第二章库存分析对于经营者来说增加销售或降低营运成本都可文档格式.docx
《第二章库存分析对于经营者来说增加销售或降低营运成本都可文档格式.docx》由会员分享,可在线阅读,更多相关《第二章库存分析对于经营者来说增加销售或降低营运成本都可文档格式.docx(16页珍藏版)》请在冰豆网上搜索。
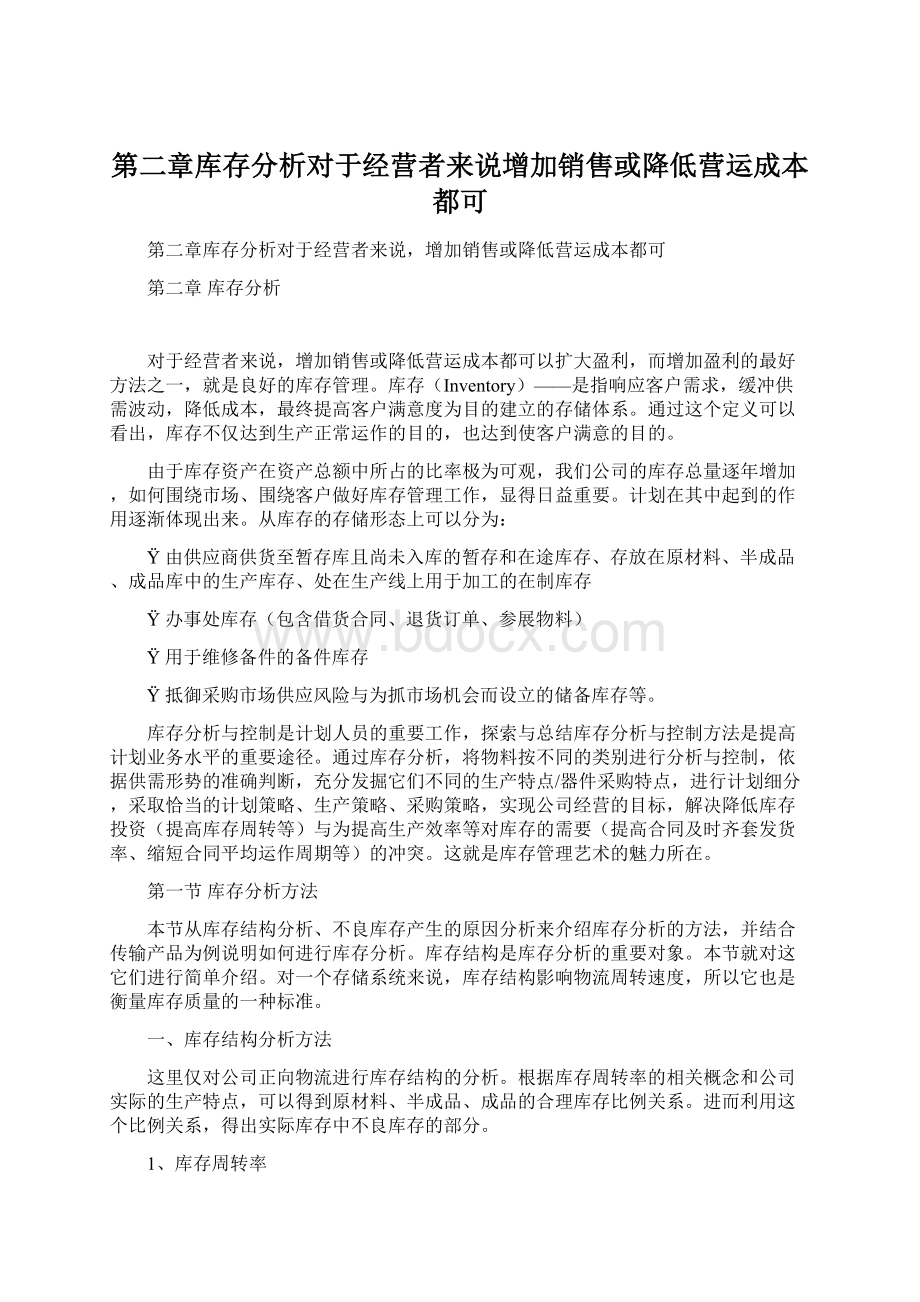
B=10天,(制造部调测周期)
C=2天,(货物部理货周期)
D=20天(用平均货龄近似)
E=5天(用单板加工周期近似)
则根据公式1得到:
原材料、半成品、成品的库存比例43:
37:
20
对比2001年5月份交换接入产品的相关数据:
þ
存货周转率为6.46次/年,
原材料、半成品、成品的库存比例为:
42:
38:
20。
公式1的推导:
用O、N分别表示出库、周转天数
V=
*
(1)
(2)
(3)
(4)
(5)
由2和3得到
(6)
由1、4、5、6可得
交换接入产品2000年6月——2001年5月存货周转率和库存结构关系图:
图3.2.1
以上分析表明:
1)在一定的时间段内,我们生产运作水平近似固定在一个水平(如半成品加工周期),这样库存周转率与库存结构两者只要知道了其一,就能推知另一个值。
2)通过控制库存结构,减少不同环节的库存浪费,就能提高库存周转率,在较低的库存水平下达到同样的客户服务水平。
二、不良库存原因分析
库存分析的重点就是关注库存中不合理部分,包括其所占整个库存的比例以及产生的原因分析,通过实际库存和理想库存的结构对比,我们可以将不良的库存从整个库存中提取出来。
1、产生的原因分析
图3.2.2要因分析图
(1)市场预测偏差
市场预测偏差会造成的额外库存资金。
我们从两个模型分别来推算要货计划偏差对库存的影响。
模型1:
为了满足发货,需要做一定的原材料库存,半成品库存,还必须有一定的半成品在制和成品在制。
通常半成品加工周期是6到10天,整机加工的周期是7到9天,整机发货1到2天,因此必须有大约10天的半成品库存(防止半成品加工出现断档等),10天的半成品在制,10天的成品在制,最多2天的整机库存,即差不多需要1/3M(半成品在制)+1/3M(半成品库存)+1/3M(成品在制和库存)=M,一个月的库存,假如我们再做一个月的原材料库存M(储备计划和正常生产需要的库存),则总库存是2M,即一个月里用2M的平均库存量保证了发货M,周转率是:
(M/2M)*12=6次/年。
在这个假设里,原材料:
半成品:
成品=50:
33:
17。
一般说来,半成品和成品的库存是按实际需求生产,控制的余地不是很大,控制的重点主要是原材料库存。
通过优化,半成品和成品的在制库存可以从20天减少到15天,半成品安全缓冲量的库存也可以从10天减少为7天,则总的半成品在制、半成品库存、成品在制和库存可从30天减少到22天,原材料的库存也可以从30天减少到20天,则通过改进、优化后库存周转率可以达到8.7次/年。
模型2:
如果原材料库存做2M,半成品和成品仍保持M,月发货料本为M,则周转率为M/(2M+M)*12=4次/年。
其他类推。
要货计划准确度为:
1-|要货计划-实际发货|/要货计划。
假设要货计划比实际发货大,准确度为80%,则因为发货小,周转率将比上面的计算小,在模型1里,周转率变为:
M*80%/2M*12=4.8次年。
在模型2里,则变为:
3.2次/年。
如果要货计划比实际发货大,准确性为50%,则模型1周转率为3次/年,模型2为2次/年。
可见要货计划准确性对库存周转率的影响很大。
上面是简化的模型分析,实际上由于计划是滚动制定的,过程有一部分被滚动冲减掉,再加上适当的到货控制,因此要货计划准确度对周转率影响没有上面计算的大,可以乘一个系数。
(2)版本切换
单板进行版本切换,基于切换的安全性考虑,各单板都有不同程度的重叠,对库存的影响较大。
(3)结构性偏差
为了应付个别定单的冲击,对一些用量少的单板需做一定量的库存,一般来说这些单板的周转速度要远远低于其他单板,造成库存增大。
(4)试产批量
由于部分试制产品实际的市场需求量比预计的要小,造成该部分产品的库存积压。
(5)备件返回
由于用服备件计划偏差,备件计划量经常大于实际的需求量。
(6)储备计划
(7)技术问题
(8)提前期不合理
(9)计划百分比
【案例】传输产品2000年某期存货分析
1、库存结构(单位:
万元)
表3.2.1
类别
总金额
生产状态
中试状态
占总量比例
原材料库存
6003
5073.9
937.6
38%
半成品库存
5223
3883.8
1343.4
33%
半成品在制
2204
1902.5
301.2
14%
成品库存及在制
2291
15%
总计
15721
100%
2、传输产品库存合理值探讨
我们从年目标库存周转率和理想周转天数两方面来讨论。
方法一:
根据公式库存周转率=当月发货料本*12/当月平均库存,来测算九月份的合理库存:
预计九月发货料本=各产品预计九月发货量*该产品料本
=110*23+350*8+(300+500)*2=6930万元
库存周转率按年初计委所确定的指标5次/年
因此,九月份的库存合理值=当月发货料本*12/库存周转率=6930*12/5
=16632万元
方法二:
根据各环节周转天数折算周转率。
从逻辑上说,当传输产品和交换接入产品要货计划准确率相等的情况下,其原材料库存周转天数、半成品库存周转天数应该与交换接入的相同。
另外由于交换接入产品六月份起做了大幅度下调,七月份、八月份的原材料库存、半成品库存周转天数不够理想。
因此,用交换接入产品四、五、六月原材料库存、半成品库存周转天数平均值替代传输产品来计算传输理想周转率。
理想库存周转率=365/18.5+9.2+13.6+3.5+11=365/55.8=6.5次/年
九月份库存理想值=当月发货料本*12/6.5=6930*12/6.5=12794万元
3、目前库存与理想值相比存在的问题
(1)差异:
目前库存总额与理想库存值存在3000万元的差异
不合理物料生产中试分布表3.2.2:
单位:
万元
表3.2.3
原材料
1,743
334
2,077
半成品
323
743
1,066
2,066
1,077
3,143
(2)差异原因分析:
主要针对金额占用大的S、A类物料,将其当前的库存与未来一个月的毛需求进行对比,如库存大于未来一个月毛需求即视为不合理,大于部分为不合理库存值,经过分析差异原因如图3.2.2所示。
(3)不合理库存的来源
造成目前3143万不合理库存主要有下面几个因素,各因素所占金额的比例如图3.2.3:
图3.2.3不合理库存来源分布图
各因素影响库存金额的详细数据如下:
①要货计划偏大:
影响库存金额842.4万元
②版本切换:
影响库存金额486.9万元
99年SDH产品90%的单板都要进行版本切换,基于切换的安全性考虑,各单板都有不同程度的重叠,对库存的影响较大。
③结构性偏差:
影响库存金额460.8万元
传输产品的单板种类较多,其中SL1、SL4、T16尤为明显,目前SL1、SL4并行发货的新旧单板分别多达7、8种,由此造成的额外库存较大。
另外每月需求量较少的单板如:
SE2、PL3、PL4、BA2、TPS、SLE等,为了应付个别定单的冲击,对这些单板需做一定量的库存,一般来说这些单板的周转速度要远远低于其他单板,这也是造成库存增大的一个原因。
④试产批量:
影响库存金额379.1万元
98年底,SS33T16试产评审定为150套料,但由于市场需求量较小,造成379.1万元的库存积压。
⑤备件返回:
影响库存金额315万元
⑥储备计划:
影响库存金额276.7万元
⑦技术问题:
影响库存金额147.7万元
1)31T16和32T16同时做入BOM清单,这两块板技术上可相互替代,因此清单中31T16和32T16的比例为1:
1,但再实际发货时才发现32T16存在技术问题,不能用于市场发货,结果导致31T16物料计划量不足,而32T16物料计划积压,并且影响了市场发货。
32T16影响库存金额74.8万元。
2)AKJ/AKM工艺问题:
编码35030075含两种型号AKJ/AKM,而传输155A主控板SCB上只能使用AKJ工艺FPGA-XC5206,为避免混发料,为AKJ工艺XC5206申请了专用编码99010080,同时清单也做了相应更改。
四月份采购突然回复说:
AKJ工艺的XC5206无法购买。
中研项目人紧急用AKM替代AKJ测试,最后确认可用AKM替代在SCB上使用,清单又改回35030075。
但更改清单时未将99010080的库存转移到35030075下,致使在跑MRP计划时未能冲减其库存使计划做大,影响库存金额57.4万元。
3)ECO更改:
占用库存金额15.5万元。
⑧提前期不合理:
影响库存金额126万元
八月中旬进行的传输库存分析中,发现2.5G整机调测提前期偏长约三天,由于提前期的不准确造成库存资金约126万元。
⑨计划百分比:
影响库存金额109万元
这里主要是指发货附件中的项目如电缆、光连接器需求不确定,物料计划失真,影响库存109万元。
第二节死料、低周转物料的分析与处理
由于市场预测与实际需求的差异、市场退货、版本切换、超存储、来料质量问题等因素的影响,不可避免会产生不良物料。
计划人员有责任将不良物料控制在一个合理水平,减少不必要的经营风险。
死料与低周转物料的控制是计划人员的一项重要工作,熟练其分析方法、处理流程是对计划人员的基本要求。
一、定义
1、死料
死料就是没有用途、要报废的物料。
华为的死料定义为:
库存项目在当前计划期内需求为零,并且在公司范围内没有最终用途的物料。
2、低周转物料
低周转物料就是周转频次低于正常物料的那部分库存。
华为的定义为:
库存大于6个月需求的物料或周转率小于1次/年的物料。
公司的计划模式是用可执行的发货计划来驱动整个供应链计划的,这样预测与实际需求就会存在差异,再加上版本切换、ECO、逆向物流、计划百分比等因素,产生死料、低周转物料是不可避免的。
但如何及时处理死料、及时利用与消耗低周转物料、通过分析发现管理中存在的问题,不断地改进的工作是我们每个计划人员的责任。
二、分析与控制
计划人员每天都要花较多的时间来进行计划分析,死料、低周转物料产生的原因分析是计划分析的重要内容。
出入库数据、MRP毛需求数据是分析的基础数据,通过查询库存的来源(采购入库时间/由谁下达计划、转库、库存调整)、推算库存形成时间、再查询物料的历史用途、曾经的替代关系、相关的版本切换信息、ECO、追溯库存产生时间的计划量及变化、计划百分比维护记录等进行计划‘考古’,对死料与低周转物料的产生原因进行分析。
同时将其中的典型问题写成案例,把失败的教训写下来,使其他计划人员及后来者少走弯路、少犯同类的错误。
常见的死料与低周转物料产生的原因归结如下:
1、计划方面原因
Ÿ市场预测波动
Ÿ计划百分比维护
Ÿ计划失误
2、技术方面原因
Ÿ版本切换
ŸECO
Ÿ产品停止销售
3、采购与认证
Ÿ最小批量过大
Ÿ风险采购
4、BOM
Ÿ清单错误
Ÿ编码合并
三、对PO的监控
发现了死料与低周转物料,仅对现有的生产库存进行处理是不够的。
还需要审视其他环节的库存情况(备件、维护库存;
逆向物流库存--待处理品相关库存、故障品库存;
等),尽可以将损失降到最低。
同时需要对PO进行监控,通过例外信息等工具,对相关PO进行处理。
由于多库存组织的计划分开运作,加大死料与低周转物料的PO处理难度。
在进行版本切换/ECO计划控制时,严格控制死料与低周转物料的产生,确保切换目标的实现;
当物料已经成为死料、低周转物料以后,通过转库或实施内部订单等方式,使其他组织在已经考虑这些物料以后,再进行处理PO(推迟或取消)、下达PR;
同时在一定的条件下,将本组织的PO转到其他组织消耗。
这样,通过对PO进行处理使公司的损失最小化。
四、处理方法
每个月对低周转物料进行处理一次,每个季度对死料进行处理一次。
先由物控人员把所有符合定义的物料清单及库存等情况提取出来,再由计划人员对用量等进行确认,得到死料、低周转物料的清单,然后通过转库、内部订单等方式进行消耗。
1、转库
单项转库金额小于限额(目前为20万元)的物料,在不使转入组织成为低周转的数量范围内,一次性转库消耗。
2、实施内部订单
对于单项转库金额大于限额(目前为20万元)时,转入与转出双方计划员共同拟定一个转库计划(每次转库量为转入组织半个月用量),通过内部订单的形式记录下来双方的协议。
这个协议‘一言九鼎’,由三方人员--物控--来实施,每周转库一次,转库不再通过双方审批。
【案例】传输产品2000年第五期低周转物料、死料分析
1、低周转物料、死料金额统计
低周转物料、死料总计168项,总金额321.53万元;
其中死料15项,金额9.99万元,占总金额的3.1%。
具体分布如表3.2.2:
表3.2.2
形成原因分类
项数
金额(元)
百分比(%)
计划
要货计划偏大
3
23.85
7.4
库存计划偏大
0.72
0.2
计划百分比偏大
1
0.24
0.1
组织拆分
6
28.26
8.8
转库量过大
4
1.4
0.4
合计
14
54.47
16.9
技术
版本切换
115
182.65
56.8
ECO更改
16
70.26
21.9
产品停止销售
2
0.52
133
253.43
78.8
认证与采购
最小采购批量过大
8
8.39
2.6
风险采购
2.07
0.6
9
10.46
3.3
BOM
编码拆分
无价格
商务需求变化
1.89
其他(器件本身问题、实验退库)
1.28
168
321.53
100
2、典型事例分析
31TPS,一月份单列计划总计330pcs,三月份单列计划总计155pcs,导致相关物料11010039等的呆料
50010074S,合同统筹提需求时提了2pcs,该合同却只用了1pcs
155A/H向622H切换后遗留呆料64万
14220003/14040090,母板电口后出线方式配套物料,与11PL4、12SLE、31SE2配套使用,三单板升级后不用;
产品组未及时提供切换信息;
由于储备计划和长单等因素,导致了38万元的呆料
最小采购
批量过大
41010069,最小批量3k,97年下计划3k,消耗到现在还剩余1500
3、呆死料的分析处理
表3.2.4
项次
金额(元)
转待处理品中心呆料库
15
9.99
转TC
13.23
转GSM
16.8
转CC
1.71
转ETS
1.27
转DDC
2.48
替代
3.48
合计
31
48.96
第三节库存控制的主要方法与应用
本节的主要内容是:
结合华为公司计划实际,介绍了目前主要采用的库存控制方法:
ABC分类、JIT、OEM、VMI、安全库存、储备等。
华为公司处在一个市场变化快、产品更新快、竞争激烈的环境中,产品配置灵活,器件采购周期长,客户要求交货期短,形成了华为特色的库存管理模式:
在合理的库存投资范围内,快速满足客户需求,支持公司持续、快速发展。
一、库存控制方法在华为公司的应用简介
1、ABC分类在华为的应用
库存ABC分类得到广泛的应用,已经成为一种有效的库存控制模式:
建立正常的物次秩序,提高了库存管理效率,有利于降低库存。
库存ABC分类,既可以用于公司、库存组织进行分类控制,也可以用于某计划员所负责的物料进行分类控制。
计划ABC和仓储ABC两种库存ABC分类方法,计划所用的是物料的计划期内需求总金额进行分类控制的,而仓储所用的是物料单价进行分类控制的。
计划ABC控制主要是控制订货点,通过设置固定供应天数来实现;
仓储ABC控制主要是采用不同的盘点频率、不同的管理方法(如贵重物品管理办法等)来确保库存数据准确率与存货安全。
计划ABC的控制方法改变(调整固定供应天数)需要采购等部门的配合,它不是计划的单独行为。
2、JIT
原材料的库存存在,其原因是需求、原材料质量的不可预测性等;
半成品的库存存在,其原因是需求的不准确、设备故障等,类似“我们为什么要保持这些库存?
”或“我们能否取消这些库存”一个一个问题的深入,发现JIT的目标确不容易实现。
目前,我们公司在占地面积大的结构件,如:
骨架、门板等实现了JIT供应,正在实施PCB、电缆等物料的JIT供应。
虽然我们许多方面还离JIT的目标很远,但应用JIT的思想指导我们日常工作所达到的成效还是随处可见。
3、OEM
通常由外协厂加工的单板、电缆等物料的原材料是由我们公司提供,而OEM将直接承担从原材料的采购到半成品加工的全部环节,这部分的原材料库存由OEM承担。
目前由OEM提供的半成品主要是电缆。
OEM从产品设计时,就需要根据产品策略,确定产品(或部件)是否按OEM方式生产。
4、安全库存
安全库存是预防急单和产能不足而设置的库存量。
它能够缓解急单对半成品生产的冲击、均衡生产能力。
目前,我们公司主要对单板、POC物料、生产辅料等实施安全库存,单板的安全库存一般设置为月用量的1/4到1/2。
5、关键器件储备
关键器件储备是为了避免或减少供货市场的波动对物料供应的影响,它包含的物料范围是未来供货市场的波动,预计会影响我司物料的正常供应的采购器件,如货期长、独家供应商、供货风险大等。
6、VMI
一般来说,库存是由库存拥有者管理的。
由于无法确切知道用户需求与供应的匹配状态,因此需要库存来应付不稳定的内部需求以及供应链的不确定需求。
供应链中的各个企业根据各自的需要独立运作,导致重复建立库存,无法达到供应链全局的最低成本。
VMI(VendorManagedInventory)是一种很好的供应链库存管理策略,它是一种用户与供应商之间的一种合作性策略,在一个相互同意的目标框架下由供应商管理库存,以最低的成本优化产品的可获得性、供应的可视性。
目前,华为公司在供需基本平衡或供大于求、货期短、与供应商合作关系良好的物料实施VMI,已经在工具软件项目实施了VMI,正在实施成套资料、结构件等物料的VMI。
三、库存控制的分析与评价
1、统计指标
从控制的基本过程:
测量(统计)、诊断(分析)、调整(纠偏)来看,统计分析也是库存控制的基本内容。
通过库存周转率、合同及时齐套发货率两项统计指标,从降低库存、满足需求两方面体现生产运作的水平。
库存周转率的提高意味着缺货风险增大,或因小批量采购导致采购成本增加。
因此,库存控制不等于一味强调低库存、高周转率。
一些企业所犯管理错误,是对库存周转率指标的刻意追求。
2、统计分析内容
物流网络各节点的物料存量、流量、周转速度,进一步细分到:
è
各库存组织
各产品线
各产品
反映各产品(线)下列计划之间的协调性、水平及问题所在:
要货计划
采购计划
加工计划
装配计划
发货计划
3、评价与分析方面
库存周转率
大小及均衡性
大小及合同及时齐套发货率
库存结构
沿物料流向各环节所占比重
单一环节(物流网络结点)的存量结构
(1)库存周转率与客户服务水平--及时齐套发货率
图3.2.4
(2)在制量比重与产能瓶颈、物料齐套的关系
产能瓶颈、物料不齐套,使物料不能顺利通过系统。
原材料及在制品在生产线之间堆积,增加了在制品在生产线上的滞留时间。
在制品周转天数增加。
物料不齐套的后果:
不能及时交货,服务水平下降
制造成本增加:
大量的人员协调、或停工待料、或加班加点。
4、通过理论数据与实际数据对比,发