微尺度群凸起电火花加工试验设计本科毕业论文设计40论文41Word下载.docx
《微尺度群凸起电火花加工试验设计本科毕业论文设计40论文41Word下载.docx》由会员分享,可在线阅读,更多相关《微尺度群凸起电火花加工试验设计本科毕业论文设计40论文41Word下载.docx(26页珍藏版)》请在冰豆网上搜索。
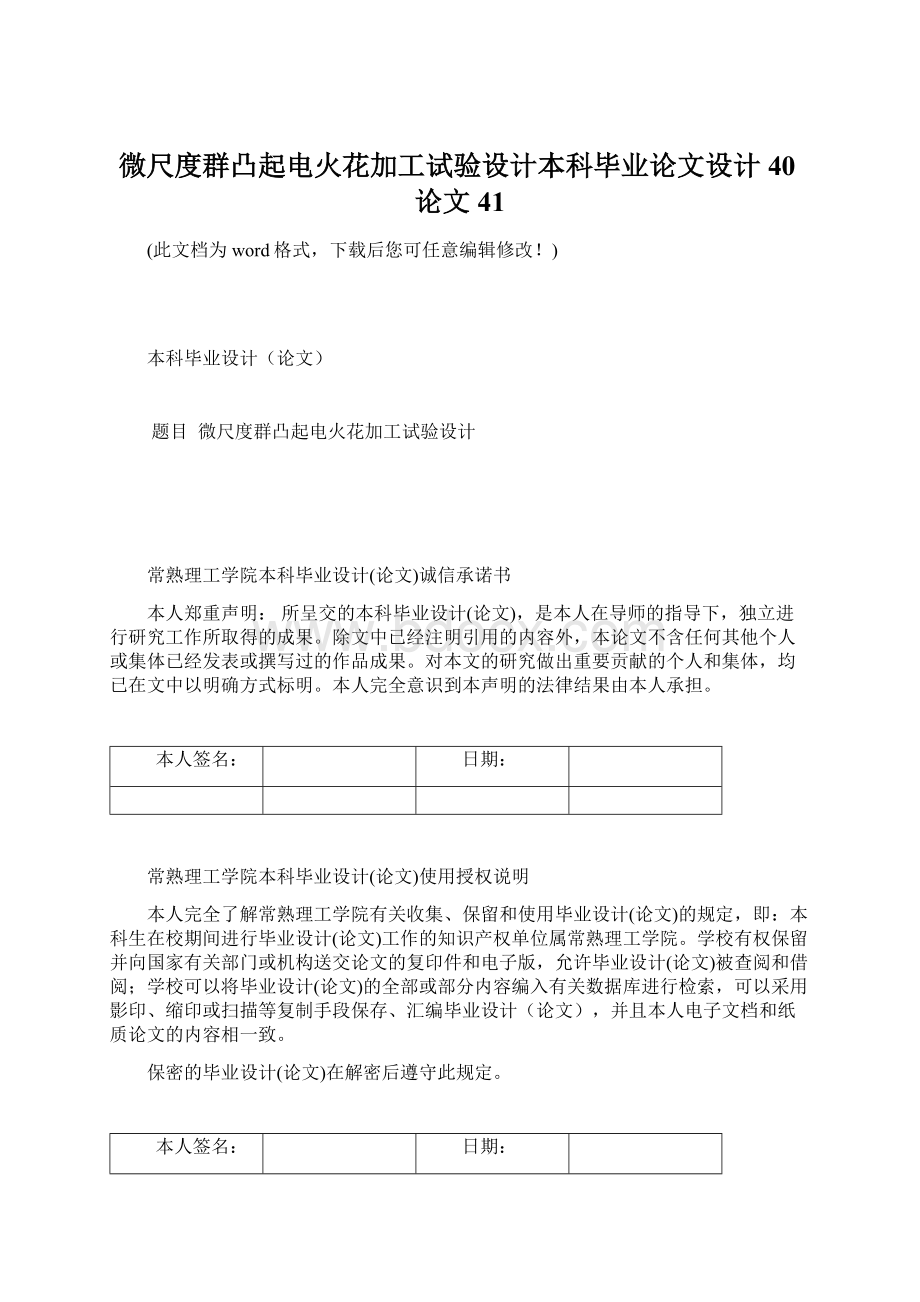
随着工业生产的发展和科学技术的进步,具有各种复杂结构与特殊工艺要求的工件越来越多,这就使得传统的机械加工难以持续。
微尺度群凸起电火花加工作为新的一门技术,通过电极间的重复脉冲放电腐蚀材料,能够更精细的对工件进行加工。
在本工作中,首先设计出专用夹具,通过电火花加工技术对微型散热器的圆柱表面实施微凸起加工。
构建出凸起形状为边长200um的正方形,且凸起间距也是200um,并且通过一次装夹同时完成圆柱的轴向与周向两道加工工序。
最终在圆柱表面加工出微凸起结构,经电子显微检测凸起间距以及长和宽大约都为200um,高大约为150um的立体,符合实验设计要求,实现了设计的预期目标。
关键词:
群凸起夹具电极
MicroEDMExperimentalDesignGroup
Abstract
Withthedevelopmentofindustryandtheprogressofscienceandtechnology,therearemoreandmoreworkpiecewithcomplexstructureandspecialtechnology,whichmaketheprocesstopreparetheseworkpiecebecomingmoredifficultfortraditionalmechanicalprocessingmethods.MicroEDMgroupisanewtechnologywithelectrodesandworkpiecetocorrodematerial.
Inthiswork,aspecialfixturedesigned,whichcanprocessthecylindricalsurfacetoattainthemicroconvexconfigurationsonthesurfaceofcylindricalusingelectricsparkmachiningtechnology.Thesemicroconvexconfigurationsaresquaredandtheside-lengthis200um.Thedistanceamongthesemicroconvexconfigurationsisalso200um.Throughourdesignedfixture,theprocessforaxialandcircumferentialareemployedatthesametime.Indeed,microconvexconfigurations,whichtheside-length,anddistanceare200um,microscopicdetection.Theaimofthisworkachieved.
Keywords:
groupraised;
fixture;
electrode
第一章引言1
1.1电火花加工简介1
1.2电火花加工原理1
1.3电火花的加工特点及形势3
1.4设计的内容及目的4
第二章微凸起结构的加工技术5
2.1微凸起结构的研究及应用5
2.2几种微凸起结构的加工方法5
2.2.1电火花成型加工5
2.2.2超声加工7
2.2.3电火花放电加工8
2.3微凸起结构加工方法的选择8
第三章加工电极的制作10
3.1电极的制作方法及选择10
3.2设计和制作电极11
3.3电极的标准制作与安装13
第四章夹具的设计14
4.1夹具的功用14
4.2装夹14
4.3加工夹具的设计15
4.3.1整体设计15
4.3.2选择电机16
4.3.3选择轴承16
4.3.4设计主轴17
4.3.5设计箱体18
4.3.6设计零部件18
4.4夹具设计总结19
第五章加工工艺20
5.1工艺参数20
5.2加工微凸起的步骤20
5.2.1周向加工20
5.2.2轴向加工21
5.3电参数的正确匹配21
5.4检测与分析22
5.4.1检测方法22
5.4.2检测结果22
5.4.3小结24
第六章设计总结与展望25
6.1设计总结25
6.2展望25
参考文献26
致谢27
第一章引言
1.1电火花加工简介
电火花加工是经历了人们从生产改革到科技文明的一门新的学科,新的技术。
数十年的发展路程,使得它能够更好地被人们所接受并加以应用,完善生产操作,促进效率。
十九世纪后期,人们通过对光电应用的研究,发现开关解电器的触点在打开的时候会产生放电效应,使得接触点烧蚀,损坏了接触面。
这种放电效应在电极产起的烧蚀现象我们称之为电腐蚀。
在开始一段时间,电腐蚀是被人们认为有害的,针对健康环保,减少和避免该类电腐蚀,人们开展了对电腐蚀产生的原因和防止的办法的研究。
在人们了解了它的规律之后,开始转变研究方向,将电腐蚀用到生产过程中,转害为利。
研究结果表明,当两个正负极放电的时候,通道里面会在瞬间产生极多的热量,这些能量足以使得电极材料表层发生局部的熔化或汽化;
同时,这些熔化或汽化的材料碎屑会能脱离电极的表面,形成我们所能看到的放电腐蚀形成的坑穴。
在二十世纪四十年代初,人们通过对电火花的进一步研究,认识到了在液体介质中进行重复性脉冲放电,可以对导电材料进行相对的尺寸加工,“电火花加工法[1]”由此产生,并将得到发展应用。
1.2电火花加工原理
图1-1电火花加工的原理图
电火花加工是利用低压和液介所形成的火花放电来对材料进行标量尺寸的腐蚀,达到预期的加工目标,我们称这种方法为电火花加工法。
如上图1-1所示,电火花加工原理可详述成以下几个工序,其中图1-1(a)为加工原理的模拟框图。
(1)两极间介质的电离、击穿所形成的放电通道(图1-1(b))。
接通脉冲电压,工具与工件各自的电极慢慢靠拢(维持放电间隙在0.01~0.05mm),这导致它们之间的电场强度会逐步增大,不过受两极的细微表面是凹凹凸凸的影响,两极间最近的A、B两点处电场强度是所有里面最大的。
两极之间所存在的介质是液体的(通常用煤油,矿物油或去离子水),众所知道,这样的液体介质中或多或少地会含有微分子,自由电子等其他杂质。
在强大的电场力作用下,正粒子(带正电)和负粒子(带负电)会出现分离,随着电场强度增大,带电粒子也就变多,最终会使得液体介质电离和击穿,出现放电通道。
因为通道的截面太过细微,通道内受热膨胀所形成的压力最高可达几万帕,这样的情况下,高温高压的放电通道以一个难以想象的速度扩展,产生一个强烈的冲击波辐射到四周。
在放电的同一刻,还伴随着产生光以及声效应,由此造成了我们习以为常看得见的电火花。
(2)电极工具材料的熔化和气化所导致得热膨胀(图1-1(c)、(d))。
当液体介质中形成放电通道的那一刻,通道间的那些带负电的粒子会向正极运动,同时带正电的粒子也就向负极运动,这样的运动中,各粒子之间磕磕碰碰,导致热量的产生,相应的周边温度升高,通道里面环境发生剧变,一瞬之后,高温达到一个极限(10~107Wmm)。
这样的情况下工作液先出现汽化,进一步发生气化,高温范围向周边延伸出去,金属材料的表层逐步开始出现熔化以及气化。
最终气化后的金属蒸气和工作液会一瞬间体积增长,导致了形如爆炸的性质。
因此在观察电火花加工的时候,我们能够很明显地看到工件与工具电极之间有烟出现,同时伴有轻微的爆炸声。
(3)电极工具局部材料的抛出(图1-1(e))。
当正负电极之间产生电火花,放电通道便会产生高温高压的情况。
通道的中心与边缘存在着一个温差,这个温差也造成了压力差,致使上述的蒸汽液之类向外排出,甚至是被抛出去。
在这个加工过程中,我们可以通过仔细观察,很明确地看到四处溅射的橘红色火花,这些便是被抛出的不需要的电极局部材料。
(4)两极之间所存在液体介质的消电离(图1-1(f))。
在上面的过程结束后,也意味着放电的结束,那些废液之类会渐渐流出,最终冷却下来,恢复到原来的样子,即绝缘态。
倘若在这个过程中,腐蚀所造成的产物以及废液没有能够得到尽快的排出,使得热量也同样不能有效地被疏导,这样局部的介质便会超出标准的热容量,致使其他介质,就是所谓的工作液因为高温而分解积炭,加工无法正常进行,并且有损电极。
因此为了保证电火花加工过程的正常持续进行,在两次放电之间必须有足够的时间间隔让电腐蚀产物完全充分排出,恢复放电通道的绝缘性能,使工作液体介质消电离[2]。
从上述加工原理可以看出,进行电火花加工所具备得三个必要条件:
(1)采用脉冲电源,放电时间控制在10-7~10-3s;
(2)控制自动进给调节装置,通过该设施使得工件与工具电极之间放电间隙维持在一个很小的范围内;
(3)放电过程必须具备在相应的绝缘介质中,一般来说,绝缘度在10~107m,从而实现加工过程的稳定。
1.3电火花的加工特点及形势
区别于机械加工,电火花加工是一种完全不同的新工艺。
随着科学技术和先进生产力的不断提高,对于性能更高的材料也有了新的生产理念。
先进的生产力对于实现加工更为精细严格。
传统的加工渐渐不能适应新社会的要求。
在人们逐步摸索之中,电火花加工作为一类新的工艺展现在人们面前。
一般来说电火花加工主要特点:
可以加工任何韧、强、脆、硬和纯等高性能的导电材料;
加工的时候没有很明显的机械力,非常适合用到对微细结构和低刚度工件进行加工;
通过调节脉冲参数实现在一台机床上进行粗,半精和精加工;
电火花加工后的形成的表面呈现凹形,用于贮油和削弱噪声;
电火花加工的生产效率明显比切削加工低;
加工过程受放电能量影响,有一些能量会在工具电极上出现消耗,损伤电极,从而影响了加工的精度。
不过电火花加工法能够适应生产发展的需要,并在应用中显示出很多优异性能,
因此,得到了迅速发展和日益广泛的应用[3]。
就电火花加工过程而言,它的性能决定了其特点,主要说来如下所述:
(1)在操作过程中,电极与材料之间不触碰,所以宏观上而言,两者之间作用力极小,这对电极的材料要求没必要那么苛刻,电极材料硬度可以小于工件的硬度。
因此,工具电极方便制作。
(2)脉冲放电时候的能量密度高,便于加工。
用普通的机械加工方法难于加工或无法加工的特殊材料和复杂形状的工件。
而且电火花加工不受材料硬度和热处理状况影响。
(3)放电的过程存在着一个电极损耗的过程,会影响工件成型的精确度。
不过在实际生产操作中,通常脉冲电压放电极为短暂,导致热能量辐射面小,对于材料的加工不会有太大的影响。
(4)电火花加工是以工件结构为基础的加工,简化了工艺,提高了效率和质量,同时降低了工人的操作难度。
目前,大多数发达国家的微细电火花加工技术已进入工业生产应用阶段,甚至步入商业销售阶段,例如美国麦威廉斯、瑞士夏米尔、日本松下精机等公司在这方面尤为突出。
其中松下精机可以说是领先一步,该公司能稳定加工出小于5μm的微细孔和小于2.5μm的微细轴,不过它的价格过于昂贵,大概得花费20万美元,而且还是对国内禁运的。
此外,丰田工业大学的毛利尚武和日本东京大学的增泽隆久等学者是研究机床方向上的主要代表,对机床方面的研发也有很高的水平[4]。
对于国内来说,我国南航和哈尔滨工业这两个大学在这方面的也取得了很大的成就,哈尔滨工业大学已经实现小于8μm的微细孔和小于4.5μm的微细轴的加工,达到了世界领先水平。
不过国内在将微细电火花加工技术转向商业化[5]和产品化方面仍远远落后于日本与欧美那些技术发达的国家[6]。
就全世界微细加工领域来看,欧美这些国家突出对硅原料实现微结构的加工制作,就这细分下来的领域技术人员普遍称为微细电子机械领域。
而相对的日本,则更侧重利用传统的加工方法或其他特种加工方法来实现从宏观上对尺寸零件的加工,渐渐地发展过度到向微观上的零件加工逼近(如微微细轴、孔、小齿轮或其他微小模具)。
相对像目前已广泛流行利用放电加工技术来加工微细零件,如对微细轴、微孔的加工,针对微坑结构、微凸起的加工还欠缺深入的研究,甚至是还未开始对阵列形状的加工研究应用。
微坑结构和微凸起都有相对应的形状,适合利用电火花成形加工,而其中关键在于工具电极的制备。
其中一种有效的方法是用电火花线切割微精加工。
仿生微制造方面和摩擦学上,阵列微凸起结构同样具有良好的应用前景,所以,微细电火花加工必定会成为这一领域发展的重中之重[7]。
1.4设计的内容及目的
通过设计出专门的夹具,使用电火花加工方法来对圆柱表面进行微凸起加工,凸起结构的形状是200um为边长的正方形,并且凸起之间的间隔也是200um,在加工过程中实现一次装夹就能完成对圆柱周向和轴向同时进行的两道加工工序。
(1)了解在精细零件加工领域,电火花加工工艺的应用以及研究成果;
(2)掌握精细加工中对电极的设计和制作的方法;
(3)掌握对精细零件加工后的检测方法。
此外:
掌握各种器件的正确使用方法,以及对于实验环境尤其是微电流的正确控制。
第二章微凸起结构的加工技术
2.1微凸起结构的研究及应用
1980年初,微弹流动力润滑理论建立在摩擦学的基础上呈现在大众的视野里,促进了人们对该领域的深入研究。
以传统的弹流润滑(EHL)理论基础,微弹流动力润滑理论是在其上发展起来的。
把弹性力学与流体润滑理论相结合所建立起来的弹流润滑理论,它是一个可以解决滚动接触的润滑理论。
相应的,微弹流润滑理论,则是建立在宏弹流的基础上,对微凸体产生的微弹流加以一系列的研究,所得出的新润滑理论。
微弹流动力润滑理论,提出了新观念。
原来机械领域中认为滚动接触的机械零件表面应该越光滑越好,而它针对这关键给出相对的理念,打破了传统观点。
事实上,微凸起结构所形成的粗糙表面不但没有因为接触面的不光滑而降低制作的机械零件表面抗磨损能力,而且很大程度上提高了使用寿命和承载能力[8,9],实现了现代机械客观传动高速和重载的要求。
所以来说,微弹流动力润滑理论是能过成为润滑理论这一领域的重大突破。
两年后,美国人William.H.Belke在微凸起结构的制作成形方面,依靠激光加工出首件囊括了微凸体(注:
本文统称微凸体为微凸起结构)的轴承;
紧跟着,1984年,日本的成濑芳夫提出了将多种排列方式及多种微凸体形状加工到发动机缸体内表面上,这个提出进一步推动了微凸起结构向实际应用的转变[10]。
起初,他依靠微弹流方面的最新研究成果,实现了将微凸起结构的纵轴方向从与零件运动方向一致转变成为相垂直。
此外,他不但提出了三角形和圆形的微凸起结构,而且进一步提出了两端是凹圆弧的长方形、两端是凸圆弧的长方形、斜平行四边形、交错排列的长方形这样四种微凸起结构,微凸体的长比宽大概在21~11之间。
之后他又在通过多次试验比较针对微凸起结构逐步掌握其规律以及最佳实现方案,这种方案可以有效地加强发动机缸体耐烧和耐磨的性能,同时也减少发动机工作时的漏气和油耗。
2.2几种微凸起结构的加工方法
2.2.1电火花成型加工
电火花成型加工技术从起步到现阶段已经历了70来年,由于高速铣加工在工作效益上大大超出它,故而一些人认为应该将这项技术划出模具加工的范畴。
反对声音也有,电火花机床制造商认为,对于部分窄槽加工来说,高速铣依旧不能解决。
同属于电火花加工,仅仅40多年的发展,线切割技术作为型腔加工已存在的主体,它的技术已经相当的成熟,在产值方面,它仍高出成型加工的数倍。
由于电火花成型加工的复杂机理,电火花成型加工现阶段不怎么如意,不过它还处于的成长期,距离它成为型腔中精加工工艺的主体目标还有好长一段路要走,所以这就要求它要更努力一些[11]。
电火花成型加工技术长期以来难以推广应用,这其中的的内因主要是:
加工对象随着科技发展,日趋复杂,操作员工对加工参数难以控制以及不能很好地维持加工过程的稳定可靠性,加工生产的厂方虽然提供部分成套参数。
不过这些数据还达不到实用的要求,就安全规范、成型效率、粗糙指数、电极的损耗、尺力精度等等指标,怎样在它们之间取得平衡,来达到预期的权衡序列,难以实现。
电火花成型加工的优点:
(1)电火花成型加工的过程中没有切削力的存在,所以被加工的材料不会发生变形很大程度上保证其加工精度。
(2)电火花成型加工的过程中没有过大的机械加工力,因而加工用的机床相对轻巧,也不需要再去考虑安装基础设备。
(3)电火花成型加工能够加工一切硬、软、脆、韧、高熔点的金属材料。
(4)电火花成型加工是一类不触碰的加工,也就是说加工的时候工具与工件两电极之间是不触碰的;
相比较其它加工方式,这种加工方式是不会对工件造成硬性的伤害。
(5)电火花成型加工技术可以加工硬度较高的工件,我们一般所遇到的加工是用硬的刀具来加工较为软的物体,不过电加工却是利用软的电极来加工较硬的工件。
(6)电火花成型加工不会因为像存在R角的铣加工那样,它可以对工件根据要求构建竖直拐角,从而达到目标加工。
(7)电火花成型加工过程中所利用的工具电极材料没有必要去比工件材料硬,所以工具电极是比较容易制造出来的[12]。
(8)电火花成型加工过程中受热很小,可以忽略其影响,所以可以削弱影响的层面,这样工件质量会大大提高。
电火花成型加工的缺点(主要是电极材料的选择方面):
(1)铜钨合金材料最大的缺点就是是价格昂贵,所以材料来源是十分困难的。
(2)紫铜材料本身熔点低,不适合承载较大的电流密度,一般实验过程中不能够利用超过30A的电流来加工,否则会导致电极材料表面龟裂、严重受损,影响加工的效果。
此外该材料热膨胀系数比较大,假如加工深窄筋位的部分,在较大电流下会很容易因为局部高温使电极材料发生形变,通常紫铜电极是采用低损耗,这样的加工平均电流较小,所以其生产率并不是很高[13]。
(3)石墨电极材料的缺点是放电稳定性通常不尽人意,受电弧放电影响不适合精细加工,一般是用来加工损耗较大要求的加工。
而且石墨电极材料最终加工出来的工件表面粗糙度十分差,加工过程伴随着掉渣等情况,甚至是表层脱落。
最主要的是要利用专门的加工机器来制作石墨电极。
2.2.2超声加工
在现代功能陶瓷材料中,压电陶瓷是处于非常重要的地位,用途十分广泛。
压电陶瓷是一种新型的功能电子材料,具备有高智能化。
随着科技不断发展,材料及工艺也得到不断研究和改良,信息、电子、航空航天等高科技领域也是一天一个面目的改进,压电陶瓷材料的制作技术与开发应用也将前途远大,备受到社会的关注和重视。
依赖于精良的加工工艺,压电陶瓷受到广泛的应用。
针对压电陶瓷,为了提高其加工精度和材料的性能,就需要不断地开发新材料及新的加工工艺。
压电陶瓷是一种非金属脆性材料,由于一般的机械加工方法作用力过大,加工时容易出现裂纹和脆断,对其进行精确加工十分艰难,又因为其是非金属材料,所以不适合用电加工方法。
而超声加工既无宏观机械作用力、没有热作用、不依赖于材料的导电性,又可加工确定比值的高深宽三维立体结构,加工精度和零件表面质量效果都很好,因此超声微细加工在压电陶瓷材料加工上具有独特的优势,有着良好进步空间和发展前景。
超声加工英文简称为USM,它是一种利用超声频来使工具做小振幅振动,通过游离于它与工件之间的液体中的磨料来捶击被加工表面,使得工件材料表面逐步破碎以实现预期目标的特种加工。
超声加工常用于焊接、切割、套料、穿孔和抛光。
超声加工的优点
(1)能使得加工表面质量和精度提高,而且加工迅速,生产效率高。
(2)超声加工没有造成损耗的热效应,也没有影响精度的粗显的切削力。
这样的性能可以高效地加工各种硬脆材料。
超声加工的缺点
(1)需要针对相应的材料研制出专门的超声加工机床。
图2-1超声加工
2.2.3电火花放电加工
通过微细放电加工技术来制作微坑表面结构和微凸起结构,主要是利用微坑和微凸起的相对几何关系,再利用电火花微精线切割技术来加工制备所需要的不同形状阵列的凹槽电极,然后根据反拷贝原理,用电火花成型加工技术加工微坑阵列,将工件和电极的凹凸关系反置一下设计出来,最终实现将微凸起结构阵列加工到工件表面[14]。
放电加工的优点
(1)一般的加工机会在加工过程中受切削力影响有损工件,而电火花放电加工不会。
(2)放电加工可以制造出传统切削加工机不能加工生产所要求的特殊形状的产品。
(3)即使是加工坚硬的材料,也会有较好的公差精度。
放电加工的缺点
(1)加工的速度相对缓慢。
(2)不能加工非导体材料。
2.3微凸起结构加工方法的选择
微凸起结构的加工是一种高精密的加工,要综合考虑到加工的效率、精度、设施、材料等各方面要求。
(1)就加工精度,将上面三种加工方法相比较,电火花成型加工可以保证相对较好的加工精度,而超声加工的加工精度次之,最后电火花放电加工只有加工硬质的材料才能保证较好的加工精度。
(2)就设施的要求,只有超声加工需要针对加工材料设计出专门的超声机床,所以说它对设施的要求比较高,而电火花放电加工和电火花成型加工都可以使用一般的电火花机床。
(3)就材料的要求,电火花成型加工在一般情况下适宜加工具有高熔点的金属材料,电火花放电加工无法对非导体材料进行加工,而超声加工大多数情况下适宜用来对硬、脆等性能的材料实施加工。
(4)就加工效率,就上述三种加工方法进行比较,电火花放电加工相对效率比较低,反之,超声加工迅速,生产效率相对高,而电火花成型加工只能在小电流下加工,生产效率也是相对较低的。
综上所述,电火花成型加工具备更好的加工优势,其最大优势在于不需要与工件相接触,同时保证相对较高的加工精度,在目前阶段有现成的加工机床,另一边它的工具电极比较容易制造出来,唯一的缺陷就是在加工效率上还有待提高。
经过以上比较,最终选择利用电火花成型加工来对微凸起结构进行加工。
第三章加工电极的制作
3.1电极的制作方法及选择
在以前,通常有两个方法可以用来制作微电极:
第一个方法是将通过磨削或切削加工出来的电极直接装置到电火花机床上;
而另一个方法则是单纯的经过冷拔的效果拉出来的所预期的