一种小型压力机的设计Word下载.docx
《一种小型压力机的设计Word下载.docx》由会员分享,可在线阅读,更多相关《一种小型压力机的设计Word下载.docx(14页珍藏版)》请在冰豆网上搜索。
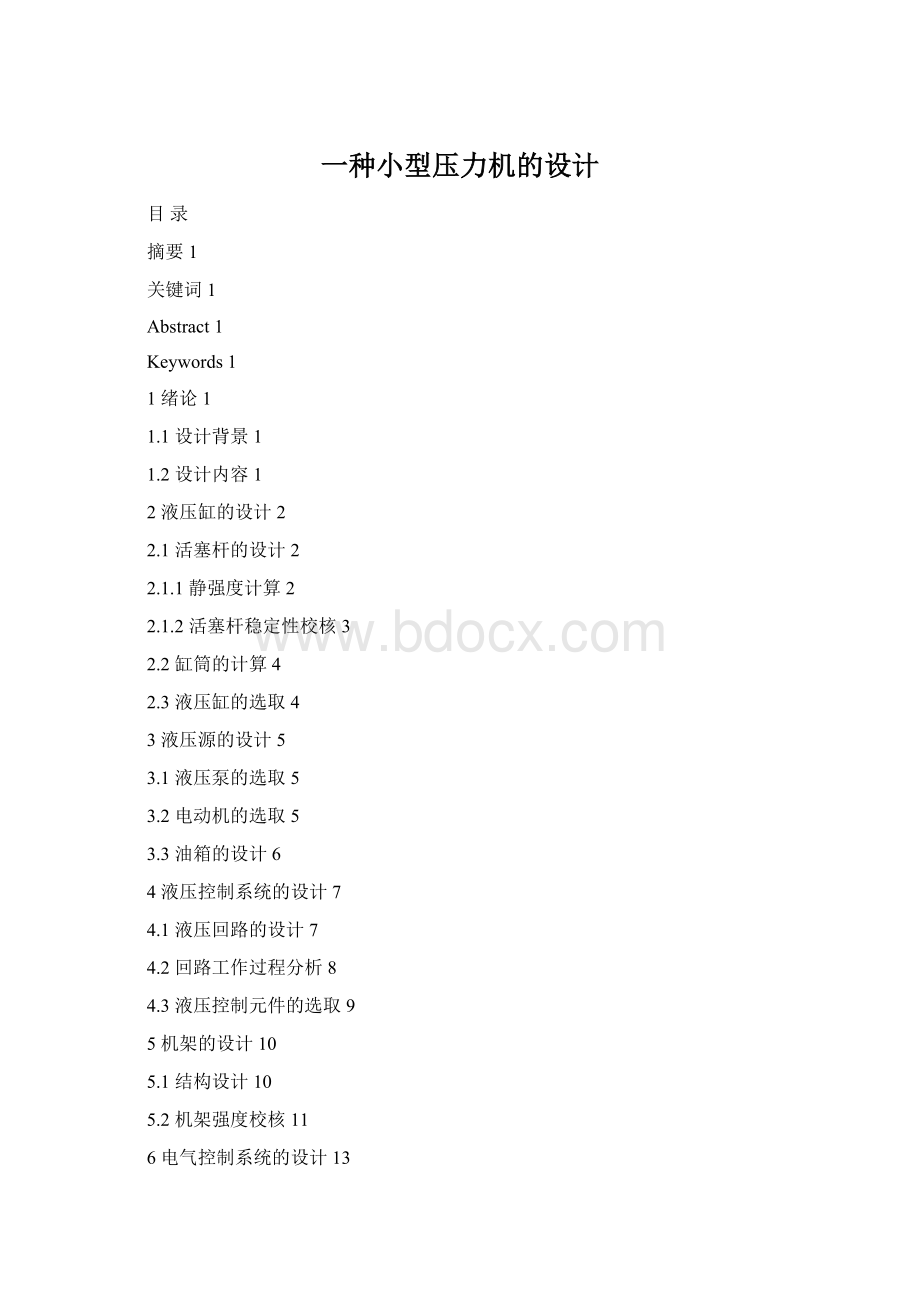
快进时液压缸为差动式连接,工进时液压缸有杆腔存在背压,工作稳定。
机架采用单臂式结构。
电气控制系统具有点动、连动功能,控制方式为行程控制,控制准确。
用户使用方便、操作简单。
该机型在工业生产中应用较广,体积小巧,结构简单,具有一定的市场前景。
关键词:
液压;
压力机;
调速;
循环动作
Designofaminipunchingmachine
StudentmajoringinmechatronicsTianYu
TourWangDongfeng
Abstract:
Punchingmachineisakindofsetwhichreachpressworkbyexportforcethroughthepressurehead.Theessaydescribeamicropunchingmachinedesignprocessbyfiveaspect,hydrauliccylinder,hydraulicsource,hydrauliccontrolparts,frame,electricalcontrolsystem.Itusesthedoubleactingsinglerodhydrauliccylinder,independenthydraulicsource.Thehydrauliccylinderisindifferentialmotioncirclewhenthepressureheadisfastfeedandtherodchamberhasanextrapressurewhilethepressureheadisinworkingfeed,thismadeitworksteadily.Theframeissingle-armstyle.Theelectricalcontrolsystemhasthecrawlandlinkagefunctionandthecontrolmodeisstrokecontrol.Itisconvenientforworkstouseandeasytocontrol,it’sveryaccurate.Thepunchingmachinehasawideruseinindustrialproduction,andits’volumeiseverysmall,fractureissimple,whichhasabettermarketforward.
Keywords:
hydraulic;
punchingmachine;
adjustspeed;
circlemotion
1绪论
1.1设计背景
在工业生产中使用着各种各样的压力机,有曲柄压力机、油压压力机、水压机、摩擦式压力机、空气锤、蒸汽锤。
市场上压力机的型号较多,已成为一种通用机械,基本上能满足生产的需要。
但有时仍需工厂自行设计压力机以满足大批生产的需求。
常见压力机的工作过程如下:
将工件置于工作台上(一般需要预先安装夹具);
压头快速下降(快进);
压头碰到工件后转为低速下降(工进);
低速下降至压力加工完成系统压力升高到最大值;
压头快速上升(快退);
其工作程中要求能随时停止进给,以确保安全。
液压系统应有过压保护,以防损坏机床。
1.2设计内容
根据现有的生产状况拟定该油压压力机的主要技术参数为:
额定压力30kN,压头行程150mm,压头工进下降速度50mm/s。
本设计定位为小型油压压力机,用于普通压力加工,如装配滚动轴承、销轴、压扁套管。
为扩大其适用范围,便于细长工件的压力加工,机架结构采用单臂式。
采用标准型号的液压缸可以避免生产制造对精密内孔加工机床的需求,有利于组织生产。
为减少液压油温升引起的机床热变形,采用液压源与机架分离的设计方案,便于用户充分利用厂区内闲置的液压泵站,减少购机成本。
液压控制系统采用电磁换向阀,减少工人手动操作的劳动强度,同时也便于实现自动控制。
电气控制系统要求具有点动与循环动作功能,工人可以根据工件的特点灵活选用压力机的动作方式,既方便又省力。
为了保证运动的准确性,电气控制系统的控制方式应选为行程控制。
该压力机由液压缸、液压源、液压控制系统、机架、电气系统五部分组成,下面依次对各个系统进行分析计算。
2液压缸的设计
由图2-1压力机工作简图可知,液压缸应选用双作用单杆活塞液压缸。
2.1活塞杆的设计
从工作简图可以看出:
油液压力通过活塞杆作用于工件上,当忽略缸壁摩擦时油液对活塞的压力与工件对塞杆的反作用力平衡。
活塞杆所受反作用力的大小为压力机的额定压力F=30000N。
活塞杆两端都有螺纹以便安装压头和活塞,直径尺寸变化小。
用棒料作为毛坯加工余量小。
鉴于活塞杆受力较大,选用45钢,最终热处理为调质。
2.1.1静强度计算
查设计手册知:
45钢的屈服极限σS=353MPa。
取活塞杆安全系数n=2.活塞杆的许用应力为:
近似取[]=170MPa
活塞杆的最小横截面积为:
活塞杆最小直径为:
该液压缸工作时用无杆腔作为工作腔,一般的齿轮式液压泵输出压力在16MPa左右。
取P=12MPa,活塞的最小横截面积为:
活塞最小直径为:
为保证压力机的通用性,活塞的行程选为150mm。
活塞杆的最小导向长度为:
2.1.2活塞杆稳定性校核
由于活塞杆工作时受压,其破坏形式可能为挠性弯曲,需要对活塞杆进行稳定性校核。
当活塞杆完全从缸筒中伸出且正处于额定工作压力时,活塞杆柔度最大,此时是最危险的工况。
对于圆截面的活塞杆,其惯性矩为:
惯性半径为:
根据活塞杆的工作情况构建力学模型,考虑到活塞杆端部对工件施加压力时可能由于工件的随机移动而发生横向位移,活塞杆下端应简化为自由端。
上端应简化为固定端。
力学模型如图2-2所示。
查设计手册得:
柔度系数μ=2,活塞杆的柔度:
对于45钢,E=206GPa。
则
因为
所以在此工况下,活塞杆属于中柔度杆。
其许用压力为:
活塞杆稳定性足够。
2.2缸筒的计算
缸筒毛坯采用灰铸铁铸造,然后机械加工、表面淬火、磨内孔。
材料为HT150。
查手册得灰铸铁HT150的强度极限=150MPa。
取安全系数n=2,材料的许用应力为:
缸筒内部承受压强,筒壁处于二向应力状态,可将其视为薄壁圆筒。
最大正应力为:
则最小壁厚为:
由数据可知:
内压不是限制最小壁厚的条件。
根据铸造技术规范,铸铁件壁厚至少为8~10mm时才不会出现浇不透、冷隔、裂纹等缺陷。
2.3液压缸的选取
为了方便往压力机机架上安装液压缸,应选用头部法兰式液压缸。
且杆径d>
15mm,活塞直径D>
55mm。
对照产品目录,选取UYTF1063X150-12型双作用单杆活塞液压缸。
该产品属于冶金用液压缸,常规工作温度为(-35~+100℃),安装形式为头部法兰式。
活塞杆端连接方式为外螺纹,缸径φ63mm,杆径φ45mm,行程150mm,额定压力12MPa。
工作介质为矿物油。
头部法兰固定孔为8×
φ13,孔中心轨迹φ155,法兰盘外径φ180mm。
收缩状态活塞杆伸出长度88mm,缸筒最大外径φ126mm。
活塞杆螺纹M30×
2,高压油管接口螺纹M27×
1.5。
实际选择的液压缸活塞杆直径为φ45mm,远大于计算值φ15mm,这样可以大大提高系统的刚度。
无杆腔活塞面积:
有杆腔活塞面积:
压力机工进时,无杆腔作为工作腔。
忽略有杆腔的回油背压,输入液压油的额定压力为:
3液压源的设计
液压源由液压泵、电动机、油箱及附件组成。
电动机带动液压泵转动,使液压泵在吸油管处形成真空度,液压油在大气压力的作用下进入液压泵吸油腔。
在两齿轮的啮合处,液压油受挤压而从出油口排出。
油箱用来容纳液压油。
3.1液压泵的选取
根据压力机的使用特点,初选压头工进下降速度为50mm/s,则工进时无杆腔的最大进油流量为:
综合考虑管路、阀体的压力损失和缝隙油液泄漏。
初步拟定液压泵的额定压力为10MPa,额定流量10L/min。
由于该液压源属于中低压类型,应选用外啮合齿轮式液压泵。
齿轮泵是一种最常用的液压泵,其结构简单、制造方便、价格低廉、体积小、重量轻、自吸特性好、对油液污染不敏感、工作可靠。
其压力脉动对压力机的正常工作影响不大,可以在小型压力机上使用。
对照产品目录,选取CB-FC10-1S-85-L型外啮合齿轮泵。
该型号齿轮泵采用铝合金压铸泵体,轴向密封采用浮动式压力平衡侧板,公称排量10mL/r。
轴连接形式为平键,矩形法兰安装,旋转方向为右旋。
额定压力16MPa,最高压力20MPa。
额定转速2000r/min,最低600r/min。
容积效率90%,总效率81%。
轴向全长168mm,输入轴φ20h7,平键6×
6×
28,固定孔中心距130mm,进油口螺纹M33×
2,出油口螺纹M27×
2。
要使液压泵的输出流量达到10L/min,转速为:
液压泵输出功率为:
液压泵输入功率为:
3.2电动机的选取
此液压源的电动机空载启动、连续运行,但负载为间歇式。
工作冲击较小,不需要调速、制动和反转。
对转速恒定性要求不高,通风散热良好。
三相鼠笼式异步电动机价格低、性能好、维修方便,电气控制也比较简单,工厂中都接有三相交流电源,适合于液压泵站使用。
对照产品目录,选取Y2-112M-6型三相异步电动机。
该机型额定功率2.2kW,额定电流5.6A,额定转速940r/min,效率79%,功率因数0.76,最大转矩2.1TN,堵转电流6.5IN,空载噪声65dB,转子转动惯量0.0138kg?
m2,质量45kg,机座中心高112mm,电动机轴向全长400mm,外壳外径φ240mm,机座固定螺孔横向中心距190mm,纵向140mm,机座横向长230mm,纵向长180mm,轴伸长度60mm,输出轴端面距机座近轴端面70mm,伸出轴直径φ28mm,键槽宽8mm,槽深3mm。
电动机的额定转矩为:
电动机输出的最大转矩为:
由于该液压泵的理论转速为1000r/min,与电动机的额定转速相差不大,可直接采用联轴器作为电动机与液压泵之间的传动部件。
这种设计具有体积小、效率高、安装方便的优点,成本较低。
联轴器一端轴孔为φ28mm,键槽宽8mm,与电动机输出轴相连接。
另一端轴孔为φ20mm,键槽宽6mm,与液压泵相连接。
3.3油箱的设计
压力机属于固定设备,液压源位于设备周围,车间内温度较高,冷却效果较差。
查机械设计手册知:
锻压设备的液压系统油箱容积是液压泵流量的6~12倍。
取中间值9,则油箱容积为:
V=9×
10L=90L
为使液压泵与电动机能安装在油箱上端面上,油箱上端面的长度至少应为电动机与液压泵轴向长度之和:
L=400mm+168mm=568mm,取为600mm。
油箱上端面宽度至少应大于电动机外壳直径φ240mm,取为300mm。
由此解出油箱理论高度为:
为保证油箱加满油后仍能留有一部分空间,取h=600mm。
油箱由钢板焊接而成,上端面需设置安装电动机及液压泵的机座。
油箱内部应设置隔板,防止油液严重起泡。
加油口应安装空气过滤器,油箱底部应增加放油螺栓。
为防止锈蚀,表面应喷涂油漆。
根据液压泵进油接口螺纹型号,选择型号为GB/T3738L28的卡套式可调向端弯通管接头连接液压泵进油口和进油管,安装后保证弯头出口垂直于油箱水平面。
从产品目录中选取外径为φ28mm的钢管作为进油管,公称通径为φ20mm。
进油管口部应切成45°
斜角以增加通流面积。
吸油管横截面积:
吸油管内油液流速:
符合要求。
4液压控制系统的设计
通过对压力机工作过程的分析,要求液压回路能实现调压、调速、换向、速度换接。
4.1液压回路的设计
常用的溢流调压回路、回油路节流调速回路、三位四通换向阀换向回路如图4-1.
常见的两种快进、工进速度换接回路如图4-2所示。
将各基本回路合并组成的液压回路如图4-1所示
4.2回路工作过程分析
准备:
液压泵电动机通电后,液压泵输出油液从三位四通电磁换向阀P口流入,从T口流出,进入过滤器上口,经过滤器过滤后进入油箱。
此时液压泵卸荷,输出压力极低。
快进:
三位四通电磁换向阀处于左位工作状态,液压油从三位四通电磁换向阀P口进入,从A口流出,沿管道进入液压缸无杆腔,推动活塞向下运动。
有杆腔油液受压从B口流出,沿管道进入二位三通电磁换向阀P口,该换向阀此时未动作。
油液从A口流出,沿管道进入三位四通电磁换向阀A口。
液压缸此时为差动连接,运动速度较快,液压泵输出压力较低。
工进:
活塞杆快速下降,碰到工件后,阻力增大,系统油液压力开始升高。
达到压力继电器BP的整定值时,二位三通电磁换向阀动作,转为右位工作状态。
此时三位四通电磁换向阀仍处于左位工作状态。
从液压泵输出的液压油一部分流入三位四通电磁换向阀P口,从A口流出,沿管道进入液压缸无杆腔推动活塞向下运动。
液压缸有杆腔油液从B口流出,沿管道进入节流阀,从节流阀流出后,沿管道进入三位四通电磁换向阀B口,从T口流出后沿管道进入过滤器,再进入油箱。
液压泵输出油液的另一部分通过溢流阀溢流进入油箱。
此时液压泵输出压力即为溢流阀整定值10MPa。
由于压力机一般不会工作在额定负载下,活塞上面受油液的压力不能与工件对活塞杆的反作用力相平衡。
有杆腔的油液必然存在一定的压力,其数值因负载不同而不同(空载时最大,为20MPa,额定载荷时最小,理论上为0MPa)。
当活塞杆工进到达加工结束位位置后,遇到硬限位,停止下降。
节流阀内油液停止流动,活塞上面受油液压力与工件对活塞杆的反作用力相平衡,有杆腔压力降为零。
此时压力继电器BP动作,三位四通电磁换向阀恢复中位,工进停止。
快退:
三位四通电磁换向阀处于右位工作状态,二位三通电磁换向阀处于右位工作状态。
液压泵输出的油液从三位四通电磁换向阀P口流入,从B口流出,沿管道进入单向阀,从单向阀流出后,再沿管道进入二位三通电磁换向阀B口,从P口流出,沿管道进入液压缸有杆腔,推动活塞向上运动。
有杆腔油液从A口流出,沿管道进入三位四通电磁换向阀A口,再从T口流出,沿管道进入过滤器、油箱。
4.3液压控制元件的选取
压力机对压力调整的快速性和准确性要求不高,选用直动式溢流阀即可满足要求。
对照产品目录,选取DBDS6G10/2512型直动式溢流阀。
该溢流阀的连接板长80mm,宽60mm。
油路接口螺纹为M14×
由于液压缸无杆腔活塞面积是有杆腔活塞面积的两倍,轻载工进时回油压力远大于进油压力(回油压力约为进油压力的2倍)。
节流阀的额定工作压力选为20MPa,流量为5L/min即可。
需要的单向阀额定流量10L/min,额定压力为20MPa。
对照产品目录,选取MK6G1.2/2型单向节流阀。
该阀是节流阀与单向阀的组合阀,使用组合阀可以减小液压控制系统的体积、降低成本。
该单向节流阀全长65mm,外径φ34mm,接口螺纹为M14×
电磁换向阀的额定压力为20MPa,额定流量为10L/min。
压力、流量都较小,属于小型换向阀。
选用一般的电磁换向阀即可满足要求,为了简化电气控制系统的设计,采用交流电磁铁。
对照产品目录,液压控制回路中的三位四通电磁换向阀应选择4WE6G50/AW220-50B12型三位四通电磁换向阀。
该换向阀换向过渡阶段P、A、B口通过节流孔连接,可减少换向时系统压力骤增引起的振动和噪声。
其外形尺寸为:
231mm×
44mm×
84mm,安装板接口螺纹M44×
1.5,电磁铁额定电压AC220V,吸合功率46VA,接通功率130VA。
液压控制回路中的二位三通电磁换向阀应选择4WE6FB50/AW220-50B12型二位四通电磁换向阀。
该换向阀过渡阶段P、A、B口通过节流孔连接。
可有效避免过渡阶段全截止阀换向引起系统压力突然上升到溢流阀整定值所引起的液压冲击和振动噪声。
安装时需要用螺栓将T口堵住,将其改装为二位三通换向阀。
其安装底板尺寸同三位四通换向阀。
以上两换向阀推荐使用20μm过滤器,以提高换向阀的使用寿命和性能。
根据液压泵的额定流量10L/min,对照产品目录,选取YLH-10×
20型箱上回油过滤器。
其压力损失ΔP<
0.01MPa,可通过外壳上的法兰盘直接安装在油箱上端面上,维护保养十分方便。
压力机工作时振动较小,液压缸无杆腔进油压力为10MPa。
对照产品目录,选取Y-60-ZT型压力表。
测量范围0~16MPa,油路接口螺纹为M14×
根据系统回油路油液压力,选取HED4×
A15/10Z14L229S型柱塞式压力继电器。
该压力继电器外形尺寸120mm×
40mm×
93mm,油管接口螺纹为M14×
为使压力机结构紧凑,液压控制元件应安装在机架内部。
而液压源独立于机架之外单独放置,液压源与三位四通电磁换向阀之间的连接属于活动连接。
应根据油路接口螺纹型号选用软管,进油路用高压胶管,回油路用低压胶管。
为了方便施工和降低生产成本,其余管路的连接采用卡套式接头,管路采用铜管。
5机架的设计
压力机在生产中用量较大,生产厂家批量生产。
机架一般为箱体类型,应采用铸造毛坯,然后对重要表面进行机械加工,非工作表面去毛刺后喷涂油漆。
机架底部应预留各种液压控制元件、电器、管路安装孔。
工作台下方应设加强肋以增加强度。
因小型压力机机架受力较小,工作时冲击较小,选择灰口铸铁HT100作为铸造材料十分经济。
根据铸造工艺规范,初选壁厚δ=10mm。
5.1结构设计
根据液压缸缸筒直径、活塞杆伸出长度、压力机工作行程要求,拟定机架各处的几何尺寸,如图5-1所示。
5.2机架强度校核
分析压力机工作时的受力形式,构建如图5-2的力学模型。
静载荷F1、F2分别作用在弯曲构件ABCD的D、A两点上。
以B为原点建立空间直角坐标系,框架各段的受力分析如下:
AB段发生弯曲变形。
FS(x)=F1=30000N
M(x)=FSx-F1lCD=30000x-8250(N?
m)
BC段发生拉弯组合变形。
FN=F1=30000N
FS(y)=0
M(y)=FNlBA=30000N×
0.35m=8250N?
m
CD段发生弯曲变形。
FS(x)=﹣F2=﹣30000N
M(x)=FSx+F2LAB=﹣30000x+8250(N?
剪力图、弯矩图、轴力图如图5-3所示。
对于细长梁,弯曲切应力一般不作为强度校核标准。
将弯曲正应力与拉伸正应力相叠加。
BC段右侧面地方弯曲正应力与拉伸正应力同号,数值最大,为危险截面。
截面形状如图5-4所示。
截面的惯性矩为:
最大弯曲正应力为:
横截面面积为:
立柱右侧面的拉伸正应力为:
则立柱右侧面的最大正应力为:
立柱安全系数:
满足要求。
机架铸件铸完后,应露天放置自然时效或进行人工时效以消除铸造内应力。
工作台上应加工出T形槽,以便于固定夹具。
并且应进行表面淬火,以减少使用过程中的磨损。
安装液压缸的法兰盘平面与工作台的平行度应在许可的范围内,以保证活塞杆与工作台面的垂直度。
6电气控制系统的设计
6.1电气原理设计
根据液压系统原理图,做出电磁阀电磁铁的动作顺序表。
表6-1电磁铁动作顺序表
MB1MB2MB3发信元件
快进+--下降按钮或循环启动按钮
工进+-+压力继电器BP
快退-++上升按钮或压力继电器BP
电磁阀、压力继电器的动作时序如图6-1.
图6-1时序图
该压力机的电气控制系统属于小型单机电气控制系统,从电磁铁的动作顺序图可以看出:
该系统只有三种工作状态和三种过渡状态,所有输入和输出都是数字量。
需要控制的电器有:
液压泵电动机M、电磁铁MB1、MB2、MB3,共四个。
电器的开关频率不高,控制原理较简单。
采用传统的继电接触系统可显著降低成本,且系统适合于一般技术等级的维修电工进行检修,给用户使用带来极大便利。
电气原理图如图6-2.
各按钮的功能如下:
SF1:
液压泵电动机启动
SF2:
液压泵电动机停止
SF3:
点动下降(快进、工进)
SF4:
点动上升(快退)
SF5:
循环启动
SF6:
紧急停车
6.2电气系统工作过程分析
合上低压断路器QA0,电源指示灯PG亮,表示电源接通。
按下液压泵电动机启动按钮SF1,交流接触器QA1线圈得电。
QA1主触点闭合,电动机开始转动。
QA1常开触点闭合形成自锁。
松手后,QA1继续吸合,电动机常动。
点动下降:
当压头未触及工件时,按下点动下降按钮SF3,电磁铁MB1得电。
压头快速下降,即快进。
松手后,MB1失电,压头下降停止。
压头触及工件后,继续按SF3,回油路油液压力升高。
达到压力继电器BP的整定压力时,BP动作,常开触点闭合。
电磁铁MB3得电,压头的运动转为工进,慢速下降。
松手后MB1、MB3失电,工进停止。
加工完成后,如继续按SF3。
系统以额定压力保压。
点动上升:
不论压头处于何种位置,按下点动上升按钮SF4,电磁铁MB2、中间继电器KF1得电。
KF1常开触点闭合,电磁阀MB3、中间继电器KF3得电,压头快速上升。
松手后,MB2、KF1、MB3、KF3失电,压头停止上升。
连续运动:
当压头未触及工件时,按下循环启动按钮SF5。
中间继电器KF2得电,常开触点闭合,KF2自锁,电磁铁MB1得电,压头快速下降。
压头碰到工件后,回路油液压力升高,压力继电器BP动作,常开触点闭合,电磁铁MB3、中间继电器KF3得电,压头转为工进。
KF3常开触点闭合,中间继电器KF4得电,KF4常开触点闭合,KF4自锁当压力加工完成时,压头不能继续向下下降,液压缸无杆腔油液压力降到压力继电器BP的整定值以下。
BP动作,常闭触点闭合,中间继电器KF5得电。
KF5常闭触点断开,使KF2失电,KF2常开触点断开,使MB1、MB3、KF3失电,压头工进停止。
KF5常开触点闭合,使KF5自锁,MB2、KF1得电。
KF1常开触点闭合,使MB3、KF3得电,压头快速上升。
当上升到上止点后,液压缸活塞停止运动,致使有杆腔内压力升高。
超过压力及电器BP的整定值时,BP动作,常开触点闭合。
中间继电器KF