CKⅡ型车床主轴箱加工6Ф17孔两面卧式组合钻床设计Word格式.docx
《CKⅡ型车床主轴箱加工6Ф17孔两面卧式组合钻床设计Word格式.docx》由会员分享,可在线阅读,更多相关《CKⅡ型车床主轴箱加工6Ф17孔两面卧式组合钻床设计Word格式.docx(28页珍藏版)》请在冰豆网上搜索。
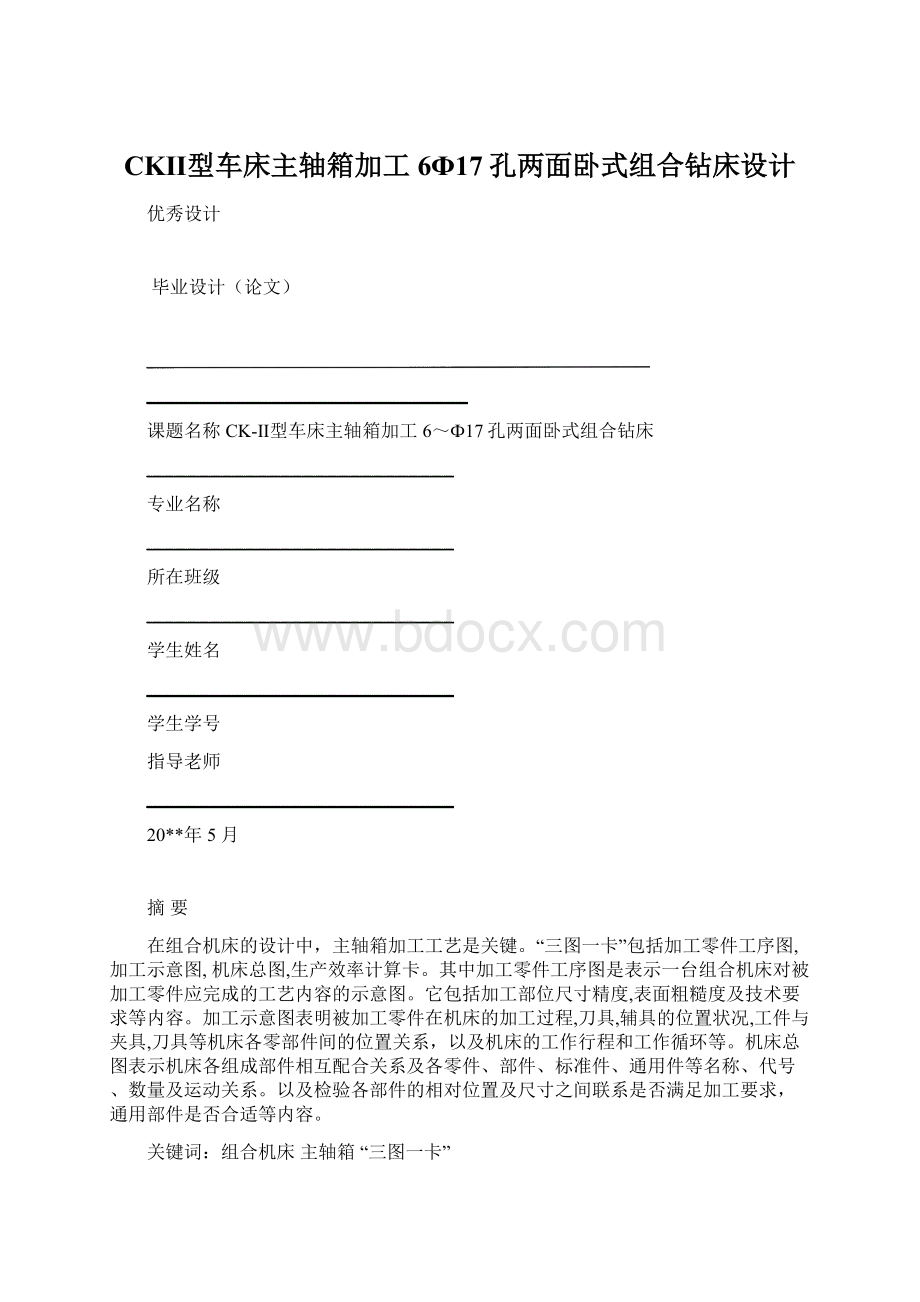
六、多轴箱CAD系统………………………………………32
七、设计总结………………………………………………33
八、参考文献……………………………………………….34
一、设计任务书
一设计课题:
钻加工轴箱6-ф17孔两面卧式组合钻床
二任务书
1工序图
2加工示意图
3机床布置总图
4传动系统图
5多轴箱总图
6CAD零件图
7加工效率计算卡
8设计说明书
生产纲领:
6万台/年
二、概述
(一)组合机床(transferandunitmachine)的设计内容
组合机床是按系列化,标准化通用件及按工件的形状和加工工艺要求设计的专用件所组成的高效机床,组合机床90%为通用件,10%为专用件,故来加工产品有很大的优点.
组合机床的特点:
1.主要用于棱体其零件和杂件的孔面加工.
2.生产高,因工序集中,可多共面、多轴、多刀同时加工.
3.加工精度稳定.
4.研制周期短、便于设计、制造和使用维护,成本低.
5.自动化程度高,劳动强度低.
6.配置灵活,因结构是横块化,组合化,可按工件或工序,因大量通用部件和少量部件灵活组成或各种类型的组合机床及自动化.
(二)组合机床(transferandunitmachine)的功用及未来的发展
组合机床一般采用多轴、多刀、多工序、多面或多工位同时加工的方式,生产效率比通用机床高几倍至几十倍。
由于通用部件已经标准化和系列化,可根据需要灵活配置,能缩短设计和制造周期。
因此,组合机床兼有低成本和高效率的优点,在大批、大量生产中得到广泛应用,并可用以组成自动生产线。
组合机床一般用于加工箱体类或特殊形状的零件。
加工时,工件一般不旋转,由刀具的旋转运动和刀具与工件的相对进给运动,来实现钻孔、扩孔、锪孔、铰孔、镗孔、铣削平面、切削内外螺纹以及加工外圆和端面等。
有的组合机床采用车削头夹持工件使之旋转,由刀具作进给运动,也可实现某些回转体类零件(如飞轮、汽车后桥半轴等)的外圆和端面加工。
二十世纪70年代以来,随着可转位刀具、密齿铣刀、镗孔尺寸自动检测和刀具自动补偿技术的发展,组合机床的加工精度也有所提高。
铣削平面的平面度可达0.05毫米/1000毫米,表面粗糙度可低达2.5~0.63微米;
镗孔精度可达IT7~6级,孔距精度可达O.03~O.02微米。
专用机床是随着汽车工业的兴起而发展起来的。
在专用机床中某些部件因重复使用,逐步发展成为通用部件,因而产生了组合机床。
最早的组合机床是1911年在美国制成的,用于加工汽车零件。
初期,各机床制造厂都有各自的通用部件标准。
为了提高不同制造厂的通用部件的互换性,便于用户使用和维修,1953年美国福特汽车公司和通用汽车公司与美国机床制造厂协商,确定了组合机床通用部件标准化的原则,即严格规定各部件间的联系尺寸,但对部件结构未作规定。
通用部件按功能可分为动力部件、支承部件、输送部件、控制部件和辅助部件五类。
动力部件是为组合机床提供主运动和进给运动的部件。
主要有动力箱、切削头和动力滑台。
支承部件是用以安装动力滑台、带有进给机构的切削头或夹具等的部件,有侧底座、中间底座、支架、可调支架、立柱和立柱底座等。
输送部件是用以输送工件或主轴箱至加工工位的部件,主要有分度回转工作台、环形分度回转工作台、分度鼓轮和往复移动工作台等。
控制部件是用以控制机床的自动工作循环的部件,有液压站、电气柜和操纵台等。
辅助部件有润滑装置、冷却装置和排屑装置等。
为了使组合机床能在中小批量生产中得到应用,往往需要应用成组技术,把结构和工艺相似的零件集中在一台组合机床上加工,以提高机床的利用率。
这类机床常见的有两种,可换主轴箱式组合机床和转塔式组合机床。
组合机床未来的发展将更多的采用调速电动机和滚珠丝杠等传动,以简化结构、缩短生产节拍;
采用数字控制系统和主轴箱、夹具自动更换系统,以提高工艺可调性;
以及纳入柔性制造系统等。
三、组合钻床的总体设计
加工对象主轴箱箱体
材料HT200
加工内容钻6~φ17孔
加工精度孔位置精度0.1
生产批量6万台/年
(一)CK-Ⅱ型数控机床主轴箱加工工艺过程:
1.木模:
确定造型的分型面,拔模斜度,芯头芯盒的几何尺寸,内外横浇口,有浇口的几何形状及尺寸;
浇片后的素水量等工步.
2.造型:
采用渗加固化剂的肤腩树脂造型,在造型机上制造外型与泥芯经氯化硬化后进行合模,在外模中下泥芯,然后经合箱、扣箱工步制造浇杯、冒口杯等.
3.浇注:
先进行点火将砂型中有机物质燃烧排气,将熔化温度在1400左右的铸铁铁水净化,待气孔渣子上浮,清楚干净后冷却到1300度左右进行浇注.
4.清砂:
铸件冷却1~2小时后开箱送入振动落砂机上清砂.除去铸件的浇冒口系统,并对坯件进行打磨去刺.
5.退火:
清除坯件体凝固的内应力,加温在350℃左右,保温在4~6h并随炉冷却.
6.刷涂料:
在需要加工的四周表面上刷上冷却带色涂料
7.钳:
以三大孔为基准,划四周平面加工线.
8.龙门铣:
找正工件一次粗铣4~5个主轴箱件的外表面.并在箱体底平面及两侧平面上留0.5㎜的精刨余量.
9.龙门铣:
精刨工件的底平面及有孔系两侧平面.
10.摇臂钻:
以钻模为夹具,钻加工φ8的孔并钻铣2-φK两销孔.
11.粗镗:
以卧式单工位双面组合镗床,粗镗φ100,2-φ60三大孔.并留单边余量0.5㎜
12.精镗:
以卧式单工位双面组合镗床精镗上叙三个大孔至图式尺寸并倒角1×
45°
.
13.以大孔Φ100为基准,采用活动钻模板在单工位卧式组合钻床加工6-Φ17孔.
14.钳:
去除机加工毛刺.
15.检验:
检验各加工平面与孔的尺寸是否合图.
16.钳:
在CK-Ⅱ数控机床主轴箱上打印标记.
17.入库:
涂刷防锈剂,分类堆放.
根据工件主轴箱箱体的结构特点,以及考虑定位基准与设计基准重合原则,必须选用一面A及两孔Φ100,2-Φ16的销孔为定位基准.
注:
①加工精度的影响:
从表4-1中看出,当工件的加工精度要求高时,应采用具有固定夹具的单工位组合机床.因为对孔的位置精度要求较高,所以采用单工位卧式组合机床.
②工件的大小形状和加工部位特点影响:
因工件尺寸较大,所以采用单工位机床.又因被加工孔的中心线与定位基准平行,且需从两个方向同时加工,故采用卧式组合钻床,同时卧式组合钻床排屑方便.
(二)“三图一卡”的设计:
1.所谓“三图一卡”是指加工零件工序图,加工示意图,机床总图,生产效率计算卡.
1.被加工零件工序图:
1.1被加工零件工序图的工艺方案,表示一台组合机床对被加工零件应完成的工艺内容的示意图.它包括加工部位尺寸精度,表面粗糙度及技术要求等内容.它不能用产品的零件图代替,其内容包括:
1)表示出被加工零件的形状和轮廓尺寸及本机床设计相关的部位的结构形状和尺寸.
2)表示出加工用定位基准,夹紧部位及夹紧方向.以便进行夹具的定位支承,限位,夹紧及导向系统的设计.
3)表示出本道工序加工部位的尺寸,尺寸精度,表面粗糙度,形状位置精度及技术要求.另外还应该表示出本道工序对前道工序提出的要求.
4)表示出必要的文字说明.如被加工零件的编号,名称,材料硬度,重量及加工部位的余量等.
1.2绘制被加工零件工序图注意事项:
5)绘制时按一定比例,选择足够的视图和剖视图突出加工部位,并把零件的轮廓及机床,夹具设计有关部位表示清楚.
6)应注明零件加工对机床提出的某些特殊要求.
7)对工件毛坯应有要求,对孔的加工余量要认真分析.
8)当本工序有特殊要求应注明.
1.3如下图是主轴箱箱体工序图(其余部分见图纸)
2.加工示意图
2.1加工示意图的作用和内容:
表明被加工零件在机床的加工过程,刀具,辅具的位置状况,工件与夹具,刀具等机床各零部件间的位置关系.以及机床的工作行程和工作循环等.
内容有:
1)反映机床加工部位的特点及加工要求决定道具等类型。
2)根据加工部位的特点及加工要求决定道具等类型。
3)决定主轴的结构类型规格尺寸及外伸长度。
4)选择标准或设计专用接杆,浮动卡头,导向装置,攻丝靠模装置,刀杆托架等。
5)表明主轴,接杆,夹具与工件之间的联系尺寸,配合及精度。
6)根据机生效率及刀具和工件的材料等,合理并标注各主轴的切削用量。
7)决定机床动力部件的工作行程及工作循环。
2.2加工示意图的画法及注意事项
1)加工示意图的绘制顺序:
先按比例用细实线绘出工件加工部位和局部结构的展开图,然后用粗实线绘出加工表面。
2)㎜在加工示意图上,主轴的分布可不按其真实距离绘制
3)主轴应从主轴箱端面画起,刀具画在加工位置。
2.3选择刀具,导向装置及有关计算
1)刀具选择
因加工孔的直径为17mm,选直径D=17mm的高速钢钻头在硬度为HBS170~200的零件上钻孔深40mm。
1首先确定切削用量,查《组合机床设计》
表3-7
取v=24m/minf=0.2mm/r
轴向力F=26Df0.8HB0.6
=26×
17×
0.20.8×
2000.6
=2930N
F=6×
2930=17580N
扭矩:
M=10D1.9f0.8HB0.6
=10×
171.9×
=14431N·
mm
M总=6M=6×
14431=86586N·
功率:
N切=M×
V/(9740×
3.14×
D)
=14431×
24/(9740×
3.14
×
17)=0.67KW
P电=N切/K功=0.67/0.8=0.8375KW
P总=6P电=6×
0.8375=5.03KW
查表中的电机为:
ITD40IY132S-4型
滑台:
IHY40ZA型
侧底座:
ICC401
∵用45正火钢,于非刚性主轴
∴取[Ф]=1/v则B=6.2
故:
d=B(M/100)1/4
=6.2×
(14431/100)1/4
=21.5
取d=25mm
⑵导向装置的选择:
组合机床加工时,采用非刚性主轴加工方案外,零件上孔的位置精度主要是靠刀具的导向装置来保证的。
在组合机床上使用钻头为标准刀具时,通常采用可以调节轴向尺寸的摇杆和卡头等中间夹具安装在主轴孔中。
⑶确定主轴类型、尺寸、外伸长度:
因为刀具与主轴是刚性连接,且用于组合双面钻床上,由《毕业设计指导书》中表4-8选主轴为长轴,且轴端的外径为内径的38/26,外伸长为115,接杆材料为45钢,莫氏圆锥度为2,即2-240-7635-01A类。
D1=24mmD2=38mm圆螺母B=12mm,L=240mm
采用接杆连接,且D·
t=26×
2
刀具切出长度:
L2=1/3dQ+(3~8)=1/3×
17+(3~8)
=8mm
动力部件的工作进给长度:
L工进=L工件+L1+L2
=40+10+8=58mm
L快进=142mm
L快退=L工进+L快进=58+142=200MM
因动力部件的快速退回长度L快退须保证所有刀具均至夹具的导套内,而不影响工件的装卸。
L前备=30mmL后备=170mm
L总=L2+L前备+L后备=20+30+170
=400mm
用钻孔Ф17活动钻套为Ф27与钻头的配合为H7/g6的间隙配合,固定钻套为Ф35H7/g6与活动钻套为过盈配合,活动导向板与工件的距离为10mm,活动钻套伸出长为5mm,总长为34mm,活动钻模板为24mm。
2.4如下图是多轴箱中间体加工图(其余部分见图纸)
3.机床总图
3.1总图的作用和内容:
表示机床各组成部件相互配合关系及各零件、部件、标准件、通用件等名称、代号、数量及运动关系。
以检验各部件的相对位置及尺寸之间联系是否满足加工要求,通用部件是否合适,其内容有:
⑴以适当数量视图,按一定比例画出机床所有部件、零件、通用件、标准件等完整表明装配关系。
⑵运动零件的极限位置及行程开关,应在图中表示且完整。
3.2选择动力部件:
影响动力部件选择的主要因素有切削功率、进给力、进给速度、行程、主轴轮廓尺寸、动力滑台导轨形式等。
查《组合机床简明手册》表5-39可得.
电机型号IY132S-4功率5.5KWL3=395mm
n电=1440r/minn出=720r/min
⑴动力滑台查《毕业设计指导书》表4-11
HY40IA型
⑵配套通用件:
底层座CC401
⑶机床的架料高度;
H=200+320+560=1080mm
3.3总装图的技术要求
⑴本机床为批量生产CK-Ⅱ型数控车床主轴床。
⑵本机床安装调试时,其导轨水平面度控制在0.5%mm以内,如钻一安装在多轴箱的定位导柱中心线的同轴度控制在±
0.05mm以内。
⑶本机床的夹具和工作台进给液压系统采用25-8MPa/m压力,工作进给速度为125-500mm/min,但不小4mm/min,以免油路系统产生爬行,影响产品质量。
⑷本机床用20#-40#机油润滑,每三年定期更换一次。
⑸本机床内表面涂上红色硝基防锈漆,其外表面涂遍油漆腻子和底漆进行,次打磨,一次水磨抛光,烘干后进行喷漆烘干,主色为翠绿色。
⑹本机床一件产品所需时间3.297min,年产6万台。
3.4总图中液压系统的设计:
⑴动力滑台控制的液压原理图:
动力滑台控制的液压系统是一种以速度变换为主、最高工作压力不超过6.3MPa的中压系统。
⑵液压夹紧元件示意图:
液压夹紧力的计算:
油缸压力F油=P(s活+s杆)
=18×
(60-30)
=540
作用在工件上的正压力P2
F油l1=P(l1+l2)
p2=F油l1/(l1+l2)
=540×
1.5/(1.5+1.8)
=246N
l1.l2由上图知
l1=1.5mm
l2=1.8mm
颠覆力矩:
2×
P2×
p/2>
F切消力Xh
246×
300/2>
2930×
200
即:
73800>
58460
4.生产效率计算卡:
根据选定的机床工作循环所要求的工作行程长度,切削用量,功力部件的快速及工进速度等,就可以计算机床的生产效率计算卡,用以反映机床的加工过程.完成每一次动作所需时间,切削用量,机床生产率及机床效率,机床负荷率.
4.1理想生产率Q
Q=A/K=6×
104/4600=13.04件/时
4.2实际生产率Q1
Q1=60/T单
T单生产一个零件所需时间.
T单=t切+t辅=(L/Vt+力停)+(L快速+L快退/V+K+力停+T装卸)
L1、L2分别为刀具第Ⅰ、Ⅱ工作进行形程长度
L1=40
Ut1=24m/min
Uf1=6m/min
T移=0.1min
大装卸0.8min
T单=(40/24+8×
60/720)+(142+200)×
10-3/6+0.1+0.8
=1.67+0.67+0.057+0.1+0.8
=3.297min
所以Q1=60/t单=60/3.297=18.19/件
Q1>
Q
所以切削刀量与机床设计方案合理
4.3负荷率Y负
y=Q/Q1=13.04/18.19=0.72
4.4机床的生产效率计算卡
被加工零件
图号
A3
毛坯种类
铸 件
名称
CK-Ⅰ型数控车床主轴箱箱体
毛坯重量
材料
HT200
毛坯硬度
HBS170-240
工序名称
钻6-ø
17孔
工序号
13
序
号
工步
被加工零件数量
加工直径(
)
加工长度
工作行程
切削速度
m/
min
转
速
进刀量
工时(min)
mm/r
mm/
机动时间
辅
助
时
间
共
计
1
装卸工件
0.9
动力部件
滑台快进142
0.024
钻6个ø
17
40
24
720
0.20
89.9
2.34
滑台快退
0.033
备
注
1.双班制:
8.37万件每年,满足6万件/年的要求。
2.装卸工件时间取决于操作者的熟练程度,对本机床,计算时取3min生产一件。
总计
3.297min
单件工时
机床生产率
18.19件/h
机床负荷率
72%
四、组合钻床的专题设计
(一)组合机床的主轴箱传动系统设计
主轴箱的传动系统设计就是通过一定的传动链把动力箱输出轴传来的力分配到各主轴.
∵n0=720r/min
又∵n主=u.1000/π.D
=24×
1000/(3.14×
17)=449r/min
∵n0×
(Z1/Z2)×
(Z0/Z0,)=ni
Mi(Z1+Z1,/2)=DL/2
取:
Z0=24,M=3,M,=2,ΦL=150
Z1=45.Z1,=30
∵Z0,=720×
4×
Z1/(Z1,×
49)=57.7≈57
2.验算
A=∣n实-n理/n理∣<
5%
N主=720×
(24/57)×
(45/30)=454.73r/min
N主=449r/min
A=(454.73-449)/49
=1.23%<
经验算合理
Z0=24M=3D0=72
Z0,=57M=3D0=171
Z1=45M=2D1=90
Z1,=30M,=2D1,=60
3.主轴传动轴上齿轮强度效核
效核小齿轮Z0=24M0=3
大齿轮Z0,=57M=3
按《机械设计》为指导校核齿轮的模数齿厚.按齿根弯曲强度设计.其公式为:
m≥{2×
KT1×
(YFa×
Ysa/[δ]F)/ФdZ12}1/2
=2.94∴m=3
1)确定公式内的各计算数值:
①10-20d查得大小