高炉自动测控系统设计大学论文Word格式.docx
《高炉自动测控系统设计大学论文Word格式.docx》由会员分享,可在线阅读,更多相关《高炉自动测控系统设计大学论文Word格式.docx(33页珍藏版)》请在冰豆网上搜索。
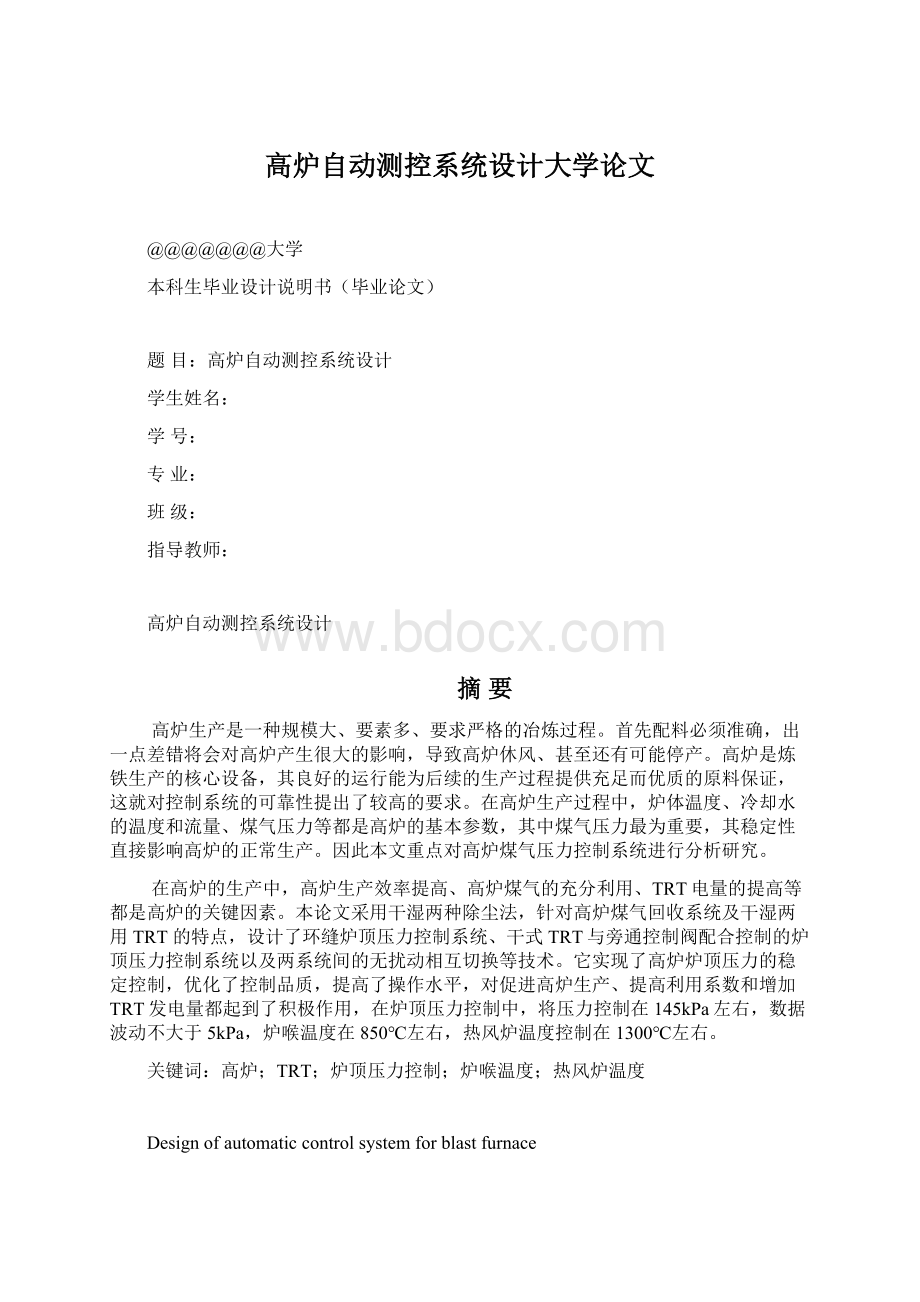
TRT;
炉顶压力控制;
炉喉温度;
热风炉温度
Designofautomaticcontrolsystemforblastfurnace
Abstract
Theproductionofblastfurnaceisakindoflargescale,multiplefactors,thesmeltingprocessofstrictrequirements.Firstofalltheingredientsmustbeaccurate,alittlemistakewillhaveagreatinfluenceontheBF,resultinginblast-furnacedamping-down,mayevenstopproduction.Theblastfurnaceisthecoreequipmentoftheiron-smeltingproduction,anditsgoodoperationcanprovidesufficientandhighqualityrawmaterialguaranteeforthefollow-upproductionprocess,thereliabilityofthecontrolsystemputforwardhigherrequirements.Intheprocedureofproductionofblastfurnace,furnacetemperature,coolingwatertemperatureandflowrate,gaspressurearethebasicparametersofblastfurnace,thegaspressureisthemostimportant,thenormalproductionanddirectlyaffectthestabilityofblastfurnace.Thispaperfocusesontheanalysisofblastfurnacegaspressurecontrolsystem.
Inblastfurnaceproduction,improveproductionefficiencyofblastfurnace,blastfurnacegas,thefulluseofTRTimprovedcapacityarekeyfactorsofblastfurnace.Inthispaper,thedryandwettwodedustingmethod,accordingtothecharacteristicsofthedual-purposeTRTblastfurnacegasrecoverysystemandthedesignofwetanddry,theannularfurnacetoppressurecontrolsystem,dryTRTandbypasscontrolvalvewithtoppressurecontrolundisturbedswitchingtechnologysystemandthetwosystem.Itrealizesthestablecontrolofblastfurnacetoppressure,optimizingthecontrolquality,improvetheoperationlevel,topromotetheproductionofblastfurnace,improvetheutilizationcoefficientandtheincreaseofTRTpowergenerationhasplayedapositiverole,inthecontroloftoppressure,thepressurecontrolinabout145kPa,datafluctuationislessthan5kPa,thetemperatureinthefurnacethroat850℃,hot-blastfurnacetemperatureat1300℃.
Keywords:
TRT;
blastfurnace;
furnacetoppressurecontrol;
furnacetemperature;
hotblaststovetemperature
前言
高炉自动化技术的发展是随着工艺技术和设备的发展而进步的。
高炉炼铁技术历史悠久,随着近年来Corex、Finex等融熔还原炼铁技术的发展,炼铁技术逐步多样化。
但现代化高炉投入更少,产能更大,特别是高炉炼铁的能耗持续降低环境条件大幅改善。
焕发出了新的活力,体现出越来越强的生命力。
在传统高炉炼铁工艺中通过许多模拟仪表来监控炼铁生产过程。
它包括高炉本体及热风炉众多温度、压力、流量数据的监测,综合鼓风的风量、风压、风温、富氧量等参数的检测控制,以及上料和炉内布料过程模拟显示盘等。
到20世纪80年代,实现了以微机为核心的PLC或DCS控制系统取代高炉传统电器和仪表作为基础自动化控制的目标,实现了高炉和热风炉本体参数、槽下配料称量、上料及炉顶布料、煤粉喷吹等工艺参数的集中监控。
而多台PC机集中显示各种监控画面、趋势画面、报警画面的应用,使计算机能更直观地、更准确地反映高炉过程的动态变化特征。
基础自动化主要完成生产过程的数据采集和初步处理,数据显示和记录,数据设定和生产操作,执行对生产过程的仪表调节电气传动控制。
近年发展起来的现场总线控制技术、以太网技术也逐步在高炉基础自动化系统中应用,分布控制系统替代集中控制已成为现代高炉控制的主流。
在PLC或DCS控制算法的应用上,已普遍采用PID算法,智能控制、先进控制技术等,并在高炉炉顶压力控制、炉顶布料自学习控制、热风炉燃烧控制、喷煤控制等方面有了较好的应用,取得了一定成果。
在检测方面,与回路控制、安全生产、能源计量、以及与高炉模型和专家系统相配套的流量、压力、温度、液位、重量等信号的各类检测仪表的配备上比较齐全。
色谱仪、质谱仪、微波液位计等高技术智能仪表大量采用:
双文丘里流量计、无基坑不断轨道衡等具有自有知识产权的仪表设备的应用。
绪论
课题背景及研究意义
钢铁产业是国民经济的重要支柱产业,涉及面广、产业关联度高、消费拉动大,在经济建设、社会发展、财政税收、国防建设以及稳定就业等方面发挥着重要作用。
在国民经济快速发展的动下,中国钢铁工业进入快速发展阶段,这也带动了高炉炼铁的快速发展。
伴随着中国生铁产量的高速增长,中国高炉炼铁技术水平也取得了一定进展。
由于生铁产量的高速增长造成了全国铁矿石,焦炭供应紧张,价位攀升,质量下降,成分不稳定,导致了部分高炉技术经济指标下滑。
表现在入炉品位虽提高,但入炉焦比升高喷煤比下降等现象。
以宝钢、武钢、鞍钢、首钢、邯钢、梅山、莱钢、三明和新兴铸管等企业的高炉部分指标达到了国际先进水平,大大地缩短了中国高炉炼铁技术与工业发达国家之间的差距。
中国炼铁产业集中度低,高炉座数多,多是小型高炉,大型高炉较少。
各高炉生产技术水平在高效、低耗、优质、长寿、高效益等方面取得了不同程度的新进展。
同时,高炉炼铁技术取得了显著进展,炼铁生产技术经济指标大幅度改善。
高炉工艺技术和装备水平显著提高,在高炉现代化,大型化、喷煤、长寿和环保节能技术和装备得到了长足的发展。
高炉炼铁技术现状与发展趋势
展望新世纪的炼铁技术,离不开资源、能源和经济等形势变化这些主要课题。
21世纪也是高炉炼铁“变革的世纪”,期望在新时期钢铁产业能够进入资源、能源和环境的和谐,这是确立炼铁业持续发展的重要关键,也必须从这个理念和观点展开高炉炼铁技术的研究和开发。
我国许多高炉已经感到当前形势的变化,并采取了相应的措施。
对高炉炼铁技术发展的方向有了新的认识,为振兴炼铁工业打下了基础。
在此很有必要综观世界高炉炼铁技术发展现状及今后的方向。
⑴炉顶布料技术
我国高炉在大型化、高效化、低排放过程中,对高炉设计、生产中出现的一系列新问题已经得到各方面的重视,并正在进行研究,更需要多方协作。
好的装料制度,是为了创造长期稳定顺行的炉况。
以大角度、大角差、大力度稳定边沿气流,以合理的中心加焦量来强化和稳定中心气流,不断优化布料矩阵促使煤气利用率的提高。
实践证明,矩阵大角度外推有利于形成稳定的边缘矿焦平台及中心漏斗式料面分布,有利于形成稳定的边缘、中心两道煤气流,降低煤气阻损,改善料柱透气性。
⑵炉身维护技术
济钢非常重视高炉操作炉型的维护,认为合理操作炉型是高炉得到强化冶炼和获得稳定良好指标的基础。
在降料面至风口更换好风口段冷却壁后,实施炉内喷涂造衬,在短时间内修复高炉炉型,以满足高炉操作的需要。
喷补后高炉内型表面均匀、平整,目测效果很好。
高炉喷补后,开炉非常顺利,快速达产达效。
结合高炉实际情况,研究开发了高炉炉衬温度与热负荷监测模型,描绘冷却壁温度分布及炉体热负荷分布,实现对高炉炉体的工作状况在线监测,从而推测高炉炉型和煤气流分布情况,为高炉操作者调整炉况寻求合理操作炉型提供借鉴。
⑶高风温、富氧喷煤技术
通过采取强化标准化操作、禁止开冷风大闸等措施,高炉所用风温基本稳定在1200℃以上。
高风温不但为高炉带入了宝贵的物理热,而且可以快速加热煤粉,促进煤粉提前着火,利于煤粉化学能的充分利用。
提高富氧率不仅可以减少单位生铁的煤气量,减缓大量喷煤及高强度冶炼时的透气性变坏,改善间接还原,而且可以提高风口前的理论燃烧温度,改善煤粉的燃烧条件。
随着制氧能力的提高,高炉富氧率得到了大幅度提高。
高炉炼铁控制技术现状与发展趋势
在民国时期,钢铁业在中国已经有了一定的发展,但那时的控制主要靠人工,机械化不高,产量也很低;
新中国成立后,当时在苏联的帮助下,钢铁行业有了进一步的发展,自动化有了提高,实现了版自动化,产量明显提高;
在70年代中期,中国大力发展钢铁,这一时期中国钢铁产量增长迅速,实现也很大的突破;
现在高炉炼铁控制技术已经完全实现了自动化,形成了一套完整的自动化控制系统。
主要研究内容及章节安排
主要研究内容
本文主要研究高炉控制技术,其中主要研究了压力检测和控制系统、温度检测系统、流量检测系统。
炉顶压力对于高炉炼铁来说是很重要的,压力的稳定度控制机直接决定着产量,因此在此着重介绍炉顶压力控制。
文章以高炉控制为基点,画出了相应的组态王控制界面图,CAD原理图,以及相应的程序。
文章对主要的参数、控制仪表进行分析,实现了真正的模拟高炉生产的画面。
章节安排
论文主要分为五章,具体如下:
第一章为绪论,主要介绍高炉炼铁技术的发展,高炉控制技术的发展,详细说明了现代钢铁行业的一些控制方式。
第二章为高炉炼铁生产工艺流程,介绍了高炉炼铁生产工艺流程,主要对生产工艺流程的细节分析,并且将国内知名企业的相关技术进行对比。
第三章为高炉自动测控系统设计,介绍了高炉自动测控系统设计,其中测控要求及测控参数的相关知识介绍,以及自动检测系统设计、自动控制系统设计,自动检测系统包括温度检测系统、压力检测系统、流量检测系统。
第四章为高炉自动测控系统实施方案,主要是高炉自动测控系统实施方案,其中包括硬件系统和软件系统。
第五章为上位机监控系统设计,主要研究上位机监控系统,用组态王进行监控画面的设计。
最后进行论文总结,并且附上相关程序和参考文献。
高炉炼铁生产工艺流程
高炉结构组成
高炉在炼铁占据主导地位,主要包括高炉炉壳、炉身、炉腰、炉腹、炉缸、炉缸、炉底、炉基、炉衬以及炉喉护板。
主要部分原理如下说明。
⑴高炉炉壳:
现代化高炉广泛使用焊接的钢板炉壳,只有极少数最小的土高炉才用钢箍加固的砖壳。
炉壳的作用是固定冷却设备,保证高炉砌体牢固,密封炉体,有的还承受炉顶载荷。
炉壳除承受巨大的重力外,还要承受热应力和内部的煤气压力,有时要抵抗崩料、坐料甚至可能发生的煤气爆炸的突然冲击,因此要有足够的强度。
炉壳外形尺寸应与高炉内型、炉体各部厚度、冷却设备结构形式相适应。
⑵炉喉:
高炉本体的最上部分,呈圆筒形。
炉喉既是炉料的加入口,也是煤气的导出口。
它对炉料和煤气的上部分布起控制和调节作用。
炉喉直径应和炉缸直径、炉腰直径及大钟直径比例适当。
炉喉高度要允许装一批以上的料,以能起到控制炉料和煤气流分布为限。
⑶炉身:
高炉铁矿石间接还原的主要区域,呈圆锥台简称圆台形,由上向下逐渐扩大,用以使炉料在遇热发生体积膨胀后不致形成料拱,并减小炉料下降阻找力。
炉身角的大小对炉料下降和煤气流分布有很大影响。
⑷炉腰:
高炉直径最大的部位。
它使炉身和炉腹得以合理过渡。
由于在炉腰部位有炉渣形成,并且粘稠的初成渣会使炉料透气性恶化,为减小煤气流的阻力,在渣量大时可适当扩大炉腰直径,但仍要使它和其他部位尺寸保持合适的比例关系,比值以取上限为宜。
炉腰高度对高炉冶炼过程影响不很显著,一般只在很小范围内变动。
为了在操作技术上能正确处理高炉冶炼中经常出现的复杂现象,就要切实了解炉内状况。
在尽量保持高炉的原有生产状态下停炉、注水冷却或充氮冷却后,对从炉喉的炉料开始一直到炉底的积铁所进行的细致的解体调查,称为高炉解体调查。
它虽不能完全了解高炉生产的动态情况,但对了解高炉过程、强化高炉冶炼很有参考价值。
高炉还有一些相应的装置,主要有高炉冷却装置、高炉除尘器、高炉鼓风机及高炉冷却装置。
高炉炉衬内部温度高达1400℃,一般耐火砖都要软化和变形。
高炉冷却装置是为延长砖衬寿命而设置的,用以使炉衬内的热量传递出动,并在高炉下部使炉渣在炉衬上冷凝成一层保护性渣皮,按结构不同,高炉冷却设备大致可分为:
外部喷水冷却、风口渣口冷却、冷却壁和冷却水箱以及风冷(水冷)炉底等装置。
高炉除尘器用来收集高炉煤气中所含灰尘的设备。
高炉用除尘器有重力除尘器、离心除尘器、旋风除尘器、洗涤塔、文氏管、洗气机、电除尘器、布袋除尘器等。
粗粒灰尘(>60~90um),可用重力除尘器、离心除尘器及旋风除尘器等除尘;
细粒灰尘则需用洗气机、电除尘器等除尘设备。
高炉工艺原理
高炉的生产工艺是比较复杂的过程,高炉炼铁原则工艺流程图如2.1所示。
图2.1高炉炼铁原则工艺流程图
炼铁工艺是是将含铁原料(烧结矿、球团矿或铁矿)、燃料(焦炭、煤粉等)及其它辅助原料(石灰石、白云石、锰矿等)按一定比例装入高炉,并由热风炉向高炉内鼓入热风助焦炭燃烧,原料、燃料随着炉内熔炼等过程的进行而下降。
在炉料下降和煤气上升过程中,先后发生传热、还原、熔化、脱炭作用而生成生铁,铁矿石原料中的杂质与加入炉内的熔剂相结合而成渣,炉底铁水间断地放出装入铁水罐,送往炼钢厂。
同时产生高炉煤气,炉渣两种副产品,高炉渣水淬后全部作为水泥生产原料。
炼铁方法主要有高炉法、直接还原法、熔融还原法等,其原理是矿石在特定的气氛中(还原物质CO、H2、C;
适宜温度等)通过物化反应获取还原后的生铁。
生铁除了少部分用于铸造外,绝大部分是作为炼钢原料。
高炉炼铁是现代炼铁的主要方法,钢铁生产中的重要环节。
这种方法是由古代竖炉炼铁发展、改进而成的。
尽管世界各国研究发展了很多新的炼铁法,但由于高炉炼铁技术经济指标良好,工艺简单,生产量大,劳动生产率高,能耗低,这种方法生产的铁仍占世界铁总产量的95%以上。
高炉生产时从炉顶装入铁矿石、焦炭、造渣用熔剂(石灰石),从位于炉子下部沿炉周的风口吹入经预热的空气。
在高温下焦炭(有的高炉也喷吹煤粉、重油、天然气等辅助燃料)中的碳同鼓入空气中的氧燃烧生成的一氧化碳和氢气,在炉内上升过程中除去铁矿石中的氧,从而还原得到铁。
炼出的铁水从铁口放出。
铁矿石中不还原的杂质和石灰石等熔剂结合生成炉渣,从渣口排出。
产生的煤气从炉顶导出,经除尘后,作为热风炉、加热炉、焦炉、锅炉等的燃料。
本章小结
本章主要介绍了高炉结构组成和高炉工艺原理,高炉对于炼铁来说是至关重要的,高炉相关技术的自动化程度直接决定着钢铁的产量,因此,先进的技术,对钢铁企业的发展,钢铁的质量,有着很大的影响。
测控要求及测控参数
测控要求
主要完成高炉自动控制系统的温度、压力、流量的检测。
对温度来说,主要检测炉顶温度、炉喉温度、炉身温度、炉基温度、炉底温度、热风温度;
流量主要冷风流量和冷却水流量,本文主要进行炉顶煤气压力的检测和控制,压力控制是主要设计点,压力控制油两种方式,利用减压阀组控制高炉顶压和利用TRT装置控制顶压。
主要分析了这两种控压的原理分析。
测控参数
主要研究的测控系统有压力测控系统、温度测控系统、流量测控系统;
压力测控系统主要参数是炉顶煤气压力、过滤器前冷却水压力;
温度测控系统主要参数是炉顶温度、炉喉温度、炉身温度、炉基温度、炉底温度、热风温度;
流量测控系统主要参数是冷风流量、冷却水流量。
以上参数以炉顶煤气压力为主,这也是主要控制对象,因为炉顶压力的控制精度直接影响高炉的顺行、产量。
自动检测系统设计
温度检测系统设计
主要检测参数包括炉顶温度、炉喉温度、炉身温度、炉基温度、炉底温度、热风温度、冷却水温度。
温度测量原理图如图3.1所示。
图3.1温度测量原理图
高炉的炉喉,炉身、炉底、炉基、热风护的温度变化范围为0-1000℃,在高炉炉喉、炉身、炉底、炉基、热风护邓地方分别安装有测量仪表,测量点为5个,最终数据有着5个测量点综合而来,并且选用热电偶作为检测元件。
冷却水的温度范围为0-500℃,用热电阻作为检测元件。
压力检测系统设计
压力检测系统主要检测炉顶煤气压力、过滤器前冷却水压力、过滤器后冷却水压力、热风管道压力。
压力测量原理图如图3.2所示。
图3.2压力测量原理图
经过压力变送器的变送将压力信号转换为电信号经过模数转换后送计算机进行显示。
压力检测主要是炉顶压力,煤气压力的测量实在炉顶安装相应的仪器,在测量时选择多点测量,并且选择更高的数据为最终结果。
在检测出仪表压力后,系统会对数据进行分析,并且判断炉顶压力是否有所波动,从而系统选择相应的控制方式。
流量检测系统设计
流量检测系统由节流装置、引压导管、差压变送器及显示仪表组成,我们测量的主要参数是冷风流量、冷却水流量。
流量检测原理图如图3.3所示。
图3.3流量检测原理图
流量检测室在水通道安装相应的仪器,测量器流量,再将数据传送到计算机,系统进行分析,根据实际情况来控制冷却水流量大小,当然,本文主要是炉顶压力的设计,在流量和温度的测量方面讲述得比较简单。
自动控制系统设计
炉顶压力自动控制系统设计
炉顶压力控制一般有两种方法,利用减压阀组控制高炉顶压和利用TRT装置控制顶压,这两种方法在高炉处于不同情况时相互转化,在各自不同的状态控制高炉煤气压力,将煤气压力控制在一定的范围之内。
稳定性达到一定程度,产量也随之提高,能源得到充分利用。
TRT实物图如图3.4所示。
图3.4TRT装置实物图
TRT系统全名为高炉煤气余压能量回收透平发电装置(BlastFurnaceTopGasPressureRecoveryTurbineUnit)。
它的作用是回收高炉出口煤气中所蕴含的压力能和热能。
上图即为工厂生产中实际TRT系统,它对工厂生产是至关重要的。
TRT主要由调速阀、透平机静叶、发电机组等设备组成。
调速阀:
用于调节透平机的冲转转速,使之达到发电机发电所需的额定转速,保证发出的电为50Hz。
改进前炉顶煤气压力自动控制工艺流程图如图3.5所示。
图3.5改进前炉顶煤气压力自动控制工艺流程图
改进后炉顶煤气压力自动控制工艺流程图如图3.6所示。
图3.6改进后炉顶煤气压力自动控制工艺流程图
经湿式AGS或干式布袋除尘后的净煤气送至TRT入口管后,从入口蝶阀(IV)、入口插板阀(TIV)、紧急切断阀(TSV)、调速(TCV)阀和可调静叶(SB)进入透平机膨胀作功,然后透平机带动发电机发电。
膨胀后的煤气经TRT出口插板阀(TOV)、出口蝶阀(OV)送到净煤气主管上。
在透平入口与出口间并联2台旁通控制阀(BCV1、BCV2)及主旁通阀(BV),在TRT启动、停机、干湿相互切换以及特殊工况时参与控制,以确保高炉炉顶压力不会产生大的波动。
TRT调节控制顶压目的主要有两个:
一是正常生产时,在保证高炉顶压稳定的前提下,充分利用炉顶煤气资源,驱动发电机发电;
另一个是当TRT发生故障停机时,在保证高炉顶压稳定的前提下,能及时安全地从煤气管网中退出。
因此TRT高炉炉顶压力控制系统从控制系统的结构上来看,可分为TRT停运时的炉顶压力控制(湿式),TRT停运时的炉顶压力控制(干式),TRT启动、运行时的炉顶压力控制三种控制系统。
⑴TRT停运时的炉顶压力控制(湿式)
当湿式AGS除尘运行且TRT停机时,煤气流经AGS和主旁通阀(BV),主旁通阀全开,AGS的三个环缝装置同步动作调节炉顶压力。
此时准备启动TRT,则手动慢慢关闭主旁通阀(BV)提高TRT前压,为TRT启动建立前后差压。
当主旁通阀全关闭后,TRT前压全部由TRT系统旁通控制阀(BCV1,BCV2)控制,顶压与TRT前压之差即为AGS除尘所需要的差压。
⑵TRT停运时的炉顶压力控制(干式)
当干式除尘运行且TRT停机时,煤气流经布袋除尘器和旁通控制阀(BCV1,BCV2),BV全关闭,旁通控制阀(BCV1,BCV2)调节炉顶压力。
⑶TRT启动、运行时的炉顶压力控制
当满足所有启动条件(共30多项,湿式与干式运行条件略有不同),TRT开始启动,随后进入速度控制。
TRT速度逐渐提高,BCV1,BCV2逐渐关小。
TRT完成同步操作并网后进入功率控制,接着进行升功率操作,BCV1,BCV2进一步关小。