饭盒注塑模设计Word格式文档下载.docx
《饭盒注塑模设计Word格式文档下载.docx》由会员分享,可在线阅读,更多相关《饭盒注塑模设计Word格式文档下载.docx(25页珍藏版)》请在冰豆网上搜索。
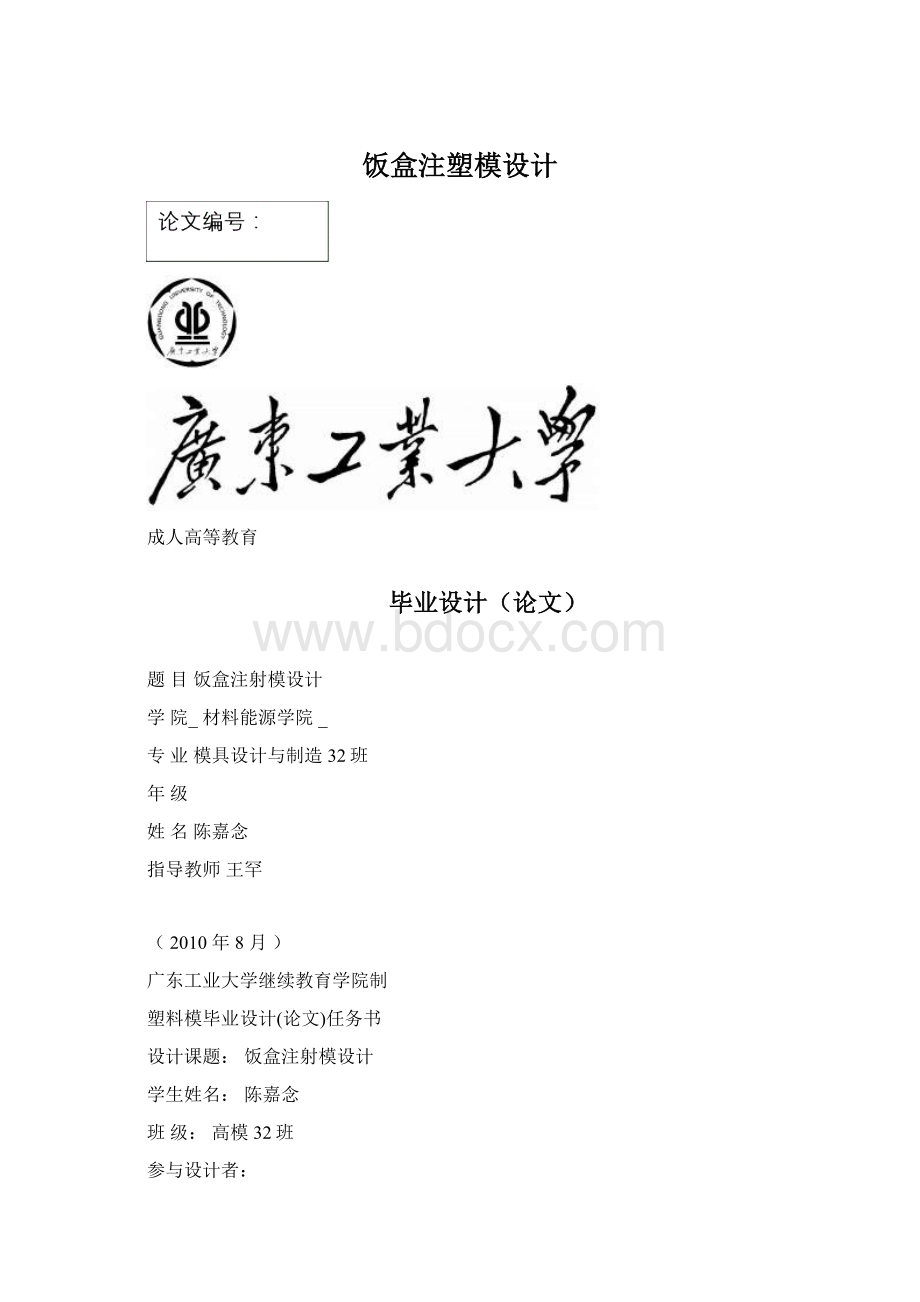
二.注射机型号的初步拟定-----------------------------------------------------------------3
三.模具结构方案的确定--------------------------------------------------------------------4
1分型面的确定-------------------------------------------------------------------------5
2型腔的布置方案的比较与确定----------------------------------------------------6
3浇注系统形式和浇口的设计-------------------------------------------------------7
4成型零部件系统的设计-------------------------------------------------------------9
5温度调节系统------------------------------------------------------------------------10
6顶出机构的确定----------------------------------------------------------------------11
7其它系统与结构---------------------------------------------------------------------12
四.模具中相关的校核----------------------------------------------------------------------13
1注射机与模具尺寸的关系校核---------------------------------------------------14
2成型零部件系统中成型零件的工作尺寸计算----------------------------------15
3承板强度和刚度的校核-------------------------------------------------------------16
五.模具的工作过程-------------------------------------------------------------------------17
六.相关零件的加工工艺过程-------------------------------------------------------------18
七.结束语-------------------------------------------------------------------------------------19
附录一成型零件加工工艺卡片
附录二成型零件零件图
附录三模具总装图
前言
光阴似箭,在校的大学三年的学习一晃而过,为具体的检验这三年来的学习效果,综合检测理论在实际应用中的能力,除了平时的考试、实验测试外,更重要的是理论联系实际,即此次设计的课题为饭盒的注塑模具。
本次毕业设计课题来源于生活,应用广泛,模具结构较为简单,对模具工作人员提高理论联系实际的能力是一个很好的练习。
它能加强对塑料模具成型原理的理解,同时锻炼对塑料成型模具的设计和制造能力。
本次设计以饭盒注射模具为主线,综合了成型工艺分析,模具结构设计,最后到模具零件的加工方法,模具总的装配等一系列模具生产的所有过程。
能很好的学习致用的效果。
在设计该模具的同时总结了以往模具设计的一般方法、步骤,模具设计中常用的公式、数据、模具结构及零部件。
把以前学过的基础课程融汇到综合应用本次设计当中来,所谓学以致用。
在设计中除使用传统方法外,同时引用了CAD、Pro/E等技术,使用Office软件,力求达到减小劳动强度,提高工作效率的目的。
由于本人才疏学浅,知识根底不牢,缺少经验,在模具结构设计计算和编写
设计说明书的全工程中,得到汪老师、邓老师以及其他机械、模具基础课的老师的细心指导,同时也得到同学的热情帮助和指点,在此谨以致谢。
敬请各位老师和同学批评指正,以促我在以后的工作中减少类似的错误,做出成绩,以报恩师的淳淳教诲和母校的培养。
一、塑料制品的工艺性分析
如图1所示为饭盒
图1.1饭盒零件图
(1)塑件形状分析
此塑料制品的形状比较简单,整体不带凹槽,型腔可以和四周的槽做成一个整体式的型腔,不用侧向抽芯,给模具带来了方便.饭盒的注塑材料首先选用ABS,饭盒绝大部分的决定了饭盒的重心的位置的所在。
所以我们必须很好多处理制件壁厚的均匀,譬如在注塑成型过程中因为壁厚的不均匀造成了收缩率的不一致,这样就只能通过有效的控制模具温度来调节收缩率。
由于饭盒的主体要求牢固实用,生产量较大.主要是它螺钉孔的壁厚相对壁厚有一定的差距,势必会在注塑的时候到来很大的牛顿减力,造成塑件填充不满的缺陷,可以考虑采用一模四腔,利用侧浇口进胶.但应用了Pro/E的塑料顾问对其进行模仿CAE的注塑之后,发现会给饭盒的表面带来更多的熔接痕和气孔。
也可以利用模具的可靠的精度来定位,但是这样的话成本太高,而且易造成模具损坏。
因为考虑到凹凸模形状的简单,利用整体形式方便脱模,减少了对侧向的抽芯机构.解决这些问题,大大增加了效率.
(2)材料分析
饭盒所用的原料为ABS。
丙烯腈-丁二烯-苯乙烯共聚物ABS树脂微黄色或白色不透明,是丙烯腈-丁二烯-苯乙烯共聚物。
丙烯腈使聚合物耐油,耐热,耐化学腐蚀,丁二烯使聚合物具有优越的柔性,韧性;
苯乙烯赋予聚合物良好的刚性和加工流动性。
因此ABS树脂具有突出的力学性能和良好的综合性能。
ABS无毒、无味,呈微黄色,成型的塑料件有较好的光泽。
密度为1.02-1.05g/cm3.ABS有极好的抗冲击强度,且在低温下也不迅速下降。
水、无机碱、酸类对ABS几乎无影响;
ABS塑料表面受冰醋酸、植物油等化学药品的侵蚀会引起应力开裂。
ABS有一定的硬度和尺寸稳定性,易于成型加工。
其特点是耐热性不高。
连续工作温度为70℃左右,热变形温度约为93℃左右。
耐气候性差、在紫外线作用下易变形发脆。
成型特点:
ABS在升温时粘度增高,所以成型压力较高,ABS吸湿强、成型加工前应进行干燥处理;
易产生熔接痕,模具设计时应注意尽量减少浇注系统对料流的阻力;
在正常的成型条件、壁厚、熔料温度及收缩率影响极小。
要求塑件精度高时,模具温度可控制在50-60℃。
要求塑件光泽和耐热性时,应控制在60-80℃。
ABS的成型特性与工艺参数如表1.1所示:
ABS塑料主要的性能指标:
表1.1:
项目/单位
值
密度(Kg.dm-3)
1.13——1.14
收缩率%
0.3~0.8
熔点℃
130~160
热变形温度45N/cm
65~98
弯曲强度Mpa
80
拉伸强度MPa
35~49
拉伸弹性模量GPa
1.8
弯曲弹性模量Gpa
1.4
压缩强度Mpa
18~39
缺口冲击强度kJ/㎡
11~20
硬度HR
R62~86
体积电阻系数Ωcm
1013
击穿电压Kv.mm-1
15
介电常数
60Hz3.7
二、
注射机的初步拟定
(1)选择注射机
根据工厂现有的条件,并考虑到该制品的结构特征,这里初步选择HS150A型注射机,该注射机的技术参数如下表2.1所示:
表2.1HS150A注射机主要技术参数表:
机型MODEL
单位
HS150A
注射重量(按PS计算)
OZ
11
ShotWeightofInjection(ps)
g
311
螺杆直径
mm
45
注射体积
CM3
325
注射行程
210
注射压力
kg/c㎡
2300
螺杆转速
R.P.M.
10-190
锁模力
TON
150
四柱内空间
410X410
开模行程
360
模板最大开距
820
容模厚度
203-460
顶出力
4.5
顶出行程
90
油缸容量
Litre
340
电热功率
KW
10.8
电马达功率
机身重量
5
付船尺码
m
4.8X1.3X2
3、模具结构方案的确定
3.1分型面的确定
分型面的选择原则:
(1)分型面应选择在塑件外形最大轮廓处。
(2)确定有利于的留模方式,便于塑件顺利脱模。
(3)保证塑件的精度要求。
(4)满足塑件的外观质量要求。
(5)便于模具加工制造。
(6)对成型面积的影响。
(7)有利于提高排气效果。
(8)对侧向抽芯的影响。
综合考虑以上分型面的选择原则,结合制品的结构形状,该塑料饭盒的分型面设计如图3.1.1所示:
图3.1.1饭盒制件示意图
3.2型腔的布局方案的比较与确定
型腔的布置方案常用的有两种,第一种方案为平衡式,该方案特点是从主流道到各型腔浇口的分流道的长度,截面形状尺寸均对应相同,可实现均衡进料和同时充满型腔的目的。
第二种方案为非平衡式,该方案特点是从主流道到各型腔浇口的分流长度不相等,因而不利于平均衡进料,但可以缩短流道的总长度,为达到同时充满型腔的目的,各浇口的截面尺寸制作不相同。
该模具布置为一模四腔,平衡式布置如图3.2.1所示:
图3.2.1平衡式布置
非平衡式布置如图3.2.2所示:
图3.2.2非平衡式方案
该模具选择图3.2.1所示平衡式方案。
3.3浇注系统形式和浇口的设计
普通浇注系统由主流道、分流道、浇口和冷料井组成。
在设计浇注系统之前必须确定塑件成型位置,可以才用一模两腔,浇注系统的设计是注塑模具设计的一个重要的环节,它对注塑成型周期和塑件质量(如外观,物理性能,尺寸精度)都有直接的影响,设计时要遵循如下基本原则:
(1)了解塑料的成型性能和塑料熔体的流动性。
(2)采用尽量短的流程,以减少热量与压力损失。
(3)浇注系统设计应有利于良好的排气。
(4)防止型芯变形和嵌件位移。
(5)便于修整浇口以保证塑件外观质量。
(6)浇注系统应结合型腔布局同时考虑。
(7)流动距离比和流动面积比的校核。
3.3.1主流道的设计
主流道是浇注系统中从注射机喷嘴与模具相接触的部位开始到分流道为止的塑料熔体的流动通道。
主流道部分在成型过程中,其小端入口处与注射机喷嘴有一定温度、压力的塑料熔体要冷热交替地反复接触,属易损件,对材料的要求较高,因而模具的主流道部分常设计成可拆卸更换的主流道衬套式(俗称浇口套)以便有效地选用优质钢材单独进行加工和热处理。
一般采用碳素工具钢如T8A、T10A等,热处理要求淬火53-57HRC。
浇口套应设置在模具的对称中心位置上,并尽可能保证与相联接的注射机喷嘴为同一轴心线。
主流道的设计要点如下:
(1)截面形状为圆形,整体形状为圆锥形。
(2)锥度a=2°
--6°
一般取(2°
--4°
)。
(3)小端孔径=喷嘴孔径+(0.5-1)mm。
(4)球面半径=喷嘴球面半径+(1-2)mm。
SR=Sr+(1-2)mm。
(5)主流道长度L尽量短。
(6)内表面粗糙度小于等于0.8微米。
(7)主流道末端与分流道相接处采用圆弧过渡r=1-3mm。
(8)球面配合高度H=3-5mm。
该模具的主流道设计如下图3.3.1所示:
图3.3.1浇口套结构图
3.3.2分流道的设计
分流道是指主流道末端与浇口之间这一段塑料熔体的流动通道。
一般开在分
型面上,起分流和转向的作用。
分流道截面的形状可以是圆形、半圆形、矩形、梯形和U形等,圆形和正方形截面流道的比面积最小(流道表面积于体积之比值称为比表面积),塑料熔体的温度下降小,阻力小,流道的效率最高。
但加工困难,而且正方形截面不易脱模,所以在实际生产中较常用的截面形状为梯形、半圆形及U形。
分流道设计要点:
(1).在保证足够的注塑压力使塑料熔体能顺利的充满型腔的前提下,分流道截面积与长度尽量取小值,分流道转折处应以圆弧过度。
(2).分流道较长时,在分流道的末端应开设冷料井。
对于此模来说在分流道上不须开设冷料井。
(3).分流道的位置可单独开设在定模板上或动模板上,也可以同时开设在动,定模板上,合模后形成分流道截面形状。
(4).分流道与浇口连接处应加工成斜面,并用圆弧过度。
分流道的长度
分流道的长度取决于模具型腔的总体布置方案和浇口位置,从在输送熔料时减少压力损失,热量损失和减少浇道凝料的要求出发,应力求缩短。
分流道的断面
分流道的断面尺寸应根据塑件的成形的体积,塑件的壁厚,塑件的形状和所用塑料的工艺性能,注射速率和分流道长度等因素来确定。
因ABS的推荐断面直径为4.5~9.5(查表5-3),部分塑件常用断面尺寸推荐范围。
分流道要减小压力损失,希望流道的截面积大,表面积小,以减小传热损失,同时因考虑加工的方便性。
分流道应考虑出料的流畅性和制造方便,熔融料的热量损失小,流动阻力小,比表面和小等问题,由于采用的是潜伏式二级分流道对热损失及流动提出了较高的要求,采用圆形的份流道,为了保证外形无浇口痕,浇口前后两端形成较大的压力差,增加流速,得到外形清晰的制件,提高熔体冷凝速度,保证熔融的塑料不回流,同时可隔断注射压力对型腔内塑料的后续作用,冷却后快速切除。
同时它的效果与S浇注系统有同样的效果,有利于补塑。
该模具设计分流道方案如图3.3.2所示:
图3.3.2分流道的设计方案
3.3.3浇口的设计
浇口亦称进料口,是连接分流道与型腔之间的一段细短流道(除直接浇口外),它是浇注系统的关键部分。
其主要作用是:
(1)型腔充满后,熔体在浇口处首先凝结,防止其倒流。
(2)易于在浇口切除浇注系统的凝料。
浇口截面积约为分流道截面积的0.03~0.09,浇口的长度约为0.5mm~2mm,取其下限值,然后在试模是逐步纠正。
常用浇口形式主要分为11种形式:
(1)直接浇口
(2)侧浇口(3)扇形浇口(4)平缝浇口(5)环形浇口(6)盘形浇口(7)轮辐浇口(8)爪形浇口(9)潜伏浇口(10)护耳浇口(11)点浇口
该制品选择的是侧浇口。
当塑料熔体通过浇口时,剪切速率增高,同时熔体的内磨檫加剧,使料流的温度升高,粘度降低,提高了流动性能,有利于充型。
但浇口尺寸过小会使压力损失增大,凝料加快,补缩困难,甚至形成喷射现象,影响塑件质量。
浇口位置的选择原则:
(1)尽量缩短流动距离。
(2)浇口应开设在塑件壁最厚处。
(3)必须尽量减少或避免熔接痕。
(4)应有利于型腔中气体的排除。
(5)考虑分子定向的影响。
(6)避免产生喷射和蠕动。
(7)不在承受弯曲或冲击载荷的部位设置浇口。
(8)浇口位置的选择应注意塑件外观质量。
该模具选择如图3.3.3所示:
浇口设计方案如图3.3.3所示
3.3.4冷料穴设计
冷料穴位于主流道正对面的动模板上,或处于分流道末端,其作用是接受料流前锋的“冷料”,防止“冷料”进入型腔而影响塑件质量,开模时又能将主流道的凝料拉出。
冷料穴的直径宜大于大端直径,长度约为主流道大端直径。
基于本次设计的模具,可采用底部带有拉料杆的冷料穴,这类冷料井穴的底部由一个拉料杆构成。
拉料杆装于型芯固定板上,因此它不能随脱模机构运动。
利用球头形的拉料杆配合冷料穴。
该冷料穴如附录三模具总装图所示。
3.4成型零部件系统的设计
此成型零部件的作用是决定塑件的内外表的形状,尺寸和尺寸精度。
其凹模是成型塑件外表面的主要零件;
凸模和型芯均是成型塑件内表面的零件,按其结构不同可分为整体式和组合式两类。
整体式结构牢固,但不便于加工,消耗的模具钢多,维修价格高,主要用于工艺试验模或小型模具上的形状、简单的。
组合式结构便于加工,消耗的模具钢少,维修方便,方法是将型芯单独加工,再镶入模板中,用垫板螺钉紧固。
该模具成型零部件系统采用整体式机构,如附录二型芯与型腔零件图所示。
3.5温度调节系统
在注射成型过程中,模具温度直接影响到塑件的质量如收缩率、翘曲变形、耐应力开裂性和表面质量等,并且对生产效率起到决定性的作用,在注射过程中,冷却时间占注射成型周期的约80%,然而,由于各种塑料的性能和成型工艺要求不同,模具温度的要求有尽相同,因此,对模具冷却系统的设计及优化分析在一定程度上决定了塑件的质量和成本,模具温度直接影响到塑料的充模、塑件的定型、模塑的周期和塑件质量,而模具温度的高低取决于塑料结晶性,塑件尺寸与结构、性能要求以及其它工艺条件如熔料温度、注射速度、注射压力、模塑周期等。
影响注射模冷却的因素很多,如塑件的形状和分型面的设计,冷却介质的种类、温度、流速、冷却管道的几何参数及空间布置,模具材料、熔体温度、塑件要求的顶出温度和模具温度,塑件和模具间的热循环交互作用等。
(1)低的模具温度可降低塑件的收缩率。
(2)模具温度均匀、冷却时间短、注射速度快,可降低塑件的翘曲变形。
(3)对结晶性聚合物,提高模具温度可使塑件尺寸稳定,避免后结晶现象,但是将导致成型周期延长和塑件发脆的缺陷。
(4)随着结晶型聚合物的结晶度的提高,塑件的耐应力开裂性降低,因此降低模具温度是有利的,但对于高粘度的无定型聚合物,由于其耐应力开裂性与塑料的内应力直接相关,因此提高模具温度和充模,减少补料时间是有利的。
(5)提高模具温度可以改善塑件的表面质量。
在注射成形过程中,模具的温度直接影响塑件的成型质量和生产效率,根据塑料的要求,注射到模具内的塑料温度为2000C左右,而从模具中取出塑件的温度约为600C,温度降低是由于模具通入冷却水,将温度带走了,普通的模具通入常温的水进行冷却,通过调节水的流量就可以调节模具的温度。
因饭盒使用的塑料是ABS,要求模温高,若模具温度过低则会影响塑料的流动性,增加剪切阻力,使塑件的内应力较大,甚至还出现冷流痕、银丝、注不满等缺陷。
因此在注射开始时,为防止填充不足,充入温水或者模具加热。
总之,要做到优质、高效率生产,模具必须进行温度调节。
对温度调节系统的要求:
(1)确定加热或是冷却;
(2)模温均一,塑件各部分同时冷却;
(3)采用低的模温,快速且大量通冷却水;
温度调节系统应尽量结构简单,加工容易,成本低谦。
根据模具冷却系统设计原则:
冷却水孔数量尽量多,尺寸尽量大的原则可知,冷却水孔数量大于或等于3根都是可行的。
这样做同时可实现尽量降低入水与出水的温度差的原则。
根据书上的经验值取4根,冷却水口口径为8mm.另外,冷却系统的过程中,还应同时遵循:
(1)冷却水道应尽量多,截面尺寸应尽量大。
(2)冷却水至型腔表面距离应尽量相同。
(3)浇口处加强冷却。
(4)冷却水道出入口温差应尽量小。
(5)冷却水道应沿着塑料收缩的方向设置。
(6)冷却水道的设计还必须尽量避免接近塑件的熔接部位,以免产生熔接痕,降低塑件强度。
(7)冷却水道要易于加工清理,一般水道孔径为10毫米左右(不小于8毫米)
(8)冷却水道设计要防止冷却水泄漏,凡是易漏的部位要加密封圈。
其冷却系统结构如图3.5.1所示
图3.5.1模具的冷却系统结构示意图
3.6顶出机构的确定
塑件从模具上取下以前,还有一个从模具的成型零件上脱出的过程使塑件从成型零件上脱出的机构称顶出机构。
顶出机构可以分为:
(1)推杆推出机构。
(2)推管推出。
(3)推件板推出机构。
(4)活动镶块及模推出。
(5)多元综合推出机构。
设计原则:
(1)推出机构应尽量设置在动模一侧。
(2)保证塑件不因推出而变形损坏。
(3)机构简单动作可靠。
(4)良好的塑件外观。
(5)合模时的正确复位。
该制件的内表面顶部要求的粗糙度不高,所以选择顶杆顶出机构。
顶杆多用T8AV、T10A材料,头部淬火硬度达50HRC以上,表面粗糙度取Ra值小于0.8微米,和顶杆孔呈H8/f8配合。
位置的设置:
(1)应设在脱模阻力大的地方。
(2)应均匀布置。
(3)应设在塑件强度刚度较大处。
如下图3.6.1所示:
图3.6.1顶出机构示意图
3.7其它系统与结构
3.7.1合模导向机构
合模导向机构对于塑料模具是必不可少的部分,因为模具在闭合时要求有一定的方向和位置,所以必须设有导向机构,导柱安装在动模一边或定模一边均可,通常导柱设在主型腔周围。
导向机构的主要作用有:
定位、导向和承受一定侧压力。
定位作用:
为避免装配时方位搞错而损坏模具,并且在模具闭合后使型腔保持正确形状,不至因为位置的偏移而引起塑件壁厚不均。
塑件在注入型腔过程中会产生单向侧压力,或由于注射机的精度限制,使导柱工作中承受一不定的导向作用。
动定模合模时,首先导向机构接触,引导动定模正确闭合,避免凸模或型芯先进入型腔,产生干涉而坏零件。
由于注塑压力的各向性就会对导柱进行径向的剪力,导致导柱容易折断。
对型芯和型腔改进后,其的配合可以进行定位。
导柱、导套零件如下图3.7.1所示:
图3.7.1导柱.导套示意图
3.7.2模架的选定
根据塑件选定模架为:
S3540—CI—50—60—90。
见图2.1:
图2.1模架的选择
3.7.3排气引气系统设计
塑料熔体在填充模具的型腔过程中同时要排出型强及流道原有的空气,除此以外,塑料熔体会产生微量的分解气体。
这些气体必须及时排出。
否则,被压缩的空气产生高温,会引起塑件局部碳化烧焦,或塑件产生气泡,或使塑件熔接不良引起强度下降,甚至充模不满。
该模具设计为分型面排气,零件间隙排气。
四.模具中相关的校核
4.1注射机与模具尺寸的关系校核
4.1.1最大注射压力的校核
饭盒的原料为ABS,所需注射为70-90MPa,而所选注射机压力为2300kg/c㎡,所以注射压力符合要求。
(1)最大注塑量的校核
注塑机的最大注塑量应大于制品的质量或体积(包括流道及浇口凝料和飞边),通常注塑机的实际注塑量最好是注塑机的最大注塑量的80%。
所以选用的注塑机最大注塑量应满足:
0.8V机≥V塑+V浇
式中V机————注塑机的最大注塑量,325cm3
V塑————塑件的体积,该产品V塑=150c