GR一体机操作与维修Word下载.docx
《GR一体机操作与维修Word下载.docx》由会员分享,可在线阅读,更多相关《GR一体机操作与维修Word下载.docx(26页珍藏版)》请在冰豆网上搜索。
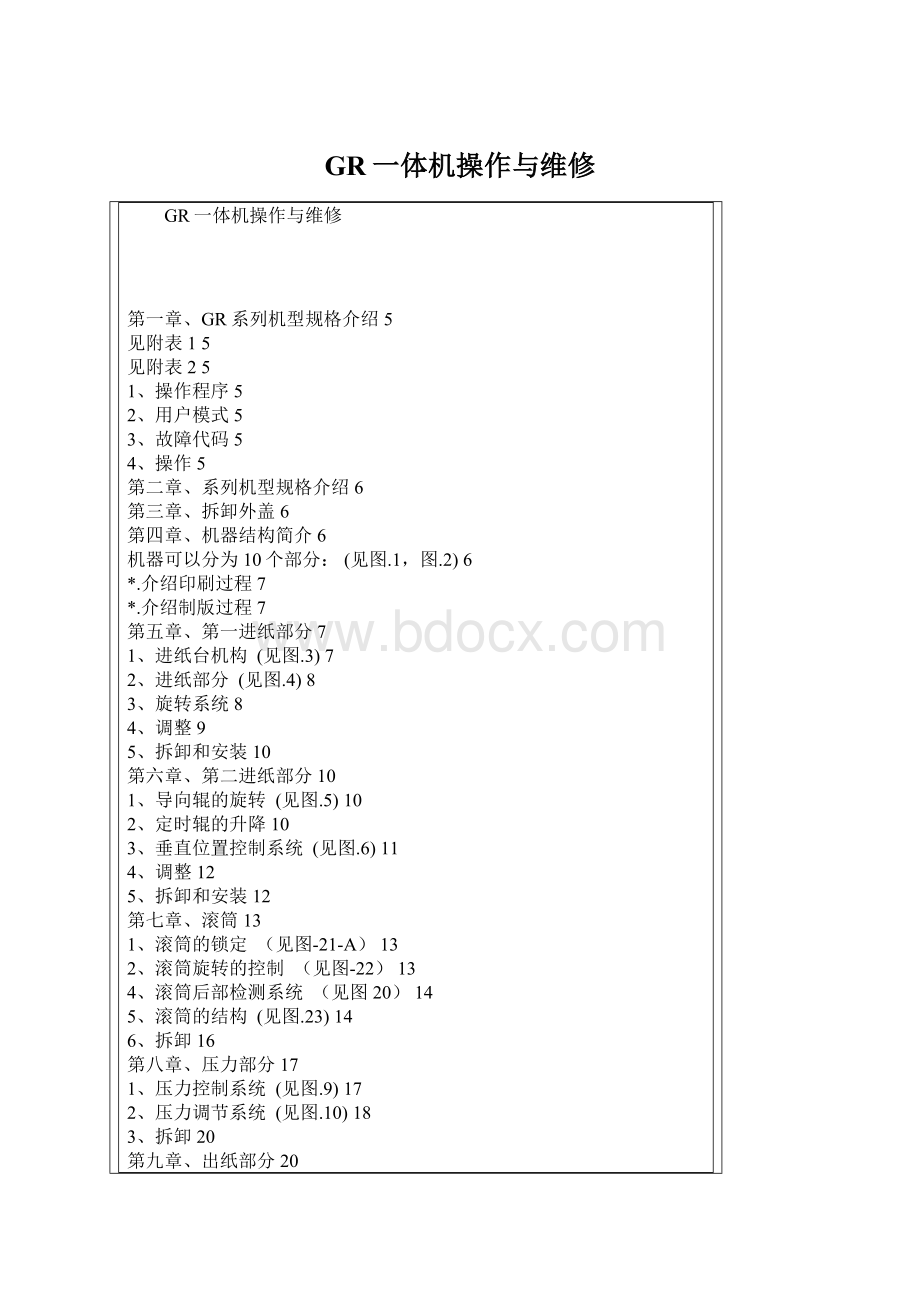
1、压力控制系统
(见图.9)
2、压力调节系统
(见图.10)
18
3、拆卸
20
第九章、出纸部分
1、分离单元(见图.15)
2、吸风单元
21
3、出纸传感器1(NO.19)和出纸传感器2(NO.20)
4、出纸形状的控制(GR1700/1710无)
(见图.18)
5、调整:
6、拆卸:
22
第十章、扫描部分(自动进稿)
1、概述
2、原理
(见图.27)
3、调整
23
4、拆卸
24
第十一章、扫描部分(平台式)
1、适用机型:
(见图.28)
25
第十二章、制版部分
1、工作原理:
2、热敏打印头定位系统
(见图.30)
3、制版系统
(见图.31)
26
27
第十三章、卸版部分
28
2、装夹系统
(见图.32)
3、卸版系统
4、卸蜡纸检测系统
29
5、故障提示
6、调整
30
7、拆卸和安装
第十四章、上版部分
31
2、装载系统
(见图.34)
3、故障提示:
32
4、蜡纸装载的检查系统
5、调整
6、拆卸和安装
33
附表1:
34
附表2:
35
GR系列机型
三级培训教材
2.0版本
2000年1月
珠海理想科学工业有限公司-技术服务部
第一章、GR系列机型规格介绍
见附表1
见附表2
1、操作程序
1.1.进入测试功能
*同时按住操作面板上的“L/P”键和“M/P”键,然后打开电源。
1.2.测试的操作
*键入测试代码→按“START”键进入该项测试→再按“START”键退出该项测试→按“C”键或“STOP”键消除该测试代码→键入新的测试代码→执行该项测试。
1.3.退出测试功能
*先按“C”键或“STOP”键,清除测试代码,然后按“ALL
RESET”键退出。
2、用户模式
2.1.用户的操作人员可使用用户模式以选择机器的初始设定值。
2.2.No.97测试状态将把机器所有用户模式初始化。
2.3.先按下“*”键再按下“8”键即可进入用户模式,用START键改变设定值。
2.4.按“ALLRESET”键1秒钟,退出用户模式。
2.5.重点:
No.05:
制版面积设定(GR1710无)
No.07:
最少印刷量的限制
No.12:
二合一功能版面(A5X2或B5X2)(只有1710有)
No.17:
语言选择
3、故障代码
3.1.LED显示机器:
故障代码有两种:
“E**”直接显示,可用RESET键消除,一般需联络技术人员解决;
“C**”大部分不直接显示,需按“*”键来显示,另有一些直接显示,如C24、C60、C61、C62等。
3.2.LCD显示机器:
只有一种故障代码:
“T**”,含义与“E**”相同。
其他则以文字显示。
4、操作
4.1.编程印刷功能(程序A和程序B印刷)
4.2.自动印刷功能
4.3.二合一功能
第二章、系列机型规格介绍
RC系列:
RC4000,RC4500,RC5600,RC5600D,RC5800,RC6300
RA系列:
RA4200,RA4300,RA4900,RA5900
GR系列:
GR1700/1710,GR1750,GR2000,GR2700,GR2710,GR2750,GR3710,GR3750,GR3770
FR系列:
FR2950,FR3910,FR3950,FR3950α
第三章、拆卸外盖
*前门/后盖/右前盖/入纸盖板/上盖板单元
*实际操作
第四章、机器结构简介
(见图.1,图.2)
1、第一进纸部分:
通过搓纸轮、拾纸轮和搓纸垫,将单张纸送入第二进纸部分。
2、第二进纸部分:
通过定时辊和导向辊,控制进纸时序和纵向印刷位置,并把纸张送入印刷区域。
3、印刷部分:
通过压力辊将纸张压向滚筒上的版纸,使油墨透过钢网、纱网、版纸,将图象和文字印在纸上。
4、出纸部分:
从滚筒上分离出印刷过的纸,并送到收纸盘内。
5、滚筒部分:
从油墨筒向滚筒供墨并控制油墨量。
6、卸版部分:
从滚筒上分离出废版纸,并送到废版盒中。
7、扫描部分:
通过图象扫描器扫描原稿,将原稿的影像转为数字信号。
8、制版部分:
通过热敏打印头将影象打印在蜡纸上。
9、上版和夹版部分:
将制好版的蜡纸传送至滚筒上,并在适当的长度切断版纸。
10、主驱动部分:
由主电机带动的部分。
*.介绍印刷过程
*.介绍制版过程
第五章、第一进纸部分
(见图.3)
1.1.作用:
在印刷过程中,使进纸台不断提升,始终为搓纸轮提供进纸压力。
1.2.组成:
进纸盘,升降电机,上限传感器,下限传感器(NO.03),上限安全开关,下限安全开关,纸检测传感器,纸张幅面传感器(NO.02),纸张幅面电位计(简述每个部件的作用)
1.2.1.GR1700/1710、GR2700无纸张幅面传感器和纸张幅面电位计
1.2.2.纸张幅面传感器和纸张幅面电位计一起检测纸台上纸的尺寸及方向,从而决定制版的面积和出纸的形状。
1.2.3.纸检测传感器和上限传感器无检测代码。
纸检测传感器可通过操作面板的LED提示来判断,上限传感器可通过系统电路板和电机控制板上的LEDP-UP灯的亮灭来判断。
1.3.工作过程:
纸检测传感器检测到纸→“印刷信号”至→升降电机旋转,进纸盘上升→当上限传感器的光路导通时,电机停止(电机回转、停、正转,到上限传感器光路打开。
减小惯性,使升降台定位准确)→随着印刷过程纸的减少,上限传器的光路被挡住→升降电机旋转至上限传感器的光路再次导通→当纸用完后→升降电机反转,进纸盘下降→当下限传感器的光路被挡住时,电机停止。
1.4.故障提示
1.4.1.C60:
进纸盘紧急停止
判断:
上限或下限安全开关被触动。
原因:
A、下限安全开关的活动臂变形,使开关断开。
B、上限传感器位置过高或脱落,使上限安全开关被触动。
C、连线断或对地短路。
D、F3保险管烧。
E、进纸台上下有异物
1.4.2.E02:
升降电机锁定
A、升降台上升,9秒内上限传感器的光路未打开。
B、升降台上升,2秒内下限传感器的光路未打开。
C、升降台下降,2秒内上限传感器的光路未挡住。
D、升降台下降,9秒内下限传感器的光路未挡住。
A、上限或下限传感器故障。
B、升降台卡死。
C、电机控制板故障。
(见图.4)
2.1.组成:
搓纸轮,拾纸轮,搓纸片,堆进纸开关
2.2.进纸:
进纸盘中的纸张是靠搓纸轮输到拾纸轮和搓纸片之间的。
拾纸:
搓纸片靠弹簧压向拾纸轮,产生进纸阻力,可从纸堆上分离出单张纸(拾纸轮转速快于搓纸轮)。
堆进纸开关:
防止多张进纸。
2.3.搓纸轮和拾纸轮都装有单向轴承(当印刷时,进纸离合器释放,拾纸轮轴不转,而纸张可自由向前输送。
)
3、旋转系统
3.1.组成:
入纸离合器,入纸离合器传感器(NO:
24),P盘,入纸检测传感器(N0:
25)
3.2.工作过程:
印刷时,主电机旋转→P盘旋转→当入纸离合器传感器的光路导通时→入纸离合器吸合→主皮带带动的主动件和从动件咬合→拾纸轮轴转动→搓纸轮和拾纸轮转动→第一进纸进纸。
3.3.入纸离合器吸合条件:
3.3.1.有“印刷信号”;
3.3.2.入纸离合器传感器的光路导通;
3.3.3.堆进纸开关未被压下。
3.4.入纸离合器释放条件:
3.4.1.无“印刷信号”;
3.4.2.入纸离合器传感器光路中断;
3.4.3.入纸检测传感器光路检测到纸张前缘;
3.4.4.堆进纸开关被压下。
3.5.进纸离合器吸合时间随速度而变化(GR)
3.6.正常印刷时入纸检测传感器先检测到纸,但在出样张和“CARD”时入纸检测传感器不起作用。
(I-6)
4、调整
4.1.上限传感器的位置
(见图.7)
4.1.1.进入测试N0:
102将进纸盘上升到最高位,使拾纸轮和进纸盘之间的间隙为1±
0.5mm。
4.1.2.如果上限传感器装的太高,输纸压力会过大,易产生多张进纸。
4.1.3.如果上限传感器装的太低,输纸压力会过小,易产生卡纸或空进纸。
4.2.堆进纸开关的位置
4.2.1.在拾纸轮和搓纸片之间插入1.5mm厚的塞规,此时堆进纸开关应被压下。
4.2.2.如果间隙过小,入纸离合器不能吸合,卡纸。
4.2.3.如果间隙过大,多张进纸时堆进纸开关不接通,多张纸会进入第二进纸区,造成卡纸,容易损坏机器。
4.3.搓纸片的角度
4.3.1.角度为18°
-28°
,标准值为22°
。
4.3.2.角度大:
进纸阻力大,防多张,易卡纸
4.3.3.角度小:
进纸阻力小,易进纸,易多张
4.4.搓纸片的压力
4.4.1.压力有4档:
250g,300g,350g,400g,标准值为350g。
4.4.2.压力大:
不易进纸,防多张,易卡纸。
4.4.3.压力小:
易进纸,易多张。
4.5.P盘的位置
(见图-7-A)
4.5.1.确认机器的垂直印刷位置正确,滚筒处于A位置。
4.5.2.B4机器:
P盘的对位点应与入纸离合器传感器上沿对齐。
A3机器:
P盘的对位点应与入纸离合器传感器中间对齐。
4.5.3.P盘转动时不能碰撞入纸离合器传感器的任何部分。
4.5.4.如果P盘位置不当,会产生输纸故障,或使印刷位置不稳定。
4.6.P盘缺口的调整(GR)
*调整P盘的缺口范围,可以改变入纸离合器断开的时间(一般用于印厚纸时调整)。
5、拆卸和安装
5.1.进纸台
*使用No.102使进纸盘上升到1/3处——方便拆卸升降电机
5.2.观察下限安全开关、纸检测传感器、纸张幅面传感器、纸张幅面电位计
5.3.升降电机
5.4.搓纸单元(观察搓纸片角度的调整,搓纸片压力的调整,堆进纸开关)
5.5.上限安全开关活动板
5.6.上限传感器(观察上限传感器位置的调整对进纸力的影响)
5.7.拾纸装置
5.8.搓纸轮和拾纸轮(注意方向)
5.9.恢复注意:
进纸台的平行.
第六章、第二进纸部分
(见图.5)
1.1.组成:
导向辊,导向凸轮,扇形齿轮,扇形齿轮弹簧,导向辊齿轮,单向弹簧,装载弹簧(制动,使印刷定位准确),纸传感器(NO.06),入纸检测传感器(NO.25)
1.2.工作过程:
主电机顺时针旋转→导向凸轮顺时针旋转→凸轮突起带动扇形齿轮逆时针旋转→扇形齿轮带动导向辊齿轮顺时针旋转→导向辊顺时针旋转→第二进纸进纸→导向凸轮的低点转到凸轮随动轮处时→弹簧使扇形齿轮顺时针旋转→导向辊齿轮逆时针旋转→由于单向弹簧的作用,此时导向辊齿轮不传送动力给导向辊,导向辊不旋转。
2、定时辊的升降(见图.5)
定时辊,定时凸轮,定时杆,定时杆弹簧
2.2.工作过程:
主电机顺时针旋转→定时凸轮顺时针旋转→突起带动定时杆逆时针旋转→定时辊轴逆时针旋转→定时辊的托架使定时辊下降→定时凸轮的低点转到凸轮随动轮处时→弹簧使定时杆顺时针旋转→定时辊轴顺时针旋转→定时辊的托架使定时辊抬升。
2.3.定时辊抬起接触导向辊时,定时辊弹簧提供二者间的压力。
有3档,如果压力小,导致纸打滑,印刷定位不准或卡纸。
2.4.定时辊抬起时,导向辊轴上的齿轮A和定时辊轴上的齿轮B咬合,导向辊带动定时辊同步旋转,将纸张送到印刷部分。
2.5.导向辊轴上的装载弹簧防止导向辊在旋转力未传递到辊上时旋转,其用作印刷定位。
2.6.改变导向凸轮的位置,可以改变第二进纸的启动时刻,从而改变垂直印刷位置。
2.7.纸传感器:
2.7.1.检查印刷时的卡纸。
2.7.2.印刷时,当纸传感器的光路被挡住时,压力线圈吸合。
2.8.入纸检测传感器:
印刷时(标准纸),当入纸检测传感器的光路被挡住时,入纸离合器释放。
(见图.6)
3.1.作用:
当使用操作面板上的印刷位置调整时,该控制系统改变垂直印刷位置。
3.2.组成:
印刷位置电机,滑动齿轮,滑动板,惰性轮,垂直居中传感器
3.3.工作过程:
3.3.1.操作面板上印刷位置向前调整时→印刷位置电机顺时针转动→通过滑动齿轮使滑动板下降→固定在滑动板上的两个惰性轮也一起下降→使主皮带上紧下松→主皮带带动滚筒顺时针转(由于主电机比滚筒的旋转阻力大)→当滚筒回到A位置时,导向凸轮相对于滚筒逆时针旋转了一定的角度,从而导向凸轮凸起部顶起扇形齿轮的时间推后,推后进纸时刻→印刷位置前移。
3.3.2.操作面板上印刷位置向后调整时→印刷位置电机逆时针转动→滑动板上升→惰性轮上升→使主皮带上松下紧→主皮带逆时针旋转→提前进纸时刻→印刷位置向后移。
3.4.E05:
印刷位置电机锁定
判断:
当印刷位置电机开始旋转后12秒内,如果垂直中心传感器状态未从通转到断(或从断转成通)。
原因:
A、垂直中心传感器工作故障,导致印刷位置电机一个方向走。
(向上走)
B、印刷位置电机未安装好,与滑动齿轮未咬合好,电机空转。
C、电路板上电机控制部分损坏。
4.1.定时杆的位置
(见图.8)
4.1.1.旋转系统电路板上SW1,使定时凸轮的小半径对着定时杆的凸轮随动轮。
4.1.2.检查并调整定时凸轮与凸轮随动轮之间的间隙,使其为2.5~3.0mm。
4.1.3.如果间隙过小,定时辊会下降得过多过早,当定时辊在最低位时,齿轮A和齿轮B会脱开,会出现印刷定位无规则性或卡纸。
4.1.4.如果间隙过大,定时辊会下降过少,造成印刷重影。
4.2.定时辊的平行度(见图-8-A)
4.2.1.用两根纸条检查两辊的平行度。
4.2.2.如不平行,纸会在第二进纸处被拉皱,可调整定时辊的平行调整环。
4.3.垂直印刷位置机械调整
标准位置时:
A位置垂直居中位置时,主电机皮带轮、滚筒皮带轮与主轴面板上的孔分别对齐。
4.3.1.调整导向凸轮
A、当印刷位置偏差在12mm以内时,使用导向凸轮调整。
B、凸轮顺时针移动→印刷位置向后调整。
C、凸轮逆时针移动→印刷位置向前调整。
4.3.2.调整凸轮皮带轮(见图-8-B)
A、当印刷位置偏差大于12mm时,使用凸轮皮带轮调整。
B、滚筒停在A位置,用一根内六角扳手固定住主皮带轮和滚筒,松开主皮带:
C、凸轮皮带轮相对主皮带顺时针错一格移动→印刷位置向后调整12mm。
D、凸轮皮带轮相对主皮带逆时针错一格移动→印刷位置向前调整12mm。
4.4.导纸板的平行度
4.4.1.导纸板不平行则可能出现卡纸、纸皱、纸破损等现象。
4.4.2.调整导纸板两边固定螺钉。
5.1.按系统板上点动开关SW1观察第二进纸部分的动作
5.2.进纸台、拾纸装置和上限安全开关(进纸台处于最低位置,否则导纸板无法拆卸)
5.3.定时弹簧,定时杆
5.4.导向辊(观察单向弹簧和装载弹簧)
5.5.导纸板(注意螺丝应从内部拆卸)
5.6.纸传感器电路板-两对传感器(前:
入纸检测传感器;
后:
纸传感器。
灵敏度可调)
5.7.印刷位置电机
5.8.恢复
5.9.调整定时杆位置和定时辊平行度
第七章、滚筒
(见图-21-A)
1.1.拉出滚筒时:
锁定板插入滚筒体右支承的缝隙中。
1.2.放入滚筒时:
由锁定钩钩住滚筒导轨弯曲处;
1.3.A位置时,前门打开,锁定线圈吸合,带动锁定钩移开,滚筒可被拉出,此时滚筒初始位置灯应是亮的。
1.4.滚筒到位开关:
检查滚筒是否装入机器。
(见图-22)
主电机、主皮带、凸轮皮带轮、编码盘、编码盘传感器
2.2.工作原理:
主电机顺时针旋转→主皮带→主皮带轮顺时针旋转→主轴离合器→滚筒顺时针旋转
2.3.主电机速度:
由编码盘和编码盘传感器控制
2.4.滚筒转速:
2.4.1印刷速度60,80,100,120,130rpm
(No.62)
2.4.2.装载蜡纸速度15rpm(No.60)
2.4.3.自由转速SW130rpm(No.61)
3、滚筒的位置
(见图.21)
3.1.滚筒的位置是通过滚筒控制电路板上的位置A和位置C传感器检查在滚筒右支承上的A、C-1和C-2三块金属板来实现的。
3.2.A位置:
位置A传感器光路刚好被板A挡住
这是滚筒一个周期的基本位置,上版、卸版和印刷等许多操作的初始位置,并是装、取滚筒的位置。
3.2.1.卸版前,角度传感器检测角度磁铁的位置;
3.2.2.卸版和印刷前,印版传感器检查滚筒上有无印版。
(RA机型)
3.2.3.位置A传感器通过检测滚筒旋转情况检测主电机锁定故障。
3.3.E01:
主电机锁定
A、在主电机启动后2秒后,位置A传感器仍能检测到A位置。
B、在主电机启动后5秒后,位置A传感器未能检测到A位置
(1)滚筒(主电机)实际上能够转动
A、A金属片松脱
B、位置A传感器损坏——更换滚筒控制电路板
C、连线
(2)拉出滚筒后主电机能够转动
A、滚筒被分离爪或卸蜡纸钩卡住
B、滚筒被后部螺丝卡住(拆卸驱动部分后易发生)
(3)拉出滚筒后主电机仍不能转动
A、驱动部分被异物卡住
B、电机控制板损坏
C、主电机连锁开关
D、连线不良
3.4.C-1位置:
位置C传感器光路刚好被板C-1挡住
*装版时,装版传感器检查蜡纸是否正确地装在滚筒上。
*印刷和卸版前,装版传感器检查滚筒上是否有版纸。
(GR机型)
3.5.C-2位置:
位置C传感器光路刚好被板C-2挡住
*装版后,切刀电机导通,裁切蜡纸。
(见图20)
4.1.检查点1:
压力检测传感器光路刚打开(A位置→不到1/4)
*压力线圈断开,纸传感器检测无纸。
4.2.检查点2:
压力检测传感器光路刚阻挡(A位置→不到3/4)
*印数累加,纸传感器检测有纸,出纸1传感器检测无纸
(见图.23)
组成:
油墨电机,油墨泵,油墨分配器,挤压辊,刮墨辊,油墨驱动轴,油墨电路板,挤压皮带,钢网,纱网,滚筒体支承(左、右),滚筒控制电路板。
5.1.供墨系统工作:
油墨电机带动油墨泵从油墨筒中抽出油墨→通过布墨辊将油墨分散送到挤压辊上→挤压皮带带动油墨驱动轴反向旋转使油墨摊开→挤压辊旋转时油墨通过挤压辊和刮墨辊之间0.08~0.12mm的间隙给挤压辊盖上一层油膜→印刷时压力辊上抬,使油膜传送到滚筒内表面。
5.2.油墨的检测:
通过油墨电路板上的油墨检测传感器来检测油墨。
(No.37)
未检测到→油墨电机工作
检测到→油墨电机停止工作
5.2.1.油墨电机开始工作20秒内,还未检测到油墨,机器显示“更换油墨筒”(No.101)
5.2.2.E04:
油墨溢出传感器检测到油墨。
(No.38)
A、油墨传感器损坏;
B、油墨电路板损坏;
C、有油墨的滚筒竖放;
D、挤压辊和刮墨辊不平行,造成锥形油墨。
E、使用假油墨。
F、滚筒未到位时触发滚筒到位开关。
5.3.滚筒控制电路板的设置:
AOX(V)-22
RA、GR机器可以通过滚筒控制电路板上的开关SW1来设置滚筒的尺寸和颜色等信息。
*如果设置不对,则可能会出现C61,C62,C63故障代码。
5.4.挤压间隙的调整:
(见图.24)
挤压间隙----挤压辊和刮墨辊之间的间隙----0.08~0.12mm。
可通过调节两端的间隙调整螺丝来改变挤压间隙的大小。
*间隙过大:
过多的油墨被送到滚筒体内表面,造成尾部漏墨。
*间隙过小:
油墨在挤压辊表面铺展不良,使印件不均匀。
5.5.挤压压力的平衡间隙:
(见图.25)
5.5.1.调整板-背面用,顺时针旋转,间隙增大,逆时针,间隙减小。
5.5.2.调整环A-前面用,调整方法相同。
5.5.3.挤压辊和滚筒体之间标准间隙为:
0.5~1.0mm。
5.5.4.挤压辊和滚筒体之间间隙过小:
油墨被挤到滚筒尾部,造成漏墨。
5.5.5.挤压辊和滚筒体之间间隙过大:
印刷不均匀,滚筒体变形过大,降低其寿命。
5.5.6.挤压压力不平衡,则印件的水平方向印刷浓度不均匀。
5.5.7.调整完成后,制机密版,并印刷500张,检查有无漏墨,如有漏墨,则需重新调整。
5.6.油墨挡板的位置:
(见图.26)
5.6.1.油墨挡板尖点与安装螺钉的距离大于10mm,离挤压辊各端里边约2mm。
5.6.2.油墨挡板过于靠里:
印张两边的内容印不出来。
5.6.3.油墨挡板离挤压辊过远或其与滚筒体内表面未紧密接触:
油墨从滚筒体两侧溢出。
6、拆卸
6.1.制一张保密版
6.2.观察滚筒锁定机构、到位开关
6.3.滚筒塑料盖
6.4.滚筒控制电路板(观察设置)
6.5.金属板A、C-1、C-2(做好标记,防止装错。
A位置是可以调整的)
6.6.整个滚筒体
6.7.观察滚筒内部结构和调整挤压间隙、压力平衡的方法(无须调整)
6.8.油墨电路板保护片(安装位置)
6.9.油墨泵单元(观察油墨检测传感器和溢出传感器。
用纸包好油墨电路板插头防止油墨污染)
6.10.观察GR滚筒油墨瓶检测开关(与RC、RA不同)
6.11.检查油墨挡板的位置
6.12.恢复(注意油墨电路板保护片的位置,主轴皮带轮和滚筒体的相对位置,滚筒控制电路板的连线一定要扎好)
6.13.纱网(注意纱网弹簧的拉升方向,挂板的安装方式。
卸下后不要取下蜡纸,将纱网对折后放好,勿卷起或压叠,勿让纱网粘上沙粒)
6.14.角度磁铁片
6.15.夹板组件
6.16.恢复(注意特殊螺丝的安装位置)
6.17.制一保密版后印刷500张以上进行测试
第八章、压力部分
(见图.9)
压力凸轮,连动板,压力钩,压力线圈(No.68),压力盘,压力检测传感器(No.7),压力杆,压力辊。
1.2.工作原理:
通过压力凸轮旋转带动连动板上下运动→以压力轴为轴心带动钩形杆上下运动→纸传感器检测到纸,并有印刷信号→启动压力线圈,令钩杆咬合压力杆→带动压力轴旋转→压力辊上升,挤