模具毕业设计140油封骨架冲压模具Word格式文档下载.docx
《模具毕业设计140油封骨架冲压模具Word格式文档下载.docx》由会员分享,可在线阅读,更多相关《模具毕业设计140油封骨架冲压模具Word格式文档下载.docx(14页珍藏版)》请在冰豆网上搜索。
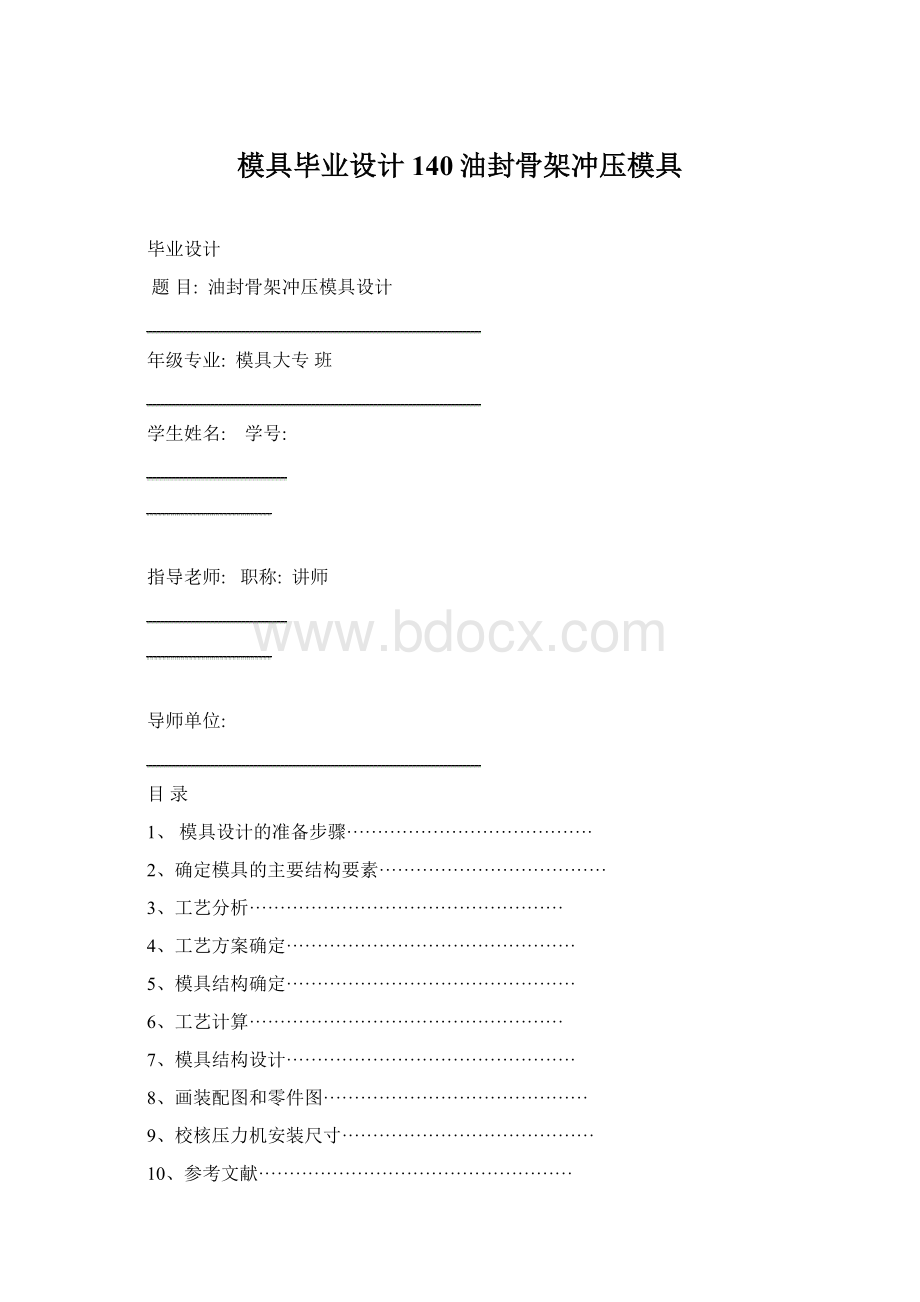
Thatgraduationdesignismainlyanoilsealframeworkwhichorderstoourfactorybusinessmanbutdesignofaninsidewaitcomplicateddegreeofcoldbluntpressamoldingtool,includethedesigntothemoldingtoolandcalculation,themoldingtoolprocessescraftanalysis,thepressureiswaitedabasiccontentsbydintanalysis.Passingthisdesignmademeinitialtohavetodesignaninsidewaitcomplicateddegreebluntpressthecraftrulesofmoldingtooltheabilityofthedistanceandcontroledanusagebluntpressbasicprincipleandmethodof[with]moldingtooldesign,step,draftdesignproject,acquaintwithtohaverelationwithusagereference,chartetc.basictechnicalability,makethusoneselfintheabilitycancertainlytheexaltationof[with]degree,beengagedinmoldingtooldesignanddevelopmenttobeatforthefutureundergoodfoundation.
该毕业设计主要是针对我们厂客商订货的一个油封骨架而设计的一个中等复杂程度的冷冲压模具,包括对模具的设计与计算,模具的加工工艺分析,压力的受力分析等基本内容.通过这次设计使我初步具备了设计一个中等复杂程度冲压模具的工艺规程的能力和掌握了运用冲压模具设计的基本原理和方法,步骤,拟定设计方案,熟悉和运用有关参考资料,图表等基本技能,从而使自己在能力方面得以一定程度的提高,为未来从事模具设计与开发打下了良好的基础.。
关键词:
油封骨架,冲压模具,工艺分析,工艺规程。
设计项目内容
制件如图所示,材料为黄铜H68(半硬),料厚1㎜,制件尺寸精度为IT14级,
产量20万件。
1,模具设计的准备步骤:
(1)拟定冲压工序安排方案、画出冲压工序图、画出待设计模具的排样图
(2)计算冲裁力、确定模具压力中心、计算凹模周界、确定待设计模具的有关结构要素、选用模具典型组合等,初选压力机吨位
(3)确定压力机吨位
(4)设计及绘制模具装配图
(5)设计及绘制模具零件图
(6)按规定格式编制设计说明书
(7)课程设计面批后或答辩
2,确定模具的主要结构要素:
根据冲压模具产品图排样方案论证结果,已确定本模具采用倒装式复合模结构。
在此基础上,尚须确定如下结构要素。
(1)确定送料方式
模具相对于模架是采用从前往后的纵向送料方式,还是采用从右往左的横向送料方式,这主要取决于凹模的周界尺寸。
如L(送料方向的凹模长度)<B(垂直于送料方向的凹模宽度)时,采用纵向送料方式;
L>B时,则采用横向送料方式;
L=B时,纵向或横向均可。
就本例的圆形凹模板而言,其送料方式应采用纵向送料。
另外采用何种送料方式,还得考虑压力机本身是开式还是闭式而定。
(2)确定卸料形式
模具是采用弹压卸料板,还是采用固定卸料板,取决于卸料力的大小,其中材料料厚是主要考虑因素。
由于弹压卸料模具操作时比固定卸料模具方便,操作者可以看见条料在模具中的送进动作,且弹压卸料板卸料时对条料施加的是柔性力,不会损伤工件表面,因此实际设计中尽量采弹压卸料板,而只有在弹压卸料板卸料力不足时,才改用固定卸料板。
随着模具用弹性元件弹力的增强(如采用矩形弹簧),弹压卸料板的卸料力大大增强。
根据目前情况,当材料料厚约在2mm以下时采用弹压卸料板,大于2mm时采用固定卸料板较为贴近实际。
本模具所冲材料的料厚为1mm,因此可采用弹压卸料板。
(3)模架形式
如采用纵向送料方式,适宜采用中间导柱导套模架(对角导柱导套模架也可);
横向送料适宜采用对角导柱导套模架:
而后侧导柱导套模架有利于送料(纵横向均可且送料较顺畅),但工作时受力均衡性和对称性比中间导柱导套模架及对角导柱导套模架差一些;
四角导柱导套模架则常用于大型模具;
而精密模具还须采用滚珠导柱导套。
本模具采用中间导柱导套模架,一是对纵向送料方式较适宜,二是中间导柱导套模架工作时受力比较均衡、对称。
3.工艺分析
该制件形状简单,尺寸较小,厚度适中,一般批量,属普通冲压件,但有几点应注意:
1)2×
Φ3.5两孔壁距及周边距仅2.25~2.5㎜,在设计模具时应加以注意。
2)制件头部有15°
的非对称弯曲,控制回弹是关键。
3)制件较小,从安全考虑,要采取适当的取件方式。
4)有一定的批量,应重视模具材料和结构的选择,有一定的模具寿命。
4.工艺方案的确定
根据制件工艺性分析,其基本工序有落料,冲孔和弯曲三种。
按其先后顺序组合,可的如下五种方案:
(1)落料—弯曲—冲孔,单工序冲压。
(2)落料—冲孔—弯曲,单工序冲压。
(3)冲孔—切口—弯曲—落料,单件复合冲压。
(4)冲孔—切口—弯曲—切断—落料,两件连冲复合。
(5)冲孔—切口—弯曲—切断,两件连冲级进冲压。
方案1)、2)属于单工序冲压。
由于此制生产批量较大,尺寸又较小,这两
种方案生产率低,操作也不安全,故不宜采用。
方案3)、4)属于复合冲压。
由于制件结构尺寸小,壁厚小,复合模装配较困难,强度也会受影响,寿命不高;
又因冲孔在前,落料在后,以凸模插入材料和凹模内进行落料,必然受到材料的切向流动压力,有可能使Φ3.㎜凸模纵向变形,因此采用复合冲压,除解决了操作安全性和生产效率等问题外,又有新小难题,因此使用价值不高,也不宜采用。
方案5)属于级进冲压,既解决了方案1)、2)的问题。
也不存在方案3)、4)的难点,故此方案最为合适。
5.模具结构的确定
因制件材料较薄,为保证制件平整,采用弹压卸料装置。
它还可对冲孔小凸模起导向作用和保护作用。
为方便操作和取件,选用双柱可倾压力机,纵向送料。
因制件薄而窄,故采用侧刃定位,生产率高,材料消耗也不大。
综上所述,决定选用弹压卸料纵向送料典型组合结构形式,对角导柱滑动导向模架。
6.工艺计算
(1)计算毛坯尺寸相对弯曲半径为
R/t=2/1=2>
0.5
式中R——弯曲半径(㎜);
t——料厚(㎜)。
可见,制件属于圆角半径较大的弯曲件,应先考虑弯曲变形区中性层曲率半径ρ(㎜)。
中性层的计算公式为
ρ=R+Xt
式中X——由实验测定的应变中性层位移系数。
查表得应变中性层位移系数X=0.38
ρ=(2+0.38×
1)㎜=2.38㎜
查表得圆角半径(R>
0.5t)的弯曲件毛坯长度计算公式
l0=∑l直+∑l弯;
l弯=180°
-α/180πρ
式中l0——弯曲件毛料展开长度(㎜)
∑l直——弯曲件各直线段长度总和(㎜)
∑l弯——弯曲件各弯曲部分中性层展开长度之和(㎜)
由图可知
∑l直=AB+BC∑l弯=CE+CF
式中
AB=20㎜
BG=(36-20)㎜=16㎜
OD=(2+1+2㎜)=5㎜
CD=(2+1)㎜=3㎜
OC=(52-32)1/2㎜=4㎜
BO=16/cos15°
㎜=16.56㎜
BC=BO-OC=(16.56-4)㎜=12.56㎜
β=arccos4/5=36.87°
α=90°
-36.87°
=53.13°
则
∑l直=(20+12.56)㎜=32.56㎜
∑l弯=πρ(53.13°
/180°
+(180°
-36.87)/180°
)=8.14㎜
l0=(32.56+8.14)㎜=41㎜
(2)画排样图因2×
Φ3.5孔壁距较小,考虑到凹模强度,将两小孔分步冲出,冲孔与切口工序之间留一空位工步,故该制件需六个工步完成。
查表切断工序中工艺废料带的标准值、切口工序中工艺废料的标准值、条料宽度公差△、侧刃裁切的条料的切口宽F,得
F=1.5㎜S=3.5㎜△=0.5㎜C=3㎜(考虑到凹模强度,实取C=5㎜)
查表的采用侧刃条料宽度尺寸B(㎜)的确定公式
B=(L+1.5a+nF)—△
得条料宽度B
B=(2l0+C+2F)=(41×
2+5+2×
1.5)0-0.5㎜=900-0.5㎜
如图所式,画排样图。
查表,选板料规格为1500㎜×
600㎜×
1㎜,每块可剪600×
90㎜规格条料16条,材料裁剪利用率达96%。
(3)计算材料利用率η查表得材料利用率通用计算公式
η=A0/A×
100%
式中A0——得到制件的总面积(㎜2);
A——一个步距的条料面积(L×
B)(㎜×
㎜)
得
η=(41×
8.5×
2)/(12×
90)×
100%=65%
(4)计算冲压力完成本制件所需要的冲压力由冲裁力、弯曲力及卸料力、推料力组成。
不需计算弯曲时的顶料力和压料力。
1)冲裁力F冲——由冲孔力、切口力、切断力和侧刃冲压力四部分组成。
F冲=KLtТ0或F冲=Ltσb
其中K——系数,K=1.3;
L——冲裁周边长度(㎜)
Т0——材料的抗建强度(MPa)
σb——材料的抗拉强度(MPa)
查表得
σb=343MPa(为计算方便,圆整为350MPa)
F冲=350×
1×
(4×
3.5×
3.14+2×
(3.5+41×
2)+2×
(12+1.5)+2×
8.5+5)N=93.1KN
2)弯曲力F弯——为有效控制回弹,采用校正弯曲。
查表得校正弯曲力F弯(N)的计算公式
F冲=32Ap
式中A——变形区的投影面积(㎜2);
p——单位校正力(MPa),查表取p=60MPa
F弯=2Ap2×
39×
60N=39.8KN
3)卸料力F卸和推料力F推,卸料力和推料力的计算公式
F卸=K卸F冲
F推=K推F冲n
式中K卸K推——系数查表得K卸=K推=0.05;
n——卡在凹模直壁洞口的制件(或废料)件数,一般卡3~5件,这里取n=5。
F卸=0.05×
93.1KN=4.7KN
F推=5×
0.05×
93.1=23.3KN
F=F冲+F弯+F卸+F推=(93.1+39.8+4.7+23.3)KN=160.9KN
(5)初选压力机查表开式可倾压力机参数,初选压力机型号规格为J23-25。
(6)计算压力中心由于图形规则,两件对排,左右对称,故采用解析法求压力中心较为方便。
建立坐标系如图所示:
因为左右对称所以XG=0,只需求YG。
根据合力矩定理有
YG=(Y1F1+Y2F2+Y3F3+Y4F4+Y5F5)/(F1+F2+F3+F4+F5)
=[2×
350×
(6×
12+7.8×
3.14+19.8×
3.14×
3.5+37.8×
(3.5+2×
41.5*)+66×
(8.5+2))+55.8×
39800]/(93.1+39.8)×
1000
=37㎜
上式中注*尺寸比制件展开毛坯尺寸大0.5㎜,目的是避免在切口工序时模具或条料的误差引起制件边缘毛刺的增大。
(7)计算凸凹模刃口尺寸本制件形状简单,可按分别加工法计算刃口尺寸。
查表可知材料抗剪强度和间隙值的关系和规则形状冲裁凸、凹模的制造工差
Zmin=0.012㎜Zmax=0.2㎜δp=0.020㎜δd=0.020㎜
δp+δd=(0.020+0.020)㎜=0.040㎜
Zmax-Zmin=(0.20-0.012)㎜=0.08㎜
满足δp+δd≤Zmax-Zmin
所以可用分注尺寸法计算。
查表的分开加工刃口尺寸计算公式及磨损系数X=0.5
1)冲孔刃口尺寸
dp=(3.5+0.5×
0.30)0-0.02㎜=3.650-0.02㎜
dd=(3.65+0.12)+0.0200㎜=3.77+0.0200㎜
2)切口和切断尺寸:
由于在切口和切断工序中,凸、凹模均只在三个方向与板料作用并使之分离,并由图可知,尺寸C和S既不是冲孔尺寸也不是落料尺寸,要正确控制C和S两个尺寸才能间接保证制件外形尺寸,为方便计算,直接取C和S值为凹模基本尺寸,间隙取在凹模上。
①切断刃口尺寸
dp=50-0.02㎜
dd=(5+0.12)+0.0200㎜=5.12+0.0200㎜
②切口刃口尺寸
dp=3.50-0.02㎜
dd=(3.5+0.12)+0.0200㎜=3.62+0.0200㎜
3)侧刃尺寸:
侧刃为标准件,根据送料步距和修边值查侧刃表,按标准取侧刃尺寸。
查表得侧面切口值尺寸
侧刃宽度B=6㎜侧刃长度L=12㎜
间隙取在凹模上,故侧刃尺寸为
B=6.12+0.0200㎜L=12.12+0.0200㎜
(8)凹模各孔位置尺寸这类尺寸较多,包括两侧刃孔位置尺寸、两切口模孔位置及切断孔口位置尺寸。
其基本尺寸可按排样图确定。
其制造公差可查表,冲裁精度应为IT9级,但这里送进工步较多,积累误差过大,会造成凸、凹模间隙不均,影响冲裁质量和模具寿命,故而应将模具制造精度提高。
考虑到加工经济性,在送料方向的尺寸按IT7级制造,其他位置尺寸按IT8~IT9级制造,凸模固定板与凹模配制。
具体尺寸参照图。
(9)卸料板各孔尺寸卸料板各型孔应与凸模保持0.5Zmin间隙,这样有利于保护凸、凹模刃口不被“啃”伤,据此原则确定具体尺寸,如图所式。
(10)凸模固定板各孔口尺寸凸模固定板各孔与凸模配合,通常按H7/n6或H7/m6选取,这里选H7/n6配合。
查表可得各型孔尺寸公差,如图所式。
(11)回弹值由工艺分析可知,本制件弯曲回弹影响最大的部位是在15°
角处,R/T=2<
5。
此处属于小圆角V形弯曲,故只考虑回弹值。
回弹值可查相关图表进行估算。
如手边无该种材料的回弹值数据,也可根据材料的σb值,查与其相近的回弹值作为参考。
据此,查表弯曲回弹值可知15°
角处由于回弹,可能小于15°
,但回弹值不会很大,故弯曲凸、凹模均可安制件基本尺寸标注,在试模后稍加修模即可。
7.模具结构设计
(1)凹模设计因制件形状简单,虽有六个工步,但总体尺寸不大,选用整体矩形凹模较为合理。
因生产批量较大,查表,选用Cr12为凹模材料。
1)确定凹模厚度H值:
查表凹模厚度计算公式
H=F冲1/3=93101/3㎜=21㎜
2)
确定凹模边界尺寸L×
B:
查表凹模孔壁厚的计算公式,凹模孔口轮廓线为直线时:
W=1.5H。
查表及由图得
W=1.5H=1.5×
21㎜=32㎜
L=150~160㎜
B=130~140㎜
查表矩形凹模标准可查到较为靠近的凹模周界尺寸为160㎜×
140㎜×
20㎜。
根据此值查表,可得典型组合160×
140×
140~170(单位为㎜)。
而由此典型组合标准,既可方便地确定其他冲模零件的数量、尺寸和主要参数。
需要说明的是凹模宽度140㎜这个尺寸虽然不是优先选用参数,但根据图计算出的B值与之最接近,而且当B=140㎜时,压力中心与凹模几何中心重合,故选用此尺寸。
(2)选择模架及确定其他冲模零件尺寸由凹模周界尺寸及模架闭合高度在140~170之间,查表选用对角导柱模架,标记为160×
140~170I,并可根据次标准画处模架图。
类似也可查出其他零件尺寸参数。
8.画装配图和零件图:
(1)先绘制模具装配图后,应对照装配图来拆画零件图
1)为了绘制一张美观、正确的模具装配图,必须掌握模具装配图面的布置规范。
2)处通常布置模具结构主视图。
在画主视图前,应先估算整个主视图大致的长与宽,然后选用合适的比例作图。
主视图画好后其四周一般与其它图或外框线之间应保持有约50~60mm的空白,不要画得“顶天立地”,也不要画得“缩成一团”,这就需要选择一合适的比例。
推荐尽量采用1:
1的比例,如不合适,再考虑选用其它《机械制图国家标准》上推荐的比例。
3)处布置模具结构俯视图。
应画拿走上模部分后的结构形状,其重点是为了反映下模部分所安装的工作零件的情况。
俯视图与边框、主视图、标题栏或明细表之间也应保持约50~60mm的空白。
4)处布置冲压产品图。
并在冲压产品图的右方或下方标注冲压件的名称、材料及料厚等参数。
对于不能在一道工序内完成的产品,装配图上应将该道工序图画出,并且还要标注本道工序有关的尺寸。
5)处布置排样图。
排样图上的送料方向与模具结构图上的送料方向必须一致,以使其他读图人员一目了然。
6)处主要技术要求。
如模具的闭合高度、标准模架及代号及装配要求和所用的冲压设备型号等。
7)处布置明细表及标题栏。
结合图4标题栏及明细表填写示例,应注意的要点如下。
(1)明细表至少应有序号、图号、零件名称、数量、材料、标准代号和备注等栏目;
(2)在填写零件名称一栏时,应使名称的首尾两字对齐,中间的字则均匀插入;
(3)在填写图号一栏时,应给出所有零件图的图号。
数字序号一般应与序号一样以主视图画面为中心依顺时针旋转的方向为序依次编定。
由于模具装配图一般算作图号00,因此明细表中的零件图号应从01开始计数。
没有零件图的零件则没有图号。
(4)备注一栏主要标标准件规格、热处理、外购或外加工等说明。
一般不另注其它内容。
(2)根据装配图拆画零件图
绘制模具装配图后,应对照装配图来拆画零件图。
推荐如下步骤。
绘制所有零件图的图形,尺寸线可先引出,相关尺寸后标注,以装配图为例。
模具可分为上下两大部分。
在画上半部分的零件图时,绘制的顺序一般采用“自下往上,相关零件优先”的步骤进行。
凹模是工作零件可以首先画出;
绘完凹模的图形后,对照装配图,推块与凹模相关,其外形与凹模洞口完全一致,厚度应比凹模大出0.5mm,根据这一关系马上画出推块的图形;
接下来再画冲孔凸模固定板的图形画好凸模固定板以后,再对照模具装配图画出装在冲孔凸模板内的冲孔凸模、冲孔凸模等与之相关零件的图形……。
在画上模部分的零件图时,应注意经过上模座、上垫板、冲孔凸模固定板及凹模等模板上的螺销钉孔的位置一致。
在画下模部分的零件图时,一般采用“自上往下,相关零件优先”的步骤进行。
先画卸料板的图形,然后对照装配图上的装配关系,画活动挡料钉、挡料钉的图形。
再画凸凹的图形……。
在画下模的零件图时,也应注意经过卸料板、凸凹模固定板、下垫板、下模座上的螺丝钉孔的位置及凸凹模、下垫板、下模座上漏料孔位置的一致。
按照上述步骤,根据装配关系对零件形状的要求,绘制各零件图的图形,能很容易地正确绘制出模具零件的图形,并使之与装配关系完全吻合。
(3)标注尺寸:
要使尺寸标注正确,就要把握尺寸标注的“思路”。
前面要求绘制所要零件图的图形而先不标注任何尺寸,就是为了在标注尺寸时能够统筹兼顾,用一种正确的“思路”来正确地标注尺寸。
(1)标注工作零件的刃口尺寸
根据模具设计法则,先标注基准件上刃口尺寸,再标注对应件上的刃口尺寸;
但符合模中也可将凸凹模作为基准件,凸模、凹模作为对应件进行尺寸标注。
所有零件图的图形绘好后,先找出本模具的工作零件即凸凹模、冲孔凸模、落料凹模,把着三张图纸对照起来,按照尺寸布置后安排好的“地点”标注刃口尺寸。
这样可保证刃口尺寸标注的正确性。
(2)标准相关零件的相关尺寸
相关尺寸正确,各模具零件才能装配组成一幅模具,必须保证正确。
在上模部分,相关尺寸的标注建议按照“自上而下”的顺序进行。
(3)补全其它尺寸及技术要求
这个阶段可逐张零件进行,先补全其它尺寸,例如轮廓大小尺寸、位置尺寸等;
再标注各加工面的粗糙度要求及倒角、圆角的加工情况,最后是选材及热处理,并对本零件进行命名等。
9.校核压力机安装尺寸
模座外形尺寸为250㎜×
230㎜,闭合高度为60㎜,查表J23-25型压力机工作尺寸为370㎜×
560㎜,最大高度为270㎜,连杆调节长度为55㎜,故在工作台上加一50~100㎜的垫板,即可安装。
模柄尺寸也与本副模具所选模柄尺寸相符。
10,附:
参考文献
1.王小沛冲压手册机械工业出版社,2000
2.孙凤琴冲压与塑压设备机械工业出版社,2001
3.刘飞模具设计手册机械工业出版社,2003
4.王亚男冲模图册上海科技出版社,2001
5中国模具协会2004中国模具工业年鉴机械工业出版社2004-9
6钟敏斌冲压工艺与模具设计机械工业出版社2004
7.傅建军模具制造工艺机械工业出版