BP墨西哥湾事故分析报告Word格式.docx
《BP墨西哥湾事故分析报告Word格式.docx》由会员分享,可在线阅读,更多相关《BP墨西哥湾事故分析报告Word格式.docx(8页珍藏版)》请在冰豆网上搜索。
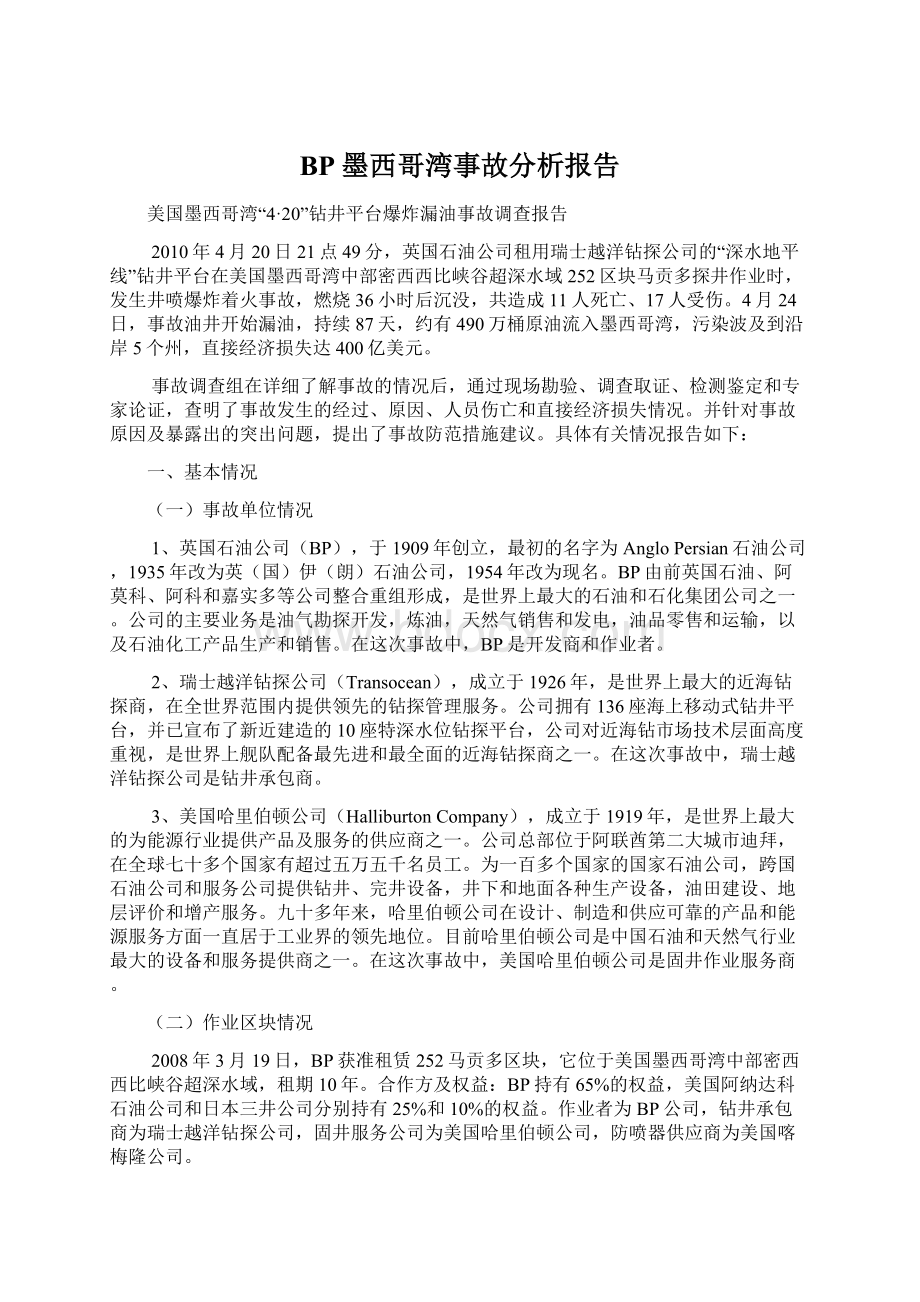
目前哈里伯顿公司是中国石油和天然气行业最大的设备和服务提供商之一。
在这次事故中,美国哈里伯顿公司是固井作业服务商。
(二)作业区块情况
2008年3月19日,BP获准租赁252马贡多区块,它位于美国墨西哥湾中部密西西比峡谷超深水域,租期10年。
合作方及权益:
BP持有65%的权益,美国阿纳达科石油公司和日本三井公司分别持有25%和10%的权益。
作业者为BP公司,钻井承包商为瑞士越洋钻探公司,固井服务公司为美国哈里伯顿公司,防喷器供应商为美国喀梅隆公司。
(三)钻井平台情况
“深水地平线”钻井平台是第五代动力定位深水半潜式钻井平台,韩国现代重工于2001年建成。
尺寸为121米×
78米,定员130人,实际126人(其中,瑞士越洋钻探公司79人,BP公司6人,美国哈里伯顿公司41人),造价为7亿美元,工作吃水深度23米,型深41米,隔水管外径21英寸,最大作业水深为2438米,额定钻深能力9100米。
平台重量32588吨,排水量52587吨,甲板最大可变载荷8202吨。
定位方式为DP-3动力定位,DP-3系统有8个推进器,最大航速4节(7.41公里/小时)。
(四)钻井情况
马贡多井号为MC252#-01,井别属于探井,井型为直井。
设计井深20000英尺/6096米,实际井深18360英尺/5596米,作业水深5067英尺/1544米。
井身结构有9层套管,分别是:
1、36″导管下至1622米,固井水泥返至海床面;
2、28″表层套管下至1912米,水泥返至海床面;
3、22″技术套管下至2421米,水泥未返至上层28″表层套管内;
4、18″技术套管下至2736米,水泥未返至上层22″技术套管内;
5、16″技术尾管下至3533米,水泥未返至上层18″技术套管内;
6、135/8″技术尾管下至4009米,水泥未返至上层16″技术尾管内;
7、117/8″技术尾管下至4606米,水泥未返至上层135/8″技术尾管内;
8、97/8″技术尾管下至5236米,水泥未返至上层117/8″技术尾管内;
9、97/8″+7″复合生产套管下至5596米,水泥未返至上层97/8″技术尾管内。
该井配套的水下防喷器为美国喀麦隆公司生产,最大工作压力15000psi(103Mpa)。
配有一个双闸板、两个单闸板。
两个单闸板中,一个为剪切闸板,一个为变径闸板。
二、事故发生经过及应急处置情况
(一)、井喷导致爆炸及漏油过程
4月19日,97/8″+7″复合套管下至5596米(18360英尺),固井后坐密封总成,候凝16.5小时,正向试压证实井内套管抗压合格,然后负压测试检查井底固井作业的完整性,尽管两次负压测试数据异常,但BP现场负责人草率地做出了“合格”的结论。
4月20日,计划在井深2454米处(8049英尺)打水泥塞,然后临时弃井,换上生产平台作业。
BP公司决定采用“先用海水替完井液,再打水泥塞临时弃井”的方案。
候凝16.5小时后,下钻至2454米(8049英尺)处,用海水顶替完井泥浆。
4月20日20:
00,开始用海水替泥浆。
20:
08,出口返出泥浆,此时泵入量3.6m³
。
这些数据印证了该井存在井漏。
25,隔水管返出流量明显大于泵入量,显现溢流征兆。
52,降低泵入排量,出口流量在2.23-2.73m³
/min间波动,溢流明显。
58,继续降低泵入排量,出口流量3.6m³
/min,溢流加重。
21:
08,停泵观察。
立压为1.0kpsi。
出口流量0.45m³
/min,在此过程中,立压逐步由1.0kpsi上升到1.5kpsi。
14,重新开泵循环,进口流量1.82m³
/min,返出泥浆绕过流量计直接排海。
立压逐步上升到1.75kpsi。
18,停泵。
立压下降为1.4kpsi。
20,开泵循环。
立压由1.5kpsi上升为2.52kpsi,泵入排量3.2m³
/min,出口无泥浆返出。
29,停泵。
立压下降为1.25kpsi后,在6分钟内上升为1.75kpsi,之后直线下降为0.6kpsi,接着上升为1.49kpsi后,又下降为0.4kpsi。
此过程中,出口无泥浆返出。
42,立压由0.4kpsi上升为1.3kpsi。
然后突然出现激烈直线上升。
进出口流量依然几乎为零。
21:
49,立压已直线猛增到35.7Mpa,出口流量猛增到8.2m³
/min,发生强烈井喷,天然气从井口喷出后,发生爆炸,共造成11人死亡、17人受伤。
爆炸发生36小时后,“深水地平线”钻井平台沉入墨西哥湾。
底部油井自4月24日起开始漏油不止,漏油量从5000桶/天上升到30000桶/天,持续87天,约有490万桶原油流入墨西哥湾。
(二)、应急处置情况
1、成立应急指挥机构
事故发生后,BP公司快速在休斯敦设立了一个大型事故指挥中心。
从160家石油公司调集了500人参与其中,成立联络处、信息发布、油污清理、井喷事故处理、专家技术组等相关机构,并与美国当地政府积极配合,寻求支援。
2、清理油污
主要措施有围堵清理、化学制剂分散法、襒油法、可控燃烧法、收集法、打井救援等。
共动用4.7万人,7000多艘船,十几架飞机,使用了400多万米围油栏和700多万升分散剂等,在沿岸建立了72公里的沙护堤。
3、聘请道达尔、埃克森等公司专家制定井喷漏油治理措施
①设法启动水下防喷器关井
4月26日出动多台水下机器人(ROV),尝试关闭水下防喷器来实现关井,没有成功。
②安装控油罩控油
5月7日,BP工程师将一个重达125吨的大型钢筋水泥控油罩沉入海底,希望用它罩住漏油点,将原油疏导到海面的油轮。
但由于泄漏点喷出的天然气遇到冷水形成甲烷结晶,堵住了控油罩顶部的开口,使得这一装置无法发挥作用。
随后又用小一号的钢筋水泥罩,可减少甲烷结晶的形成,但这个方法同样失败。
③安装吸油管回收部分原油
5月14日,BP尝试在海底漏油口安装类似虹吸管的装置进行吸油。
在约1600米深处,利用水下机器人成功将吸油装置下端连接到海底吸油管,上端连接到一艘油轮,每天可回收约3000桶漏油。
④顶部压井法
5月26日,BP启用顶部压井法,从井眼顶部向破损油井注入重钻井液和水泥,试图封堵漏油井,但未能取得成功。
⑤切管盖帽法
6月3-4日,BP利用水下机器人切除防喷器上端隔水管,并在漏油点上方成功安放一个漏斗状装置,将部分漏油引流到钻井船上。
实施切管盖帽法的第一天,共收集6000桶原油。
6月22日收集了1.66万桶泄露的原油。
7月12日,又成功更换一个新的、可以完全封堵井口的控油罩。
7月15日,BP首次宣布不再有漏油流入海洋。
⑥实施静态压井法封住油井
8月5日,BP采用静态压井法,连续8小时内向油井顶部灌注超过2000桶的压井泥浆,成功实现井筒压力平衡,产生了比较明显的效果,基本封堵了油井。
⑦依靠救援井实施彻底封堵
9月16日在井底97/8″套管处实现救援井与事故井联通。
9月17日通过救援井向事故井灌注水泥。
9月19日压力测试后,BP宣布漏油井被彻底封死。
三、事故原因
(一)直接原因
施工固井的质量不合格,当井底压力发生剧烈的变化时,这会产生极大的压力并突破了钻井的密封,从而造成瞬间井喷。
发生井喷后,海底的天然气和原油沿着管道冒上来,混合易燃易爆气体四处扩散,当这些气体进入引擎室后,发生了第一起爆炸,随后发生了一系列地爆炸,造成钻井平台严重地原油泄露,同时点燃了部分冒上来的原油。
原因分析:
通过调查组在现场勘验、物证检测、调查询问、查阅资料,并经综合分析后认定:
原本完井套管串设计计划采用“7″尾管悬挂固井和97/8″套管回接固井”设计方案,可提供四道密封防护(井底固井密封、所下尾管的悬挂器部位密封、尾管悬挂处的固井密封、井口密封总成密封)。
但为了节约资金和工期,BP墨西哥湾深水勘探的项目经理在施工前将完井方案调整为“97/8″和7″符合套管串”,一次下到井底,变更后的方案只能提供井底固井和井口密封总成两道密封。
海底底层压力梯度复杂并且泥浆密度窗口极窄,在固井质量不合格的情况下,增加了发生事故的风险,最后造成了上喷下漏,并导致了这次爆炸和泄露事故。
(二)间接原因
1、施工过程多个环节存在漏洞
该钻井属于低地温梯度井,使用充氮气水泥浆体系存在产生超缓凝现象的潜在风险。
水泥候凝仅为16.5小时,用海水顶替井筒泥浆,压力失衡,最后油气突破尚未胶结水泥,引发单流阀损坏。
另外,固井过程中存在违章作业,没有按要求充分地循环泥浆,导致井底含油气的钻井液上行至海底防喷器的上部,这样增加了导致溢流井喷的风险。
2、装备管理和维护有缺陷
井口密封总成安装完成后,现场施工组未按技术规程的要求在密封总成中安装锁止滑套,这使得使密封系统留下缺陷。
另外,在险情发生后,应急模式下的紧急切断程序(ESD)、自动模式功能(AMF)和遥控水下机器人干预等3套关井系统先后失灵失效。
事故后,在对水下防喷器的两个控制模块进行检查时,发现一个控制模块电池没电。
同时,钻井采用的自灌式套管浮箍销钉存在质量问题,设计剪切压力为3.5-4.9Mpa,但实际经过9次剪切,压力达到21.2Mpa后才剪断。
3、现场生产组织决策上出现一系列重大失误
在钻井固井候凝后,固井胶结质量检测的工作临时被取消,并且在负压测试数据异常地情况下现场负责人竟然草率地做出了合格的结论;
对固井后的井控风险缺乏足够的认识,现场采取了“先替海水,后打水泥塞”的错误程序;
现场发生溢流迹象时,没有引起足够重视,未能及时采取压井措施,导致险情的进一步恶化;
当大量油气进入隔水管后,没有考虑超出液气分离器处理能力的应急措施,却直接把流体引入了分离器,造成了大量油气在钻井平台上迅速扩散;
管理及作业人员在思想上均处于高度松懈状态,对现场生产过程失去了有效监控。
4、政府缺乏监管
从有关的报告了解,负责出租钻井平台的矿产管理局的监管人员存在玩忽职守的行为,对有关安全警告置若罔闻,私自收受被监管公司的礼物。
另外,还有活动报告表明,这个管理局曾经允许被监管的石油公司用铅笔自行填写现场的检查报告。
(三)事故性质
经调查认定,美国墨西哥湾“4·
20”钻井平台爆炸漏油事故是一起生产安全责任事故。
四、对事故有关责任人员及责任单位的处理建议
(一)司法机关处理建议
1、该钻井平台BP项目经理为节约成本和工期在施工前擅自调整完井方案,使得密封强度降低,应移交司法机关依法独立开展调查。
2、该钻井平台施工固井过程相关负责人违章作业,没有按要求充分循环泥浆,应移交司法机关依法独立开展调查。
3、该钻井平台负压测试数据现场负责人在负压测试数据异常情况下,却草率作出合格的结论,应移交司法机关依法独立开展调查。
4、该钻井平台设备管理和维护相关负责人未尽职尽责,设备存在质量不合格以及保养不完善,应移交司法机关依法独立开展调查。
5、该钻井平台液气分离器应急措施的相关负责人未能正确采取有效措施,导致险情进一步恶化,应移交司法机关依法独立开展调查。
6、该钻井平台相关管理和作业人员思想上高度松懈,未能对现场进行有效监控,应移交司法机关依法独立开展调查。
7、该钻井平台的相关政府监管人员玩忽职守,对有关监管不到位,没有进行提前警示,应移交司法机关依法独立开展调查。
8、该钻井平台相关设备和技术提供商的产品和服务存在缺陷,司法机关应依法独立对其开展调查。
(二)相关行政处罚及问责建议
1、依据《石油污染法》、《清洁水法》、《综合环境相应补偿与责任法》等有关法律的规定,应对BP公司处以相应的罚款。
对BP公司CEO和安全主管处以相应的罚款。
2、建议BP公司、瑞士越洋钻探公司、美国哈里伯顿公司作出深刻检查,并抄送至上级相关监管部门;
责成负责监管该钻井平台的矿产管理局想上级政府作出深刻检查。
五、事故防范措施建议
(一)控制成本要以满足安全环保基本要求为底线
本次事故中,MC252井是一口日费井,因台风耽误43天工期,钻机租费至少增加2100万美元,加之该井已获得重大勘探发现,为了节约费用,加快进度,公司在多个生产环节采用了多项省钱、省时、赶工期的不科学方案。
最后酿成了这次严重事故,结果得不偿失。
因此,我们要牢固树立科学发展、安全发展理念,牢牢坚守“发展决不能以牺牲人的生命为代价”这条底线。
坚持管行业必须管安全、管业务必须管安全、管生产经营必须管安全的原则,把安全责任落实到领导、部门和岗位,谁踩底线谁就要承担后果和责任。
所有工程设计必须满足安全规定和条件。
要坚决纠正单纯以经济增长速度评定政绩的倾向,科学合理设定安全生产指标体系,加大安全生产指标考核权重。
(二)加强内部管理,深入隐患排查
事故发生前,BP忽略了大量关键性的安全预防措施。
一些例行检查、监管流于形式,过于依赖自动化仪器设备,对公司的处置能力过于自信,尤其是对一个已经连续7年安全无事故的钻井平台来说,管理者、操作者都在一定程度上存在麻痹大意思想。
因此,要加强内部管理,内部例行检查、监管要落实到位,不要过于依赖设备,对安全问题要时刻放在心上,不能麻痹大意。
同时要建立健全隐患排查治理制度,落实企业主要负责人的隐患排查治理第一责任,实行谁检查、谁签字、谁负责,做到不打折扣、不留死角、不走过场。
(三)加强外部监督,保障安全运行
应加强外部相关政府监督管理力度,认真履行有关监督责任的相关职责,各级政府要加强相关保护监督工作的领导,督促、检查有关部门依法履行相关保护职责,组织排查重大外部安全隐患。
在出现问题时,要及时与企业进行沟通会商,制定并落实相关具体的完善措施。
相关安全监管部门要配备专业人员,加强监管力量,要充分发挥组织协调作用,对不符合安全环保要求的立即进行整治,对自查自纠等不落实的企业要及时警告。
(四)须对承包商监管像对待内部单位一样强化集中统一管理
这次事故中,BP本身是开发商和作业者,瑞士越洋钻探公司是钻井承包商,美国哈里伯顿公司是固井作业服务商,水下井口防喷器由美国喀梅隆公司提供。
尽管项目各方的合作关系比较成熟规范,但毕竟存在着信息不对称和管理风格、文化差异,加之BP的监督现场决策出现问题,结果造成连环失误、多道防护屏障失守,事后又相互推卸责任。
因此,在任何作业过程中,承包商监管是安全管理的重要组成部分,必须像对待内部单位一样强化集中统一管理,要实现相关信息共享,做到尽量同步。
(五)切实重视应急管理能力建设
各级领导干部要带头熟悉、掌握应急预案内容和现场救援指挥的必备知识,提高应急指挥能力;
接到事故报告后,基层领导干部必须第一时间赶到事故现场。
企业要根据工作危险特性,制定有针对性的专项应急预案和现场处置方案,并定期组织演练,检验预案的实用性、可操作性,不能“一定了之”、“一发了之”;
要加强应急队伍建设,提高人员专业素质,配套完善安全检测及安全预警等应急装备。
同时技术物资储备要充分,能够实现在较短的时间内实施一系列解决方案及技术措施,总体上有条不紊。
必须高度重视应急管理能力建设,突出加强工程抢险技术研究及能力建设,尤其是各种堵漏清污技术,加大区域性的应急物资储备,共同应对突发事故。
美国墨西哥湾“4·
20”钻井平台爆炸漏油事故调查组
注:
此次事故对我国相关安全工作的意义
目前,我国近海石油开采正处在较高活动水平,仅在渤海湾就有4000多个钻井平台,而且最近几年开始在深海进行钻探。
同时,我国还是一个石油进口大国,进口石油的90%都要依赖海上运输。
所以在我国海上石油开发和运输过程中,都存在发生大规模石油泄漏事故的风险,并且最近几年风险有上升趋势。
但是,我国海上溢油处理能力严重不足,主要体现在:
海洋污染应急组织体系不完善,未能形成合力;
应急处置能力不足,技术装备落后;
物资储备匮乏,处置技术科技含量低。
因此,针对BP此次事故,我们要分析、挖掘海洋开采工程技术方面的经验教训,强化风险分析与管控,强化设施完整性管理和工艺安全分析,不断提升技术、工艺、装备及管理水平。
同时应重新评估海上设计标准,加大隐患排查力度,强化风险管理,加强作业者与承包商沟通,加强员工培训,包括承包商员工,强化设计变更管理,设置多道安全屏障,实现零事故。
此外,要完善海和健全洋污染应急组织体系,加强应急处置能力,提高技术装备质量,加大物资储备。
这样在海洋开采中,无论是事故前预防,事故中处理或是事故后救援都能形成强有力的应对能力。