注塑机设置手册Word文件下载.docx
《注塑机设置手册Word文件下载.docx》由会员分享,可在线阅读,更多相关《注塑机设置手册Word文件下载.docx(19页珍藏版)》请在冰豆网上搜索。
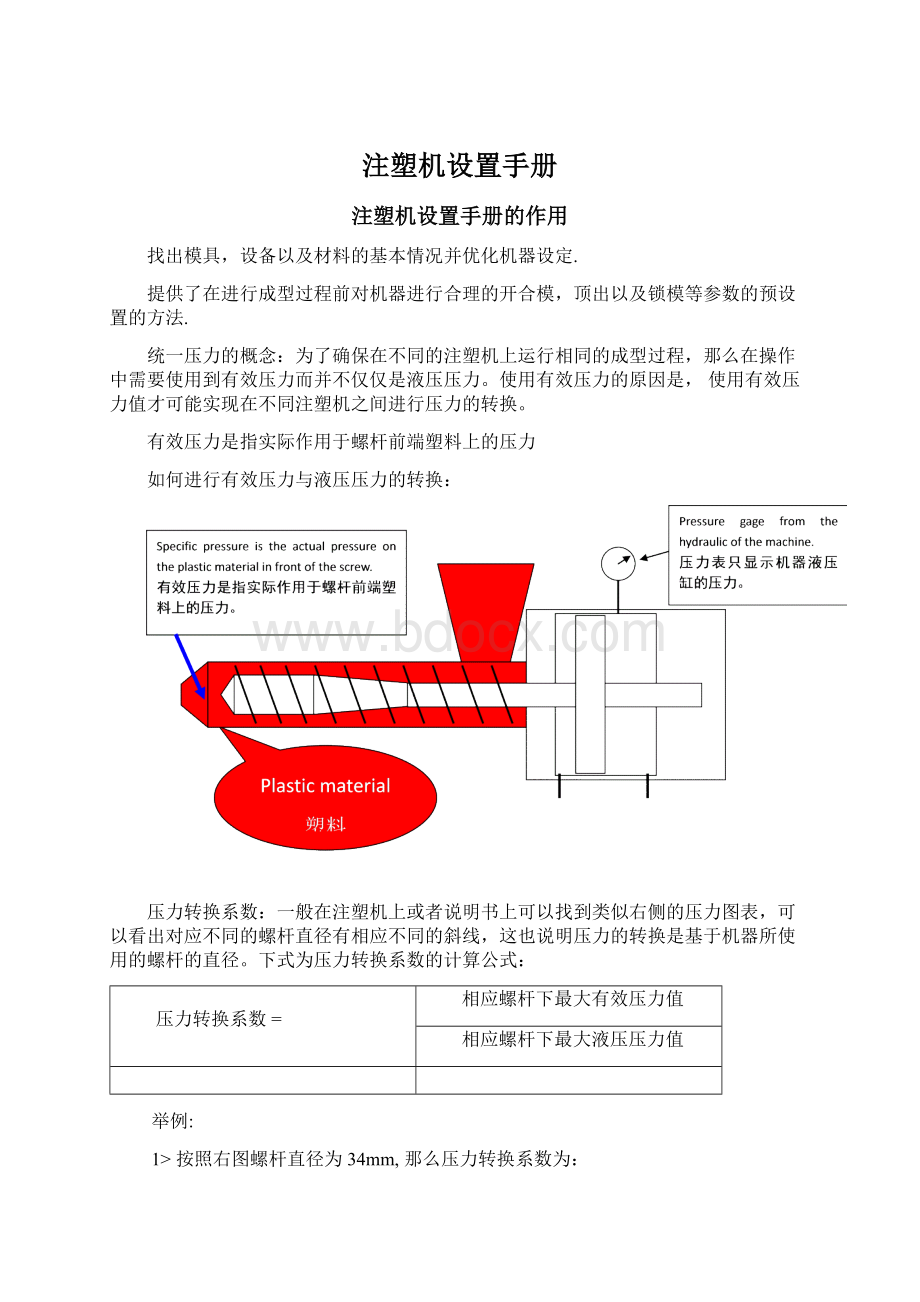
干燥方法
干燥温度(oC)
干燥时间(小时)
备注
PC
去湿干燥机
120~
4
PA
70~80
4~6
PA6;
PA66;
PA601;
PA11;
PA12
PMMA
70~100
8
TPU
100~110
1~2
ABS
2~4
POM
热风干燥机
60~80
根据环境的湿度情况,目的是去除材料表面的湿气。
PP
PE
SEBS
对于具体型号的材料,请参考相应的材料规格书。
2.模具安装
2.1将模具吊装入相应规格的注塑机。
2.2接驳冷却水。
通常接驳冷却水的方法有并联和串联,而模具在设计时对于每一组运水要求有独立的冷却水,因此我们要求使用并联的连接方法,对每一组运水使用独立的出入水管。
只有在中小型模具上才根据设备情况使用串联,但是极限是两组串联成一组。
下表供参考:
正常要求
两组并一组,基本接受
不接受
2.3检查并确保水管畅通。
水管不允许有折叠现象,如有发现应及时更换。
.
2.4检查机台的冷却系统压力差,确保压力差大于3.5巴,否则需要使用增压泵。
2.5前后模必须使用相同的冷却介质及温度设定。
2.6检查射嘴孔,根据制件的大小选用合适的射嘴。
2.7彻底清洗炮筒并装入正确的塑料材料。
3.注塑机的基本设置
3.1设置炮筒温度
炮筒温度设置参考值如下表:
温度(oC)
射嘴
一段
二段
三段
模具温度
310~350
305~350
285~310
235~290
80~120
PA6
230~260
240~260
220~230
200~210
70~110
PA66
260~280
255~280
230~255
190~215
195~215
180~205
150~180
70~120
200~250
185~225
140~180
50~80
205~240
180~210
180~200
220~260
215~260
190~230
50~90
240~300
240~290
210~250
150~210
20~75
LD-PE
140~200
20~70
HD-PE
220~300
215~300
10~90
195~205
185~195
160~185
20~40
备注:
3.2设置注射量
打开模具观察型腔大小估算所需的注射量,并设置足够的注射量。
3.3设置螺杆转速
螺杆转速参考值如下表:
螺杆转速
mm/s
400~600
300~500
800~1000
600~800
800~1200
200~300
rpm
N=19.1xV/DD=螺杆直径(mm)
3.4设置背压
根据制件的材料及颜色,设置相应的背压并检查射嘴是否漏料。
背压的压力值对于液压注塑机是指液压部分的压力,与有效压力无关,不需要进行任何换算。
3.5设置倒索及射嘴回退距离
3.5.1倒索:
设置适当的值,防止开模时射嘴处漏料,一般情况下设3~5mm.
3.5.2射嘴回退距离:
由于此动作占用一定的机器时间,因此一般情况下建议不使用此设置。
3.6调节注塑机的锁模力
根据模具的锁模力计算值设置注塑机的锁模力。
3.7设置开合模距离及速度
3.7.1开合模距离
对于开合模距离的基本要求是距离越短越好,只要满足制件及流道可以坠落而不触及前模模面,或者适合机械手或手工取件的需要即可。
3.7.2开合模速度:
对于开合模速度的基本要求是越快越好。
基本上至少设置3个步骤及相应的速度;
第一段:
距离5~10mm(根据模具的具体结构进行调整);
速度采用低速约为5%~8%;
第二段:
采用高速;
第三段:
开模距离的最后10~15mm作为缓冲;
使用低速约为(20%~30%);
以上是常规的设定,同时请关注以下情况并做适当调整:
∙模具结构:
2P/3P/有无抽芯机构模具大小
∙考虑机器的承载能力,在最后调整时必须确保机器的运动顺畅且无震动。
3.8设置顶出距离及速度
3.8.1顶出距离:
制件及模具结构决定了可以顶出以及需要顶出的距离。
一般情况下在满足制件质量要求的前提下制件可以容易的跌落或由机械手或手工取出的最短距离。
3.8.2顶出速度:
制件结构,塑料材料以及模具结构决定了允许的顶出速度,因此需要针对不同的情况进行调整。
顶出速度的一般设置(仅供参考):
顶出速度
15%~30%
60%~80%
ABS;
PA;
PP;
PE;
POM;
3%~8%
30%~60%
PC;
PMMA;
SEBS;
TPU
0
10mm
复位速度
80%~95%
次数
1~2次
4.预运行及对注塑机的评估
4.1预设置
∙关闭保压设置,采用一段注射。
∙注射速度=99%
∙注射时间=8~10sec
∙冷却时间=8~10sec
∙压力:
以低压开始,逐渐加压至刚刚添满型腔。
4.2在半自动或全自动下运行.
∙保持稳定地,周期性地连续运转约20~30分钟。
4.3注塑机评估
∙评估止回阀,螺杆及炮筒的间隙是否存在回料现象
在注塑机运行越10分钟左右可以将注射时间延长并超过20秒,观察螺杆在整个注射过程中是否会保持在某个位置不变。
如果螺杆在整个注射过程中始终处于前进状态,这就意味着止回阀或螺杆及炮筒的间隙过大,存在回料现象,那么就必须更换注塑机。
测试完成后请设回原来的注射时间值。
∙评估系统压力是否稳定
在注塑机运行越20分钟左右观察压力显示值及油压表的指示,当表板上的压力在每次注射时都是一致的(只在小数位存在0.1~0.3的偏差),而且油压表的指针的指示也是一致的并且不存在颤抖现象则表明压力已经趋于稳定可以进行后续的工作。
∙检测模具温度
将磁性温度计吸附于模胚上,观察温度是否稳定在某个值上。
5.浇注系统的评估
此步骤只针对多型腔的模具。
5.1降低注射压力直至第一个(批)型腔填充到99%或刚刚添满。
记录此时的压力值。
5.2增加注射压力直至最后一个(批)型腔填充到99%或刚刚添满。
5.3对以上两个压力值进行分析及判断:
当上述两个压力差小于等于50(60)巴时,浇注系统被认为是平衡的,否则是不平衡的。
注释:
1.当发现浇注系统是不平衡状态时必须进行记录并在下次试模时重新评估并且重新进行全过程来寻找正确的压力窗口。
2.当压力差超过150巴时,原则上不必再继续后续的步骤,必须对浇注系统进行修改后再重新开始。
因为在如此大的压力差下得到的压力窗口已经没有实际意义。
6.寻找成型方法
6.1记录末件填充至99%时的注射量为D99。
6.2测量并记录末件填充至99%时的时间。
(可以使用秒表进行测量。
)
6.3判断:
当末件99%的填充时间短于2秒,同时填充压力小于800巴时,采用单一压力法。
当以上任何一个条件不满足时则采用分压法。
7.对于不同方法的预设置
7.1单一压力法
单一压力法是指使用同一个压力进行注射和保压的成型方法,注射时间包括了填充和保压时间,填充与保压的转换是以时间进行切换的。
而这种切换又是由注射过程自动完成的。
7.1.1当使用此方法时,除了注射量以外,保持其他现有的设置不变。
7.1.2调整注射量为D99x1.25mm,并取整到10,15,20,25….mm。
7.2分压法
分压法是指对注射和保压分开进行独立的设置。
7.2.1设置总注射量为D99mm.
7.2.2设置切换点为D99X25%mm,并取整到10,15,20,25….mm
7.2.3设置保压压力为零或注塑机最低要求设置值
7.2.4设置保压速度为零或注塑机最低要求设置值
7.2.5设置保压时间为6~8秒或更多(基于入水口的尺寸,但必须确保足够)
7.2.6将注射速度调整为90%,开始注塑,并等待1~2啤。
7.2.7检查并确保螺杆的开始位置与设置一致。
7.2.8设置注射压力为取整后的末件99%的填充压力加上600巴。
8.寻找99%填充板
8.1单一压力法
8.1.1当使用单一压力法时,目前的注塑机状态已经是99%的填充状态。
因此可以连续成型5~8啤来判断填充是否稳定。
根据样板的填充状态无法确定是否稳定时则必须加大取样数量至20啤。
如果从大量的样板情况分析到填充状态不稳定时,检查炮筒的发热装置是否出现故障或者是炮筒尚未清洗干净。
8.1.2称每一整啤不含流道的制件总重量,计算平均重量值并记录。
.留取5啤(连同流道)作为今后试模和生产参考。
8.2分压法
3.2.4增加总注射量直至填充到整啤的98~99%,此过程必须注意,切忌将型腔充满。
这样有机会造成模具承受过高的压力而造成不必要的伤害。
连续成型5~8啤比较并判断填充的稳定性。
3.2.5称每一整啤不含流道的制件总重量,计算平均重量值并记录。
8.3两种方法的区别
单一压力法:
通过对调整注射压力的方法来寻找99%的填充状态。
分压法:
通过调整总的注射量的方法来寻找99%的填充状态。
9.寻找外观合格压力
外观合格是指制件被完全填充并符合外观上的质量要求。
9.1单一压力法
增加注射压力直到制件的外观看上去符合质量要求,记录压力值。
9.2分压法
将保压速度设为90%
建立并不断增加保压压力制件的外观看上去符合质量要求,记录保压压力值。
9.3两种方法的区别
对于单一压力法,外观合格板是在99%填充的注射压力上继续增加注射压力实现的。
数据的记录是相对于99%填充压力的增加值。
例如:
某制件的99%填充压力为500巴,外观合格的绝对压力值为600巴,那么外观合格的记录值是“+100”。
对于分压法,外观合格板是在保压压力为零的情况下建立保压压力实现的。
注射压力是固定不可变的值。
因此数据的记录是保压压力的绝对值。
某制件的外观合格的保压压力是300巴,那么记录值就是“300”
10.设定压力窗口的低压值并寻找最短保压及冷却时间
10.1压力窗口的低压值
压力窗口的低压值等于外观合格压力加70~80巴。
对于单一压力法,压力窗口的低压值同样是在99%填充的注射压力上继续增加注射压力实现的。
因此数据的记录是相对于99%填充压力的增加值。
某制件的99%填充压力为500巴,压力窗口的低压值为650巴,那么压力窗口的低压值的记录值是“+150”。
对于分压法,压力窗口的低压值是在保压压力为零的情况下建立保压压力实现的。
注射压力值仍然是固定不可变的值。
某制件的压力窗口的低压值是350巴,那么记录值就是“350”
10.2寻找最短保压时间
10.2.1以0.5秒为单位,缩短注射或保压时间同时增加冷却时间,保持注射或保压时间与冷却时间的总和不变。
留取对应时间下的样板并称不含流道的整啤制件的重量,记录时间及对应的重量值。
10.2.2重复步骤10.2.1直到注射或保压时间为0.5秒或者发现制件出现明显的缩痕为止。
10.2.3根据上述的数据绘制时间-重量曲线图,从图中找到重量开始趋于稳定的时间点,在此基础上增加0.5秒作为最短注射或保压时间
10.3寻找最短冷却时间
10.3.1以1秒为单位,缩短冷却时间用手感觉制件的重要部位及流道的温度。
10.3.2重复步骤10.3.1直到手感微烫。
10.3.2测量制件的重要部位或流道的温度,当温度等于下表中的温度值或低于表中值5oC左右,那么在对应此温度的冷却时间上加上1秒作为最短冷却时间。
LDPE
HDPE
PA6
PA66
维氏软化温度(oC)
65
90
138
165
180
200
85
102
表面温度(oC)
<
=60
=85
=130
=160
=175
=195
=80
=95
1.制件与流道的温度必须相互兼顾,通常情况下制件表面温度会远远低于表中的值,而流道温度已经很高,因此必须注意流道保证流道可以顺利脱落。
2.此时间必须经过在生产条件下并运行2小时以上来最后确认。
3.对于某些注塑机冷却时间必须长于螺杆计量时间,为了提高生产效率应尽量避免使用转速低的螺杆装置甚至注塑机。
11.建立压力窗口并制备样板
11.1单一压力法
11.1.1以70~80巴为单位,从注射压力窗口的最小值开始增加注射压力,连续做2个循环。
检查每一循环中制件的质量情况。
数据的记录形式是记录相对于99%填充压力的增加值“+XXX”
11.2分压法
11.2.1以70~80巴为单位,从保压压力窗口的最小值开始增加保压压力,连续做2个循环。
数据的记录形式是记录保压压力的绝对值。
11.3样板制备
针对上述的三个压力参数分别按照要求的数量准备样板,并且在样板上标注该样板相对应的压力值。
11.4确定压力窗口
压力窗口的确定是基于制件尺寸测量报告。
根据测量报告可以清楚地知道要求的尺寸公差所对应的压力区间,从而确定压力窗口的范围。
11.5压力窗口的要求
压力窗口的范围必须满足于100~200巴之间,即100≤Window≤200巴。
12.填充顺序板的制备
12.1
单一压力法
12.1.1设置保压
设置保压压力为零或注塑机最低要求设置值
设置保压速度为零或注塑机最低要求设置值
设置保压时间为1秒
切换点为5毫米
此设置是为了保护炮筒部分。
12.1.2保持其他的设置,确认注射压力为中压值。
12.1.3分5步减少注射量,分别制备填充状态为25%;
40%;
55%;
70%和85%的样板。
12.2分压法
12.2.1关闭保压
12.2.2分5步减少注射量,分别制备填充状态为25%;
13.测量溶胶温度
∙对测温棒进行预加热,直至温度接近被测温度。
∙用测温杯从射嘴处取适量的熔融塑料。
∙将棒式温度计插入熔融塑料的芯部。
∙在熔胶芯部均匀搅动测温棒。
∙观察温度显示值直到显示值停止上升并出现下降为止,记录温度最高显示值。
∙重复上述过程,确保测量的准确性。
测量熔胶温度在整个过程中是一个极其重要的步骤,它是整个成型参数可否在后续阶段和生产中被使用,并且是否可以获得相同制件品质的重要基础。
14.完成成型参数卡
按照注塑机表板的显示,将参数卡中未填写的部分完成。
第二部分:
成型参数卡在开发阶段及生产中的应用
模卡使用流程图
条件:
当完成第一次试模后,并且也找到了一定范围的压力窗口,那么原则上在后续的各个阶段的试模过程中必须使用相同的设置。
只有当流道系统或浇口在上次试模后做了修改,那么整个过程必须重新进行。
同第一部分的步骤一。
同第一部分的步骤二。
3.1检查并确定使用正确射嘴口径。
3.2按照模卡设置炮筒温度。
3.3参照模卡上的啤重记录设置足够的注射量。
3.4参照第一部分步骤3.3设置螺杆转速,并按照模卡上的“螺杆回退时间”调整转速获得相同的螺杆回退时间。
3.5按照模卡设置相应的背压,检查螺杆计量时射嘴有没有流延现象。
3.6按照模卡设置倒索或炮筒回退距离。
3.7按照模卡调整机器锁模力。
3.8参照第一部分步骤3.7设置开合模的距离和速度。
3.9参照第一部分步骤3.8设置顶出距离和速度。
4.1参数设置
4.1.1单一压力法
初步设置
∙按照模卡设置注射速度。
∙按照模卡设置注射时间。
∙按照模卡设置冷却时间。
∙按照模卡将注射压力设置为99%填充压力。
4.1.2分压法
∙关闭保压设置部分。
∙按照模卡将注射压力设置为99%填充压力减去600巴.
4.2注塑机的评估
4.2.1评估止回阀,螺杆及炮筒的间隙是否存在回料现象
4.2.2评估系统压力是否稳定
在注塑机运行越10分钟左右观察压力显示值及油压表的指示,当表板上的压力在每次注射时都是一致的(只在小数位存在0.1~0.3的偏差),而且油压表的指针的指示也是一致的并且不存在颤抖现象则表明压力已经趋于稳定可以进行后续的工作。
4.2.3检测模具温度
5.测量溶胶温度
测量得到的熔胶温度必须与模卡上的记录进行比较,确保与模卡一致。
当测量温度与模卡记录不符时需要调节炮筒的温度设置,待温度稳定或重复上述测量过程并与模卡进行比较。
6.寻找99%填充板
6.1单一压力法
∙根据初步设置,确定当前状态是在99%填充状态下。
否则调节注射压力使其达到99%填充状态。
∙参照99%的填充签板以及模卡上记录的99%的重量,比较并确认实际的99%填充与之一致。
否则继续调整注射压力使其一致。
6.2分压法
∙从第二部分步骤4所设的压力开始逐渐增加注射压力知道达到99%填充,记录当前的99%的注射量。
按照第一部分步骤7.2.1和7.2.2的方法设置保压切换点和总注射量。
∙检查并确认螺杆的起始位置与设置一致,按照模卡上的值设置99%的注射压力。
∙检查并调整总注射量直到99%的填充状态近似于99%填充签板。
否则继续调整总注射量使其一致。
∙比较实际的填充时间与模卡记录的填充时间,当两者的偏差超出允许范围时,则对注射压力进行调整使彼此匹配。
7.按照模卡设置成型参数.
7.1单一压力法
∙按照模卡设置注射压力。
注射压力=实际99%填充压力+模卡上的中压压力值。
7.2分压法
∙设置保压的中压压力值=模卡上的中压压力值。
8.校核循环周期
∙检查注塑周期,确保与模卡一致,否则需要对机器时间部分的设置进行调整。
9.制件的质量评估
∙准备高,中,低压样板。
∙QA/QC必须对高,中,低压板进行测量与测试以确保生产的质量达到预期的要求。
第三部分:
如何使用成型参数卡?
1.
作用
对成型的过程数据进行保存。
作为测量,模具修改,过程,模具和制件的批核的依据。
优势在于模卡上的参数在生产时可以在任何型号的注塑机上使用,由于过程参数的统