总装工艺文件范例Word下载.docx
《总装工艺文件范例Word下载.docx》由会员分享,可在线阅读,更多相关《总装工艺文件范例Word下载.docx(113页珍藏版)》请在冰豆网上搜索。
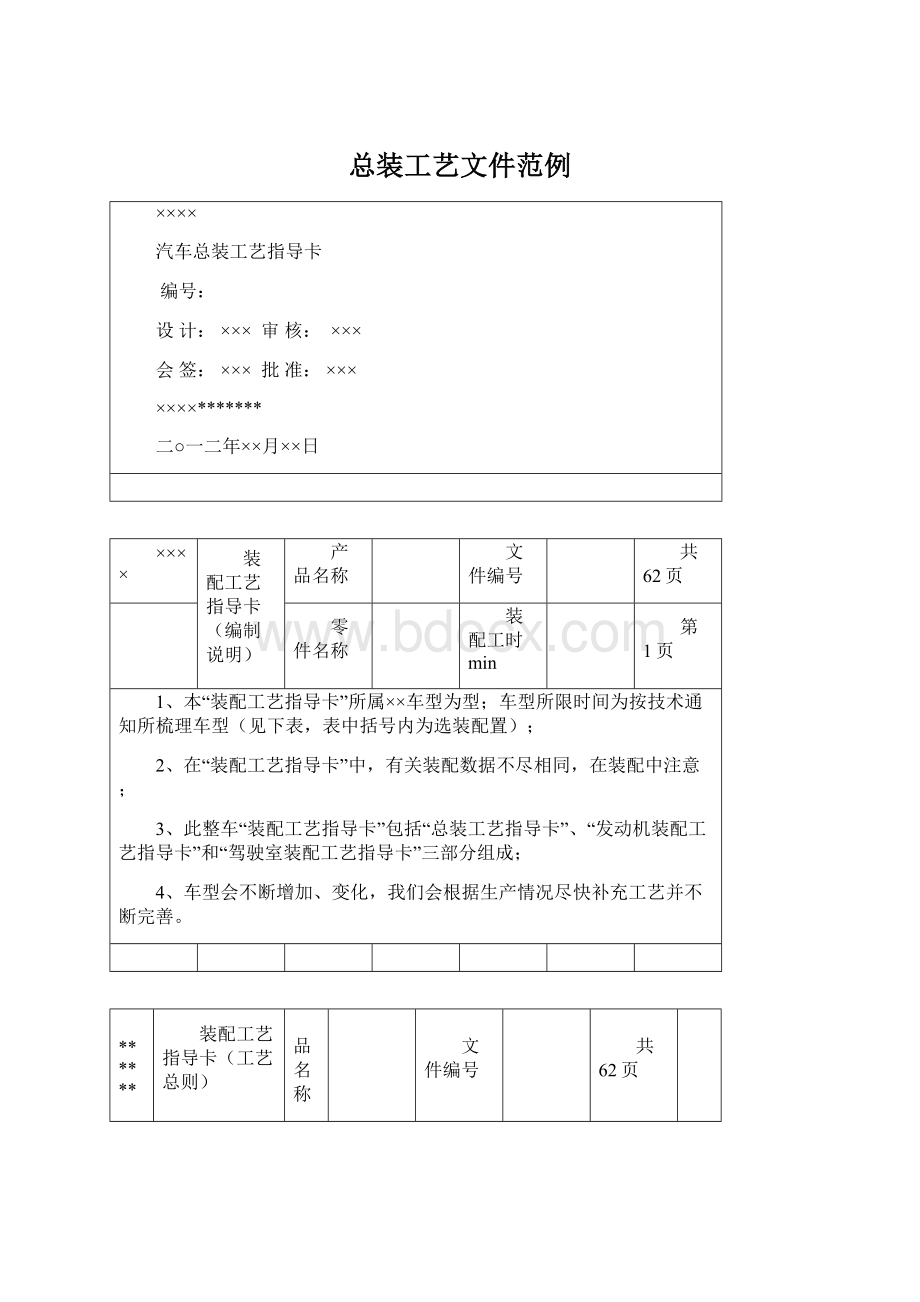
1、进入装配车间的零部件必须通过质量部检验合格后才能投入。
2、装配的零部件,不得有飞边、毛剌、锐角、型砂、锈蚀、铁屑及其它脏物。
3、装配线上的标件、外协件须按技术要求进行表面处理,并且标记完好无损。
未进行表面处理的零件不得装配。
4、所有配合面、密封面不得有损伤;
有黄油嘴的零部件装配后必须加注润滑脂。
5、内饰件(塑料件、橡胶件等非金属件)装配必须使用指定专用工具。
6、燃油系统、动转系统、制动系统、进气系统的零部件必须保持清洁;
油管、柴滤器、接头及油箱、方向机接口、齿轮泵等在装配线上拆包装,并保证装配前的清洁。
7、制动系统的锥接头、铜接头的装配必须使用呆扳手或指定工具;
接头必须紧固后才能装管路的联管螺母。
8、装车后各管路(油管、制动管、水管、软轴、线路)走向整齐美观、不得有扭曲、死角、干涉、破损、泄漏等现象,尽量远离排气热源,过孔处必须安上过线胶圈或其它保护套;
管、线路每400~450mm处须有管卡或扎带固定,扎带固定后剪去尾部,留6~10mm。
9、平键、开口销、卡箍、开槽螺母的装配按规定进行;
装双螺母时,不装弹垫,必须按规定并紧(先将第一颗螺母紧固至规定力矩,然后用呆扳手锁住第一颗螺母,拧紧第二颗螺母至规定力矩)。
10、严格锉刀、二锤、錾子、铰刀、砂布的使用,确需使用须技术主管同意后方可进行,使用后必须清洗干净。
11、货箱、挂钩等焊接时,必须对相邻其它件套上保护装置,以防损伤。
12、检验方案中要求的抽检就是不定期不定量的巡回检查,抽检率≥2%。
关键工序的抽检率在“装配工艺指导卡”中明确。
经常可能出问题的部位按规定加倍检验,具体检验由质量部确定。
13、除已规定的拧紧力矩外,无特殊要求的螺栓按下表所列拧紧力矩(N·
M):
材料
M6
M8
M10
M12
M14
M16
M18
M20
普通碳素钢
5~10
15~25
30~40
50~70
80~110
130~160
170~200
260~320
装配工艺指导卡(工艺流程图)
第3页
装配工艺指导卡
车架
第4页
工序名称
车架上线、布线束
工序号
1
主要设备或工装
行车、专用吊具、安全帽
安全要点
注意车架吊运安全
内容及要求
一、车架上线
1、根椐生产计划选择上线车架型号,检查车架外观质量、漆面。
表面不允许有明显磨损、灰尘。
车架吊耳无松动、锈蚀等缺陷,目测车架左右纵梁不得有明显扭曲、变形,钢板弹簧吊耳不得有明显歪斜,吊耳与车架接合面不得有间隙。
车架上各铆钉铆接应可靠。
2、吊运操作员必须戴安全帽,使用车架专用吊具吊运车架上线。
吊运过程中严禁磕碰和擦伤车架表油漆。
车架下翼面朝上,车架中心线与生产线中心重合,车架下垫上工艺垫木。
两根工艺垫木分别垫在车架前板簧和后板簧的中间位置,并对称于生产线中轴线。
整个吊运过程特别要注意安全。
检查及控制项目
检具及方法
1、车架合格:
无锈蚀、漏漆、变形、吊耳不歪斜、铆钉铆接应可靠。
2、吊具是否安全可靠,操作人员戴安全帽操作。
目测
线束
第5页
二、布车架线束(线束沿着车架下翼面布置)
1、根据车型选择正确型号线束,并检查线束,接头损坏或断线线束不得装配。
2、线束沿纵梁幅面靠下霬面走向并用线卡固定。
每400~450mm固定一次,注意线束各接头位置正确。
线束松紧适度,不得过度弯曲、扭曲,线束不得承重,严禁拉扯,线束装配好后应大致成一条直线,确保线束各分线及插头排布位置正确。
3、线束沿第二横梁下翼面横跨车架并固定。
4、线束过车架纵梁孔和横梁孔处用胶圈保护。
5、线束上无用的接头用黑胶布包扎好。
要求:
线卡安装好后应与车架大梁贴合良好,不能翘起。
三、安装倒车报警器
1、将倒车报警器安装在大梁尾第二横梁处,螺栓配平垫、弹垫,拧紧螺母、弹垫压平。
注意:
倒车报警器喇叭口不应朝上(在车架翻转后)。
2、将倒车报警器线插接在底盘线束上,线路插接到位,工作可靠。
1、线束型号正确,无损坏。
2、线束走向、固定正确,不缠绕、拉扯。
3、线束各接头位置正确。
无用接头用黑胶布包扎。
呆板手
后悬
第6页
悬架系统
2
工序简图:
气扳机(B=16、20)、套筒(S=16、18、24、32)
注意吊装安全,当心板簧、桥掉落伤人
内容及要求
一、安装后悬
1、安装后簧限位块:
穿螺栓,依次戴上平垫、弹垫、螺母,并用气扳机拧紧螺母。
2、根据车型选择正确型号的钢板弹簧,并检查。
板簧卡螺栓、中心螺栓松动的拧紧,凡变形、生锈的板簧不得装配。
左右两边钢板弹簧是同厂家的同一组号的产品。
3、将钢板弹簧吊入装配,同组板簧左右对号入位,不得左右不分或组号不分。
用铜锤将销子敲入后簧前吊耳,黄油嘴一端朝外,敲击时不得敲坏黄油嘴安装孔,穿入限位螺栓并用气扳机紧固。
1、板簧左右、组号是否正确。
2、各部件有无错装、漏装。
3、U型螺栓螺栓长短是否符合要求,抽检:
5%;
呆扳手
第7页
二、安装后桥总成
1、按总装配线质量流转卡要求选用相应规格的后桥总成。
检查后桥总成外观质量,应无明显锈蚀,轮胎螺栓齐全,无严重磕碰痕迹。
2、拧开后桥通气孔的通气塞检查是否有残余的油,如有必须放净。
放尽后用专用橡皮塞密封通气孔。
(此工序在后桥上线前完成)。
3、用行车将后桥总成吊在后钢板弹簧上。
后桥总成上定位孔应与后钢板弹簧上的定位孔对正。
吊装过程中避免碰伤后桥和其它零部件。
4、将垫块放在板簧上下两面,用骑马卡把板簧和后桥连为一体。
对角渐次拧紧螺母,弹垫压平。
安装后确保板弹与车架纵梁平行度误差不大于4mm。
渐次对角拧紧法
前悬
第8页
缺图
呆扳手(13X16)、气扳机(B12、B20)、套筒(S13、S16、S27)
三、安装前钢板弹簧
1、按总装配线质量流转卡选用正确型号的前钢板弹簧总成(见附图及表)。
(包括前簧前销、前簧后销、前钢板吊耳左、前钢板吊耳右、上盖板)检查前钢板弹簧、中心螺栓、板簧卡螺栓是否松动,如松动需紧固后方可装配。
2、将前悬前钢板吊耳安装车架吊耳上(注意区分左右),用销子将前钢板吊耳与车架吊耳连接起,
销端头止动平面与前钢板吊耳止动平面对正,带上弹垫、锁紧螺母、弹垫压平。
3、吊运前钢板弹簧上线,左件装在车架右侧、右件装在车架左侧,且左、右钢板厂家、弧高分组标记应一致。
前钢板弹簧两端对正夹在车架吊耳中,用撬棍将前钢板弹簧双卷耳孔与前簧前吊耳中心孔对齐,将前簧前销按规定方向用铜榔头敲入孔内,锤击方向应沿销轴方向(不得击坏黄油嘴安装孔)。
销端头止动平面与车架前悬前吊耳止动平面对正,带上弹垫、锁紧螺母、弹垫压平。
2、横、直拉杆球头的锥度应与前桥弯臂孔锥度相一致,紧固后无松旷现象;
抽检:
3、U型螺栓规格是否符合要求,拧紧力矩是否符合要求;
5%。
第9页
四、安装前桥总成
1、按总装配线质量流转卡要求选用相应规格型号前桥总成。
2、检查前桥总成外观质量,应无明显锈蚀,轮胎螺栓齐全,无严重磕碰痕迹。
气室环箍连接螺栓锁紧。
3、专用吊具吊运前桥总成上线,使前桥总成定位孔与前簧总成中心螺栓对正。
4、U型螺栓中间开口穿过前钢板弹簧,从下向上将U型螺栓穿入前桥总成工字梁孔内,依次装上上盖板、加平垫,对角渐次拧紧螺母。
车架翻身
第10页
车架翻身、安装车轮、调前束
3
车架翻转机构
车架翻身时生产线两侧不得站人
1、底盘检查
1、检查前二道工序安装部件是否完成。
U型螺栓等螺栓是否紧固、弹垫压平。
2、检查前二道工序的线束布置是否合理、走向是否美观、线束是否捆扎等。
二、车架翻身
1、下降翻转机构并将链条套于底盘两端。
前链不得把直拉杆套入链条中;
注意后链条销插入车架孔内。
2、起升底盘,抽掉车架下方垫木。
底盘升起到1.5m~2.5m高度内,之后缓慢进行翻转。
底盘翻转后下降。
(注意翻转时在底盘翻转区域内不得站人)
3、把专用后桥支架放于传输链上,等待底盘放于支架上后取下翻转机构链条。
4、升起翻转机构链条并回车。
每翻转一次后必须回车到初始位置。
严禁不回车反向使用。
1、翻转机构链条不得把直拉杆套住,车架翻转是方向否为逆时针方向。
2、严禁不回车反向使用翻转机构。
3、U型螺栓力矩,抽检:
车轮
第11页
气扳机(B24)、专用套筒(S38、、S41)
当心车轮掉落伤人
三、安装车轮
1、同一辆车上的主胎和备胎必须是同一厂家生产的型号、规格、偏矩、花纹等完全一致;
并且气已加足。
2、轮胎螺栓用对角渐次拧紧法分两次拧紧达规定力矩。
下图为对角拧紧法。
对安装好的轮胎用白色油漆笔标记。
3、安装备胎,先用备胎升降器把轮胎升到备胎安装支架横梁上再戴上螺母并拧紧。
4、后双轮胎装配时两轮胎的气门嘴不能在同一个方向,应对角装配(如右图)
1、轮胎花纹型号、规格、偏矩、花纹一样.
2、轮胎螺母紧固达力矩要求,并用蓝漆标记。
轮胎螺栓的拧紧力矩是否符合要求;
抽检5%;
第12页
气扳机(B12)、套筒(S16)、2m圈尺
四、调前束
1、松开横拉杆两头的调整锁紧螺母。
转动横拉杆调整其长度。
2、用圈尺测量L1和L2,如图所示调整L2-L1,调整后,锁紧横拉杆两头的调整锁紧螺母。
L1为车轮最前两腹面中心点的距离。
L2为车轮最后的两腹面中心点的距离。
3、用白色油漆笔标记横拉杆锁紧螺母。
横拉杆锁紧卡箍与球头螺杆末端间距》10mm。
1、横拉杆调整螺母是否紧固,打上蓝色标记。
5%
2、转向角是否符合要求;
3、前束值是否符合要求;
圈尺
管路
第13页
布制动管路、安装支架、车架附件
4
呆扳手(22X24)、气扳机(B12)、套筒(S24)
注意板簧、桥吊装安全和支架划伤人
一、布制动管路
1、根据车型选择正确型号的油刹硬管,并检查。
表面划伤、破损、折弯的管路不得装配。
2、沿纵梁内侧幅面布管路。
用呆扳手拧紧管路接头。
管道内清洁无异物、不得堵塞管道。
3、具体管路长度和代码见制动原理图:
制动原理图号1020A-3500001/A
1、管路型号正确,无损坏。
2、线管路走向、固定正确,不缠绕、拉扯。
3、各阀体、接头、部件紧固达力矩要求。
支架
第16页
气扳机(B=10)、套筒(S=13、16、)
注意支架划伤人
二、安装柴油滤清器、备胎升降器
1、选择正确型号的柴油滤清器、其表面不得有损坏、刮花等现象
2、选择正确型号、长度的螺栓、平垫、螺母,螺栓由外向内穿入,用气扳机拧紧螺母。
柴油滤清器安装牢固可靠。
3、选择规定型号的备胎升降器,将螺栓有上往下穿入、并用气扳机拧紧螺母;
三、安装电瓶支架、消声器吊架
1、选择正确型号的电瓶支架和消声器吊架;
2、将支架安装孔对应在车架相应的位置上、螺栓有外向内穿入、依次带上平垫和螺母、并用气扳机拧紧螺母;
3、电瓶支架和消声器吊架安装牢固、且不的歪斜;
4、取搭铁线将其一段用螺母安装在车架的相应位置上;
1、各支架型号选择正确;
位置安装正确。
2、各支架无生锈、变形等缺陷。
3、支架安装端正无歪斜。
4、螺母紧固达到力矩要求。
第17页
四、安装燃油箱支架
1、选用正确型号燃油箱支架并检查。
生锈、变形、开裂、损坏部件不得安装。
2、安装支架时选用规定长度的螺栓,所有螺栓从外向内穿,依次戴上平垫、弹垫、螺母,并用气扳机拧紧螺母。
1、油箱支架型号选择正确,位置安装正确。
2、油箱支架无生锈、变形等缺陷。
3、油箱支架安装端正无歪斜。
减震器
第19页
减震器、方向机
5
呆扳手(S18)、气动扳手、套筒(S18、S21)
注意车架架翻身安全、一号、二号链连接处工作环境安全
一、减震器
1、用专用工具拉长前后减震器,将减震器拉长至安装尺寸。
2、减震器上端戴上垫圈、胶垫再穿过车架上支架孔并戴上胶垫、垫片和螺母。
暂不拧紧。
3、用减振器下销将垫圈、减振胶垫、减振器下端孔、减振胶垫、垫圈穿于减振器下支架孔内再套上弹垫、螺母并用气扳机紧固螺母至弹垫压平。
4、紧固减震器上端螺母。
1、减震器安装是否正确。
2、螺母紧固是否达力矩要求。
力矩扳手
方向机
第20页
气动扳手、套筒(S16、S21、S30)
当心方向机掉落伤人
二、方向机
1、把方向机安放在车架正确位置后穿上螺栓、涂螺纹紧固胶后拧入螺母并用气扳机紧固达力矩要求。
2、将转向器分中后装上转向垂臂,拧紧垂臂螺母达力矩要求。
3、将垂臂与直拉杆连接,开槽螺母紧固达标后穿上并锁好开口销。
4、用白色油漆笔将转向器垂臂螺母、直拉杆上的开口销等用白色油漆笔作上记号。
5、装配完毕,扳动前轮检查方向机左右圈数应相等,轮胎左右转向角应一致。
横直拉杆球头无松旷现象,且轮胎与其它零部件无干涉现象。
6、调转向角:
松开右前轮限位调整螺母,扳动右前轮胎至右转的极限位置。
要求轮胎、各拉杆、板簧等部件之间的最小距离保持为15~50mm。
调整锁紧螺钉顶住车轮轮毂后锁紧调整螺母。
用同样的方法调整左转向角,要求左右转向角应一致。
7、把方向机安装在车架左侧的安装位置。
1、方向机螺栓是否紧固,抽检:
2、垂臂螺栓是否紧固,抽检:
3、直拉杆球头是否紧固,开口销是否符合要求,是否开张到位。
发动机
第22页
吊装发动机、传动轴、散热器
6