钢结构桥梁加工制作方案Word格式文档下载.docx
《钢结构桥梁加工制作方案Word格式文档下载.docx》由会员分享,可在线阅读,更多相关《钢结构桥梁加工制作方案Word格式文档下载.docx(25页珍藏版)》请在冰豆网上搜索。
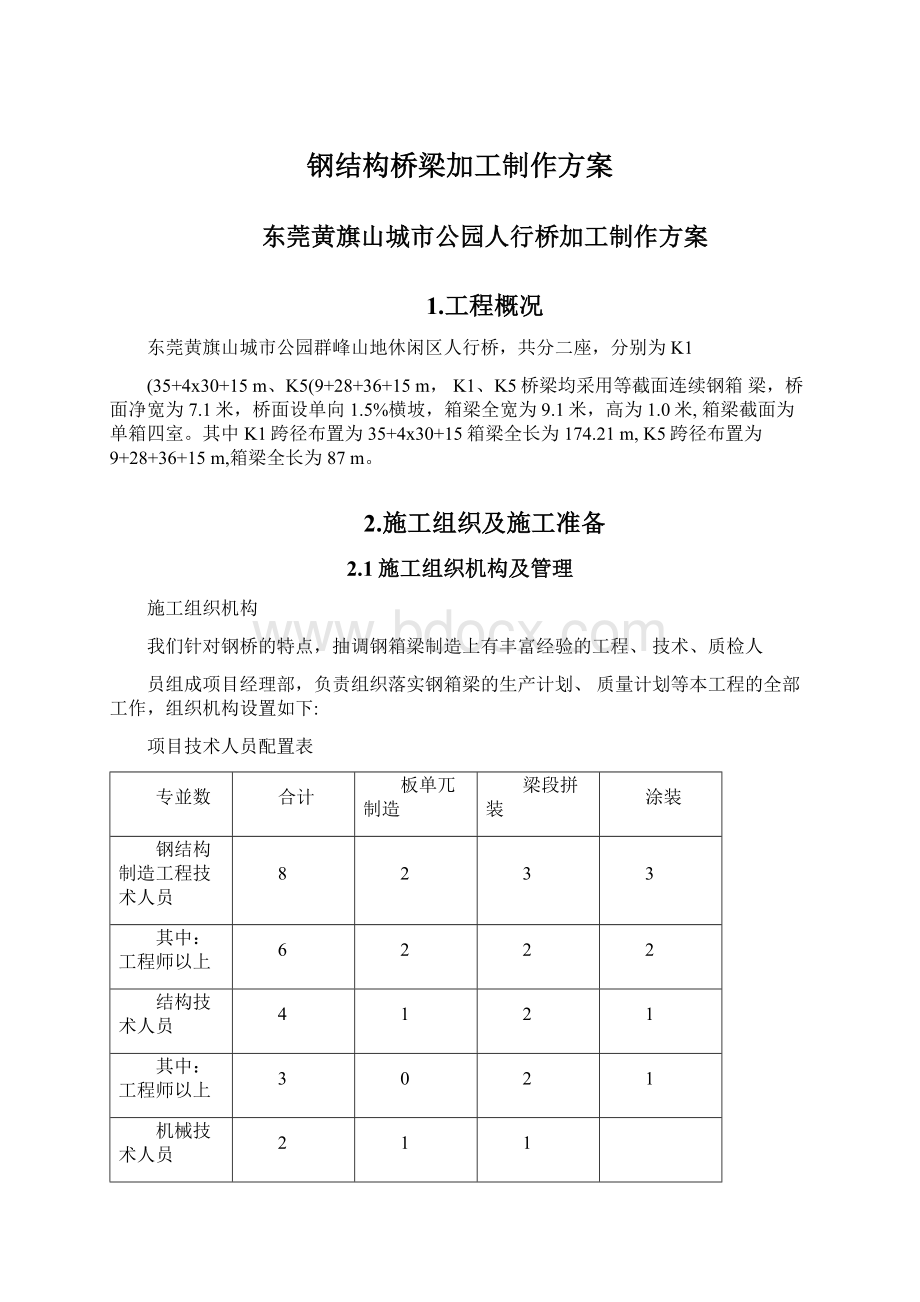
钻工
5
高强栓施拧工
20
电焊工
26
36
7
打磨工
10
涂装工
9
起重工
12
吊车司机
检杳工
探伤工
运输工(陆地)
14
运输工(水上)
15
辅助工
合计
142
168
86
抽调具有丰富经验的技术、管理人员组成项目经理部。
投入本工程的技术人员和工人是一支高素质的施工队伍,其中绝大多数人都参加了类似工程箱梁的制造工作
2.2钢桥制造施工组织流程图
2.3施工管理
(1)施工管理图
(2)拟投入本工程的主要施工机械、试验和检测仪器
序
号
设备名称
单
位
数量
完好
程度
备注
自有
租赁
新购
数控切割机
台
全自动
数控直条切割机
半自动气割机
铳边机
立式刨床
五维切割机
摆臂钻床
磁座钻
辊式板材矫正机
焊机
电焊机
17
CQ焊机
CQ角焊机
埋弧焊机
2.4材料采购及管理
1.材料采购
(1)材料采购计划
钢板的采购分批进行,分批进场。
焊接材料的采购满足生产需要,并提前考虑焊材复验时间。
(2)在材料采购过程中参照图纸上的相关技术要求执行。
2.材料复验
1)钢材首先必须进行质保书检查,即核对质保书和实物的炉批号做到证物
相符;
其次进行外观检查与板厚检验;
最后根据GB/T1591—2008和GB/T7O0-
1988标准要求,按同一厂家、同一材质、同一板厚、同一出厂状态每10个炉批
号抽检一组试件,作化学成份、力学性能试验,验收标准:
GBIT709-1988,
GBIT1591-2008。
2)焊接材料首先必须检查质保书,做到证物相符,其次进行外观检验。
最后,首批按型号、规格各取一组进行化学、力学性能试验,并按相应验收标准要求进行。
3)所有材料均应根据验收标准复检合格后方可使用。
3.材料管理
1)材料检验合格,由质检部分在质保书上加盖合格印章,编上序号,作为
领料依据,不合格材料反馈给供货单位及时换料。
2)本工程材料专料专用,物质部门必须妥善保管。
作明显的标记,严格材
料领退制度,严格退料管理,以免使用过程混用。
3)所有材料应妥善存放,避免积水积尘,防止腐蚀。
4.技术准备
技术部认真研究理解业主提供的钢桥设计技术文件(设计图纸、规范以及技
术要求等资料),并请设计部门进行设计交底。
在此基础上,完成施工图转化、工装设计等技术准备工作。
1)施工图绘制
施工图按钢桥板单元分类绘制,全部采用计算机完成。
内容包括:
板单元施工图、钢桥拼装总图、立体分段拼装顺序图、分段施工图、材料明细表等。
施工图绘制程序如下:
2)工装设计
a)为保证各梁段的制造精度,提高生产效率,将设计制造或改制一系列工
装,具体如下表:
立体分段制造
1、板单兀疋位组装平台
1、工艺拼接板
2、板单元检测平台
2、板块拼装胎架
1、施工平台
3、焊接反变形胎
3、多段匹配组焊及预拼胎架
4、横隔板单元组焊胎架
b)工装设计流程图
2.5工艺评定
1.焊接工艺评定
1)焊接工艺评定是编制焊接工艺的依据,应在钢箱梁制造开工前完成。
评
定试验用的母材应与产品一致,尽可能选用C.S.P含量上限制备试板。
试板焊接
时,要考虑坡口根部间隙、环境和约束等极限状态,以使评定结果具有广泛的适用性。
焊缝力学性能等方面和母材匹配。
焊缝的冲击韧性指标原则上与母材相等,按GB/T1591—2008标准执行。
2)根据本桥设计图纸的规定,编写《焊接工艺评定任务书》。
根据批准的焊接工艺评定任务书,模拟实际施工条件,逐项进行焊接工艺评定试验。
3)针对本桥钢箱梁的接头形式,初步拟订焊接工艺评定方案。
4)焊接工艺评定试验提供最终报告,经监理工程师审查、批准生效,并在生产中跟踪、检查、补充和完善施工工艺。
如生产过程中某焊接工艺产生不稳定低于质量要求时应立即终止使用。
5)试验报告按规定程序批准后,根据焊接工艺评定试验报告编写各种接头的焊接工艺指导书。
焊接工艺指导书经监理工程师批准后,根据焊接工艺指导书的内容组织施工。
2.工艺文件的编制
按照招标文件《技术总说明》和设计文件的要求,编制各个工序的工艺文件,用于指导生产,控制施工质量。
3.板件制作
3.1板材下料、加工
(1)放样
1)制作专用钢样条时,必须考虑加工余量及焊接收缩量。
2)样板、样杆、样条制作允许偏差应符合下表规定。
样板、样杆、样条制作允许偏差(mm)
检查项目
允许偏差
曲线样板上任意点偏差
±
0.5
样板长度、宽度,样杆长度
+0.5、-1.0
两相邻中心线距离
1.0
3)放样时必须熟悉施工图及工艺文件,严格按照施工图、工艺文件和本规
则有关规定制作,有问题及时反馈。
4)对于形状复杂的零件、部件、在图中不易确定的尺寸,应通过放样校对后确定。
5)板材标注:
板材名称、件号、材料号、规格、数量、孔的直径、孔列轴线与基准面距离等。
字迹要整齐,清晰。
(2)号料
1)由熟悉图纸及工艺的专人负责板片的号料、划线。
且号料所划的切割线必须准确、清晰。
号料尺寸允许偏差:
土1mm。
2)下料应尽量从无钢印标识端开始,零料应为具有钢厂原始刚印端,且切割端用记号笔相应移植钢板原始标记。
剩余的钢料必须标明钢材的牌号和检验号,以便下一批次使用。
3)门吊主结构均为定尺板,下料前应认真核对板材的材质、规格等,确认下料钢板的标记相符后,才能进行切割。
4)发现钢料不平直,有锈及油污,影响号料及切割质量时,应矫正清理后再号料。
5)样板、样杆、样条必须与工艺文件核对,相符后方可号料划线。
6)板材的刨(铣)加工量、焊接收缩量应按样板、草图、样条要求预留。
7)板材采用气割时,应根据钢板厚度和切割方法,一般预留2~4mm切口
量,较厚者宜多留。
8)号料的量具必须使用经计量合格的钢卷尺。
(3)切割
1)零件采用数控切割和半自动割下料,并及时清理氧化铁等杂物,所有零件的自由边应打磨光滑,做好零件代号的标识。
腹板及不规则的零件应采用数控切割。
2)气割零件尺寸允许偏差应符合下列规定:
自动切割、半自动切割:
土1.5mm
高精切割、精密切割:
土1.0mm
3)切割面垂直度偏差不应大于零件厚度的5%,且不应大于2mm。
4)需自动焊拼板的板边不直度应w0.8mm,其坡口可采用自动、半自动割或切割设备开设,坡口粗糙度w0.8mm。
5)气割前应对设备、工具进行检查,确认完好,可靠后方可气割,并根据材质厚度选择合适的工艺切割参数。
6)气割前应将料面上的浮锈及脏物清除干净。
钢料应放平、垫稳、割缝下面应留有空隙。
(4)拼板
1)认真核对材料标记,确认零件代号正确无误后,对板材进行拼焊。
2)对于厚度12mm以上的板材,使用半自动切割机开设坡口,并打磨光滑;
若使用碳弧气刨,则在气刨后彻底清除缝内氧化物等杂质,以保证焊接质量。
3)12mm以上厚度板材拼接时,应装配引熄弧板。
且引熄弧板与母材等厚,宽x长尺寸为150X(200~300)mm,并开设与板材相同尺寸的坡口。
4)拼板的间隙为0s1mm,板材错边量不大于0.8mm,且其板端对齐。
5)对焊接的角变形采用火工或压重等方法校平,板缝应经无损探伤检验合格方可转入下道工序。
为保证板材具有足够的韧性,对于采用火工矫正的板件,不得采用水冷。
6)钢板自动焊的余高为2s4mm,对大于4mm或低于母材的应打磨或补焊处理。
(5)边缘加工
1)零件磨边、磨头、磨弧时,应磨去边缘的飞刺,气割边缘的挂渣及切口棱角的波纹,并应将崩坑等缺陷部位磨修匀顺。
2)零件应根据预留加工量及平直度要求,两边均匀加工。
3)边缘加工后,必须将边缘刺屑清除干净。
4)根据板厚不同,板厚差削斜为1:
4,具体以下料图为准。
5)钢箱梁、横梁所有永久外露自由边均应把其边缘直角打磨成R>
1.0mm的
圆弧,以便满足电弧喷涂工艺要求。
(6)除刺和刨边
1)孔边的飞刺、板层间刺屑、边缘的飞刺、电焊熔渣飞溅等,均应铲除干净,并不得损伤母材,杆件边缘和端部的允许缺陷均应铲磨匀顺。
2)切割边的飞渣应铲除干净,开孔、尺孔打磨均顺。
(6)板单元的制作
1)板单元的划分
人行钢桥均采用等截面连续钢箱梁结构,人行钢桥K1共划分为24个节段,
人行钢桥K2共划分为12个节段,每个节段大体上由桥面板、桥底板、腹板及隔
板等组成。
2)板单元制造工艺
a.顶、底板制作工艺
•钢桥顶、底板精切下料后用赶板机赶平,严格控制平面度。
长板于赶平前用调直机调直。
•切割面垂直度偏差不应大于零
件厚度的5%,且不应大于2mm。
•需自动焊拼板的板边不直度应w
0.8mm,其坡口可采用自动、半自动害V或切割设备开设,坡口粗糙度w0.8mm•在反变形胎架上进行焊接作业,以减
少焊接变形,焊接结束后对变形的部位火工效正,保证制作好的板件无变形.
•组焊外壁板和球扁钢或T肋时,选用
CO2气体保护焊接,以减小焊接变形。
下料
组装纵肋
•钢桥顶、底板板块采用数控精
切(含坡口),一端留配切量。
纵肋数控精切下料。
•对板件矫正时,严格遵守火工
•采用反变形,用CO2自动焊机施
•采用磁力吊吊钢板,以防产生
•用赶板机赶平,严格控制平面
度。
长肋板于赶平前用调直机调
直。
b.隔板制作工艺
•隔板精切下料后用赶板机赶平,严格控制平面度。
长板于赶平前用调直机调直。
件厚度的5%,且不应大于2mm。
•组焊隔板和加筋板时,选用CQ气体保护焊接,以减小焊接变形,焊后控制松卡温度。
•隔板板块采用数控精切,切割完毕后用赶板机赶平,严格控制平面度。
长板于赶平前用调直机调直。
矫正工艺。
永久变形。
隔板制作工艺流程
不合格品控制程序
检查查
不合格品控制程序
N
*
C.板单元的拼焊
并按需进行火焰校正。
a)板单元拼焊前,先对纵肋进行小组装焊,
b)拼装的零件必须经过校正,并将连接表面及焊缝位置30至50mm范围
内的铁锈、毛刺、脏物、油污等清理干净。
c)焊接拼装不得超过允许的尺寸偏差,如下表所示:
类别
项目
板对
接
S
1[_
单面焊对接错边
SW0.1且Smax=2mm
双面焊对接搓边
Sw0.15且Smax=3mm
搭接
搭接长度
L>
2(合1+合2)
)二7厂
ZZXI
□
L
翼缘
板
■B
翼缘板倾斜度
△wB/500
二
、-,rri
h
J
翼缘板对垂直腹位
移
h<
3mm
相对
应的受力竖板
-
重叠尺寸
d>
2/3S
d
d)基本焊接结构件制造的允许偏差,如下所示
箱形梁或工字形梁腹板
的波浪度
以1m平尺检查,在
受压区域的H/3的区域内,不大于该区域板厚的0.7倍,且在相邻筋板间凹
凸不超过一处。
4•钢桥组装焊接工艺
拼装方式的选择
钢桥的截面尺寸为K1(9100X1000X174210)mm、K5(9100X1000X87000)mm,为了拼装方便且便于控制,采用倒装的形式,以顶板为基准面进行拼装,倒装时保证腹板和地面垂直,并严格按照起拱曲线控制起拱线形。
拼装的顺序是先铺设顶板,检验合格后安装箱梁内部横隔板,然后安装隔板,调整好线型后,安装腹板,最后安装底板。
人行桥钢箱梁K1一共24个分段,单边12个分段,拼装时第一轮4个分段进行一次整体预拼,拼装结束后将前最后一个移至段首和下一轮的第一个进行预拼,24个分段分4轮完成。
人行桥钢箱梁K2一共12个分段,单边6个分段,拼装时第一轮4个分段进行一次整体预拼,拼装结束后将前最后一个移至段首和下一轮的第一个进行预拼,12个分段分2轮完成。
典型梁段拼装
现以典型标准段的拼装为例来进行阐述钢桥拼装的一般过程,其他分段的拼
装过程类似。
步骤一:
拼装胎架的搭设
步骤二:
拼装顶板
步骤三:
完成顶板的拼装
步骤四:
安装中间腹板、中间内隔板
严护板
rr
11p1111
;
IFTTT"
T
1LI9Il丄
尸\
IrTTTT
nttir
I
钢桥分段拼装完成后,进行预拼装。
箱梁总拼采用无间隙拼装,箱梁间仅留有焊缝间隙,一般为6~10mm。
因此,箱梁基线间距L=LO箱梁长度)+A(焊缝间隙)。
另外,为保证箱梁总长,在最后一个分段上,留有二次切割量。
预拼装调整简要步骤如下:
1)水准仪配合对箱梁整体标高进行测量,如有超差,使用液压千斤顶等工具进行调整,直至符合要求;
2)使用经纬仪或全站仪等测量工具,根据板件制作横纵基线调整箱梁间距;
3)匹配完成后,在节段对接口焊缝中心两侧150mm放拼装基线,以便现
场节段对接。
尺寸公差
钢箱梁尺寸公差见下表:
箱梁制作尺寸公差见下表:
板对接
单面焊对
SW0.13,且Smax=2mm
•■■■■
2Jr;
<:
■z
接错边
双面焊对
接搓边
SW0.153,且Smax=3mm
2(31+32)
//I
翼缘板
—■-
B
翼缘板倾
斜度
翼缘板对
垂直腹位
hw3mm
相对应
的受力
竖板
d>
2/33
///////
6.涂装工艺
6.1涂装技术要求
部位
油漆种类
干膜厚度um
箱梁内
部
LS-1水性无机环氧富锌涂料
50umX2
车间喷涂
箱梁外
铝涂层
150um
露面
专用铝涂层封闭层
40umx2
面漆
50umx1
工地现场喷
涂
6.2喷砂、油漆施工顺序详述
a)打砂前检查分段表面,确认没有焊瘤、飞溅、毛刺等缺陷,自由边锐角打磨至R2。
b)清除分段表面的积水及杂物,并用清洁剂清除钢材表面的油脂、油污。
c)清除钢材表面的油污、水份、灰尘、盐分、焊接烟尘、粉笔或油漆记号。
d)分段用平板车运进油漆车间,放在专用支墩上。
e)准备通风、照明设备和脚手架。
f)保护不需打砂油漆的构件及设备。
g)环境控制:
检查并记录气温、钢板温度、相对湿度、油漆温度。
相对湿度不超过85%,
钢板温度必须高于露点3°
C。
当环境状况达不到上述要求时停止施工或加开除湿设备。
h)选用10〜30目的铜矿砂,确保打砂后的粗糙度在40〜100um之间。
i)检查压缩空气的压力、油水分离状况等,确保贮气罐内的空气压力在6〜7kg/cm2,且油水分离器工作正常。
j)砂枪距钢材表面约20〜30cm,喷砂角度保持在60〜80°
,匀速移动,
每分钟约0.5〜1.0m。
k)依据GB8923-1988《涂装前钢材表面锈蚀等级和除锈等级》或ISO
8501-1:
1988《钢材表面涂装油漆前的除锈和清洁度的目视评定》中的文字描
述和图片对照检查打砂后钢材表面的清洁度,外表面确保达到Sa2.5级,内表面
确保达到Sa2级,粗糙度介于40〜100之间,不合格部位重新打砂。
l)打砂检查合格后,用干燥、清洁压缩空气吹去表面砂粒,并用工业吸尘器除尘。
m)喷砂合格后,在尽可能短的时间内喷底漆,一般要求不超过6小时。
喷
漆后8小时内防止雨淋。
n)采用高压无气喷涂设备进行喷涂施工,大面积喷涂前对焊缝、边角、难
以喷涂到的部位先进行预涂。
为缩短打砂表面在空气中的曝露时间,底漆喷涂前可以不进行预涂,但底漆干燥后应进行补涂。
o)喷漆前用100毫米宽的胶纸保护待焊接部位,,不需油漆的构件和设备也应预先保护。
p)每道油漆的喷涂参数见附页,此为指导现场施工的技术依据。
q)按照附页中的技术参数完成底漆、中间漆、面漆的施工,喷涂下道油漆
前先对上道油漆缺陷进行修补、清洁,并先进行预涂。
r)整个分段油漆完工后,折除脚架和照明设备,用600T平板车把分段运
到储存场地。
s)清除车间内的废砂,等待下一个分段进入。
6.3.喷漆施工的操作要领
1)领料检查:
核对所领材料是否为待施工部位油漆配套中规定的材料,检查油漆桶密封是否完好,若有破损、渗漏、涨桶现象,应在征得油漆供应商许可的情况下才能使用。
2)开桶检查:
若发现有凝胶、结快、变色等现象,则基本断定涂料已变质,应当废弃。
但轻微的沉淀结快经充分搅拌均匀后仍可使用。
3)开桶:
用风动搅拌机把基料、固化剂分别搅拌均匀,按照产品说明书中
的混合比例把固化剂加入到基料中,搅拌均匀。
如有需要,再按产品说明书中的要求加入适量配套稀释剂,搅拌均匀。
4)选用无气喷漆泵,压缩比45:
1或60:
1均可,喷嘴选用IP产品说明书中推荐的喷嘴型号。
喷幅的大小取决于被涂构件的形状和大小,对于大平面,可选用喷幅较大的喷嘴,而复杂构件则选用喷幅较小的喷嘴。
5)喷涂施工前对待焊接的焊缝、不需涂漆的构件及设备进行保护。
6)一般米用先上后下、先内后外、先难后易的原则进行喷涂施工,喷涂时
注意每道漆膜之间的搭接,一般搭接宽度为喷幅的1/2。
7)喷嘴距离构件表面的距离一般为30um左右,尽量使喷枪与被涂构件表面保持垂直,运行速度均匀,避免因过快过慢引起膜厚不够或流挂、超厚现象。
8)喷涂拐角处,喷枪要对准中心线,确保两侧都得到均匀的膜厚。
9)喷涂过程中应经常使用湿膜卡,用于控制干膜厚度。
10)喷涂过程中要随时检查刚刚喷过的漆膜是否存在针孔、汽泡、鱼眼、流挂等缺陷,如有应马上停止喷涂施工,分析原因,检修设备,并试喷成功后再继续喷涂。
如发现露底时应立即补喷。
11)喷涂结束后应及时用清洁剂清洗喷漆设备,尤其是喷漆泵和喷枪,防止油漆留在其中固化导致设备无法正常使用。
12)喷涂完工后,依据产品说明书中的干燥时间等待油漆充分干燥,等油漆
干燥后及时对露底、膜厚不够部位进行补涂,并处理涂层上的流挂、颗粒、桔皮等缺陷,并对焊缝、边角及难以喷涂部位进行预涂,准备下道油漆的施工。
6.4损坏区域修补程序
在吊装、运输分段时要警惕,避免破坏涂层,如果涂层已有损坏,按下述程序修补:
1)缺陷例如针孔、气泡、流挂、流淌、过喷、桔皮、鱼眼等应采用细砂纸轻轻打磨(手工或动力工具)缺陷边缘,用吸尘器或其它合适方法去除灰尘和附着不牢的碎片,然后补涂相同油漆。
2)露出钢材基底损坏部位用动力工具打磨至St3级(ISO8501—1标准),其它需补涂的部位首先除去油污、灰尘、可溶性盐,临近至少25mm的完好涂层用砂纸打磨成45°
的坡度。
3)没有露出钢材基底的损坏区域首先除去油污、灰尘、可溶性盐,接着用砂纸把漆膜拉毛。
补涂的油漆的周边应覆盖完好的涂层25mm,后续补涂的涂层都应盖住前道涂层且再向周边延伸25mm。
7.焊接工艺
(1)目的与范围
在现代钢结构制作中,焊接工序相当重要,焊缝质量的好坏直接影响产品质量,为了确保钢桥整体焊接质量,特制定本工艺规程。
(2)参考
GB5117-85,GB5118-85,GB6417-86,GB985-88,GB986-88,