机械制造阀腔工艺过程设计Word下载.docx
《机械制造阀腔工艺过程设计Word下载.docx》由会员分享,可在线阅读,更多相关《机械制造阀腔工艺过程设计Word下载.docx(17页珍藏版)》请在冰豆网上搜索。
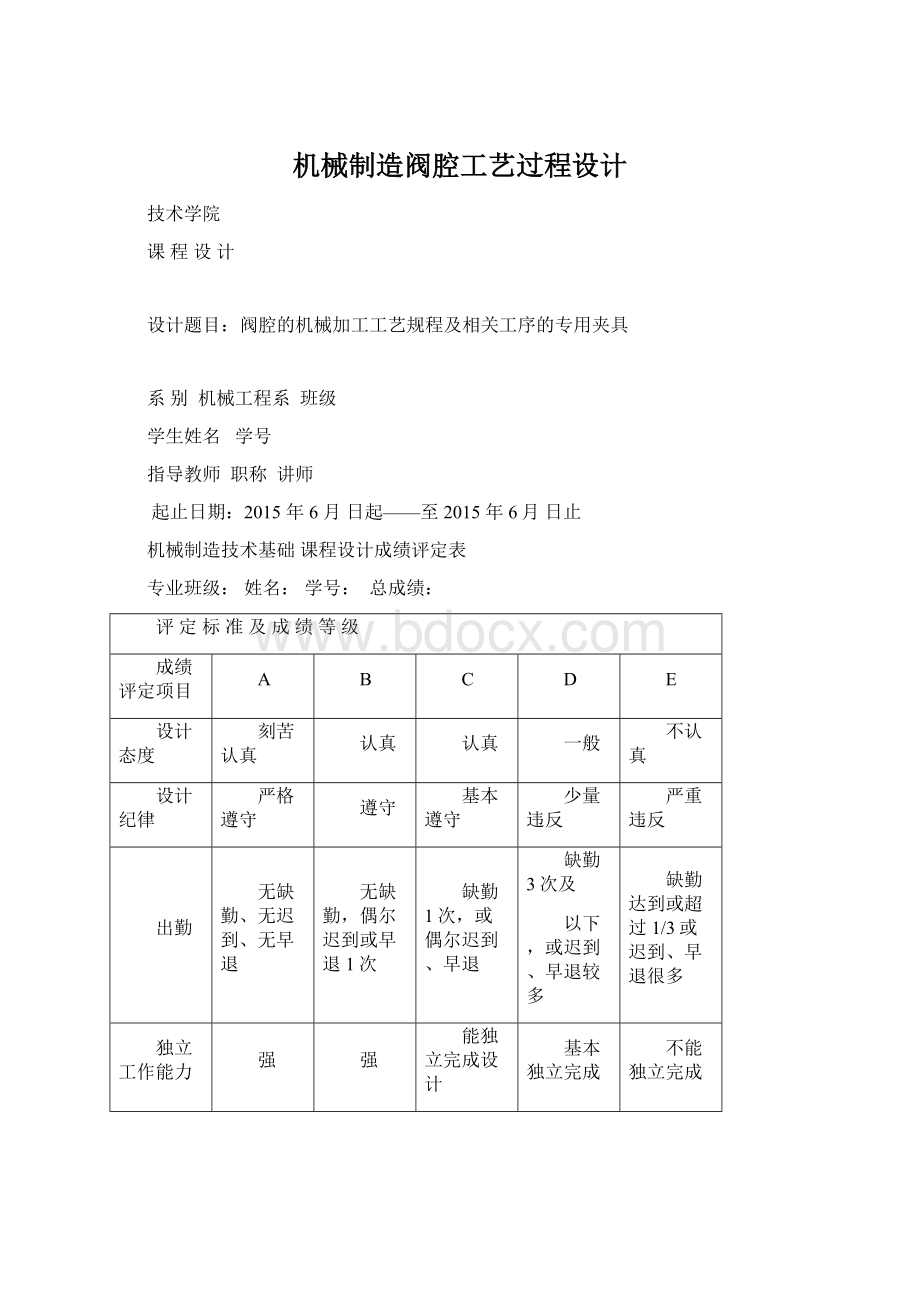
基本独立完成
不能独立完成
设计进度及上交成品时间
提早或按时
按时
滞后0.5天
滞后1天
滞后1.5天及以上
设计计算
设计思路清晰,结构方案良好,设计参数选择正确,条理清楚,内容完整,结果正确。
设计思路清晰,结构方案合理,设计参数选择正确,条理清楚,内容较完整,极少量错误。
设计思路较清晰,结构方案基本合理,设计参数选择基本正确,内容基本完整,有少量错误。
设计思路基本清晰,结构方案基本合理,主要设计参数选择正确,内容基本完整,有些错误。
设计思路不清晰,结构方案不合理,关键设计参数选择有错误,内容不完整,有明显错误。
说明书内容
规范、端正、整洁、有条理
规范、端正、
较少涂改
较工整
少量涂改
潦草
较多涂改
非常潦草
大量涂改
回答问题
基本正确
个别错误
多个错误
无正确
图面质量
好
差
非常差
综合评定
成绩
优秀
A>=7
C<=0
良好
A>=5
C<=1
中等
A>=3
D<=0
及格
D<=5
不及格
E>1或
D>=5
指导教师:
吕海鸥、王天煜
机械制造技术课程设计任务书
题目:
设计阀腔零件的机械加工工艺规程及相关工序的专用夹具
任务及要求:
一、确定零件的生产类型
年产量12000件,备品率5%,废品率2%。
(大批量生产)
二、工艺文件的设计步骤
11、详读零件图,分析零件结构及技术要求。
确定毛坯类型及精度,技术要求,毛坯余量,设计毛坯图。
初步建立零件制造的过程和方法。
12、选择加工方法,合理划分粗、精加工阶段,确定最佳工艺路线。
13、某一个加工工序设计和工艺计算:
选择加工设备与工艺装备,确定工序尺寸,选择各工序切削用量,计算时间定额。
14、设计加工工艺过程卡片,格式见《机械制造技术基础课程设计指南》,P112表4-8,卡片大小为A4幅面(可打印)。
15、设计某一个加工工序的机械加工工序卡片,格式参照《机械制造技术基础课程设计指南》,P113表4-9,幅面大小为A4幅面(可打印),卡片中的参数、工时定额及辅助时间等参阅指南中相关内容确定。
16、设计某工序的夹具,用A1图纸画出夹具的装配图。
包括定位设计、夹紧设计、辅助元件设计等。
三、设计说明书内容:
1、学院统一的课程设计封皮
2、课程设计成绩评定表
3、课程设计任务书
4、目录
5、零件图
6、零件分析
7、工艺路线的制定
8、选择定位基准
9、加工余量确定及工序尺寸计算
10、切削用量与工时定额的确定
11、参考书及资料目录
四、课程设计考核(装订成册)
1、加工工艺过程卡片
2、指定工序加工工序卡片
3、设计说明书
4、答辩
五、时间进度安排(10天)
前言
机械制造工艺学课程设计是在我们学完了大学的全部基础课、技术基础课以及大部分专业课之后进行的。
这是我们在进行毕业设计之前对所学课程的一次深入的综合性的总复习,也是一次理论联系实际的训练,因此,它在我们四年的大学生活中占有重要的地位。
就我个人而言,我希望能通过这次课程设计对自己将来从事的工作进行一次适应性的训练,希望在设计中能锻炼自己分析问题、解决问题的能力,为自己今后所参加的工作打下基础。
在设计过程当中,我通过查阅有关资料和运用所学的专业或有关知识,比如零件图设计、机械制造工艺学、以及所学软件AUTOCAD的运用,设计了零件的工艺、编制了零件的加工程序等。
我利用此次课程设计的机会对以往所有所学知识加以梳理检验,同时又可以在设计当中查找自己所学的不足从而加以弥补,使我对专业知识得到进一步的了解和系统掌握。
我希望能通过这次课程设计对自己未来将从事的工作进行一次适应性训练,从中锻炼自己分析问题、解决问题的能力,由于能力所限,设计尚有许多不足之处,恳请各位老师给予指导。
机械本081—1阀腔的课程设计
1、零件的工艺分析及生产类型确定
1.1、零件的作用
设计中所给定的阀腔是普通油腔中阀腔,它是阀体内安装其他零件的空间以及所需要的通道空间,其作用经查资料。
通过阀腔作为油的分油岔口,将液压油输送到阀体,其中φ100mm的内孔与阀体结合,φ100mm的内孔有φ110mm的凹槽,用于垫密封胶圈,阀腔底部孔φ65mm外圆有宽7.3mm深3.5mm的凹槽与阀座配合,用于垫密封橡胶圈,保证密封性,防止漏油。
1.2、零件的工艺分析
通过零件图的绘制、分析、研究。
该零件的结构要求合理,符合工艺要求。
从零件图上可以看出,阀腔零件形状,属于箱体零件,上、下端面通过粗铣、精铣即可达到所需表面粗糙度。
Φ100H8mm孔、φ65mm孔、φ76mm孔通过铣削可以达到所需技术要求,与φ76mm孔端面有平行度要求。
加工精度较高。
6×
M12—6H的螺纹孔相对φ100mmH8孔的轴线互成60º
分布,其径向设计基准为φ110mmH11孔的轴线,轴向设计基准是φ100mmH8孔外圆的左端面,2×
φ20mm孔分布于φ100mmH8孔两侧,加工要求在阀腔的对称中心线上。
1.3、零件的生产类型
按设计任务书,阀腔年产量为12000件/年,其备品率为5%,废品率为2%,则该零件的年生产纲领由
N=Qn(1+αββ%+в%)(2.1)
可得N=12000×
1×
(1+5%+2%)件/年,
即阀腔年生产量为12840件查表知,阀腔属于大批量生产(查表P72—1表)
2、毛坯尺寸和加工余量确定
2.1、选择毛坯
零件的材料为QT450—10,力学性能бb≤450,硬度:
160—210HBS,基本组织碳素体,能承受冲击、振动。
从提高生产效率和保证加工精度方面考虑,由于零件的生产类型为大批量生产,零件的轮廓不大,选用砂型铸造机器造型,铸造精度2级,铸件应符合JB140—1999《容积式压缩机球墨铸铁技术条件》的规定,能够保证铸件的尺寸要求,出于铸件的主要缺点是力学性能差,阀体在控制液压油时,在阀腔内壁会产生压力,故铸件需回火处理。
2.2、确定毛坯尺寸
根据课程设计谁提出的原始数据及加工工艺,分别确定各加工表面的加工余量,毛坯的初步设计如下:
2.2.1、阀腔的上端面
通过查表,该阀体的上端面的粗糙度要求是Ra6.3µ
m。
通过一次粗铣加工即可达到所需表面粗糙度,下端面的粗糙度要求为Ra1.6µ
m,需要经过粗铣、半精铣、精铣等加工才能满足光洁度的要求,取经济精度为IT8级,通过查表和经验得,阀腔的上端面单边的加工余量为3mm,上端面单边余量为2.5mm。
2.2.2、φ76mm孔的加工
φ76mm孔的表面粗糙度为Ra3.2µ
m,通过查阅相关资料,粗镗、半精镗达到工序要求。
粗镗、半精镗的加工余量之和为3mm。
2.2.3、φ100H8mm孔的加工
该孔的就、粗糙度为Ra1.6µ
m,通过粗镗、半精镗才可以达到加工工序要求,总加工余量之和为5mm。
2.2.4、φ65mm孔的加工
该孔的粗糙度为Ra1.6µ
m,直径较小,通过钻、扩,即可达到加工工序要求。
2.2.5、其他孔
因直径太小,不铸造出孔,故无加工余量。
综上所述,确定毛坯尺寸见表2.1(mm)
项目
上、下面
φ76孔
φ100H8孔
孔φ65
CT
9
加工面基本尺寸
85
76
100
65
铸件尺寸公差
2.2
等级
F
RMA
2.5
毛坯基本尺寸
91.1
69.9
93.9
58.9
其中:
单侧作机械加工:
R=F+RMA+CT/2(2.1)
外圆面作机械加工:
R=F+2RMA+CT/2(2.1)
内腔作机械加工:
R=F-2RMA-CT/2(2.1)
3、选择加工方法,制定工艺路线
3.1、定位基准的选择
3.1.1、粗基准的选择原则
●保证相互位置要求原则
●余量均匀分配原则
●便于工件装夹原则
●粗基准在一个定位方向上只允许使用一次
3.1.2精基准的选择原则
●“基准重合”原则
●“基准统一”原则
●“互为基准”原则
●“自为基准”原则
●便于装夹的原则
3.1.3、各工序基准选择
根据以上原则,以上表面为粗基准加工下表面,以下表面为精基准加工上表面;
加工孔时,以φ100mm孔为粗基准加工φ65mm内孔和φ76mm内孔,以φ65mm孔为精基准加工φ100mm孔;
加工2×
φ20mm孔时,以φ100mm孔为定位基准。
3.2、零件表面加工方法的选择
本零件的加工表面有面、内孔、槽以及小孔等。
材料为QT450—10。
以公差等级和表面粗糙度要求,参考相关资料,其加工方法的选择如下:
3.2.1、阀腔的上端面公差等级为IT11级,表面粗糙度为Ra6.3µ
m,只需粗铣即可达到精度要求。
3.2.2、阀腔的下端面公差等级为IT8级,表面粗糙度为Ra1.6µ
m,需粗铣、精铣。
3.2.3、φ76mm内孔公差等级为IT9级,表面粗糙度为Ra3.2µ
m,需粗镗、精镗。
3.2.4、φ100H8mm内孔公差等级为IT8级,表面粗糙度为Ra1.6µ
3.2.5、φ65mm内孔公差等级为IT8级,表面粗糙度为Ra1.6µ
m,需粗镗、精镗。
3.2.6、2×
φ20mm内孔公差等级为IT13级,表面粗糙度为Ra6.3µ
m,需先钻后粗扩孔。
3.2.7、6×
φ12mm小孔采用复合钻头一次钻出即可。
3.3、制定工艺路线
制定工艺路线的出发点,应当是使零件的几何形状、尺寸精度以及位置精度等技术要求能得到合理的保证,在生产纲领已确定为大批量生产条件下,可以考虑采用万能型机床配以专用夹具,并尽量使工序集中,提高生产率,除此之外,还应当考虑经济效益,以便使生产成本尽量降低。
3.3.1工艺方案一
工序Ⅰ
铸造毛坯
工序Ⅱ
回火处理
工序Ⅲ
粗铣底端面
工序Ⅳ
粗铣上端面
工序Ⅴ
钻、扩4—φ18mm孔锪平φ28mm
工序Ⅵ
粗镗φ76mm、φ100mm、φ110mm、φ65mm、φ85mm孔
工序Ⅶ
精铣底面
工序Ⅷ
车凹槽深3.5mm
工序Ⅸ
精镗φ76mm、φ100mm、φ110mm、φ65mm、φ85mm孔镗宽7.3mm深3.5mm凹槽
工序Ⅹ
钻、扩、绞2×
φ20mm孔
工序Ⅺ
钻孔、攻螺纹10—M12mm
工序Ⅻ
去毛刺
工序ⅰ
终检
3.3.2、工艺方案二
3.3.3、工艺方案的比较和分析
工艺方案一和工艺方案二的区别在于方案一种的粗镗孔放在精镗下端面前,这样可以保证加工精度,φ100mm、φ110mm、φ65mm、φ85mm孔的同轴度,以及与76mm孔内圆的平行度。
由于100mm与65mm孔的加工精度要求较高,110mm凹槽要求相对于B有同轴度要求。
相对于A有平行度要求。
方案二中将钻、扩4—18mm孔,锪平28mm精铣、粗镗之后,与后面的孔系加工放在一起,有利于工序集中,最后通过总结,最终方案如下:
铸造毛坯
粗铣低端面
车深3.5mm凹槽
4、选择加工设备及刀具量具
4.1、选择机床
工序Ⅸ为钻、扩、绞孔,本工序从加工要求和尺寸考虑,可选用2525型钻床进行加工。
4.2、选择刀具
本次阀腔工序设计中,主要加工孔和面,机床的选用比较集中,刀具的选择比较单一,选择如下:
4.2.1、钻孔是选用直柄麻花钻,高速钢钻头,钻盲孔是钻头为莫氏锥柄麻花钻,高速钢钻头。
4.2.2、扩孔是选用锥柄扩孔钻,高速钢钻头。
4.2.3、绞孔时选用所选铰刀为硬质合金锥柄铰刀。
4.3、选择量具
选择测量范围为0——150mm,读书值为0.02mm的三用游标卡尺作为量具
5、加工余量确定及工序尺寸计算
确定孔φ100mmH8的加工余量及工序尺寸
5.1、确定各工序的加工余量
查表得精镗加工余量为1.3mm,则可得粗镗加工余量为
100-93.9-1.3=4.8mm
5.2、计算各工序尺寸
精镗后的尺寸为φ100
,则粗镗后尺寸为φ98.7mm,毛坯尺寸为φ93.9mm
5.3、确定各工序尺寸及公差
查表得精镗后可达IT8,表面粗糙度可达Ra1.6;
精镗后可达IT12,表面粗糙度可达Ra12.5;
毛坯CT9,表面粗糙度不作要求。
由入体原则可知,精镗后的尺寸为φ100
,则粗镗后尺寸为φ98.7
mm,毛坯尺寸为φ93.9
mm。
表5.1φ100H8孔的加工余量及工序尺寸
加工表面
工序余量
工序尺寸及公差
表面粗糙度
粗镗
精镗
φ100H8
4.8
1.3
φ98.7
mm
φ93.9
Ra12.5
Ra1.6
6、确定切削用量及基本时间
工序X为钻、扩、绞2×
φ20mm孔需分三个工步进行加工
6.1、工步一:
钻φ18mm孔的切削用量及基本工时
6.1.1、切削用量
本工序为钻18盲孔,选用钻头为莫氏锥柄麻花钻,高速钢钻头,钻头直径18mm,l=228mm,l1=130mm,加工铸件的бb不小于450MPa,钻头选用Z525型立式钻床。
6.1.1.1、确定钻头钻孔时的进给量
根据《机械制造课程设计指南》表5-127,加工材料为铸铁,硬度为190HBS,查的钻头钻孔时进给量f=0.70-0.86mm/min,现取f=0.8mm/r。
6.1.1.2、选择钻头磨钝标准及耐用度
根据《机械制造课程设计指南》表5-130用高速钢钻头在铸铁上钻18mm孔,钻头后面最大磨损量0.14mm,钻头直径d=18mm,耐用度T=50min。
6.1.1.3、确定切削速度和工作进给量
根据表2-13中公式计算
(5.1)
其中Cv=11.1Zv=0.25Xv=0
=0.4m=0.125
=1
则可计算的Vc=14.98m/min
n=1000×
14.98/п*18=265r/min选择n=195r/min
根据Z265型钻床主轴转速表《机械制造课程设计指南》表5—65
选择n=195r/min
则实际钻削速度v=п*18*195/1000*560=0.184m/s
根据Z525型号钻床进给量《机械制造课程设计指南》表5—65选择,
f=0.8mm/s
6.1.2、基本时间
根据《机械制造课程设计指南》表2—26,高速钢钻头钻削时间为
l=16.5
=
cot
+(1—2)=18/2cot
+1=14.8
=0mm
基本时间:
(5.2)则有 T=16.5+14.8+0/0.8*195=12.06s=13s
6.2、工歩二:
扩φ19.8mm孔的切削用量及基本工时
6.2.1、切削用量
本工序为扩φ19.8mm孔,所选的钻头为锥柄孔扩孔钻,高速钢钻头,钻头直径为19.8mm,l=238mm,
=140mm,加工铸件的бb不小于450MPa,钻头选用Z525型立式钻床。
6.2.1.1、确定钻头钻孔时的进给量
根据《机械制造课程设计指南》表5-127,加工材料为铸铁,硬度为198HBS,查得钻头钻孔进给量是f=0.70—0.86mm/min,现取f=0.8mm/min
6.2.1.2、选择钻头磨钝标准及耐用度
根据《机械制造课程设计指南》表 5-130用高速钢钻头在铸铁上扩φ19.8mm孔,钻头后刀面最大磨损量0.6—0.9mm,钻头直径d=19.8mm,耐用度T=30min,《机械制造课程设计指南》表5-130
6.2.1.3、确定切削速度和工作进给量
由工式5.1得V
=
=24.67mm
n=1000*10.74/п*19.8=172.74r/mm
则实际钻削速度为V=272*п*19.8/1000*60=0.406m/s
根据Z525型号钻床进给量《机械制造课程设计指南》表5—65选择,
f=0.8mm/s
6.2.2、、坯__________________________________________________________________________________________________________________________基本时间
根据《机械制造课程设计指南》表2—26,高速钢钻头钻削时间为L=16.5mm,
=2.56mm,
基本时:
时间:
=
16.5+2.56+0/0.8*392=4s
6.3工步三:
绞孔至φ20mm孔
6.3.1、切削用量
所选铰刀为硬质合金锥柄铰刀,铰刀直径20mm,l=228mm,
=25mm,加工铸件的бb不小于450MPa,钻头选用Z525型立式钻床。
6.3.1.1、确定钻头钻孔时的进给量
根据《机械制造课程设计指南》表5-127,加工材料为铸铁,硬度为190HBS,查得钻头钻孔进给量是f=0.78—0.86mm/min,现取f=0.8mm/min
6.3.1.2、选择钻头磨钝标准及耐用度
根据《机械制造课程设计指南》表5-130,用硬质合金锥柄铰刀φ20mm孔,钻头后刀最大磨损量为1mm,钻头直径d=20mm,耐用度T=45min,《机械制造课程设计指南》表5-130
6.3.1.3、确定切削速度和工作进给量
由公式5.1得V
=12.76mm
n=1000*12.76/п*20=203r/mm
则实际钻削速度为V=195*п*20/1000*60=0.2m/s
根据Z525型号钻床进给量《机械制造课程设计指南》表5—65选f=0.8mm/s
6.3.2、基本时间
根据《机械制造课程设计指南》表2—26,高速钢钻头钻削时间L=16.5mm,
=1.17mm,
16.5+1.17+0/0.8*195=7s
7、专用夹具设计
根据实际需要,夹具体为铸造夹具体,加工工件时,夹具体与钻模板装配在一起
7.1、定位误差
7.1.1、基准不重合误差
由于工序基准与定位基准重合,所以不存在基准不重合误差
7.1.2、基准位移误差
定位销尺寸为Φ
定位孔尺寸为φ
则△
=X
=(ES1-EI2)=(+0.03-(-0.029))=0.059mm
7.2对刀误差
钻头与钻套之间的间隙引起的误差,钻套导向孔尺寸为Φ
钻头尺寸为Φ
Δ
=0.034-(-0.033)=0.067mm
7.3夹具的安装误差
夹具安装基面是平面,因而无安装误差,Δ
=0
7.4夹具误差
因夹具上定位元件,对刀及导向元件及安装基面三者间(包括导向元件与导向元件之间)的位置不精确而造成的加工误差。
夹具误差大小取决于夹具零件的加工精度和夹具装配时的调整与修配精度。
导向孔对安装基面的垂直度误差Δ
=0.03mm。
7.5加工方法误差
因机床精度,刀具精度,刀具与机床位置精度,工艺系统受力变形,及受热变形等因素造成的加工误差,因该项误差影响因素多,不便计算,取经验值,Δ
=δ
/3=0.2/3
综上所述,ΣΔ=
=0.115<
δ
课程设计总结
两周的课程设计结束了,在这次的课程设计中不仅检验了我所学习的知识,也培养了我如何去把握一件事情,如何去做一件事情,又如何完成一件事情。
在设计过程中,与同学分工设计,和同学们相互探讨,相互学习,相互监督。
学会了合作,学会了运筹帷幄,学会了宽容,学会了理解,也学会了做人与处世。
课程设计是我们专业课程知识综合应用的实践训练,着是我们迈向社会,从事职业工作前一个必不少的过程.”千里之行始于足下”,通过这次课程设计,我深深体会到这句千古名言的真正含义.我今天认真的进行课程设计,学会脚踏实地迈开这一步,就是为明天能稳健地在社会大潮中奔跑打下坚实的基础.
通过这次机械制造课程设计,本人在多方面都有所提高。
通过这次机械制造课程设计,综合运用本专业所学课程的理论和生产实际知识进行一次工艺设计工作的实际训练从而培养和提高学生独立工作能力,巩固与扩充了机械制造等课程所学的内容,掌握了设计的方法和步骤,懂得了怎样分析零件的工艺性,怎样确定工艺方案,了解了机械制造课程的基本结构,提高了计算能力,绘图能力,熟悉了规范和标准,同时各科相关的课程都有了全面的复习,独立思考的能力也有了提高。
在这次设计过程中,体现出自己单独设计机械制造工艺的能力以及综合运用知识的能力,体会了学以致用、突出自己劳动成果的喜悦心情,从中发现自己平时学习的不足和薄弱环节,从而加以弥补。
在此感谢我们的王天煜和吕海鸥老师.,老师严谨细致、一丝不苟的作风一直是我工作、学习中的榜样;
老师循循善诱的教导和不拘一格的思路给予我无尽的启迪;
这次机械制造课程设计的每个实验细节和每个数据,都离不开老师您的细心指导。
而您开朗的个性和宽容的态度,帮助我能够很顺利的完成了这次课程设计。
同时感谢对我帮助过的同学们,谢谢你们对我的帮助和支持,让我感受到同学的友谊。
由于本人的设计能力有限,在设计过程中难免出现错误,恳请老师们多多指教,我十分乐意接受你们的批评与指正,本人将万分感谢。
参考文献
1、崇凯.机械制造技术基础课程设计指南.