焊接接头Word文档下载推荐.docx
《焊接接头Word文档下载推荐.docx》由会员分享,可在线阅读,更多相关《焊接接头Word文档下载推荐.docx(10页珍藏版)》请在冰豆网上搜索。
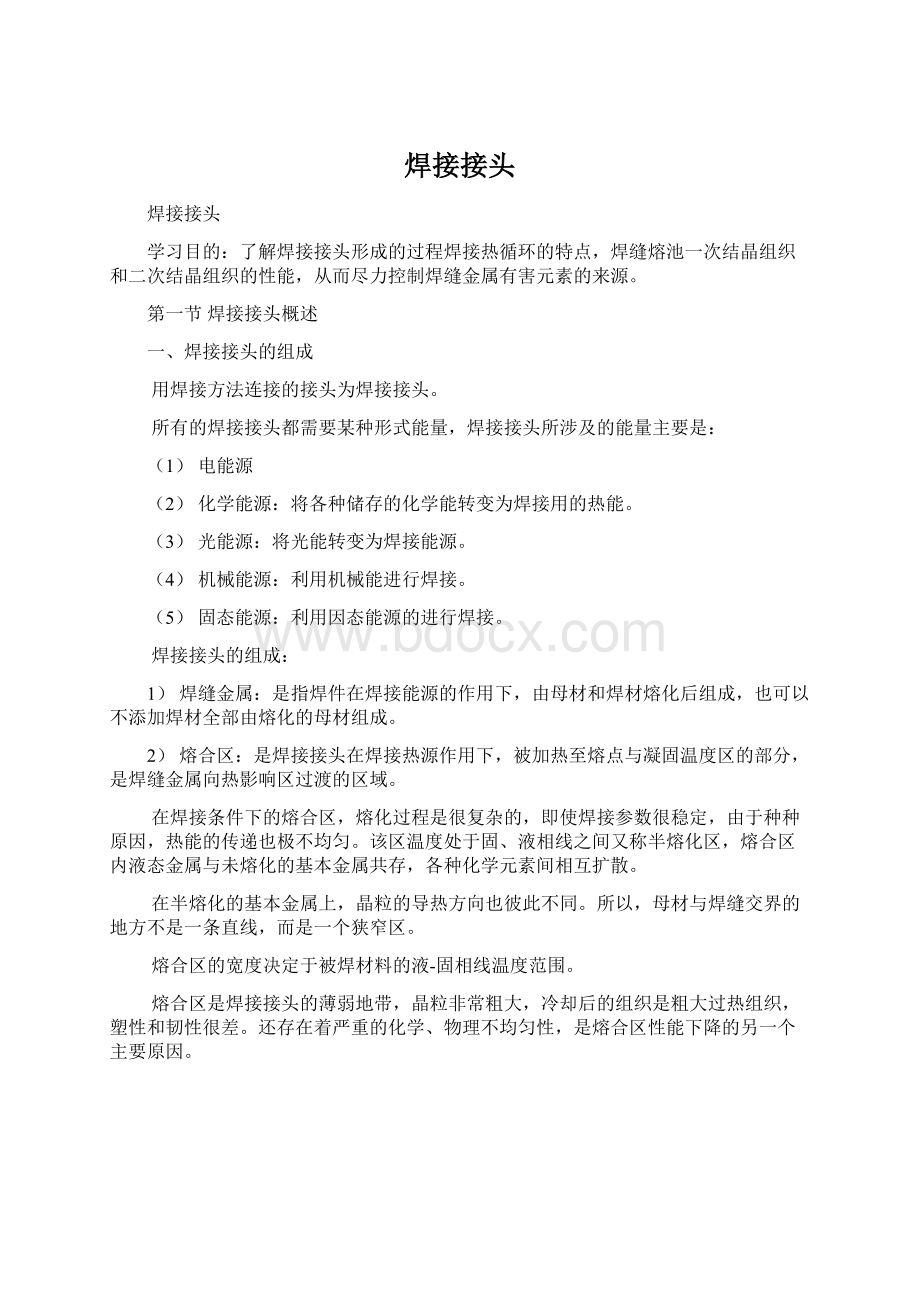
3)热影响区:
母材在焊接过程中因受加热的影响(但还没有熔化),而发生的金相组织和力学性能变化的区域。
焊接接头是整个焊接结构的重要部位,焊缝的性能决定于焊缝的化学性能和组织;
焊接热影响区域性能的变化决定于组织变化,而母材的组织变化又决定于在焊接过程中对母材的加热和冷却,即焊接热循环。
二、焊接接头的形式
1.对接接头:
是指两件表面构成大于135°
,小伙于或等于180°
夹角的接头;
2.搭接接头:
是指两件部分重叠构成的接头;
3.角接接头:
是指两件表面构成大于30°
、小于135°
4.T形接头:
是指一件之端面与另一件表面构成直角的接头;
5.端接接头:
是指两件重叠放置或两件表面之间的夹角不大于30°
构成的端部接头;
第二节焊接热循环概述
一、焊接热循环的特点
热能传递方式主要有传导、对流、辐射三种。
在利用电弧热进行焊接时,电弧热传递给焊件的方式是传导和辐射。
由于在焊接过程热源在不断的移动,不同的距离、不同的时刻焊件各点的温度都是不同的。
焊接温度场,是焊接过程中的某一瞬间在焊件上各点的温度分布
焊接温度场能反映出焊件温度在某一瞬间在空间的分布情况,但不能说明焊件上各点温度随时间变化的情况。
这种反映焊件上的某一点,在焊接热源的作用下,其温度随着时间的变化由高到低的过程为焊接热循环。
焊接热循环的主要参数是加热速度、加热最高温度、禁止变温度以上的停留时间和冷却速度。
特征:
1)虽然焊接过程加热温度高,加热速度和冷却速度都大,但是,加热速度比冷却速度更大。
2)焊件各点的热循环不同,越靠近焊缝中心位置,,峰值温度越高,加热温度和冷却温度也越大,反之亦然。
二、影响焊接热循环的温度的因素
(1)焊接热输入:
是综合焊接电流、电弧电压、焊接速度的参数,当焊接电流或电弧电压越大,而焊接速度不变或减小,则焊接热输入越大;
当焊接速度越大,而焊接电流或电弧电压不变或减小,则焊接热输入越小。
由此,焊接热输入越大,在高温停留的时间就越长,焊后冷却速度也就变慢。
焊接热输入变小,在高温停留时间也变短,焊后的冷却速度将变快。
(2)焊接方法:
焊接方法不同,加热速度、高温停留时间、焊后冷却速度及焊接热输入都有所不同。
不同焊接方法的热输入
焊接方法
焊接电流
电弧电压
焊接速度
焊接热输入
焊条电弧焊
180
24
0.25
17280
(3)焊前预热在焊接热输入相同的情况下,焊前预热可以降低焊后冷却速度。
但是,不会增加在高温停留的时间。
所以焊前预热不会使焊弧组织晶粒粗化加剧,力学性能变差。
相反却可以避免焊缝组织淬硬。
(4)层间温度:
层次温度与焊前预热的作用相同。
(5)其他因素:
1)焊件厚度增加时,焊件在高温停留的时间减小,冷却速度加快。
2)接头形式的影响:
由于接头的散热面的不同,冷却速度各不相同。
3)热导率的影响:
热导率大的材料,冷却速度快,焊件在高温停留的时间短;
反之。
第三节焊缝金属的组织与性能
一、焊缝熔池的一次结晶
1.焊缝一次结晶的特点
焊缝熔池的结晶都经过晶核生成和长大的过程。
有如下特征:
(1)焊缝熔池小,冷却速度快;
(2)焊缝熔池中的液态金属处于过热状态;
(3)焊缝熔池金属是在运动状态下结晶;
2.焊缝熔池一次结晶组织的特征:
是从熔合线未完全熔化的晶粒上开始,沿着垂直熔合线的方向,向与散热方向禁止反的方向长大,形成柱状晶。
1.焊缝熔池一次结晶的组织性能
由液态凝固后所得到的组织是一次组织,而在室温显微镜下所观察到的焊缝组织都是二次组织。
要观察一次组织时,必须用特殊的浸蚀方法才能将它显示出来。
焊缝对一次结晶时性能的影响是很吸显的。
粗大的柱状晶不但降低焊缝的温度,而且还降低焊缝的韧性。
此外,焊缝的一次结晶形态还对产生裂纹、气孔、夹渣、腐蚀都有很大的影响。
2.焊缝中的偏析
焊接过程中,由于冷却速度过快,焊缝熔池在结晶时,其化学成分还来不及扩散均匀就已凝固,出现偏差;
此外,还有一些非金属夹杂物,因来不及浮出熔池表面残存在在焊缝内也形成偏差。
焊缝中的偏差,常常是力学性能最薄弱的地带。
焊缝中的偏析分3种
1)显微偏析:
焊缝熔池在结晶过程中,先结晶的固相比较纯,后结晶的固相含合金元素和杂质略高,最后结晶的固相含合金元素和杂质最高。
影响显微偏析的主要因素是金属的化学成分。
2)区域偏析:
焊缝熔池在结晶时随着电弧向前移动,熔池中的柱状晶也在不断的推移和大,此时会把未凝固的合金成分和杂质推向焊缝熔池中心,使中心的杂质浓度逐渐升高形成区域偏析。
3)层状偏析:
在焊缝断面上,不同分层的化学成分分布不均匀的现象为层状偏析
焊缝熔池结晶时,在结晶前沿的液体金属中,熔质的浓度较高,同时也集结一些杂质,当冷却速度较慢时,这一层的浓度较高的熔质和杂质可以通过扩散来减轻偏析的程度;
当泠却速度较快时,浓度较高的熔质和杂质还没来不及“均匀化”就已凝固,使这个区域形成层状偏析。
二、焊缝金属的二次结晶
1.二次结晶的组织
焊缝熔池金属一次结晶结束后,熔池金属将转变为固体焊缝。
随高温的焊缝金属被逐渐冷却到室温,焊缝金属组织将进一步发生转变,这种组织变化的过程为焊缝金属的二次结晶。
2)二次结晶组织的性能
1)从塑性、韧性看出,奥氏体组织在温度下降的时候,没有明显的脆性转变现象,塑性、韧性、比其它组织好;
铁素体加珠光体组织次之;
珠光体组织的强度比铁素体组织高,塑性,韧性比铁素体组织低;
下贝氏体组织既具有较高的强度,又有较好的韧性;
粒状氏体组织的强度较低,但韧性较好,上氏体组织韧性最差;
高碳马氏体则既有相当好的强度,又有相当好的塑性和韧性。
2)从抗裂性能看:
铁素体组织加珠光体组织和奥氏体组织的抗裂性能较好;
奥氏体组织加少量铁素体组织的双相组织抗裂性能比单相奥氏体组织更好;
贝氏体组织、贝氏体组织加马氏体组织则对冷裂纹的敏感性最大。
3)焊缝金属的二次结晶组织越均匀、越细,与粗大而不均匀的焊缝金属二次相比,其力学性能就越好。
三、焊接热影响区的组织与性能
热影响区:
把焊接材料因受热的影响(但没有熔化),而发生金相组织力学性能变化的区域。
焊接热循环:
是在焊接热源的作用下,焊件上的某点温度随时间变化(即温度由低到高,达到最高值后,又由高到低)的过程。
焊接是一个不均匀加热和冷却的过程,从而使焊接热影响区形成一个不均匀的组织和性能,产生复杂的应力和应变。
由于母材的成分不同,在焊接热影响区各点经受的热循环不同,使焊后热影响区发生的组织和性能变化也不相同,主要有2种:
1.不易淬火钢热影响区组织;
2.易淬火钢热影响区组织;
3.焊接热影响区的性能
(1)硬度变化:
热影响区熔合线附近的硬度最高,而离深合线越远的地方就越接近被焊金属基体的硬度。
说明熔合线附近金属的塑性最差,是焊接的薄弱地带。
(2)强度和塑性变化:
在1200°
C左右的粗晶区,其硬度和强度都高于被焊金属,而塑性则低于被焊金属。
在700-900°
C的区域中,屈服点稍低于被焊金属。
(3)韧性变化:
通常焊接热输入越大,高温停留时间越长,晶粒越粗大,韧度降低越明显。
第四节改善焊接接头性能的方法
一、选择合适的焊接工艺方法
同一接头、同一材料采用不同的焊接方法、焊接工艺,焊接接头的性能会有很大的差异。
所以,选择合适的焊接工艺方法应根据对焊接接头性能的影响及其他要求,综合考虑对焊接工艺、焊接方法的合理选择。
二、选择合适的焊接参数
焊接过程中,焊缝熔池中晶粒成长方向,会随着焊接速度的变化而改变。
当焊接电流一定时,不同的焊接电流对焊缝熔池的结晶形成、也有较大的影响。
焊接电流较小时(150A)P容易得到胞状晶;
电流增大时(300A)得到胞状树枝晶;
继续增大时(450A)会得到粗大的胞状枝晶组织,影响焊接接头的力学性能。
此外焊接参数时焊缝形成系数也有较大的影响,大焊接电流、中等速度焊接速度时得到咬宽的焊缝;
小电流时、快速焊接时,焊缝的宽度将变敞。
三、选择合适的焊接热输入
焊接热输入的大小,不仅影响焊接接头的热循环特性。
而且还对焊接接头的组织和脆化倾向及冷裂倾向有限影响,各类钢的脆化倾向和冷裂倾向是不同的。
四、选择合理的焊接操作方法
采用多层焊或多层多道焊,既可以减小每层焊道层的厚度,改善焊接接头的热输入,可以利用又每层焊缝的附加热外理作用,改善焊接接头的力学性能。
五、正确选择焊接材料
同种钢结构焊接时,按与钢材抗拉强度等强的原则选用焊接材料;
异种结构钢焊接时,按强度较低的钢训选用焊接材料。
对于承受动载荷的焊接接头,要选用熔敷金属具有较高冲击韧度的焊接材料;
对于承受静载荷的焊接接头,只要选用抗拉强度与被焊金属相当的焊接材料可以了。
六、正确选择焊后热外理方法
正确选择焊后热外理方法,可以消除或减少焊接残余应力;
消除焊缝中的氢,防止产生延迟裂纹;
提高焊缝金属抗应力腐蚀的能力;
对焊接热影响区进行回水软化;
提高焊缝金属抗拉强度、冲击韧度和蠕变强度;
提高焊接结构尺寸的稳定性。
一、控制熔合比
被熔化的母材在焊缝金属中所占的百分比为熔合比。
就是在焊后获得所希望得到的焊缝金属化学成分和组织及性能。
第五节焊缝金属中的有害元素
一、焊缝金属中的氧
1.氧的来源
在正常情况下,焊缝中的氧主要来源于焊接材料中的水分、焊件周围的水分、焊件和焊丝表面上的铁锈、氧化膜等,而不是来源于焊接热源周围的空气。
氧在焊缝金属中的存在形式主要是FeO。
2.氧对焊缝的影响
焊缝中的含氧量增加,不仅焊缝的强度、塑性、韧性明显下降,还会引起红脆、冷脆和时效硬化。
对金属的物理和化学性能也有影响使导电性、导磁性和抗腐蚀性能等下降。
3.控制氧的措施
(1)纯化焊接材料:
尽量用不含氧或含氧少的焊接材料。
(2)正确选择焊接参数:
尽量采用短弧焊接、合适的保护气体流量、焊接速度,焊接电流选择要合理。
(3)脱氧反应:
在焊丝、焊剂、或焊药中加入合适的元素。
二、焊缝金属中的氢
1.氢的来源
来源于焊接材料中的水分、含氢物质、电弧周围空气中的水蒸气、焊丝和被焊金属表面的铁锈、油污等。
2.氢对焊缝的影响
(1)氢脆:
氢在室温附近使钢的塑性严重下降的现象为氢脆。
白点:
含氢量较高,则常常在其拉伸或弯曲断面上,出现银白色的圆形局部脆断点。
(2)气孔:
熔池吸收大量的氢,结晶时,由于熔解度的下防,使氢外于饱和状态,氢不熔于金属,于是在液态金属中形成气泡沫,当气泡向外勉出速度小于液态金属结晶速度时,气泡就留在焊缝中形成气孔。
(3)冷裂纹:
焊接接头冷却到较低的温度下产生的一种裂纹。
也有限的冷裂纹在焊后要推迟很长的时间才产生,这种裂纹被称为延迟裂纹。
延迟裂纹的三种形态:
(1)焊趾裂纹:
起源于被焊金属和焊缝交界的应力集中处,裂纹的走向与焊道平行,由焊趾表面的应力集中处开始向被焊金属的深处扩展。
(2)焊道下裂纹:
一般走向与熔合线平行,也有的裂纹是垂直熔合线的,这种裂纹经常产生在淬硬倾向大、含氢量较高的焊接热影响区。
(3)根部裂纹:
起源于焊缝根部应力集中最大的部位,可能出现在焊接热影响区的粗晶部,或焊缝金属内。
主要发生在含氢较高、预热温度不足的情况下。
3.控制氢的措施
(1)限制焊接材料的含氢量;
(2)清除焊件和焊丝表面的杂质;
(3)进行冶金处理;
1)在焊条药皮和焊剂中加入氟化剂;
2)控制焊接材料的氧化还原势;
3)在焊条药皮或焊芯中加入微量的稀士元素;
4)控制焊接参数;
5)焊后脱氢处理;
三、焊缝金属中的氮
1.氮的来源
电弧周围空气中的气相氮是焊接区氮气的主要来源。
(1)不与氮气发生作用的金属;
(2)与氮气发生作用的金属;
2.氮对焊接的影响
氮是有害的杂质,它是促成焊缝产生气孔的主要原因。
3.控制氮的措施
(1)焊接区的保护影响:
焊条药皮中加入造气剂.
(2)焊接参数的影响:
1)尽量采用短弧焊接;
2)加大焊接电流;
3)增加焊丝直径。
(3)合金元素的影响:
增加焊丝或药皮中的碳元素。
四、焊缝金属中的硫
1.硫的来源
三个方面
(1)来自母材;
(2)来自焊丝;
(3)来自药皮或焊剂;
2.硫对焊缝的影响
硫是焊缝金属中有害杂质,增加焊缝裂纹,降低焊缝的冲击韧度和耐腐蚀性。
3.控制硫的措施
(1)严格限制焊接材料中的硫含量;
(2)用冶金方法进行脱硫;
五、焊缝金属中的磷
1.磷的来源
来自母材、药皮、填充金属和焊剂,而药皮和焊剂中的锰矿是导致焊缝增磷的主要来源。
2.磷对焊缝的影响
磷在焊缝中是有害杂质,降低冲击韧度,增大焊缝金属的冷脆性.
3.控制磷的措施
1)严格限制焊接材料中的磷含量
2)采用脱磷的方法:
(1)将磷生成氧化磷
(2)使渣中的碱性氧化物生成稳定的磷酸盐。
复习思考题
1.焊接接头按接头的构造形式分为几大类?
2.焊接接头在焊接结构中的作用如何?
3.对接接头受力状况如何?
4.搭接接头的受力状况如何?
5.什么是角接头?
6.什么是端接头?
7.常用的坡口形式有哪几种?
8.简述对接接头的坡口尺寸及符号。
9.简述角焊缝各部分名称。
10.焊接参数时焊缝形状的影响?
11.焊缝的外现质量有何要求?