最新课件文档格式.docx
《最新课件文档格式.docx》由会员分享,可在线阅读,更多相关《最新课件文档格式.docx(21页珍藏版)》请在冰豆网上搜索。
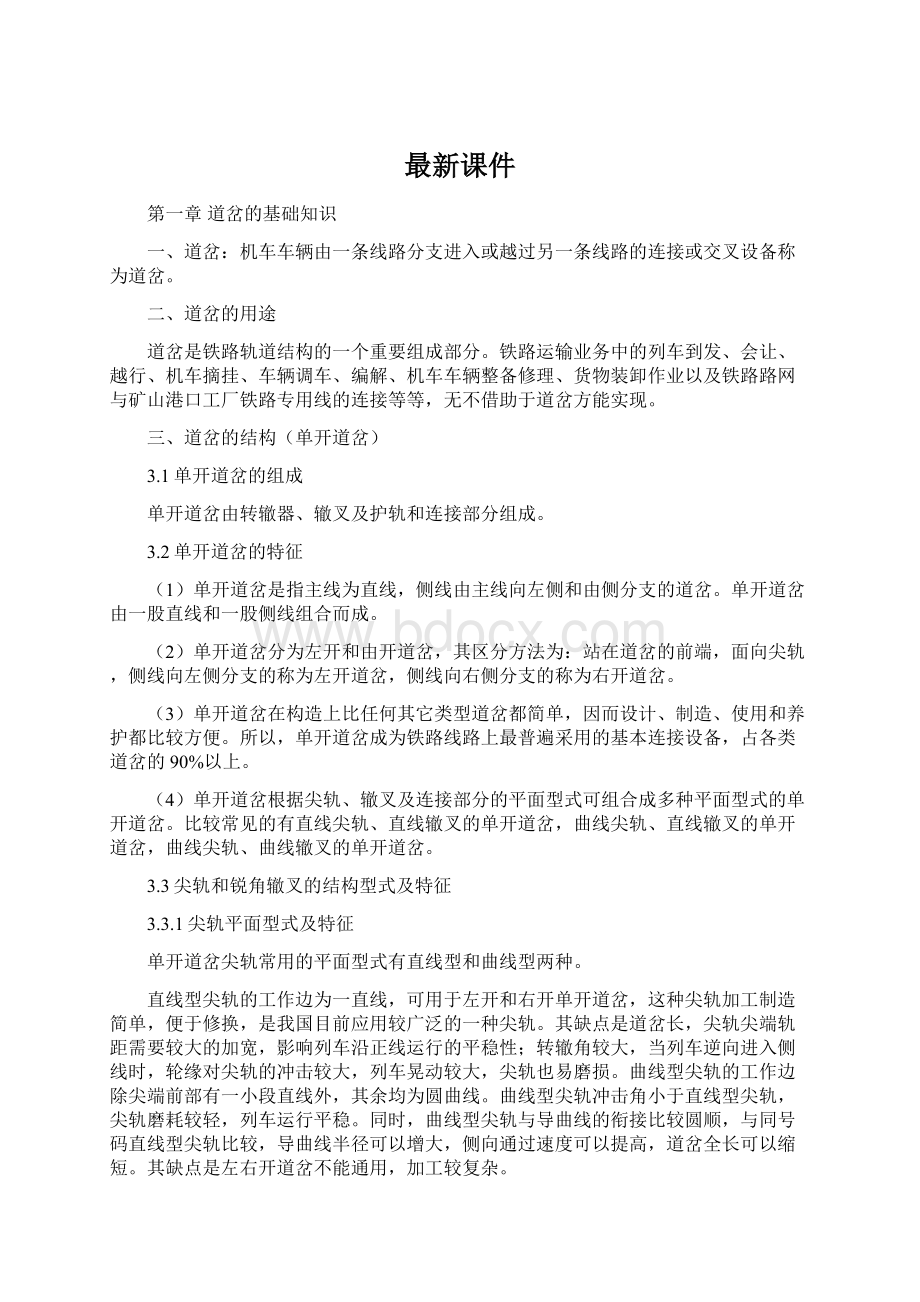
3.3.3AT轨的主要优点
⑴取消了标准钢轨尖轨6mm抬高量,消除了列车过岔的垂向不平顺,可提高道岔直股过岔速度。
⑵AT轨整体性强,刚度大,在使用中不易出现拱腰现象,养护维修量小。
⑶AT轨下设24mm高的台板,可将基本轨轨底扣住,增加了基本轨的稳定性和道岔的整体性。
⑷AT轨下的台板较高,可减少沙、雪的影响,提高行车的安全性。
3.3.4尖轨与基本轨的接触型式及特征
⑴贴尖式尖轨:
尖轨与不加工轨颚的基本轨相贴形式。
采用这种型式尖轨的道岔加工简单,备品方便。
我国“75”道岔均采用这种贴尖式尖轨。
⑵藏尖式尖轨:
通过切削基本轨轨颚,使尖轨尖端藏在基本轨工作边内,以保护尖端不被车轮轧伤,并使尖轨在动载荷作用下保持良好的竖向稳定性。
通常采用的藏尖面斜度有1:
3和1:
4两种。
这种型式要求基本轨和尖轨接触面良好,加工要求严格。
我国“92”型AT道岔和其它新型道岔均用这种藏尖式尖轨
3.3.5尖轨跟端结构型式及特征
⑴间隔铁式活结头
在尖轨跟端设置间隔铁,利用间隔铁保持基本轨与尖轨、导轨的间隔尺寸,并在基本轨外侧、尖轨工作边一侧设置轨撑(外轨撑、内轨撑)及轨下设辙跟垫板连接,以保持辙跟不爬行、不跳动。
在跟部设双头螺栓保持间隔铁与夹板的距离,以使尖轨扳动灵活。
但尖轨跟端不能固定,形成活接头,稳定性较差,容易发生病害。
⑵可弯式尖轨
尖轨跟部采用普通钢轨接头型式,用间隔铁或支距垫板保持与基本轨的距离,并用轨撑或扣件保持跟部位置和稳定性。
如为间隔铁式可弯尖轨,为减轻扳动力,在间隔铁前将尖轨轨底一侧或两侧切削掉一部分(长度一般为1-2m),成为柔性点,尖轨便可围绕该点转动和弹性弯曲。
近几年的新型道岔(如提速道岔),为适应跨区间超长无缝线路的要求,在尖轨跟端附近设置限位器,以限制尖轨与基本轨的相对纵向位移。
可弯式尖轨结构简单,坚固,易于现场维护保养。
3.3.6尖轨的降低值
尖轨的降低值直接关系到行车安全和尖轨的使用寿命。
我国尖轨各部位采用以下的降低值。
根据尖轨轨顶面的形状,可以看出,尖轨轨头宽50mm以后部位完全承受车轮的荷载;
尖轨轨头宽20mm以前完全由基本轨承受车轮的荷载;
尖轨轨头宽20~50mm部分为承受车轮荷载的过渡段。
⑴尖轨尖端降低值:
尖轨尖端的降低值不应大于车轮轮缘高度25mm,以免车轮逆向进岔时爬上尖轨。
另外还应考虑在车轮轮缘最大磨耗18mm时,基本轨轨顶也有一定垂直磨耗时也不会轧伤尖轨。
经过多年实践证明,尖轨尖端降低值采用23mm是安全可靠的。
⑵尖轨轨头宽20mm处降低值
在尖轨轨头宽20mm处,基本轨与尖轨共同承受车轮的垂直载荷。
因车轮踏面有1:
20和1:
10的坡度,因此在此断面处尖轨应有一定的降低值。
我国道岔规定该位置的降低值为2mm。
⑶尖轨轨顶降低始点的尖轨轨头宽度
为了保证行车安全,当具有最小轮背距和轮缘极限磨耗的轮对紧贴一侧基本轨,另一侧车轮踏面外侧圆弧相接触的尖轨轨顶宽度为50mm,该位置确定为轨顶降低始点。
⑷尖轨轨头宽5mm处降低值
为简化尖轨加工,尖轨尖端到尖轨轨头宽20mm断面处采用一个坡度,因此,计算轨头宽5mm断面处的降低值为14mm。
⑸为提高尖轨的使用寿命,避免列车逆向进岔时车轮对尖轨前部小断面的撞击,在尖轨设计时加大20mm断面以前的降低值。
如“92”型道岔和新型道岔将5mm断面处的降低值设计为18mm,20mm断面处的降低值设计为4mm。
第二章产品的加工工艺
一.轨件产品各工序工艺
1、钢轨件的下料
1.1钢轨下料的操作要求
(1)将所需的钢轨摆放在工作台上,检查钢轨的表面质量。
(2)核对工件轨型、生产计划、配料单、产品图纸,准确无误才能进行下料。
(3)测量摆放在料台上所有钢轨的实际长度,并作出标记,与当月生产计划及配料单结合,实行配料下料,以降低材料消耗。
(4)根据配料方案下出所需长度(全长淬火钢轨根据工艺要求增加淬火缩尺量),按下列步骤操作:
a、用定尺钳把卷尺定在长度数值上;
b、将锯口样板卡在卷尺零点上;
c、将手钳口对准钢轨下料起点,用5kg拉力把卷尺拉直;
d、按锯口样板位置用划针在轨顶面上划两条锯口线;
e、在每条锯口线上打两个样冲眼,并作出标记。
(5)完成以上步骤后在轨腰部位用油漆将长度及名称写上。
(6)下料时,两根钢轨之间必须留出锯口宽度的尺寸。
(7)下料后自检、互检、专检下料长度,标注长度尺寸。
(8)下料时,应注意钢轨原有螺栓孔是否需要保留,需要保留时,原螺栓孔与新钻螺栓孔或轨端距离不得小于孔径的二倍。
1.2钢轨下料的质量要求
(1)钢轨下料公差按图纸及工艺要求确定。
(2)样冲眼的直径为1mm。
(3)锯切宽度线应垂直于钢轨中心线,样冲眼打在锯切宽度线上。
2.钢轨件的锯切
2.1锯切操作内容
锯切必须按下料尺寸锯切,锯切后锯口必须留有大于1/2的样冲眼直径
2.2锯切的质量要求
(1)锯切应垂直于钢轨轴线,钢轨端部面应与钢轨轴心线的垂直度偏差不得超过1mm。
(2)各种钢轨件长度偏差应执行TB412《标准轨距铁路道岔技术条件》或其他指明技术条件及产品图纸的规定
(3)由于全长淬火的钢轨件会产生收缩,根据淬火钢轨的收缩率,钢轨件的下料偏差按照《钢轨件淬火下料偏差》执行。
(4)锯切后的钢轨应按型号、规格、材质分类堆放整齐,并做好标识。
3、钢轨件的钻孔
批量生产的钢轨件应用钻孔模板钻孔,非批量生产的钢轨件可以先划出螺栓孔线,然后按线钻孔。
3.1钻孔操作要求
(1)核对工件轨型、生产计划、配料单、产品图纸,准确无误后才能进行钻孔。
使用模板钻孔时,应预先检查所用样板是否正确。
(2)钻孔时钢轨件摆放应符合要求,轨头下加垫板,以免钻孔出现歪斜。
其垫板厚度由钢轨类型确定。
钢轨类型
43
50
60
75
50AT
60AT
垫板厚度
22
31
40
39
20
26
(3)带有补强板的“75”型道岔的尖轨,补强板与尖轨同时进行钻孔,注意补强板上下方向应与钢轨吻合,补强板端头与钢轨端头平齐,补强板外侧平面与钢轨轨腰中心线平齐。
(4)钻孔完成后,应检查是否有漏孔或未钻通的孔。
(5)带有补强板的尖轨应先用一条螺栓将补强板固定在钢轨上,再用起重设备吊下胎型。
(6)钢轨件的所有螺栓孔应进行到能棱处理。
3.2钻孔的质量要求
(1)螺栓孔径偏差除图纸注明外,均为+1mm。
(2)螺栓孔中心位置上下偏差为1.5mm。
(3)各接头螺栓孔中心至轨端距离偏差为±
1mm。
(4)相邻螺栓孔中心距离为±
(5)两最远螺栓孔中心距偏差:
中心距小于1.5m时,偏差为1.0mm,中心距大于或等于1.5mm时,偏差(基本轨、尖轨、护轨)为±
2mm或1.5mm(长心轨、短心轨、翼轨、邦轨、扶轨、活动心轨等)。
4.钢轨件的切削
4.1钢轨件的切削方式和种类
钢轨件的切削方式主要有刨切铣削两种。
钢轨件的切削主要包括轨头和轨底的切削,也有的钢轨需要进行轨腰的切削。
钢轨件的切削按切削进刀方向与钢轨横轴的关系分为垂直与水平切削两类。
水平切削:
进刀方向与钢轨横轴平行。
垂直切削:
进刀方向与钢轨横轴垂直。
4.2基本轨的切削
当道岔的尖轨是藏尖式尖轨时,需要对基本轨的轨头下颚进行切削加工。
即在基本轨顶面以下16mm处进行水平方向的斜切削,斜度与尖轨非工作边斜度一致(1:
3或1:
4)。
一般采用铣床铣削加工。
4.3尖轨的切削
4.3.1尖轨的主要切削部位
尖轨一般要进行轨头及轨底部位的切削。
轨头非工作边水平切削,轨头工作边水平切削,轨头垂直切削,轨底水平切削,轨底垂直切削(只限于普通断面尖轨)。
4.3.2尖轨切削的目的
⑴结构的需要,即为了使尖轨前端呈尖形,能够引导车轮从基本轨过渡到尖轨,或从尖轨过渡到基本轨,并能够保证尖轨与基本轨的密贴,尖轨应进行轨头水平和轨底水平或垂直切削。
⑵为保证尖轨尖端部分不被车轮轧伤和不过多地承受车轮垂直载荷,使尖轨轨顶面(轨头宽50mm以前)较基本轨低,应进行尖轨轨顶面的垂直切削。
4.3.3尖轨轨头非工作边水平切削
尖轨轨头非工作边水平切削,与基本轨轨头工作边侧面的斜度一致(一般为1:
4),以保证尖轨与基本轨的密贴。
切削深度一般在低于基本轨轨头侧面下边缘以下3mm处。
位块靠严。
4.3.4尖轨轨头工作边水平切削
尖轨轨头工作边水平切削坡度一般采用1:
5或1:
4。
4.3.5尖轨轨顶面垂直切削
尖轨轨顶面垂直切削的刀具应具有与尖轨轨顶面相同的轮廓线。
尖轨尖端应在基本轨顶面以下有足够的距离,以保证当车轮轮缘有最大垂直磨耗及基本轨顶面有最大垂直磨耗的最不利情况下,车轮也不会轧伤尖轨。
但尖轨尖端也应不低于基本轨顶面以下25mm,即不得使尖轨尖端位于轮缘下部,以免尖轨与基本轨不密贴时,发生车轮轮缘(逆向进岔)爬上尖轨。
4.3.6尖轨轨底水平切削
尖轨轨底水平切削一般只限于非工作边一侧,切削面垂直于尖轨轨底。
尖轨轨底水平切削一般按直线进行,有时为了增加尖轨与基本轨轨底的接触面积,轨底水平切削按折线进行,折点一般在尖轨顶弯处。
4.3.7尖轨轨底垂直刨切
普通钢轨断面尖轨在水平切削完成后,还要进行轨底水平切削,这样才能使尖轨完全紧贴在基本轨轨底上。
4.3.8尖轨铣削
传统上尖轨采用刨切的加工方法,上述介绍的尖轨加工就是尖轨刨切的工艺内容。
在我国,用铣削的方法加工钢轨是近年出现的一种新工艺,主要是用数控铣床进行各种尖轨的轨头工作边、非工作边、轨顶面的加工,用龙门铣床进行各种直线尖轨的轨头工作边和非工作边的加工。
用铣床加工尖轨需要制做专用的成型铣刀。
采用数控铣床加工尖轨,一次装卡后就可以进行轨头工作边、非工作边、轨顶面的铣削,既提高了产品质量,也提高了生产效率,得到了广泛的应用。
4.4各种钢轨件切削质量要求
各种钢轨件切削尺寸公差,按产品要求执行有关的技术标准。
道岔生产制造一般执行TB412规定。
5、钢轨件的淬火与时效
钢轨件淬火的主要目的是改变钢轨表层金属的金相组织,提高硬度,从而增强钢轨的耐磨性,延长使用寿命。
5.1中频淬火的加热原理
中频淬火是利用感应器线圈在中频(1-10kHz)交流电作用下,在线圈内外产生交变磁场,将工件放入感应器线圈内,工件就会产生与感应器电流频率相等、方向相反的感应电流,这个电流自成回路称之为“涡流”。
它能使电能变成热能,使工件变热。
“涡流”主要集中在工件表面称之为“集肤效应”,利用这个原理可以使工件表面层快速加热到淬火温度,并立即快速冷却,使工件表面层达到淬火的目的。
5.2淬火钢轨件时效的目的
由于钢轨件淬火残余应力的影响,致使道岔钢轨件尺寸及形状的稳定性不好,尖轨在运营过程中有时发生翘尖现象;
另外在钢轨件淬火的顶弯调直过程中,也是由于残余应力的影响,钢轨件会产生折断现象,既给工人的人身安全造成威胁,也造成经济损失。
为了降低残余应力或改变应力的分布,需要对道岔钢轨件进行淬火后的时效处理。
5.3钢轨件时效处理方法
钢轨件的时效处理方法有自然时效和振动时效两种方法。
自然时效就是钢轨件淬火后,在不施加任何外力的条件下,在自然环境放置一段时间,使钢轨件得到自然充分的冷却,以达到降低残余应力或改变应力分布的目的。
这种方法时效周期很长,占用场地面积很大,不利于均衡生产。
另一种方法是振动时效,这是近几年发展起来道岔钢轨件时效新工艺。
6、钢轨件的顶弯
6.1钢轨件顶弯的作用
(1)使钢轨件的工作边成折线或曲线。
(2)有轨头水平切削的钢轨件,保证切削后的钢轨头部都能得到轨腰的支承,不至于悬空。
(3)对于具有曲线工作边的尖轨、心轨等,除为了避免轨头悬空外,同时配合切削工序使钢轨工作边形成曲线型。
6.2钢轨件顶弯的操作内容
(1)核对顶弯样板与产品图纸无误后才能顶弯。
(2)测量出各弯折点的位置,并作出标记。
(3)首先将尖轨调直,然后按图纸要求进行顶弯。
(4)需要区分左、右开的钢轨件要注意区分左、右开。
(5)用平尺及样板检测。
6.3钢轨顶弯时的支点距离
钢轨顶弯时,有一个顶点和两个反作用的支点,两支点的距离为2T,T值由顶弯机的结构决定。
一般设计中选择T=150mm。
在生产制造中一般选择T=200~400mm。
在顶弯点处并不是一个折角,而呈曲线型,曲线半径随着T值的大小而变化。
在小号码道岔的钢轨件顶弯时,要特别注意对T值的选择。
6.4钢轨顶弯的质量要求
(1)钢轨不允许加热顶弯,仅在特殊情况时,可允许钢轨局部加热顶弯,加热的温度不得超过500℃。
提速道岔基本轨、尖轨及可动心轨辙叉翼轨、心轨不允许加热顶弯。
(2)顶弯产生的压痕深度不得超过1mm。
(3)顶弯产生裂纹的钢轨严禁使用
6.5顶弯样板及圆顺样板的算法
其中a1a2a3分别为E、C、N点的支距
A点进行顶弯弯折样板a1×
0.6
E点进行圆顺圆顺样板(a2-2×
a1)×
C点进行圆顺圆顺样板(a3-3×
a1-2×
c1)×
以50-12单开道岔CZ2227中CB2232-02曲基本轨为例
如上图所示:
A点进行顶弯弯折样板7.1×
0.6=4.26
B点进行圆顺圆顺样板17.1-2×
7.1=2.9
2.9×
0.6=1.74
C点进行圆顺圆顺样板30-3×
7.1-2×
2.9=2.9
D点进行圆顺圆顺样板45.7-4×
7.1-3×
2.9-2×
2.9=2.8
2.8×
0.6=1.68
E点进行圆顺圆顺样板64.3-5×
7.1-4×
2.9-3×
2.8=2.9
F点进行圆顺圆顺样板85.8-6×
7.1-5×
2.9-4×
2.8-2×
G点进行圆顺圆顺样板
110.1-7×
7.1-6×
2.9-5×
2.8-3×
H点进行圆顺圆顺样板
123-7.489×
7.1-6.489×
2.9-5.489×
2.9-4.489×
2.8-3.489×
2.9-2.489×
2.9-1.489×
2.8=1.02
1.02÷
489×
600=1.25
7、轨件的组装
7.1带有补强板钢轨件的组装,补强板的始端应与钢轨的始端对齐,允许相差不得大于1mm,补强板应与钢轨轨头下颚和轨底上颚密贴,如不密贴时允许有不大于1mm的空隙,补强板长度小于设计长度时,允许两段焊接,此时,尖轨或活动心轨两侧的补强板的焊缝应交错布置,其交错距离不小于300mm,在尖轨或活动心轨轨头宽50mm断面前,不允许焊缝存在,焊缝至螺栓孔净距不得小于40mm。
7.2尖轨与基本轨组装技术要求
(1)整组道岔转辙器应将尖轨和基本轨组装出厂。
(2)尖轨轨头非工作边切削面应与基本轨轨头密贴,允许尖端至第一拉杆部分有不大于0.2mm空隙,其余部分允许有不大于1mm空隙。
(3)直线尖轨工作边的轨距线应成一条直线,全长直线度为2mm(只允许空线,不允许抗线,下同);
曲线尖轨工作边应保持圆顺,无硬弯。
(4)顶铁与尖轨(或基本轨)轨腰的间隙不得大于1mm。
(5)尖轨跟端处尖轨与基本轨轨底平行度为1mm,两轨底面高度的偏差为±
(6)设置轨撑的尖轨基本轨组件,轨撑的顶部圆弧应与基本轨轨头下颚密贴,如不密贴时,允许有不大于0.5mm局部缝隙。
(7)尖轨与基本轨组装后,尖轨跟距偏差为+2,-1mm。
7.3尖轨与基本轨配合不密贴的原因及处理方法
(1)尖轨50mm断面内刨切长度不够
(2)尖轨顶铁过长,尖轨补强板螺栓凸出
(3)扳道器或转辙机的位置与尖轨动作拉杆的位置不在同一水平直线上
(4)基本轨弯折点错后
(5)钢轨内侧有飞边
(6)基本轨横向移动
(7)基本轨或尖轨有硬弯
(8)第一、二位连接杆与尖轨耳铁连接的距离不合适
(9)基本轨、轨撑、滑床板挡肩之间有离缝
处理方法:
(1)对刨切长度不足的尖轨再作刨切。
(2)顶铁与补强板螺栓可作打磨、焊补或更换
(3)调整扳道器或转辙机及尖轨拉杆位置,使其在同一水平线上
(4)拨正基本轨方向,矫正弯折点的位置
(5)打磨基本轨内侧飞边
(6)打靠道钉,消除假轨距
(7)调直尖轨或基本轨,拨正方向,改好轨距
(8)调整连接杆长度,改变尖轨耳铁的孔位或者加入绝缘垫片,误差较大时
(9)更换尖轨耳铁或方钢
二、垫板件工序工艺
道岔垫板按作用及结构形状一般分为滑床板、支距垫板、护轨垫板、辙叉垫板等几类.
2.1道岔垫板的结构:
“75”型及“92”型道岔垫板一般采用厚20mm,宽180mm的扁钢制造,其上需要设挡肩、挡铁、道钉孔等。
提速道岔及其它新型道岔的垫板一般采用厚20mm,宽170mm的扁钢制造,其上根据需要设铁座、与岔枕连接的螺栓孔等;
对于设置轨顶坡的道岔,垫板采用厚22mm、宽170mm的扁钢制造,承轨槽加工成1:
40的斜面。
制造垫板(底板)的材料一般采用Q235-A。
护轨垫板(底板)的材料采用16Mn,以提高护轨垫板的强度。
新型道岔的垫板按其制造工艺的方式有焊接组合式和整体铸造垫板等。
当前我国的道岔垫板大多采用焊接组合式垫板。
以下以滑床板为例对各阶段技术进行比较
75型道岔
92型道岔
提速道岔
滑床板
6mm厚滑床台,轨撑设在铁座上,用两个长方头螺栓与垫板联结
24mm厚滑床板,可调式栓接轨撑,刚性扣压
32mm厚滑床台,弹性轨撑,弹性扣压
(“75型”道岔常用滑床板)
(“92型”道岔滑床板)
(60kg/m钢轨提速道岔CT5-40滑床板)
2.2焊接道岔垫板的制造工艺过程一般为:
下料、钻孔(或冲孔)、调平、机加工、焊接、矫正。
(1)道岔垫板的下料
道岔垫板的下料一般采用剪切或火焰切割下料工艺,对于外型不规则的垫板,有时也采用数控火焰切割工艺手段。
(2)道岔垫板的制孔
道岔垫板的制孔有钻孔和冲孔两种工艺方式。
钻孔一般在摇臂钻床上采用覆盖式钻孔模板进行。
冲孔一般在剪冲机床上采用专用冲孔胎型进行。
带弧型槽的垫板孔,钻孔后采用专用弧型槽铣床制成。
(3)道岔垫板的机加工
道岔垫板一般不进行机加工,有特殊要求的垫板(如设轨顶坡道岔的垫板)有时要对垫板的周边或承轨槽位置进行机加工处理。
垫板的加工一般在铣床或刨床上进行。
(4)垫板打印标记
垫板应按图纸要求和标记位置打印标记,铁垫板的产品标识应包括以下相关内容:
图号、件号或规格;
左、右开别;
偏心距。
(5)道岔垫板的焊接
道岔垫板的焊接一般采用二氧化碳气体保护焊,特殊情况时也采用手把焊。
垫板焊接时,确定垫板上零件位置一般以孔为基准采用画线(画线样板)或焊接样板的工艺方式。
(6)道岔垫板的调平和矫正
道岔垫板在下料后一般要进行调平处理,调平一般在压力机上进行。
道岔垫板在焊接后,为消除焊接变形,一般要对垫板进行矫正处理,焊接后的矫正处理一般在专用的压力机上进行,特殊结构的垫板(如护轨垫板、可动心轨道岔带撑板的辙叉垫板)为保证垫板质量,通常采用火焰矫正的工艺方式。
第三章道岔技术条件及标准
一、钢轨件长度允许偏差
1.1、钢轨件不得采用焰割的方法下料,钢轨端面对于长度方向的垂直度不应大于1.0mm;
时速为200km/h的钢轨端面对于长度方向的垂直度不应大于0.5mm
1.2、钢轨件长度的允许偏差:
时速≤160km/h
时速200km/h
时速250km/h和350km/h
尖轨、长心轨、短心轨
0-4
0-3mm
0-3mm,长度大于40m时0-5mm
基本轨、配轨
±
3(长度≤12.5m)
0.25‰(长度≥12.5m)
2(长度≤12.5m)
4(长度≥12.5m)
2(长度≤25m)
4(长度≥25m)
叉跟尖轨
2mm
+1-2mm
翼轨、护轨
6mm
4
5
二、钢轨件上的螺栓孔规定
2.1时速小于等于160km/h
(1)螺栓孔径允许偏差为+10mm
(2)螺栓孔壁粗糙度Ra值为25um
(3)螺栓孔中心位置上下允许偏差为±
1.0mm
(4)接头螺栓孔中心至轨端距离允许偏差为±
(5)两相邻螺栓孔中心距离允许偏差为±
(6)两最远螺栓孔中心距离允许偏差按下表规定
(7)螺栓孔(含其他用途的孔)应倒棱不小于1.0mm×
45°
并消除毛刺,普通钢轨与补强板拼装尖轨的道岔可仅对接头螺栓孔倒棱
两最远螺栓孔中心距离允许偏差
钢轨件名称
螺栓孔中心距<1500
螺栓孔中心距≥1500
长心轨、短心轨、翼轨、帮轨、抚轨
1.0
1.5
基本轨、尖轨、护轨
2.0