精细化调试质量控制考核办法161108Word文档下载推荐.docx
《精细化调试质量控制考核办法161108Word文档下载推荐.docx》由会员分享,可在线阅读,更多相关《精细化调试质量控制考核办法161108Word文档下载推荐.docx(19页珍藏版)》请在冰豆网上搜索。
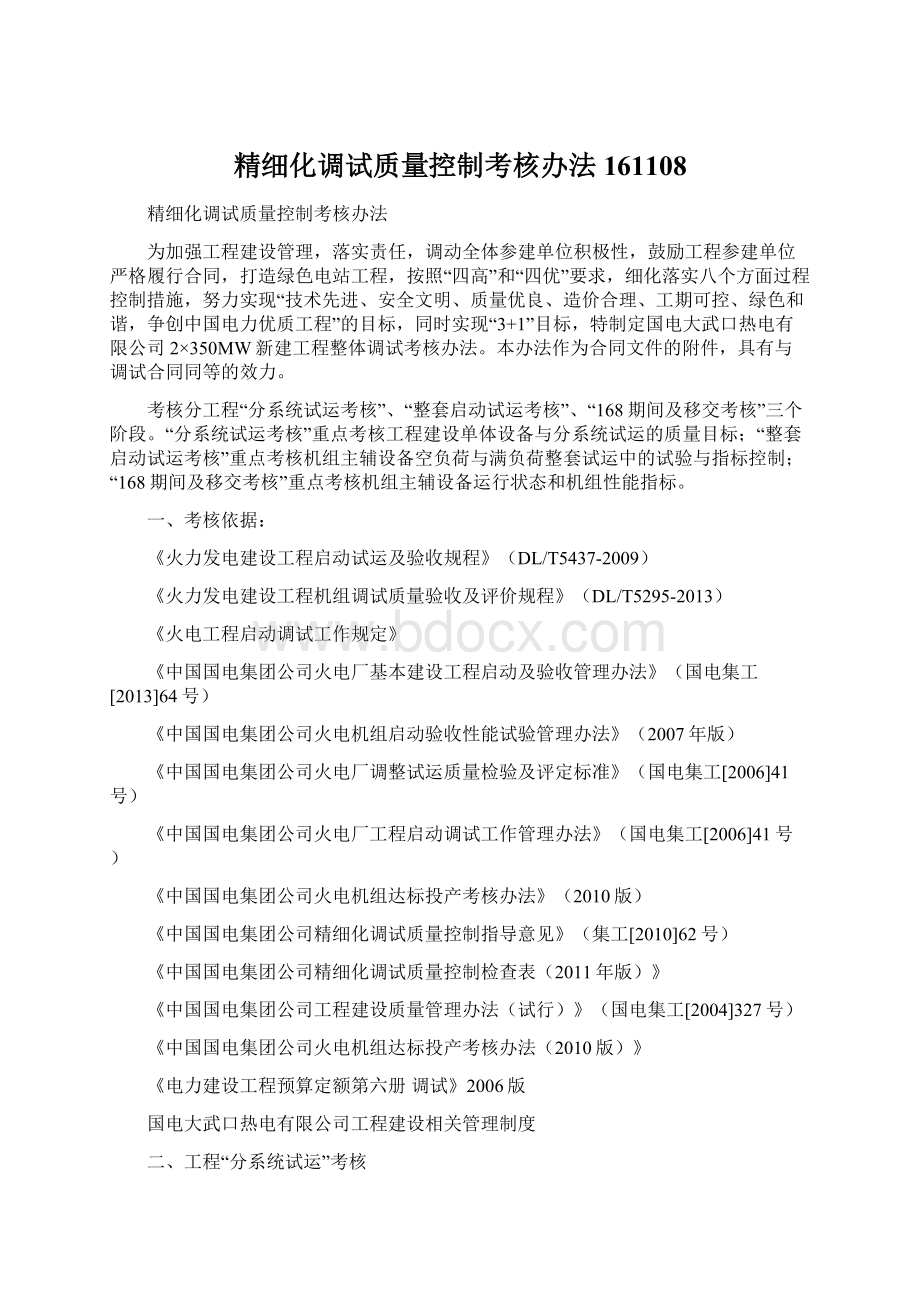
热交换器与滤水器无泄漏、投入切除正常。
(2)辅助蒸汽系统(含工业用汽及减温减压装置等):
系统管道吹扫合格且法兰管道无泄漏;
系统阀门验收试验符合标准、安全门动作正常;
工业用汽系统及减温减压装置无泄漏、投入切除正常。
(3)凝结水及补水系统:
凝结水泵轴承振动、轴承温度、电流、进口滤网差压、出口压力、电机线圈温升符合规定;
法兰无泄漏盘根温度正常;
系统管道冲洗合格、无泄漏;
系统阀门验收试验符合标准。
(4)除氧器及给水系统:
调整试运质量符合检验及评定标准,联锁保护及信号试验齐全动作准确;
给水泵轴承振动、轴承温度、进口滤网差压、出口压力、油温油压、电机线圈温升符合规定;
系统管道冲洗合格无杂物、严密无泄漏;
系统阀门验收试验符合标准;
除氧器无泄漏、安全门动作正常。
(5)真空系统:
真空泵轴承振动、轴承温度、电流符合规定;
换热器无泄漏、投入切除正常;
气体分离箱水位自动调节正常;
凝汽器真空系统灌水试验满足规范、系统抽真空达到设计要求。
(6)抽汽回热系统、加热器及疏水系统:
系统管道冲洗合格、正常和危急疏水无异常;
系统与换热器无泄漏、投入切除正常;
(7)轴封供汽、回汽系统(含汽缸法兰螺栓加热系统):
系统管道吹扫合格无泄漏、减温减压装置投入切除正常;
风机轴承振动、轴承温度、电流、电机线圈温升符合规定;
(8)发电机内冷水系统:
水泵轴承振动、轴承温度、电流、出口压力符合规定;
水箱水位自动调节正常;
定子冷却水流量、温度、压力试验满足规范达到设计要求。
(9)发电机密封油系统:
油泵轴承振动、轴承温度、电流、出口压力符合规定;
油箱油位自动调节正常;
油/氢差压调节试验满足规范达到设计要求。
(10)发电机氢冷系统(含气密试验):
氢气运行压力、纯度、湿度、CO2纯度、漏氢量与漏氢率符合规定;
系统管道吹扫打压合格、严密无泄漏;
(11)调节保安系统(含高、中压主汽门、调速汽门严密性试验及关闭时间、开关行程测试,保安系统静态试验,EH油系统管道冲洗及调试,热工信号及联锁保护检查、试验,配合热工对电调系统进行静态调试等工作):
油泵轴承振动、轴承温度、电流、油温油压符合规定;
系统管道冲洗合格严密无泄漏;
系统阀门验收试验符合标准、汽门关闭时间和开启顺序与重叠度符合设计要求、调节无卡涩无晃动。
(12)顶轴油及盘车系统:
调试调整试运质量符合检验及评定标准,联锁保护及信号试验齐全动作准确;
油泵轴承振动、轴承温度、电流、油压符合规定;
系统阀门验收试验符合标准、盘车运行正常。
(13)旁路及疏水系统:
系统管道吹扫合格严密无泄漏、支吊架牢固正确无异常;
系统阀门验收试验符合标准、旁路阀开关时间符合设计要求;
旁路阀调节特性符合设计要求、投入切除正常;
制冷压缩机试验满足规范达到设计要求。
(14)润滑油系统及净化装置:
油泵和风机轴承振动、轴承温度、电流、油压符合规定;
系统阀门验收试验符合标准、油净化效果达到设计要求;
油温自动调节正常满足规范;
事故排油系统随时投运。
(15)汽动给水泵小汽轮机系统及其润滑油系统、盘车装置:
油泵和风机轴承振动、轴承温度、电流、油温油压符合规定;
系统阀门验收试验符合标准、汽门关闭时间符合设计要求、无卡涩无晃动。
(16)循环水系统:
水泵轴承振动、轴承温度、电流、出口压力、电机线圈温升符合规定;
系统阀门验收试验符合标准、液控蝶阀装置调节灵活动作正常;
胶球系统加球及收球装置操作灵活、收球率达到要求。
(17)热网首站:
水泵与调速装置轴承振动、轴承温度、电流符合规定;
系统管道冲洗合格无杂物、严密无泄漏、正常和危急疏水无异常;
换热器无泄漏、投入切除正常。
(18)空压机及系统:
转动设备轴承振动、轴承温度、电流、电机线圈温升符合规定;
系统管道吹扫合格、严密无泄漏;
空气压力、干燥度与含油量达到设计要求。
(19)暖通系统:
水泵和风机轴承振动、轴承温度、电流符合规定;
系统管道冲洗合格无杂物严密无泄漏、正常和危急疏水无异常;
2、锅炉专业分系统调试质量目标
(1)空气预热器及其系统:
润滑油油压、油温符合设计要求;
转动机械转速符合设计要求,转动机构不卡、灵活;
密封系统投运正常;
空预器漏风率小于4%。
(2)风烟系统(含三大风机):
轴瓦温度符合设计要求;
轴承振动符合质量标准要求;
轴瓦温度保护、轴承振动保护、喘振保护投入、整定正确;
联锁保护、报警全部投入;
隔离风门开、关位置正确,动作灵活;
调节风门开度指示正确,动作灵活;
液压系统油压正常,动作灵活;
润滑油系统油压、油温正常,无泄漏;
风量测量装置已标定,指示正确;
高压电动机运行符合试运要求;
噪声符合设计要求;
冷却水系统符合设计要求。
(3)暖风器及其系统:
进口蒸汽压力符合设计要求;
设计风量下的加热能力符合设计要求;
额定风量下的空气侧阻力符合设计要求;
疏水系统畅通,运行正常;
阀门、管道开关灵活,严密不漏,保温完整。
(4)吹灰器及其系统:
减压装置符合设计要求;
调节阀调节性能良好,动作灵活,开度指示准确;
法兰、阀门无堵塞,无泄漏,操作方便;
管道系统膨胀自如、无卡涩;
疏水坡度准确,疏水畅通;
吹灰器动作灵活,伸缩自如,限位开关动作正常;
旋转方向符合设计要求;
冷态程序试验符合设计要求;
系统汽压稳定,且基本符合设计要求。
(5)制粉系统:
给料装置出力调节范围符合设计要求;
中心给料装置与给煤机的出力相匹配、协调;
自润滑系统投运正常、不漏油。
给煤机出力符合设计要求;
给煤机机械传动符合设计要求;
给煤机不漏煤;
给煤机程控系统符合设计要求;
给煤机保护系统符合设计要求;
给煤机电子称重装置计量准确,显示正确。
磨煤机电机电流符合设计要求;
磨煤机轴承温度符合设计要求;
磨煤机进出口压差符合设计要求;
磨煤机出口折向门开闭灵活;
磨煤机不漏油、不漏粉;
磨煤机出力符合设计要求;
磨煤机出口风温符合设计要求;
磨煤机控制系统投入、动作正确;
磨煤机联锁保护投入、动作正确;
磨煤机自动系统投入、动作正确;
磨煤机轴瓦振动符合质量标准要求;
磨煤机噪音符合设计要求。
(6)空气压缩机及其系统:
联锁保护全部投入、动作正确;
状态显示正确;
管道系统干净无杂物、无泄漏;
阀门灵活、无泄漏;
安全门动作灵活、整定值符合设计要求;
空气干燥度、含油量、压力符合设计要求;
空压机振动符合现行国家标准规定;
空压机电流不超过额定电流;
空气干燥净化装置符合设计要求。
(7)除灰系统:
空压机轴承振动符合质量标准要求;
空压机轴承温度符合设计要求;
空压机出口压力符合设计要求;
空压机出力符合设计要求;
空压机噪声符合设计要求;
空气干燥器投运正常;
灰仓泵上、下给料阀严密不漏,开关灵活;
阀门开关灵活,状态正确,严密不漏;
灰斗气化风加热器加热空气温度达到设计要求;
灰斗气化风机符合设计要求;
灰斗气化板符合设计要求;
灰斗料位计指示准确;
顺序控制正常投入、动作正确;
联锁保护正常投入、动作正确;
压力、压差、温度开关定值准确,动作灵敏、有效;
输灰管和伸缩节畅通、不堵、不漏、膨胀良好;
灰库气化风加热器加热空气温度达到设计要求;
灰库气化风机符合设计要求;
灰库气化板符合设计要求;
库顶除尘器除尘效率符合设计要求;
干灰散装机投运正常;
湿式搅拌机投运正常,灰水比符合设计要求。
(8)电除系统:
电源系统符合设计要求;
自动控制投入、控制灵活;
保护系统动作正确;
连锁系统投入、动作正确;
整流变电压≤额定电压;
整流变电流≤额定电流;
控制设备操作正常;
显示装置信号、报警显示正确;
高压输出网络无异常放电;
极板工作电压符合设计要求;
极板电压波动符合设计要求;
火花频率控制符合设计要求;
振打运作方式符合设计要求;
振打效果符合设计要求;
加热器温度均匀、参数正确;
灰斗阀门开启灵活。
(9)湿式静电除尘器系统:
阴极冲洗水和阳极冲洗水冲洗水泵运转正常;
阴极冲洗水和阳极冲洗水管道无泄漏。
(10)除渣系统:
干渣机出力满足运行要求,能正常稳定运行;
渣斗液压闸门动作灵活准确,关闭严密不漏;
碎渣机运转正常;
斗提机运转正常;
压力开关定值正确,动作灵敏、有效;
料位计指示准确,动作灵活;
管道固定牢靠,不振不漏。
(12)锅炉烟气余热回收系统:
除盐水出口温度符合设计要求;
烟气侧压降符合设计要求;
循环水泵、疏水泵运行正常处理符合设计要求;
热媒辅助加热及疏水系统、热媒补水系统、热媒加药系统、热媒稳压系统、热媒循环水系统,吹灰及疏水系统、水冲洗系统以及系统所需的所有阀门及部件、控制系统所需的测温、测压装置及其它控制装置、换热器的检修装置及轨道梁投运正常;
各部烟温、水温控制符合设计要求。
(13)锅炉蒸汽管路吹洗:
炉水品质符合规定;
冲管临时管道通流截面大于正式管道的截面;
消音装置已装设;
锅炉燃烧正常;
冲管临时阀开启时间≤60s;
冲管时压力参数符合设计要求;
试吹参数调整符合设计要求;
第一阶段炉膛出口烟温、排汽口处蒸汽压力、排汽口处蒸汽温度符合设计要求;
第二阶段冲管再热器入口压力符合设计要求;
每次冲管停炉冷却时间≥8h;
靶板材质铜板或铝板抛光;
靶板宽度≥25mm;
靶板长度≥临时管直径;
连续吹二次,第二次靶板斑痕点数应少于第一次;
靶板斑痕粒度≤0.2~0.5mm;
靶板斑痕数量≤5个;
锅炉水质记录齐全、正确;
冲管记录齐全、正确,并经签证合格。
(14)脱硝系统
尿素水解系统能满足SCR系统烟气脱硝的需要;
脱硝效率≥85%;
氨气逃逸率≤3ppm;
SO2/SO3转化率<1%;
反应器及催化剂内部洁净、无杂物;
催化剂固定牢固、密封良好;
氨气/空气管道安装正确、严密不漏;
阀门开关灵活、动作正确、严密不漏;
热控仪表指示准确;
声波吹灰器满足催化剂吹灰要求、顺序控制步序正确;
稀释风机符合设计要求。
3、电气专业分系统调试质量目标
(1)高压开关装置系统:
高压开关装置的分、合闸动作正确率100%,气体开关室通风符合设计要求,密封性试验符合厂家标准,分、合闸指示准确,瓷套检查清洁无闪络,内部声响无异常,辅助开关动作正确、接触良好,六氟化硫气体含水量有电弧分解气室不高于150ppm,无电弧分解气室不高于250ppm,套管不高于350ppm。
(2)高压厂用电开关系统:
开关保护动作率100%,电压互感器无异常,所有表计指示灵活、准确,手车进出灵活、可靠,无卡涩,二次连接接触良好,分、合闸标识明显正确,电动机满足负荷要求,事故照明投入可靠。
(3)柴油发电机组系统:
柴油发电机组供油系统供油正常,机组试运无振动,无异常,绝缘电阻符合设计要求,控制屏电气测量仪表工作正常,保护装置投入率100%,保护装置动作正确,自启动时间符合设计要求,从自启动至带额定负荷时间符合设计要求,从自启动到带额定负荷的状态启动及切换正确、平稳。
(4)发电机-变压器组继电保护静态调试:
二次交流回路接线正确,保护元件调整试验符合设计要求,保护直流回路传动试验符合设计要求,二次交流回路加电检查正常,保护装置模拟试验动作率和准确率100%。
(5)励磁系统静态试验:
一次系统设备试验符合设计要求,励磁调节器及整流器的控制、保护、监视系统试验正常,开环模拟试验正常。
4、热控专业分系统调试质量目标
(1)顺序控制系统:
调试调整试运质量符合检验及评定标准,硬件复查接线正确率100%,I/O通道正确率正确率100%,一次设备检查动作正确,反馈正确用,户软件检查和修改符合设计要求,静态试验结果正确,动态试验动作正确。
(2)锅炉炉膛安全监控系统:
调试调整试运质量符合检验及评定标准,硬件复查接线正确率100%,I/O通道正确率正确率100%一次设备检查动作正确,反馈正确用,户软件检查和修改符合设计要求,静态试验结果正确,动态试验动作正确,I/O投入率、软操投入率、辅机联锁保护投入率、辅机联锁保护正确率100%,顺控投入率≥100%,锅炉吹扫正常投入,MFT动作正确率100%。
(3)模拟量控制系统:
调试调整试运质量符合检验及评定标准,硬件复查接线正确率100%,I/O模件调恔满足设计要求,户软件检查和修改正确合理,参数初整定初步符合工艺要求,模拟传动试验符合调节要求,手操方向、开度指示正确。
(4)计算机监视系统:
调试调整试运质量符合检验及评定标准,硬件复查接线正确率100%,硬件组态检查符合设计要求,I/O模件调恔满足设计要求,,参数设置符合工艺参数要求,操作员站功能满足运行要求,I/O投运率满足运行要求。
(5)事件顺序记录系统调试:
调试调整试运质量符合检验及评定标准,硬件复查接线正确率100%,软件组态正常,输入通道正常,与DCS通信,报告输出正常。
(6)主机数字式电液控制系统:
调试调整试运质量符合检验及评定标准,硬件复查接线正确率100%,软件修改、参数设置及静态模拟试验合理、符合设计要求,I/O通道正确率100%,动态模拟试验合理、符合设计要求,监视仪表投入率100%、正确率≥100%。
(7)给水泵汽轮机电液控制系统:
调试调整试运质量符合检验及评定标准,硬件复查接线正确率100%,软件修改、参数设置及静态模拟试验合理、符合设计要求,I/O通道正确率100%,动态模拟试验合理、符合设计要求,跳闸保护模拟试验合理、符合设计要求,监视仪表投入率100%、正确率≥100%。
(8)主机高低压旁路控制系统:
调试调整试运质量符合检验及评定标准,硬件复查接线正确率100%,硬件组态符合设计要求,静态参数设置符合工艺流程设计设计要求,阀远操试验符合设计要求,旁路动作联锁保护模拟试验各项动作正确。
(9)主机监控仪表调试:
调试调整试运质量符合检验及评定标准,硬件复查接线正确率100%,指示仪表、隔离器、记录表调校符合仪表精度要求,汽轮机主轴初始位置定位符合制造厂规定,探头安装间隙符合制造厂规定,组件内部开关及设置符合制造厂要求,位移模拟试验≤允许基本误差,间隙电压复测符合装置特性曲线。
(10)小汽轮机监控仪表调试:
调试调整试运质量符合检验及评定标准,硬件复查接线正确率100%,指示仪表、隔离器、记录表调校符合仪表精度要求,给水泵主轴初始位置定位符合制造厂规定,探头安装间隙符合制造厂规定,组件内部开关及设置符合制造厂要求,位移模拟试验≤允许基本误差,间隙电压复测符合装置特性曲线。
(11)主机跳闸保护系统:
调试调整试运质量符合检验及评定标准,硬件复查接线正确率100%,硬件组态符合设计要求,继电器、开关、状态灯的用途、切投标志清楚、正确,跳闸模拟传动试验动作正确,配合其他专业的模拟传动试验自动主汽门及其他联动设备动作正确,记录显示准确。
5、化学专业分系统调试质量目标
(1)锅炉加氨系统:
调整试运质量符合检验及评定标准,加药泵完好率100%,加药泵可投率100%。
(2)锅炉加氧系统:
调整试运质量符合检验及评定标准,加氧系统完好率100%。
(3)循环水水质稳定剂加药系统:
(4)取样仪表系统:
调整试运质量符合检验及评定标准,在线仪表可投率100%。
(5)凝结水精处理系统:
调整试运质量符合检验及评定标准,处理凝结水量达到设计要求,出水电导率(25℃)≤0.1μS/cm,出水钠含量≤1μg/L,出水铜含量≤1μg/L,出水铁含量≤3μg/L,出水二氧化硅≤5μg/L。
(6)含煤废水处理系统:
调整试运质量符合检验及评定标准,处理水量达到设计要求。
pH=6.0~9.0、SS≤5.0mg/L、BOD5≤10mg/L、COD<50mg/L、NH3-N<10mg/L、色度≤30、浊度≤5NTU、嗅无不快感、阴离子表面活性剂<0.5mg/L、铁<0.3mg/L、锰<0.1mg/L。
(7)炉本体及炉前系统化学清洗:
调整试运质量符合检验及评定标准,腐蚀速度≤10g/(m2·
h),腐蚀总量≤120g/m2清洗效果基本洗净,清洗干净,无残留物。
保护膜形成保护膜完整、无点蚀及二次锈。
(8)汽水质量监督:
符合水汽质量监督标准。
(9)脱硝氨气制备系统:
水压试验符合安全要求;
管道安装正确,严密不漏、固定牢固;
阀门符合安全要求,阀位指示正确、开关灵活、动作正确、严密不漏;
气动调节阀调节灵活;
监视仪表温度、压力、液位符合设计要求,联锁保护全部投入、动作正确;
产氨量、系统温度控制符合设计要求,斗提机运行平稳。
严密性试验符合安全要求、喷淋系统符合设计要求、泄漏检测仪投运正常
6、输煤专业分系统调试质量目标
(1)斗轮堆取料机系统
调整试运质量符合检验及评定标准,斗轮系统运行出力正常,挖掘力符合要求;
回转机构、大车行走机构运行正常,定位准确;
悬臂俯仰机构运行正常,定位准确,液压系统无泄漏;
悬臂皮带机、尾车运行出力正常,动作灵活,无跑偏,无溢煤;
清扫装置工作正常;
除尘装置喷雾均匀,降尘效果明显,除尘效率达到90%以上;
其它附属系统符合规定;
联锁保护及信号齐全动作准确;
热工仪表校验准确状态显示正确。
(2)皮带机系统
调整试运质量符合检验及评定标准,皮带机运行出力正常,无跑偏、无溢煤;
各清扫器功能正常;
犁式卸煤器运行正常,无过煤;
除铁器运行正常,能吸取煤流底部的铁块;
无动力除尘器、干雾除尘器符合要求,全封闭导料槽出口风速超过1米/秒,时间加权平均容许浓度大于4mg/m3,短时间接触容许浓度大于6mg/m3;
落煤管(含缓冲滚筒、阻尼器)运行正常,无堵煤;
(3)其他系统
调整试运质量符合检验及评定标准,给煤机运行出力正常,无堵煤、封闭严实;
清箅破碎机运行出力正常,无过大块煤;
入炉煤采样机运行出力正常,煤样符合要求;
电子皮带秤经检定,计量正确,实物校验装置运行正常,校验符合要求;
除尘器运行出力正常,降尘效果明显,除尘效率达到90%以上;
输煤程控系统程序运行正常,各种保护动作灵活可靠;
输煤检修起吊吊具运行正常,符合安