空心桨叶干化原理与工艺特征的深度剖析Word文档下载推荐.docx
《空心桨叶干化原理与工艺特征的深度剖析Word文档下载推荐.docx》由会员分享,可在线阅读,更多相关《空心桨叶干化原理与工艺特征的深度剖析Word文档下载推荐.docx(26页珍藏版)》请在冰豆网上搜索。
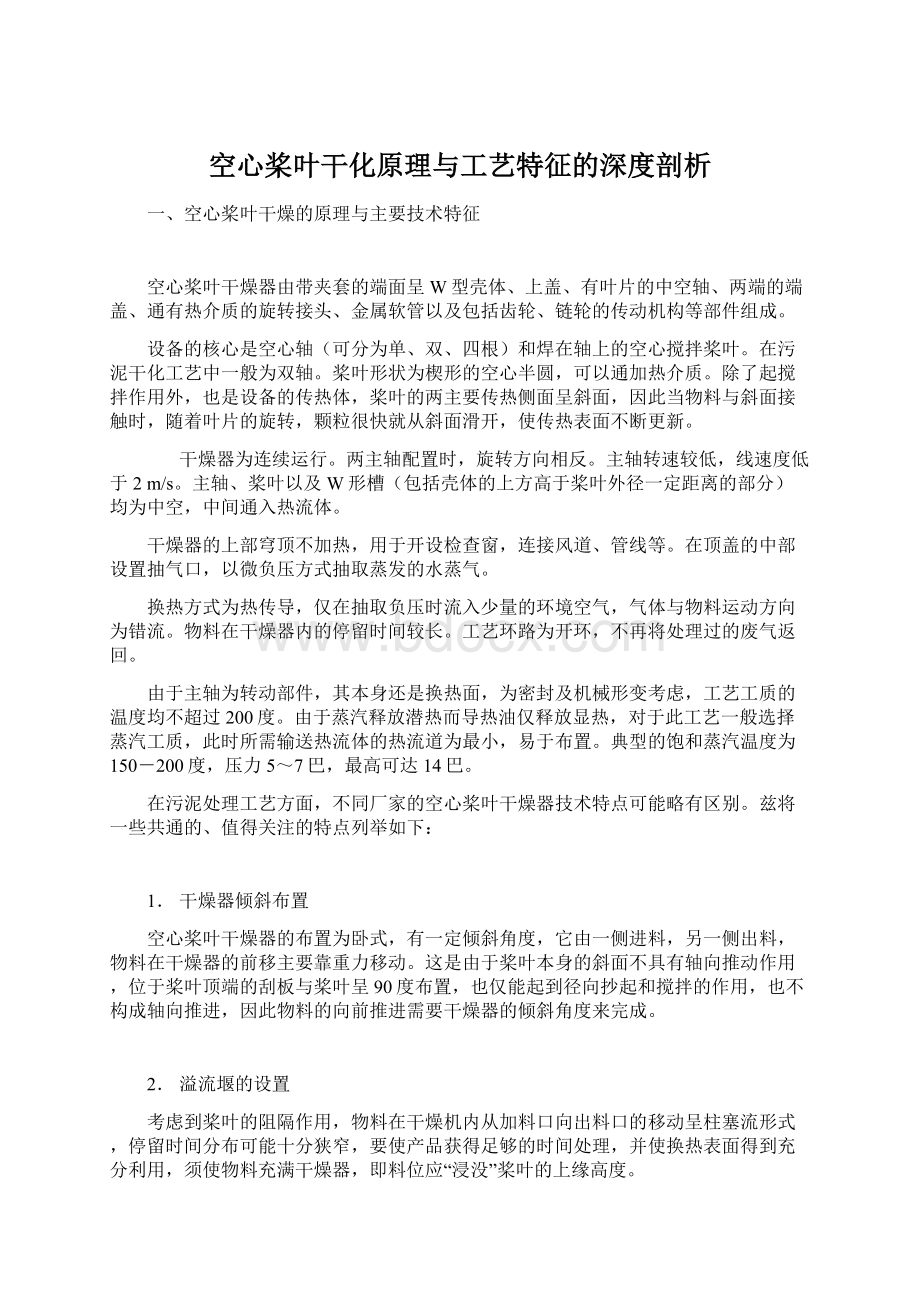
溢流堰位于干燥器尾部,干泥下料口的上方,它应具有类似“提升闸”的机械结构,以维持工艺所需的料位高度。
3.
加热轴类型
设备的加热介质既可以用蒸汽,也可用导热油或热水,但热载体相态不同,中空轴结构也不同。
用蒸汽加热的热轴管径小,结构会相对简单;
用热水或导热油加热的轴结构则可能比较复杂,因需要考虑管内液体流速,管径越粗,旋转接头及密封的难度越大。
向中空桨叶中供给热量,采用蒸汽工质时进出管线直径较小,这是由于释放潜热的特点所决定的。
但采用导热油时,要使之能够通过足够的热流体量,这些管线的直径可能变得较大,而这对于主轴来说可能降低其结构强度。
由于主轴本身具有多项功能(桨叶支撑、热流体输送、传热换热等),它需克服物料的粘滞力、物料与桨叶间摩擦以及物料本身对主轴表面的磨损等,主轴所需克服的应力可能较大。
这样在设计时,既要保证其机械强度,又要保证其换热性能,同时还需兼顾材料的硬度等,这些可能相互矛盾的条件将使设计变得复杂,而最终应用结果会具有较大变数。
如为了提高换热面积,需增加桨叶数量和直径,但这将导致主轴的应力增加。
要提高主轴的强度,需增加主轴直径,但这会相应减少桨叶的换热面积。
在项目中,主轴类型的选择常常是不可预见的,如原来采用蒸汽作为工质的定型产品,当改用导热油时,其热流道将完全不同,传热能力也有很大变化,无法简单复制原来的工艺参数。
这对于首次开发的新机型用户来说,可能意味着很多意想不到的问题。
4.
停留时间
理论上空心桨叶干化的停留时间可通过加料速率、转速、存料量等调节,在几十分种到几小时之间任意选定,其中溢流堰是调节干燥器内污泥滞留量的主要手段。
为了使换热面积得到充分利用,干燥器内污泥滞留量需求较高,料位需超过桨叶的上缘高度,即一般所说的“有效容积”需100%加以利用。
如果按蒸汽罩在内的整个干燥器筒体容积考虑,有效容积可能要占到干燥器总容积的70~80%。
干燥器内物料存留率高,将使得污泥在干燥器内的实际停留时间相应较长,为3-7个小时。
5.
干泥返混
理论上,由于空心桨叶互相啮合,具有自清洁作用,空心桨叶干燥器进行污泥干化应可完成各种含固率的污泥半干化和全干化,而无需进行干泥返混。
但实际上,要通过桨叶互相啮合而形成的物料剪切实现自清洁仍需要一定的前提条件,这就是设备中的啮合精度足够高,机械间隙足够小,以及物料间的剪切力足以克服产品在换热表面上的附着力。
在分析空心桨叶干燥器内部结构时,不难注意到其机械结构之间是存在较大间隙的。
完全靠机械咬合清理死区是不可能的。
这意味着真正实现空心桨叶热表面自清洁和更新的手段是物料之间的相互摩擦,即金属表面与物料之间以及物料与物料之间的剪切力。
实现物料之间相互摩擦可采用加大物料填充密度的方法,维持料位高度,可提高物料间的相互接触机会,配合桨叶叶片的挤压,可实现对某些换热面的自清理。
由于湿泥本身特性的原因,在干化过程中有成团、成球和搭桥的倾向,纯粹靠提高料位是无法克服的,因为湿泥颗粒之间的剪切力可能造成湿泥在无法更新的间隙中“压实”,而不会使其颗粒间产生疏松和流动性。
只有干泥因其颗粒表面已完全失水,具有在短时间内复水性不佳的特性,颗粒间隙大,遇到机械剪切力,才有滑离金属表面的可能性。
因此实际工程上,空心桨叶干化均考虑了干泥返混,其做法是对干泥进行筛分,细小干化污泥与湿泥进行预混合(美国KomlineSanderson一般均做此考虑,但有些厂家则声称无此必要)。
从换热效率角度考虑,干泥返混应该是必要手段之一。
根据污泥的失水状况,空心桨叶干燥器的蒸发速率具有明显的峰谷变化。
在含固率低于25%时,污泥在加热状态下有明显的液态性质,换热条件较佳,但物料易形成附着层而导致蒸发强度的降低,且污泥因高分子聚合物的作用,自身有形成团块的倾向,与换热面的接触率降低;
在含固率25%-75%之间时,污泥可能具有表面黏性,结团倾向明显,换热效果较差。
当含固率大于76%时蒸发速率回升,这是由于干细疏松的颗粒与换热面重新获得了较好的接触(据P.Arlabosse等的文章Dryingofmunicipalsewagesludge:
fromalaboratoryscalebatchindirectdryertothepaddledryer,BrazilianJournalofChemicalEngineering,vol.22no.2Sã
oPauloApr./June2005)。
空心桨叶工艺一般根据干燥目标,采取回流部分干燥污泥的做法(干泥返混),使干泥起一定的“润滑”作用,获得较好的流动性,避免黏着,回流量仅为出口干泥的小部分。
这就是说,空心桨叶的返混对干泥湿泥混合后比例要求不高,一般可能在40%左右(远低于一般要求的65%,如转鼓机),此时干泥粉末的存在,已足以在热表面起到“润滑”和“清理”的作用。
6.
干燥器内不清空
凡需要干泥返混的污泥干化工艺,对于湿泥的进料均有严格的要求:
湿泥进料须在干燥器已有大量干“床料”的条件下才能进行,这样才能避免湿泥一进去就糊住换热面、产生结垢。
因此,典型的做法是,在干燥系统停车时,应维持返料系统继续工作,停止进料装置,干燥产品实行全返料,同时系统降温,系统温度低于60℃时才全线停车,干燥机内不进行清料,开车时直接带料启动。
这意味着在停机时,干燥器内始终充满了干泥,在关机过程和开机过程中可能始终存在高粉尘、低湿度的特点,此时需关注干化安全问题。
7.
桨叶顶端刮板
任何机械都是有公差间隙的,主轴啮合的空心桨叶干燥器也不例外。
湿泥在一定含固率下具有黏性,在这些间隙之间可能造成黏壁。
在热表面上的任何黏结,将降低换热效率。
为避免污泥垢层的加厚,需采用机械刮削的方式,这就是位于桨叶顶端的刮板(paddleplates)所起的作用。
从刮板的作用可知,随着长期运行,刮板对且仅对落在桨叶与W形槽换热面之间的物料有抄起作用,同时也对附着在W型槽壁上的物料有刮取作用,无论抄起还是刮取,由于刮板的运动速度大约为2~5米/秒,在抄起或刮取的过程中,此速度下刮板外缘的污泥的运动方向有两个:
向外挤压(磨W形槽)和向后运动(磨刮板)。
8.
金属表面硬化处理
磨损可能是空心桨叶干燥器所面临的重要挑战之一。
污泥中含有磨蚀性颗粒,空心桨叶干燥器属于典型的传导接触型换热,金属与磨粒的反复、长期接触,金属磨蚀是不可避免的。
涂层和硬化可减轻磨蚀的速度,但受限于被磨蚀的金属面同时也是换热面(如W形槽、桨叶、主轴,刮板可更换),所能采取的硬化措施不多(喷涂碳化硅等),在加热条件下耐磨层的附着力、实际硬度都不甚理想,只能起到减缓磨蚀的作用。
由于干泥颗粒和粉尘中磨粒的磨蚀作用较为突出,一般对后半段(15~25%)的桨叶进行热处理保护。
但对于有干泥返混的工艺,其磨蚀则是全程的。
磨蚀倾向的存在,无疑也将影响到干燥器的材质选定。
空心桨叶干燥器的换热金属面中,只有W形槽因与刮板间隙最小,在热表面更新过程中有明显的挤压作用。
当存在这种挤压缝隙时,一般磨蚀强烈的是相对较“软”的金属面。
这可能意味着要保护作为换热面的W形槽,刮板则不能做硬化。
而不做硬化的刮板寿命将十分有限。
9.
机械死角
机械死角是空心桨叶干燥器必需解决的设计难题之一。
它可分为三类:
1)无表面机械清理的金属外缘;
2)有表面清理但存在不可触及的公差;
3)因磨蚀造成的不可触及公差加大。
楔形桨叶本身的旋转方向是一定的,即两个主轴均向内侧旋转,此时楔形桨叶的窄侧在前,刮板在后,桨叶从窄而宽的换热面上均无机械清理,需要靠物料自身的剪切力更新。
刮板大于楔形部分最宽换热面的部分将始终刮带污泥,并在W形槽上形成挤压。
此外,刮板与主轴仅在某一点(即扇形缺口的中心部位)上有“切线相交”(其实是接近,清理作用微乎其微),主轴在绝大部分情况下表面没有机械清理。
上述均属于无表面机械清理的金属外缘,它占总换热面积的70~80%。
有机械清理的换热表面,按照楔形桨叶的排布规则,存在以下因不可触及公差所造成的死角:
-
第一排和末排桨叶的刮板与加热主轴外侧的空隙,介于干燥器桨叶与主轴填料密封之间。
轴向刮板间的空隙,此间隙可明显观察到。
由于前述磨蚀问题,可能造成特别是径向刮板空隙的增大,即刮板因磨蚀而变薄,刮板与W形槽换热面的不可触及公差加大。
此时刮板所起的刮取作用减低,在物料之间的剪切力不足以克服湿泥在换热面上的附着力时,在换热面上的堆料和结垢就会产生。
当形成一定厚度时,将导致轴跳、震动和噪声等。
无法清理的换热表面均可称之为“机械死角”。
综合来看,空心桨叶干燥器无法进行机械清理的部位占了换热面积的大部分,因此对于这种工艺来说,核心问题在于如何避免产品的黏性。
10.
传热系数
空心桨叶干燥器由于桨叶垂直于主轴,刮板平行于主轴,桨叶两端的换热面无推动而仅起换热作用,物料的径向混合充分,物料与换热面的接触频率较高,停留时间长,理论上应可实现较好的换热,其综合传热系数应在80~300W/m2.K之间。
在污泥干化应用方面,由于不同的污泥黏性不同,干化产品含固率也影响到工艺过程(如能否进行低干度半干化),实际项目中给出的传热系数可能相差较大。
11.
传热面积
根据前面的描述可知,热轴上的楔形桨叶和主轴是主要的加热面,换热面积占总换热面积的70%以上(后面将加以证明)。
设计上对制造精度、主轴类型和热流道布置上有较高要求,因此一般认为这种干燥器“结构复杂,加工难度高,大型干燥机的设计有一定难度”。
截至2008年底,国外已制造出单机换热面积1.5
~295平方米、理论最大蒸发能力12
吨/小时的空心桨叶干燥器。
在污泥干化领域,目前最大装机换热面积约300平方米,蒸发能力不到5000公斤/小时。
据不完全统计,国内目前的系列化设计最高110平方米,已见于报道的用于污泥干化的空心桨叶干燥器换热面积多为25~50平方米,最高达160平方米。
由于污泥干化是有技术难度、大宗、无增值的产品应用,设备的大型化是节约投资的重要手段。
但基于前述空心桨叶的特点,设备放大具有较高的技术难度。
12.
吹扫空气量
空心桨叶干燥器属于典型的传导型干燥器,其传热和蒸发是靠热壁而不是靠气体对流实现的。
因此,大多数空心桨叶厂家均声称不需要吹扫空气。
实际应用中,由于干燥过程产生的水蒸气需要及时离开干燥器,且污泥干化产生恶臭,为防止臭气溢出到环境,一般均需采用抽取微负压方式。
这样就事实上存在了使用“吹扫空气”的必要性。
抽取负压必然会造成环境空气从干燥器和回路的缝隙中(轴缝、湿泥入口、干泥出口、溢流堰密封等)进入回路,为了防止这部分气体在干燥器中造成水蒸气冷凝,有时还需要对此气体进行加热。
吹扫空气的量与工艺本身相关,以升水蒸发量所需的环境空气干空气量衡量,一般在0.1~1.2kg/kg.H2O之间。
此值的高度对干化系统的净热耗有重要影响。
典型的空心桨叶干燥一般考虑0.5kg/kg.H2O左右的干空气量。
13.
蒸发强度
传导型干燥器的蒸发能力一般以每平方米、每小时的蒸发量来衡量,它在理论上可实现10~60kg/m2.h的蒸发量。
但在污泥干化实践中,根据我对世界上主要空心桨叶制造商业绩的统计,设计值取值范围一般在6~24kg/m2.h之间,以14~18kg/m2.h的取值居多。
对于蒸发强度的取值,可以从多个技术文献得到印证。
如日本奈良机械制作所污泥干化专利“特开平9-122401”,试验条件下的污泥干化蒸发强度在6~6.8kg/m2.h之间。
浙江大学热能工程研究所的试验在90分钟后、40%干燥率下也只有6kg/m2.h。
得利满研发部的研究报告则提出空心桨叶计算模型取值在11.5~13.8kg/m2.h之间。
参考其它传导型干化(如转碟机、圆盘机),典型值均在8~14kg/m2.h之间。
考虑到空心桨叶干燥器的换热条件与其它传导型干燥器事实上非常相似,较为可靠的实际蒸发强度应该在8~14kg/m2.h之间。
14.
产品出口温度
由于污泥在干燥器内停留时间长,污泥在离开干燥器时的出口温度较高,应在90~100℃左右。
污泥温度高,则产品在筛分以及输送(包括返混)过程中,可能对安全性产生影响。
因干泥返混的原因,在筛分前或是否后降温将关系到系统的净热耗。
此外,进入停机序列后,热载体撤除或停供后,产品的降温仍需要走一个非常缓慢的过程,理论上剩余产品均需经外部的冷却措施才能实现。
基于空心桨叶的工作原理及其内部容积,很难想象空心桨叶干燥器能够采用喷水降温这样的快捷方式进行安全保护。
二、空心桨叶干燥器的结构与特点
要真正了解一种干化工艺,进行一些设计分析是必要的。
空心桨叶从过程工艺角度看是较为简单的,其特性主要是机械形式决定的。
根据日本TsukishimaKikai
公司系列空心桨叶设备的尺寸,我尝试建立了一个空心桨叶干燥器的设计模型。
选择其中换热面积100平方米、有效容积6.66立方米的ID1000DSL-K型双轴设备作为参考,根据其标注的尺寸,利用几何学知识,不难求出截面上各位置的面积。
对加热主轴长度进行设定,即可求出干燥器的总容积。
由量图知,桨叶所围出的两个扇形面积夹角一般为144度左右。
桨叶直径已知(1米),给出主轴直径(0.3~0.5米),则扇形换热面面积可求。
根据干燥器内桨叶布置需要,可设定刮板宽度、桨叶最大厚度、桨叶最小厚度、刮板间最小公差。
在上述参数给出时,可认为桨叶的径向外缘为一梯形,其高为桨叶扇形的弧长;
主轴的换热面积为加热主轴总面积减去桨叶焊接面积(主轴上144度扇形弧长,宽度为厚度),则桨叶的外缘换热面积、主轴有效面积均可求,从而得到干燥器的实际换热面积。
由于换热面积和有效容积已知,上述假设各项尺寸、主轴直径、桨叶数量以及加热轴有效长度的给定均会影响上述两个已知参数。
通过建立体积和换热面积的两个方程组,可解出一组同时满足两个方程组的数据:
当主轴直径为0.41
米时,加热主轴的长度约为6.15米,基本符合干燥器体长度6.27米的原设计值。
此时,桨叶、主轴和W形槽的换热面积分别占总换热面积的64.6%、13.5%、22.0%,也符合一般所说的换热面比例分配。
在结论基本正确的基础上,可确认以下几个关键取值具有可参考性:
刮板宽度50mm、桨叶换热面最大厚度40mm、最小厚度14mm、刮板间最小公差3mm;
桨叶总数量58对,116个;
W形槽的弧直径1.006米,即桨叶刮板与W形槽换热面的距离只有3毫米;
分析过程中可注意到取值范围极窄,特别是刮板宽度和刮板间最小公差。
这意味着干燥器的设计极为紧凑、“精密”,其目的可能是为了减少W形槽换热面的死角。
套用此模型,可分析其它一些机型的参数。
比较这些参数,可发现其中的某些规律。
这些规律是解读空心桨叶干燥器的钥匙。
Komline13W2200机型
已知KS干燥器13W2200具有204平方米换热面积、18立方米的有效容积。
应用模型可分析其可能的构成如下:
当主轴直径为0.50
米时,加热主轴的长度约为10.06米。
与ID1000DSL-K型比较,换热面积增加一倍,有效容积增加约2.7倍,而加热主轴部分的长度仅增加0.67倍。
此时,桨叶、主轴和W形槽的换热面积分别占总换热面积的64.6%、13.0%、22.5%。
其它关键取值:
刮板宽70mm、桨叶换热面最大厚度60mm、最小厚度20mm、刮板间最小公差4mm;
桨叶总数量68对,136个;
W形槽的弧直径1.34米,即桨叶刮板与W形槽换热面的距离仍只有3毫米;
Komline13W2500机型
已知1995年美国某个工业污泥项目上提供了一台型号为13W2500的空心桨叶干燥器,换热面积232平方米。
该项目处理量每小时4535kg,含固率25%,干化至90%。
在前述204平方米干燥器模型基础上,分析此干燥器的可能构成如下:
因所需桨叶数量增加,适当增加主轴直径至0.56
米;
桨叶总数量78对,156个;
加热主轴长度约为11.54米;
其余设置不变,此时有效容积增加为20.5立方米,较13W2200机型增加了约14%。
桨叶、主轴和W形槽的换热面积分别占总换热面积的62.4%、14.6%、23.0%。
3.
W12机型
已知三门峡百得干燥有限公司空心桨叶干燥器系列最大机型W12的参考尺寸如下:
传热面积110平方米,有效容积9.46立方米,器体宽2.21米,长6.122米,进出料口距离5.664米。
这意味着干燥器加热主轴长度应在器体长度和进出料距之间(5.664~6.122米)。
与ID1000DSL-K相比,12W的换热面积增加了10%,有效容积增加了42%,而加热主轴长度可能短了约40~60厘米,这意味着所增加的换热面积主要在桨叶上,需增加桨叶直径。
试算获得如下一组数据:
当桨叶直径为1.25米、主轴直径为0.56
米时,加热主轴的长度约为5.84米。
此时,桨叶、主轴和W形槽的换热面积分别占总换热面积的60.7%、16.1%、23.2%。
其它取值:
刮板宽68mm、桨叶换热面最大厚度50mm、最小厚度14mm、刮板间最小公差5mm;
桨叶总数量40对,80个;
W形槽的弧直径1.256米,即桨叶刮板与W形槽换热面的距离只有3毫米;
将上述计算数据列表如下:
机型
单位
ID1000DSL-K
13W2200
13W2500
12W
换热面积
m2
100
204
232
110
有效容积
m3
6.66
18
20.5
9.46
桨叶数量
个
116
136
156
80
桨叶直径
m
1.0
1.3
1.25
加热主轴长度
6.15
10.06
11.54
5.84
主轴直径
0.41
0.50
0.56
刮板宽度
mm
50
70
68
刮板间最小公差
3
4
5
桨叶换热面最大厚度
40
60
桨叶换热面最小厚度
14
20
换热面积/有效容积比
15.0
11.3
11.6
长径比*
20.1
20.6
10.4
桨叶占换热面积比
%
64.6%
62.4%
60.7%
主轴占换热面积比
13.5%
13.0%
14.6%
16.1%
W形槽占换热面积比
22.0%
22.5%
23.0%
23.2%
*
仅指加热主轴部分的长度与主轴直径之比,不同于实际主轴长度与主轴直径比
计算所得到的结果与实际机型对照肯定会有某种差距,但它在一定程度上可仍可反映空心桨叶干燥器内部结构的关系,这些关系是进一步分析空心桨叶干燥器特点的参考。
根据上述计算,主要观察要点如下:
—
从换热面积/有效容积比可以看出,空心桨叶干燥器直径越大,有效容积越大。
有效容积是反映空心桨叶干燥器污泥干化的重要状态参数。
刮板的宽度及其间距是决定干燥器加热主轴长度的重要数据。
它直接影响W形槽换热表面的更新状况。
主轴越长,则桨叶的直径可以越小;
反之,桨叶的直径越大,主轴可以越短。
短(粗)主轴便于加强其机械强度,但也带来有效容积的上升。
长径比越大,主轴制造的精度和结构强度要求越高。
国产机的长径比较国外设备低了很多。
桨叶换热面的厚度应与钢板厚度相关。
一般传导型干燥器的换热面均采用12~14mm碳钢或10~12mm不锈钢板成型焊接。
桨叶的最大厚度减去两倍的钢板厚度,即为中空热流道的最大理论厚度(若不考虑其它支撑的话)。
从换热面积的分配比例看,桨叶占60~65%,主轴占14~16%,W形槽占22~23%,这一范围是基本确定的。
这意味着空心桨叶干燥器真正靠机械更新的换热表面只有22~23%,其余均需纯靠物料本身的剪切力(这一点与文献所提到的数据完全吻合)。
以物料本身剪切力为特征的换热表面更新将不得不十分倚重物料本身的流动性。
而要实现此流动性,干泥返混可能是惟一可用和可行的手段。
在上述参数给出时,可认为桨叶的径向外缘为一梯形,其高为桨叶扇