《整理锻造部分习题总结铸造工艺习题部分含答案Word下载.docx(10页珍藏版)》请在冰豆网上搜索。
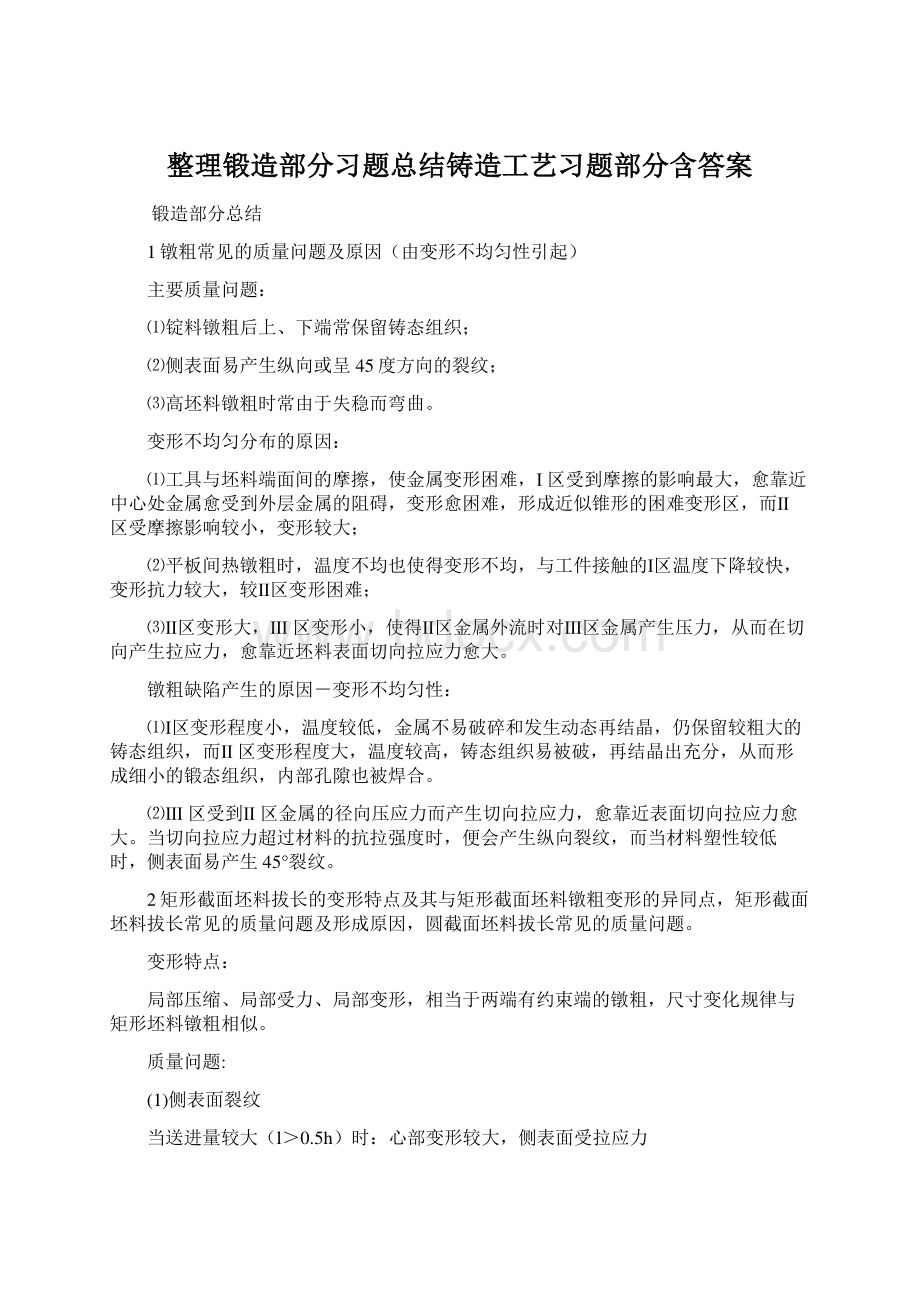
心部变形较大,侧表面受拉应力当送进量过大(lh)和压下量也很大时:
展宽过多而产生较大的拉应力引起侧表面开裂,类似于镦粗裂纹。
(2)角裂拔长时外端的存在加剧了轴向附加拉应力,尤其是边角部分冷却较快,塑性降低,更易开裂。
因此在拔长高合金工具钢和某些耐热合金时,易产生角裂,操作时需注意倒角。
(3)内部纵向裂纹:
当送进量较大,并且在坯料同一部位反复重击时:
对角线裂纹(4)内部横向裂纹拔长大锭料时,常遇到l0.5h的情况,此时变形主要集中在上、下两部分,中部变形小,在轴心部分沿轴向受到附加拉应力,在拔长锭料和低塑性材料时,轴心部分原有的缺陷(缩松等)进一步扩大,易产生横向裂纹。
(5)表面折迭原因:
送进量很小,压下量很大,上、下两端金属局部变形引起的。
(6)侧表面折叠原因:
拔长时压得太扁,翻转90压缩时坯料弯曲形成。
(7)端面内凹原因:
送进量太小,表面金属变形大,轴心部分金属未变形或变形较小引起的。
此时端部需有足够大的压缩长度和较大的压缩量(8)倒角时对角线裂纹原因:
不均匀变形和附加拉应力引起的圆截面坯料拔长常见的质量问题:
形成裂纹和空腔3冲孔时坯料高度变化的特点及原因。
(可用应力应变的顺序对应规律来解释)D/d较小时,环壁较薄时,r较小,较大,应力顺序,z和r,且zr,由应力应变顺序对应规律可知z0,冲孔后坯料高度减小。
D/d较大(D/d5),环壁较厚,r较大,较第一种情况小,应力顺序,z和r,且z0.5(r+),坯料高度变化不大D/d很大,环壁很厚,外侧的,z和r均较小,内侧应力顺序z,和r,可算得冲孔后坯料内侧高度增加。
4芯轴扩孔的变形特点及其与芯轴拔长(空心件拔长)的差别。
与长轴件的拔长不同,是沿坯料圆周方向的拔长。
主要沿切向流动,并增大内外径的原因:
1)变形区沿切向的长度远小于宽度;
2)马杠上扩孔锻件一般比较薄,外端对变形区金属切向流动的阻力远小于宽度方向(t/d越大,切向流动阻力越大);
3)马杠与锻件的接触面呈弧形,有利于金属切向流动。
(拔长时弧形砧拔长)5模具形状对金属变形和流动有哪些主要影响控制锻件的最终尺寸和形状控制金属的流动方向控制塑性变形区提高金属塑性控制坯料失稳提高成形极限6开式模锻时影响金属变形流动的主要因素?
模膛(模锻件)的具体尺寸和形状;
飞边槽桥口部分的尺寸和飞边槽的位置;
终锻前坯料的具体形状和尺寸;
(复杂件预锻,很重要)坯料本身性质的不均匀情况,主要指由于温度不均引起的各部分金属流动极限s的不均匀情况;
设备工作速度。
(载荷性质影响)7挤压时筒内金属的变形流动特点及原因分析,挤压时常见的缺陷及原因分析?
第一种情况仅区域内金属有显著的塑性变形,死角区(a)较小。
(摩擦系数较小)第二种情况是挤压筒内所有金属都有显著的塑性变形,并且轴心部分的金属比筒壁附近的金属流动得快,死角区较第一种情况大。
第三种情况是挤压筒内金属变形不均匀,轴心部分金属流动得快,靠近筒壁部分的外层金属流动很慢,死角区也较大。
(摩擦较大和坯料较高)挤压时常见的缺陷:
1“死角区”剪裂和折迭;
2挤压“缩孔”;
矮坯料挤压时:
A区金属往凹模孔流动带动B区金属流动,以及径向压应力作用引起。
3裂纹。
主要是由于筒内各区域的变形不均引起的附加应力导致的。
“死区”形成原因:
1凹模底部摩擦。
越靠近凹模侧壁处摩擦阻力越大,而孔口部分较小,因此“死区”一般呈三角形。
2热挤压时,越靠近筒壁处,金属温度降低越多,变形也越困难。
7锻件图(冷锻件图)设计的内容?
1选择分模面的位置和形状;
2确定机械加工余量、余块和锻件公差;
3确定模锻斜度;
4确定圆角半径;
5确定冲孔连皮的形式和尺寸;
6制定锻件技术条件;
7绘制锻件图。
选择分模面的最基本原则:
保证锻件容易从锻模模膛中取出,锻件形状尽可能与零件形状相同。
锻件分模位置应选择在具有最大水平投影尺寸的位置上。
计算毛坯:
是根据平面变形假设进行计算并修正所得的具有圆截面的中间坯料,其长度与锻件相等,而横截面积应等于锻件上相应截面积与飞边截面积之和。
即:
9热锻件图设计需要考虑的因素,钳口及其作用?
热锻件图是将锻件图的所有尺寸计入收缩率而绘制的。
钢锻件1.5%,细长杆、薄锻件1.2%。
终锻模膛易磨损处,应在锻件负公差范围内预先增加磨损量,以提高锻模寿命,保证锻件的合格率;
锻件上形状复杂且较高的部分应尽量放在上模。
如放在下模,需在相应处局部加厚以防缺肉。
对某些具有高筋的锻件,其终锻模膛在相应部位应设有排气孔,以保证筋部充满;
当设备的吨位偏小,模锻不足现象严重时,应使热锻件图高度尺寸比锻件图上相应高度减小一些,以抵消模锻不足的影响。
相反,当设备吨位偏大或锻模承击面偏小,则热锻件图高度尺寸应接近于正公差,以保证在承击面下陷时仍可以锻出合格锻件。
锻件的某些部位在切边或冲孔时易产生变形而影响加工余量时,则应在热锻件图的相应部位适当地增加一定的祢补量,以提高锻件的合格率;
当锻件的形状不能保证坯料在下模膛内或切边模内准确定位时,则应在热锻图上增加必要的定位余块,以保证多次锻击过程中的定位以及切飞边时的定位。
钳口是指在锻模的模膛前面所做的空腔,它是由夹钳口与钳口颈两部分组成。
用途是:
夹钳口在模锻时用来放置棒料及钳夹头;
钳口颈用来加强夹钳料头与锻件之间的连接强度;
齿轮类零件在模锻时无夹钳料头,钳口是作为锻件起模之用;
在锻模制造时,钳口作为浇铸模膛检验件(金属盐或铅、树脂、腊等)的浇口。
10折迭的形成原因及控制措施,充不满的形成原因。
形成原因1)靠近接触面附近的金属有流动;
2)该部分金属必须沿水平方向外流;
3)有中间部分排出的金属量较大。
防止措施1)是中间部分金属在终锻时的变形量小一些,亦即由中间部分排出的金属量少一些;
2)创造条件使终锻时由中间部分排出的金属尽可能向上和向下流动,继续充填模膛。
(如增加桥口阻力或减小充填模膛阻力)充不满原因:
1)在模膛深而窄的部分由于阻力大不易充满;
2)在模膛的某些部位,由于金属很难流到而不易充满;
3)制坯时某些部分坯料体积不足,或操作时由于放偏,某部分金属量不足引起充不满。
11锻模中心和模膛中心。
锻模中心:
指锻模燕尾中心线与键槽中心线的交点,它位于锤杆轴心线上,是锻锤打击力的作用中心。
模膛中心:
即锻造时模膛承受锻件反作用力的合力作用点。
可依据锻件在分模面的面积重心确定。
铸造工艺部分总结1怎样审查铸造零件图样?
其意义何在?
一从避免缺陷方面审查铸件结构:
(一)铸件应由合理的壁厚
(二)铸件结构不应造成严重的收缩阻碍,注意壁厚过渡和圆角(图)(三)铸件内壁应薄于外壁(四)壁厚力求均匀,减小肥厚部分,防止形成热节(五)有利于补缩和实现顺序凝固(六)防止铸件翘曲变形(七)避免浇注位置上有水平的大平面结构二、从简化铸造工艺方面改进零件结构
(一)改进妨碍起模的凸台、凸缘和肋板的结构
(二)取消铸件外表侧凹(三)改进铸件内腔结构以减少砂芯(四)减少和简化分形面(五)有利于砂芯的固定和排气(六)减少清理铸件的工作量(七)简化模具的制造(八)大型复杂件的分体铸造和简单小件的联合铸造对产品零件的审查、分析有两方面的作用)审查零件结构是否符合铸造工艺的要求。
)在既定的零件结构条件下,考虑铸造过程中可能出现的主要缺陷,在工艺制定中采取措施予以防止.2浇注位置的选择或确定为何受到铸造工艺人员的重视?
应遵循哪些原则?
浇注位置的选择关系到铸件的内在质量、铸件的尺寸精度及造型工艺的难易程度确定浇注位置的原则:
)铸件的重要部位应尽量置于下部)重要加工面应朝下或呈直立状态)使铸件大平面朝下,避免夹砂结疤类缺陷对于大平板类铸件,可采用倾斜浇注,以便增大金属液上升速度。
)应保证铸件能充满具有大面积的薄壁铸件,应将薄壁部分放在铸型的下部,同时要尽量使薄壁部分处于垂直位置或倾斜位置。
)应有利于铸件的补缩对于易产生收缩缺陷的铸件因优先考虑实现顺序凝固的条件)避免用吊砂、吊芯或悬臂式砂芯,便于下芯合箱及检查)应使合箱位置、浇注位置和铸件冷却位置相一致避免合箱后,或浇注后再次翻转铸型3为什么要设分型面?
怎样选择分型面?
)分型面应尽量采用平面分型,避免曲面分型,并应尽量选在最大截面上,以简化模具制造和造型工艺。
)尽量将铸件全部或大部放在同一砂箱以防止错型、飞翅、毛刺等缺陷,保证铸件尺寸的精确。
)应尽量减少分型面数目)便于下芯、合箱和检查型腔尺寸尽量)不使砂箱太高)受力构件的分型面选择不应削弱铸件的结构强度)注意减轻铸件清理和机械加工量4芯头是长些好,还是短些好?
间隙留大好,还是不留间隙好,请举例说明。
5压环、防压环、积砂槽各起什么作用?
什么条件下应用?
不用他们行不行?
6要想使单件生产的大铸件不报废,你认为应使用哪些铸造工艺参数?
7铸造优缺点?
优点:
1)可以生产出形状复杂,特别是具有复杂内腔的零件毛坯,如各种箱体、床身、机架等。
2)铸造生产的适应性广,工艺灵活性大。
工业上常用的金属材料均可用来进行铸造,铸件的重量可由几克到几百吨,壁厚可由0.5mm到1m左右。
3)铸造用原材料大都来源广泛,价格低廉,并可直接利用废铸件,故铸件成本较低。
缺点:
1)铸造组织不致密、晶粒粗大,内部易产生缩孔、缩松、气孔等缺陷,因此,铸件的力学性能,特别是冲击韧度低于同种材料的锻件。
2)铸件质量不够稳定。
8浇注系统的主要作用?
保证金属液体平稳地、无冲击地充满型腔;
防止熔渣随同金属液体进入型腔;
防止金属液卷入气体带入型腔;
防止铸件产生渣眼、砂眼、气孔缺陷;
9浇注系统的组成浇口杯承接浇包中的液体金属。
直浇道将金属液由浇口杯引入到横浇道。
横浇道将金属液引入到内浇道,阻挡熔渣、气体、砂粒进入型腔。
内浇道将金属液体引入型腔。
10浇注系统开设的原则1)从铸件的薄壁处引入这种方法适用于薄壁而轮廓尺寸又大的铸件。
(因为可以实现同时凝固,应力小,适合收缩不大的灰铁铸件)-适合同时凝固原则的合金2)从铸件的厚壁处引入创造顺序凝固,有利补缩铸件,(适合有一定壁厚差而凝固时合金的收缩量较大的铸件,如铸钢件))内浇道尽可能不开在铸件重要部位局部过热,粗大(组织)易缩松)内浇道要引导液流不正面冲击铸型、砂芯等)浇注系统位置选择,应该使金属液在型腔内流动路径尽可能短,还应考虑不妨碍铸件收缩)内浇道应开在加工表面11铸钢件的浇注系统铸钢的特点:
熔点高,易氧化,流动性差,在凝固中收缩大,易产生如缩孔、缩松、热裂和变形及缺陷。
设计要点:
、遵循方向性(顺序)凝固原则,浇口多设在冒口下,配给使用冷铁、收缩筋等;
、使用柱塞包浇注时,直浇道设计成不充满的开放式,以保证钢液不溢出(即包口为最小截面积);
、中小件多采用底注,大件多采用阶梯式;
、浇注系统简单、截面尺寸大,以保证快浇。
12冒口位置选择原则方向性(顺序)凝固,要使凝固进行方向朝向冒口;
一般在热节上方,厚壁部分设置;
冒口应比铸件晚凝固,最后凝固才能补缩;
冒口在满足补缩条件下,尺寸尽量小;
防止裂纹产生,冒口不设在铸件应力集中处(阻碍收缩),防止引起裂纹;
尽可能地将冒口设在方便和容易消除冒口残根的地方;
冒口的补缩距离要大于冒口的有效补缩范围。
(7)环境影响评价的结论。
(3)是否符合区域、流域规划和城市总体规划。
13冒口补缩原理(基本条件)3)规划实施的经济效益、社会效益与环境效益之间以及当前利益与长远利益之间的关系。
(1)一般来说,冒口系统(冒口和冒口颈)的凝固时间应晚于铸件的凝固时间。
3.政府部门规章
(2)冒口要能根据设计的要求提供足够的金属来补偿铸件的液态收缩,凝固收缩以及由于型腔扩大而增加的体积。
而且要力求铸件的成品率高。
第1页(3)冒口和铸件受补缩部位之间,要保持一定的温度梯度和凝固梯度,以保证补缩通道畅通大纲要求14提高冒口补缩效率的方法提高冒口中金属液补缩压力大气压力冒口2.间接市场评估法延长冒口中金属液保持时间保温冒口、发热冒口(四)安全预评价内容15冷铁作用:
加快铸件热节部分的冷却速度,使铸件趋于同时凝固,有利于防止铸件变形或出现裂纹。
并有可能减少偏析。
(二)建设项目环境影响评价的工作等级与冒口配合使用,使铸件局部冷却加速,强化了铸件顺序凝固的条件,有利于冒口补缩和扩大冒口补缩范围。
这样不仅有利于防止铸件产生缩孔、缩松缺陷,还有可能减少冒口的数目或体积及补贴的斜度,提高工艺出品率。
加快铸件某些特殊部位的冷却速度,以期达到提高铸件表面硬度和耐磨性、细化基体组织的目的。
在难于设置冒口或冒口不易补缩到的部位放置冷铁以减少或防止出现缩孔、缩松。
大纲要求对球铁,用冷铁进行激冷可以增大铸件表面和中心的温度梯度,有利于提高石墨化膨胀的利用程度和提高冒口补缩效果。