汽车研发整车座椅制作设计开发方法与流程Word文件下载.docx
《汽车研发整车座椅制作设计开发方法与流程Word文件下载.docx》由会员分享,可在线阅读,更多相关《汽车研发整车座椅制作设计开发方法与流程Word文件下载.docx(25页珍藏版)》请在冰豆网上搜索。
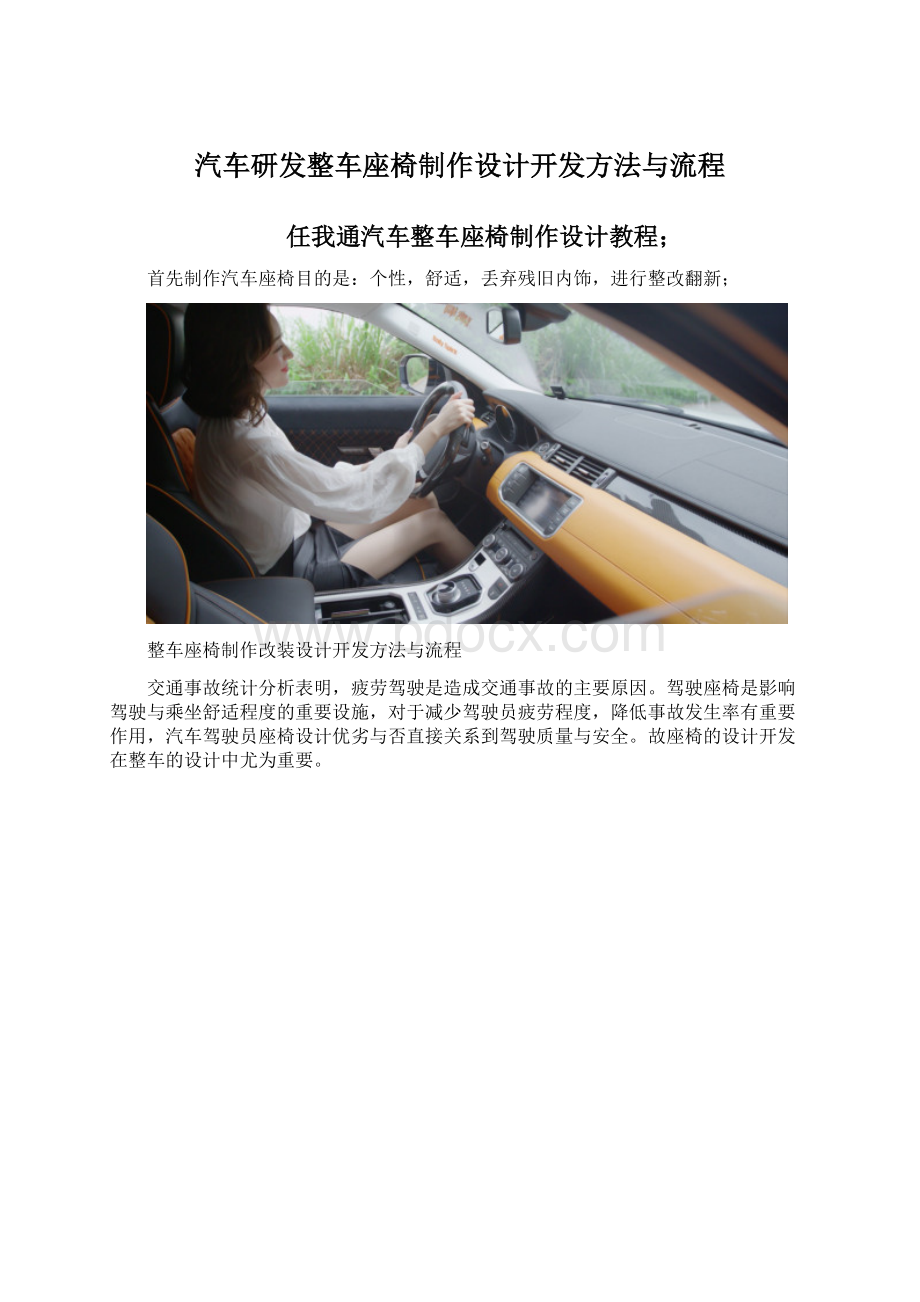
1外观要求
1)外形尺寸要点
A.座面
座椅座面尺寸要求
项目
参数
横向高度差
H≥25mm
座面前沿拱起高度
H1≥40mm
拱起半径
40mm≤R1≤120mm
座椅前沿纵向起供时
前部倾角
α1=4°
-5°
后部倾角
α2=10°
-15°
纵向高度差
H2≤40mm
B.腰靠
腰靠角度调节量应≥20°
;
腰靠若装有软垫,则其沿座深方向垂直剖面内的曲率半径应>1400mm。
C.头枕
驾驶员头部到顶棚间隙>50mm,乘客头部到顶棚间隙>30mm;
头枕中心线与靠背中心线应保持0°
-20°
夹角。
D.扶手
座椅扶手尺寸要求
扶手上沿与座面垂直距离
230±
20mm
双扶手内沿水平距离
<500mm
扶手长度
200-280mm
扶手前沿与座面前沿水平距离
90-170mm
扶手倾角
固定式
0°
可调式
E.靠背
靠背的基准角度与水平面成105°
-115°
前排座椅靠背高度≥800mm;
后排高度≥700mm。
2)座椅外观
A.座椅总成蒙皮装配后,造型应挺括、饱满,不允许有破损、污损、皱折等疵病;
B.座椅总成蒙皮整体缝合应牢固。
缝制针距明线5-8针/30mm,且应均匀、清晰、平直,无漏针、脱线、跳沙等现象。
座椅总成坐垫缝制线条与靠背缝制线条应对齐,相差不大于±
5mm;
每条线缝的两端应回针,不应有大于10mm的多余线头;
C.座椅总成各焊接、铆接部位应牢固可靠,不应有松动现象;
总成不应有焊接错位、气孔、虚焊等缺陷,外表面应平整、光洁、无油污、无毛刺,运动部分应涂润滑油;
D.座椅头枕应无局部凸起、尖棱等触感;
E.座椅总成的金属件应进行防锈处理,表面涂层均匀,无气泡、划伤、堆积和流痕等现象;
所有金属件表面不允许有锈蚀及漆膜脱落现象,符合QC/T484-1999《汽车油漆涂层》标准要求,需耐盐雾试验48小时以上;
F.装饰件之间的间隙均匀,泡沫、骨架、C型钉无外露;
G.装饰塑料件色泽均匀一致,无凹凸、飞边;
塑料装饰件料厚要求≥2.5mm。
2材料要求
1)泡沫指标要求
泡面指标要求
座椅泡沫指标
座椅
靠背
头枕
认可标准
密度Kg/m³
50-55
45-50
GB/T6343-1995
回弹率%
≥50
GB/T6670-2008
拉伸强度KPa
≥100
GB/T6344-2008
断裂伸长率%
≥90
≥80
撕裂强度N/m
≥2.2
≥2.0
GB/T10808-2006
25%压缩强度N/314m²
200-240
160-200
GB/T10807-2006
50%压缩永久变形%
≥7
GB/T6669-2008
燃烧性能
≤100L/min
GB8410
2)面套要求
A.座椅面料(单层)物理机械性能指标
座椅面料(单程)物理机械性能指标
序号
试验项目
规格值
试验方法
1
断裂强度(N/50mm)
径向/维向
以选定面料实测为准
GB/T3923.1-1997
(复合体)
2
断裂伸长率
3
引裂强度(N/50mm)
GB/T3917.3-2009
4
定负荷伸长率(%)
见1.4.6.1
5
残留变形率(%)
6
燃烧特性(mm/min)
常燃/老化
<100
7
摩擦色牢度(级)
干摩
≥4
GB/T3920-2008
8
湿摩
耐挫韧性(级)
由面料厂到主机厂认可测试机构检测
9
耐磨韧性(级)
10
耐高温(100℃*4h后)
外观无明显变化
高低温试验箱
11
耐光色牢度(级)
≥3
有面料厂自行检查,主机厂认可
12
污渍粘着性(级)
13
污渍去除性(级)
14
同批次色差(级)
△E≤1
15
不同批次色差(级)
GB250
B.座椅面料(复合)物理机械性能要求
座椅面料(复合)物理机械性能要求
规格/性能要求
检验方法/器具
有效幅宽
>1500mm
刚直尺
阻燃性
>100mm/min
纬斜度
在1500mm幅宽内<20mm
剥离强度
>5N/50mm
按逢强度
>400N
耐高温性
100℃*4h后无起层/起泡现象
3)座椅面料(复合)物理机械性能要求
A.
各塑料件应无变形、破损、飞边、毛刺、划痕及污物,色泽一致,皮纹清晰,并符合色标、皮纹样本,不应有异样斑点,不能变色,表面质量应一致,不能有折皱,与座椅总成风格要相匹配。
B.
各塑料件装配要牢固可靠,不能有松动现象,更不能有异响。
C.
各塑料件经过常规耐热性能、耐寒性能、冷热交变性后,产品的形状、外观应满足下表的要求:
塑料件试验满足要求
实验项目
评价项目
耐热性
(90℃/16h)
耐寒性
(-40℃/16h)
冷热交变性能
(90/3h→室温/1h→-40/3h→室温1/h)
循环三次
形状
尺寸变化<0.59%
外观
不允许有明显的气孔/熔接痕/银纹/龟裂/变形/光泽不均等缺陷存在
D.
各塑料件燃烧特性应符合GB8410的有关规定。
E.
各塑料件物理性能应满足下表要求:
塑料件物理性能要求
材料
指标
改性PP
拉伸强度(MPa)
≥18
玩去弹性模量(MPa)
≥1800
弯曲强度(MPa)
≥20
洛氏硬度(HRR)
65±
热变形温度(0.4MPA)(℃)
≥110
密度(g/cm³
)
1.07±
0.02
悬臂梁冲击强度(23℃)KJ/m²
≥15
F.
各塑料件产品尺寸公差应满足GB14486《工程塑料模塑塑料件尺寸公差》的要求。
G.
对于调角器、限位器、座椅锁、解锁机构等座椅零部件装饰,塑料件装饰参照标杆车。
4)金属骨架结构
金属骨架应符合按规定程序批准的图样和技术文件。
金属骨架的焊接应符合GB/T5943《工程机械焊接件通用技术条件》的规定,焊接方式采用点焊、弧焊、气体保护焊。
零件表面不得有焊渣、飞刺。
金属骨架进行除锈、防锈处理,表面电泳涂漆,漆层应符合QC/T484-1999《汽车油漆涂层》的规定,需耐盐雾试验48小时以上。
金属骨架与其他零部件装配为总成后,强度应符合GB15083汽车座椅系统强度要求及试验方法》及《TBD-681201汽车座椅疲劳试验方法及评价标准》的规定。
3机械结构的组成
1)座椅滑轨机构
A.滑轨参数
座椅滑轨参数
参数名称
备注
有效行程
200左右(空间校核)
前后方向
步距
10mm或者12mm(限位结构齿距)
解锁力
15-55N
滑动助力
30-225N(承载75Kg)
锁止力
滑轨≥17000N
间隙
左右方向
<0.5mm
加100N负荷
上下方向
B.滑轨技术要求
解锁手柄操作力15-55N,解锁调节灵活、无异响;
总成滑动阻力(在承受75kg向下载荷时)为30-225N,且滑动过程中无异响、全行程无涩点、滑动畅,同步锁止、同步解锁;
耐久性能:
在座椅上加载80KG载荷,前后往复滑动滑轨15000次以上,不允许有滚柱、滚珠脱落,零件变形、机构失效等缺陷;
其余要求按照QCT805-2008《乘用车座椅用滑轨技术条件》执行。
2)座椅调角器机构
座椅调角器机构要求
座椅靠背设计基准位置
105°
调角器调整杆操作力矩
<
1.0-3.5N.M
单边锁止强度
≥12500N
≤30N
后拍调节范围
-110°
1/沿靠背顶端垂直于靠背基准线方向施加50±
5N的力,背靠晃动间隙≤10mm;
2/耐久性能:
开、关锁≥15000次试验后个零件不应有变形、破损现象,且能正常工作;
3)座椅锁机构
A.
锁止强度≥25000N,座椅在完成GB14167试验后,座椅锁的锁止功能不损破、失效。
解锁力≤50N
4其它要求
1)舒适性
座椅泡沫造型应符合人机工程学的要求,并给出A面的分析报告。
人体乘坐时,最大布置人体与骨架(硬物)间距≥30mm。
选用高回弹的优质冷发泡沫,选用优质复合面料,面料与泡沫采用火焰复合方式,提高面料的舒适度和环保性。
前排座椅的舒适性设计参考应当满足人机工程相关法规和行业标准(根据设计可作相应调整);
座椅各零部件的外露部分不得有易于伤人的尖角锐边,各部结构不得存在可能造成的挤压、剪钳伤人部分。
工作座椅的结构材料和装饰材料应耐用、阻燃、无毒。
坐垫、腰靠、扶手的覆盖层应使用柔软、防滑、透气性好、吸汗的不导电材料制造。
若坐垫直接固定在底板上(通常为后排座椅坐垫),一般泡沫上表面到底板的距离不小于50㎜;
H.
在震动和乘员进行座椅特性操作的过程中,不得有摩擦声音和尖刻声音等异响。
2)其它重要技术要求(特别说明事项)
后排座椅中间位置必须满足安装三点式安全带的新法规要求和骨架强度要求。
B.座椅骨架模态的要求:
座椅TRIM状态(即附属件的质量加在骨架承载点上)主要模态定在18Hz以上,但要避开发动机怠速频率22.6Hz~25Hz
(680~750转/分)。
座椅模态要求见下表:
座椅骨架模态的要求
阶次
振型
频率
前后摆动
>
18&
避开怠速2Hz
左右摆动
C.后排座椅对安装ISO-FIX固定装置,其强度和有效固定点及布置区域满足最新法规和GB27887-2011《机动车儿童乘员用约束系统》等相应ISO-FIX法规要求。
三、设计参数依据案例
设计参数案例
尺寸
靠背与坐垫之间的夹角
坐垫与水平面夹角
10°
坐垫深度
300mm
坐垫高度
350mm
靠背高度
490mm
坐垫宽度
860mm
靠背宽度
790mm
头枕高度
650mm
四、设计开发流程
1项目预研
2Benchmark座椅分析
Benchmark阶段的分析与研究工作是为了标——为后续的设计工作设计一个基准、模仿标杆车的基本构造、规避标杆车的专利,完成设计车的设计制作工作。
在此阶段,需完成如下的工作:
1)确定对Benchmark车进行分析和研究的方案设计阶段;
2)完成Benchmark车的测量工作,包括整车外廓尺寸测量、基本性能测量、总布置测量、外观品质测量、电器测量等等;
3)拆车扫描阶段。
在本阶段,根据已经确定的研究方案,完成对标杆车的拆解工作,边拆解边记录标杆车的基本数据,并对标杆车的部件进行扫描。
本阶段的工作量相当的大,需要一套相对完善的拆车流程以与支持;
4)数据整理阶段。
本阶段,将上述的大量数据进行分类整理,以便于后续的详细设计工作使用;
5)针对座椅,主要对座椅的配置、在整车中的布置及边界进行测量分析。
接着对Benchemark座椅进行拆解及相关分析,包括座椅的调节力、功能及相关结构、材料等信息进行收集整理。
3座椅配置表及设计构想
根据市场调研及销售确定的预售价格及整车配置、市场要求,对座椅相关配置进行细化整理,完成初版的座椅配置表。
然后,根据确定的配置表设定设计参数及法规、性能要求明细,制作座椅的设计构想书。
根据以上信息,完成座椅技术招标方案,确定座椅供应商。
4座椅造型效果图制作
将确定的座椅配置及设计构想输入给造型部门,进行整车及座椅的造型草图设计,进而完成座椅的造型效果图。
5座椅造型可行性分析
设计针对座椅的造型效果图进行分析,其中包括法规及配置相关符合性分析、造型的工艺可行性分析等方面。
一旦在效果图分析中发现重大工艺问题或者法规、配置符合性问题,则需要将问题反馈输入给造型部门,重新制作并交付造型效果图。
6座椅造型冻结
造型部门根据工程部门针对造型效果图的问题输入及反馈,修改并重新提交效果图以供分析评审,直至最终确认效果图并冻结。
7A面数据制作
造型根据确认冻结的效果图制作座椅A面数据并提交工程部门。
工程部门对座椅A面数据进行检查,包括和造型效果图的匹配,以及座椅在整车总布置进行的人机工程、法规符合性、舒适性等方面。
然后完成A面数据冻结并下发座椅供应商。
8座椅骨架及附件设计
座椅供应商根据输入的A面数据进行匹配的骨架及相关附件设计(包括座椅调节机构及装饰件、面套等)。
其中骨架设计的相关参数设定需要输入给整车总布置进行布置分析,并最终确定座椅的相关设计参数(包括调节行程、头枕调节高度等)。
9手工件制作及设计验证
完成座椅骨架及附件设计后,座椅供应商需对原始设计进行验证。
首先按照设计数据制作手工样件,然后对手工样件进行DV验证(设计验证)。
在此过程中发现问题即对数据进行相应修改,并再次制作样件进行试验验证直至完成DV试验验证。
另外,目前有限元分析(FEA)在汽车领域应用比较广泛,在条件允许的情况下,可针对设计验证完成的数据状态,按照相关市场及国家要求的标准如GB4167-2006、GB15083-2006、ECER14及ECER17等法规所定义的要求,对座椅进行FEA分析,并针对FEA分析结果对座椅进行有针对性的改进。
10数据冻结及工装开模
完成DV验证后,即可对当前数据状态进行冻结并下发开指令,开始进行工装模具开发。
11工装件制作及实验验证
制作工装样件,进行工装件试装车匹配及相关PV实验验证。
其中PV验证试验要根据OEM(代工生产)与座椅供应商签订的PVP进行。
与此同时,座供应商需要依据销售地区的法规要求完成座椅相关强检及认证(如国内的强检及36C认证)。
若工装件试验验证未通过相关地区的强检及认证,则要针对情况进行数据及样件分析改进直至完成以上实验验证为止。
12OTS认可及PPAP准备
完成工装件试装车、PV实验及相关强检认证后,即可对当前的数据及工装样件状态进行确认并完成产品的工装件认可(OTS认可)。
座椅供应商在完成OTS认可后,需要对工装件生产进行生产规划及准备,其中包括设备投入、生产培训、物料管理等。
然后开始进行小批量生产试制。
13小批量试装车
座椅供应商进行小批量试生产,OEM按照批量生产程序启动小批量试装车,对整车批量生产装配进行试生产验证。
14PPAP批准
PPAP是APQP在试生产阶段的一个输出:
在第四阶段(试生产阶段)
要向顾客提交PPAP资料(APQP有策划阶段、设计阶段,工艺开发阶段、试生产阶段、量产阶段)。
完成小批量试装车并解决相关装车问题后,即可有座椅供应商提交PPAP资料并由OEM相关工程师对座椅及生产进行PPAP审核并最终批准完成。
15产品SOP(StartofProduction)
各项验证完成,进入投放市场的小批量生产。
五、结语
在汽车设计过程中,座椅的确定至关重要。
它不仅影响到整车设计和乘坐体验,还和安全紧密相关。
特殊设计的汽车座椅,可以把臀部、大腿根部的压力分散到膝盖,腰部的压力也能由背部上方以及肩部分担。
更重要的是,座椅还要保证行车时的人员安全。
座椅企业纷纷推出了具有辅助驾驶功能的汽车座椅,比如在事故发生前出现车道偏移提醒,座椅会自动调节到最安全的位置;
追尾时,座椅会出现电子主动式头枕等。
伴随汽车智能化发展,座椅可以自动感知乘员体重和体型、识别身体部位、自动调节气囊的形状、完全贴合乘员的身体轮廓、减小脊柱的受力,甚至辅助驾驶。