花生脱壳机结构造型设计Word文档下载推荐.docx
《花生脱壳机结构造型设计Word文档下载推荐.docx》由会员分享,可在线阅读,更多相关《花生脱壳机结构造型设计Word文档下载推荐.docx(16页珍藏版)》请在冰豆网上搜索。
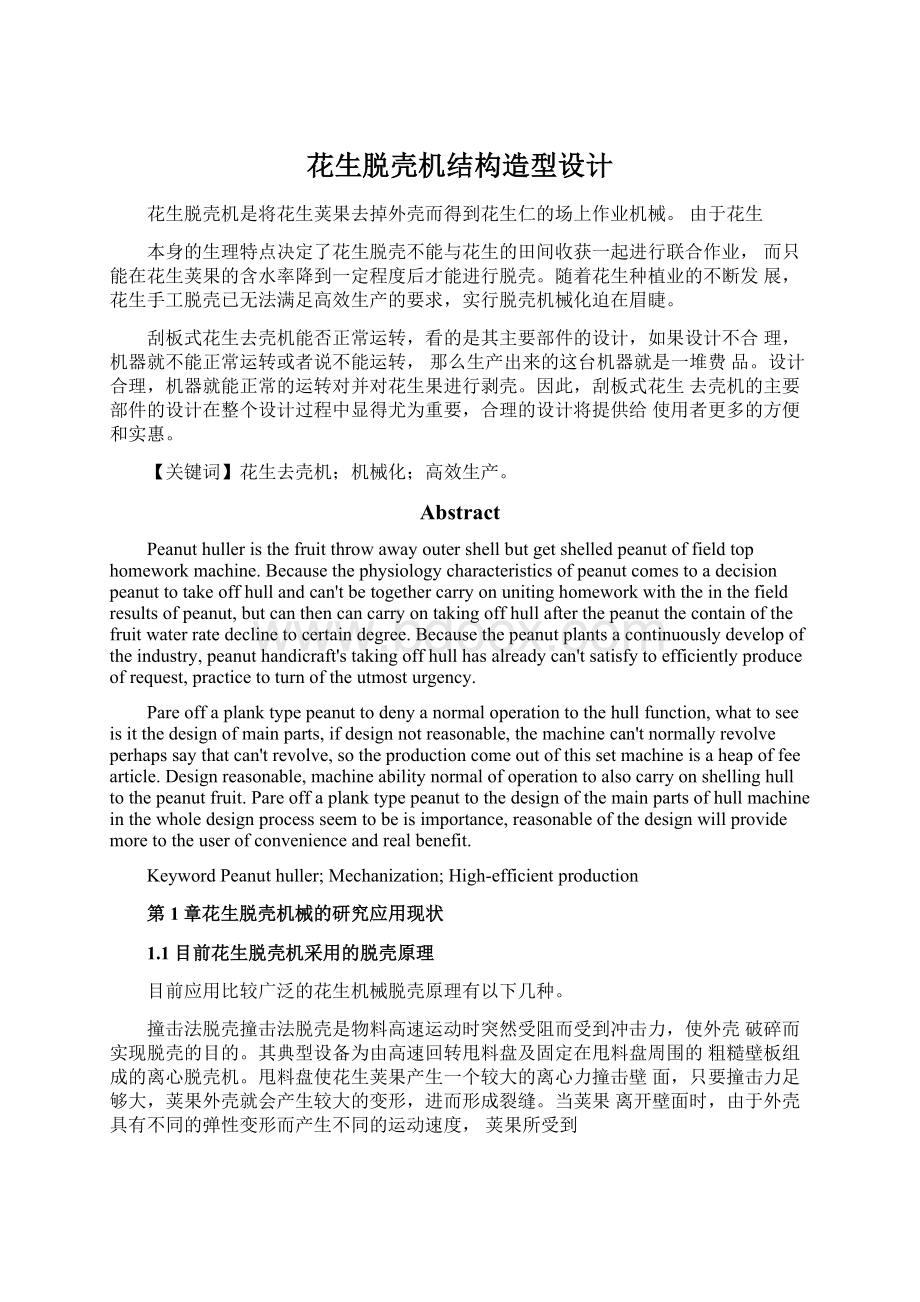
该种方法影响因素有,荚果的水分含量、圆盘的直经、转速高低、磨片之间工作间隙的大小、磨片上槽纹的形状和荚果的均匀度等。
剪切法脱壳花生荚果在固定刀架和转鼓间受到相对运动着的刀板的剪切力的作用,外壳被切裂并打开,实现外壳与果仁的分离。
其典型设备为由刀板转鼓和刀板座为主要工作部件的刀板剥壳机。
在刀板转鼓和刀板座上均装有刀板,刀板座呈凹形,带有调节机构,可根据花生荚果的大小调节刀板座与刀板转鼓之间的间隙。
当刀板转鼓旋转时,与刀板之间产生剪切作用,使物料外壳破裂和脱落。
主要适用于棉籽,特别是带绒棉籽的剥壳,剥壳效果较好。
由于其工作面较小,故易发生漏籽现象,重剥率较高。
该种方法影响因素有,原料水分含量、转鼓转速的高低、刀板之间的间隙大小等。
挤压法脱壳挤压法脱壳是靠一对直径相同转动方向相反,转速相等的圆柱辊,调整到适当间隙,使花生荚果通过间隙时受到辊的挤压而破壳。
荚果能否顺
利地进入两挤压辊的间隙,取决于挤压辊及与荚果接触的情况。
要使荚果在两挤压辊间被挤压破壳,荚果首先必须被夹住,然后被卷入两辊间隙。
两挤压辊间的间隙大小是影响籽粒破损率和脱壳率高低的重要因素。
当荚果到达荚果受压产生弹性一一塑性变形,此时
在上述相反方向撕搓力的作用下完成脱壳过胶压辊的硬度、轧入角、轧辊半径、轧辊
搓撕法脱壳搓撕法脱壳是利用相对转动的橡胶辊筒对籽粒进行搓撕作用而进行脱壳的。
两只胶辊水平放置,分别以不同转速相对转动,辊面之间存在一定的线速差,橡胶辊具有一定的弹性.其摩擦系数较大。
花生荚果进入胶辊工作区时,与两辊面相接触,如果此时荚果符合被辊子啮人的条件,即啮人角小于摩擦角,就能顺利进入两辊问.此时荚果在被拉人辊间的同时,受到两个不同方向的摩擦力的撕搓作用;
另外,荚果又受到两辊面的法向挤压力的作用,辊子中心连线附近时法向挤压力最大,荚果的外壳也将在挤压作用下破裂,程。
影响脱壳性能的因素有,线速差、间间隙等。
1.2新型脱壳技术
压力膨胀法原理是先使一定压力的气体进入花生壳内,维持一段时间,以使花生荚果内外达到气压平衡,然后瞬间卸压,内外压力平衡打破,壳体内气体在高压作用下产生巨大的爆破力而冲破壳体,从而达到脱壳的目的。
主要影响因素有,充气压力、稳定压力维持时间、籽粒的含水率等。
真空法将花生荚果放在真空爆壳机中,在真空条件下,将具有相当水分的荚果加热到一定温度,在真空泵的抽吸下,荚果吸热使其外壳的水分不断蒸发而被移除,其韧性与强度降低,脆性大大增加;
真空作用又使壳外压力降低,壳内部相对处于较高压力状态。
壳内的压力达到一定数值时,就会使外壳爆裂。
激光法用激光逐个切割坚果外壳。
试验显示,用这种方法几乎能够达到1009/6的整仁率,但因其费用昂贵、效率低下等原因,很难得到推广。
1.3花生脱壳机械的工艺研究
在脱壳技术方面,除了在原理和设备上进行研究外,人们还在工艺上进行了研究以提高籽粒的脱壳率及脱壳质量。
分级处理物料的粒度范围大,必须先按大小分级,再进行脱壳,才能提高脱壳率,减少破损率。
水分含量花生荚果的含水率对脱壳效果有很大的影响,含水率大,则外壳的韧性增加;
含水率小,则果仁的粉末度大。
因此应使花生荚果尽量保持最适当的含水率,以保证外壳和果仁具有最大弹性变形和塑性变形的差异,即外壳含水
率低到使其具有最大的脆性,脱壳时能被充分破裂,同时又要保持仁的可塑性,不能因水分太少而使果仁在外力作用下粉末度太大,可减少果仁破损率。
1.4花生脱壳机械存在的问题
目前我国在花生脱壳技术研究方面一直没有大的突破,资金投入也不足,脱
壳部件的研制仍在2O世纪90年代初的技术水平上徘徊,所以在脱壳性能上并没有很大的提高。
由于机械脱壳时对花生仁的损伤率偏高,用于种子和较长期贮存的花生仁至今仍是手工剥壳。
脱壳机械在技术性能和作业环节上存在以下问题:
①
脱壳率低,脱壳后的果仁破损率高,损失大。
②机具性能不稳定,适应性差。
③通用性差,利用率低。
④作业成本偏高,多数是单机制造,制造的工艺水平较低,同时能耗较高。
⑤有些产品仅进行了样机试制或少量试生产,未进行大量生产性考核和示范应用,作业性能及商品性等方面还存在不少问题。
第2章刮板式花生去壳机的结构及工作原理
2.1刮板式花生去壳机的结构
根据刮板式花生去壳机的剥壳原理可知道,花生是从上至下依次经过集料斗、剥壳箱、栅格、下箱出口、分选口,花生仁收集斗这些部件的,因此设计剥壳机的整体结构的依据就出来了。
设计过程是从上往下,从花生的装集开始,最上面是集料斗,集料斗下方是
剥壳箱,集料斗可与剥壳箱设计为一个整体。
在剥壳箱内,花生必须经过刮板的撞击和挤压作用才能进行剥壳,因此,将刮板设计置在剥壳箱内。
花生经过刮板的撞击和挤压进行剥壳后,要经过位于剥壳箱底部的栅格,于是可以把栅格设计成一个半圆栅笼,将其固定在剥壳箱的下半箱内。
花生穿过栅格后经过剥壳箱底部的出口往下落,在下落过程中,设计一个风机的吹入口,其作用是将经过剥壳的花生壳与花生仁进行分离,重量稍重的不被风吹走,而重量较轻的花生壳将被风机吹来的气流带入到花生壳收集通道,通道的底部设计成一定角度。
经过分离的花生仁往下落,落入花生仁收集通道,将此通道与花生壳收集通道的底面设计成一个整体,这样的设计可以让被风吹走的花生仁通过自身的重量往下回滚到花仁收集通道。
为保证整机的各部分的安装,需设计一个机架,机架起到其它几个部分的支承、定位、连接作用,并将电机安装在机架里面,剥壳机安装在机架的上方。
其结构简图如图2-1所示。
图2-1
2.2工作原理
刮板式花生去壳机以前也称为刀笼剥壳机,是借助转动轴上的刮板与笼栅的
操作
挤压和打击作用,将花生果外壳破碎的一种机械设备,其特点是结构简单、
方便。
其结构如图2-2所示。
它主要由进料机构、剥壳机构和支承机构等部分组
花生果进入存料斗后,经下部的入料窄口形成薄层流落下来进入剥壳箱内,与高速旋转的刮板相互碰撞,在刮板的锤击下,花生壳发生破裂,从而进行第一次剥壳。
部分花生果在下落过程中没有与刮板发生碰撞,有些发生碰撞了而花生壳却未撞裂,这部分花生落入到由圆钢棒排列成的栅格上,由于栅格顶部与刮板的旋转外径间的间距不足以容纳一个花生果,因此花生果将在落入栅格的同时被刮板再次锤击和挤压,从而使这些花生果的果壳也被压碎。
剥壳后的仁与壳通过栅格间的间隙落下,在下落的同时,受到风机吹来的经调节好的气流作用,果壳因重量轻而被气流送入集壳通道,而花生仁因重量大,继续往下落,从而达到了
壳仁分离的目的。
第3章刮板式花生去壳机主要部件的结构设计
3.1设计前各项参数的确定
3.1.1刮板的半径及转速初定
刮板的旋转必须确保能将部分花生壳撞碎,当花生果与钢质物体相对速度达到5m/s时,可使花生壳破碎而不会破坏到花生仁,可根据此依据设计刮板的转速与半径。
计算半径
V=2耐
取半径R=250mm,则n=382.2r/min
结论:
R=250mm,
n=382.2r/min
3.1.2刮板所需功率计算
根据公式可计算出刮板所需的功率
刮板对花生做功
Q=Ek+Ep
Ek:
刮板改变花生的动能
Ep:
刮板改变花生的势能
Ek=E1+E2Jmu+^mv;
22
Ep=mgh=mgR
122
”Q=—(v-i+v2+gR)
2m
cQ1m“22f
P=—=—(V1+V2+gR)
t2t
根据所给产量要求1500kg/h,即0.417kg/s,此为花生仁的产量,折合花生果产量为0.417/纯仁率,根据国家标准,湖南所处地理位置可取花生的纯仁率为69%,折合花生果产量为0.604kg/s,此即每秒进入剥壳箱内被破碎的花生果的重量。
花生接触刮板时初速度设为1m/s,方向向下,脱离刮板时速度为15m/s,方向向左,脱离刮板时相对初位置高度为500mm
t=1sm=0.604kg/s
v1=1m/s
V=15m/s
R=0.5m
Q1m22
P=—=—(V1+V2+gR)=(0.302+67.95+2.96)W=71.212wt2t
加上刮板与花生在栅格中挤压所需要的能量,P也不会超过500w。
为计算电动机的所需工率Pd,先要确定从电动机到工作机之间的总效率n。
设n1、n2分别为滚动轴承和V带传动的效率,于是有
n=町+巧=-0.8668
电动机所需功率Pd=¥
不会超过700W,由于给定电动机的功率为1.5kW,远
大于此计算值,故所给电动机的功率完全符合要求。
3.1.3传动方案拟定
由于刮板式花生去壳机的工作轴旋转速度较高,达到n2=382.2r/min可有两
种选择,第一种是采用一级V带传动,第二种是采用两级混合传动,而很明显的,
所以选用一级
Y90L-4型和
若采用两级传动方案,将会致使机器的结构复杂,而且成本升高,V带传动。
3.1.4电动机的选择
根据所给的功率及同步转速,可选用的电机型号有两种:
Y100L-6型。
根据电动机的满载转速和刮板转速可算出总传动比,现将此两种电动机的数据和传动比列于下表
方案号
电机型号
额定功率kw
同步转速
r/min
满载转速
总传动比i
1
Y100L-6
1.5
1000
940
2.459
2
Y90L-4
1500
1400
3.663
由上表可知:
方案1总传动比虽小,转速低,但价格高,作为家用机械的电机不是太合算,故选择方案2,即电机型号为丫90L-4。
查表得此种电动机的中心高H=90mm外伸轴径为24mm轴的外伸长度为
50mm3.1.5传动装置的运动和参数计算
轴的转速
ni=1400r/min
门2=m/i=382.2r/min
轴的输入功率
P2=Pd咒*2=1.5X0.95=1.35kw
轴的转矩
T^955OP2/n2=33.732N.m
3.2V带传动
首先列出设计的基本条件
电机型号:
额定功率:
1.5kw
传动比:
i=3.663
假设每天运转时间t<
10h1.确定计算功率PCa
查表得工作情况系数KA=1.1
FCa=KAP=1.1X1.5=1.65(kw)
2.选择V带带型根据Pea、m查得最适合的带型为A型3•确定带轮基准直径由主动轮基准直径系中选取dd1=75mm,从动轮基准直径为
dd2=!
2才=3.663x75mm=274.725mm
验算带的速度
v=
60x100060X1000
呵dmZ75"
400m/s=5.498m/s
v=5.498m/s<
Vmax=25m/s
因此所选带的速度合适4•确定中心距a和带的基准长度根据0.7^6+dd2)<
a0<
2(dd<
^dd2)初步确定中心距a0=700mm,计算
带的基准长度
由V带的基准长度系中选取基准长度Ld=2000mm
计算实际中心距a
a=a0+^^=(700+^72Amm=713.82mm
5.验算主动轮上的包角%
713.82
%=180”-280~75X57.5"
=160.68”A120
主动轮包角合适
6.计算V带的根数z
由片=1400r/min,dd^75mm,i=3.663查表得
P0=0.68kw,AP0=0.17kw,=0.95,K|=1.03
代入数值,经计算
Z=1.984
取z=2
7.计算预紧力Fo
F。
=500生(^-O+qv2=125.436NvzKa
&
计算作用在轴上的压轴力Fp
a1
Fp=2zF0Sin—
代入数值计算得
Fp=482.7N
9.V带轮的结构尺寸计算及选用
带轮材料选用HT200
根据基准直径的大小选用不同的带轮类型,小径带轮采用实心式,大径带轮
采用轮辐式,主要结构尺寸如下
单位:
mm
尺寸类型
小带轮
大带轮
dd
75
280
基准宽度bd
11.0
基准线上槽深hamin
2.75
基准线下槽深hfmin
8.7
槽间距e
15±
0.3
第一槽对称面至端面距离f
10:
1^2
轮缘厚d
12
带轮宽B
35
外径da
80.5
285.5
轮槽角护
38"
极限偏差
±
r
孔径do
26
16
轮毂长
50
d1
48
32
轮辐厚b1
8
h1
20
h2
D1
230.5
具体结构设计见零件图
3.3轴
“2=m/i=382・2r/min
P2=Pd叫=1・5X0・952=1.35kw
T2=955OP2/n2=33・732N・m
1初步确定轴的最小直径
先按经验公式算邮轴的最小直径,选取轴的材料为45钢,调质处理。
查表选取Ao=105,于是得
IIp2135
dmin闷丁105fe35r15・99mm
2拟定轴上零件的装配方案
通过对各种方案的比较,现选用图3-3所示装配方案
—
/
图3-3
3根据轴向定位的要求确定轴的各段直径和长度
(1)为满足V带轮的轴向定位,1-2轴右端制一轴肩,故取2-3段直径
d23=22mm,左端用轴端挡圈定位,取直径D=22mm。
V带轮与轴配合的毂孔长
试为35mm,为保证轴端挡圈只压在半联轴器上而不压在轴端面上,故1-2段长度取为I12=32mm
(2)初步选择滚动轴承因轴承只承受径向力,故先用深沟球轴承。
参照
工作要求并根据d23=22mm,初步选取深沟球轴承6205,其基本参数如下表
6204
基本尺寸
安装尺寸
极限转速
a
D
B
rsmin
da
Da
ras
脂润滑
油润滑
25
52
15
31
46
12000
16000
(3)安装刮板架段轴直径d45=60mm。
刮板架段安装宽度取145=542mm,
I=40mm,故取123=60mm
(5)取刮板距箱体内壁
a=20mm,取[34=40mm,|5^26mm。
至此,已初步确定了轴的各段直径和长度。
(6)轴上零件的周向固定
V带轮与轴的周向定位采用平键联接,按其直径查手册得平键截面如下
V带轮与轴的配合为H7/n6,滚动轴承与轴的周向定位是借过渡配合来保证的,此处选轴的直径尺寸公差为k6。
(7)确定轴上圆角和倒角尺寸
取轴端倒角2x45:
各轴肩处圆角半径见零件图
3.4刮板结构
刮板结构是整个机器的关键部分,它的作用就是对花生果进行剥壳。
此结构采用四钢板十字交叉固定在旋转筒架上,其结构如图3-4所示
图3-4
图3-3因为采用的是打击和挤压两种方式配合进行剥壳,所以对刮板的强度
M10螺栓联接。
有一定要求,采用材料是45号钢,而且刮板的表面必须进行处理,表面渗碳1-1.5mm,热处理硬度HRC56-62。
刮板选用四块8mm厚钢板,长咒宽=500mmx129mm,刮板外缘距旋转中心距离250mm。
固定刮板的筒架结构,其内径为26mm,外径120mm,刮板固定支架长度为140mm,截面尺寸40mm%20mm,每块刮板由两根固定支架固定,两者间采用
3.5半栅笼
半栅笼在机器中的作用是让已经被剥壳的花生与未被剥壳的花生进行分离,其分离的原理就是“小个通过,大个不过”。
半栅笼的每一个栅格都只能容许一个花生仁大小的物体通过,被剥壳的花生由于花生壳的破裂,被变成破碎的花生壳和整粒的花生仁,花生仁的大小刚好可以穿过栅格,而花生果因为太大,无法
通过栅格,将被阻挡在剥壳箱内,继续进行剥壳直到其外壳破碎为止。
其结构如图3-5所示。
图3-5
栅条是利用两块墙板对两端进行固定的,墙板材料为HT200,栅条材料为20号钢。
栅条采用*10圆截面长条,长度为538mm,因其特殊的作用,还需对其进行表面处理,要求渗碳1-1.5mm,热处理硬度HRC56-62。
栅条的两头装砌在墙板的圆形槽内,组成半圆栅笼,栅条间距为10mm,这样可使剥出的花生仁能通过栅格,而未剥壳的刚不能通过。
装砌完成后要太上锁紧条,防止栅条松动。
半栅笼内径为*516mm。
3.6箱体
箱体的作用是提供给刮板一个封闭的剥壳环境,并对相关结构起到支承和定位作用。
为了便于轴系部件的安装和拆卸,将箱体做成剖分式,箱由箱座和箱盖组成,取轴的中心线所在平面为剖分面。
箱座和箱盖采用普通螺栓联接,用圆锥销定位。
箱体的材料选用HT200,铸造成型。
具体结构设计见零件图。
3.7壳仁分离装置
壳仁分离装置分为两个部分,一个是气流通道,它的一端接风机,另一端安装在箱体的下方,还有就是壳与仁的收集板,它同样也安装在箱体下方。
花生经过箱体内的剥壳过程后,将由此装置对其进行壳仁分离,分离的基本原理是利用花生壳与花生仁的重量及受力面积的不同,用气流对其进行分离。
重量稍重的不被气流吹走,直接下落到花生仁收集通道,而重量较轻的花生壳将被风机吹来的
气流带入到花生壳收集通道。
具体结构见装配图。
3.8机架
整个机架采用L63*63*6角钢焊接而成,起到其它几个部分的支承、定位、连接作用,并将电机安装在机架里面。
剥壳机安装在机架上面,联接采用普通螺栓联接。
第4章总结
本文是围绕农用机械产品一一花生去壳机的设计,实现了花生剥壳的机械化,应用本机器后,可使广大农民群众大大节省劳动量,提高生产效率和生产质量。
该机的关键部分是刮板结构与半栅笼结构,因为花生剥壳的整个过程都是由这两部分完成的,剥出来