0410210230+吴毛毛+包装桶塑料模具设计++++Word格式.docx
《0410210230+吴毛毛+包装桶塑料模具设计++++Word格式.docx》由会员分享,可在线阅读,更多相关《0410210230+吴毛毛+包装桶塑料模具设计++++Word格式.docx(28页珍藏版)》请在冰豆网上搜索。
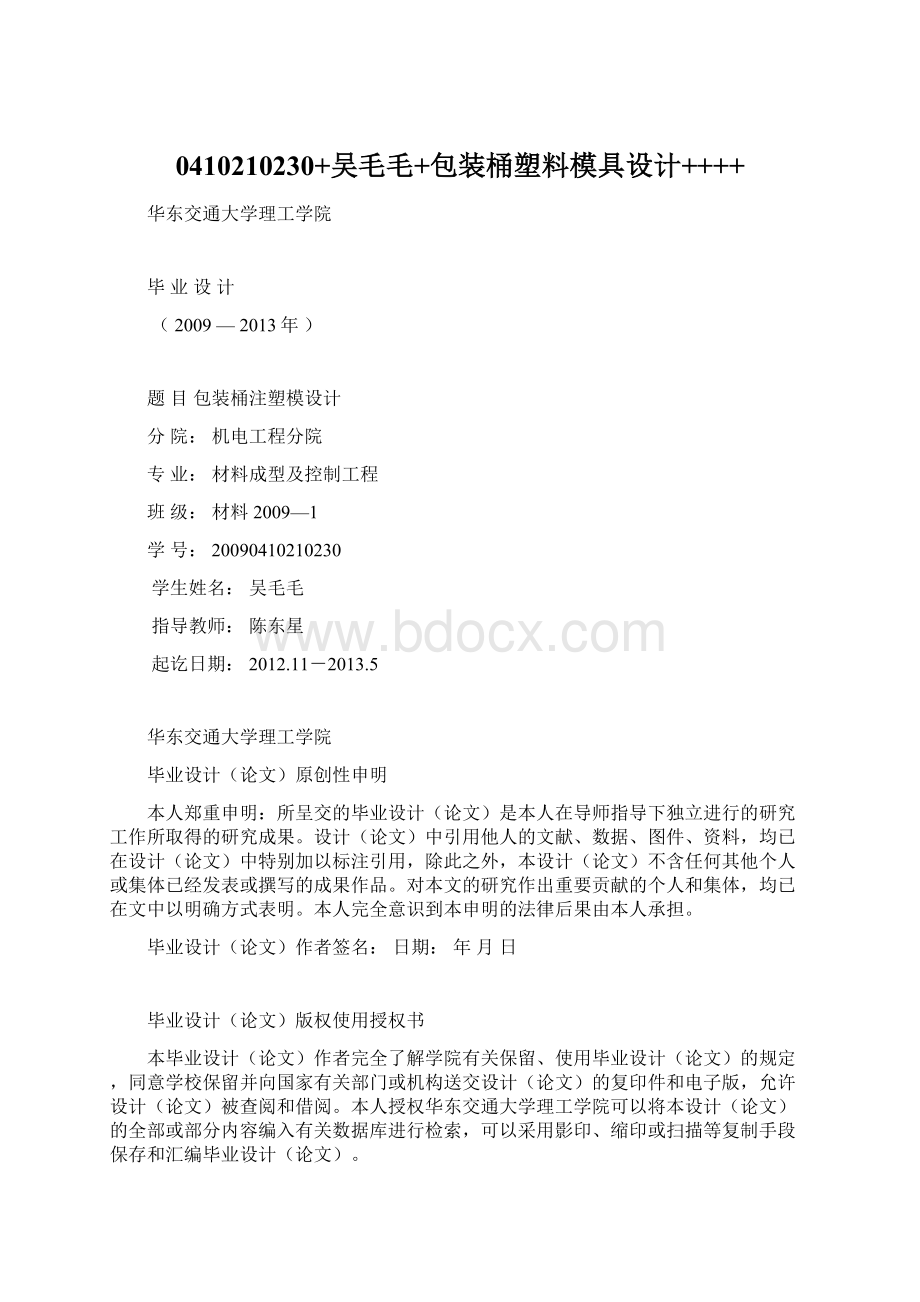
本人授权华东交通大学理工学院可以将本设计(论文)的全部或部分内容编入有关数据库进行检索,可以采用影印、缩印或扫描等复制手段保存和汇编毕业设计(论文)。
(保密的毕业设计(论文)在解密后适用本授权书)
指导教师签名:
签字日期:
年月日签字日期:
引言
模具是工业产品生产用的重要工艺装备,在现代工业生产中,60%~90%的工业产品需要使用模具,模具工业已成为工业发展的基础,许多新产品的开发和研制在很大程度上都依赖于模具生产,特别是汽车、摩托车、轻工、电子、航空等行业尤为突出。
塑料成型技术发展十分的迅速,新的成型工艺层出不穷,因此必须了解新的成型工艺与成型技术,以便掌握和推广。
在塑料成型生产中,先进的模具设计、高质量的模具制造、优质的模具材料、合理的加工工艺和现代化的成型设备等是成型优性塑件的必要条件。
一副优良的注塑模具可以成行成千上万次,一副优良的压缩模具可以成型25万次,这与上述因素有很大的关系.由于塑料成型工艺与模具设计是一门实践性很强的课程,所以学习是必须理论联系实际。
必须以负责的态度去完成毕业设计、积极参加生产实习,将所学的知识与模具工业的生产实际进行联系与比较、归纳与提升,从而使学生在凭自己的能力以及查阅有关资料的前提下,在校期间能够设计具有一定难度的塑料模具。
这次毕业设计不仅让我熟悉了课本所学知识,而且让我做到所学的运用到实践当中,更让我了解了塑料模具设计的全过程和加工实践的各种要点。
使我在本次设计实践当中有一个质的飞跃。
我很喜欢塑料模具设计这份工作,从进入大学我就励志要做一名很好的模具工程师!
Introduction
Mouldisoneoftheimportanttechnologyandequipment,industrialproductsproductioninthemodernindustrialproduction,60%~90%oftheindustrialproductsneedtousethemould,mouldindustryhasbecomethebasisofindustrialdevelopment,thedevelopmentandthedevelopmentofmanynewproductslargelydependsonthemoldproduction,especiallyinautomobile,motorcycle,lightindustry,electronic,aviationandotherindustries.Plasticmoldingtechnologydevelopmentisveryrapid,newformingtechnologyemergeinendlessly,somustunderstandthenewmoldingprocessandmoldingtechnology,Diestructuredesignisoneofthemainelementsofthisdesign,whichcontainsthemoldpartinglineselection,makingiteasytounderstand,easytoprocess.inordertomasterandpopularize.Inplasticmoldingproduction,advancedmolddesign,highqualityofmouldmanufacturing,high-qualitymoldmaterial,thereasonableprocessingtechnologyandmodernmoldingequipmentisnecessaryconditionofoptimalityplasticformingparts.Agoodpairofinjectionmoldcanmaketensofthousandsoftimes,agoodpairofcompressionmoldcanmolding250000times,ithasalottodowiththesefactors.Becausetheplasticmoldingprocessandmolddesignisapracticalcourse,solearningisamustintegratetheorywithpractice.Muststartwitharesponsibleattitudetocompletegraduationdesign,activelyparticipatedinproductionpractice,thelearnedknowledgeandtheactualproductionofmoldindustrycontactandcomparison,inductionandascension,whichmakethestudentsownabilityaswellasaccesstorelevantinformationunderthepremiseof,duringtheperiodofschoolcandesignhasthecertaindifficultyofplasticmold.
Thisgraduationdesignnotonlymakesmefamiliarwiththetextbookknowledge,butalsoletmedowhattheyhavelearnedintopractice,moreletmeknowthewholeprocessoftheplasticmolddesignandprocessingpracticeofthevariouspoints.Ipracticeinthedesignhaveaqualitativeleap.ThejobIlikeplasticmolddesign,fromenteringtheuniversityIwantedtodoagoodmouldengineer!
1.塑件工艺分析
1.1塑件分析
此包装桶上雕刻有文字,还有侧孔以及外螺纹,精度等级为4级,要求比较高。
为了便于分型,简化模具结构,我采用哈呋结构来分型包装桶。
1.2塑件材料的确定
考虑到包装桶的工作环境的恶劣以及所受的力的大小来看,其在运输过程中需要承受外在的压力,还要经受风吹雨打以及认为的破坏。
要求包装桶具有一定的强度,耐腐蚀性。
综上各种塑料的性能来考虑,高密度聚乙烯(HDPE)具有以上工作环境所需的性能,为此确定使用材料为:
高密度聚乙烯(HDPE)
1.3工艺特点
HDPE在熔融温度下有较好的流动性,充模性能好,成型性能好。
高密度聚乙烯(HighDensityPolyethylene,简称为“HDPE”),是一种结晶度高、非极性的热塑性树脂。
原态HDPE的外表呈乳白色,在微薄截面呈一定程度的半透明状。
PE具有优良的耐大多数生活和工业用化学品的特性。
某些种类的化学品会产生化学腐蚀,例如腐蚀性氧化剂(浓硝酸),芳香烃(二甲苯)和卤化烃(四氯化碳)。
该聚合物不吸湿并具有好的防水蒸汽性,可用于包装用途。
HDPE具有很好的电性能,特别是绝缘介电强度高,使其很适用于电线电缆。
中到高分子量等级具有极好的抗冲击性,在常温甚至在-40F低温度下均如此。
1.4塑料的收缩率及密度确定
表1.1材料性能参数
材料
代号
密度
(kg.m-3)
收缩率
(%)
模具温度
(℃)
注射压力P注
(Mpa)
最大不溢料间隙/mm
PE
940-960
1.5-3.6
60-70
60-100
0.02
HDPE
941-960
1.5-3.0
30-60
70-100
0.03
ABS
1030-1070
0.3-0.8
50-80
0.04
PVC
1380
0.6-1.5
80-130
由表1.1知高密度0聚乙烯HDPE的收缩率(1.5-3.0)%。
由高密度聚乙烯的成形特点可知其成形收缩率范围及收缩率大,所以在选择高密度聚乙烯的收缩率时应考虑使用大的收缩率确定收缩率值为2.0%,其平均密度为0.9505g/cm3。
1.5模具种类与模具设计的关系
不同种类的塑料其工艺性能、成形特性也不相同,因此为了确定塑料的工艺性能、成形特征,并在模具中充分利用以获得优质的塑料制件。
表1.2塑料种类与模具设计关系
塑料
特征
注意事项
高密度聚乙烯(HDPE)(结晶型)
直接浇口增大塑料熔体流动性。
冷却速度快
流动性好具有铰链性能
尽量采用直接浇口,尤其是深型腔的桶装塑件。
浇注系统散热面积要小,以降低冷却速度,保证塑料顺利充填型腔
塑件的成型要求:
化学性能稳定,宜于成形加工等,闭合弯折不容易产生损坏和断裂现象。
塑件表面要求无飞边或缩孔现象。
塑料成型工艺参数:
模具温度:
30℃--60℃
喷嘴温度:
150℃--180℃
料筒温度:
前段温度:
180℃--190℃
中段温度:
180℃--200℃
后段温度:
140℃--160℃
注射压力:
70—100MPa
注射机类型:
螺杆式
保压压力:
40--50MPa
喷嘴形式:
直通式
注射时间:
0—5S
保压时间:
15—60S
冷却时间:
成形周期:
40—140S
二.注射机的选用及型腔数的确定
2.1.利用PRO/E进行体积的计算
根据产品图纸,将塑料包装桶按1:
1的尺寸比例在PROE里完成三维构图。
利用PROE分析指令对塑料包装桶进行体积的计算如图所示
体积=7.6376041×
mm3
=76376.041mm3
2.2确定型腔数及其排列
图-型腔的布置
2.3注射机的选用
利用PROE分析指令对塑料包装桶进行体积,可计算浇注系统的体积为76.376041cm3,以包装桶为例,分析了包装桶的结构特点和使用要求,在此基础上选择了制品材料,设计了一种成型外螺纹塑件塑料模具。
就塑件的成型工艺性、浇注系统、成型零部件结构、推出系统、冷却系统等的设计进行了研究与探讨,为外螺纹塑件的脱模提供了一种新的思路与研究方法。
经设计研究表明,该模具采用一模一腔的哈呋结构。
直浇口进料,模架为本人自己设计的一副模架。
模板周界尺寸W×
L为290×
300。
注塑机型号为XS-ZY-60/125。
2.4锁模力的校核1.1塑件分析
锁模力为注射机锁模装置用于夹紧模具的力。
所选注射机的锁模力必须大于由于高压熔体注入模腔而产生的胀模力,此胀模力等于塑件和流道系统在分型面上的投影
面积与型腔压力的乘积
F>
P×
A/1000
式中F——锁模力,kN
p——型腔压力,MPa
A——塑件及流道系统在分型面上的投影面积,㎜²
已知型腔压力为25或30MPa;
浇注系统的投影面积为1倍的塑件投影面积;
塑件及流道系统在分型面上的投影面积为
A=n×
πR2+S
式中S——流道系统在分型面上的投影面积,㎜²
n——模腔数
注:
带入数据得,该注塑机的锁模力是合格的(计算均在草稿纸是完成)
2.5模架的简介
我国目前标准化注射模零件的国家标准有24个;
另外还制订了塑料注射模具的标准模架,分《中小型模架》(GB/T12556.1—90)和《大型模架》(GB/T12555.1—90)两种。
《中小型模架》标准中规定即基本型,A、B、C和D四个品种。
现举几例,如下图所示
ABCD
此处只是对于标准模架才有的选,对于我做的包装桶,是没有标准模架的,故我自己设计了一副模架,见下图:
3.模具结构设计
3.1模具结构
该塑件为中小型制品,尺寸精度较高。
采用Pro/E设计后,一个制件的体积为76.376041cm3。
为了提高生产效率,设计一模一腔的直接浇口模具结构。
总体模具结构如图所示。
3.2分型面位置确定
注塑过程完成后。
需要将制件和流道凝料一起推出模外,在进行下一次注塑循环。
由于这是一模一腔,故流道凝料占很少一部分体积,因而凝料脱模比较容易。
因此笔者在设计模具的时候采用了直接浇口简单模具结构,具有一个分型面,为A—A分型面。
3.3浇注系统设计
浇注系统是指模具中由喷嘴到型腔之间的进料通道。
普通浇注系统一般由主流道、分流道浇口和冷料血等四部分组成。
主流道垂直于分型面的浇口称为直接浇口。
主流道平行于分型面的浇口称为横浇口式浇注系统。
浇注系统的设计师模具设计的一个重要的环节,设计的合理与否对塑件的性能、尺寸、内在的质量、外在质量及模具结构、塑件的利用率有较大的影响。
对浇注系统进行设计时,一般应遵循以下基本原则:
(1):
了解塑料的成型性能;
(2):
尽量避免或减少产生熔接痕;
(3):
有利于型腔中气体的排出;
(4):
防止型芯的变形和嵌件的移位;
(5):
尽量采用较短的行程充满型腔;
(6):
流动距离比的校核。
主流道整体设计成圆锥形,锥角60,内壁粗糙度为0.8微米,其它部分粗糙度为0.32。
主流道上部小端直径比注塑机喷直径嘴大lmm,为了补偿喷嘴与主流道的对中误差,避免注塑时喷嘴与主流道衬套之间由于配合不准造成溢料现象,通常球面半径比注塑机喷嘴球面半径大2mm。
由于本人设计的此副塑料模具是一模一腔,故只要一个主流到即可,没有分流道。
3.4主流道设计
主流道是指浇注系统中从注射机喷嘴与模具浇口套接触处开始到分流到为止的塑料熔体的流动通道,是熔体最先流进模具的部分,它的形状与尺寸对塑料熔体的流动速度和充模时间有较大的影响,因此,必须使溶体的温度降低和压力的损失最小。
为防止主流道与喷嘴处溢料,与主流道对接处紧密对接,主流道与注塑机连接处应制成半球形凹坑,主流道的小端直径大于注射机的喷嘴直径1-2mm,半球型凹坑的半径应大与注射机喷嘴的球型半径2mm左右。
为减小料流转向流动时的阻力,主流道大端呈圆角过渡,其圆角半径r=1~3mm.在保证塑料良好成型的前提下,主流道应尽量短,否则将增加流道凝料。
主流道通常设计在浇口套中,为了让主流道凝料能顺利从主流道中拔出,主流到应设计成圆锥型的。
锥角a为2~6度,流道的粗糙度小于等于0.8微米。
由于主流道与塑料熔体及喷嘴反复接触和碰撞,根据互换性原理。
因此常将主流道制成可拆卸的主流道衬套,便于用优质钢材加工和热处理,但此处我并没设计衬套。
主流道是注射机喷嘴与分流道的塑料熔体的流动通道,其形状尺寸对熔体的流动和充模时间有很大的影响。
主流道一般设计在浇口套中,为更容易的取出,主流道通常设计成圆锥形。
锥角在2~3度,内壁粗糙度为Ra=0.16μm。
根据制件的实际情况,结合所选注塑机的型号,主流道的锥角选2°
,主流道如下图所示
3.5浇口的形状及其位置选择
浇口亦称进料口,是连接分流道与型腔的熔体通道。
交口的设计与位置的选择恰当与否,直接关系到塑件能否被玩好高质量的注塑成型。
按浇口的结构形式和特点,常用的浇口可分为以下几种形式:
1:
直接浇口直接浇口又称主流道型浇口,塑料熔体由主流道的大端进入型腔,因而具有流动阻力小、、流动路程短及补塑时间长等特点。
2:
侧浇口侧浇口一般开设在分型面上,塑料熔体从内测或外侧充填型腔,其截面型腔多为矩形,改变交口的宽度可调节熔体的剪切速率及浇口的冻结时间。
3:
环形浇口环形浇口的特点是均匀,圆周上各处流动的速度大致相等,熔体流动状态好,型腔中的空气容易排出,熔接痕基本避免。
4:
轮辐式浇口这种浇口的好料量比环形浇口少得多,且去除浇口容易。
5:
点浇口点浇口又称针点浇口或菱形浇口,是一种界面尺寸很小的交口,俗称小浇口。
6:
潜伏式浇口潜伏式浇口又称剪切浇口,是由点叫孔浦变异而来。
7:
爪型浇口爪型浇口可在星新的头部开设流道,也可在主流道下端开设流道。
3.5.1浇口位置的选择
浇口的形式很多,但无论采用什么形式的浇口,其设计的位置对塑件的成型性能及成型质量影响很大,因此,合理的选择浇口的开设位置是提高塑件质量的一个重要的设计环节。
选择浇口位置时,需要根据塑件的结构与工艺特征和成型的质量要求,并分析塑料原料的工艺特性与塑料熔体在模具内的流动状态、成型的工艺条件,综合进行考虑:
尽量缩短流动距离;
避免熔体破裂现象引起塑件的缺陷;
浇口应开在塑件壁厚处;
考虑分子定向的影响;
减少熔接痕提高熔接强度。
3.6冷却系统的设计
注塑模具的温度对塑料溶体的充模流动,固化定型,生产效率,塑件形状尺寸精度独有影响。
注射模具中设置温度调节系统的目的,是通过控制模具温度,是注射成型具有良好的品质和较高的生产力。
我们知道的最近常见的冷却系统的结构:
下面是介绍的常见的冷却贿赂的设置的基本原理
冷却水道也多冷却通道孔越大越好,它们要达到一定的尺寸冷却睡到越多就越好,截面,和型腔表面的温度也和其他因素有关。
冷却水道至型腔的表面区离应尽量相等
浇口处加强冷却
冷却水道出入口温差应较小
冷却沿收缩的地方设置
二.常见的冷却系统结构
(1)直流和直流循环式
(2)循环式
(3)喷流式
(4)隔板式
(5)特深型腔塑件的冷却
(6)间接冷却
我设计的这副模具哈呋上采用了大的直通孔,型芯上采用了冷却系统,这样有力与保持模具在一定的温度范围内。
四.脱模机构设计
4.1推出结构设计
该制件是一包装桶,外螺纹常采用哈呋来成型。
桶装产品一般采用推件板推出机构,但由于我采用了哈呋来分型此产品,故不能用推件板,只能用推杆。
另外,也可考虑气领方式脱模。
需要说明的是对这种较深的容器件,顶杆应沿轴向加工气槽,顶出时与模外相通,避免制品与型芯之间“闭气”,造成顶出困难,甚至损坏制品。
顶杆一弹簧复位是应用较普遍也是简单的一种方式,缺点是用的时间长了可能出现弹力下降现象,使用过程中应注意并及时更换。
为此,在设计此模具的时候,推出机构具体结构见图
顶杆
五.导向及定位机构
注射模的导向机构主要有导柱导向和锥面定位两种类型。
导柱导向机构用于动、定模之间的开合模导向和脱模机构的运动导向。
锥面定位机构用于动、定模之间的精密对中定位。
导套:
导套分为直导套和带头导套,直导套装入模板后,应有防止被拔出的结构,带头导柱轴向固定容易导向机构整体如图所示.我设计的导柱导套如下:
导柱:
国家标准规定了两种结构形式,分为带头导柱和有肩导柱,大型而长的导柱应开设油槽,内存润滑剂,以减小导柱导向的摩擦。
若导柱需要支撑模板的重量,特别对于大型、精密的模具,导柱的直径需要进行强度校核[11]。
设计导柱和导套需要注意的事项有:
(1)导柱的直径应根据模具大小而决定。
(2)合理布置导柱的位置,导柱中心至模具外缘至少应有一个导柱直径的厚度;
导柱不应设在矩形模具四角的危险断面上。
通常设在长边离中心线的1/3处最为安全。
导柱布置方式常采用等径不对称布置,或不等直径对称布置。
(3)导柱设在动模一侧可以保护型芯不受损伤,而设在定模一侧则便于顺利脱模取出塑件。
(4)导柱工作部分长度应比型芯端面高出6~8mm,以确保其导向与引导作用。
(5)导柱工作部分的配合精度采用H7/f7,低精度时可采取更低的配合要求;
导柱固定部分配合精度采用H7/k6;
导套外径的配合精度采取H7/k6。
配合长度通常取配合直径的1.5~2倍,其余部分可以扩孔,以减小摩擦,降低加工难度。
(6)导柱可以设置在定模或动模,设在动模一边可以保护型芯不受损坏,设在定模一边有利于塑件脱模。
(7)一般导柱滑动部分的配合形式按H8/f8,导柱和导套固定部分配合按H7/k6,导套外径的配合按H7/k6。
(8)除了动模、定模之间设导柱、导套外,一般还在动模座板与推板之间设置导柱和导套。
六.注射成型原理及工艺特性
6.1注射成型原理
注射成型是塑料成型的一种重要方法,它主要适应热塑性塑料的成型。
注射成型的特点是:
成型周期短,能一次成型形状复杂、、尺寸精确、带有金属或非金属嵌件的塑件注射成型的生产效率高,易实现自动化生产除氟塑料以外,几乎所有的热额素性塑料都可以用注射成型的方法成型。
6.1.1柱塞式注射机注射成型
柱塞注射机的结构主要由柱塞式塑化装置、开合模机构和电器液压控制系统三大部分组成。
首先塑料原料被加入到注射机的料斗中,经过料筒外的加热器加热,塑料变为粘流态,然后注射机工作室模具合模,塑化的塑料注入模具型腔,充满模具型腔的塑料熔体在受压力的情况下经冷却固化而保持模具型腔所赋予的形状。
最后,柱塞复位,开合模机构带动模具的动模打开模具,在推出机构的作用下,注射成型的塑料制件被推出膜外。
如此完成注射的一个成型周期。
6.1.2螺杆式注射机注射成型
将颗粒状或粉状塑料加入到外部安装有电加热圈的料筒内,在螺杆的作用下,边塑化边向前移动,在螺杆的作用下,欲塑化的塑料向前移动;
螺杆的转动使塑料进一步塑化,料温在剪切摩擦热的作用下进一步提高,塑料得以均匀塑化,随着螺杆的进一步推进,塑料熔体开始注模,充满模具型腔的塑料熔体在受压力的情况下经冷却固化而保持模具型腔所赋予的形状。
如此完成注射的一个成型周期
6.2注射成型工艺参数
正确的注射成型工艺过程可以保证塑料熔体良