检验标准指导书优秀word范文 10页.docx
《检验标准指导书优秀word范文 10页.docx》由会员分享,可在线阅读,更多相关《检验标准指导书优秀word范文 10页.docx(9页珍藏版)》请在冰豆网上搜索。
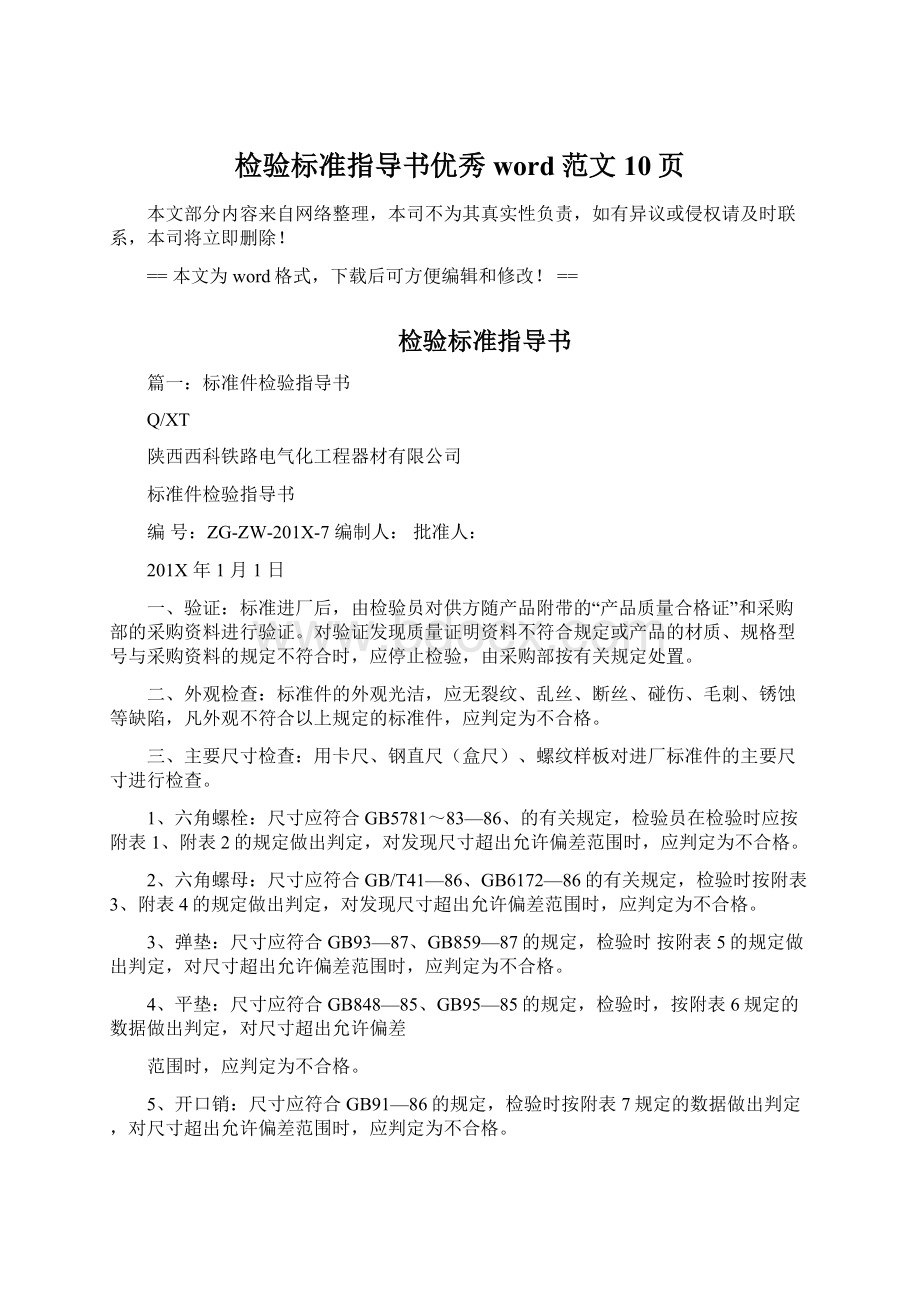
检验标准指导书优秀word范文10页
本文部分内容来自网络整理,本司不为其真实性负责,如有异议或侵权请及时联系,本司将立即删除!
==本文为word格式,下载后可方便编辑和修改!
==
检验标准指导书
篇一:
标准件检验指导书
Q/XT
陕西西科铁路电气化工程器材有限公司
标准件检验指导书
编号:
ZG-ZW-201X-7编制人:
批准人:
201X年1月1日
一、验证:
标准进厂后,由检验员对供方随产品附带的“产品质量合格证”和采购部的采购资料进行验证。
对验证发现质量证明资料不符合规定或产品的材质、规格型号与采购资料的规定不符合时,应停止检验,由采购部按有关规定处置。
二、外观检查:
标准件的外观光洁,应无裂纹、乱丝、断丝、碰伤、毛刺、锈蚀等缺陷,凡外观不符合以上规定的标准件,应判定为不合格。
三、主要尺寸检查:
用卡尺、钢直尺(盒尺)、螺纹样板对进厂标准件的主要尺寸进行检查。
1、六角螺栓:
尺寸应符合GB5781~83—86、的有关规定,检验员在检验时应按附表1、附表2的规定做出判定,对发现尺寸超出允许偏差范围时,应判定为不合格。
2、六角螺母:
尺寸应符合GB/T41—86、GB6172—86的有关规定,检验时按附表3、附表4的规定做出判定,对发现尺寸超出允许偏差范围时,应判定为不合格。
3、弹垫:
尺寸应符合GB93—87、GB859—87的规定,检验时按附表5的规定做出判定,对尺寸超出允许偏差范围时,应判定为不合格。
4、平垫:
尺寸应符合GB848—85、GB95—85的规定,检验时,按附表6规定的数据做出判定,对尺寸超出允许偏差
范围时,应判定为不合格。
5、开口销:
尺寸应符合GB91—86的规定,检验时按附表7规定的数据做出判定,对尺寸超出允许偏差范围时,应判定为不合格。
6、锁紧销:
尺寸应符合GB11031—89的规定,检验时按附表8规定的数据做出判定,对尺寸超出允许偏差范围时,应判定为不合格。
7、其它外购标准件:
检查主要尺寸时,应以该产品相对应的国家标准或行业标准为依据,对产品主要尺寸进行检查并做出判定,对尺寸超出允许偏差范围时应判定为不合格。
四、扭矩试验:
对螺栓、螺母每批小于1000件抽样数为3件;1000~5000件抽样数为5件;大于5000件抽样数为10件。
用0~300N·m力距扳手做紧固力矩试验,试验数值达到附表9规定的数值时,应无咬死、无裂纹、无变形,试验发现有1件不合格时应加倍检验,若仍发现不合格时则应判定为该批标准件不合格(对标准件其它项目的检查时抽查数量按本条款规定的数量执行)。
五、对不合格外购件的处置办法:
对检验发现的不合格品要及时隔离并予以标识,由采购部按有关规定实施退货处理。
绝不允许不合格品入库,任何人无权指示将不合格品进入生产工序。
六、对检验、测量器具的规定:
检验使用的检验、测量器具必须是经检定合格并在规定周期内且示值精确无异的检验、测量器具,使用时应按规定操作,防止损坏。
七、对质量记录的要求:
检验员必须按规定如实填写检验记录,并按规定归档。
陕西西科铁路电气化工程器材有限公司附表1:
GB/T5780—
GB/T5781—
篇二:
检验作业指导书
检验作业指导书
1.进料检验
1.1定义
进料检验又称来料检验,是制止不良物料进入生产环节的首要控制点。
进料检验由IQC执行。
1.2检测要项
IQC在对来货检验前,首先应清楚该批货物的品质检测要项,不明之处要向本部门主管问询,直到清楚明了为止。
在必要时,IQC验货员可从来货中随机抽取两件来货样,交IQC主管签发来货检验临时样品,并附相应的品质检测说明,不得在不明来货检验与验证项目、方法和品质允收标准的情况下进行验收。
1.3检验项目与方法
1.3.1外观检测
一般用目视、手感、限度样品进行验证。
1.3.2尺寸检测
一般用卡尺、千分尺、塞规等量具验证。
1.3.3结构检测
一般用拉力器、扭力器、压力器验证。
1.3.4特性检测
如电气的、物理的、化学的、机械的特性一般采用检测仪器和特定方法来验证。
1.4检验方式的选择
1.4.1全检方式
适用于来货数量少、价值高、不允许有不合格品物料或公司指定进行全检的物料。
1.4.2免检方式
适用于低值、辅助性材料或经认定的免检厂来料以及生产急用而特批免检的,对于后者IQC应跟进生产时的品质状况。
1.4.3抽样检验方式
适用于平均数量较多、经常性使用的物料。
样本大小:
批量的10%(不少于20件),允收数AC=0,拒收数RE=1。
1.5检验结果的处理方式
1.5.1允收
经IQC验证,不合格品数低于限定的不合格品个数时,则判为该批来货允收。
IQC应在验收单上签名,盖检验合格印章,通知货仓收货。
若不合格品数大于限定的不良品个数,则判定该送检批为拒收。
IQC应及时填制《IQC退货报告》,经相关部门会签后,交仓库、采购办理退货事宜。
同时在该送检批货品外箱标签上盖“退货”字样,并挂“退货”标牌。
1.5.3特采
特采,即进料经IQC检验,品质低于允许水准。
IQC虽提出“退货”的要求,但由于生产的原因,而做出的“特别采用”的要求。
若非迫不得已,公司应尽可能不启用“特采”。
“特采”必须由总经理批准,可行时还必须征得客户的书面许可。
1.5.3.1偏差
送检批物料全部不良,但只影响工厂生产速度,不会造成产品最终品质不合格。
在此情况下,经特批,予以接收。
此类货品由生产、质检单位按实际生产情况,估算出耗费工时数,对供应商做扣款处理。
1.5.3.2全检
送检批不合格品数超过规定的允收水准,经特批后,进行全数检验。
选出其中的不合格品,退回供应商,合格品办理入库或投入生产。
1.5.3.3重工
送检批几乎全部不合格,但经过加工处理后,货品即可接受。
在此情况下,由公司抽调人力进行来货再处理。
IQC对加工后的货品进行重检,对合格品接受,对不合格品开出《IQC退货报告》交相关部门办理退货。
此类货品由IQC统计加工工时,对供应商做扣款处理。
1.6紧急放行控制
1.6.1紧急放行内涵
a.紧急放行的定义
紧急放行是指生产急需来不及验证就放行产品的做法,称为“紧急放行”
b.紧急放行条件
产品发现的不合格能在技术上给以纠正,并且在经济上不会发生较大损失,也不会影响相关、连接、相配的零部件质量,可紧急放行。
1.6.2紧急放行的具体操作步骤
1.6.2.1应设置适当的紧急放行的停止点,对于流转到停止点上的紧急放行产品,在接到证明该批产品合格的检验报告后,才能将产品放行。
1.6.2.2若发现紧急放行的产品经检验不合格,要立即根据可追溯性标识及识别记录将不合格品追回。
2.过程检验:
过程检验(IPQC)指来料入仓后,至成品组装(或包装)完成之前所进行的质量检验活动。
2.1.1及早发现不合格现象,采取措施,以防止大量不合格品的产生。
2.1.2过程检验作为过程控制的一部分,用来评估过程的稳定性并预知过程发展的趋势,以便在不合
格尚未发生之时就采取有效的预防措施。
2.1.3通过过程检验,防止不合格品流入下一道工序,甚至可能装在最终的产品上,以致造成不合格
品出厂。
2.2首件检验
2.2.1定义及目的
首件检验是在生产开始时(上班或换班)或工序因素调整后(换人、换料、换活、换工装、调整设备等)对制造的第1件(大件产品)或前3件(非大件)产品进行的检验。
目的是为了尽早发现过程中影
响产品质量的系统因素,防止产品成批报废。
2.2.2操作者
首件检验由操作者、检验员共同进行。
操作者首先进行自检,合格后送检验员专检。
2.2.3要求
2.2.3.1首件正式生产时,检验员应对操作员领用的物料、设备状态、使用的工模具、作业指导书的
版本进行核对。
2.2.3.2检验员应按规定在检验合格的首件上作出标识,并保留到该批产品完工。
2.2.3.3首件未经检验合格,不得继续加工或作业。
2.2.3.4首件检验必须及时,以免造成不必要的浪费。
首件检验后要填写《首件检验记录表》,以保
留必要的记录。
2.2.3.5机加工、冲压过程应实施首件检验。
2.3巡回检验
2.3.1定义
巡回检验是指检验员在生产现场每间隔2小时对各工序的产品和生产条件进行监督检验
。
2.3.2巡回检验的内容:
巡回检验不仅要抽检产品,还需检查影响产品质量的生产因素(4M1E-人、机、料、法、环境)。
巡检以抽查产品为主,而对生产线的巡检,以检查影响产品质量的生产因素为
主。
生产因素的检查包括:
2.3.2.1当人员有变化时,对人员的教育培训以及评价有无及时实施。
2.3.2.2设备、工具、工装、计量器具在日常使用时有无定期进行检查、校正、保养,是否
处于正常状态。
2.3.2.3物料和零部件在工序中的摆放、搬送及拿取方法是否会造成物料不良。
2.3.2.4不合格品有无明显标识并放置在规定区域。
2.3.2.5工艺文件能否正确指导生产,工艺文件是否齐全并得到遵守。
2.3.2.6产品的标识和记录能否保证可追溯性。
2.3.2.7生产环境:
生产环境是否适宜产品生产的需求,有无产品、物料散落在地面上。
2.3.2.8对生产中的问题,是否采取了改善措施。
2.3.2.9员工的技能能否胜任工作。
2.3.2.10生产因素变换时(换活、修机、换模、换料)是否按要求通知质检员到场验证等等。
2.3.3巡检问题处理
巡检中发现的问题应及时指导操作员或反馈到生产单位加以纠正,问题严重时,要适时向有关部门
发出《纠正和预防措施要求单》要求其改进。
2.4完工检验
2.4.1定义
完工检验,是指对全部加工活动结束的半成品、零件进行的检验。
完工检验的工作包括验证前面各工序的检验是否已完成,检验结果是否符合要求,即对前面所有的检验数据进行复核。
2.4.2要求及重点
2.4.2.1完工检验要求:
应该按照工序卡、产品图样、抽样方案等有关文件的规定,做好完工检验工
作。
2.4.2.2完工检验的重点
2.4.2.2.1核对加工件的全部加工程序是否全部完成,有无漏序、跳序的现象存在。
在批量的完工件中有无尚未完成或不同规格的零件混入。
必要时采取纠正和预防措施,以防止问题的再发生。
2.4.2.2.2核对被检物主要质量特性值是否真正符合规范要求。
2.4.2.2.3复核被检物的外观,对零件的倒角、毛刺、磕碰划伤应予以特别地注意。
2.4.2.2.4被检物应有的标识、标志是否齐全。
2.5末件检验
2.5.1定义
末件检验,是指依靠模具或专用工装加工并主要靠模具、工装保证质量的零件加工场合,当批量加
工完成后,对加工的最后一件或几件进行检验验证的活动。
2.5.2要求
末件检验由检验人员和操作人员共同进行,检验合格后,双方均应在末件检验记录表上签字,并把
记录表和末件实物(大件可只要检验记录)拴在工装上。
3成品入库检验
3.1检验方法
3.1.1数量≤20时,采用全检方式。
合格品入仓,不合格品退回车间返工。
3.1.2数量≥21时,如客户有特殊要求,按客户要求检验,否则,抽检10%,判断标准:
AC=0,
RE=1。
3.2检验要求
3.2.1产品检查前,应首先查看内外箱及包装是否用错,如用错,则整批退车间返工。
3.2.2产品检查前,查看随产品发出的配件、资料,包括说明书、保证卡等是否齐全,如不齐全或装
错则整批退车间返工。
3.2.3如发现有产品混装则整批退车间返工。
3.2.4批量构成:
批量为一个班组一天的产量。
4出货检验
4.1检验内容
4.1.1外观检查:
检查产品是否变形、受损、配件/组件/零