IE工程师年工作总结表Word格式.docx
《IE工程师年工作总结表Word格式.docx》由会员分享,可在线阅读,更多相关《IE工程师年工作总结表Word格式.docx(18页珍藏版)》请在冰豆网上搜索。
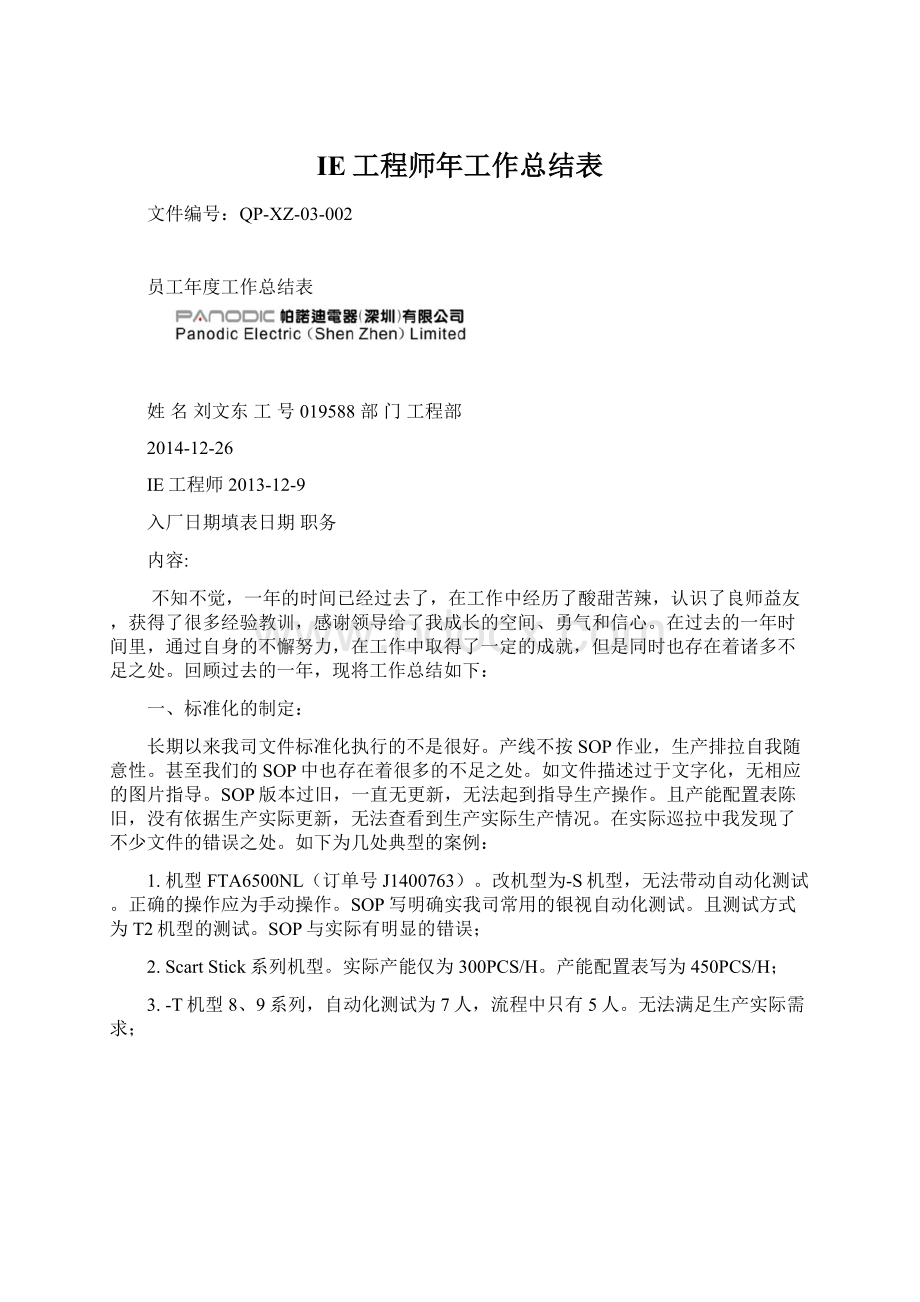
文字过多,且存图文不符在错别字文件版本过低,无需为带手套作改工序2011业,SOP年编制发布中要求带手套
图片
无图片指不全
5.生产人员不按SOP操作。
生产排拉随意性。
如DT-3050HD机型,,流程中装锁主板工位。
第一次生产工序为1人装主板,1人锁主板。
第二次生产更改为装锁主板2人操作。
第三次生产排拉时又变成1人装主板,1人锁,反复中,没有严谨的按照标准操作。
DVB-T2PRO-HD机型包装段贴贴纸位置为1工序粘贴贴2张贴纸。
标准人力为10人。
但生产为1人粘贴1张贴纸,实际包装人员16人。
以下为生产未按标准化操作,包装人员超过流程编制6人,导致生产平衡率差,人员处于等待状态:
综上,需规划标准化文件且需严格要求生产标准化生产。
6.文件及产能标准化与统计改进实施步骤:
阶段实施方式工时测试及汇总结果
统计实际产能工时测量工序平衡性分析第1阶段
更改作业手法阶段第2流程改进动作分析
制定新的流程改善后工时测定流程改进第3阶段现场排拉,指导生产按照新的产能统计第4汇总阶段,优化流程及作业方式操作
第5阶段修改SOP及更新产能配置表标准化,执行
第6阶段核查及矫正矫正生产严格按照SOP作业标准化操作
经过以上阶段的实施,以更新最新的工程文件发放生产。
文件规范化。
严格监督员工按照SOP作业,并检查SOP中的质量。
经过一段时间的优化跟进,以重新更新新的工程文件,重新制作与发放。
将版本过低或者有明显错误的工程文件回收。
同生产相关人员重新探讨相关流程问题。
从而使SOP及相关工程文件符合生产需求,并达到指导员工生产操作的作业,进而达到生产标准化的目标。
以下为更新后SOP图片:
增加防静电标示
文字简明,通俗,易懂
看图说话
同时,考虑的生产过程中产品因结构变化,软件变更,客户要求及其他等因素的变更,需重新更新相关文件。
特制定了工艺流程图:
工艺变更流程图
确认异常内容
回收旧文件
异常分析
发放新文件
确认异常NG
文件登记
工艺变更申请
OK
生产使用
更改工艺文件更改工艺文件NG
文件审核
文件受控
通过与生产、品质共同执行,SOP的问题已完成。
能够符合生产实际需求,且产能配置表依据实际生产变化不断更新。
使之达能显示生产实际需求。
在新机首次大货时与生产、品质共同讨论,制定合理的流程。
目前,生产以严格按照SOP作业,无无SOP及SOP明显错误的现象。
依据产品结构,并根据样机制作新机型SOP,及依照产品变更等方面因素更新相关文件。
以下为本年度制作及更新文件统计汇总:
月份1月2月3月4月5月6月7月8月9月10月11月12月汇总
新制153
11
8
作8
15
12
21
20
更新39
3
4
1
0
5
文件7
完成100%
100%100%100%
率100%
100%100%100%100%100%
100%
其他标准化的设定:
1.电动起子扭力标准的设定:
依据生产实际经过验证,规范化电动起子扭力范围如下
锁主板扭力值:
5±
0.5kgf/c㎡;
塑胶外壳扭力:
3±
五金金属外壳扭力值:
0.5kgf/㎡
特殊螺丝扭力值标准设定如下:
PA2*6螺丝:
电批力距控制在1.8+/-0.3kgf/c㎡;
PA1.4*8螺丝:
2.总装焊接烙铁温度范围标准值:
烙铁温度由之前的320℃-390℃修改为380±
10℃;
(无铅锡丝焊接烙铁温度)
3.设定SMT产能核算公式:
(板卡点数)
SMT产能统计与实际不符合,产能配置表无法显示实际的SMT产能;
公式:
CHIP点数/16666=单机工时
备注:
机器工作能力50000点/小时一条拉3人即每人1小时50000/3=16666个点
以下为SMT实际生产产能与统计对比:
生产日期板卡名称实际产能(PCS/H)统计产能(PCS/H)差异
19235216DGQ300F解码板(MC6396-01#)9Oriel790解码板(MC6454-01#)1543月3号163
2100102解码板正面(PCH2862MC6310-01#)21137MC6404-01#解码板()15893014号3月12152164RT0407HD解码板(MC6387-01#)
3152)149T303SD解码板(MC63525号3月5
)RT0140U解码板(MC6395-01#98
93
以CHIP点数/16666=SMT工时作为SMT工时导入计算方法可以发现:
产线实际生产的产能与IE制定的产能标准相比产能前后相差不超过20PCS,当机器每小时点数超过50000时实际产能比IE产能高,反之机器每小时点数低于50000时实际产能比IE产能低,这是完全合理的。
二、改善方案
本年度乐视2次生产改善。
通过2次改善在人员减少的情况下产能由150PCS/H,提升到目前的250PCS/H。
乐视产品第1次改善:
产能由150PCS/H提升到200PCS/H,单机工时由0.186H减低到0.135H,生产效率提升13.77%。
装配拉流程调整,改善前后流程对比如下:
改善前
改善后
序列
工位
人员
序列
工位
取上盖,外观检查
2
装锁前控板
装wifi天线,插前控板排线
天线,插前控板排线装wifi
装锁前控板
天线到主板,装主板wifi插
插wifi天线到主板,装主板
锁主板螺丝
锁主板螺丝
6
扣下盖
扣下盖,外观检查,装机
人员和产量对比人员:
产量:
单机工时:
测试段改善:
wifi测试”检查27.12wifi号强度是否为满格。
消耗工时
USB+改善前操作步骤:
耗费工时
改善后操作步骤:
时
人员和产量对比—测试段:
1.工作业轻松,提高生产效率;
2.3.4.
1.拉作业;
2.化产能;
流程对比(包装段)
7
外观检查,取机,装机
--装配段由原来的7人精简为现在的6人由原来的180PCS/H增加到220PCS/H由原来的0.038H降低为0.027H效率:
提升14.07%选择“wifi,整机连接服务器后按遥控器返回键进入菜单键测试工站改善前操作步骤:
整机自动进入乐视网页检查码流播放是否顺畅。
消耗工时50.wifi信号强度不低于″。
检查“dlink”信:
机进入菜单选项,选择“网络”,打开wifi测试工站改善后操作步骤16.25″高清工位和光纤,AV和USB1工位:
开机后进入乐视菜单界面,取遥控器选择“媒体中心-外接存储1”选择视频文件。
26.53″设定产测软件,开机后直接进入菜单界面“视频”菜单,选择视频文件。
耗费工16.42″通过调整,生产平衡率明显提高。
流水线无堆积,流水线生产顺畅。
同时因为操作步骤简化,员人员:
由7人操作减少为6人操作,节约1人力成本;
生产产能由原来的150PCS/H,提升到200PCS/H;
单机工时由0.04H降低到0.03H,效率提高13.33%包装段改善设计方案:
增加附件加工为。
将装遥控器,电池,HDMI线和适配器工序移到线外皮带改进包装结构,使之优化包装操作手法。
即将遥控器和电池放置在同一面。
减少了动作时间,优
外观检查
拆彩盒,取彩盒附件拆附件彩盒装遥控器,电池
1111
拆包装,取包装附件
装电池,遥控器
线,适配器装HDMI
HDMI装线,适配器
内卡纸/装快速指南/贴纸MAC贴
将附件段加工产能
人员和产量对比—包装段:
与客户沟通改进包装方式后,装遥控器,电池由
产能:
改善汇总
乐视产品产品改善前1.2.3.4.
产品改善后:
1.2.3.4.
整机入彩盒,套包装上盖
贴纸套腰封/贴MAC/称重
贴MAC贴纸/称重套腰封/
红色字体的工序改为线外加工,线外操作,在生产前提前将附件包装好。
:
400CS/H2人减少为1人;
由150PCS/H,提升为200PCS/H;
:
由0.046H增加到0.02H;
效率:
提升23%;
附件加工同时供应2条拉,即人员由8人精简为4人。
改善前改善后
2730总装人数
200pcs/H150pcs/H总装产能
0.135H
0.2H单机工时13.77%提高效率
0.065H每台节约时间
/PCS0.714元每台节约成本
节约成本/年464100元65万订单)(每年约NewC1S第2次改善:
装配工段拉平衡率过低;
测试工作岗位重复动作,无效动作过多;
生产平衡率过低,产线有过多的MIP,影响生产产能;
产能:
200PCS/H单机工时:
0.15H;
生产平衡率提高,产线无堆积的状态;
简化作业方式,优化流程,减少生产人员劳力;
产能:
250PCS/H单机工时:
0.12H生产效率提升:
20%
流程及工时对比(装配段)
改善前改善后
人序工时序人工时工位工位员(秒)员(秒)列列19.87119.87取上盖,外观检查1取上盖,外观检查
2装锁前控板2装wifi天线,插前控板排线1110.018.45
3装锁前控板15.86
wifi3装天线,插前控板排线119.35
4插wifi天线到主板,装主板110.154插wifi天线到主板,装锁主板233.24
55锁主板螺丝10.42扣下盖,外观检查,装机112.671
119.35
12.67
6扣下盖,外观检查,装机6
--装配段:
拉平衡对比改善前:
?
拉平衡率=[(9.87+10.01+15.86+16.62+16.62+12.67)/(16.62×
6)]×
100%=81.88%
改善后:
拉平衡率=(9.87+8.45+9.35+10.15+10.42+9.35)/(10.42×
6)]×
100%=92.11%
产量和效率对比--装配段
在人员不变的情况下产能由220PCS/H,升到300PCS/H
由0.027降低为0.02效率提升:
26.67%
设计方案(测试段)
1.人机结合法,生产工位增加电源插座。
作业时整机测试时生产人员将下1PCS整机连接电源线。
减少开机等待时间和测试时间
2.烧录和复位工序等待时间过长。
人员长期处于等待状态。
针对此现象将该工位分解为2工序操作,即烧录工序和恢复出厂设置工序。
优化生产平衡率。
产测软件改善
改善前:
测试进入菜单界面工作步骤:
按遥控器“上下左右+OK”按键—进入系统界面—按遥控器“菜单”按键—选择菜单界面
整机通电开机后直接按遥控器“设置”按键即可进入菜单界面
测试段改善前后工时对比:
改善后改善前
序人工时序人工时工位工位员列(秒)列(秒)员113.01
1USB1,高清测试113.011USB1,高清测试
2光纤,AV,USB2测试112.452光纤,AV,USB2测112.45
试
3wifi测试116.273wifi测试111.59
112.76
蓝牙,SD卡测试15.484蓝牙,SD卡测试14
5打印底板贴纸,贴底板116.445打印底板贴纸,贴底113.84
贴纸板贴纸
6烧录,打印流水号贴纸115.846烧录,打印流水号贴112.68
纸
7检查软件版本,复位116.667检查软件版本,复位111.85
8复位检查116.858复位检查112.76
改善前后对比—测试段
改善前:
0.04
改善后:
0.032效率提升:
设计方案—热缩段
流程对比如下
取彩盒,装热缩膜(1人)热缩热缩膜(2人)热缩膜外观检查(1人)核对流水号(1人)—装箱,摆板
(1)
取彩盒,投彩盒(1人)—核对流水号(1人)—装箱,摆板(1人)
导入热缩设备热缩,热缩工位人员由6人减少为3人,产能由250PCS/H提升到550PCS/H.热缩膜工段由原先满足1条拉生产提升为满足2条拉生产。
改善汇总
总装产能
200pcs/H
250pcs/H
单机工时
0.15H
0.12H
提高效率
每台节约时间
0.03H
每台节约成本
/PCS
元0.45
节约成本万订单)(每年约65
292500元/年
以下为其他机型改善前后效果对比:
改善前改善后序人数UPPH提升幅度产HPPH人数能号机型产能1OpticumAXLion
333512.8615.1545015.12%500
PCH-280B383.421304037.80%5.50220
DVB-934003716.67%4803712.9710.81
DVB-90403812.0048010.5340012.28%
SD-0126261301805.006.9227.78%
E21133015.005003010.00%16.67450
DCT-280HD232209.572313040.91%5.65
8RCG-Miniline-C
7.333018018.18%6.0030220
9
SRT81069.52%5.24425.7938220220
10
RT5130HR3412.6543014.00%50014.7134
LYHC-HC120740.13%
200
35
38
3.42
130
5.71
经过一年来共同的努力,生产平衡率明显的提升。
目前平衡率总体保持在87.52%,比去年84.27%提升了3.71%。
其中8、9系列机型平衡率稳定在90.45%范围内。
产能和效率有明显的提升。
三、工作中遇到的问题
1.由于我司的产品机型较多,开展工作时对部分机型的产能和流程设计上不大合理,影响生产的实际操作。
目前的状况是,在新机首次导入时现在跟进,依据产品结构状态及测试软件产能重新核实产能及流程。
汇总后修改SOP后再次重新发放
2.信息不顺畅。
在机型大货时,我依据试产时的机型状态制作SOP,但实际中大货机型结构、软件的变更与试产中的变化很大,因而制作的SOP及产能与实际不对应
3.EV直接大货,且在大货前无样机提供,导致大货生产时工程部才能知晓整机状态,无法提前对该机型预估
4.机型过多,同时相应的SOP也很多。
在生产过程中因研发更改、客户要求和软件方面的原因。
文件未能及时更新
以上,会在今后的工作中加强各部门的沟通,并在生产前验证机型及相关文件,争取克服,努力改进!
四、展望及来年计划
未来的一年时间,结合工作的实际及运用,继续完成精益生产、现场IE管理、文件标准化和试产持续跟进中。
将在实际的生产过程中导入六西格玛等生产方面的理念,产品持续改善中。
1.发扬在工作中遇到问题时的问题观,再错误中学习、改进及预防错误的思维;
2.学习整机异常的分析,多学多问,艺多不压身;
3.在标准化中持续更进,制程文件化、流程顺畅化、员工操作简单化和效率的不断改进;