冲压件的缺陷及检验标准文档格式.docx
《冲压件的缺陷及检验标准文档格式.docx》由会员分享,可在线阅读,更多相关《冲压件的缺陷及检验标准文档格式.docx(18页珍藏版)》请在冰豆网上搜索。
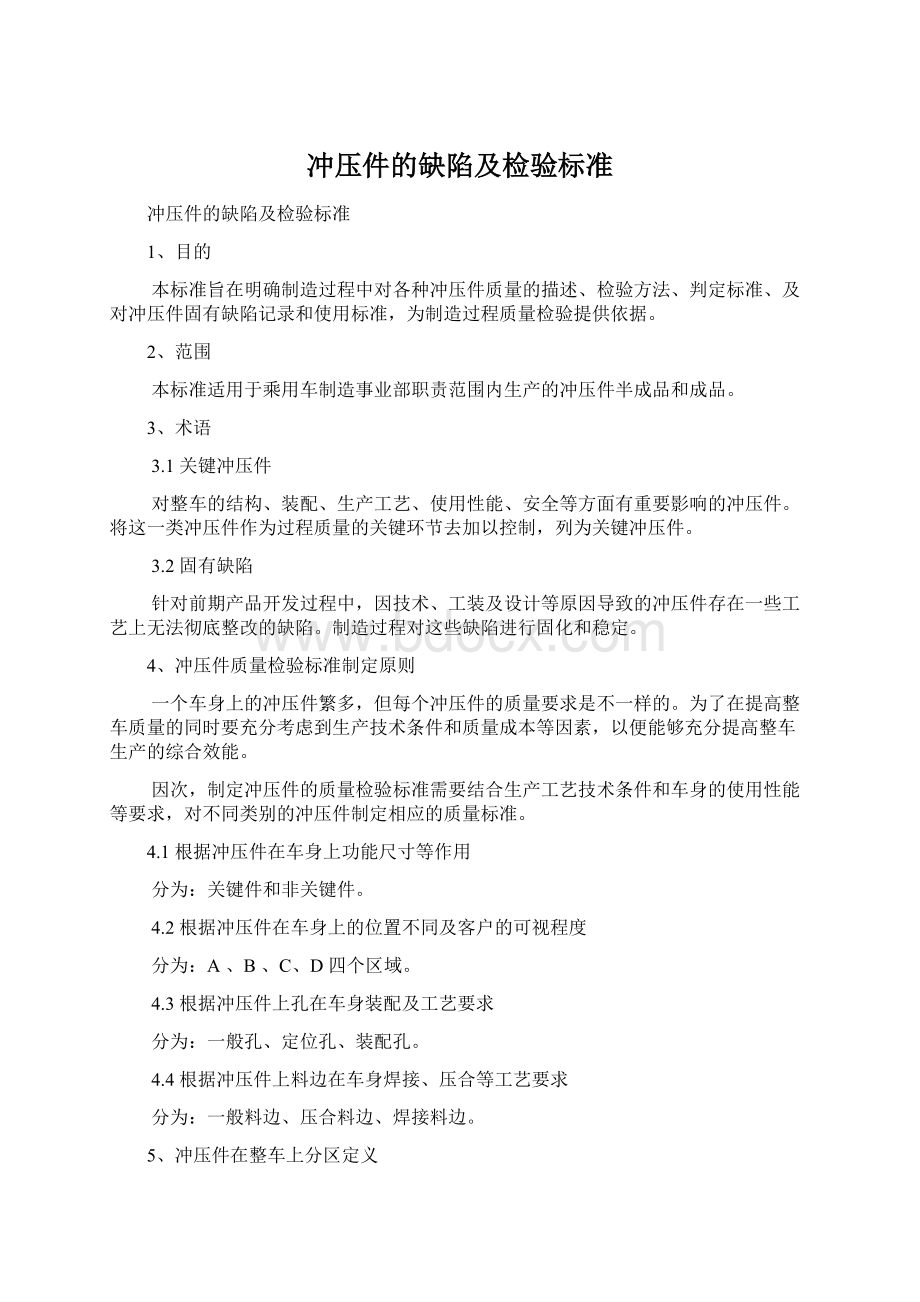
5.3(C区)
打开车门上车时能看到的部位;
坐在司机或乘客座位上,关上车门后能看得见的部位;
车身发动机盖、行李盖打开后看得见区域;
天窗窗框,油箱加注孔入口等其他区域。
5.4(D区)
除A、B、C三个可视区域,车身上被内饰件等覆盖的、客户一般所不能察觉或发现的部位。
6、冲压件质量缺陷类型
冲压件质量缺陷类型一般分三类。
6.1外观缺陷
包括:
裂纹、缩颈、坑包、变形、麻点、锈蚀、材料缺陷、起皱、毛刺、拉、压痕、划伤、圆角不顺、叠料、及其他。
6.2功能尺寸缺陷
孔偏、少边、少孔、孔径不符、多料、型面尺寸不符、其他。
6.3返修缺陷
裂纹、孔穴、固体夹杂、未溶合和未焊透、形状缺陷、变形、坑包、刨痕、抛光影、板件变薄、及其他。
7、冲压件的检验方法
7.1外观检验方法
7.1.1触摸检查
用干净的纱布将外覆盖件的表面擦干净。
检验员需戴上纱手套沿着零件纵向紧贴零件表面触摸,这种检验方法取决于检验员的经验,必要时可用油石打磨被探知的可疑区域并加以验证,但这种方法不失为一种行之有效的快速检验方法。
7.1.2油石打磨
用干净的纱布将外覆盖件的表面擦干净。
打磨用油石(20×
13×
100mm或更大)。
有圆弧的地方和难以接触到的地方用相对较小的油石打磨(例如:
8×
100mm的半园形油石)油石粒度的选择取决于表面状况(如粗糙度,镀锌等)。
建议用细粒度的油石。
油石打磨的方向基本上沿纵向进行,并且很好地贴合零件的表面,部分特殊的地方还可以补充横向的打磨。
7.1.3柔性纱网的打磨
用柔性砂网紧贴零件表面沿纵向打磨至整个表面,任何麻点、压痕很容易地被发现(不建议用此方法检验瘪塘、波浪等缺陷)。
7.1.4涂油检查
用干净的刷子沿着同一个方向均匀地涂油至零件的整个外表面。
把涂完油的零件放在高强度的灯光下检查,建议把零件竖在车身位置上。
用目视法可很容易地发现零件上的微小的麻点、瘪塘、波纹。
7.2尺寸检验方法
7.2.1检具测量
利用检具、钢板尺、间隙尺等测量工具,对冲压件的孔位置、大小、型面尺寸、料边等部位进行测量。
同时结合产品数模,对冲压件的尺寸进行确认。
7.2.2三坐标、扫描测量
利用专业测量设备对冲压件孔位置、型面尺寸等进行精确测量。
8、冲压件缺陷检查标准及描述
8.1外观缺陷检查标准及描述
8.1.1裂纹
检查方法:
目视。
对于外覆盖件任何碎裂都是不可接受的。
对于内覆盖件仅细微的碎裂允许作补焊返修处理,但返修部位是顾客不易发觉的且必须满足冲压件的返修标准。
8.1.2缩颈
目视、剖解。
缩颈是冲压件成形过程潜在的危险破裂点,对冲压件的功能、强度、耐疲劳度有着至关重要的影响。
根据缩颈的程度判定冲压件是否合格、返修、报废等。
外覆盖件缩颈影响整车外观,客户是不可接受的。
8.1.3坑包
坑包的存在严重影响覆盖件油漆后的外观质量,是客户所不能容忍的缺陷。
大面积的坑包还影响制件强度、疲劳度,无法修复。
8.1.4变形(突起、凹陷、波浪)
目视、油石打磨、触摸、涂油
A类缺陷:
是用户不能接收的缺陷,没有经过培训的用户也能注意到
B类缺陷:
它是在冲压件外表面上摸得着和看得见、可确定的
C类缺陷:
是需要修正的缺陷,绝大多数处于模棱两可的情况下,只有在油石打磨后才看得出。
8.1.5麻点
A类缺陷:
麻点集中,超过整个面积2/3都分布有麻点。
B类缺陷:
麻点可看到、可摸到。
打磨后可见单独分布的麻点,要求麻点间距离为300mm或更大。
8.1.6锈蚀
锈蚀是冲压件长期存放或者存放不当导致生锈,对冲压件的功能、强度、耐疲劳度有着至关重要的影响。
8.1.7材料缺陷
目视
标准:
材料强度不符合要求,轧钢板留下的痕迹、重叠、桔、有条纹、镀锌表面疏松、镀锌层剥落。
8.1.8起皱
外覆盖件不允许存在任何顾客容易察觉的起皱,内覆盖件不允许存在严重的起皱从而导致材料叠料。
8.1.9毛刺
毛刺的长度要求小于板料厚度的10%。
任何影响焊接搭边贴合程度的毛刺是不可接受的。
任何容易导致人身伤害的毛刺是不可接受的。
任何影响零件定位及装配的冲孔毛刺是不可接受的。
8.1.10拉、压痕及划伤
外覆盖的外表面不允许存在拉及划伤、压痕;
外覆盖件的内表面不允许存在影响外表面质量的划伤、压痕。
内覆盖件表面不允许存在潜在的导致零件拉裂的严重划伤、压痕。
8.1.11圆角不顺
目视、检具测量
圆角半径不够均匀,不够清晰光顺。
外覆盖件不允许存在,内覆盖件的一些装配面、搭接面圆角不顺不仅影响制件外观,严重的还影响焊接、装配。
8.1.12叠料
外覆盖件不允许存在叠料缺陷,内覆盖件的的不同程度的叠料缺陷导致客户抱怨,功能类冲压件还影响制件的装配和车身强度。
8.1.13打磨缺陷、打磨印
目视、油石打磨
打磨穿了,在外表面上明显可见,所有顾客都立即可见。
能看到、摸到,在有争议的地方打磨后也能证明。
用油石打磨后能看出
8.2尺寸缺陷检查标准及描述
8.2.1孔偏、少孔
检具测量、三坐标测量
冲压件的孔根据孔偏移的大小、孔的作用而质量标准不同。
对于定位、安装孔的位置精度要求高,一般工艺孔、过孔位置精度要求低。
冲压件少孔是产品设计和要求所不允许的。
8.2.2孔径不符
间隙尺、游标卡尺
冲压件的孔直径偏差大小,根据孔的作用而质量标准不同。
对于定位、安装孔的偏差精度高低直接决定了整车的装配性能。
一般工艺孔、过孔位置偏差进度要求相对低。
8.2.3少边、多料
检具测量、间隙尺、钢板尺、三坐标测量
冲压件少边、多料在不同类别的冲压件上影响程度大不相同。
例如:
焊接边少边影响焊点分布和操作,压合边少边和多料决定压合后总成质量。
8.2.4型面尺寸不符
冲压件型面尺寸偏差由于设计、规划等工艺水平是避免不了的,但是其偏差的大小直接决定了整车的外观配合、冲压件匹配、零部件装配等质量水平。
9、冲压件缺陷检验判定标准
以下标准,遵循“质量从严”的原则进行判定。
同一问题按严重程度从严判定。
9.1外观缺陷检验判定标准
冲压件外观缺陷检验标准
项目
描述
关键件
判定(整车区域)
A
B
C
D
裂纹
1、封闭裂纹:
长度≥50mm
宽度≥3mm
2、不封闭裂纹:
长度≥30mm
宽度≥2mm
/
所有件下同
报废
10mm≤长度<50mm
宽度<3mm
10mm≤长度<30mm
宽度<2mm
是
非
返修
1、封闭裂纹:
长度<10mm
2、不封闭裂纹:
长度<10mm
宽度<2mm
缩颈
缩颈部位材料厚度:
厚度≥料厚的
80%;
缩颈部位长度≥60mm
料厚的50%≤厚度<料厚的80%;
缩颈部位长度:
30mm≤长度<60mm;
厚度<料厚的
50%缩颈部位长度:
长度<30mm
坑包
面积≥8m㎡;
长度≥10mm;
高度≥1.5mm
面积<8m㎡;
长度L<10mm;
高度<1.5mm
合格
变形
零件表面出现明显起伏;
目视明显;
严重影响外观及装配
零件表面出现起伏;
目视不明显;
手感明显
手感不明显;
油石检验明显
麻点
零件2/3面积上能看到麻点或小凸包
零件表面用油石磨件之前用手感觉明显的麻点或麻点群;
麻点面积<2/3零件面积;
材料缺陷
料厚明显不符合要求;
表面有明显的桔皮滑移线、镀锌层疏松;
锌脱落长度≥300mm;
宽度≥5mm
轻微的材料缺陷;
磨件后可见的材料缺陷;
锈蚀
锈蚀厚度≥料厚的40%;
锈蚀面积≥全部面积的25%;
型面比较复杂无法消除锈迹;
锈蚀厚度:
料厚的20%≤厚度<料厚的40%;
锈蚀面积:
全面积5%≤厚度<全面积25%;
表面质量受锈蚀影响但可通过打磨修复;
起皱
肉眼能看出的严重皱折、棱线错位,严重影响焊接及装配;
棱线、弧度不够清晰光顺;
肉眼可见的皱纹、波纹、棱线错位;
毛刺
毛刺高度H大于料厚的40%;
有操作危险性的粗毛刺;
毛刺高度:
料厚的20%≤高度<料厚的40%;
毛刺影响定位、装配、焊接、压合的;
一般孔
定位孔装配孔
一般料边
压合/焊接料边
高度<料厚的20%;
拉毛压痕划伤
深度≥料厚的30%;
宽度≥2mm;
长度≥5mm;
料厚的10%≤深度<料厚的30%;
宽度<2mm;
长度<5mm
深度<料厚的10%;
圆角不顺
圆角半径不均匀,未达到要求;
明显地不清晰、不光顺;
配合间隙达2mm以上;
圆角半径不均匀,不够清晰光顺;
配合间隙达2mm以下
叠料
板料重叠宽度:
宽度≥8mm
3mm≤宽度<8mm
其他
能引起严重功能障碍的缺陷
对使用有明显影响的缺陷
9.2尺寸缺陷检验判定标准
尺寸缺陷检验判定标准
零件与检具的间隙用d表示,
平度用h表示,单位mm
判定结果
压合料边面
定位面特殊料边面
-0.5≤h≤0.5;
2.5≤d≤3.5
焊缝搭接边
-1.0≤h≤1.0;
2.0≤d≤4.0
点焊搭接边
涉及外观\装配面料边
定位孔
0≤直径≤0.2;
-0.5≤d≤0.5;
-0.5≤圆心位置偏移量≤0.5;
装配孔
-0.2≤直径≤0.2;
一般过孔
-0.5≤直径≤0.5;
-1.0≤d≤1.0;
-1.0≤圆心位置偏移量≤1.0
一般边缘
1.5≤d≤4.5;
-1.0≤h≤1.0
一般型面
说明:
1、表中数值为制件检具测量的平度、间隙大小。
若检具无法测量,应配合三坐标扫描进行确认分析,其数据应结合数模、车身坐标等加以确定。
2、不符合上表规定的全部判定不合格。
3、尺寸类缺陷,只判定合格与不合格。
4、出现不合格,应制订措施或更改模具等。
9.3返修缺陷检验判定标准
返修缺陷检验判定标准
整车区域
焊接质量
不允许出现裂纹
气孔缩孔
焊缝长度内出现一个气孔缩孔径≤0.5mm焊缝长度内出现2个以上的连续气孔缩孔径≤1mm
固体夹杂
夹渣、氧化物夹杂、金属夹杂
未溶合
在焊缝金属和母材之间或焊道金属和焊道金属之间未完全熔化结合的部分
未焊透
焊接时接头的根部未完全熔透的现象
形状缺陷
焊瘤\错边\烧穿\未焊满
表面缺陷
未做振动处理或处理后在检验区正常灯光条件下仍有抛光总面积的1/3以上可见
处理后在检验区正常灯光条件下仍有抛光总面积的1/3以下可见
1、未做抛光/振动处理或处理后在检验区正常灯光条件下仍有刨痕长度在5mm以上可见
2、深度占板厚的15%
1、处理后在检验区正常灯光条件下仍
有刨痕长度在5mm以下
2、手指甲触感觉不太明显
3、刨痕个数≤3条