广东省表面涂装汽车制造业挥发性有机废气治理技术指南设计粤环号Word格式文档下载.docx
《广东省表面涂装汽车制造业挥发性有机废气治理技术指南设计粤环号Word格式文档下载.docx》由会员分享,可在线阅读,更多相关《广东省表面涂装汽车制造业挥发性有机废气治理技术指南设计粤环号Word格式文档下载.docx(16页珍藏版)》请在冰豆网上搜索。
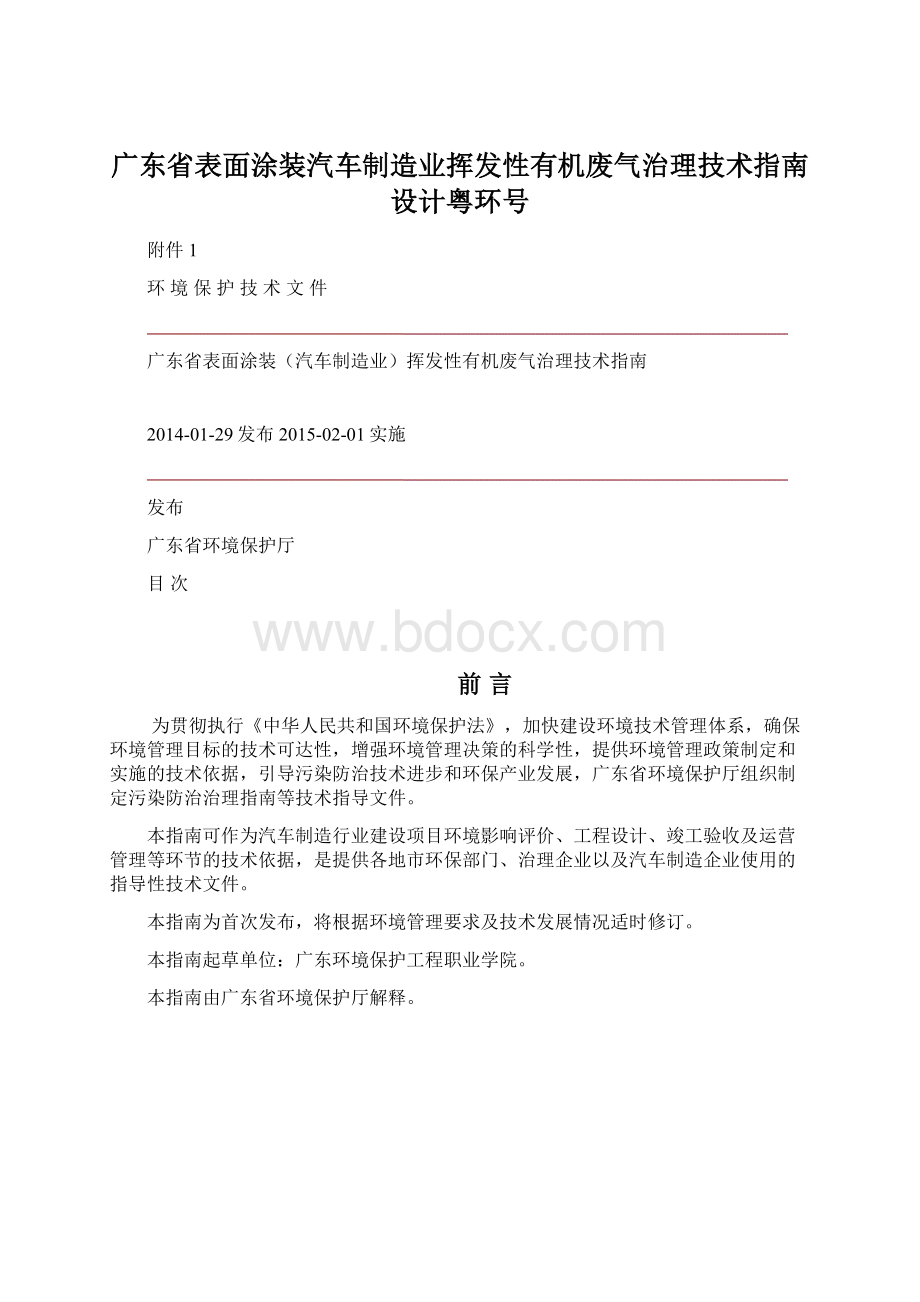
[3]《关于珠江三角洲地区严格控制工业企业挥发性有机物(VOCs)排放的意见》
[4]《广东省珠江三角洲地区大气污染防治“十二五”规划2013年度实施方案》
[5]《重点区域大气污染防治“十二五”规划》
[6]《挥发性有机物(VOCs)污染防治技术政策》
[7]《吸附法工业有机废气治理工程标准规范》(HJ2026—2013)
[8]《催化燃烧法工业有机废气治理工程标准规范》(HJ2027—2013)
[9]环境保护产品技术要求工业废气吸附净化装置(HJ/T386-2007)
[10]环境保护产品技术要求工业废气吸收净化装置(HJ/T387-2007)
[11]环境保护产品技术要求湿法漆雾过滤净化装置(HJ/T388-2007)
[12]环境保护产品技术要求工业有机废气催化净化装置(HJ/T389-2007)
[13]《汽车涂料中有害物质限量》(GB24409-2009)
[14]《涂装作业安全规程涂漆工艺安全及其通风净化》(GB6514-2008)
[15]《涂装作业安全规程喷漆室安全技术规定》(GB14444-2006)
[16]《涂装作业安全规程有机废气净化装置安全技术规定》(GB20101—2006)
[17]《涂装作业安全规程涂层烘干室安全技术规定》(GB14443—2007)
[18]《涂装作业安全规程喷漆室安全技术规定》GB14444—2006
[19]《涂装作业安全规程浸涂工艺安全》(GB17750-2012)
[20]《涂装作业安全规程涂漆前处理工艺安全及其通风净化》(GB76922012)
1.3术语和定义
1.3.1汽车
由动力驱动,具有四个或四个以上车轮的非轨道承载的车辆,载运人员和/或货物;
牵引载运人员和/或货物的车辆;
其他特殊用途的车辆。
1.3.2表面涂装
为保护或装饰车体,在其表面覆以膜层的过程。
1.3.3挥发性有机化合物
在101325Pa标准大气压下,任何沸点低于或等于250℃的有机化合物,简称VOCs。
1.3.4烘干室
加热、烘烤使车体表面涂料产生聚合、干燥或固化的场所。
1.3.5流平室
密闭、清洁的、有一定空气流速的室内空间,使喷漆后涂装表面漆滴摊平,溶剂挥发的场所。
2涂装工艺及VOCs排放
2.1涂装工艺
2.1.1轿车、商务车涂装工艺
轿车、商务车一般采用流水线生产方式,在现代化的涂装车间进行整车涂装。
汽车车身的涂膜由底漆层、中间涂层(简称中涂)、面漆涂层(简称面涂)等组成,涂层的总厚度一般为80~120μm。
(1)底漆层
汽车底漆是直接涂敷在经过表面预处理工件表面上的第一道漆,是整个涂层的基础。
当前广东省轿车底漆涂装基本采用环保型水性阴极电泳涂料进行阴极电泳浸涂。
载重车、客车等则大多采用溶剂型底漆进行手工喷涂。
(2)中涂、面涂层
汽车中涂、面涂工艺传统是“3C2B”工艺,近几年开发了“3C1B”涂装工艺以降低汽车涂装成本和VOCs的排放量,另有新的涂装工艺,将正常的中涂层取消,采用免中涂的2C1B工艺。
三种工艺流程及各涂层的厚度如图1所示。
图1轿车涂装工艺
部分企业中涂采用水性涂装工艺,由于水性溶剂挥发慢,其工艺与油性漆涂装稍许不同,主要在“3C1B”工艺中涂之后或者是“2C1B”工艺底色漆1之后增加一段闪干工段(闪干室)加快水性涂料的干燥,车间温度60~80℃。
2.1.2载重车、客车涂装工艺
载重车、客车等涂装工艺以底漆、面漆两层涂装为主,但已逐渐趋同于轿车涂装,目前主要的涂装工艺流程有三种,如图2所示。
(a)
(b)
(c)
图2载重车、客车等涂装工艺
2.1.3涂装技术
我省轿车制造的中涂、面漆涂装过程大致相同,车身内表面多采用人工喷涂;
车身外表面采用自动静电喷涂,个别先进的生产线车内外表面均采用机器人喷涂,少数产量相对小的企业内外表面仍采用全人工喷涂。
载重车、客车等以手工静电或空气喷涂方式为主。
静电喷涂涂料利用率高,约为60~70%,人工空气喷涂涂料利用率约为30~40%。
2.1.4汽车制造其他工序
汽车制造喷涂过程中还设置维修喷涂,对部分漏喷的车身进行补喷。
汽车在原厂的维修喷涂和补漆工艺主要为漆前表面处理、补灰、喷漆和补漆、烘干。
2.2VOCs产生与排放
涂装过程需用到涂料、稀释剂、固化剂、清洗剂等含VOCs原辅材料,在涂装、烘干过程中有机溶剂挥发出来污染环境,如图3所示。
另外还包括车身的后续补漆和塑料件加工的涂漆工序。
图3汽车制造VOCs来源
各涂层采用的涂料类型有油性涂料、水性涂料和粉末涂料等。
油性涂料可分为低固体分(20-45%)、中固体分(接近46-59%)和高固体分(60%或以上)。
高固体分即用状态下VOCs含量约30-40%,中低固体分约为40-80%。
水性涂料VOCs含量<10%。
目前我省汽车制造业涂料使用概况如表1所示。
表1各涂层涂料使用概况
涂料功能
类型
主要用漆类别
应用情况
底漆
阴极电泳漆
水性阴极电泳漆
轿车、商务车基本使用水性电泳漆、少部分载重车也有使用。
油性底漆
环氧树脂漆等、醇酸环氧氨基
载重车、客车等使用。
中涂
油性漆
聚酯树脂、环氧树脂、氨基树脂、聚氨酯树脂、醇酸树脂等
载重车、客车等使用,国内品牌车、中小企业采用,部分中外合资轿车生产企业采用。
水性漆
双组份聚氨酯、丙烯酸氨基树脂等
外资、中外合资轿车生产企业基本都采用水性漆。
粉末涂料
环氧聚酯混合型、聚酯型、聚氨酯型、丙烯酸型等
目前应用较少。
底色漆
聚氨酯、丙烯酸树脂、氨基醇酸树脂、氨基树脂、聚酯氨基树脂等
载重车、客车等使用,国内品牌车、中小企业采用油性漆。
罩光清漆
丙烯酸氨基树脂、聚氨酯、等
不同类型车基本都采用油性漆。
双组份聚氨酯等
修补漆
油性涂料
聚氨酯、丙烯酸树脂、环氧树脂等
水性涂料
丙烯酸树脂、聚氨酯树脂等
汽车涂装过程VOCs的产生量主要由涂料种类,涂装设备工艺水平和企业溶剂管理决定。
中涂、面涂过程中,约80-90%的VOCs在喷漆室和流平室排放,10-20%的VOCs随车身涂膜在烘干室中排放。
溶剂型涂料体系的VOCs主要来源于底色漆,其次来源于清漆和中涂,还有少量来源于清洗溶剂。
一般来说,对于中低固体分的涂料体系而言,色漆VOCs占总VOCs的50%左右、清漆占35%、中涂占15%。
表面积为80m2左右的普通轿车用单位涂装面积排出的VOCs量(g/m2)表示,平均为125gVOCs/m2。
当涂装生产线为水性涂料化时,电泳、中涂、底色涂采用水溶性涂料涂装,仅罩光清漆采用溶剂型涂料,VOCs可大量降低,达到30gVOCs/m2以下,最低可降到12~13gVOCs/m2。
喷漆、流平室产生的是常温有机废气,风量大、浓度低;
烘干室产生的有机废气风量小,浓度高,为高温气体。
我省汽车制造业涂装工序VOCs废气特点及收集方式如表2所示。
表2汽车制造业涂装工序VOCs废气特点及收集方式
工序
废气特点及收集方式
电泳漆浸涂
常温、常压气体,整个工序封闭,跟外界换气
涂装工序
油性底涂(载重车、客车等)
整个工序封闭,通过抽风机排出,常温常压废气,流水线长,废气排放量大,在15万-70万m3/h,废气浓度低
烘干工序
电泳烘干
密闭式,通过抽风系统集中排放,废气温度140℃左右,废气排放量小,在3000-60000m3/h,废气浓度相对较高
中涂烘干
罩光清漆后烘干
汽车制造业涂装工序产生VOCs成分与所使用的原辅材料直接相关,主要包含芳香烃类、醇类、酯类、醇醚类,还有少量的酮类。
3表面涂装(汽车制造业)VOCs防治技术推荐
表面涂装(汽车制造业)属于溶剂产品使用源,VOCs污染防治可从源头控制、过程控制、末端治理三方面着手。
3.1源头控制
源头控制主要指低VOCs原辅材料的使用,可行技术及主要技术指标见下表3。
表3表面涂装(汽车制造业)VOCs源头控制可行技术
涂层
可行技术
潜在可行技术
应用范围(或要求)
水性电泳漆
——
适用于所有汽车。
高固分底漆
适用于暂时无法使用水性电泳漆的车型,需安装废气治理设施。
水性中涂漆
高固分中涂
适用于暂时无法使用水性中涂漆的车型,需安装废气治理设施。
水性底色漆
高固分底色漆
适用于暂时无法使用水性底色漆的车型,需安装废气治理设施。
清漆
高固分罩光清漆
适用于所有汽车,需安装废气治理设施。
水性清漆
水性修补漆
密封胶
PVC胶
备注:
粉末涂料指VOCs含量≤0.5%的涂料,高固分漆指即用状态下VOCs含量≤30%,水性电泳漆指即用状态下VOCs含量≤1%,水性中涂漆、底色漆、清漆指即用状态下VOCs含量≤10%。
3.2生产过程控制
生产过程控制包括生产工艺改进、提高废气和漆雾的捕集率。
3.2.1生产工艺改进
汽车制造业表面涂装工艺改进的可行技术如表4所示。
表4生产工艺改进可行技术
可行生产工艺
应用范围(或技术要求)
水性3C1B工艺
所有汽车类型。
水性免中涂2C1B工艺
油性3C1B工艺
适用于暂时无法使用水性涂装工艺的车型,需安装废气治理设施。
油性免中涂2C1B工艺
3.2.2废气收集
为减少无组织排放,最大限度的控制VOCs排放量,需做好有机废气收集工作。
(1)应规范涂料、稀释剂、固化剂、密封胶、清洗剂等含VOCs原辅材料的使用,限定区域存放。
选用密封式调漆罐调漆,通过压力泵、管道输送涂料到喷漆位,否则在调漆点安装废气收集系统。
生产过程及生产间歇均应保持盛放含VOCs原辅材料的罐密封;
(2)清洗过程中产生的废溶剂宜密闭收集,有回收价值的废溶剂经处理后回用,其他废溶剂应妥善处置;
(3)涂装工艺线(所有的喷漆、喷胶、修补环节)应密封,换气风量根据车间大小确定,一般手工喷涂区段风速为0.35~0.50m/s,自动静电喷涂区段风速为0.25~0.30m/s,擦净间风速为0.20~0.30m/s。
因涂装工艺线距离长、风量一般为几十万立方米,抽风能耗高,若中小型企业操作困难,可采用分区段收集废气,但均应保证VOCs废气捕集率不低于95%;
(4)闪干室、流平室、烘箱应密封,换气风量根据车间大小确定,流平室及连接烘干室的防尘通道一般风速为0.1-0.2m/s,保证VOCs废气捕集率不低于95%;
(5)废气收集经漆雾处理后需进入治理设施,可分车间单独处理,也可多车间废气集中到同一治理设施处理;
(6)废气收集系统应保证与生产同时正常运行;
(7)废气收集系统材质应防腐防锈,定期维护,存在泄漏时需及时修复;
(8)废气捕集率评价方法:
按照车间空间体积和60次/小时换气次数计算新风量,以有组织排放的实际风量与车间所需新风量的比值作为废气捕集率。
当车间实际有组织排气量大于车间所需新风量时,废气捕集率以100%计。
3.2.3漆雾捕集系统
喷漆室的除漆雾(尘埃)效果应达到:
(1)除去效率:
95%以上;
(2)颗粒物排出量:
<
10mg/m3,若后处理设施有相关标准要求,按标准要求;
(3)目测见不到排风管的排气色(即排风管出口风帽不被所喷涂料着色);
(4)湿式漆雾捕集系统应对水进行循环利用,减少耗水量,废水需处理后达标排放,漆渣(HW12,HW49)应统一收集后交由有资质的危险废物处理公司处理。
漆雾捕集装置一般设置在喷漆室的格栅底板下或喷漆室一侧的排风通道中,包括干式和湿式漆雾捕集装置,可行技术见表5。
表5漆雾捕集系统可行技术
名称
干式漆雾捕集系统
过滤棉、无纺布等
适用于涂料用量少的涂装线。
石灰石为滤料
静电漆雾捕集装置
适用于涂料用量大的大批量生产涂装线。
湿式漆雾捕集系统
湿式漆雾捕集装置
3.3废气治理
3.3.1废气采样口建设要求
治理设施应在废气处理前后设置永久性采样口,采样口的设置应符合《气体参数测量和采样的固定位装置》(HJ/T1-92)要求。
采样口应优先设置在垂直管道,避开烟道弯头和断面急剧变化的部位,距弯头、阀门、变径管下游方向不小于6倍直径,和距上述部件上游方向不小于3倍直径处。
对矩形烟道,其当量直径D=2AB/(A+B),式中A、B为边长。
采样口所在断面的气流速度最好在5m/s以上。
若现场条件有限很难满足上述要求时,采样口所在断面与弯头等的距离至少是烟道直径的1.5倍。
采样平台应有足够的工作面积使工作人员安全、方便的操作。
平台面积应不小于1.5m2,并设有1.1m高的护栏和不低于10cm的脚部挡板,采样平台的承重应不少于200kg/m2,采样孔距平台面约为1.2m~1.3m。
3.3.2治理技术推荐
VOCs治理技术种类较多。
传统的有吸附法、吸收法、燃烧法、冷凝法,联用技术有吸附-冷凝回收、吸附浓缩-催化燃烧。
新技术主要有低温等离子体技术、光催化氧化、生物法、膜分离技术等。
从方法原理与应用实例来看,以上技术均有一定的治理效果。
关键是治理设施技术参数符合设计要求、与企业工况匹配、后期运行管理规范合理。
表面涂装(汽车制造业)VOCs废气可分为两部分,一部分为烘干废气,温度在140℃左右,风量在3000-60000m3/h,属于中小风量高浓度废气。
另一部分为喷涂废气,为常温常压,风量在15万-70万m3/h,属于大风量低浓度废气。
废气成分复杂,主要为芳香烃、醇醚类、酯类、醇类,还有少量的酮类,无回收价值。
根据表面涂装(汽车制造业)有机废气排放特点及治理技术的适用性,本指南推荐表6中的治理技术。
优先选择蓄热式直接焚烧法(RTO)技术进行高浓度废气的处理、吸附浓缩-(催化)燃烧法进行低浓度废气的处理。
吸附法处理废气不能单独使用,需与其他可行的技术进行联合应用,吸附剂需定期更换,保证处理效率。
对于吸附法,包括联用技术中采用吸附法,除有配套脱附装置,都应安装VOCs在线监测仪器,以便实时监测吸附剂的饱和更换情况。
表6表面涂装(汽车制造业)VOCs治理技术推荐
治理技术
单套装置适用气体流量范围(m3/h)
适用VOCs浓度范围(mg/m3)
适宜废气温度范围(℃)
适用生产工艺
蓄热式直接焚烧法(RTO)
<100000
1000~1/4LEL
<800
适用于烘干室、闪干室废气。
蓄热式催化燃烧法(RCO)
<5000
<350
吸附浓缩-(催化)燃烧法
10000-180000
100-2000
<45
适用于喷涂、流平室废气。
吸附法
1000~60000
200
对上述治理技术进行经济成本和环境效益分析,结果如表7所示。
表7典型治理技术的经济成本和环境效益分析
单位处理能力初次投入
万元/(10000m3/h)
处理单位气体年运行费用
可达治理效率(%)
30~60
1~2
>95
80~120
100~120(包含VOCs自动在线监测系统)
20~35
50~90
在不产生二次污染,治理效率高,能耗低的基础上,也鼓励新的治理技术的开发应用。
3.3.3各类治理技术的应用要求
为持续保证设备的治理效率和使用寿命,需严格要求治理设备的设计、安装、施工及管理。
(1)热力氧化法(RTO、RCO)治理技术应用要求
RTO治理技术的安装与运行可参考《催化燃烧法工业有机废气治理工程技术规范》(HJ2027-2013),RCO治理技术的安装与运行符合《催化燃烧法工业有机废气治理工程技术规范》(HJ2027-2013)。
RTO与RCO应用需满足如下要求:
1)应根据废气的组成浓度,确定废气起燃温度、炉内停留时间,混合气体按照起燃温度最高的组分确定,确保有机废气燃烧完全;
2)蓄热体的使用寿命应大于24000h,换热效率达到90%以上;
3)换向阀的泄漏量能够控制在3%以下;
4)助燃燃料为清洁能源,燃烧过程中不产生二次污染,能根据炉内燃烧气体温度自动调节燃料用量,以节省燃料;
5)有机废气经处理后,排烟温度低于100℃;
6)实现PLC自动控制,具有实时监控系统、预警系统,具有防火防爆的安全措施;
7)RCO装置应明确催化剂的更换周期和后处理方式;
8)装置净化效率不得低于97%,废气排放达到《广东省表面涂装(汽车制造业)挥发性有机化合物排放标准》(DB44/816-2010)的规定。
(2)吸附浓缩-(催化)燃烧法治理技术应用要求
治理技术的安装与运行需满足《吸附法工业有机废气治理工程技术规范》(HJ2026-2013)和《催化燃烧法工业有机废气治理工程技术规范》(HJ2027-2013)。
吸附装置的应用要求同吸附法。
配套的原位再生手段(脱附)设施,应有规范的管理制度,明确再生周期,并有相应的记录。
(催化)燃烧法需满足如下要求:
1)需给出与废气浓度、吸附剂再生周期相适应的催化剂使用寿命,更换周期;
2)根据废气成分明确(催化)燃烧装置的起燃温度,确保废气温度达到起燃温度并燃烧完全;
3)燃烧过程产生的热量应进行回收,热能回收效率不得低于35%;
4)根据废气浓度、废气排放量、吸附剂的使用量以及企业的生产时间,明确吸附剂的再生周期,定期进行吸附剂再生;
治理设施能实现自动控制,安装有警报防火防爆装置,有应急处理方案;
5)吸附浓缩-(催化)燃烧装置的净化效率不得低于97%,废气排放达到《广东省表面涂装(汽车制造业)挥发性有机化合物排放标准》(DB44/816-2010)的规定。
(3)吸附法治理技术应用要求
吸附法治理技术的建设应符合《吸附法工业有机废气治理工程技术规范》(HJ2027-2013)的规定。
吸附法应用需满足如下要求:
1)具备完整的治理技术设计方案,保证吸附材料的正常可靠实用,注明所用吸附材料的吸附容量;
2)需给出与废气排放相适应的吸附材料使用寿命,明确吸附材料的更换周期,同时安装VOCs在线监测仪器,实时监测吸附剂的饱和更换情况;
3)为吸附法治理设施设定专门的管理人员(部门),确保吸附材料按时更换;
4)吸附饱和后被更换的吸附剂归为危险废物(HW12、HW49),需移交有资质的危险废物处理公司处理,应有规范的危险废物转移记录,便于核查;
5)吸附装置的净化效率不得低于90%,废气排放达到《广东省表面涂装(汽车制造业)挥发性有机化合物排放标准》(DB44/816-2010)的规定。
(4)其他治理技术应用要求
有机废气的处理方法仍在不断更新与改进,应用于汽车制造行业VOCs的治理也将可能出现以上所列方法之外可用的方法,如考虑溶剂回收,对于这些方法,同样需在设计方案、运行维护记录、是否产生二次污染、二次污染处理处置等方面提出具体明确的规范,以保证企业持续稳定的达标排放。
对于治理效率随耗材消耗降低过快的治理设备需安装VOCs在线监测仪器。
3.4治理技术监管要求
3.4.1企业管理要求
治理设施(包括漆雾捕集系统)的管理应纳入生产管理中,配备专业管理人员和技术人员,并对其进行培训,使管理和运行人员掌握治理设备及其它附属设施的具体操作和应急情况下的处理措施。
企业应根据实际生产工况和治理设施(包括漆雾捕集系统)的设计标准,建立相关的各项规章制度以及运行、维护和操作规程,明确耗材