产品质量先期策划控制程序文件Word文件下载.docx
《产品质量先期策划控制程序文件Word文件下载.docx》由会员分享,可在线阅读,更多相关《产品质量先期策划控制程序文件Word文件下载.docx(22页珍藏版)》请在冰豆网上搜索。
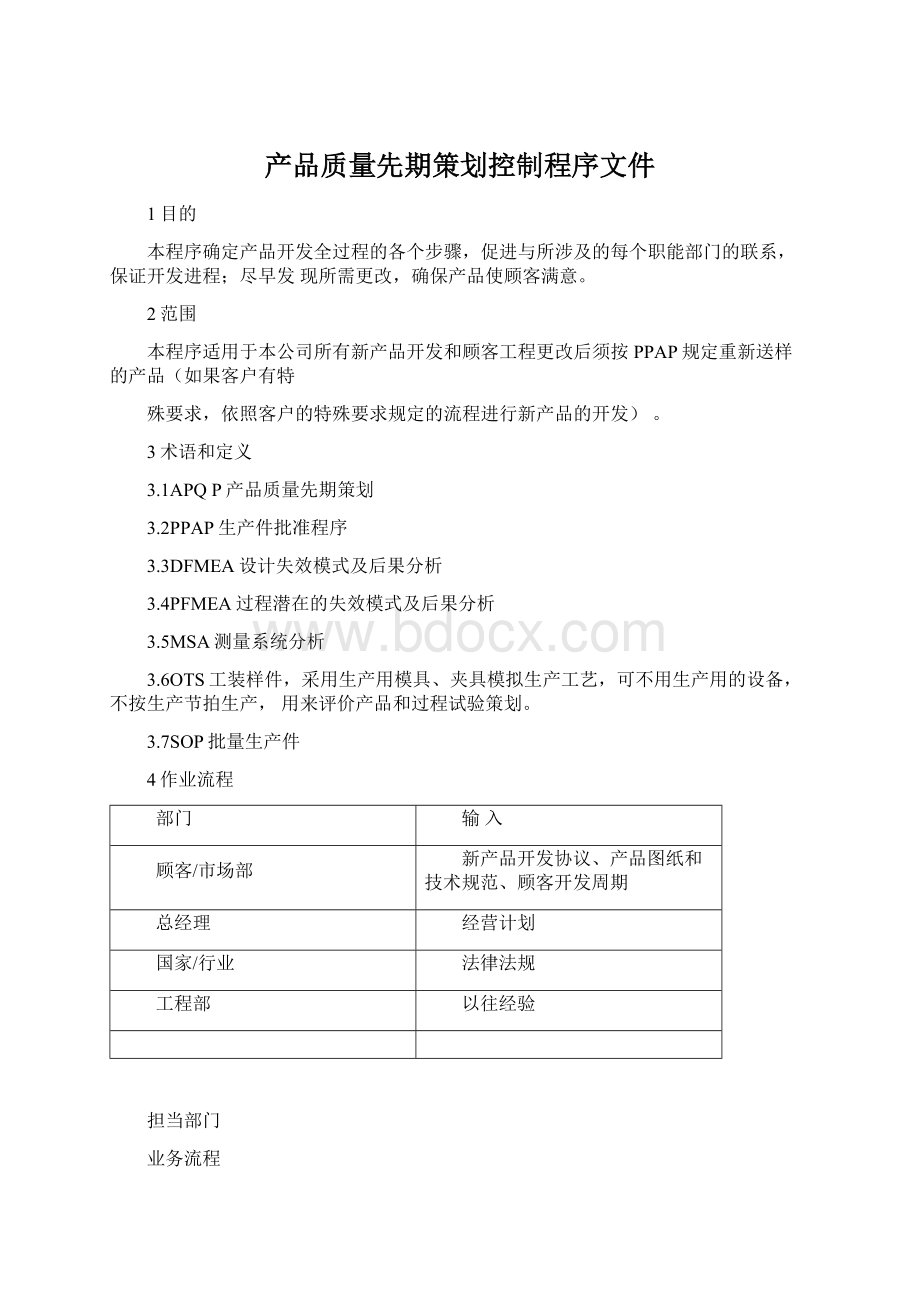
顾客代表
成本分析
NO
评审
项目小组组
长
成立项目小组
1
T
APQP实施计划
r
确定设计目标
Yes
初始材料清单
初始过程流程
项目小组
初始特殊特性明细
f
费用预算
J
L
小组可行性承诺
F
输岀评审
阶段总结
1第一阶段:
计划和确定项目
根据公司发展方向、经营计划及顾客要求编写顾客访谈报告,部门评议后将访
谈的新产品背景信息、技术和质量要求及开发周期、费用预期价格等形成《产品建议书》附带产品图纸、样件、标准、特殊要求等提交给工艺工程部;
组织成立项目小组(包括:
生产部及工程部、品质部、财务部、资材部、业务部、管理部等部门)根据:
产品开发建议书、图纸/样件/数模/技术规范,在
考虑工艺、工装、设施、材料、人员等要求,并与冋类产品进行比较后进行;
组织进行成本核算工作,成本核算包含商务及技术成本并提供报价单;
组织各职能部门对产品建议书、技术可行性分析、成本分析及产品其他的信息进行评审。
评审意见记录在“立项评审表”中,评审通过经总经理批准后立项。
1组织成立项目小组并确立项目负责人,小组成员应来自以下部门:
工程部、品质部、生产部及资材部、业务部、财务部、管理部,必要时,可有供方或顾客代表参加。
2明确小组成员及职责、开发周期、费用和关键时间节点:
小组全体成员须按公司保密性承诺对客户项目所有信息予以保密。
组织小组成员及相应部门负责人召开开发项目会议制定“APQF实施计划”,在
制定计划时应考虑产品的类型、复杂性和顾客的期望并运用同步工程来确定具体的策划事项。
所有小组都应在每一事项、措施和进度上取得一致意见。
针对顾客的要求“产品建议书”起草“设计任务书”,其中包括顾客要求、设计目标、可靠性和质量目标及达成目标所采取的措施,质量目标根据顾客和公司质量目标规定。
“设计任务书”由总经理审核批准后生效。
工程部负责制定开发产品的初始材料清单及初始过程流程图。
根据顾客要求识别初始特殊特性(如顾客无此要求则自己识别)。
组织将成本目标分解到相关阶段和部门,在新品开发、设计、产品验证时,在保证产品质量的前提下,兼顾成本目标,由各阶段负责人作好开发费用监控记录与预算值作对比评估,并交项目负责人对各阶段产品开发费用进行审核、监
控。
其宗旨在于控制开发成本,并力求在此后向顾客报价才能够准确地估算真实成本,费用预算由总经理批准。
根据以上工作总结在保证所提供的图样和/或规范已被用来作为分析满足所有
规定要求能力的基础上对是否能达到质量要求、是否足够的过程能力、是否能
按预定计划完成、成本是否适中作岀小组可行性承诺,确保所提岀的设计能以
顾客可接受的价格付诸于制造、装配、试验、包装和足够数量的交货。
组织小组成员及相应部门负责人对本阶段的输岀结果是否符合输入要求进行评定,对本阶段所有工作内容和文件进行检查,对本阶段的工作成果、积累的经验、采用的新技术方法、成本控制状况、阶段输岀是否满足输入要求等内容进行总结并编写阶段总结报告总经理批准以寻求其支持。
第一阶段输出
市场调查与可行性分析报告、
产品立项建议书、立项评审表
APQP实施计划、设计任务书、产品保证
计划
初始材料清单、初始过程流程图
小组可行性承诺、输岀评审
产品和过程特殊特性初始清单
资材部
初始供应商名单
2第二阶段:
产品设计开发和验证
组长
产品结构、性能分析
项目小组根据顾客提岀的产品型号、技术要求或图样等,在分析以往重大的教
训、经验、关键特性、功能要求及所有其他失效模式的基础上,进行产品结构、
性能分析等分析。
项目小组设计工艺时应考虑可制造性和可装配性,其中包括:
1设计、概念、
功能和对制造变差的敏感性;
2制造和/或装配过程;
3尺寸公差;
性能要
求;
4部件数;
5过程调整;
6材料搬运。
根据设计目标、可靠性和质量目标、DFMEA顾客的特殊要求等对设计图纸、工程规范、材料规范、特殊特性等进行评审,并完成设计评审报告、验证报告。
可制造性和(装配设计)
―・工艺
设计
项目小组根据顾客要求、产品的特性和生产设备、检测设备情况、人员操作等因素,进行工艺设计,编制样件控制计划;
样件i
式制|
项目组试制人员按项目组的工艺设计及产品要求,进行样件试生产。
及时将制岀的样件进行性能测试,如果部分性能不能符合要求,则需重做调整,
重新做试样,直至符合产品要求。
一
1样件性能试验
样件送用
户确认
当客户要求时,项目组业务部人员应及时向用户提交所要求的资料,资料可以
包括:
样件,原材料性能测试报告,样件检测规范及报告、样件控制计划等。
只有当用户确认后,才能进行试生产。
设计责任部门的输岀(作为第二章的输岀)
品质部
技术质量协议
样件测试/确认报告
采购订单/合同
新设备、工装和设施清单;
原材料样件认可报告
工装和试验设备检查表
样件控制计划、控制计划检查表
第二阶段评审输岀报告
样件检验规范/条件
3第三阶段:
过程设计开发和验证
产品/过程质量体系评审
组织小组成员及有关人员,对公司现有类似产品的过程进行评审,就以下内容与开发产品要求进行差距分析,采用多方论证的方法解决问题并将解决措施列入开发计划:
a)现有质量管理体系;
b)、现有技术和顾客要求的差距;
c)公司平面布置图;
d)生产工艺装备;
e)检测和试验设备;
f)质量能力。
生产部
设备、工装、检测设备、设施要求
1对提供的开发基准进行评估,输岀新设备、工装、设施清单和需求计划;
2对顾客提供的产品基准资料评审后输岀量检具/试验设备清单和需求计划;
供方选择策划
过程流程设计<
场地平面布置设计
资材部/生产部
生产部管理部
采购员根据采购技术要求按照供方选择程序进行供方的选择和开发
分析制造、装配过程自始自终的机器、材料、方法和人力变化的原因进行过程流程设计,作为PFMEA控制计划及场地平面布置图的输入。
生产部组织、工程部配合进行场地平面布置策划确定检测总数、控制图位置、限度样品、返工区和缺陷材料的储存区、原辅材料/成品的储存区、半成品流动储存工
具以上应与过程流程图和控制计划相协调。
采用矩阵分析方法用来显示产品和过程特性和制造工位之间关系。
在矩阵分析、过程流程图基础上进行过程的潜在失效和后果分析-PFMEA并针对分
析结果采用相应技术方法并进行效果验证以降低过程风险顺序度数。
PFMEA是一种
动态文件,当发现新的失效模式时,需要对它评审和更新。
借助过程设计、PFMEA和以往制造过程获得的经验进行试生产控制计划的编制,应包括正式生产前要实施的附加产品/过程控制。
如:
增加检验次数、增加生产过程
中的检查和成品检验频次、统计评价、增加审核。
根据控制计划项目要求,编制包括:
作业指导书、设备操作指导书、检验指导书等。
进行包装规范(包含供方)的设计,任何情况下包装设计应保证产品性能和特性在包装、搬运和开包的过程中保持不变,包装应与所有的材料搬运装置像匹配。
适当时可使用顾客的包装标准或一般的包装要求。
根据过程流程图检查清单、过程FMEA检查清单、控制计划检查清单、场地平面布
置图检查清单、产品过程质量检查清单等进行过程设计有效性的评审。
如存在不符合检查清单要求的醒目,应立即制定纠正措施并明确责任人和完成期限,纠正后应重新进行评价。
工装模具、设备规划:
由生产部提岀新的生产设备要求,工程部提岀新的工装模具需求,生产部负责外协制作模具,品质部提岀检测设备需求并协助采购。
模具设计/制造参照《工装模具控制程序》实施。
采用生产用模具、夹具模拟生产工艺,可不用生产用的设备,不按生产节拍生产,生产的零部件由品质部进行检验和试验;
用来确认工装、模具的设计策划结果并根据顾客要求决定是否提交。
制定测量系统分析计划,分析范围应包括控制计划中产品特殊特性的量具测量系统分析;
客户有要求时,测量系统分析必须覆盖控制计划中所有的量具。
依产品特殊特性及小组制定之特性为基础制定设备能力CMK和PPK分析计划,CMK
和PPK>
1.67。
若顾客有指定做法及能力水准时依顾客指定,若顾客无指定则按SPC手册执行。
依APQP计划制定试生产计划。
对于试生产员工制订与其从事其工作资格相适应的培训计划。
组织小组成员及相应部门负责人对本阶段的输岀结果是否符合输入要求进行评定,对本阶段所有工作内容和文件进行检查,对本阶段的工作成果、积累的经验、采用的新技术方法、成本控制状况、阶段输岀是否满足输入要求等内容进行总结并编写阶段总结报告总经理批准以寻求其支持。
第三阶段输岀
过程流程图/过程流程图检查表、场
地平面布置图/场地平面布置图检
查表
产品审核报告
PFMEA/PFME检查表、试生产控制计
划/控制计划检查表
过程审核报告
过程作业指导书
测量系统分析计划
产品检验/试验指导书
初始过程能力分析计划
产品检验报告
试生产
测量系统分析
4第四阶段:
产品和过程确认
组织采用正式生产工装、设备、生产操作工人、场地按一定节拍来进行试生产。
试生产的最小数量由顾客设定,但可超过这个数量,详细参考“满负荷生产确认管理规定”
测量系统评价,参照MSA手册实施。
顾客
初始过程能力研究
试生产确认
PPAP认可
PPAP提交
文件更新
质量策划认定
输岀评审阶段总结
设备能力CMKT价;
初始过程能力PPK研究,参照SZHFC手册实施。
验证试生产的产品符合要求后按照顾客要求等级或依
PPAP程序提交PPAP
生产件批准:
验证试生产的产品是否符合要求,并取得顾客书面认可,如顾客为要求PPAP批准,则以顾客开始批量订货为PPAP批准的默认。
根据生产经验来更新试生产控制计划形成生产控制计划;
范,规范必须包括对批量生产的所有要求。
完善批量生产的技术规
组织小组成员及相应部门负责人对本阶段的输岀结果是否遵循了产品和过程设计进行评价和认定,在首次产品装运之前需要对以下项目:
控制计划、过程指导书、量具和试验装备进行评审,评审应形成书面文件,并通报管理者取得他们的承诺以及在未解决议题上得到其帮助。
质量策划认定由小组作岀产品质量策划总
结认定报告。
组织小组成员对本阶段所有工作内容和文件进行检查,
对本阶段的工作成果、积
生产确认试验:
评价产品是否满足工程标准的试验;
工装的验收和确认;
评价工装是否符合产品/过程的品质要求及生产性要求;
包装评价;
所有的试装运和试验方法都应评价产品承受在正常运输中损伤和在不利环境下受到保护,顾客规定
的包装不排除小组对包装的评价;
累的经验、采用的新技术方法、成本控制状况、阶段输岀是否满足输入要求等内容进行总结并编写阶段总结报告报总经理批准。
经顾客认可和总经理批准的项目
由项目小组组长负责整理相关资料并移交给各相关部门。
包装规程
产品、过程体系评审检查表
第四阶段输岀
小组可行性承诺报告
PFMEA
工艺装备首件认可记录
生产控制计划
全尺寸检验报告
工艺工程部
包装作业指导书
初始过程能力指数PPK
第四阶段评审
测量系统分析报告
质量策划认定报告
厂房,设备,设施布局有效性评估报告
试生产转移报告
5反馈、评定和纠正措施
质量策划不随过程确认和就绪终止,在这一阶段生产控制计划是评价产品和服务的基础,应对计量和计数型数据进行评价。
可结合以下两种方法评价APQP的有效性:
a)
新开发产品利用本次APQP资料时,如采用新的设计/过程(包括设备等)作出对比评价。
b)结合每年一次的过程审核。
APQP有效性评价
通过应用控制图和其他统计技术来识别过程变差,应用分析和纠正措施来减少变差。
要持续地改进产品需要注意变差的原因并寻找解决途径。
供方应积极地提岀基于价值分析、减少变差等建议。
由顾客来决定是否实施或进行协商或进入下一个产品设计水平。
可依SZHFC手册及《纠正和预防措施控制程序》执行。
减少变差1
业务部
为了达到顾客满意,业务部应和顾客合作以进行必要的改动来纠正缺陷。
可依《顾客满意度调查程序》执行
顾客满意1
!
在质量策划的交付和服务阶段,要继续合作以解决问题作不断改善,对于顾客的备件和服务操作也同样考虑其质量、价格和交付。
这一极端所获取的经验为顾客和本公司提供所需知识来建议通过减少过程、库存和质量成本达到降低价格为下一个产品提供合理的零件或系统。
依《持续改进控制程序》执行。
交付和服务
第五阶段输出
过程能力指数CPK
顾客满意调查表
持续改进计划
量产采购订单
5支持文件
5.1潜在失效模式及后果分析控制程序
6质量记录
6.1市场调查与可行性分析报告
6.2产品立项建议书
6.3立项评审表
6.4项目小组名单
6.5APQP计戈卩
6.6设计任务书
6.7设计任务书评审表
6.8产品保证计划
6.9初始材料清单
6.10早期供应商清单
6.11初始过程流程图
6.12产品和过程特殊特性初始清单
6.13培训计划和记录
6.14第一阶段评审输出报告
6.15设计验证报告
6.16技术质量协议
6.17采购合同/订单
6.18原材料样件认可报告
6.19样件控制计划
6.20样件检验规范/条件
6.21样件测试/确认报告
6.22新设备、工装和设施清单
6.23工装和试验设备检查表
6.24第二阶段输出评审报告
6.25过程流程图
6.26过程流程图检查表
6.27场地平面布置图
6.28场地平面布置图检查表
6.29PFMEA(试产)
6.30PFMEA检查表
6.31试生产控制计划
6.32控制计划检查表
6.33产品检验报告
6.34包装规程
6.35产品审核报告
6.36过程审核报告
6.37产品/过程质量体系评审检查表
6.38测量系统分析计划
6.39初始过程能力分析计划
6.40第三阶段输岀评审报告
6.41小组可行性承诺报告
6.42工艺装备首件认可记录
6.43全尺寸检验报告
6.44初始过程能力指数PPK
6.45测量系统分析报告
6.46厂房、设备、设施布局有效性分析报告
6.47PFMEA(批产)
6.48正式生产控制计划
6..49控制检查表
6.50第四阶段评审报告
6.51质量策划认定报告
6.52过程能力指数CPK
6.53持续改进计划
6.54顾客满意调查表
6.55量产采购订单
更改履历
更改日期
更改内容
更改人
备注
2015.07.24
新版发行
张朝平
2017.3.10
IATF16949新版标准升级修订
编制:
审核:
吴玲艳
批准:
谈俊强