双头自动机床设计主轴箱设计.docx
《双头自动机床设计主轴箱设计.docx》由会员分享,可在线阅读,更多相关《双头自动机床设计主轴箱设计.docx(28页珍藏版)》请在冰豆网上搜索。
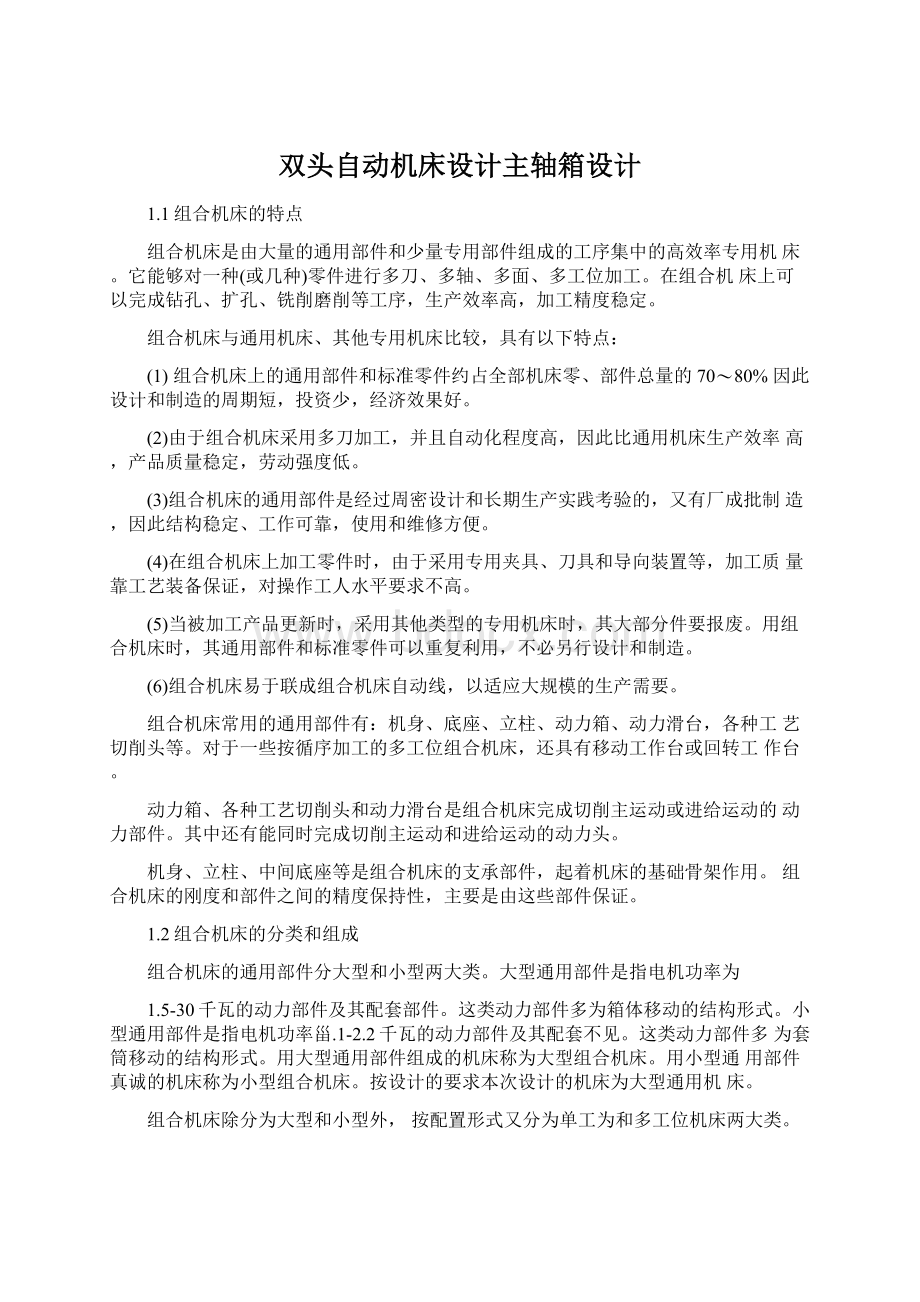
双头自动机床设计主轴箱设计
1.1组合机床的特点
组合机床是由大量的通用部件和少量专用部件组成的工序集中的高效率专用机床。
它能够对一种(或几种)零件进行多刀、多轴、多面、多工位加工。
在组合机床上可以完成钻孔、扩孔、铣削磨削等工序,生产效率高,加工精度稳定。
组合机床与通用机床、其他专用机床比较,具有以下特点:
(1)组合机床上的通用部件和标准零件约占全部机床零、部件总量的70〜80%因此设计和制造的周期短,投资少,经济效果好。
(2)由于组合机床采用多刀加工,并且自动化程度高,因此比通用机床生产效率高,产品质量稳定,劳动强度低。
(3)组合机床的通用部件是经过周密设计和长期生产实践考验的,又有厂成批制造,因此结构稳定、工作可靠,使用和维修方便。
(4)在组合机床上加工零件时,由于采用专用夹具、刀具和导向装置等,加工质量靠工艺装备保证,对操作工人水平要求不高。
(5)当被加工产品更新时,采用其他类型的专用机床时,其大部分件要报废。
用组合机床时,其通用部件和标准零件可以重复利用,不必另行设计和制造。
(6)组合机床易于联成组合机床自动线,以适应大规模的生产需要。
组合机床常用的通用部件有:
机身、底座、立柱、动力箱、动力滑台,各种工艺切削头等。
对于一些按循序加工的多工位组合机床,还具有移动工作台或回转工作台。
动力箱、各种工艺切削头和动力滑台是组合机床完成切削主运动或进给运动的动力部件。
其中还有能同时完成切削主运动和进给运动的动力头。
机身、立柱、中间底座等是组合机床的支承部件,起着机床的基础骨架作用。
组合机床的刚度和部件之间的精度保持性,主要是由这些部件保证。
1.2组合机床的分类和组成
组合机床的通用部件分大型和小型两大类。
大型通用部件是指电机功率为
1.5-30千瓦的动力部件及其配套部件。
这类动力部件多为箱体移动的结构形式。
小型通用部件是指电机功率甾.1-2.2千瓦的动力部件及其配套不见。
这类动力部件多为套筒移动的结构形式。
用大型通用部件组成的机床称为大型组合机床。
用小型通用部件真诚的机床称为小型组合机床。
按设计的要求本次设计的机床为大型通用机床。
组合机床除分为大型和小型外,按配置形式又分为单工为和多工位机床两大类。
单工位机床又有单面、双面、三面和四面几种,多工位机床则有移动工作台式、回转工作台式、中央立柱式和回转鼓轮式等配置型式。
本次设计的机床为单工位双面铣床。
1.3组合机床的方案选择
(1)制定工艺方案要深入现场了解被加工零件的加工特点、精度和技术要求、
定位夹压情况以及生产率的要求等。
确定在组合机床上完成的工艺内容及其加工方法。
这里要确定加工工步数,决定刀具的种类和型式。
(2)机床结构方案的分析和确定根据工艺方案确定机床的型式和总体布局。
在选择机床配置型式时,既要考虑实现工艺方案,保证加工精度,技术要求及生产效率;又要考虑机床操作、维护、修理是否良好;还要注意被加工零件的生产批量,以便使设计的组合机床符合多快好省的要求。
(3)组合机床总体方案这里要确定机床各部件间的相互关系,选择通用部件
的刀具的导向,计算切削用量及机床生产率。
给制机床的总联系尺寸图及加工示意图等。
(4)组合机床的部份方案和施工方案制定组合机床流水线的方案时,与一般
单个的组合机床方案有所不同。
流水线上由于工序的组合不同,机床的型式和数量
都会有较大的变化。
因此,这时应按流水线进行全面考虑,而不应将某一台或几台机床分裂幵来设计。
即使暂时不能全面地进行流水线设计,制定方案时也应综合研究,才能将工序组合得更为合理,更可靠地满足工件的加工要求,用较多的工作,也为进一步发展创造了有利条件。
2组合机床总体描述
2.1组合铣床工艺方案的制定
工艺方案的制定是设计组合铣床最重要的步骤之一。
其制定过程应从以下的几
个方面考虑:
1、加工的工序和加工精度的要求。
2、被加工零件的特点3工件的生
产方式。
等诸多方面综合考虑。
图3-1为拖拉机发动机连杆零件,合件简图。
图2-1发动机连杆零件简图
连杆和
连杆由大、小头和杆身等部分组成。
大头为幵式结构(系直剖式连杆)连杆盖用螺栓,螺母连接。
为减少磨损和便于修理,大头孔和小头孔内分别安装轴瓦和铜套。
连杆身的截面为工字形,可减少重量和减少惯性力又使连杆具有足够的强度和刚度。
连杆头两端面有落差且杆身对称。
大小头侧面设计有定位凸台作为机械加工时的辅助定位基准,便于定位基准的统一。
连杆总的工艺特点是:
外形复杂,不易定位;大、小头有细长的杆身连接,所以弯曲刚性差,易变形;尺寸精度,形状精度和位置精度及表面粗糙度要求很高。
连杆所选的材料为45钢(精选含碳量为0.42%~0.47%),并经调质处理以提高其强度及其抗冲击能力,其硬度为217~287HBS。
其锻件重量为7.5kg。
根据以上的工艺特点下面初步拟订工艺方案。
1、工艺基面的分析及选择
采用以V形铁为主要定位元件的方法。
为提高其定位精度,要把V形铁的角度做大一些。
如图2-2
图3-2工艺基面的选择
2、工序间余量的确定
3、刀具结构的选择
按相关的资料选取端铣刀的形式。
在铣削过程中,端铣刀的直径要大于加工工件的最大宽度,由给定的加工零件图可知最大为Bmax=135mm故端铣刀的直径选取150mm为宜,其齿数按标准选7。
即D=150
Z=7
4、铣削用量的选择
为使组合铣床更好的提高生产效率,便于人工操作,最少的停车损失和使刀具的寿命更长、加工质量更好,合理的选择铣削用量是非常必要的。
表3-3为硬质合金端铣刀的铣削用量。
加工材料
工序
铣削深度
铣削速度
每齿走刀量
钢b52~70
粗
2~4mm
80~120米/分
0.2~0.4
(公斤/毫米J
精
0.5~1mm
100~180米/分
0.05~0.02
表3-3硬质合金端铳刀的铳削用量表
加工工件为45号钢,所以选如下的铣削用量
铣削深度T=3mm
铣削速度V=120m/min
每齿走刀量Sz=毫米/齿
铣削用量的选择应该使选择的刀具充分发挥其性能。
所以就不能选择太低。
考虑到批量生产时也没必要把切削用量选太高,以免增加刀具损耗。
总之要根据加工精度和加工材料,工作条件和技术要求进行分析。
所以以上的选择是可行的。
2.2确定切削力、切削功率根据选定的切削用量(组要指切削速度v及进给量f),确定切削力,作为选择动力部件(滑台)及夹具设计的依据;确定切削扭矩,用以确定主轴及其他传动件(齿轮、传动轴等)的尺寸;确定切削功率,用以选择主传动电机功率。
一铣削力和主切削功率计算
1主切削力Fc
因选取硬质合金端面铣削45,钢工件,由<机床设计手册>得:
Cf――系数
af――铣削接触弧深
af每齿的进给量
dt――铣刀的深度
ap――铣削深度
Z――铣刀齿数
故由上则有:
Fc553.86N
2切削功率:
N切1
2.3组合机床配置型式的选择
对于加工发动机连杆这样的工件,特别适合大、中箱体件的加工。
为尽可能地提高生产率,最理想的是将工件一次性全部加工。
经过和指导老师商量后,我们决定设计四根主轴两端同时进行铣削。
在满足条件的情况下,采用卧式双面铣床是可行的。
在加工连杆过程中,还必须考虑到加工零件特点对配置型式和结构方案的影响。
在加工精度要求影响方面,不仅提高原始精度,提高工件的定位基准和减少夹压变形等措施,还要采用如下措施。
1、采用液压进给系统。
液压系统能够稳定,便捷的操作,提高了加工过程精度和光洁度。
2、采用刚性主轴方案,由于机床导轨间隙及导轨磨损的影响。
在加工过程中就不易产
生振动,并且有足够的刚性保证其径向切削力。
2.4影响总体布置的因素
1、加工精度的影响
当工件的加工精度要求较高时,应采用具有固定夹具的单工位组合机床,加工精度要求较低时,可采用具有移动夹具的多工位组合机床。
此外,还要考虑到不同布置形式的机床所能达到的加工精度。
例如,对于同轴度要求较高的各孔,应采用从同一面对工件进行加工机床布置形式。
2、工件大小、形状和加工部位特点的影响
对于较大的工件,宜采用单工位机床,反之,宜采用多工位机床;对于大直径深孔的工件,宜采用具有刚性主轴结构的立式机床;对于小直径深孔的工件,通常采用专门的深孔加工机床;对于被加工孔的中心线与定位基准垂直的工件,一般采用立式机床。
本原则也可根据机床的使用条件综合考虑。
根据上述原则,对于本章实例,可采用立式机床。
但考虑工件排屑方便,机床空间的高度可矮些,故可采用卧式组合钻床。
3、生产率的影响
零件的生产批量大小是决定采用单工位、多工位或自动线,还是按中小批量生产特点来设计组合机床的重要因素。
有时从工件的外形及轮廓尺寸上看,可采用单工位固定夹具的机床布置形式,但是由于生产率要求很高,就不得不采用多工位的机床布置方案,以便使装卸工件时间与机动时间重合。
被加工的零件的生产批量越大,工序安排一般就越趋于分散,且粗、半精、精加工
应分别在不同的机床上完成。
对于中小批量生产的情况,则要力求减少机床的台数,并应将所有工序尽量集中在一台或少数几台机床上完成,以提高机床的利用率。
2.5组合铣床的总体分析一一三图一"卡
被加工零件工序图是指根据已确定的工艺方案,表示一台组合机床或自动线对加工零件应完成的工艺内容的示意图,它包括加工部位尺寸、精度、表面粗糙度及技术要求等内容。
它不能用产品的零件图代替,而须在原零件图的基础上,突出本机床或自动线的加工内容及必要的说明进行重新绘制。
它是进行组合机床设计的主要依据,也是制造、使用、检验和调整机床的重要技术文件。
其内容应包括以下几个方面:
(1)表示出被加工零件的形状和轮廓尺寸及与本机床设计有关的部位的结构形状和尺寸。
尤其是当需要中间导向套时,应表示出零件内部的筋、壁布置及有关结构的形状和尺寸,以便检查工件、夹具、刀具是否发生干涉。
(2)表示出加工用定位基准、夹紧部位及夹紧方向,以便依此进行夹具的定位支承
(包括辅助定位支承)、限位、夹紧及导向系统的设计。
(3)表示出本道工序加工部位的尺寸、尺寸精度、表面粗糙度、形状位置精度及技
术要求,另外还应表示出本道工序对前道工序提出的要求(主要指定位基准)。
(4)表示出必要的文字说明,如被加工零件的编号、名称、材料、硬度、重量及加工部位的余量等。
(5)绘制时,按一定的比例,细实线表示与本道工序加工无关的部分,粗实线表示被加工部位精度、粗糙度、位置精度、定位面及夹压方向。
(6)凡本道工序保证的尺寸、角度等,应在基尺寸数值上打上方框,并在下面加一横线(粗实线)。
以下为被加工零件图,其材料为45钢并经调质处理,其其硬度为217~287HBS。
图2-4连杆零件图
2.5.2加工示意图
零件加工的工艺方案要通过加工意图才能反映出来。
加工示意图表示:
被加工零件在机床上的加工过程,刀具、辅具的布置状况,工件与夹具、刀具等机床各部件间的相对位置关系,以及机床的工作行程和工作循环等。
因此,它是刀具、辅具、夹具、主轴箱、液压和电气装置设计及通用部件选择的主要原始资料,也是对整台机床布置和技术性能的原始要求,同时还是调整机床、刀具及试车的依据。
其内容包括以下几方面:
(1)应反映机床的加工方法、加工条件及加工过程。
(2)根据加工部位的特点及加工要求,决定刀具的类型、数量、结构、尺寸(直径和长度)。
(3)决定主轴的结构类型、规格尺寸及外伸长度。
(4)选择标准或设计专用的接杆、浮动卡头、导向装置、攻丝靠模装置、刀杆托架等,并决定它们的结构参数及尺寸。
(5)