机械工艺夹具毕业设计144减震支架加工工艺编制实体加工仿真及夹具设计Word文档下载推荐.docx
《机械工艺夹具毕业设计144减震支架加工工艺编制实体加工仿真及夹具设计Word文档下载推荐.docx》由会员分享,可在线阅读,更多相关《机械工艺夹具毕业设计144减震支架加工工艺编制实体加工仿真及夹具设计Word文档下载推荐.docx(31页珍藏版)》请在冰豆网上搜索。
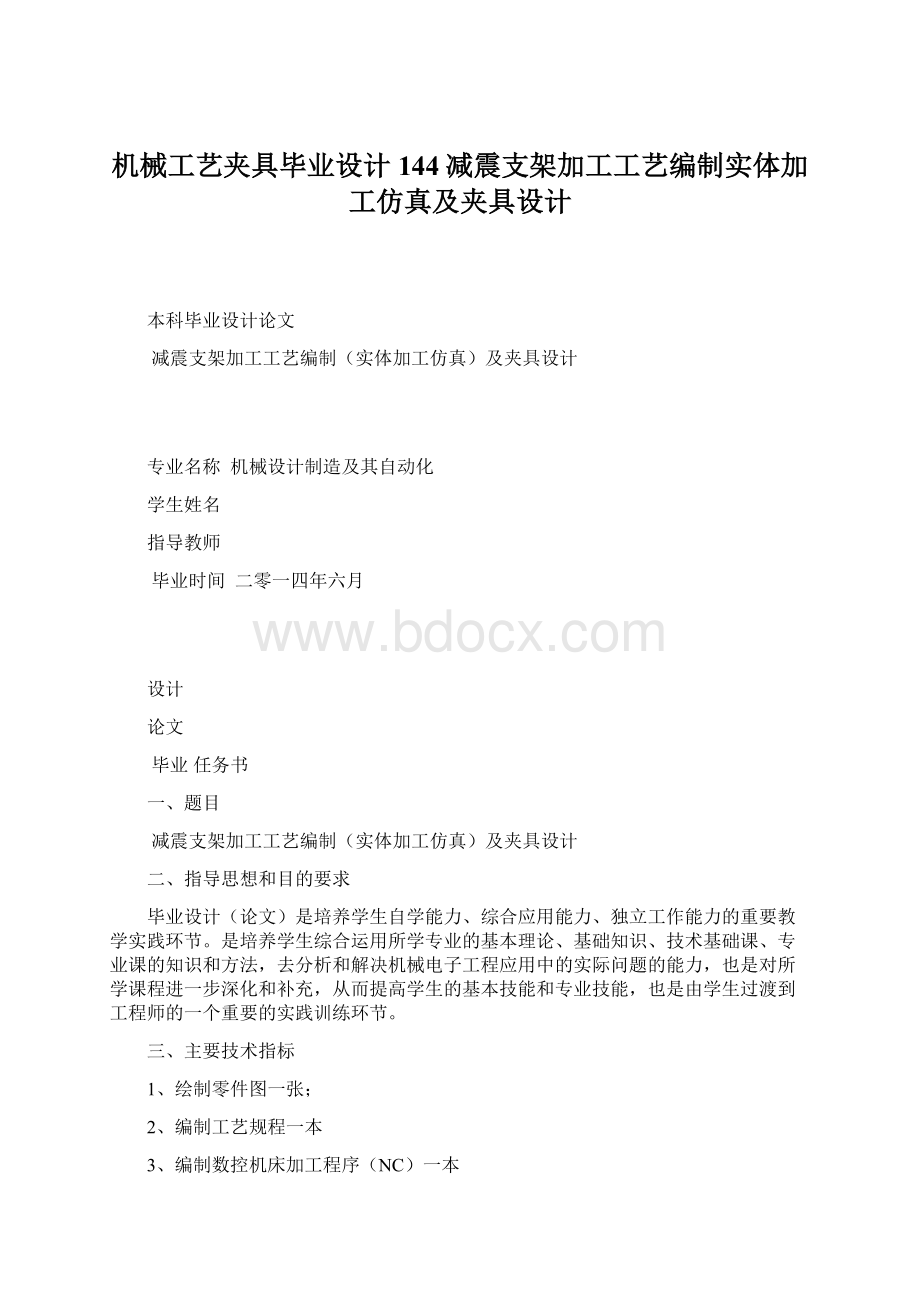
3、《实用机械制造工艺师手册》王凡主编机械工业出版社
摘要
减震器主要用来抑制弹簧吸震后反弹时的震荡及来自路面的冲击。
在经过不平路面时,虽然吸震弹簧可以过滤路面的震动,但弹簧自身还会有往复运动,而减震器就是用来抑制这种弹簧跳跃的。
支架起支撑作用的构架。
减震支架保护内装的零部件不因外部的冲击震动导致其损坏。
机械制造过程中用来固定加工对象,使之占有正确的位置,以接受施工或检测的装置,又称卡具。
从广义上说,在工艺过程中的任何工序,用来迅速、方便、安全地安装工件的装置,都可称为夹具。
在机床上加工工件时,为使工件的表面能达到图纸规定的尺寸、几何形状以及与其他表面的相互位置精度等技术要求,加工前必须将工件装好(定位)、夹牢(夹紧)。
夹具通常由定位元件、夹紧装置、对刀引导元件、分度装置、连接元件以及夹具体(夹具底座)等组成。
利用模型复现实际系统中发生的本质过程,并通过对系统模型的实验来研究存在的或设计中的系统,又称模拟。
当所研究的系统造价昂贵、实验的危险性大或需要很长的时间才能了解系统参数变化所引起的后果时,仿真是一种特别有效的研究手段。
仿真的重要工具是计算机。
仿真与数值计算、求解方法的区别在于它首先是一种实验技术。
仿真的过程包括建立仿真模型和进行仿真实验两个主要步骤。
关键词:
减震支架夹具仿真
ABSTRACT
Mainlyusedtosuppressthevibrationdamperafterareboundduringthespringandshock-absorbingimpactfromtheroad.Afteraroughroadwhen,althoughshock-absorbingspringcanfiltertheroadshock,buttherewillbeareciprocatingmovementofthespringitself,andthedamperspringisusedtosuppresssuchjumping.Bracketplayasupportiveroleinthearchitecture.Built-inshockabsorberbracketpartsprotectionduetoexternalshockandvibrationwithoutcausingdamage.
Mechanicalmanufacturingprocessforfixingtheobject,sothatoccupiesthecorrectpositiontoreceivethedetectingmeansortheconstruction,alsoknownfixtures.Broadlyspeaking,anystepintheprocess,usedquickly,easilyandsafelyinstallthedeviceworkpiececanbecalledafixture.Whentheworkpieceonthemachine,inordertomakethesurfaceoftheworkpiececanreachthesizeofthedrawingrequirements,andthemutualpositionofthegeometryprecisiontechnicalrequirementsandothersurfaces,theworkpiecemustbeinstalledpriortoprocessing(positioning),clipprison(clamping).Fixtureusuallyconsistsofapositioningelement,clampingdevice,theknifeguideelements,indexingdevice,connectingelementsandspecificfolder(clampbase)andothercomponents.
Thenatureofthemodelusingthereproductionprocessoccursintheactualsystemandthemodelofthesystemthroughtheexperimentaldesigntoinvestigatethepresenceorsystem,alsoknownassimulation.Whenthesystemunderstudyisexpensive,largeordangerousexperimenttakesalongtimetounderstandtheconsequencescausedbychangesinsystemparameters,simulationisaparticularlyeffectivemeansofresearch.Computersimulationisanimportanttool.Simulationandnumericalcalculation,thedifferencebetweensolvingapproachisthatitisanexperimentaltechniquefirst.Thesimulationprocessincludingtheestablishmentofasimulationmodelandsimulationexperimentsoftwomainsteps.
Keywords:
shockbracketfixturesimulator
第1章绪论
1.1课题背景
减震器从出现到今天已经有了100多年的历史,最早车辆的减震系统由弹簧构成,虽然弹簧可以减轻路面冲击,性能较可靠,但它容易产生共振现象。
在1908连,世界第一台液压减震器研制成功,它用隔板将橡胶制成节流通道分为两部分,通过油液与节流通道摩擦,达到减震目的。
之后,在20世纪30年代,摇臂式减震器得打哦普遍应用,工作压力在10MPa~20MPa之间,但是结构复杂、易损坏、体积大,最终被淘汰。
二战后,简式液压减震器取代了摇臂式减震器,其成本低,寿命成,但是容易出现充油不及时的问题,若充油不及时,会影响减震效果,产生噪音与冲击。
直到20世纪50年代,充气式减震器的出现解决了以上的问题,在双筒内充入低压0.4MPa~0.6MPa的氮气可以解决充油不及时的问题。
同时单筒式充气减震器也开始发展,其采用浮动活塞的结构,使充入的氮气形成2.0MPa~2.5MPa的高压气体,性能优于双筒式减震器,而且质量轻、性能好,但其成本较高。
在国外发达国家,现在已经研制出由电子系统操控的自适应式液压减震器,根据激振频率与振幅的大小来调节。
在工业发达的国家,液压减震器的生产是建立在广泛的标准化和系列化基础上的,并且其减震CAD设计制造技术已经比较成熟。
我国减震器起步晚,起点低,技术落后。
研制开发出自主品牌的减震器已经成为一个亟待解决的问题。
尽管我国已有较大的减震器生产规模,借鉴了国外先进设计,已经取得了较快发展,但是与发达国家仍然存在较大的差距。
1.2设计目的和意义
作为减震器中的减震支架起到保护内装的零部件不因外部的冲击、震动导致其损坏的目的。
可以看出减震支架在减震器中的重要地位。
完成毕业设计任务和撰写论文,培养了学生综合分析和解决问题的能力和独立工作能力、组织管理和社交能力;
同时,对学生的思想品德,工作态度及作风等诸方面都会有很大影响。
对于增强事业心和责任感,提高毕业生全面素质具有重要意义。
是学生在校期间的学习和综合训练阶段;
是学习深化、拓宽、综合运用所学知识的重要过程;
是学生学习、研究与实践成果的全面总结;
是学生综合素质与工程实践能力培养效果的全面检验;
是实现学生从学校学习到岗位工作的过渡环节;
是学生毕业及学位资格认定的重要依据。
第二章减震支架零件结构与工艺分析
2.1机械加工工艺要求
机械加工工艺是机械产品质量的根本保证。
零件的质量包括零件加工的尺寸精度和表面质量等。
加工精度是指零件的实际几何参数对理想几何参数的符合程度,符合程度越高,加工精度则越高。
在一定加工设备的前提下,制定合理的机械加工工艺,可以提高零件加工精度,降低废品率,提高劳动生产率。
对于同一种零件,不同的工艺人员制定的工艺路线也不尽相同。
工艺人员应当在多个加工路线中寻找一个较好的方案,以最短的工序和最少的投入加工出合格的零件。
1、编制机械加工工艺的基本要求
(1)机械加工工艺应按统一的技术术语和格式进行编制,内容、文字应简洁易懂、准确无误。
(2)编制加工工艺时,要根据零件结构特点、精度要求、毛坯状况、零件质量等条件,选择相应的加工设备。
比如对于大型零件,尤其是铸锻件,应首先估算零件毛坯质量,以免超出起重设备或机床额定负荷,影响生产安全。
(3)若需用工装时,应首先考虑采用标准工装及现有专用工装,尽量减少采用新设计专用工装。
对批量大的零件应设计专用工装,以提高生产效率。
2、加工阶段的划分
零件的加工是一个由粗到精的过程,需通过若干工序的加工逐步达到质量要求。
对加工精度要求较高的零件,加工过程可划分为粗加工、半精加工和精加工等阶段。
各加工阶段的基本要求如下。
(1)粗加工阶段。
去除毛坯黑皮和大部分加工余量,为后序加工提供精准基面,并留均匀而合适的余量。
(2)半精加工阶段。
提高精加工所需要的定位基准的精确性和控制精加工余量,为主要表面的精加工创造条件。
(3)精加工阶段。
进一步改善精度和表面粗糙度等要求较高的表面,使零件的各项参数达到技术要求。
制订工艺路线的出发点,应当是使零件的几何形状、尺寸精度及位置精度等技术要求能得到合理的保证。
根据以上加工工艺的要求,本文通过对减震支架的结构进行分析来确定其加工工艺。
2.2减震支架结构分析
如图2-1所示为减震支架的零件图。
由图可知减震支架为一圆柱形壳体零件,减震支架是用来保护其内装的零部件不因外部的冲击、震动导致损坏。
整体尺寸为直径Φ158高80,材质为45#钢。
主要技术要求有热处理、表面处理和孔的位置精度。
通过对零件图的仔细审读,该零件上表面分布有众多孔,其圆柱外表面分布均匀的槽,底部有型腔并有孔分布。
由此可知该零件结构相对复杂,外形加工部位多,加工难度较大,在加工孔的过程中容易产生偏差,难以保证加工精度和表面质量。
图2-1减震支架零件图
2.3减震支架加工工艺分析
通过对减震支架零件的结构分析,现在对其加工工艺进行分析。
2.3.1基准面的选择
正确的选择定位基准是设计工艺的一项重要内容,也是保证加工精度的关键。
定位基准分为精基准与粗基准
1.粗基准的选择原则
粗基准影响:
位置精度和各加工表面的余量大小。
对于一般轴类零件而言,以外圆为粗基准是完全合理的。
按照有关的粗基准选择原则(保证某重要表面的加工余量均匀时,选该表面为粗基准。
若工件每个都要求加工,为了保证各表面都有足够的余量,应选择加工余量最小的表面为粗基准。
)
重点考虑:
如何保证各加工表面有足够的余量,使不加工表面和加工表面间的尺寸和位置符合零件图要求。
⑴合理加工余量的原则
⑵保证零件加工表面相对于不加工表面具有一定位置精度的原则
⑶便于装夹的原则:
选表面光洁的平面做粗基准,以保证定位准确 夹紧可靠。
⑷粗基准一般不得重复使用的原则:
在同一尺寸方向上粗基准通常只允许使用一次,这是因为粗基准一般都很粗糙,重复使用同一粗基准所加工的两组表面之间位置误差会相当大,因此,粗基一般不得重复使用。
在本文减震支架加工过程中,根据粗基准选择原则,选取零件外圆为粗基准。
2.精基准的选择
如何较小误差,提高定位精度。
基准重合原则:
利用设计基准做为定位基准,即为基准重合原则。
基准统一原则:
在大多数工序中,都是用同一基准的原则。
互为基准原则:
加工表面和定位表面互相转换的原则。
自为基准原则:
以加工表面自身做为定位基准的原则。
基准不重合误差最小条件:
因基准不重合而引起的最小的表面作为定位基准。
2.3.2减震支架的加工概括
在工艺研究中,采用车削加工外形和内部型腔,钻、铣、镗来加工零件上的孔,低温去应力退火的热处理方式以及采用定位工装等工艺方法,减小零件在加工过程中的变形和位置精度偏差的问题,从而提高了零件的加工精度和表面质量。
在划分了加工阶段后安排零件的机械加工工序。
安排零件表面的加工顺序如下:
1、本文减震支架零件加工顺序先主后次。
根据零件的功用(可从装配图上知道)和技术要求,分清零件的主要表面和次要表面。
主要表面系指装配基准面、重要工作表面和精度要求较高的表面等;
次要表面是指光孔、螺孔、未标注公差表面及其他非工作表面等。
分清零件的主、次要表面后,重点考虑主要表面的加工顺序,以确保主要表面的最终加工。
按照先主后次的原则。
安排机械加工工序的一般顺序是:
加工精基准面--粗加工主要表面--半精加工主要表面--精加工主要表面--光整加工--超精密加工主要表面。
次要表面的加工安排在各阶段之间进行。
2、本文减震支架零件应先加工出选定的后续工序的精基准,如外圆、内孔、中心孔等。
如在加工轴类零件时,应先钻中心孔;
加工盘套类零件时,应先加工外圆与端面。
3、先粗后精在加工工件时,一般先粗加工,再进行半精加工和精加工。
本文减震支架零件先粗车外圆,后进行精车保证尺寸。
4、先面后孔为了保证加工孔的稳定可靠性,应先加工孔的端面,后加工孔。
如本文减震支架零件,应先加工端面后加工孔。
这是因为端面的轮廓平稳,定位、装夹稳定可靠。
先加工好孔端平面,再以端面定位加工孔,便于保证端面与孔的位置精度。
此外,由于平面加工好后再加工孔时,可使刀具的初始工作条件得到改善。
第三章减震支架加工工艺路线
3.1减震支架加工工艺路线的拟定
该零件毛坯选用圆柱棒料,采用粗加工、精加工的工艺方案。
整体工序过程如下
01粗车外形
粗加工主要是去除大余量,并为后序精加工打好基础,该工序要求按所示零件图粗车外圆、端面、内孔,刀具为车刀,钻φ12的孔。
结束后用游标卡尺进行检验。
第一工步车外圆、车端面。
保证Φ161±
0.5和82±
0.5。
(图3-1)
第二工步车内孔。
保证Φ112.5±
0.2和54.8。
(图3-2)
第三工步钻孔。
钻Φ12的孔。
(图3-3)
图3-1车外圆和端面图3-2车内孔图3-3钻孔
02车外形
第一工步车外圆,车端面,保证尺寸83。
图3-3粗车外形、顶孔
03热处理
粗加工后材料组织会有应力或其他缺陷,通过热处理可以消除这些缺陷,保证材料性能,所以本文把热处理安排在粗加工之后精加工之前。
按热处理工艺规程处理零件,使HRC18~22。
04精加工外形
第一工步如图3-4车端面见光保证尺寸φ160±
0.1;
70±
图3-4车端面
05车外圆、端面、车型腔、铣孔
第一工步车外圆,车端面保证尺寸φ159;
71.5±
0.2;
81.5±
0.1。
(图3-5)
第二工步加工φ130深4的型腔起固定作用,为了后续加工定位方便。
(图3-6)
第三工步车型腔54.8,φ115.5,保证圆角R0.5;
R1。
(图3-7)
第四工步用铣刀加工φ18,深19.2的孔。
(图3-8)
图3-5车外圆和端面图3-6加工型腔图3-7车型腔
图3-8铣孔
06车外圆、车端面、车孔、车台阶圆
第一工步车外圆车端面保证尺寸φ158.5;
80±
0.05。
(图3-9)
第二工步车φ14的的孔。
(图3-10)
第三工步车台阶圆,保证φ142±
0.05;
8;
13。
(图3-11)
图3-9车外圆和端面图3-10车孔图3-11车台阶圆
此工序结束后需用游标卡尺进行检验以保证各尺寸公差符合图纸要求。
07车外表面凹槽
第一工步加工5.5±
0.07;
6.5±
4×
4.5±
10.5±
0.07的凹槽此时因为零件一端开口,为了提高精度使用φ130的定位板和顶尖。
加工结束需要进行尺寸检验以保证精度要求。
(图3-12)
图3-12车外槽
零件后续工艺在加工中心中完成。
08钻孔、铣缺口
第一工步预点所有孔的中心孔,以Φ115.5的孔为定位基准。
(图3-13)
第二工步选取φ12钻头刀具钻5×
Φ12底孔。
(图3-14)
第三工步选用φ3.3钻头钻4×
M4底孔,后用φ3.3样柱进行测量。
(图3-15)
图3-13预点中心孔图3-14钻Φ12孔图3-15钻M4孔
第四工步选用φ5.5,φ7.5钻头钻φ6,φ8的底孔,后用游标卡尺检验钻孔尺寸。
(图3-16)
第五工步选用φ12的铣刀在原来φ12孔基础上铣出2×
φ23,3×
φ15.5的底孔,后用游标卡尺进行尺寸检验。
(图3-17)
第六工步选用合适镗刀镗φ6,φ8底孔,同时保证45°
偏角,完成后用样柱和三坐标对其进行检验(图3-18)
图3-16钻孔图3-17铣孔图3-18镗孔
第七工步选用φ12的加长铣刀铣外圆的4处缺口,加工结束用R规量具检验尺寸8×
R5和8×
R11。
(图3-19)。
图3-19铣缺口
09钻孔
第一工步将零件翻面,用压板压紧,用中心钻钻5×
M3,2×
φ4的中心孔。
(图3-20)
第二工步选用φ2.5的钻头钻φ2.5的孔。
(图3-21)
第三工步选用φ3.5刀具钻、镗2×
φ4的孔,后用φ4样柱和三坐标测量仪检验保证φ153±
0.02尺寸和45°
角度要求(图3-22)。
图3-20钻中心孔图3-21钻孔图3-22镗孔
10攻丝
转钳工选用M3丝锥攻丝5×
M3,倒棱去毛刺后用M3螺纹样柱进行尺寸检验(图3-23)。
图3-11攻丝
11表面处理
最后对零件进行表面处理。
这样所有工序完成。
第四章减震支架配套夹具设计
4.1机床夹具
机床夹具是机床上用以装夹工件(和引导刀具)的一种装置。
其作用是将工件定位,以使工件获得相对于机床和刀具的正确位置,并把工件可靠地夹紧。
4.1.1机床夹具
1、专门化分类
(1)通用夹具
通用夹具是指已经标准化的,在一定范围内可用于加工不同工件的夹具。
例如,车床上三爪卡盘和四爪单动卡盘,铣床上的平口钳、分度头和回转工作台等。
这类夹具一般由专业工厂生产,常作为机床附件提供给用户。
其特点是适应性广,生产效率低,主要适用于单件、小批量的生产中。
(2)专用夹具
专用夹具是指专为某一工件的某道工序而专门设计的夹具。
其特点是结构紧凑,操作迅速、方便、省力,可以保证较高的加工精度和生产效率,但设计制造周期较长、制造费用也较高。
当产品变更时,夹具将由于无法再使用而报废。
只适用于产品固定且批量较大的生产中。
(3)通用可调夹具和成组夹具
其特点是夹具的部分元件可以更换,部分装置可以调整,以适应不同零件的加工。
用于相似零件的成组加工所用的夹具,称为成组夹具。
通用可调夹具与成组夹具相比,加工对象不很明确,适用范围更广一些。
(4)组合夹具
组合夹具是指按零件的加工要求,由一套事先制造好的标准元件和部件组装而成的夹具。
由专业厂家制造,其特点是灵活多变,万能性强,制造周期短、元件能反复使用,特别适用于新产品的试制和单件小批生产。
(5)随行夹具
随行夹具是一种在自动线上使用的夹具。
该夹具既要起到装夹工件的作用,又要与工件成为一体沿着自动线从一个工位移到下一个工位,进行不同工序的加工。
2、按使用分类
由于各类机床自身工作特点和结构形式各不相同,对所用夹具的结构也相应地提出了不同的要求。
按所使用的机床不同,夹具又可分为:
车床夹具、铣床夹具、钻床夹具、镗床夹具、磨床夹具、齿轮机床夹具和其他机床夹具等。
3、按夹紧分类
根据夹具所采用的夹紧动力源不同,可分为:
手动夹具、气动夹具、液压夹具、气液夹具、电动夹具、磁力夹具、真空夹具等。
本文根据减震支架的结构特性,通用夹具在加工过程中不能很好的保证加工精度和位置精度,并且此零件需要大批量生产,产品结构已经固定。
所以综合考虑,设计一套专用夹具来进行夹装生产。
4.1.2组成原理
1、定位元件
它与工件的定位基准相接触,用于确定工件在夹具中的正确位置,从而保证加工时工件相对于刀具和机床加工运动间的相对正确位置。
2、夹紧装置
用于夹紧工件,在切削时使工件在夹具中保持既定位置。
3、对刀、引导元件或装置
这些元件的作用是保证工件与刀具之间的正确位置。
用于确定刀具在加工前正确位置的元件,称为对刀元件,如对刀块。
用于确定刀具位置并导引刀具进行加工的元件,称为导引元件。
4、连接元件
使夹具与机床相连接的元件,保证机床与夹具之间的相互位置关系。
5、夹具体
用于连接或固定夹具上各元件及装置,使其成为一个整体的基础件。
它与机床有关部件进行连接、对定,使夹具相对机床具有确定的位置。
6、其它元件及装置
有些夹具根据工件的加工要求,要有分度机构,铣床夹具还要有定位键等。
以上这些组成部分,并不是对每种机床夹具都是缺一不可的,但是任何夹具都必须有定位元件和夹紧装置,它们