制氢甲烷化催化剂的性质和使用Word文档下载推荐.docx
《制氢甲烷化催化剂的性质和使用Word文档下载推荐.docx》由会员分享,可在线阅读,更多相关《制氢甲烷化催化剂的性质和使用Word文档下载推荐.docx(8页珍藏版)》请在冰豆网上搜索。
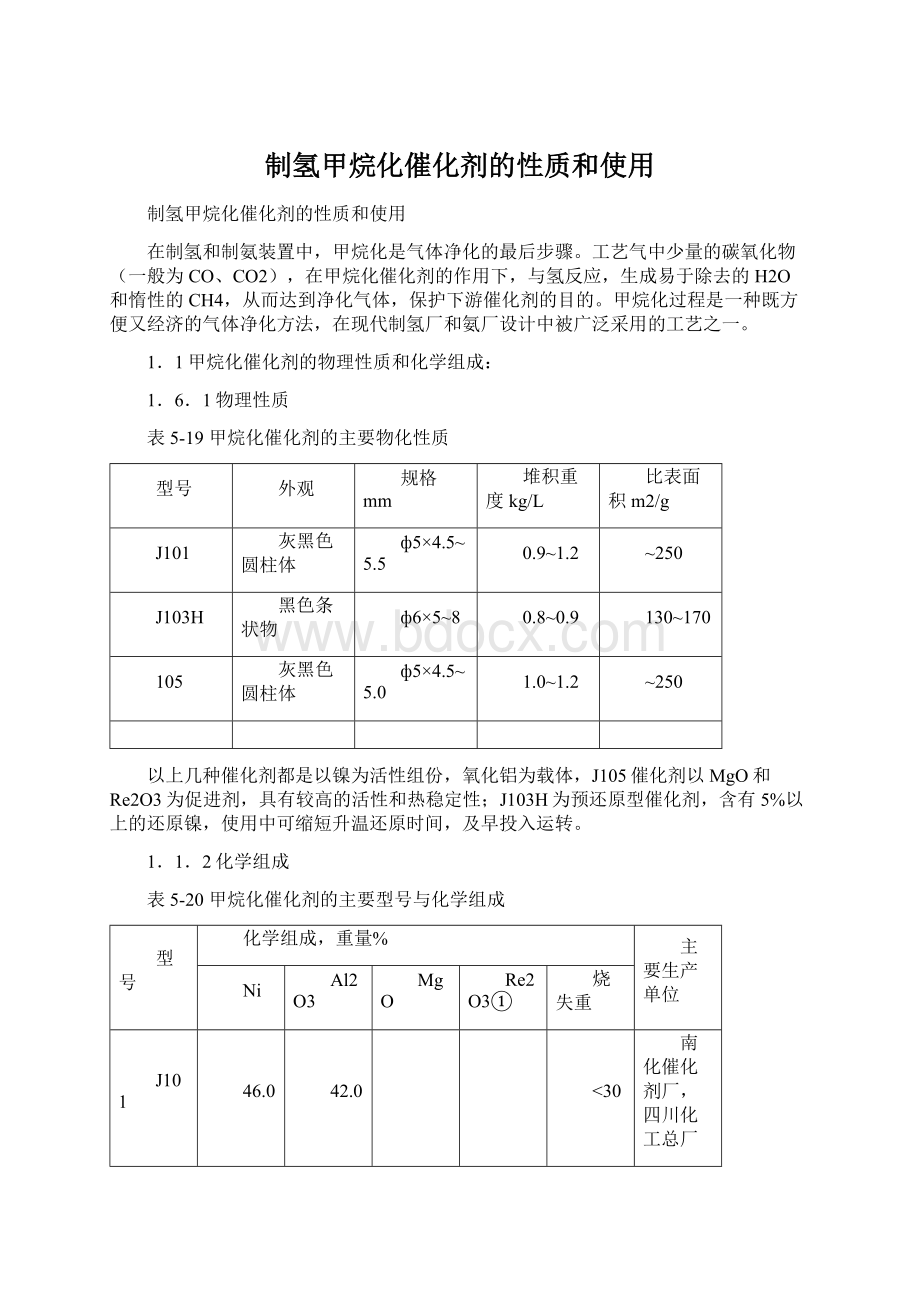
0.8~0.9
130~170
105
4.5~5.0
1.0~1.2
以上几种催化剂都是以镍为活性组份,氧化铝为载体,J105催化剂以MgO和Re2O3为促进剂,具有较高的活性和热稳定性;
J103H为预还原型催化剂,含有5%以上的还原镍,使用中可缩短升温还原时间,及早投入运转。
1.1.2化学组成
表5-20甲烷化催化剂的主要型号与化学组成
化学组成,重量%
主要生产单位
Ni
Al2O3
MgO
Re2O3①
烧失重
46.0
42.0
<
30
南化催化剂厂,四川化工总厂
≥12②
余量
辽河化肥厂催化剂分厂
≥21.0
24.0~30.5
10.5~14.5
7.5~10.0
28
南化催化剂厂,南化研究院
①Re2O3—稀土氧化物,②含5%以上还原态镍
1.1.3化学反应式:
CO+3H2=CH4+H20Q=-206.28KJ/mol
CO2+4H2=CH4+2H2OQ=-165.09KJ/mol
O2+2H2=2H2OQ=-483.99KJ/mol
在操作的过程中,每1%CO转化的绝热温升为72℃,每1%CO2转化的绝热温升为60℃。
5.6.2催化剂的装填、还原和钝化
5.6.2.1催化剂的装填
对甲烷化催化剂的装填应引起充分的重视。
因为该催化剂是在高转化率的条件下操作的,一般入口气中的CO+CO2为数千ppm,而出口仅几个ppm,几乎百分百地转化。
如果催化剂装填不均匀,产生沟流,使部分原料气短路穿透,将导致出口微量上升而产生严重的后果。
所以在装填前,应仔细检查反应器,清除一切杂物。
若运输过程中因搬运不当造成粉尘或碎片增多时,应过筛除去。
以防碎粒催化剂堵住反应器出口的筛网。
检查合格后,铺上一层厚度为50~100mm,直径为10~15的而耐火瓷球或瓷环,但任何一种材料的熔点均应超1000℃。
装催化剂时,应保证催化剂在床层内分布均匀,一般采用布袋软管或人进入反应器内的方法将催化剂均匀铺设,严禁采用将全部催化剂从某一位置倒入反应器内,堆成一堆后再耙平的做法。
这样的装填方法会使催化剂有分级散开的倾向,小颗粒和粉尘主要留在堆子中心,而较大颗粒的催化剂滚向边缘,造成气体分布不均匀。
催化剂层耙平后,在催化剂床层上铺一层厚度为50~100mm,直径为10~15mm的耐火瓷球或瓷环,以避免顶层催化剂受到扰动,并有助于原料气体分布均匀。
在这些瓷球(环)和催化剂之间应有一层不锈钢丝网隔开,当气体线速度较大而且气体入口直接指向催化剂床层且距离又不到1.0米时应考虑在入口处装有气体缓冲分布板,以减少高速气体直接冲击催化剂而造成催化剂床层的移动。
注意事项:
(1)催化剂自由落下的高度不能超过1.0米;
(2)人进入反应器装剂时,不能直接踩踏催化剂及热电偶,应垫以木板,防止催化剂破碎。
(3)装填人员应戴防尘面具。
5.6.2.2催化剂的还原:
在部分型号的甲烷化催化剂都是以氧化态的形式提供给用户的,首次使用时,必须用氢将氧化镍的催化剂还原成金属镍才具有活性,还原反应式如下:
NiO+H2=Ni+H2OQ=2.55kJ/mol
NiO+CO=Ni+CO2Q=-30.25kJ/mol
这些反应都不是强放热的,还原过程本身不会引起催化剂床层大的温升。
从热力学考虑,催化剂的还原是比较容易的,在300~400℃范围内,还原气体中H2浓度在1%以上即能使还原反应进行,但要还原完全并获得最大的活性镍表面积就比较复杂,和还原过程中的温度,空速等因素有关,催化剂的组成及制备方法对还原结果也有很大的影响。
1.温度压力等因素对还原的影响
温度是还原过程中的主要因素,镍催化剂一般在300℃左右即开始还原,350℃时巳有可观的还原度,为还原彻底,还原温度需升到400℃。
表5-20列出工业催化剂还原度与还原温度的关系。
表5-20工业催化剂在不同温度下的还原度。
还原温度,℃
304329354379405
还原度,%
4.827.969.690.6101.2
注:
还原度超过100%是由于试验误差引起的
在实验室中,进行了温度、压力对催化剂性能影响的试验,其结果是J105催化剂在300~400℃下还原一段时间巳获得合格的活性,在入口气CO2为0.9~1.1%、空速为8·
103h-1等条件下,出口CO2小于6ppm,为获得更高的活性,还原温度可提高到400℃。
另外,还原压力对催化剂活性影响不大,但采用工艺气还原时,还原过程中伴随有甲烷化反应,提高压力有利于对甲烷化反应的进行,这样,可提早获得合格的工业氢。
2.催化剂的升温还原操作:
甲烷化催化剂的还原可分为装置原始开工的还原和正常更换催化剂时的还原。
如果是原始开工的还原,可用纯N2作升温介质,用开工加热炉作热源在线外进行还原操作,也可在开工后期采用粗气进行还原,但开工周期太长。
如果是正常更换催化剂时的还原,可在开工后期采用粗氢进行升温还原操作。
由于催化剂的还原反应是微放热反应,因此还原几乎是等温的,整个还原过程可分为:
升温期、还原主期和还原末期。
(1)升温期
先用N2把整个系统中的O2置换干净,系统压力充N2至0.5MPa,以提高气流线速度,缩短床层温差。
升温阶段可通过控制导入工艺气入口温度的高低来调节升温速率在50~70℃/h,把床层温度升至200~250℃,工艺气量一般在20~50%负荷即可。
(2)主还原期
当床层温度加热到200~250℃以后,开始还原,但速度较慢,当床层温度升到300℃以上还原明显加快,为了避免温升过大,这时应小心控制进口温度的升温速率在20~30℃/h。
按上述的升温速度把反应器床层最低点温度升至350℃(但要严格控制床层最高温度≯400℃时),还原6小时巳具有合格的活性。
(3)还原末期
继续加热催化剂,直到入口温度达到350℃,并维持这个条件保持到床层出口温度等于床层中最高温为止,且要求床层最高温度达到400℃并维持2~6小时,以获得最佳的活性。
这时,催化剂还原结束,然后将入口温度逐渐降至设计温度并转化正常操作。
3.升温还原中应注意的问题:
(1)在催化剂还原过程中,操作人员必须时刻注意反应器内床层温升情况,发现床层温度有突然上升趋势时,立刻把入口温度降下来,以免反应器超温损坏设备。
(2)由于催化剂中尚有残留的碱式碳酸盐会分解,当床层温度升到300℃时,有CO2放出,而这部分CO2也会参加甲烷化反应,若采作循环升温方式,应适当加大循环的放空量,保持CO2<1%,以防积累CO2伴随甲烷化反应而引起温升。
(3)在用上游来的工艺气还原时,要严格控制工艺气中碳的氧化物含量,因为在床层温度达250℃后还原与甲烷化反应会同时进行,因此要特别注意防止超温。
(4)还原过程中氢耗并不明显,在床层温度达到预定计划指标后,维持一定时间,以出口气体中碳的氧化物符合设计指标后稳定数小时,即可认为还原基本结束,转入正常生产。
(5)J101、J105催化剂在还原过程中有较多水放出,其理论出水量为65~75kg/m3,所以在还原期间应及时排放分离器中的水,降低气体中的水汽浓度。
(6)有些工厂,可能达不到应有的进口温度350℃,而床层温度也难以达到400℃下进行还原,此时也可以使部分气体绕过低变反应器旁路以增加碳的氧化物含量,成功地还原催化剂。
但要小心谨慎地操作,防止CO+CO2浓度超高,引起催化剂床层激烈温升而导致催化剂活性的损失,或造成甲烷化炉设备的损坏。
1.2.3甲烷化催化剂的钝化
巳被还原的甲烷化催化剂从反应器中卸出时与空气接触会发生剧烈的氧化反应,并放出大量的热量,其反应式如下:
Ni+1/2O2=NiO(剧烈放热)
所以催化剂必须经过钝化处理后才能卸出。
当要卸催化剂时,可将系统压力降至常压,充N2置换降温至250℃。
当催化剂需要再使用时,可在N2气流中配入少量的空气(控制床层温度≯400℃)缓慢进行钝化处理,逐步加大空气量,直到全部通入空气冷却至40℃后,把催化剂卸出过筛,密封包装,保存备用。
如需从新更换催化剂,在切断工艺气后可导入蒸汽,用蒸汽将催化剂冷却到能达到的最低温度,切断蒸汽用N2气置换,打开人孔,卸出催化剂并用水喷洒,使其保持湿润,马上装袋拉走深埋或回收,防止污染环境。
1.催化剂钝化操作步骤
催化剂钝化在装置停工后期进行,其操作步骤如下:
(1)当甲烷化床层温度降至250℃时,改好流程,从开工联箱将排干净冷疑水的1.0MPa蒸汽引入甲烷化反应器,蒸汽量由小到大,缓慢进行,直至甲烷化出口有蒸汽放出。
(2)根据净化风的压力,用蒸汽阀控制开工联箱出口压力比净化风压力低0.05~0.10MPa,待压力稳定和转化、脱硫系统循环置换分析合格后,开始配入净化风(先用小阀配),这时要密切注意床层温升的变化,控制温升小于50℃/h,若温度上升趋势较快,则关小净化风阀;
若无温升,稳定一小时后,再开大净化风阀(小阀全开后再开大阀),若上升趋势较快,则关小净化风阀;
若无温升,再开大净化风阀,余类推,直到净化风阀全开。
在钝化的过程中,控制床层最高温度≯400℃。
一般来说每次增加空气小阀开度不大于60度,时间间隔≮1小时;
若温升较快,必须立即切断空气,加大蒸汽量降温,待床层温度正常后,再恢复钝化操作。
(1)当床层热点温度下移至出口(出口温度稍有下降),且耗氧不明显时,可全开配空气小阀。
在此条件下,氧化1~2小时,若温升较快,则把配空气小阀关小到原来开度;
(2)若床层无温升,则小开净化风大阀,同时调节好净化风与蒸汽的压力,观察床层温度变化,若温升过快,则立即把空气大阀关闭。
按温升<50℃/h,床层最高温度不大于400℃的原则逐步开大空气大阀。
(3)当空气大阀开大而床层无温升且不耗氧时,稳定2小时后,逐步关小联箱蒸汽阀,每次关蒸汽阀使联箱压力只下降0.01MPa即可。
同时观察床层温度变化,若有温升,立即把蒸汽阀开大。
半小时后,若床层无温升,则继续关小蒸汽阀,方法同上。
当床层最高点降至180℃后,把蒸汽阀全关,单独通空气降温。
这时要注意床层温度,如有温升则要开蒸汽降温。
(4)钝化结束的标准是:
出口含氧达21%,床层温度下降,钝化结束。
钝化结束后,继续用空气降温至床层温度<50℃时,便可把催化剂卸出。
2.注意事项
(1)岗位人员在操作前必须熟悉钝化方案,掌握钝化流程、调节手段及异常情况的处理方法,操作上要有极大的耐性。
(2)开始配空气后,至少要有一个小时的观察期,因其测温滞后现象较大,要有极大的耐心。
(3)在钝化的过程中,按提氧不提温,提温不提氧的原则进行操作。
(4)床层温升始终控制≯50℃/h,最高≯400℃,以防催化剂烧结。
(5)每半小时记录一次反应器床层温度,发现异常,立即处理。
1.3甲烷化催化剂的停车、再活化与正常使用条件
1.3.1停车:
甲烷化催化剂如需短期停车,可以短期内保存在合格的工艺气流中,仅需关死甲烷化炉进出口阀门,保持炉温与压力。
如果停车时间较长,需降温降压。
当温度降到200℃时要用N2置换干净,并维持正压,防止空气进入炉内生成羰基镍。
如果要更换催化剂,必须将催化剂钝化后才能卸出。
1.3.2再活化:
甲烷化炉用纯N2升温到250℃,切换成工艺气,再升温到300℃,待出口CO+CO2符合工艺指标即可转入正常操作,如没有条件使用纯N2升温,可采用工艺气,但应尽快将床层各点温度提到200℃以上,以防羰基镍的生成。
再活化的条件可参考下表5-21:
5-21催化剂再活化的条件
温度范围,℃
室温~250
250~300
300
时间,h
累计时间,h
气体介质
4
纯N2,或N2—H2气
2
6
工艺气
12
1.3.3正常操作条件:
甲烷化催化剂的正常操作条件如下表所示。
在催化剂投入运转时,空速、压力等操作参数基本固定,无多大调节余地;
原料气组成主要为变换系统与脱碳岗位所控制,主动权不在甲烷化工序,有足够调节余地的操作参数为温度。
通常,使用初期催化剂性能较好,入口温度可调节在操作温度的低限,床层温度保持在300~320℃,以后,随着使用时间的延长,可适当提高反应温度,保证出口微量符合指标。
使用中期,床层温度控制在350℃左右,使用后期可在380℃左右操作。
应该说明的是,操作温度的选择还受到反应器材质、防止羰基镍生成等因素的限制,就催化剂性能而言,可使用的范围较宽,如J105催化剂可在500℃下较长时间运转。
5-22甲烷化催化剂的正常操作条件
催化剂型号
J105
压力:
MPa
常压~3
常压~20
温度:
℃
270~400
270~450
空速:
h-1
2000~3000
6000~10000
原料气组成
CO2:
0.3%,CO:
0.4%,余H2-N2气
CO2:
0.4%,余H2-N2气
1.4催化剂的使用寿命
甲烷化催化剂活性较好,按照技术要求操作,出口CO+CO2含量指标是没有问题的,如果脱碳工序稳定,甲烷化入口气中H2S等毒物脱除干净,甲烷化催化剂使用寿命可达8~10年。
一般来说,催化剂使用寿命的终止是由于催化剂活性的丧失或由于催化剂强度破坏造成催化剂破碎粉化,床层阻力降明显增大的缘故。
而影响甲烷化催化剂活性的主要因素是由于中毒或烧结。
砷、卤素是镍催化剂的毒物,最常见的毒物是硫。
硫是一种累积性毒物,即使浓度很小但也会使催化剂中毒,影响催化剂的使用寿命。
催化剂只要吸收了0.1~0.2%的硫即能导致活性明显地降低,而且这种中毒是不可逆的永久性中毒。
甲烷化催化剂的硫中毒是分层进行的。
起初,入口气中H2S几乎完全被上层催化剂所吸收,引起其活性衰退,而下层催化剂仍处于无硫气氛下。
当上层催化剂吸硫达0.2%,活性衰退大半,但这部分催化剂仍有较强的吸硫能力,对下层催化剂继续起到保护作用。
最后,当吸硫量达到0.6~1.0%时,H2S就有可能穿透到下层催化剂,使其逐渐中毒,导致催化剂失效而被迫更换。
所以,为了保证催化剂有较长的使用寿命,应采取措施将入口气中的硫浓度降到ppb级的水平。
1.5常见事故及处理
1.1.1甲烷化炉温升高于正常值
1.原因:
(1)变换系统出故障引起甲烷化入口气中CO含量增加;
(2)脱碳系统操作不当,引起CO2超高。
2.处理方法:
(1)调节变换系统各项操作参数,使其恢复正常,以保证出口CO含量符合指标。
如变换催化剂活性严重衰退,则更换催化剂。
短期内更换有困难需继续维持生产时,甲烷化炉可在保证出口微量符合指标的情况下,尽可能降低入口温度(但不得低于250℃)使热点温度不超过500℃,
(2)认真检查脱碳系统各操作环节,脱碳溶液的浓度、循环量及循环泵的运转状态,尽快使脱碳系统恢复正常。