齿轮轴热处理Word文档下载推荐.docx
《齿轮轴热处理Word文档下载推荐.docx》由会员分享,可在线阅读,更多相关《齿轮轴热处理Word文档下载推荐.docx(25页珍藏版)》请在冰豆网上搜索。
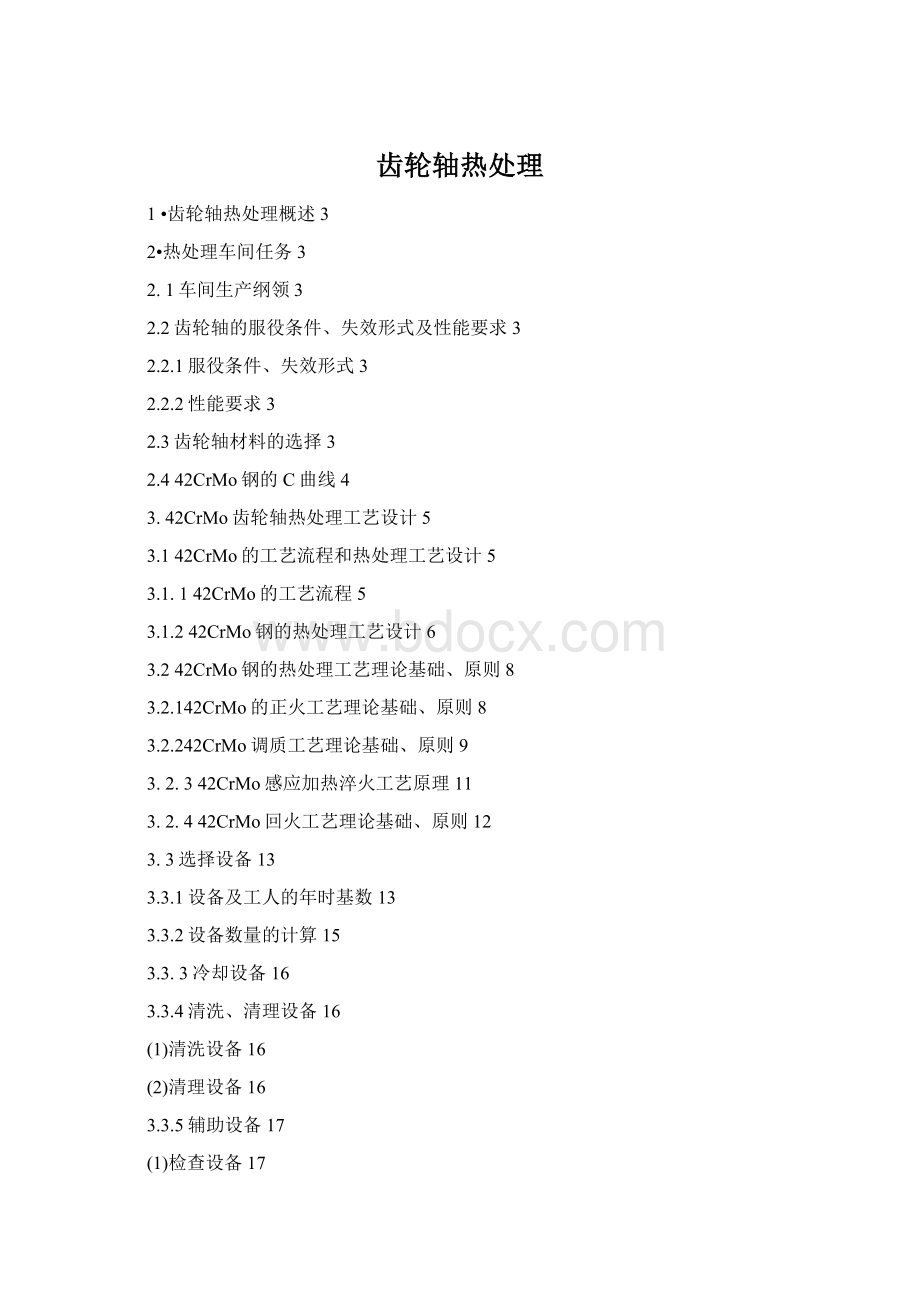
6.3蒸汽22
6.4生产用水22
7•工作人员22
8.热处理的生产安全与环境保护23
8.1生产安全23
8.2环境保护23
9.结论24
参考文献错误!
未定义书签。
1•齿轮轴热处理概述
轧机是现代工业生产的重要机械,而轧机的齿轮轴是轧机中重要的传动部分,主要承受交变载荷,冲击载荷,剪切应力和接触应力大。
轴部易产生裂纹,齿部易磨损。
因此对齿轮轴的心部要求有一定的强度和韧性,有较高的疲劳极限和抗多次冲击能力。
表面还应具有一定的硬度和耐磨性。
为了满足这些性能要求,材料要有很好的力学性能,常釆用42CrM。
钢经正火,调质,感应加热淬火加低温回火己达到所要求的性能。
42CrMo为中碳合金钢,预备热处理是正火,主要目的是为了获得一定的硬度,便于钢坯的切削加工,为调质做好组织准备。
调质的目的是为了提高轧机齿轮轴的综合力学性能。
中频感应加热表面淬火是使零件表面得到高的硬度和耐磨性,而心部仍保持一定的强度及较高的塑性、韧性。
通过对42CrM。
钢热处理工艺的分析,明确在执行热处理工艺过程中所需要注意的问题。
能够正确确定加热温度、时间,保温时间,冷却方式,其目的就是通过正确的热处理工艺,达到所需要的性能,保证质量。
根据齿轮轴的工作条件,失效形式及性能要求,大部分材料选择为合金中碳钢,在设计正火-调质-中频感应加热淬火加低温回火热处理工艺中,本设计借鉴了《热处理工程师手册》,《热处理实用数据速查手册》,《钢的热处理》,《机床零件用钢》,《金属工艺学》等。
根据工艺设计的理论基础设定了完整的热处理工艺流程,使热处理的42CrMo中碳合金结构钢表面除具有高硬度,高耐磨性外,高的疲劳强度,在高温下的强度,还要使心部具有高的的强度和韧性,从而满足齿轮轴的质量要求。
2.热处理车间任务
本设计的任务是设计一间主要生产轧机齿轮轴的热处理车间。
2.1车间生产纲领
所设计的热处理车间的年产量为1200吨的轧机齿轮轴,属于中等批量的生产任务。
2・2齿轮轴的服役条件、失效形式及性能要求
2.2.1服役条件、失效形式
齿轮轴在转动时主要承受剪切应力,交变弯曲应力,传递动载荷等工作,受到多次冲击应力。
在工作过程中,由于不同的应力作用,导致不同的失效形式,主要有疲劳磨损,裂纹,表面点蚀,弯曲疲劳折断,冲击折断等。
2.2.2性能要求
1.具有高的疲劳极限;
2.具有高的抗弯强度;
3.具有较高的韧性;
4.具有高的耐磨性;
5.具有抗多次冲击能力;
6.具有高温下的高强度;
7.具有一定的精度。
2.3齿轮轴材料的选择
齿轮轴材料的选用根据齿轮轴的工作条件,要求以及性能來确定。
主要是工作时载荷的大小,转速的高低及齿轮的精度要求來确定的。
载荷大小主要是指齿轮传递转矩的大小,通常以齿面上单位压应力作为衡量标志。
一般分为:
轻载荷、中载荷、重载荷和超重载荷。
根据要求42Cr\l。
钢的性能符合度非常好,其经过正火,调质,感应加热淬火加低温回火后表面硬度可达HRC50的高硬度,表面耐磨性好,心部硬度可达HRC35"
45o42CrMo钢属于超高强钢,具有高强度和高韧性,淬透性好,调质后有较高的疲劳极限和抗多次冲击的能力。
淬火时变形小,高温时具有高的蠕变强度和持久强度,且无明显的回火脆性。
42CrMo钢中含有的合金元素Cr,Moo其中銘能增加钢的淬透性并有二次硬化作用。
可提高高碳钢的硬度和耐磨性而不使钢变脆;
含量超过12%时。
使钢有良好的高温抗氧化性和耐氧化性介质腐蚀的作用。
还增加钢的热强性,洛为不锈耐酸钢及耐热钢的主要合金元素。
辂在调质结构钢中的主要作用是提高淬透性。
使钢经淬火回火后具有较好的综合力学性能,在渗碳钢中还可以形成含辂的碳化物,从而提高材料表面的耐磨性。
而钳在钢中能提高淬透性和热强性。
防止回火脆性,增加剩磁和矫顽力以及在某些介质中的抗蚀性,在调质钢中,钳能使较大断面的零件淬深、淬透,提高钢的抗回火性或回火稳定性,使零件可以在较高温度下回火,从而更有效地消除(或降低)残余应力,提高塑性。
所以在生产中常常选用42CrMo作为轧机齿轮轴的材料。
其综合力学性能优良符合质量要求。
2.442CrMo钢的C曲线
通过查找《热处理手册》获得42CrMo钢的C曲线如下图所示,成分如表1。
图1.42CrMo钢连续转变C曲线
表142CrMo钢的化学成分
化学成分(质量分数)%
C
Si
Mn
P
S
Cr
Ni
Cu
Mo
42C1MO
0.42
0.27
0.65
0.005
1.10
0.20
3.42CrMo齿轮轴热处理工艺设计
3.142CrMo的工艺流程和热处理工艺设计
3.1.142CrMo的工艺流程
(D.加工路线
备料一锻造一正火一粗、半精加工一制齿一调质一中频感应加热淬火、低温回火一精机加工磨齿(6级以上精度齿轴)。
(2).锻造工艺设计
锻造齿轮轴的毛坯经过锻造后获得基本的形状。
锻造是利用锻压机械对金属坯料施加压力,使其产生塑性变形,己获得具有一定机械性能、一定形状和尺寸的锻件的加工方法。
齿轮轴的锻造工艺与齿轮相差不大,用棒料徹经切削加工制成的齿轴,其纤维组织弯曲呈放射状,所有齿部的正应力都平行于纤维组织的方向,力学性能得到很大的提高。
查阅《热处理工艺规范数据手册》可以找出42C1MO钢的锻造工艺的加热温度、始锻温度冷却方式,本设计具体的锻造工艺参数如表2所示。
表242CrMo钢的热加锻造工艺规范
项目
Aci
AC3
加热温度
始锻温度
终锻温度
钢坯
730°
800°
1150〜1200°
1130〜1180°
>
850°
经锻造后其最大直径约为80mm,采用缓冷。
图242CrMo齿轮轴示意图
3.1.242CrMo钢的热处理工艺设计
(D.预备热处理工序一正火
一般均安排在毛坯生产之后,切削加工之前,或粗加工之后,半精加工之前。
正火的目的是为了细化晶粒、改善组织,提高切削加工性能,为淬火和最终热处理做好准备。
正火工艺曲线如图3所示。
温度厂C
时间T
图342CrMo钢热处理正火工艺曲线
(2).42CiMo钢的调质处理
淬火后高温回火的方法为调质。
调质可以使钢的性能,材质得到很大程度的调整,其强度、塑性和韧性都较好,具有良好的综合机械性能。
调质处理后得到回火索氏体,Cr能增加钢的淬透性,提高钢的强度和回火稳定性,具有优良的机械性能。
截面尺寸大或重要的调质工件,应釆用42CrMo钢工件淬火后油冷,42CrMo钢的淬透性较好,在油中冷却能淬硬,而且工件的变形、开裂倾向小。
所以42CrMo钢采用840°
C淬油,再480度回火处理。
硬度可达HRC35-45。
图4为调质工艺曲线。
温度/°
c
图442CrMo调质工艺曲线图
(3).最终热处理工序一感应加热表面淬火、低温回火
零件经调质后具有良好的综合力学性能,但不满足其工艺要求,所以要进行感应表面淬火己达到所要求的力学性能,感应加热淬火后硬度较高,除磨削外不宜再进行其他切削加工,因此工序位置一般安排在半精加工后,磨削加工前。
经淬火后表面获得高硬度、高的耐磨性,而心部仍维持良好的综合力学性能。
为降低表面淬火的淬火应力,保持高硬度、耐磨性,淬火后应低温回火。
图5为调质后感应淬火加低温回火热处理工艺曲线。
温度厂c
900°
图542CrMo钢感应加热淬火加回火工艺曲线
3.242CrMo钢的热处理工艺理论基础、原则
3.2.142CrMo的正火工艺理论基础、原则
(D.正火加热温度
通常对于亚共析钢正火的加热温度通常为以上30〜50°
C,而对于中碳合金钢的正火温度正火温度通常为以上50〜100°
C,保温一定时间后取出喷雾冷却这种冷却方式称为高温正火。
由铁碳合金相图如图6可知42CrMo的加热温度范围为850〜900°
Co加热温度过低先共析铁素体未能全部溶解而达不到细化晶粒的作用,加热温度过高会造成晶粒粗化恶化钢的力学性能,所以我们可以选着870°
Co
图6Fe-C合金相图
(2).正火加热保温时间
保温时间,这个问题比较复杂,一般由试验确定,但也有个经验公式:
t二aKD
t—保温时间(min)a—加热系数(min/mm)K—工件加热是的修正系数D—工件的有效厚度(mm)
工件有效厚度的计算原则是:
薄板工件的厚度即为其有效厚度;
长的圆棒料直径为其有效厚度;
正方体工件的边长为其有效厚度;
长方体工件的高和宽小者为其有效厚度;
带锥度的圆柱形工件的有效厚度是距小端2L/3(L为工件的长度)处的直径;
带有通孔的工件,其壁厚为有效厚度.一般情况下,碳钢可以按工件有效厚度每25毫米为一小时来计算,合金钢可以按工件的有效厚度每20毫米一小时來计算保温时间,加热时间应为2〜3小时左右。
(3).正火的目的
正火的主要目的是消除锻造缺陷,使其成分均匀,硬度和韧性好,并改善材料的切削性,也为调质做好了组织准备。
3.2.242CrMo调质工艺理论基础、原则
(1)•淬火温度的选择。
42CrMo钢,含碳量为0.42%,属于亚共析钢,由图6可得含碳量为0.42%钢的Ac3为800°
C,
由亚共析钢淬火温度要求T二Ac3+30、50(°
C)可得,淬火温度T二830~850(°
C),我们可以设定在840°
Co
(2).淬火保温时间的确定。
根据有效长度①/2二80/2二40mm,可查知,保温时间要大于56min,为保证获得理想组织可选lho
(3).确定淬火介质。
根据零件使用要求,根据图7可知要求淬火后心部硬度大于HRC23时,至水冷端距离小于33mm方可达到要求。
(4).确定回火温度。
在图9不同含碳量与回火温度的曲线中(《钢的热处理》胡光立、谢希文西北工业大学出版社。
)查出含碳量为0.4~0.5%的曲线带,再在纵坐标上查出HRC二35、40,取中值36其曲线带相交的点即为加热温度,大约为480°
(5).确定回火保温时间。
由于回火保温时间为480°
C,根据经验公式可知回火保温时间大约为广1.5ho
回火后空冷即可。
(6)・调质的目的。
调质使工件具有优良的综合力学性能,即高强度和高韧性的适当配合,还可提高一定的耐磨性,以保证零件长期顺利工作。
图742CrMo钢的淬透性曲线
3.2.342CrMo感应加热淬火工艺原理
感应加热淬火加热速度快,淬火质量好,较一般淬火硬度高,得到极细马氏体,且淬硬层深度易于控制,易实现机械化和自动化。
其过程如下:
交变电场
交变磁场:
——:
感应电流
涡流
二表层加热——淬火冷却
感应加热淬火的原理如图9所示,电磁感应产生同频率的感应电流即涡流。
涡流在工件截面上的分布是不均匀的,心部儿乎等于零,而表面电流密度极大,称为“集肤效应”,频率愈高,电流密度极大的表面层愈薄。
依靠这种电流和工件本身的电阻,使工件表面迅速加热到淬火温度,而心部温度仍接近室温,然后立即喷水冷却,使工件表面淬硬。
图8感应加热淬火示意图
(1).感应加热淬火加频率的选择
感应加热可分为三类:
(1)高频加热
常用频率为(200〜300)KHZ,淬硬层深度为(0.5〜2.5)mm。
(2)中频加热
常用频率为(2500〜8000)HZ,淬硬层深度为(2〜10)mm。
(3)工频加热
电流频率为50HZ,不需要频设备,城市用交流电即可,硬层深度为(10〜20)mm以上,城市用交流电即。
根据工件尺寸可知,一般硬化层深§
=(10〜20)%①较为合适,其中①为工件的有效直径,①二80mm可得6^8,所以我们选择中频感应加热表面淬火。
(2).淬火加热温度的确定
加热温度及加热速度是感应加热的最基本的工艺参数,它直接决定钢的相变过程和淬火后的组织,是提高和稳定表面淬火工艺质量的重要保证,根据所要求的性能,可设定温度T=900°
(3).淬火冷却方式的选择
根据所加工的工件尺寸性能,由42CrMo钢的图7和图8,可知42CrMo钢轧机齿轮轴用油淬火可满足使用要求。
但考虑经济等综合因素,且42CrMo的淬透性高,易于淬透,在工业上常用选择乳化液作淬火介质。
(4).感应加热淬火的目的
表面感应加热淬火是为了使钢件达到所要求的表面高硬度,高耐磨性,而心部保持较好的塑性和韧性,且呈现低的缺口敏感性,高的冲击韧性和疲劳强度,己达到最优的使用性能和工艺性能。
3.2.442CrMo回火工艺理论基础、原则
(D.回火温度确定原则
42CrMo钢轧机齿轴要有较高的力学性能,在调质、感应加热淬火加低温回火后,表面硬度需要达HRC50以上,心部硬度HRC35〜45。
由不同钢含碳量的硬度与回火温度关系曲线图10,可知其在150~180°
C回火可满足使用要求。
70
粹火杰凰火沮度/T
图9不同含碳量钢硬度与回火温度关系曲线
(2)•回火温度时间确定原则
回火时间从工件入炉后炉温升至回火温度时间开始计算回火时间一般为1〜3h,可参考经验公式加以确定:
tn二Kn+AnD
式中tn-回火时间(min):
Kn-回火时间基数;
An-回火系数;
D-工件有效厚度(mm),当回火温度低于300°
C时,Kn为120min和An为1由此工件回火时间为2〜3h。
(3).回火的目的
42CrMo钢经调质、感应加热淬火和低温回火后获得显微组织表面为细马氏体、残余奥氏体和碳化物,心部组织为回火索氏体。
回火后不仅消除了淬火时产生的残余应力,降低了脆性,防止变形和开裂,调整了强度,硬度,塑性和韧性,而且稳定了显微组织和工件尺寸,使其达到了使用性能和工艺要求。
3.3选择设备
根据前述的热处理工艺设计及相关文献的表述,选择如下的几种热处理设备:
台车式炉,感应淬火式炉。
冷却及清理设备有:
冷却油槽、酸洗槽\水洗槽、喷丸机。
根据需要添置一些检验设备。
3.3.1设备及工人的年时基数
根据车间生产性质和任务,一般单件小批量生产性质的综合热处理车间,应采用两班
工作制。
其中个别工艺周期较长应连续生产的设备或大型设备应考虑三班工作制;
安装在
生产流水线上的热处理设备,应与生产线生产班制相一致。
详细见下表。
生产性质
工
作
班
制
全年
工作日
每班工
作时数
全年时间损
失
(%)
年时
基数
一、设备
一般设备
连续工作制
3
355
8
9
7722
重要设备
阶段工作制
251
16
4718
小型简易热处理
炉
7
5571
大型复杂热处理
14
7326
二、工人
一般工作条件
4
1927
较差工作条件
12
1748
1)设备年时基数为设备在全年内的总工时数,等于在全年工作日内应工作的的时数减去各种时间损失,即:
民二D设N”(l—b%)
式中耳一设备年时基数(h);
»
设一设备全年工作日,等于全年日数(365天)-全年假日(10天)-全年星期双休日(104天)=251天;
N—每日工作班数;
n—每班工作时数,一般为8小时,对于有害健康的工作,有时为6.5小时;
b-损失率,时间损失包括设备检修及事故损失,工人非全日缺勤而无法及时调
度的损失,以及每班下班前设备和场地清洁工作所需的停工损失。
2)工人年时基数
F人=D“Q_b%)
式中尸人一工人年时基数(h);
D人一工人全年工作日,等于全年日数(365天)-全年假日(10天)-全年星期双休日(104天)=251天;
"
一时间损失率,一般取4%,时间损失包括病假、事假、探亲假、产假及哺乳、设备请扫、工作休息等工时损失。
3.3.2设备数量的计算
根据热处理零件分工的年处理量,分别釆用各工序的平均生产率,可以计算得出某项设备所承担热处理任务的年负荷数,再根据该项设备的工作制度所确定的年时基数,即可计算得出该项设备的负荷率并确定台数。
设备需要量可根据热处理工序生产任务和设备生产能力计算出设备年负荷基数,再计算设备需要量。
1.设备年负荷基数
设备年负荷基数G为:
G=Q/p
式中设备年需完成的生产量(Kg/年)
p-设备生产率(Kg/h)
2.设备数量计算
C=G/F
式中尸-设备年时基数(h)
由上述的公式和己知条件:
RT-105-9台车式炉炉膛尺寸:
长为1500nun,宽为:
800mm,高为600nmi.单位炉底面积生产率g=140kg/(m2*h)
得:
P=1.5*0.8*140=168kg/h,G=1200000/l68=7143,C=7143/7722=0.93取整数C为1.
由上述计算可知整个工序所需的设备的台数如下:
序号
设备名称
型号
用途
生产率
(Kg/h)
年时基数
(h)
数量
1
台车式电阻炉
RT-1O5—9
正火、淬
火、回火
168
2
感应淬火炉
GC—1205
淬火
300
3.3.3冷却设备
使用的主要冷却设备是油槽。
油槽为冷却介质,设备主要是由盛油的槽子构成。
油的粘度对冷却能力和冷却均匀性有显著的影响。
可以通过配备介质搅拌装置和对介质进行适当加热(40〜95°
C),提高其冷却能力和冷却的均匀性。
淬火油槽通常配有如下功能:
介质搅拌功能、介质加热和换热功能、介质的油烟收集和处理功能、防火和灭火功能、输送工件完成淬火工艺过程的功能等。
3.3.4清洗、清理设备
(1)清洗设备
随着热处理工艺的发展和对环境卫生的要求日益提高,零件热处理前后的清洗更加重要。
一些化学热处理工艺操作前要求除油,有时利用热处理炉废气烧尽表面油污,以保证热处理质量。
零件的热处理后除油,可防止回火过程中产生大量的烟雾,污染环境,同时保持零件表面光亮。
目前主要清洗设备有:
室内和输送带式、悬挂输送链式、滚筒式清洗机、溶剂清洗及其他超净清洗设备。
(2)清理设备
使用的是喷丸机。
为清理零件热处理后表面的氧化皮,可釆用喷砂机、喷丸机、抛丸机、喷丸清理滚筒、砂轮机、抛光机、酸洗槽等。
随着检验设备的发展,过去常用酸洗方式清理氧化皮,现己多釆用喷丸清理,并发展了强化喷丸和应力喷丸等先进技术。
3.3.5辅助设备
(1)检查设备
为检查零件热处理后的硬度,一般采用布氏、洛氏、肖氏硬度计。
(2)其他辅助设备
其他辅助设备,包括存放工具夹装置,如工具架、吊具架、冷却盘,切取试样设备,如锯床、切割机、磨光试样机等。
为感应加热用感应器制造服务,以及为仪表的检修校正服务。
3.3.6起重运输及自动化设备
(1)常规起重运输设备
起重设备根据设备安装、修理、工艺所需起吊运输最大零件重量以及工艺平面布置决定,起重设备适用范围及选择原则见下表。
起重设备适用范围及选择原则
常用规格
主要适用范围
选用意见
桥式起重机
5〜10t
大型设备维修,大型零件运输、装卸
一般厂房长50米
选用一台
梁式起重机
1〜3t
中小型设备维修,中小零件运输、装卸
每一跨可选一台
悬臂起重机
0.25〜1
工作量较大的局部区,桥式、梁
式起重机达不到的地方
为某项设备及工
艺专设
悬挂运输链
—
卑昆道
平板车
电瓶车、叉车、
手推车
(2)生产机械化与自动化装置
热处理设备的机械化与自动化,车间之间及车间内工序之间的机械化运输装置及控制,根据零件的产量和生产过程的具体需要,合理选用与布置,以改善劳动条件,提高生产率。
a.辘道辘道可运输和贮存部分零件,将不同工序联系起来,有着不同形式布置,如直线型、U型、L型、环型等。
b.轨道车根据不同的设备操作和布置选用,如利用普通轨道车和激动轨道车联系淬火、清洗、回火等周期作业炉。
c.单轨电动葫芦单轨葫芦可将各工序设备联系起來,可布置成一字型、L型、环型。
d.悬挂运输链用于车间之间或工序之间的运输,连续运行,通过与下降段配合,可实现连续式炉生产线的全过程机械化运输。
4.车间布局
4.1车间在厂区内的位置
对热处理车间在总体布置中要求:
(1)热处理车间散发大量燃烧废气、保护气氛废气,其他有害气体及油烟、粉尘等,所以应位于其他厂房下风向,且要有卫生防护带。
(2)热处理车间靠近各类震源时,应该有一定间距或釆取相应的隔震措施,震源如锻锤、空压机、氧气机、铁路等。
热处理车间为综合性处理车间,为全厂服务,在工厂总体位置中应选择适中的位置或靠近与其联系多的车间。
4.2车间面积及面积指标
车间总面积包括工艺设计中用于基本生产设备和辅助设备所占用的面积,包括厂房、披屋、露天起重机下的有效面积。
(1)生产面积生产设备、设备之间通道、工人操作、工件存放地所占用的面积,以及清洗、清理、矫正、取样、运输设备所占用的面积,占总面积50%〜70%。
(2)辅助面积变配电间、变频间、电容期间、检验间、快速实验室、保护气氛制备间、机修间、仪表间、