数控车削零件工艺设计1学位论文Word文档下载推荐.docx
《数控车削零件工艺设计1学位论文Word文档下载推荐.docx》由会员分享,可在线阅读,更多相关《数控车削零件工艺设计1学位论文Word文档下载推荐.docx(23页珍藏版)》请在冰豆网上搜索。
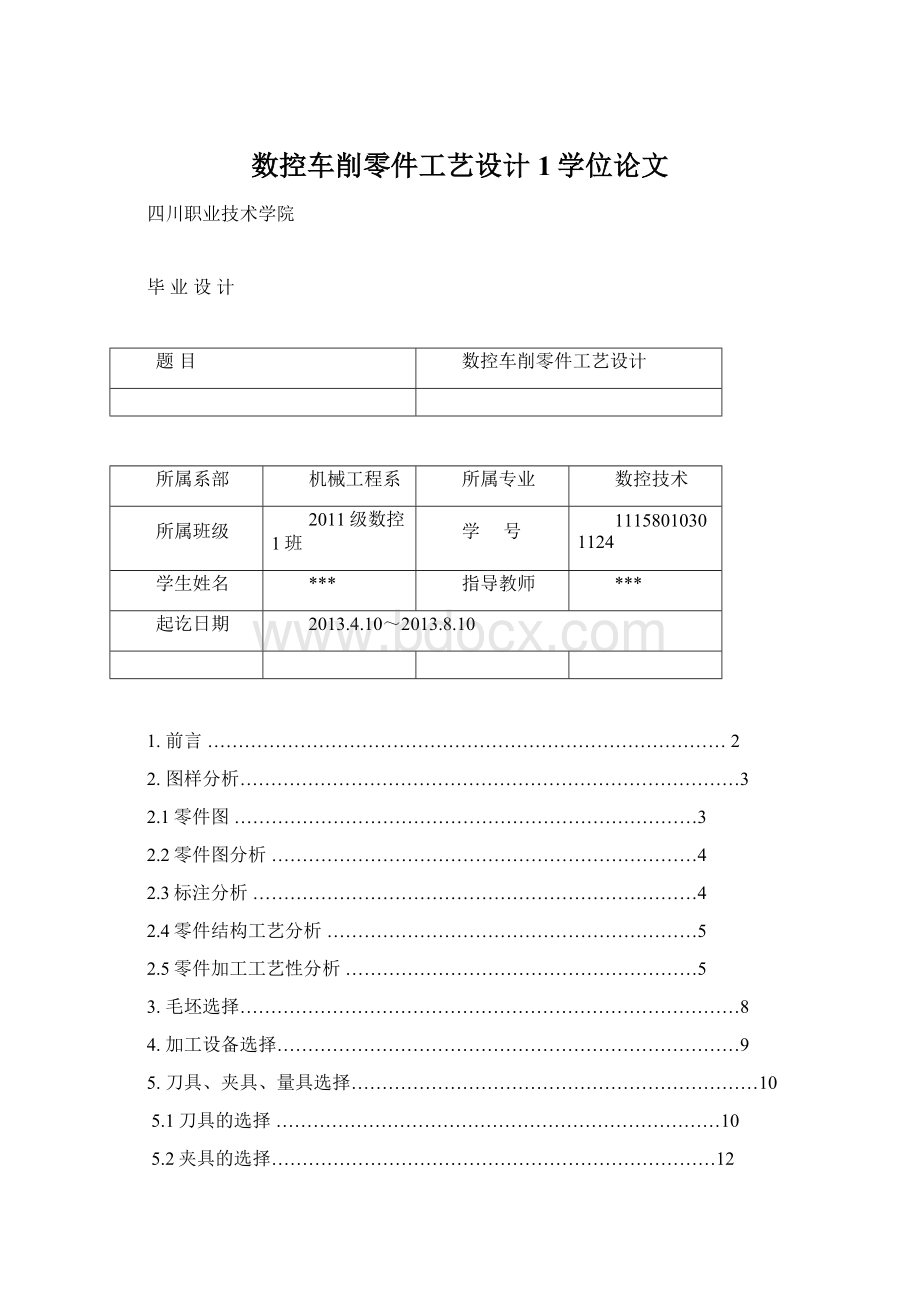
5.3量具的选择………………………………………………………………13
6.加工方案设计…………………………………………………………………13
7.数控加工工艺过程的制定……………………………………………………14
7.1加工基准的选择…………………………………………………………14
A.粗基准的选择B.精基准的选择
7.2装夹方案的选择与确定………………………………………………15
7.3加工方法的选择………………………………………………………16
7.4加工工艺路线设计……………………………………………………18
7.5加工参数的选择、计算………………………………………………19
8.数控加工工艺过程卡…………………………………………………………26
9.数控刀具卡……………………………………………………………………27
10.数控加工工序卡………………………………………………………………28
11.检验卡…………………………………………………………………………29
12.数控加工程序…………………………………………………………………30
13.毕业总结………………………………………………………………………34
14.参考文献………………………………………………………………………35
15.致谢……………………………………………………………………………36
1.前言
当今世界各国制造业广泛采用数控技术,以提高制造能力和水平,以提高对动态市场的适应能力和竞争能力。
大力发展以数控技术为核心的先进制造技术已成为发达国家加速经济发展,提高综合国力的重要途径。
数控技术也是我国制造业发展和综合国力提高的关键技术,尽快加速培养掌握数控技术的应用型人才已成为当务之急。
这次毕业设计是让我们设计出一个零件的全部加工过程。
需要我们对制图软件、编程、数控加工工艺等方面有很好的掌握。
我觉得这对我们来说是一个很好的实践机会,是对我们所学理论课程的一次深入的综合性的链接,也是一次理论联系实际的很好的锻炼机会,也让我们对大学三年的数控学习生涯进行一次总结、补充和沉淀。
在这次的毕设制作工程中,我锻炼了自己独立分析问题、思考问题、解决问题的能力,以及零件的工艺过程卡片的制作过程。
为将来的工作打下牢固的基础。
这本毕业设计,是以加工工艺制作过程为主线和重点,包括了详细的数控工艺分析,刀具选择,完整的数控编程等内容。
几乎涵盖了整个数控专业所涉及的基础知识。
2.图样分析
2.1零件图
2.2零件图分析
该零件图表面由圆锥、圆柱、逆圆弧、外螺纹、槽、内孔等表面组成。
其中多个尺寸有较严的精度和表面粗糙度等要求;
该零件图尺寸标注完整,轮廓描述清楚。
2.2.1左端表面
这一组加工表面包括:
车左端面、内孔1:
5锥度、φ34+0.0250mm内孔、φ22mm内孔、φ560-0.03mm轮廓、φ620-0.04mm轮廓、30°
倒角及1×
45°
倒角,内孔上有个1:
5锥度坐标(26,28)。
2.2.2右端表面
车右端面、R10mm外圆、φ340-0.025mm轮廓、M40×
2-5g/6g的外螺纹表面、φ37mm退刀槽、1:
5锥度及倒角,在R10与1:
5锥度处有一个节点坐标是(60.8,61.42),R10与φ37mm退刀槽处有一节点坐标(42,48),在轮廓线上有个1:
5锥度坐标(26,0)。
2.3标注分析
表示φ620-0.04与φ340-0.025、φ560-0.03同轴公差是φ0.03;
表示φ340-0.025、φ560-0.03圆跳动公差是0.025。
2.4零件结构工艺分析
零件结构工艺性的分析,可从零件尺寸和公差的标注,零件的组成要素和零件的整体结构等三方面来阐述。
车削零件加工面的标注尺寸是按照加工顺序标注,避免多尺寸同时保证,由形状简单和易接近的轮廓要素为基准标注尺寸,例如,尺寸28±
0.026以左端面为标注基准,尺寸28±
0.026以轴φ340-0.025mm右端为基准,尺寸25±
0.026以左端面为标注基准,像这样标注则可以避免不必要的尺寸换算。
对零件组成要素的工艺性分析是对组成零件各加工面的的分析,车削零件加工面为左端面,台阶面孔,整体形状比较简单,这些能采用普通和标准刀具进行加工,且刀具易进入退出和顺利通过加工表面.加工面和非加工面明显分开,加工面之间也应明显分开。
车削零件整体结构工艺性这方面主要是:
车削零件整体形状有特别处,不是通用件,但不影响装夹基准,装夹可选用φ70mm毛坯外圆为装夹基准,φ34+0.0250mm孔内壁粗糙度有要求故不可作为装夹基准,通过零件材料的分析,其综合性能较好,便于切削加工。
2.5零件加工工艺性分析
2.5.1技术要求
轴类零件的技术要求主要是支承轴颈和配合轴颈的径向尺寸精度和形位精度,轴向一般要求不高。
轴颈的直径公差等级通常为IT6-IT8,几何形状精度主要是圆度和圆柱度,一般要求限制在直径公差范围之内。
相互位置精度主要是同轴度和圆跳动;
保证配合轴颈对于支承轴颈的同轴度,是轴类零件位置精度的普遍要求之一。
图为特殊零件,径向和轴向公差和表面精度要求较高。
2.5.2定位基准选择
轴类零件外圆表面、内孔、螺纹等表面的同轴度,以及端面对轴中心线的垂直度是其相互位置精度的主要项目,而这些表面的设计基准一般都是轴中心线。
用两中心孔定位符合基准重合原则,并且能够最大限度地在一次装夹中加工出多格外圆表面和端面,因此常用中心孔作为轴加工的定位基准。
当不能采用中心孔时或粗加工是为了提高工作装夹刚性,可采用轴的外圆表面作定位基准,或是以外圆表面和中心孔共同作为定位基准,能承受较大的切削力,但重复定位精度并不太高。
数控车削时,为了能用同一程序重复加工和工件调头加工轴向尺寸的准确性,或为了端面余量均匀,工件轴向需要定位。
采用中心孔定位时,中心孔尺寸及两端中心孔间的距离要保持一致。
以外圆定位时,则应采用三爪自定心卡盘反爪装夹或采用限未支承,以工件端面或台阶儿面作为轴向定位基准。
2.5.3轴类零件的预备加工
车削之前常需要根据情况安排预备加工,内容通常有:
直--毛坯出厂时或在运输、保管过程中,或热处理时常会发生弯曲变形。
过量弯曲变形会造成加工余量不足及装夹不可靠。
因此在车削前需增加校直工序。
切断---用棒料切得所需长度的坯料。
切断可在弓形锯床、圆盘锯床和带锯上进行,也可以在普通车床切断或在冲床上用冲模冲切。
车端面和钻中心孔—对数控车削而言,通常将他们作为预备加工工序安排。
2.5.4热处理工序
铸、锻毛坯在粗前后应根据材质和技术要求安排正火火退火处理,以消除应力,改善组织和切削性能。
性能要求较高的毛坯在粗加工后、精加工前应安排调质处理,以提高零件的综合机械性能;
对于硬度和耐磨性要求不高的零件,调质也常作为最终热处理。
相对运动的表面需在精加工前或后进行表面淬火处理或进行化学热处理,以提高其耐磨性。
2.5.5加工工序的划分一般可按下列方法进行
①刀具集中分序法就是按所用刀具划分工序,用同一把刀具加工完零件上所有可以完成的部位。
再用第二把刀、第三把完成它们可以完成的其它部位。
这样可减少换刀次数,压缩空程时间,减少不必要的定位误差。
②以加工部位分序法对于加工内容很多的零件,可按其结构特点将加工部分分成几个部分,如内形、外形、曲面或平面等。
一般先加工平面、定位面,后加工孔;
先加工简单的几何形状,再加工复杂的几何形状;
先加工精度较低的部位,再加工精度要求较高的部位。
③以粗、精加工分序法对于易发生加工变形的零件,由于粗加工后可能发生的变形而需要进行校形,故一般来说凡要进行粗、精加工的都要将工序分开。
综上所述,在划分工序时,一定要视零件的结构与工艺性,机床的功能,零件数控加工内容的多少,安装次数及本单位生产组织状况灵活掌握。
另建议采用工序集中的原则还是采用工序分散的原则,要根据实际情况来确定,但一定力求合理。
2.5.6在加工时,加工顺序一般应按下列原则进行
顺序的安排应根据零件的结构和毛坯状况,以及定位夹紧的需要来考虑,重点是工件的刚性不被破坏。
①上道工序的加工不能影响下道工序的定位与夹紧,中间穿插有通用机床加工工序的也要综合考虑。
②先进行内形内腔加工序,后进行外形加工工序。
③以相同定位、夹紧方式或同一把刀加工的工序最好连接进行,以减少重复定位次数,换刀次数与挪动压板次数。
④在同一次安装中进行的多道工序,应先安排对工件刚性破坏小的工序。
在数控车床上粗车、半精车分别用一个加工程序控制。
工件调头装夹由程序中的M00或M01指令控制程序暂停,装夹后按“循环启动”继续加工。
2.5.7走刀路线和对刀点选择
走刀路线包括切削加工轨迹,刀具运动到切削起始点、刀具切入、切出并返回切削起始点或对刀点等非切削空行程轨迹。
由于半精加工和精加工的走刀路线是沿其零件轮廓顺序进行的,所以确定走刀路线主要在于规划好粗加工及空行程的走刀路线。
合理确定对刀点,对刀点可以设在被加工零件上,但注意对刀点必须是基准位或已精加工过的部位,有时在第一道工序后对刀点被加工毁坏,会导致第二道工序和之后的对刀点无从查找,因此在第一道工序对刀时注意要在与定位基准有相对固定尺寸关系的地方设立一个相对对刀位置,这样可以根据它们之间的相对位置关系找回原对刀点。
这个相对对对刀位置通常设在机床工作台或夹具上。
3.毛坯的选择
因为零件在数控加工中,由于加工过程自动化使得余量不大,以及装夹问题在毛坯设计时就要考虑好。
并且毛坯的种类以及不同制造方法对零件的质量、加工方法,材料利用率、机械加工劳动量和制造成本等都有很大影响。
因此在选择毛坯时应注意以下因素:
3.1零件材料及其机械性能
当零件的材料选定后,毛坯的类型就大致确定了。
例如,材料是铸铁,就选用铸造毛坯;
材料是钢材,且力学性能要求高时,可选锻件;
当力学性能要求较低时,可以选用型材或铸钢。
3.2零件的形状和尺寸
常见一般用途的钢质阶梯轴零件,如各台阶的直径相差不大,可以选用棒料;
如个台阶直径相差较大,宜用锻件。
尺寸大的零件,因受设备限制一般用自由锻;
中、小型零件可以选用模锻。
形状复杂的钢质零件不宜用自由锻。
3.3生产类型
大量生产应当选用精度和生产率都比较高的毛坯制造方法,用于毛坯制造的昂贵费用可由材料消耗的减少和机械加工费用的降低来弥补,单件小批量生产应采用木模手工造型或自由锻。
具体生产条件
确定毛坯必须结合具体生产条件,如现场毛坯制造的实际水平和能力、外协的可能性等。
有条件时,应积极组织地区专业化生产,统一供应毛坯,有利于保证毛坯质量和提高经济效益。
3.4充分考虑利用新工艺、新技术和新材料的可能性
为了节约材料和能源,随着毛坯制造向专业化生产发展,目前毛坯制造方面的新工艺,新技术和新材料的发展很快,例如,精铸、精锻、冷轧、冷挤压、粉末冶金和工程塑料等在机械制造中的应用日益增加。
应用这些方法后,可大大减少机械加工质量。
有时甚至可不再进行机械加工,其经济效益明显提高。
综上选择45钢为毛坯,在锯床上按110mm长度下料,直径为70mm。
4.加工设备的选择
零件的加工精度和生产效率在很大程度上是由机床的使用性能决定的,在设计工艺规程时,主要是选机床种类及型号,选择时参照相关手册,产品样品,遵循以下原则:
1.机床的主要规格尺寸应与零件的外形轮廓尺寸相适应;
2.机床的精度应与工序要求的精度相适应;
3.机床生产率应与零件的生产类型相适应。
当在车间没有相适应的机床设备时,就需要对已有的机床进行设备的改装,使其成为专用机床。
在此,应根据具体要加工的零件的要求提出设计任务书,包括:
一些必要参数、精度要求,产品要求,产品质量、经济效益等。
我们学校设备型号及技术规格如下:
①CA6140普通车床
主轴转速范围正转10—1400转/分、24级
反转14—1580转/分、12级
进给量范围纵向0.028—6.33毫米/转,共64级
横向0.014—3.16毫米/转,共64级
螺纹加工范围米制螺纹P=1-192MM,44种
英制螺纹A=24牙/IN,37种
模数制螺纹M=0.25—48MM,39种
径直制螺纹DP=1—96牙/IN,37种
主电动机7.5KW,1450转/分
②CXA6136数控车床
FANUCSeriesOiMate-TC数控系统
最大回转直径500mm
主轴转速30~2000r/min(无级调速)
X、Z行程260×
1100mm
主轴电动机功率7.5KW
综上该零件的复杂程度不高,但要求精度较高,可在数控车上完成。
5.刀具、夹具、量具选择
5.1刀具的选择
刀具寿命与切削用量有密切关系。
在制定切削用量时,应首先选择合理的刀具寿命,而合理的刀具寿命则应根据优化的目标而定。
一般分最高生产率刀具寿命和最低成本刀具寿命两种,前者根据单件工时最少的目标确定,后者根据工序成本最低的目标确定。
选择刀具寿命时可考虑如下几点根据刀具复杂程度、制造和磨刀成本来选择。
复杂和精度高的刀具寿命应选得比单刃刀具高些。
对于机夹可转位刀具,由于换刀时间短,为了充分发挥其切削性能,提高生产效率,刀具寿命可选得低些,一般取15-30min。
对于装刀、换刀和调刀比较复杂的多刀机床、组合机床与自动化加工刀具,刀具寿命应选得高些,尤应保证刀具可靠性。
车间内某一工序的生产率限制了整个车间的生产率的提高时,该工序的刀具寿命要选得低些当某工序单位时间内所分担到的全厂开支M较大时,刀具寿命也应选得低些。
大件精加工时,为保证至少完成一次走刀,避免切削时中途换刀,刀具寿命应按零件精度和表面粗糙度来确定。
与普通机床加工方法相比,数控加工对刀具提出了更高的要求,不仅需要冈牲好、精度高,而且要求尺寸稳定,耐用度高,断和排性能坛同时要求安装调整方便,这样来满足数控机床高效率的要求。
数控机床上所选用的刀具常采用适应高速切削的刀具材料(如高速钢、超细粒度硬质合金)并使用可转位刀片。
外圆车刀
内孔车
5.2夹具的选择
合理地选择夹具,能够提高定位基准精度从而保证加工精度,提高生产率,减轻工人的劳动强度.应考虑:
A、是否可用机床备有的各种通用夹具和附件。
B、生产类型。
C、夹具应尽量敞开。
D、自动换刀具和换工作台时不能与夹具或工件发生干涉。
单件小批量生产时,应优先选择通用夹具,如各种通用卡盘、平口虎钳、分度头、回转工作台等,也可使用组合夹具。
中批生产可以选用通用夹具、专用夹具、可调夹具、组合夹具。
大批大量生产应尽量使用高产效率的专用夹具,如气动、液动、电动夹具。
此外夹具的精度应能满足加工精度的要求。
由于是单件生产在加工左右端面及左端面各孔时,可用三爪卡盘夹住。
5.3量具的选择
选择量具的基本原则
1、根据量具的极限误差选择量具;
2、在保证测量精度的前提下,应选择比较经济的量具;
3、根据被测件的大小、形状、公差、质量、硬度、刚性和表面粗糙度等选择相应的量具;
4、根据被测件所处的状态及其测量条件,选择相应的量具;
5、根据工件的加工方法、批量和数量选择相应的量具。
结合零件图、原则选游标卡尺、螺纹千分尺、内径千分尺、螺旋千分尺。
6.加工方案设计
零件上比较精密表面的加工,常常是通过粗加工、半精加工和精加工逐步达到的。
对这些表面仅仅根据质量要求选择相应的最终加工方法是不够的,还应正确地确定从毛坯到最终成形的加工方案。
毛坯左端,车端面,钻中心孔,钻φ20mm孔,车左端内孔φ22mm、1:
5锥度、φ34+0.0250mm,车外圆轮廓φ560-0.03mm、φ620-0.04mm,毛坯右端,车端面,钻中心孔、加工锥度、φ340-0.025mm、螺纹M40×
2mm、φ37mm退刀槽、圆R10、1:
5锥度、φ560-0.03mm。
方案一:
预备加工---车右端外圆至φ65mm---调头装夹右端---车左端面---钻中心孔---钻φ20mm孔---粗车内孔---精车内孔---粗车左端轮廓---精车端端轮廓---工件调头包铜皮装夹---车右端面---钻中心孔---加顶针---粗车右端轮廓---精车右端轮廓---切退刀槽---车螺纹。
方案二:
预备加工---车右端面---钻中心孔---加顶针---粗车右端轮廓---精车右端轮廓---切退刀槽---粗车螺纹---精车螺纹---工件调头装夹φ34mm---车左端面---钻中心孔---钻φ20mm孔---粗车内孔---精车内孔---粗车左端轮廓---精车端端轮廓。
方案三:
预备加工---车右端面---钻中心孔---加顶针---粗车右端轮廓---精车右端轮廓---工件调头装夹---车左端面---钻中心孔---钻φ20mm孔---粗车内孔---精车内孔---粗车左端轮廓---精车端端轮廓---工件调头包铜皮装夹---切退刀槽---粗车螺纹---精车螺纹。
7.数控加工工艺过程的制定
7.1加工基准的选择
A.粗基准的选择
粗基准的选择主要影响不加工与加工表面之间的相互位置精度,以及加工表面的余量分配。
粗基准的选择应遵守的原则如下:
1)非加工表面原则为了保证加工面与非加工表面之间的位置要求,应选非加工面为粗基准。
2)加工余量最小原则以余量最小的表面作为粗基准,以保证各加工表面有足够的加工余量。
3)重要表面原则为保证重要表面的加工余量均匀,因选择重要加工面作为粗基准。
4)不重复使用原则粗基准未经加工,表面比较粗糙且精度低,二次安装时,其在机床上(或夹具中)的实际位置可能与第一次安装时不一样,从而产生定位误差,导致相应加工表面出现较大的位置误差。
因此,粗基准一般不应重复使用。
5)便于工件装夹原则作为粗基准的表面,应尽量平整光滑,没有飞边、冒口、浇口或其他缺陷,以便使工件定位准确、夹紧可靠。
综上原则应选右端为粗基准。
B.精基准的选择
精基准的选择应从保证零件的加工精度,特别是加工表面的相互位置精度来考虑,同时也必须尽量使装夹方便,夹具结构简单可靠。
精基准的选择应遵循如下原则:
1)“基准重合”的原则即应尽量能够比较容易地获得加工表面对其设计基准的相对位置精度,可以避免由定位基准和设计基准不重合而引起的定位误差。
2)“基准统一”的原则即可保证各加工表面间的互为位置精度,避免或减少因基准转换而引起的误差,也简化了夹具的设计与制造工作,降低了成本,缩短了生产准备周期。
注:
基准重合和基准统一原则是选择基准的两个重要原则,但生产实际中有时会遇到两者互相矛盾的情况。
此时,若采用统一定位基准能够保证加工表面的尺寸精度,则应遵循基准统一原则;
若不能保证尺寸精度,则应遵循基准重合原则,以免使工序尺寸的实际公差值减少,增加加工难度。
3)“互为基准”的原则为使各加工表面之间具有较高的位置精度,或为使加工表面具有均匀的加工余量,可采取两个加工表面互为基准反复加工的方法。
4)“自为基准”的原则有些精加工或光整加工工序要求加工余量小而均匀,因此选择加工表面本身作为定位基准。
综上原则应选左端为精基准。
7.2装夹方案的选择与确定
为了工件不致于在切削力的作用下发生位移,使其在加工过程始终保持正确的位置,需将工件压紧夹牢。
合理的选择夹紧方式十分重要,工件的装夹不仅影响加工质量,而且对生产率,加工成本及操作安全都有直接影响。
7.2.1数控车床常用的装夹方式
1)在三爪自定心卡盘上装夹。
三爪自定心卡盘的三个卡爪是同步运动的,能自动定心,一般不需要找正。
该卡盘装夹工件方便、省时,但夹紧力小,适用于装夹外形规则的中、小型工件。
2)在两顶尖之间装夹。
对于尺寸较大或加工工序较多的轴类工件,为了保证每次装夹时的装夹精度,可用两顶尖装夹。
该装夹方式适用于多序加工或精加工。
3)用卡盘和顶尖装夹。
当车削质量较大的工件时要一段用卡盘夹住,另一段用后顶尖支撑。
这种方式比较安全,能承受较大的切削力,安装刚性好,轴向定位准确,应用较广泛。
4)用心轴装夹。
当装夹面为螺纹时再做个与之配合的螺纹进行装夹,叫心轴装夹。
这种方式比较安全,能承受较大的切削力,安装刚性好,轴向定位准确。
7.2.2确定合理的装夹方式
装夹方法:
先用三爪自定心卡盘毛坯左端,加工右端至φ60mm,调头装夹右端,加工左端达到工件精度要求;
再工件调头装夹,用三爪自定心卡盘夹紧左端φ56mm,再加工右端达到工件精度要求。
7.3加工方法的选择
加工方法的选择的原则是保证加工质量和生产率与经济性。
为了正确选择加工方法,应了解各种加工方法的特点和掌握加工经济精度以及经济粗糙第的概念。
在选择加工方法时,一般是根据经验或查表来确定,再根据实际不同情况或工艺实验进行修改。
在查表时,满足同样要求的加工方法有很多种,所以选择加工方法时要考虑以下因素:
(1)选择相应能获得经济精度的加工方法。
(2)工件材料的性质。
(3)工件的结构形状和尺寸大小。
(4)结合生产内型考虑生产率与经济性。
(5)现有生产条件。
为了正确选择加工方法,应了解各种加工方法的特点和掌握加工经济精度及经济粗糙度的概念。
经济精度是指在正常的加工条件下所能保证的经济精度
加工精度是指在正常的加工条件下所能保证的加工精度
加工过程中,影响精度的因素很多。
每种加工方法在工同的工作条件下所
达到的精度是不同的。
例如,在一定的设备条件下,操作精细、选择较低
进给量和切削深度,就能获得较高的加工精度和较细的表面粗糙度。
但是这必然会使生产率降低,生产成本增加。
反之,提高了生产率,虽然成本降低,但会增大加工误差,降低加工精度。
7.3.1零件加工如下:
①左右两端面:
表面粗糙值Ra3.2且长度方向无尺寸公差要求,所以采用在粗车即可以达到要求。
②左端表面(φ560-0.03mm):
表面粗糙值Ra1.6,公差等级为IT7,粗车--半精车---精车即可达到要求。
③左端表面(φ620-0.04mm):
表面粗糙值Ra1.6,公差等级为IT7~IT8,粗车—半精车----精车即可达到要求。
④φ34+0.0250mm孔:
表面粗糙值Ra1.6