插入耳环说明书Word文档格式.docx
《插入耳环说明书Word文档格式.docx》由会员分享,可在线阅读,更多相关《插入耳环说明书Word文档格式.docx(13页珍藏版)》请在冰豆网上搜索。
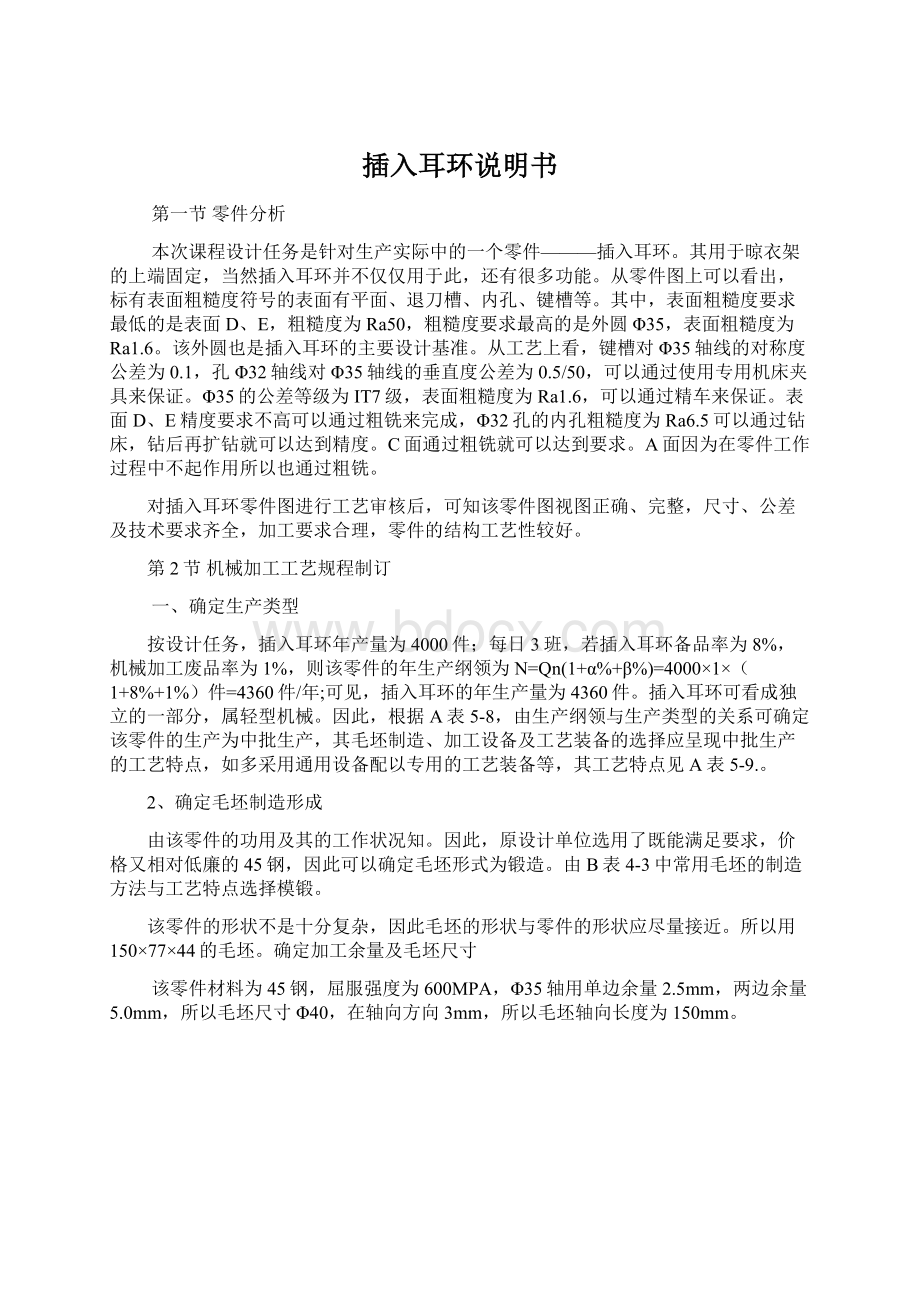
该零件材料为45钢,屈服强度为600MPA,Φ35轴用单边余量2.5mm,两边余量5.0mm,所以毛坯尺寸Φ40,在轴向方向3mm,所以毛坯轴向长度为150mm。
三、选择定位基准
定位基准的选择是工艺规程制订中的重要工作,它是工艺路线是否正确合理的前提。
正确与合理地选择定位基准,可以确保加工质量、缩短工艺过程、简化工艺装备结构与种类、提高生产率。
所以在做此零件时,我们选择Φ35轴线为基准,并且此基准为设计基准,即遵循“基准重合”的原则。
该基准还可作为大部分工序的定位基准,加工其他的次要表面,体现了“基准统一”的选择原则。
4、选择加工方法
1.平面的加工
平面的加工方法很多,有车、刨、铣、磨、拉等。
对于本零件由于表面D、E粗糙度为Ra50,通过粗铣就可以达到。
而对于C面粗糙度为Ra6.3通过粗铣也可以达到。
而表面A的粗糙度要求为Ra12.5根据GB/T1804-2000规定,选用中等级,相当于IT13级,故可考虑粗车或粗端铣。
2外圆与退刀槽、攻螺纹
外圆Φ35的加工在本零件中很重要。
本次选用CA6140车床,由于表面粗糙度Ra1.6,所以采用粗车-半精车-精车。
而对于外圆Φ27,表面要进行攻螺纹,所以进行粗车就可以了。
在粗车过后再用螺纹车刀进行攻螺纹。
3孔加工
Φ32孔内壁粗糙度为Ra6.3所以就用钻-扩,钻孔后扩孔就可以达到这个精度要求,满足安装配合E9,并且用YT锥柄麻花钻。
Φ5的销孔,直接用枪孔钻就可以加工出来。
4槽加工
对槽的加工,槽的要求为Ra3.2所以用X6132万能铣床,进过粗铣-精铣就可以达到。
5、制定工艺路线
制定工艺路线的出发点,应当是使零件的几何形状、尺寸精度及位置精度等技术要求能得到合理的保证,在生产纲领已确定的情况下,可以考虑采用万能性机床配以专用夹具,并尽量使工序集中来提高生产率。
除此之外,还应当考虑经济效果,以便使生产成本尽量下降。
1.工艺路线方案一:
工序05:
模锻毛坯
工序10:
45钢正火,为机加工作准备
工序15:
粗铣二边表面
由于表面粗糙度要求很低所以以任意端面为粗定位,用专用夹具夹紧,铣表面到尺寸。
工序20:
粗铣C面
由于C面有粗糙度要求所以用专用夹具夹紧,铣表面到尺寸。
工序25:
钻Φ32的孔
用专业的钻床夹具,进行钻孔
工序30:
扩Φ32的孔
为达到内壁粗糙度进行扩孔,满足精度要求
工序35:
粗车Φ35外圆
粗车毛坯Φ40到Φ36外圆,用专用夹具夹紧,粗车到规定尺寸
工序40:
粗车Φ27,倒角C1
在已经被粗车到Φ36的外圆上,用专用夹具夹紧,继续粗车相应尺寸到Φ27,并且倒倒角C1
工序45:
车退刀槽Φ24
在相应尺寸用切槽刀加工退刀槽Φ24,用专用夹具夹紧。
工序50:
进行热处理调质
工序55:
半精车Φ35
在粗加工过后进行半精加工,由Φ36的外圆车到Φ35.2
工序60:
精车Φ35
在半精加工后进行精加工,由Φ35.2的外圆到Φ35
工序65:
车锥面,倒角C2
进行车锥面,并且倒倒角C2
工序70:
攻螺纹M27×
1.5-6h
用螺纹车刀在Φ27外圆上进行攻螺纹
工序75:
钻Φ5的销孔
在螺纹规定尺寸处进行销孔的加工。
工序80:
粗铣键槽
用铣床专用夹具,进行键的加工。
工序85:
精铣键槽
用铣床专用夹具,进行键的加工
工序90:
铣A面
按照零件图规定铣A面
该方案中工序25、30以及工序75使用同一加工设备(钻床),所以工序25、30两道工序应该安排在后面与工序75连续加工,以减少工件的搬运时间,提高生产效率。
由此得出以下方案二。
2.工艺路线方案二:
在已经被粗车到Φ36的外圆上,用专用夹具夹紧,继续粗车相应的尺寸到Φ27,并且倒倒角C1
用螺纹车刀在Φ27外圆上进行攻螺纹。
为达到内壁粗糙度进行扩孔,满足精度要求。
工序75:
虽然方案二工序仍然是十八步,但是效率比方案一提高了。
各工序合理安排,减少工件在各加工设备间搬运的次数。
并遵循了工艺顺序安排的原则,保证了加工的精度要求。
因此,选择方案二进行加工。
六、确定加工余量
由《机械制造工艺学》第30至31页的表1—10,表1——11,表1——12确定其加工的的经济精度和经济粗糙度。
(1)Φ35的外圆表面:
工序名称
工序基本余量
工序尺寸
精度
粗糙度
精车
0.2
Φ35
IT7
Ra1.6
半精车
0.8
Φ35.2
IT9
Ra6.3
粗车
4
Φ36
IT11
Ra12.5
毛坯
Φ40
(2)加工M27x1.5-6h的螺纹:
攻螺纹
M27x1.5-6h
9
Φ27
(3)Φ32E9的孔:
扩
1
32
IT10
R6.3
钻
31
R12.5
(4)铣键槽
精铣
0.5
7.5
IT8
半精铣
2
7
粗铣
5
(5)轴向长度84尺寸:
车锥面
84
粗车Φ27端面
85
粗车Φ35端面
86
87
选择加工设备即选择机床类型。
由于已经根据零件的形状、精度特点,。
选择加工方法,因此机床的类型也随之确定。
至于机床的型号,主要取决于现场的设备情况。
若零件加工余量比较大,加工材料又较硬,有必要校验机床功率。
在本设计中,我们最终选择的机床,其经济精度和零件表面的设计要求相适应,初步选定各工序机床如下:
(1)工序15:
X62W卧式铣床。
(2)工序20、75、80、85:
X6132万能铣床。
(3)工序25、30、35、45、50、55、60:
选择CA6140车床
(4)工序65、70:
选用Z3025钻床。
选择夹具
对于成批生产的零件,大多采用专用机床夹具。
在保证加工质量、操作方便、满足高校的前提下,亦可部分采用通用夹具。
本机械加工工艺规程中所有工序采用了专用机床夹具,需专门设计,制造。
七、确定切削用量及基本时间
切削用量包括切削速度、进给量和背吃刀量,确定方法是先确定背吃刀量,再进给量,最后确定切削速度。
不同的加工性质,对切削加工的要求不一样。
粗加工时,应尽量保证较高的金属切削率和必要的刀具耐用度,故一般优先选择尽可能大的背吃刀量,其次选择较大的进给量,最后根据刀具耐用度要求,确定适合的切削速度。
精加工时,首先应保证工件的加工精度和表面质量要去,故一般选用较小的背吃刀量和进给量,而尽可能选用较高的切削速度。
(1)工序15
本道工序是粗铣端面,已知加工材料为45钢,机床选用XA5032立式铣床,选用刀具为高速钢镶齿套式面铣刀,其参数:
直径d-125mm,孔径D=40mm,宽L=40mm,齿数z=14.根据【8】表5-26确定铣刀角度,选择前角Υ=200,后角α=120,主偏角k=600,,螺旋角β=100,已知铣削宽度为57mm,铣削背吃刀量为ap=4mm
1.确定每齿进给量
根据【8】表5-13知XA5032型立式铣床的主电动机功率为7.5KW,查表5-27知当工艺系统刚性中等、镰齿端铣刀加工钢料时,其每齿进ap=0.08-0.15mm/z。
由于本工序背吃刀量和铣削宽度较大,选择最小的每齿进给量af=0.08mm/z。
根2.选择铣刀磨钝标准和耐用度
据【8】表5-28,用高速钢镰齿端铣刀粗加工钢料时,选择铣刀后刀面磨损极限为1.8mm,查表【8】5-29知铣刀直径d=125mm时,经插值得端铣刀的合理耐用度T=150min。
铣削速度可以通过计算得出,但是其计算公式比较复杂,实际生产中使用并不多,这里通过查表确定。
3.确定切削速度V和工作台每分钟进给量vf
查表【8】5-30知,高速钢铣刀铣削速度为15-25m/min,则所需铣床主轴转速范围是
n=
=38.2--63.7r/m
根据XA5032机床的标准主轴转速,由表5-13选取n=60r/min,则实际铣削速度为
V=
=23.55m/min
工作台每分钟进给量为vf=fn=afzn=0.08x14x60mm/min=67.2mm/min
根据表5-13中工作台标准纵向进给量,选取vf=60mm/min,则实际的每齿进给量为af=vf/zn=0.071mm/z;
4.校验机床功率
由表【8】5-31和5-32知,铣削力FZ和铣削功率P计算如下:
F=336.15NP=1.31KW
最后所确定的切削用量为
ap=4mm
af=0.071mm/z
vf=60mm/min
v=0.39mm/s
5基本时间
T=l/fn=0.94min
2t=1.84min
(2)粗车Φ35外圆
本道工序是粗车Φ35外圆,已知加工材料为45钢,机床为CA6140卧式车床,专用夹具,所选刀具为YT15硬质合金车刀。
1.确定背吃刀量
由前述可知,切削单边加工余量为2.0mm,即背吃刀量a
=2.0mm
2.确定进给量:
根据《金属加工工艺及工装设计》第95页表4-53可知,当加工45钢时,车刀刀杆尺寸B×
H为20×
30,背吃刀量a
=2.0mm,则进给量f=0.4~0.5mm/r,根据《金属加工工艺及工装设计》第91页表4-43进给量值可知,取横向f=0.4mm/r。
3.确定切削速度
根据《金属加工工艺及工装设计》第98页表4-58外圆切削速度参考值可知,V
=1.5~1.83m/s,
则所需车床主轴转速范围n=
=709~874.2r/min
根据《金属加工工艺及工装设计》第91页表4-43可知,n=710r/min,V
=
=89.17m/min
T=l/fn=0.306min
(三)粗车Φ27外圆。
本道工序是粗车Φ27外圆,已知加工材料为45钢,机床为CA6140卧式车床,专用夹具,所选刀具为YT15硬质合金车刀
1.确定背吃刀量
由前述可知,切削单边加工余量为4.5mm,即背吃刀量a
=4.5mm
2.确定进给量:
=4.5mm,则进给量f=0.3~0.4mm/r,根据《金属加工工艺及工装设计》第91页表4-43进给量值可知,取横向f=0.3mm/r。
3.确定切削速度
根据《金属加工工艺及工装设计》第98页表4-58外圆切削速度参考值可知
V
则所需车床主轴转速范围n=
根据《金属加工工艺及工装设计》第91页表4-43可知,n=710r/min,V
T=l/fn=0.15min
(四)半精车Φ35外圆
本道工序是半精车Φ35外圆,由粗车到Φ36后在进行半精车到Φ35.2.已知加工材料为45钢,机床为CA6140卧式车床,专用夹具,所选刀具为YT15硬质合金车刀
由前述可知,切削单边加工余量为0.4mm,即背吃刀量a
=0.4mm
根据《金属加工工艺及工装设计》第96页表4-54可知,当加工45钢时,背吃刀量a
=0.4mm,则进给量f=0.45~0.8mm/r,根据《金属加工工艺及工装设计》第91页表4-43进给量值可知,取f横向=0.5mm/r。
根据《金属加工工艺及工装设计》第98页表4-58切削速度参考值可知,V
=1.5~2.0m/s,
=511~682r/min
根据《金属加工工艺及工装设计》第91页表4-43可知,n=560r/min,V
=98.4m/min
T=l/fn=0.189min
(五)精车Φ35外圆
本道工序是精车Φ35外圆,由半精车到Φ35.2后在进行半精车到Φ35
已知加工材料为45钢,机床为CA6140卧式车床,专用夹具,所选刀具为YT15硬质合金车刀
由前述可知,切削单边加工余量为0.1mm,即背吃刀量a
=0.1mm
=0.1mm,则进给量f=0.11~0.15mm/r,根据《金属加工工艺及工装设计》第91页表4-43进给量值可知,取f横向=0.11mm/r。
3.确定切削速度:
=0.5~0.833m/s,
n=
=271.42~452.19
根据《金属加工工艺及工装设计》第91页表4-43可知n=320
Vc=
=35.36m/min
T=l/fn=1.5min
(6)钻Φ32孔
本道工序是钻Φ32的孔。
由钻Φ31的刀具:
YT锥柄麻花钻用钻床专用夹在钻
床上进行加工。
已知加工材料为45钢,机床为z3025
由前述可知,切削加工余量为36mm,即背吃刀量a
=36mm
根据《金属加工工艺及工装设计》第101页表4-64查得f=0.45~0.55mm/r根据【8】表5-51查得f=0.55
根据《金属加工工艺及工装设计》第102页表4-66查得vc=11.531m/min
N=
=122.4r/min
根据【8】表5-54可以查出n=80
T=l/fn=0.85
总结:
本设计研究过程中仍然存在一些不足,有的问题还有待进一步深入,具体如下:
1)、系统的设计不太完善,还可结合计算机数据库计算分析,整理出更加合理的设计方案;
2)、计算零件加工时间时考虑的是主要的工作时间,没将操作者辅助时间加上去。
参考文献
[1]王光斗,王春福.机床夹具设计手册.第三版.上海科学技术出版社,2002.
[2]田玉顺.机械加工技术手册.北京出版社.1992.
[3]北京第一通用机械厂.机械工人切削手册(修订第2版).机械工业出版社.1993.
[4]孟少农.机械加工工艺手册(第1、第2、第3卷).机械工业出版社.1996.
[5]杨叔子.机械加工工艺师手册.机械工业出版社.2004.
[6]徐灏.机械设计手册(第1、第2、第3、第4、第5卷).机械工业出版社.1995.
[7]金属机械加工工艺人员手册修订组.金属机械加工工艺人员手册.上海科学技术出版社.1982.
[8]王栋、李大磊机械制造工艺学课程设计指导书.北京.机械工业出版社.2010.9