大包转台涂装要求Word格式.docx
《大包转台涂装要求Word格式.docx》由会员分享,可在线阅读,更多相关《大包转台涂装要求Word格式.docx(11页珍藏版)》请在冰豆网上搜索。
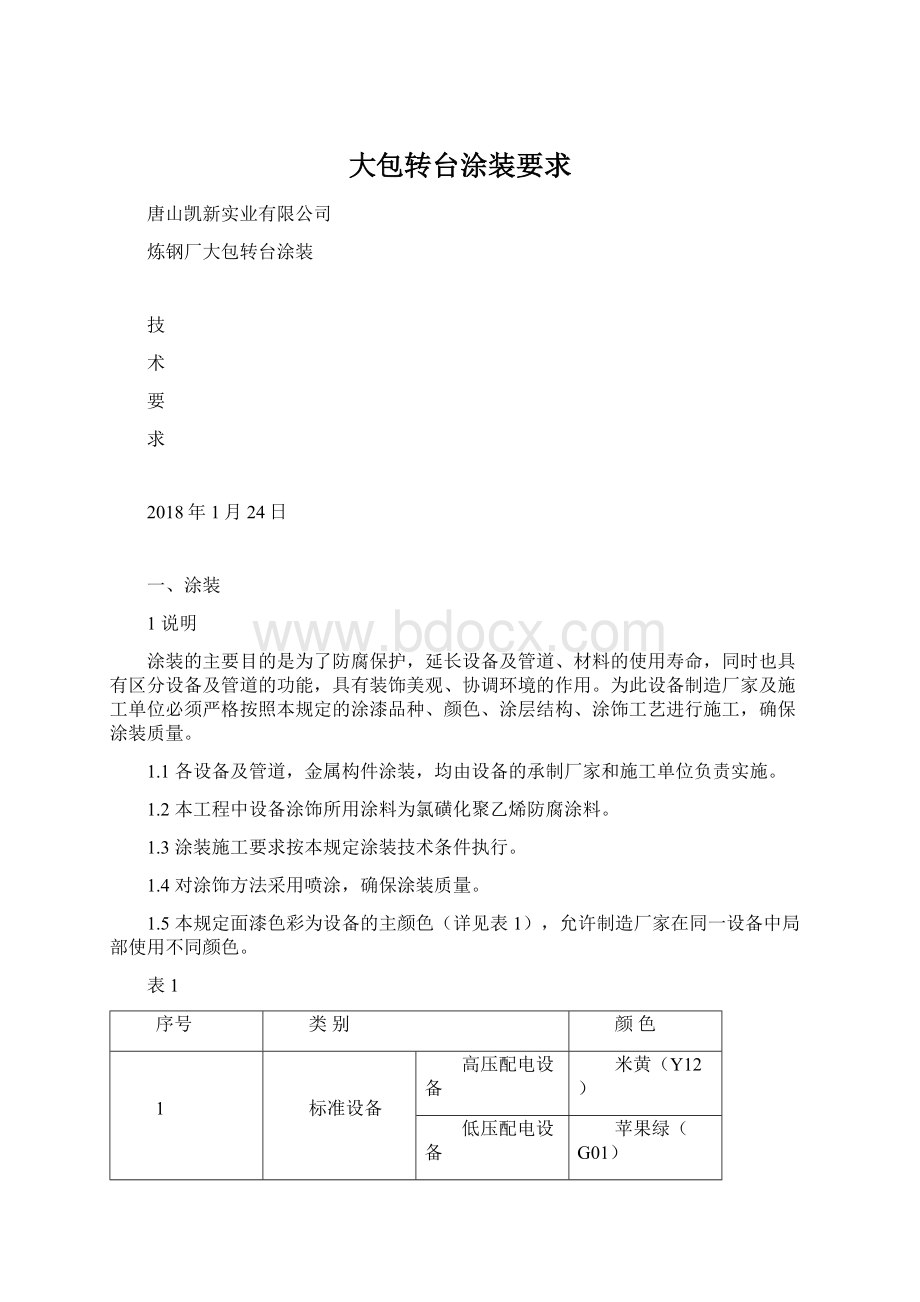
深灰(B01)
风机设备
电机:
深绿(G05)风机:
中绿灰(BG01)
破碎设备
浅灰(B03)
2
非标设备
输送设备
普通设备
平台
中黄(Y07)
3
仪器仪表
操作系统
控制系统
4
工艺管道
国际通用标准
1.6对某些设备及构件特殊部位或部件,尚须着其它色彩以装饰、警戒、转向、安全等标志(如操作手轮、阀门、联轴器、行轮轮廓和安全罩栏杆等)详见表2:
表2
产品特殊部位的名称
面漆色别(按GSBG51001)
油箱、减速机内表面及在其内零件的涂漆面
奶油色(Y03)
栏杆、扶手
黄色(Y06、Y07、Y08)
操纵室的顶插及内壁
半光浅色漆
操纵室地板
铁红色(R01)
盖板、走台板、辅板、楼梯板
与主机同色
外露的快速回转件,如飞轮、皮带轮、联轴器、人齿轮等
大红色(R03)
1.7涂装质量的验收标准
(1)所用涂料类别符合设计要求;
(2)表面处理、涂层结构、工艺符合JB/T5000.12-1998标准;
(3)面漆色彩符合色标;
(4)表面漆膜均匀、平整、光亮、无针孔、气泡、裂纹、脱落、流挂、漏涂等缺陷。
1.8本合同中所要求的漆膜颜色以GB3181-1995为准(详见该标准中的第4条)。
1.9在本文1.4中,对标准设备的涂装标明了面漆色彩的要求。
其涂层结构遵照表3中Ⅰ、Ⅱ、Ⅲ类标准。
表3
涂层
结构
涂料品种
底漆
中间漆
面漆
备
注
颜
色
涂层厚度
微米/道数
Ⅰ
氯磺化聚
乙烯涂料
铁红
50-60/2
棕褐色
40/1
各色
40-60/2-3
耐化工
大气
Ⅱ
40-80/2
60-80/3
耐酸、
碱、盐
Ⅲ
60/3
耐水、
耐油
Ⅳ
60-80/2
一般
设备
Ⅴ
保温
Ⅵ
兰陵牌W61-901
有机硅
高温防腐
E06-901
灰色
无机硅
酸锌漆
W91-9
高温
防腐漆
40/2
耐高温
设备400℃
Ⅶ
热喷涂铝
表面处理:
喷砂,喷涂材料:
铝丝,涂层厚度:
0.15~0.18
喷涂方式:
火焰线材喷涂,喷涂后用封孔技术封孔
Ⅷ
氯化橡胶
涂料
100-150/2
管道及金
属结构
注:
(1)表中涂层厚度为总厚度。
(2)兰陵牌氯磺化聚乙烯涂料型号:
底漆:
J52-81中间漆:
J52面漆J52-61。
(3)氯化橡胶涂料型号:
LJ06-1面漆:
LJB04-2。
2涂装技术要求
2.1涂装前物体表面处理
2.1.1各设备应采用喷砂除锈,处理质量不低于Sa2级或SSPC-SP6级。
2.1.2各管道及金属结构件不论采用何种除锈方式,处理质量不低于St3级要求。
2.1.3凡与高温直接接触的钢铁制件表面,表面不进行涂装或镀覆保护层时,处理质量必须达到St2级(详见附录A)。
2.1.4与混凝土接触或埋入其中的钢铁部件不必进行涂装。
2.1.5尺寸与重量较大的零件,可进行手工除锈,并达到St3级。
2.1.6进行酸洗处理的钢铁制件表面,除锈质量要求应达到Sa3级。
2.1.7铸、锻件需涂装的表面平度在任意方向600mm长度上,不得大于3mm,不允许有明显的凸起、飞边、毛刺、浇冒口等缺陷。
2.1.8焊接结构件需涂装的表面不允许有焊渣、药皮、飞溅、电弧烟尘及机械加工残存加的飞边、毛刺等。
2.2涂层厚度要求
2.2.1除锈后的金属表面与涂底漆的间隔时间不得大于6小时,酸洗处理表面经钝化与后与第一次涂底漆时间不少于48小时。
但无论间隔时间多少,涂漆前表面不得有锈蚀或污染。
2.2.2铆接件相互接触的表面,在联接前必须涂厚度30~40防锈漆。
由于加工或焊接损坏的底漆,要重新涂装。
2.2.3不封闭的箱形结构内表面,在组焊前必须涂厚度60~80防锈漆。
封闭箱形结构表面不涂漆。
2.2.4溜槽、漏斗、裙板内表面、安全罩内表面,封闭箱且在运输过程中是敞开的内表面等必须涂厚度60~80防锈漆。
2.3一般情况下,不进行涂装的产品部位及部件
2.3.1与混凝土接触或埋入其中的部件,设备安装的加工面、阀和钢管的内表面、法兰内表面、不锈钢衬板、钢轨及钢丝绳、镀锌板及镀锌件、镀铬件、衬套等及图样注明不涂漆的件,不需进行涂装。
2.3.2铸件及焊接件表面局部凹陷,需用配套性良好的常温固化型腻子进行填补。
2.3.3木制品表面不涂防锈漆,按要求涂清漆或色漆即可。
2.3.4涂装时必须严格遵守各种涂料对温度、湿度、重涂间隔时间、调配方法、注意事项等各项规定。
2.4成套设备面漆颜色必须一致。
2.5设备最后一层面漆应在总装试车合格后进行。
2.6损坏的漆膜应进行修补,修补的面应进行表面处理,与周围涂层的搭接宽度不少于50mm(或破坏面积较小时,修补的面积应比被破坏的面积大一倍以上)。
修补应按规定层次进行,补涂部位的颜色、涂层厚度与周围涂层厚度一致。
2.7喷涂前对产品不涂装的部位进行遮盖,以防漆雾污染。
2.8涂料的质量必须符合化工部或有关标准的规定。
3检查项目及方法
3.1表面处理质量按本附件附录A的彩色照片对照检验.
3.2涂层的检验
3.2.1外观检查:
底漆、中间层漆涂层不允许有针孔、气泡、裂纹、脱落、流挂、漏涂等缺陷。
检查方法可用肉眼或五倍放大镜观察。
而漆涂层允许存在少量的气泡和流挂,但主要大面上不允许出现上述缺陷。
检查方法同前。
3.2.2涂层厚度的检查,每涂完一层漆,待涂层彻底干透后,测量一次厚度,全部涂层涂装完毕后再测总厚度。
检查方法是:
用电磁式膜厚计测量。
每10m2测一个点,管路等细长体每3~4m长测一个点,三点平均值应超过标准总涂层厚度的90%;
但三点平均的最小值不应小于标准涂层总厚度的70%。
测得的涂层厚度分配标准误差(三点平均值)应小于标准涂层总厚度的20%。
3.2.3涂层附着力的检查:
准备六块规格为200mm×
200mm的试片。
试片经表面处理后,与产品涂装方式一样涂上一层,待彻底干透后,用锋利的专用刀片或保险刀片,在试片表面划一个夹角为60℃的叉,刀痕要划至钢板。
然后贴在专用胶带,使胶带贴紧漆膜,接着用手迅速将胶带扯起,如刀痕两边涂层被贴下的总宽度最大不超过2mm即为合格。
4其他
4.1供图制造设备中的操作台及钢梯、栏杆等部件,设备制造厂家涂装;
其要求如下:
·
涂料品种选用氯磺化聚烯涂料。
涂层结构采用铁红底漆两遍;
棕褐色中间漆一遍,面漆二遍。
栏杆、扶手为黄、黑相间的安全色环。
炼钢项目组
附录A:
涂装前钢材表面除锈质量等级
A.1钢材表面的原始锈蚀程度分等见表A1
表A1
锈蚀等级
说明
A
钢材表面几乎没有锈蚀,完全被氧化皮所覆盖。
B
钢材表面已开始生锈蚀,并且氧化皮已开始脱落。
C
钢材表面已因生锈蚀面剥离、或可被刮除,但几乎没有用肉眼能见的蚀孔。
D
钢材表面已因生锈蚀面剥离、并且有相当多的用肉眼能见的蚀孔。
A.2钢材表面的除锈方法与其质量等级。
A.2.1手工除锈
手工除锈(包括使用铲刀、钢丝刷,机械钢丝刷,砂轮等工具进行除锈)。
按其除锈质量要求分为St2与St3两级。
St2:
采用铲刀刮,用钢丝刷、机械钢丝刷擦刷和用砂打磨等方法,彻底地除去疏松的氧化皮、锈和污物。
最后用吸尘器、清洁干燥的压缩空气或干净的刷子清理表面。
清理后的表面应呈现淡淡的金属光泽。
其外观应相当于标示St2的照片。
St3:
采用的方法和表面除锈要求与St2相当,但更为彻底,清理后的表面应具有明显的金属光泽,其外观应相当于标示St3的照片。
A.2.2表面喷射除锈
表面经喷射各种磨料除锈,按其除锈质量要求分为Sa1、Sa2、Sa21/2、Sa3等四级。
Sa1:
轻度喷射除锈。
应除去疏松的氧化皮、锈及污物。
其外观应相当于标示Sa1的照片。
Sa2:
彻底地喷射除锈。
应除去几乎所有的氧化皮、锈及污物。
最后,用吸尘器、清洁干燥的压缩空气或干净的刷子清理表面,这时,该表面应稍呈灰色,并且外观应相当于标示Sa2的照片。
Sa21/2:
非常彻底地喷射除锈。
氧化皮、锈及污物应清除到仅有轻微的点状或条纹状痕迹的程度。
最后,表面用吸尘器、清洁干燥的压缩空气或干净的刷子清理。
其外观应相当于标示Sa21/2的照片。
Sa3:
喷射除锈到出白。
应完全除去氧化皮、锈及污物。
该表面应呈现均匀一致的金属色泽。
其外观要相当于标示Sa3的照片。
Bc:
彻底清除氧化铁皮和铁锈及残留的复盖层(相当于Sa3)。
A.3标记与评定
A.3.1标记
例如:
原始锈蚀程度是B等的钢材表面,经手工除锈到2级,则该表面的除锈质量等级标记为BSt2:
原始锈蚀程度是B等的钢材表面,经喷射除锈到21/2级,则该表面的除锈质量等级标记为BSa21/2。
A.3.2评定
a.评定原始锈蚀程度与除锈质量等级按A2.1、A2.2条规定。
附录B:
表面预处理规范
B.1金属表面除锈质量等级
SSPC表面预处理规范对金属表面订有十个除锈质量等级,这些等级的符号、名称和简明要求列示如下:
SSPC-SP.1溶剂清洗、用溶剂、蒸汽、碱或乳剂清洗,除去油脂、灰尘、泥土、盐和污物。
SSPC-SP.2手工工具除锈:
用手工铲刀铲、刮、用砂布打磨和用钢丝刷子刷,除去松动的氧化皮,疏松的锈和涂层,达到规定的要求。
SSPC-SP.3动力工具除锈:
用动力工具铲、刮,用动力钢丝刷子刷和用砂轮磨,除去松动的氧化皮、疏松的锈和涂层,达到规定的要求。
SSPC-SP.4新钢材火焰除锈:
先用火焰喷射,而后用钢丝刷子刷,脱去水分并除去锈、松动的氧化皮以及某些牢固的氧化皮。
SSPC-SP.5出白级喷射除锈:
通过抛射或喷射(干的或湿的)石英砂、棱角砂或者铁丸,除去所有可见的锈、氧化皮、涂层和污物(用于应付出高昴的除锈费用的,有严重腐蚀性的环境中)。
SSPC-SP.10接近出白级喷射除锈:
喷射除锈到接近出白,每单位表面积上,至少有95%的面积无任何可见的残留物(用于高湿、化学气氛、海洋或其他腐蚀性环境中)。
SSPC-SP.6工业级喷射除锈:
喷射除锈到每单位表面积上至少有2/3的面积无任何可见的残留物(用于相当恶劣的暴露条件下)。
SSPC-SP.7清扫级喷射除锈:
除了牢固附着的氧化皮、锈和涂层的残留物以外,喷射除去所有其他的污物,露出大量的、均匀散布的基底金属的斑点。
SSPC-SP.8酸洗:
通过酸洗、复式酸洗或电解酸洗,完全除去锈和氧化皮。
也可以使表面通过酸液。
SSPC-SP.9风蚀继以喷射除锈:
风蚀,以除去所有的或部分的氧化皮。
继之以喷射除锈达到上述标准的某一等级。
B.2喷射除锈的方法
SSPC规范列举了用以达到相应等级的,可供选择的喷射除锈方法。
这些方法主要有:
a.干喷砂
用压缩空气、通过喷嘴喷射,采用干燥的石英砂作磨料,磨料最大粒度不大于美国筛网系列的16号筛眼。
b.湿喷砂或水蒸汽喷砂
用压缩空气、通过喷嘴喷射,采用掺有水的石英砂作磨料,磨料最大粒度不大于美国筛网系列的16号筛眼。
c.喷棱角砂
用压缩空气、通过喷嘴喷射,采用除了石英砂之外的,由铸铁、锻铁、钢或合成材料制造的,捣碎的棱角砂(grit)作磨料,磨料最大粒度不大于美国筛网系列的16号筛眼。
该规范允许使用的工业级的金属棱角砂是SAENOG-25磨料。
d.喷丸
用压缩空气、通过喷嘴喷射,采用铸铁的、锻铁的钢的或合成材料的丸粒作磨料,其最大粒度不大于美国筛网系列的16号筛眼。
该规范允许使用的工业等级是SAENOS-330。
e.封闭的循环式的喷射
采用压缩空气喷射、真空回收的方式。
所用喷射工质可以是上述任何一种类型的磨料。
f.抛丸棱角砂
用离心式叶轮抛射,采用铸铁的、锻铁、钢或合成材料制造的,捣碎了棱角砂作磨料,磨料最大粒度不大于美国筛网系列的16号筛眼。
该规范允许使用的工业等级的SAZNOG-25。
g.抛丸
用离心式叶轮抛射,采用铸铁的、锻铁的、钢的或合同材料的丸粒作磨料,其最大粒度不大于美国筛网系列的16号筛眼。
这个规范允许使用的工业等级是SAENOS-330。
B.3施工注意事项
为进一步保证除锈和涂装的质量,SSPC规范对施工过程中应注意的有关事项作了详细的说明。
a.必要的保护措施
喷射除锈所使用的压缩空气应当不含冷凝水或油,必须设置适当的分离器和凝汽器。
喷射除锈作业对已部分或全部完了工作应当没有任何的损害。
对于在喷射除锈之后,涂装之前会弄湿的表面,或者在涂装之前,周围的条件会使表面产生明显的锈蚀时,干喷砂除锈作业应当停止。
如果喷射除锈之后,表面又重新生锈,则在涂装之前,该表面应重新进行喷射除锈。
必须检查已喷射除锈过的表面是否有油迹或污迹,如果有,则应按SSPC-SP1,“溶剂清洗”一节所提出的要求,将其清除掉。
在温度低于周围空气露点的表面上,就会产生凝露。
因此建议,当钢材表面温度低于露点以上3℃时,干燥砂除锈就不应进行。
b.喷射除锈和涂装之间的时间间隔
在表面可能发生化学污染的地方,钢材在喷射除锈之后应尽快涂装。
喷射除锈过的表面在生锈之前必须涂上底漆,否则就失去喷射除锈的意义。
刚刚喷射除锈过的裸露金属,在高湿条件下,或者被弄湿了时,或者处于腐蚀性气氛之中,会很快生锈。
在正常的、适中的大气条件下,最好的喷射除锈以后24小时之内就涂上底漆或进行化学处理。
不管间隔时间多少,涂装之前钢材表面无论如何也不容许锈蚀。
喷射除锈和涂底漆之间允许的时间间隔随环境不同会有很大的差别(从几分钟到几周)。
c.喷射除锈以后的清理作业
如果是干喷过的表面,为了清除掉从该表面上喷落下来的锈灰,同时也为了从低凹的地方或者从角落里清除掉磨料,必须用毛发、猪鬃或纤维材料制成的、干净的刷子清扫,用压缩空气(已除去其中有害的油和水)吹净,或用叭尘器吸净。
如果是湿喷过的表面,则必须用加有足够的缓蚀剂的淡水冲洗,或者先用淡水冲洗,继之以蚀化处理。
必要的时候,还要用刷子进行补充处理,以消除去任何残渣。
d.表面粗糙度
表面粗糙度在一定程度上是随喷射磨料颗粒的角度和速度,表面的硬度,循环使用的磨料混合比(丸粒和棱角砂),以及喷射除锈的彻底程度不同而变化的。
在表面上形成的波纹的高度必须有所限制的,其最大高度应不会对涂膜有所伤害。
磨料的最大允许粒度取决于所允许表面粗糙度,而表面粗糙度的大小又取决于将要涂装的涂层的厚度。
为使表面能得到理想的保护,在波纹的波峰之上,干燥涂膜的厚度应等于通常我们所了解的光滑表面上需要的厚度。
如果不能用小粒度的磨料喷射,以产生合乎要求的表面粗糙度的话,那么就应该增加干燥涂膜的厚度,以使在波峰之上还有足够厚度的涂料。