铝合金压铸件浇注系统优化设计论文Word格式文档下载.docx
《铝合金压铸件浇注系统优化设计论文Word格式文档下载.docx》由会员分享,可在线阅读,更多相关《铝合金压铸件浇注系统优化设计论文Word格式文档下载.docx(38页珍藏版)》请在冰豆网上搜索。
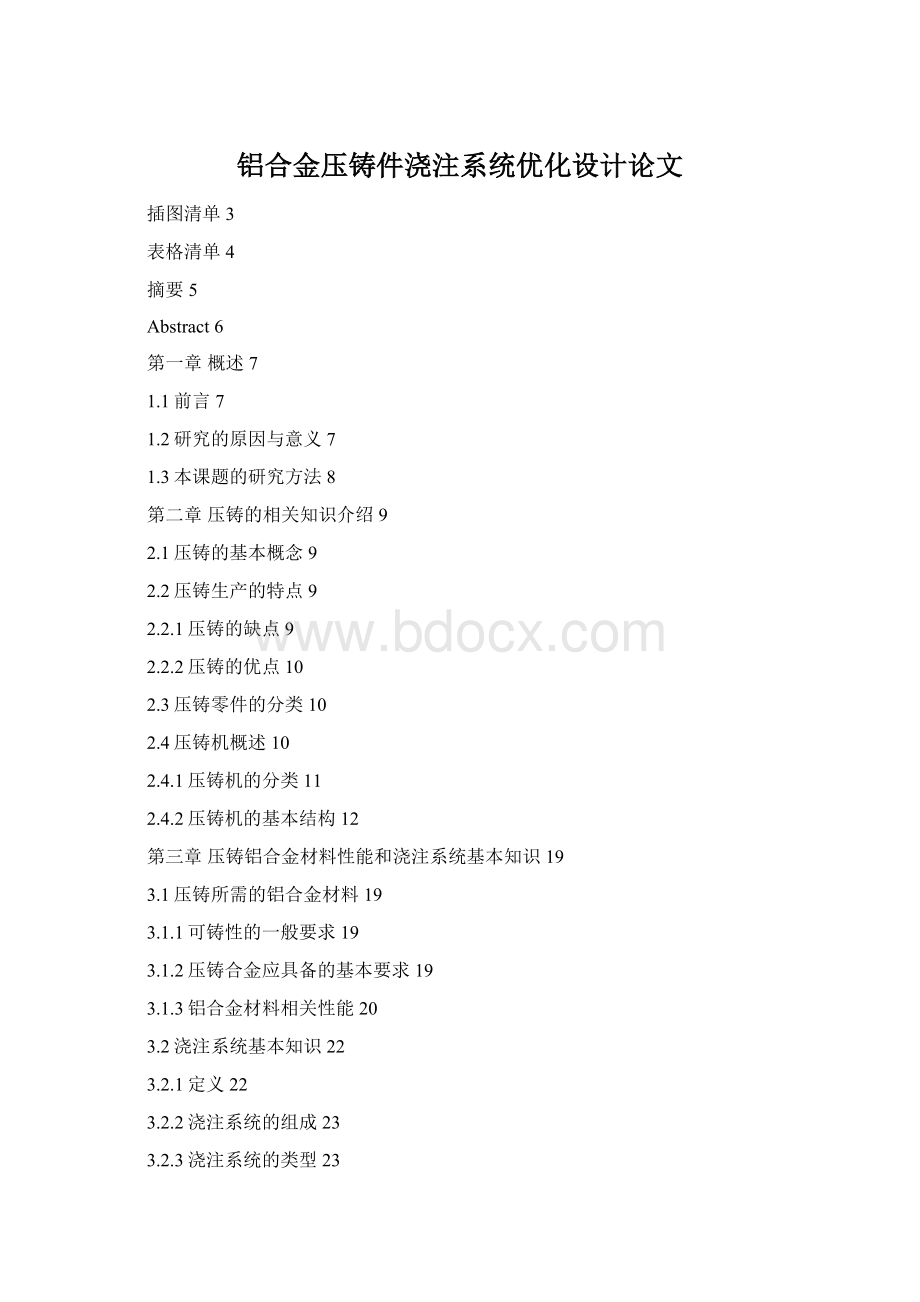
4.1.3铸造数值模拟原理25
4.2ProCAST软件功能简介27
4.2.1ProCAST软件的原理和适应范围28
4.2.2ProCAST软件的特点28
4.2.3ProCAST软件应用概况28
第五章运用ProCAST软件模流分析和选定浇注系统30
5.1ProCAST软件模拟分析步骤30
5.2浇道系统设计所遵守的一般原则31
5.3浇注系统类型的选择31
5.3模拟浇注系统流程32
参考文献40
致谢41
插图清单
图1-1铸造工艺过程简图7
图1-2凹陷7
图1-3气孔缺陷7
图2-1冷室压铸机11
图2-2热室压铸机12
图2-3压射机构原理图12
图2-4冷室压射机结构示意图13
图2-5压铸不同阶段,金属液所受压力的变化情况14
图2-6压射过程示意图16
图2-7压射过程及压射过程曲线17
图4-1数值离散方法示意图21
图4-2铸造过程数值模拟系统的组成24
图5-1ProCAST模拟流程图26
图5-2ProCAST软件工作主界面27
图5-3单浇口式扇形浇道27
图5-4双浇口式扇形浇道27
图5-5模拟浇注系统流程图28
图5-6网格划分图28
图5-7运行参数设置图29
图5-8单浇口式充填率0%时的温度场图30
图5-9单浇口式充填率20%时的温度场30
图5-10单浇口式充填率40%时的温度场30
图5-11单浇口式充填率60%时的温度场30
图5-12单浇口式充填率80%时的温度场31
图5-13单浇口式充填率100%时的温度场31
图5-14双浇口式充填率0%时的温度场31
图5-15双浇口式充填率20%时的温度场31
图5-16双浇口式充填率40%时的温度场32
图5-17双浇口式充填率60%时的温度场32
图5-18双浇口式充填率80%时的温度场32
图5-19双浇口式充填率100%时的温度场32
图6-1改善前后对比图33
表格清单
表2-1常见压铸缺陷及其影响因素8
表2-2部分压铸机的压射力及压射冲头尺寸与压射比压的关系14
表3-1压铸铝合金的化学成分和力学性能表(GB/T15115—1994)19
表3-2压铸铝合金中主要元素的作用19
表3-3中国与主要工业国家压铸铝合金牌号对应表20
表3-4冷压铸各类浇注系统的结构及特点22
表4-1ProCAST软件在我国的主要用户25
表5-1各参数设置表29
铝合金压铸件浇注系统优化设计
摘要
压力铸造是一种热加工成型工艺,它的机械化程度高的很,它在生产中的效率也是很高的。
它的最主要特点是高压、高速。
同时呢,这也是它区别其他铸造方法最本质的地方。
由于压铸的高速度、高压力和充型时间短的特点,所以,压铸件容易产生气孔、塑孔、浇不足、未浇满、热裂、冷裂等缺陷。
这些缺陷的产生与生产过程中所用的压铸模设计有密切的关系。
我们以前改进压铸模设计的方法主要为试误法和经验法,但是这些方法需要大量的实验,既消耗了大量的人力物力财力,也很难得到优良的先进的工艺生产参数。
本文首先利用CAE(ProCAST)数值模拟软件分析缩孔、浇不足、应力、裂纹、裹气、冲砂、变形等缺陷产生的原因,方便生产发现问题所在的地方,并且设计出优良的压铸工艺。
在模拟过程中,我们可以看到浇注的过程,在看的过程中发现问题所在。
这个使复杂的浇注系统变得透明和简单化,方便以后的生产研究、探讨和改进。
本文一共有五章,第一章简要介绍该课题研究的原因、意义和研究方法。
第二章介绍有关压铸法的基本知识。
第三章介绍了压铸所需的铝合金材料要求和浇注系统的基本知识。
第四章介绍铸造过程数值模拟理论和ProCAST软件。
第五章运用ProCAST软件进行模流分析,通过对比分析得出合理的浇注系统。
最后是结论和未来展望,对本文中所没有解决的问题给予指出说明,并且指出以后研究的目标和方向。
关键词:
压铸;
浇注系统;
模拟分析
Aluminumalloydiecastinggatingsystemoptimizationdesign
Abstract
Diecastingisakindofproductionefficiencyandhighmechanizationdegreearethehotworkingofmoldingprocess.Itsmaincharacteristicismetalunderhighpressure,highspeedtypefillingpressureofmouldcavity,andformingunderhighpressureandcrystallization.Highpressureandhighspeedisthemostfundamentaldifferencebetweencastingandothercastingmethod.Duetothehighspeed,highpressurediecastingandthecharacteristicsofthefillingtimeisshort,sothediecastingiseasytoproduceporosity,hole,misrun,notwater,thermalcrack,coldcrackandotherdefects.Thesedefectsgeneratedandusedduringtheproductionofdie-castingdiedesignhasacloserelationship.Weusedtoimprovediemolddesignmethodmainlyfortrial-and-errormethodandexperiencemethod,butthesemethodsneedalotofexperiments,bothcostalotofmanpower,materialandfinancialresourcesanditishardtogetgoodadvancedtechnologyproductionparameters.
Atfirst,thispaperUSESCAE(ProCAST)numericalsimulationsoftwareanalysisthestress,crack,shrinkagecavity,misrun,wrappedgas,sandwashing,thereasonsofthedefectssuchasdeformation,convenientproductionfindtheproblem,anddesignagooddiecastingtechnology.Intheprocessofsimulation,wecanseethatthecastingprocess,intheprocessofwatchingfindtheproblem.Thismakescomplicatedgatingsystembecomestransparentandsimple,convenientproduction,studyandimprovelater.
Inthispaper,atotaloffivechapters,thefirstchapterbrieflyintroducestheresearchofthereason,significanceandresearchmethods.Thesecondchapterpresentsrelevantbasicknowledgeofthediecastingmethod.Thethirdchapterdiecastingforaluminumalloymaterialrequirementsandbasicknowledgeofthegatingsystem.ThefourthchaptercastingprocessnumericalsimulationtheoryandtheProCASTsoftware.ChaptervusingProCASTsoftware,moldflowanalysisbycomparingtheanalysisreasonablepouringsystem.Finallyistheconclusionandthefutureoutlook,thisarticlegivesnotsolvetheproblemspointedout,andpointsoutthegoalandthedirectionofthefutureresearch.
Keywords:
diecasting;
Gatingsystem;
Simulationanalysis
第一章概述
1.1前言
伴随着世界经济的发展,我国的铸造业取得了快速的发展。
但是,铸造业取得快速发展的同时,问题也伴随而来。
铸造产业是消耗的能源很多,它需要大量的合金材料,生产过程中产生大量工业“三废”,严重污染了环境。
还有我国的技术比较落后,和其他欧洲发达国家相比,我国生产1吨压铸合格物品的“三废”排放量约为其10倍。
所以,“节能减排”以成为重大课题。
图1-1所示的就是一般的铸造工艺流程。
图1-1铸造工艺过程简图
浇注系统是金属液进入型腔的通道,主要功能是导入金属液和传递压力。
浇注系统设计是不是合理,对于设计模具来说很重要,因为压铸件的成型质量、生产效率和模具寿命等都要受到浇注系统很大的影响。
本文运用模拟仿真软件ProCAST对浇注系统进行优化,使得浇注系统设计成本低、周期短,有利于提高铸件的质量和节约成本。
从而达到更高的效益和节约能源的目的。
1.2研究的原因与意义
我国人口众多,铝、镁及锌等压铸所用的资源丰富且劳动力资源充足,为压铸业提供了良好的发展条件。
但是,我国的压铸行业起步相对比较晚,虽然取得了突飞猛进的发展,但是和与国外先进国家比较还存在着很大的差距。
压铸生产中所涉及的主要有压铸设备、压铸合金、压铸工艺、压铸模、工艺标准、监控等方面的问题。
我国每年因为压铸问题产生了很多资源浪费,例如2009年杭州乐荣电线有限公司生产所用的压铸模,报废率高达20.13%。
其中报废品中报废的原因气泡、气孔(占总的报废品48%)、凹陷(占总的报废品20%)、裂纹(占总的报废品13%)。
图1-2凹陷
图1-3气孔缺陷
由于生产过程造成的经济损失和能源浪费,虽然和生产者的素质有一定的关系,但是压铸工艺的改进是主要的提升方面,所以改进生产的设备和生产条件以及刻不容缓。
1.3本课题的研究方法
为了提升产品的优良率,改进传统压铸方法的那种经过多次修改、试验、再修改的过程的浪费资源和时间,而且难以保证质量的缺陷。
所以,利用计算机辅助工程CAE来改进生产。
压铸CAE是建立在数值模拟技术上的分析优化技术,借助CAE技术可实现对连续多周期生产过程中的模拟分析,变未知因素为可知因素,并分析易变因素的影响,实现对压铸过程的凝固模拟、压铸模具温度场的模拟,评价模具冷却工艺和判断模温平衡状态,评估可能出现的缺陷类型、位置和程度,帮助工程技术人员实现对生产工艺进行优化和对铸件质量的控制。
由于影响压铸工艺的因素有许许多多种,所以如果单纯的理论,很难获得合理的生产工艺参数。
所以,本文的研究方法是通过采用计算机辅助工程CAE(ProCAST)模拟分析,实现对压铸过程的凝固模拟、压铸模具温度场的模拟,评价模具冷却工艺和判断模温平衡状态,评估可能出现的缺陷类型、位置和程度,并得到合理的浇注系统,从而形成有利的充型方式,以获得优质的压铸件,使得以后的工业生产过程中的浪费率达到最低,从而获得更大的利益。
第二章压铸的相关知识介绍
现代的工业发展迅速,社会工业化的速度在飞速的前进,铸件类型的产品在我们身边也已经变得非常常见,已经融入了我们的生活,成为我们生活中密不可分的一部分。
在铸件中,压铸品更加常见。
压铸行业迅猛发展,下面我们一起来探讨有关压铸的知识。
2.1压铸的基本概念
压铸是先将半熔融或者熔融状态的合金液体浇入压铸机的压室,在高的很的压力和高速度下,将合金液体充填在压铸模的型腔中,然后让其在高压的状态下,使熔融合金冷却凝固成形,这种高效率、高效益并驾齐驱的精密铸造方法就称为压力铸造。
2.2压铸生产的特点
2.2.1压铸的缺点
(1)由于受到压铸机锁模力及装模尺寸的限制,压铸件尺寸受到限制。
(2)由于压铸模受到使用温度的限制,压铸的牌号和合金类别有所限制。
(3)压铸的生产准备费用较高,不适合小批量生产。
(4)压铸件表层有气孔,表2-1总结了常见压铸缺陷及其影响因素。
表2-1常见压铸缺陷及其影响因素
2.2.2压铸的优点
和其他铸造方法相比较,压铸有以下的优点:
(1)铸件的尺寸精度和对表面粗糙度要求很高。
(2)铸件的强度和表面硬度较高。
(3)可以压铸形状复杂的薄壁铸件。
(4)可以省略装备操作和简化制造工序。
(5)生产率极高、节省能源、节省原材料。
2.3压铸零件的分类
大体上可以分为六类,如下:
(1)圆盘类,如号盘座等。
(2)圆盖类,如表盖、机盖、底盘等。
(3)圆环类,如接插件、轴承保持器、方向盘等。
(4)筒体类,如导管、壳体形状的罩壳、上盖、深腔仪表罩、化油器等。
(5)多孔缸体、壳体类,如油泵体的汽缸体、气缸盖等复杂的壳体(这类零件对力学性能和气密性均有较高的要求,材料一般为铝合金),以及汽车与摩托车的气缸体、气缸盖等。
(6)特殊形状类,如叶轮、喇叭、字体等由肋条组成的装饰性压铸件等。
2.4压铸机概述
2.4.1压铸机的分类
根据压室的位置及工作状态,压铸机可以分为冷室压铸机和热式压铸机两类。
又因为压射机构与合模机构布置不同,冷室压铸机又可分为卧式、立式和全立式三种。
其中冷室压铸机与热式压铸机结构上的主要差异在于压射端。
冷室压铸机的压室与保温炉分开放置,压室水平放置。
而热式压铸机的压室直接放置于熔炉的坩埚内,压室竖直放置。
冷室压铸机与热式压铸机基本结构与外观如图2-1和2-2所示。
图2-1冷室压铸机
图2-2热室压铸机
2.4.2压铸机的基本结构
压铸机主要由压射机构、开合模机构、顶出及抽芯机构、液压系统、控制系统、机身等部分组成,各压射机构原理图如下图所示:
图2-3压射机构原理图
本课题研究所采用的是卧式冷室压铸机。
其结构图如2-4所示。
图2-4冷室压射机结构示意图
2.5压铸工艺参数及设定
压铸的主要特点是金属液在高压、高速下填充压铸模的腔型。
2.5.1压铸压力
压铸压力是压铸工艺中主要的参数之一。
压铸过程中的压力是由泵产生的,泵借蓄压器通过工作液体传递给压射活塞,然后由压射活塞经压射冲头施加于压室内的金属液上。
压铸过程中的压力可以用压射力和压射比压两种形式来表示。
(1)压射力压铸机压射缸内的工作液作用于压射冲头,使其推动液态金属充填模具型腔的力,称为压射力。
其大小随压铸机的规格不同,其反应了压铸机功率的大小。
压射力计算公式为
F=PA=πD²
P/4
式中F——压射力(N);
P——压射缸内工作液的压力(MPa);
A——压射冲头截面积(近似等于压室截面积)(m㎡);
D——压射缸直径(mm)。
(2)压射比压是指压射过程中,压室内单位面积上液态金属所受到的静压力。
计算公式为
P=F/A=4F/πD²
P——压射缸内工作液的压力(MPa);
A——压射冲头截面积(近似等于压室截面积)(m㎡);
D——压射缸直径(mm)。
在压铸过程中,作用在液态金属上的压射比压并不是一个常数,而是随着压射阶段的变化而变化。
变化过程如下图所示:
图2-5压铸不同阶段,金属液所受压力的变化情况
一般压铸时的压强为30~90MPa,一般压铸件强度越高,致密性越好,比压就越大。
压射力一般要根据生产过程中所使用的压铸机的规格来确定,并且也可以通过调整压射力和更换不同直径的压射冲头来实现。
使用较高的压力,就可用较低的浇注温度,这样有利于减少压铸件的缩孔和缩松,并且可以提高压铸模的使用寿命。
上述的压力变化图形,只是理论上的。
实际上当液态金属充填型腔时,因铸件复杂程度不同,金属充填特性及操作不同等因素,压射曲线也会出现不同的形式。
表2-2部分压铸机的压射力及压射冲头尺寸与压射比压的关系
2.5.2压铸速度
压铸中,压铸速度有压射速度和充填速度两个不同的概念。
压射速度是指压铸机压射缸内的压力油推动压射冲头前进的线速度。
充填速度是指液态金属在压力作用下,通过内浇口进入型腔的线速度。
充填速度的主要作用是将液态金属在凝固之前迅速输入型腔,它是获得轮廓清晰、表面质量高的铸件的重要因素。
在冷室压铸机中,压铸、浇道和铸型相连,成为一个密闭系统,因而它们之间具有连续方程的关系为
式中v——压射冲头速度(m/s)
A——压射冲头截面积(㎡)
D——压室直径(m)
Vg——充填速度(m/s)
Ag——内浇口截面积(㎡)
由公式可知,液态金属充填铸型的线速度与压室直径的平方、冲头的压射速度成正比,而与内浇口的截面积成反比。
此外,充填速度和压射比压有关,根据水力学原理,压射比压与充填速度间的关系可以用下式来表示,即
由上面分析得知,影响充填速度的因素有三个,即压射速度、压射比压和内口截面积。
所以,生产中通常采用调整充填速度的方法是:
调整压射速度、改变压射比压、调整内浇口的截面积。
总之,压力和速度是相辅相成而又相互制约的两个基本参数。
为适应各种铸件对压铸工艺的不同要求,压铸压力和压铸速度都做到无极调整。
一般压铸压力高时,铸件质量就较好。
为使压力更好的完成“充填”、“成形”“压实”的任务,在制定压铸工艺时,必须充分的考虑各因素之间的影响。
2.6压射过程与压射过程曲线
2.6.1压铸机的三级压射过程
一般情况下,压铸机采用慢速、快速、增压的三级压射过程。
图2-6压射过程示意图
2.6.2压射过程
在第一压射阶段或预压射阶段是要将压室内液态金属尽可能无涡流地引至浇口,压射活塞以恒定速度或匀加速慢慢地运动;
第二压射阶段,真正的充模过程,冲头在短的加速之后,以稳定的速度十分快地运动,以使浇口内液态金属达到稳定的流动速度。
第三压射阶段(增压)通过对压室内液态金属快速建压,对模具型腔内的压铸件增密,压力的建立是通过增压机构或直接控制压射来完成的,保持模具型腔内的增压至铸件凝固。
压铸工艺中决定着铸件质量的关键是:
在第一压射阶段压室内液态金属无涡流的运动;
在第二压射阶段快要结束充模之前降低压射活塞高的速度,此时由于对压射活塞的制动对充模时间不会有大的影响;
在铸件增密(增压)时从第二至第三压射阶段过渡的时间最短,直至压射活塞停止。
由此便产生许多不同的压射。
机构,所有的这些压射机构都力求最合理的解决以上工艺问题。
2.6.3压射曲线
压射过程曲线是进行压射过程分析的重要线图。
如下图所示。
图2-7压射过程及压射过程曲线
第三章压铸铝合金材料性能和浇注系统基本知识
压铸件对于合金有一定的要求,并不是所有的合金类型都适合做压铸的材料。
浇注系统是整个压铸工艺中十分重要的一部分,研究浇注系统,为我们的工业生产提供更好的服务,提高生产效率。
3.1压铸所需的铝合金材料
3.1.1可铸性的一般要求
压铸对所用金属材料的要求不同于其他铸造方法。
因此,决不能根据一种合金使用于砂型铸造或金属型铸造,就推断出它也直接适用于压铸。
一种理想的压铸合金应满足下列各项要求。
(1)金属尽可能在灰口铸铁或铸钢保温炉内加热和保持液态时始终不出现偏析。
(2)金属以高压和高速填充压铸模时,即使在最小的截面上也应具有足够的流动性,以获得质地良好的压铸件。
(3)在高压下,金属内不应出现化学反应或其他转变。
(4)在快速和通常不均匀的条件下,压铸件内不得产生偏析或缩孔。
(5)在无退让性的型腔内和型芯上收缩受阻时,直到顶出温度不允许在压铸件内产生裂纹和危险的应力。
(6)金属在液态或者糊状下含气体少,特别是不允许含有形成的金属氧化物或者在金属液内具有一定的溶解性的气体。
3.1.2压铸合金应具备的基本要求
根据压铸工艺的特点,对压铸合金应有如下基本要求。
(1)过热温度不高时具有较好的流动性,便于填充复杂型腔,以获得表面质量良好的压铸件。
(2)线收缩率和裂纹倾向性小,以免压铸件产生裂纹,使压铸件有较高的尺寸精度。
(3)结晶温度范围小,防止压铸件产生过多的缩孔和缩松。
(4)具有一定的高温强度,以防止推出压铸件时产生变形或碎裂。
(5)在常温下有较高的强度,以适应大型薄壁复杂压铸件生产的需要。
(6)与型壁间产生物理化学作用的倾向性小,以减少粘膜和相互合金化。
(7)具有良好的加工性能和一定的抗蚀性。
3.1.3铝合金材料相关性能
常用的压铸合金包括铝合金、锌合金、镁合金三种。
压铸一般采用铝合金。
铝合金密度小、比强度大、导热性好、耐腐蚀性好、综合性优良。
按主要成分划分,压铸合金包括以下几类:
(1)Al-Si合金。
(2)Al-Si-Cu合金。
(3)Al-Mg合金。
压铸铝合金的化学成分及力学性能如下表。
表3-1压铸铝合金的化学成分和力学性能表(GB/T15115—1994)
压铸铝合金中主要的元素为:
Si、Mg、Cu、Zn、。
各合金元素的主要作用如下表所示。
表3-2压铸铝合金中主要元素的作用
中国与主要工业国家压铸铝合金牌号对应表,如下表所示。
表3-3中国与主要工业国家压铸铝合金牌号对应表
3.2浇注系统基本知识
3.2.1定义
浇注系统是指将金属液引入到型腔的通道。
它在压铸生产中的地