水吸收二氧化硫填料塔的设计Word文件下载.docx
《水吸收二氧化硫填料塔的设计Word文件下载.docx》由会员分享,可在线阅读,更多相关《水吸收二氧化硫填料塔的设计Word文件下载.docx(25页珍藏版)》请在冰豆网上搜索。
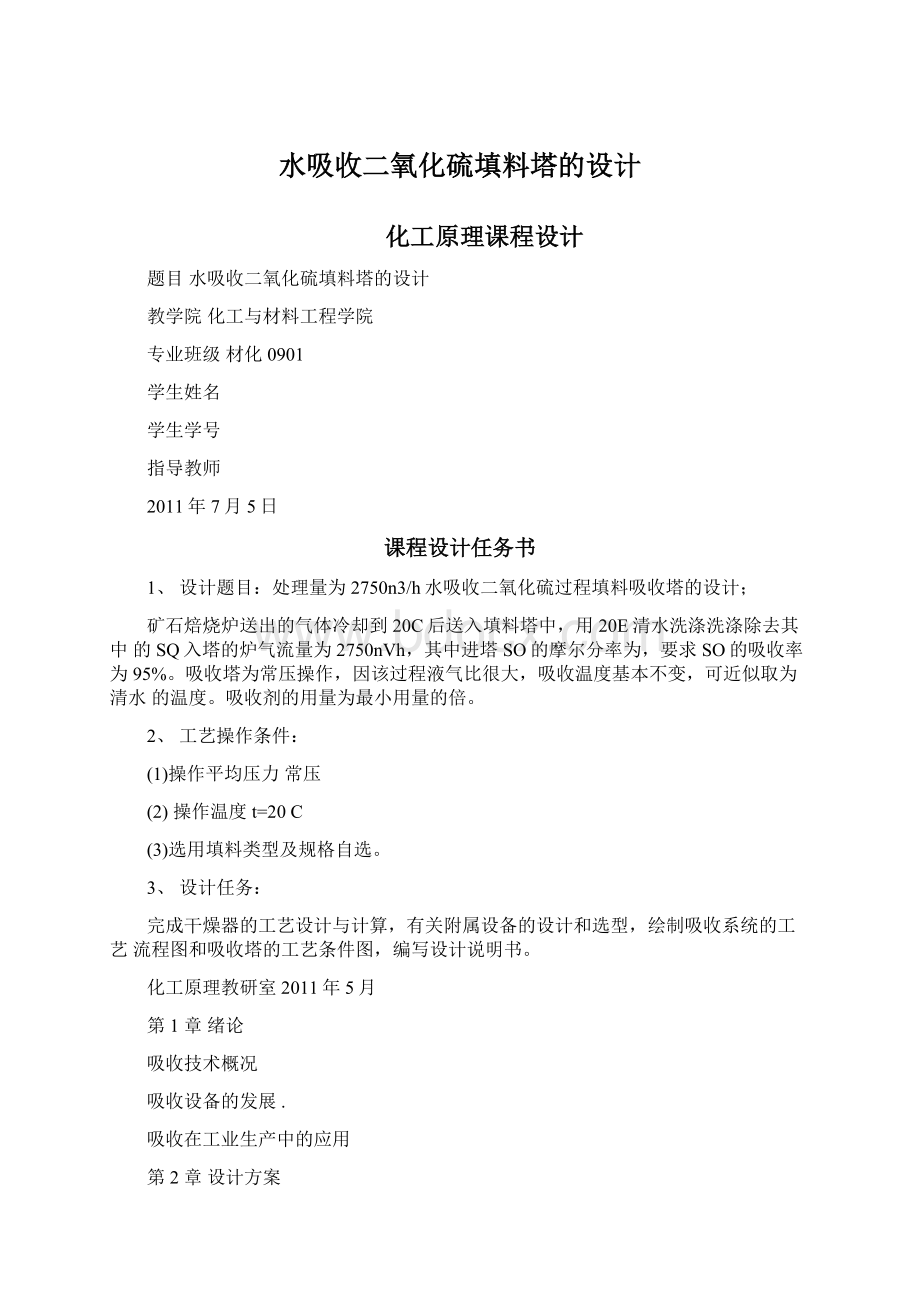
气液相平衡数据.
物料衡算
填料塔的工艺尺寸的计算.
塔径的计算.
泛点率校核.
填料规格校核:
.
液体喷淋密度校核.
填料塔填料高度计算
传质单元高度计算.
传质单元数的计算.
填料塔附属高度计算
液体分布器计算.
液体分布器.
布液孔数.
液体保持管高度.
其他附属塔内件的选择
填料支承板.
除沫器(除雾器).
管口结构.
吸收塔的流体力学参数的计算
吸收塔的压力降.
吸收塔的泛点率.
气体动能因子.
附属设备的计算与选择
离心泵的选择与计算.
吸收塔的主要接管尺寸的计算
工艺设计主要符号说明
评述与讨论.24
结束语
参考文献26
吸收技术概况
在化学工业中,经常需将气体混合物中的个各组分加以分离。
气体的吸收是用适当的液体吸收剂与气体混合物接触,吸收器气体混合物中一个或几个组分,使其中的各组分得以分离的一种操作。
在化工生产中,它主要用于原料气的净化、有用组分的回收。
制取气体的溶液作为成品,以及废气的治理等方面,因此吸收操作是一种重要的分离方法,在化学工业中应用相当普遍。
吸收操作利用气体混合物各组分在某种溶剂中溶解度不同而达到分离的目的。
气体吸收是物质自气相到液相的转移,这是一种传质过程。
混合气体中某一组分能否进入液相,既取决于气相中该组分的分压,也取决于溶液里该组分的平衡蒸气压。
如果混合气体中该气体的分压大于溶液中该组分的平衡蒸气压,这个组分便可自气相转移到液相,即被吸收。
转移的结果,溶液里这个组分的浓度便升高,它的平衡蒸汽压也随着升高,到最后,可以升高到等于它的气相中的分压,传质过程于是停止,这时称为气液两相达到平衡。
根据两相的平衡关系可以判断传质过程的方向与极限。
另外,传质速率与推动力成正比,与阻力成反比,两相的浓度距离平衡浓度越大,则传质的推动力越大,传质速率与越大。
吸收技术是从气液两相的平衡关系与传质速率关系着手,利用气体混合物中各组分在特定的液体吸收剂中的溶解度不同的基本原理,最终实现各组分分离的目的。
吸收设备的发展
吸收设备有多种类型,如填料塔、板式塔、喷洒塔和鼓泡塔等。
最常用的有填料塔与板式塔。
填料塔中装有诸如瓷环之类的填料;
气液接触在填料中进行。
板式塔中装有筛孔塔板,气液亮相在塔板上鼓泡进行接触。
工业模型的填料塔始于1881年的蒸馏操作中,1904年采用于炼油工业,当时的填料是碎砖瓦、小石块和管子缩节等。
20世纪初,填料塔进入了一个新的发展阶段。
在瓷环填料亦称拉西环填料被广泛采用后,弧鞍形填料相继问世,特别是出现了斯特曼填料后,便大大的促进了规整填料的发展,除了各种填料大大涌现外,还发展了多管塔、乳化塔等被成为高效填料塔的新塔型。
从20世纪60年代起新型填料有了较多的发展,属于颗粒型填料的有:
海佐涅尔填料、阶梯环填料、多角螺旋填料、金属鞍环填料、比阿雷茨基环、莱瓦填料以及它们的改进形式。
属于规整填料的有:
苏采尔填料、重叠式丝网波纹板填料、重叠式金属波形板填料、格里希栅格填料、格子填料、拉伸金属网填料、塑料蜂窝填料、Z形格子填料、Perform喷射式填料和脉冲填料等。
同时,还创建了使小球浮动来强化传质的湍球塔。
进入20世纪70年代后,至于新型填料的研究,希望找到有利于气液分布均匀、高效和制造方便的填料。
近年来随着化工产业的发展,大规模的吸收设备已经广泛用于实际生产当中。
具有了很高的吸收效率,以及在节能方面也日趋完善。
填料塔的工艺设计内容是在明确了装置的处理量,
操作温度及操作压力及相应的相平衡关系的条件下,完成填料塔的工艺尺寸及其他塔内件设计。
在今后的化学工业的生产中,对吸收设备的要求及效率将会有更高的要求,所以日益完善的吸收设备会逐渐应用于实际的工业生产中。
吸收在工业生产中的应用
吸收在工业上的应用大致有以下几种:
(1)原料气的净化为除去原料气中所有的杂质,吸收可说是最常用的方法。
(2)有用组分的回收如从焦炉煤气中用水回收氨,再用洗油回收粗苯蒸气(包括苯、甲苯、二甲苯等),以及从某些干燥废气中回收有机溶剂蒸气等。
(3)液体产品的制取将气体中需要的成分以指定的溶剂吸收出来,成为溶液态的成品或半成品。
如制酸工业中含HCLNQ(氮氧化物)或SO的气体制取盐酸、硝酸或硫酸;
甲醇(乙醇)蒸气经氧化后,用水吸收以制成甲醛(乙醛)半成品等。
(4)废弃的治理很多工业废气中含有SO、NO(主要是NO及NO)、汞蒸气等有害成分,虽然浓度一般甚低,但对人体和环境仍危害甚大而必须进行治理。
选择适当的工艺和溶剂进行吸收,使废气治理中应用较广的方法。
当然,以上目的有时也难以截然分开,如干燥废气中的有机溶剂,能回收下来就很有价值,任其排放则会污染大气。
第2章设计方案
吸收剂的选择
对于吸收操作,选择适宜的吸收剂,具有十分重要的意义.其对吸收操作过程的经济性有着十分重要的影响.一般情况下,选择吸收剂,要着重考虑如下问题.
(一)对溶质的溶解度大
所选的吸收剂多溶质的溶解度大,则单位量的吸收剂能够溶解较多的溶质,在一定的处理量和分离要求下,吸收剂的用量小,可以有效地减少吸收剂循环量,这对于减少过程功耗和再生能量消耗十分有利。
另一方面,在同样的吸收剂用量下,液相的传质推动力大,则可以提高吸收速率,减小塔设备的尺寸。
(二)对溶质有较高的选择性
对溶质有较高的选择性,即要求选用的吸收剂应对溶质有较大的溶解度,而对其他组分则溶解度要小或基本不溶,这样,不但可以减小惰性气体组分的损失,而且可以提高解吸后溶质气体的纯度.
(三)不易挥发
吸收剂在操作条件下应具有较低的蒸气压,以避免吸收过程中吸收剂的损失,提高吸收过程的经济性.
(四)再生性能好
由于在吸收剂再生过程中,一般要对其进行升温或气提等处理,能量消耗较大,因而,吸收剂再生性能的好坏,对吸收过程能耗的影响极大,选用具有良好再生性能的吸收剂,往往能有效
以上四个方面是选择吸收剂时应考虑的主要问题,其次,还应注意所选择的吸收剂应具有
良好的物理、化学性能和经济性.其良好的物理性能主要指吸收剂的粘要小,不易发泡,以保证
吸收剂具有良好的流动性能和分布性能•良好的化学性能主要指其具有良好的化学稳定性和热稳定性,以防止在使用中发生变质,同时要求吸收剂尽可能无毒、无易燃易爆性,对相关设备无腐蚀性(或较小的腐蚀性).吸收剂的经济性主要指应尽可能选用廉价易得的溶剂•
工业常用吸收剂
溶质
吸收剂
氨
水、硫酸
硫化铵
碱液、砷碱液、有机溶剂
丙酮蒸汽
水
苯蒸汽
煤油、洗油
氯化氢
丁二烯
乙醇
二氧化碳
水、碱液、碳酸烯酯
二氯乙烯
煤油
二氧化硫
一氧化碳
铜氨液
吸收流程的选择
工业上使用的吸收流程多种多样,可以从不同角度进行分类,从所选用的吸收剂的种类看,有仅用一种吸收剂的一步吸收流程和使用两种吸收剂的两步吸收流程,从所用的塔设备数量看,可分为单塔吸收流程和多塔吸收流程,从塔内气液两相的流向可分为逆流吸收流程、并流吸收流程等基本流程,此外,还有用于特定条件下的部分溶剂循环流程。
2.2.1吸收工艺流程的确定
(一)一步吸收流程和两步吸收流程
一步流程一般用于混合气体溶质浓度较低,同时过程的分离要求不高,选用一种吸收剂即可完成任务的情况。
若混合气体中溶质浓度较高且吸收要求也高,难以用一步吸收达到规定的吸收要求,但过程的操作费用较高,从经济性的角度分析不够适宜时,可以考虑采用两步吸收流程。
(二)单塔吸收流程和多塔吸收流程
单塔吸收流程是吸收过程中最常用的流程,如过程无特别需要,则一般采用单塔吸收流程。
若过程的分离要求较高,使用单塔操作时,所需要的塔体过高,或采用两步吸收流程时,则需要采用多塔流程。
典型的是双塔吸收流程。
(三)逆流吸收与并流吸收
吸收塔或再生塔内气液相可以逆流操作也可以并流操作,由于逆流操作具有传质推动力大,分离效率高(具有多个理论级的分离能力)的显着优点而广泛应用。
工程上,如无特别需要,一般均采用逆流吸收流程。
(四)部分溶剂循环吸收流程由于填料塔的分离效率受填料层上的液体喷淋量影响较大,当液相喷淋量过小时,将降低填料塔的分离效率,因此当塔的液相负荷过小而难以充分润湿填料表面时,可以采用部分溶剂循环吸收流程,以提高液相喷淋量,改善踏的操作条件。
吸收塔设备及填料的选择
2.3.1吸收塔的设备选择
塔型的合理选择是做好塔设备设计的首要环节,选择时应考虑的因素有:
物料性质、操作条件、塔设备性能、以及塔设备的制造、安装、运转和维修等。
(一)与物性有关的因素:
如易起泡的物系,处理量不大时,选填料塔为宜。
具有腐蚀性的介质,也可选用填料塔。
具有热敏性的物料须减压操作,可采用装填规整的散堆填料。
粘性较大的物系,可以选用大尺寸填料。
(二)与操作条件有关的因素:
气相传质阻力大,宜采用填料塔。
大的液体负荷,可选用填料塔。
低的液体负荷,不宜采用填料塔。
液气比波动的适应性,板式塔优于填料塔。
(三)其它因素
对于吸收过程,能够完成其分离任务的塔设备有多种,如何从众多的塔设备中选出合适的类型是进行工艺设计的首要工作.而进行这一项工作则需对吸收过程进行充分的研究后,并经多方案对比方能得到较满意的结果.一般而言,吸收用塔设备与精馏过程所需要的塔设备具有相同的原则要求,即用较小直径的塔设备完成规定的处理量,塔板或填料层阻力要小,具有良好的传质性能,具有合适的操作弹性,结构简单,造价低,易于制造、安装、操作和维修等.
但作为吸收过程,一般具有操作液起比大的特点,因而更适用于填料塔.此外,填料塔阻力小,效率高,有利于过程节能,所以对于吸收过程来说,以采用填料塔居多.但在液体流率很低难以充分润湿填料,或塔径过大,使用填料塔不经济的情况下,以采用板式塔为宜.
2.3.2填料的选择
填料是填料塔中传质元件,它可以有各种不同的分类:
如按性能分为通用填料和高效填料;
按形状分为颗粒型填料和规整填料。
填料品种很多,最古老的填料是拉西环;
在国外被认为较为理想的是鲍尔环,矩鞍填料和波纹填料等工业填料,现经测试验证,已被推荐为我国今后推广使用的通用型填料,填料的材质可为金属、陶瓷或塑料。
各种填料的结构差异较大,具有不同的优缺点,因此在使用上应根据具体情况选择不同的塔填料。
在选择塔填料时,应该考虑如下几个问题:
(1)选择填料材质选择填料材质应根据吸收系统的介质以及操作温度而定,一般情况下,可以选用塑料,金属,陶瓷等材料。
对于腐蚀性介质应采用相应的抗腐蚀性材料,如陶瓷,塑料,玻璃,石墨,不锈钢等,对于温度较高的情况,应考虑材料的耐温性能。
(2)填料类型的选择填料类型的选择是一个比较复杂的问题。
一般来说,同一类填料塔中,比表面积大的填料虽然具有较高的分离效率,但是由于在同样的处理量下,所需要的塔径较大,塔体造价升高。
(3)填料尺寸的选择实践表明,填料塔的塔径与填料直径的比值应保持不低于某一下限
值,以防止产生较大的壁效应,造成塔的分离效率下降。
一般来说,填料尺寸大,成本低,处理量大,但是效率低,使用大于50mm的填料,其成本的降低往往难以抵偿其效率降低所造成的成本增加。
所以,一般大塔经常使用50mn!
勺填料。
但在大塔中使用小于2025mn填料时,效率并没有较明显的提高,一般情况下,可以按表选择填料尺寸。
因此对于水吸收SC2的过程、操作、温度及操作压力较低,工业上通常选用所了散装填料。
在所了散装填料中,塑料阶梯环填料的综合性能较好,故此选用塑料阶梯环填料。
表2—2填料尺寸与塔径的对应关系
塔径/mm
填料尺寸/mm
D<
300
20〜25
300<
DK900
25〜38
D>
900
50〜80
相关的填料数据如下:
表2-3散装填料类型以及关联常数A,K值
散装填料类型
A
K
规整填料类型
塑料鲍尔环
金属丝网波纹填
料
金属鲍尔环
塑料丝网波纹填
塑料阶梯环
金属网孔波纹填
金属阶梯环
金属孔板波纹填
瓷矩鞍
塑料孔板波纹填
金属环矩鞍
表2—4聚丙烯阶梯环几何数据
规格
比表面积
mi/m3
空隙率
堆积个数
堆积重量
填料因子
-1m
16**1
370
299136
25**
228
81500
38*19*
27200
50*25*
10740
76*37*
90
3420
吸收剂再生方法的选择
依据所用的吸收剂不同可以采用不同的再生方法,工业上常用的吸收剂再生方法主要有减压再生,加热再生及气提再生等。
(一)减压再生(闪蒸)
吸收剂的减压再生是最简单的吸收剂再生方法之一。
在吸收塔内,吸收了大量溶质后的吸收剂进入再生塔并减压,使得溶如吸收剂中的溶质得以再生。
该方法最适用于加压吸收,而且吸收后的后续工艺处于常压或较低压力的条件,如吸收操作处于常压条件下进行,若采用减压再生,那么解吸操作需在真空条件下进行,则过程可能不够经济。
(二)加热再生
加热再生也是吸收剂再生最常用的方法。
吸收了大量溶质后的吸收剂进入再生塔内并加热使其升温,溶入吸收剂中的溶质得以解吸。
由于再生温度必须高于解吸温度,因而,该方法最适用于常温吸收或在接近于常温的吸收操作,否则,若吸收温度较高,则再生温度必然更高,从而,需要消耗更高品位的能量。
一般采用水蒸汽作为加热介质,加热方法可以依据具体情况采用直接蒸汽加热或采用缉间接蒸汽加热。
(三)气提再生
气提再生是在再生塔的底部通入惰性气体,使吸收剂表面溶质的分压降低,使吸收剂得以再生。
常用气提气体是空气和水蒸气。
操作参数的选择
吸收过程的操作参数主要包括吸收(或再生)压力、吸收(或再生)温度以及吸收因子(或解析因子),这些条件的选择应充分考虑前后工序的工艺参数,从整个过程的安全性、可靠性、经济性出发,利用过程的模拟计算,经过多方案对比优化得出过程参数。
一)操作压力的选择
对于物理吸收,加压操作一方面有利于提高吸收过程的传质推动力而提高过程的传质速率另一方面,也可以减小气体的体积流率,减小吸收塔径。
所以操作十分有利.但工程上,专门为吸收操作而为气体加压,从过程的经济性角度看是不合理的,因而若在前一道工序的压力参数下可以进行吸收操作的情况下,一般是以前道工序的压力作为吸收单元的操作压力。
对于化学吸收,若过程由质量传递过程控制,则提高操作压力有利,若为化学反应过程控制则操作压力对过程的影响不大,可以完全根据前后工序的压力参数确定吸收操作压力,但加大吸收压力依然可以减小气相的体积流率,对减小塔径仍然是有利的。
对于减压再生(闪蒸)操作,其操作压力应以吸收剂的再生要求而定,逐次或一次从吸收压力减至再生操作压力,逐次闪蒸的再生效果一般要优于一次闪蒸效果。
(二)操作温度的选择
对于物理吸收而言,降低操作温度,对吸收有利。
但低于环境温度的操作温度因其要消耗大量的制冷动力而一般是不可取的,所以一般情况下,取常温吸收较为有利。
对于特殊条件的吸收操作必须采用低于环境的温度操作。
对于化学吸收,操作温度应根据化学反应的性质而定,既要考虑温度对化学反应速度常数的影响,也要考虑对化学平衡的影响,使吸收反应具有适宜的反应速度。
对于再生操作,较高的操作温度可以降低溶质的溶解度,因而有利于吸收剂的再生。
(三)吸收因子的选择
吸收因子A是一个关联了气体处理量G,吸收剂用量L以及气液相平衡常数m的综合的过
程参数.
式中G气体处理量,kmol/h;
L吸收剂用量,kmol/h;
m气体相平衡常数。
第3章吸收塔的工艺计算
基础物性数据
3.1.1液相物性数据
对低浓度吸收过程,溶液的物性数据可近似取纯水的物性数据。
由参考书【】查得,20C时
水的有关物性数据如下:
密度为L998.2kg/m3
粘度为
1.004Pas=3.6kg/(m•h)
表面张力为
L72.67dyn/cm941803.2kg/h2
SO在水中的扩散系数为Dl1.47109m2/s5.292106m2/h
3.1.2气相物性数据
混合气体的平均摩尔质量为
混合气体的平均密度为
混合气体的粘度可近似取为空气的粘度,由参考书【】查得,20r时空气的粘度为
查参考书[1]得,so在空气中的扩散系数为
Dv0.108104m2s1=0.039m7h
3.1.3气液相平衡数据
由参考书查得,常压下20r时so在水中的亨利系数为
相平衡常数为
溶解度系数为
物料衡算
进塔气相摩尔比为
出塔气相摩尔比比为
进塔惰性气相流量为
该吸收过程属于低浓度吸收,平衡曲线可近似为直线,最小液气比可按下式计算,即对于纯溶剂吸收过程,进塔液相组成为
取操作液气比为
填料塔的工艺尺寸的计算
3.3.1塔径的计算
采用贝恩(Bain)-霍根(Hongerj)关联式气相质量流量为
液相质量流量可以近似按纯水的流量计算,即
Uf1.11530u0.50.85Uf取u0.7uf0.71.115300.781ms
42750
36003.140.781
1.116m
圆整塔径后取D1200mm
332泛点率校核
u
Uf
而53100%70.03%(在允许范围5。
%——8。
%内)
3.3.3填料规格校核:
有D120031.588即符合要求.
d38
3.3.4液体喷淋密度校核
对于直径不超过75mm勺散装填料,可取最小润湿速率(L对于直径大于75mm勺散装填料,可取最小润湿速率(Lw)所以,取最小润湿速率为:
查参考书[2]附录五得
故满足最小喷淋密度的要求.
经以上校核可知,填料塔直径选用D=1200m合理。
填料塔填料高度计算
3.4.1传质单元高度计算
气相总传质单元高度采用修正的恩田关联式计算:
查参考书[2]表5-13得
液体质量通量为
气膜吸收系数有下式计算:
气体质量通量为:
液膜吸收系数由下式计算:
由kGakGaw1.1,查参考书[2]表5-14得
则kGakGaw1.10.03390.635132.51.451.14.292kmol
3
)min=0.08m/(m•h)
min=0.12m3/(m•h)
/(m3hkPa)
由kGa19.5(巴0.5)1.4kGaUf
kLa12.6(乂0.5)22&
a
19.5(0.70030.5)1.44.2928.585kmol/(m3hkPa)
由Hog
V
KGa
108.67
2
1.617101.30.7851.22
0.587m
3.4.2传质单元数的计算
脱吸因数为
气相总传质单元数为:
3.4.3填料层高度计算
由ZHogNog0.5876.3643.7357m得
设计取填料层高度为Z6m
查参考书[2]表5-16得,对于阶梯环填料,h/D=8〜15,hmax6m
取一8,则h81200mm9600mm
D
计算得填料塔高度为6000mm故不需分段。
填料塔附属高度计算
塔上部空间高度可取1.2m,塔底液相停留时间按1min考虑,则塔釜所占空间高度为考虑到气相接管所占的空间高度,底部空间高度可取2.1m,所以塔的附属高度可以取2.9m.
经参考书⑷查得;
直径D=1200mr的椭圆封头总深度H为325mm
液体分布器计算
3.6.1液体分布器
液体分布装置的种类多样,有喷头式、盘式、管式、槽式及槽盘式等。
工业应用以管式、槽式及槽盘式为主。
1.液体分布器设计的基本要求。
性能优良的液体分布器设计时必须满足以下几点:
(1)液体分布均匀评价液体分布的标准是:
足够的分布点密度;
分布点的几何均匀性;
降液点间流动的均匀性。
①分布点密度液体分布器分布点密度的选取与填料类型及规格、塔径大小、操作条件等密切相关,各种文献推荐的值也相差较大。
大致规律是:
塔径越大,分布点密度越小液体喷淋密度越小,分布点密度越大,对于散装填料,填料尺寸越大,分布点密度越小。
表3-1列出了散装填料塔的分布点密度推荐值
表3-1Eckert的散装填料塔分布点密度推荐值
塔径,mm
分布点密度,点/m2塔截面
D=400
330
D=750
170
1200
42
②分布点的几何均匀性分布点在塔