课程设计传动轴的机械加工工艺设计文档格式.docx
《课程设计传动轴的机械加工工艺设计文档格式.docx》由会员分享,可在线阅读,更多相关《课程设计传动轴的机械加工工艺设计文档格式.docx(10页珍藏版)》请在冰豆网上搜索。
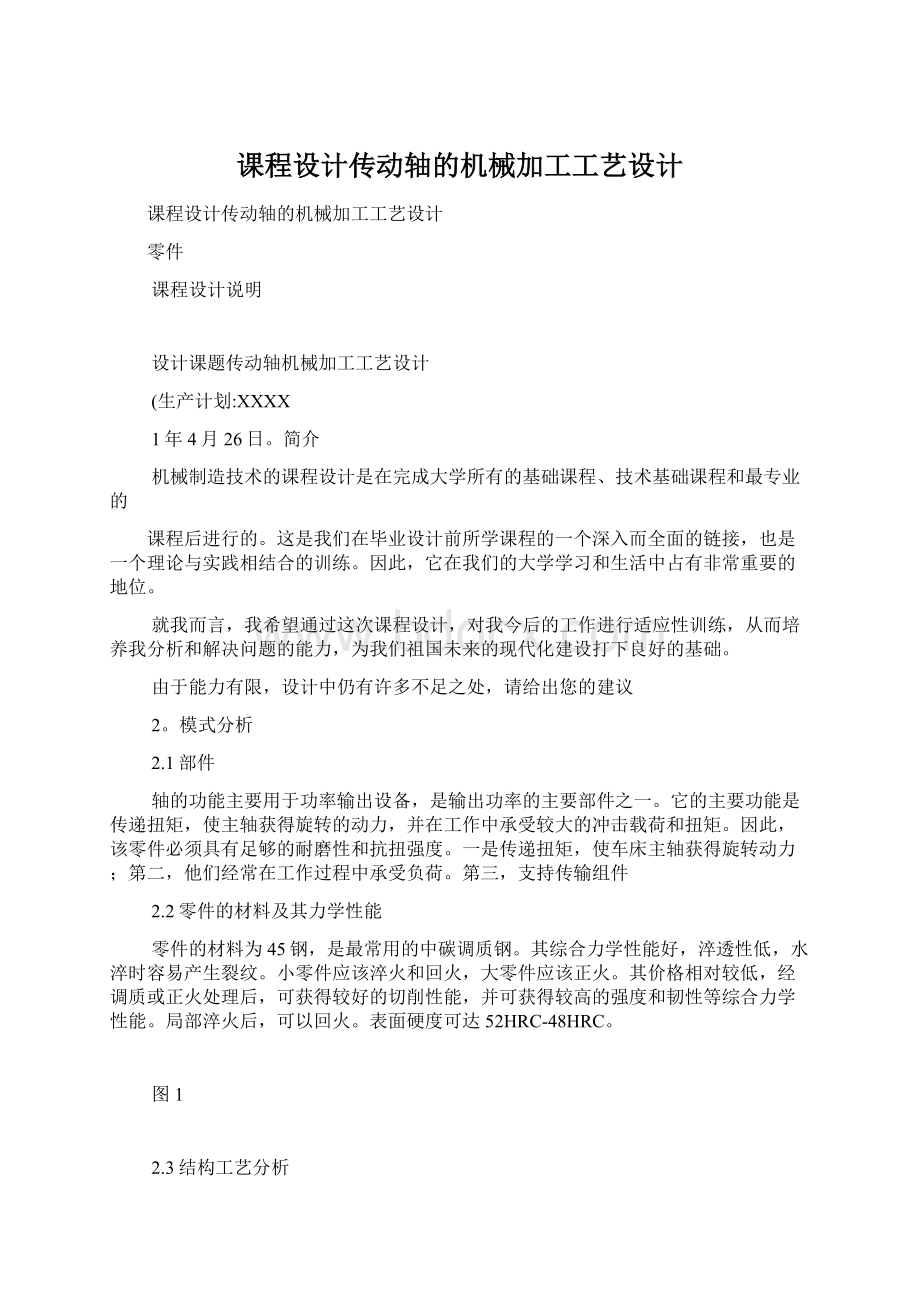
小零件应该淬火和回火,大零件应该正火。
其价格相对较低,经调质或正火处理后,可获得较好的切削性能,并可获得较高的强度和韧性等综合力学性能。
局部淬火后,可以回火。
表面硬度可达52HRC-48HRC。
图1
2.3结构工艺分析
从零件图来看,该零件是一个结构相对简单的典型轴类零件。
其主要加工面为φ45和φ30,两个φ35的外圆柱面,其中一个φ35和φ30的外圆柱面需要滚压,硬度达到52HRC。
退刀槽的一个端面上有3*1、4*1、3*0.5、3*0.5和Ra0.8零件的左端面有一个38毫米长的莫氏4号锥度和三个不同尺寸的键槽:
第一个30*10*4.5;
第二个24*6*3;
三是100*10*5,键槽内壁表面粗糙度Ra3.2。
零件左端有两个螺纹,中间尺寸。
第一个标称尺寸为20毫米,间距为1.5。
第二标称尺寸33,间距1.5;
零件的最右端有一个深度为9毫米的横向凹槽,一个关于中心轴对称宽度为8毫米的凹槽和一个深度为9毫米、内壁粗糙度为Ra3.2的孔
图尺寸精度较高,大多为IT5或6级;
粗糙度显示三个键槽的内壁为Ra3.2,φ30,两个φ35和莫氏锥度4的外表面为Ra0.8,其余为粗糙的原始粗糙度。
位置要求严格,如莫氏锥度4号表面相对于两个φ35轴线的跳动量为0.015毫米,35JS5外表面相对于两个φ35轴线的跳动量为0.01毫米,45°
外表面相对于两个φ35轴线的跳动量为0.02毫米。
φ35的外表面相对于两个φ35的轴线的跳动为0.01毫米,φ30的外表面相对于两个φ35的轴线的跳动为0.015毫米;
表示当外圆表面绕轴旋转一次时,任何测量平面的径向跳动不得大于给定值。
莫尔斯锥度中部键槽轴线与锥头轴线平行度为0.03毫米,φ35h5键槽轴线与φ35h5轴线平行度要求为0.03毫米
。
热处理要求回火处理至200HBW,并保持均匀。
通过对零件的分析,
布局合理,便于加工。
我们可以通过径向夹紧来保证其加工要求。
整个图纸清晰,尺寸完整合理。
它能充分表达物体的形状和大小,满足要求。
空白分析
3。
选择毛坯
和绘制毛坯图是工艺规划的初始阶段之一,也是相对重要的阶段。
毛坯的形状和特征(硬度、精度、金相组织等。
)对加工难度和工序数量有直接影响。
因此,合理选择毛坯在生产中占有非常重要的地位,毛坯加工余量的确定也是一个非常重要的问题。
3.1毛坯选择选择
毛坯类型决定了零件的实际功能、材料、形状、生产性能以及在生产中获得的可能性。
坯料的制造方法主要如下:
1.概况2。
锻造3。
选角4。
焊接5。
其他空白因此,建议使用铸造或锻造,但考虑到机械性能,如铸造中的材料,机械性能较差,而锻造具有较高的强度和机械性能,冲击韧性通常用于重载荷或冲击载荷下的工作部件。
该零件的生产批量为中批量,因此,总的来说,选择锻件间的锻造。
3.2毛坯图设计
毛坯(锻件)图是根据产品零件设计的。
查看《加工工艺手册》和《金属加工工艺人员手册》后,可以知道精车、半精车和粗车的余量,从而得到毛坯的余量。
见图2
图2
4。
加工方法的选择
在市场经济的前提下,一切都是为了创造更多的财富和提高劳动生产率
选择相同的加工方法一般是在保证工件加工要求的前提下考虑的。
选择工人
的加工效率和经济性,具体选择一般根据加工数据和工人经验确定。
由于方法多种多样,工人在选择时通常会结合特定的工件和现场加工条件来确定最佳加工方案。
在选择这部分的加工方法时也考虑了工件的具体条件和我们学校的具体加工条件。
总的来说,我们将按照加工顺序详细说明加工方案:
加工表面φ35h5外圆柱面φ30js6外圆柱面φ45外圆柱面φ35js5外圆柱面莫氏锥度4M20*1.5螺纹M33*1.5键槽30*10*4.5键槽24*6*3键槽100*10*5键槽30*8*9卸荷槽3*1卸荷槽3*1个离隙槽3*1个离隙槽3*1表面粗糙度ra0.8ra0.8ra6.3ra0.8ra6.3ra6.3ra3.2ra3.2ra3.2ra6.3ra6.3ra6.3ra6.3ra6.3ra公差/精度等级IT5IT6自由公差IT6IT7IT7IT9自由公差自由公差自由公差自由公差加工方法粗车-半精车-精车粗车-半精车-精车粗车-精车粗车-精车粗车-精车粗车-精车粗车-精车粗车-精车粗车-精车粗车粗车粗车粗车粗车粗车精车粗车精车粗车精车粗车精车精车精车粗车精车精车精车粗车精车精车精车精车精车精车粗车精车精车精车精车粗车精车精车精车精车粗车精车精车精车精车精车精车精车精车精车精车精车精车精Ra6.3Ra6.3Ra6.3ra6.3自由公差自由公差粗车粗车钻孔-铰孔粗车粗车
5,工艺浓度和分散考虑
5.1工艺浓度中的
工艺浓度是将零件的加工集中在几个工艺中。
每个流程都有许多处理内容和短流程。
其主要特点是:
1。
它可以使用高效率的机床和高生产率的技术设备。
2.减少了设备数量、操作人员数量和占地面积,节省了人力物力;
3.工件安装次数减少,有利于保证表面之间的位置精度;
所采用的工装设备结构复杂,调整维护困难,生产准备工作量大
5.2工艺分散
工艺分散是将零件的加工分散成多个工序来完成,每个工序都有较少的加工内容和较长的工艺路线其主要特点是:
设备和工艺设备相对简单,易于调整,易于适应产品变化,对工人的技术要求低。
最合理的切削量可以用来减少机动时间;
所需设备和工艺设备数量多,操作人员多,占地面积大。
工艺的浓缩或分散程度主要取决于生产规模。
在正常情况下,当小批量生产单件时,采用集中工序在普通机床上加工尽可能多的表面。
当进行大规模生产时,过程是分散的在一天结束时,结合图纸的要求,该过程是分散的。
6。
排列处理顺序
|排列处理顺序
6.1
加工阶段的划分
当零件的加工质量要求很高时,通常不可能用一种工艺来满足要求。
相反,有必要通过几道工序逐步达到所需的加工质量,并合理使用设备。
人力,零件的加工过程通常根据过程的性质分为三个阶段,即粗加工、半精加工和精加工①
粗加工阶段:
其任务是去除毛坯的大部分余料,使毛坯在形状和尺寸上接近成品。
因此,主要目标是提高生产率,车床加工大部分多余的螺纹、端面和外圆表面,并为后续加工提供良好的参考,如加工φ45、φ35、φ30、φ29.295莫氏4号外圆表面②
半精加工阶段:
其任务是使主表面达到一定的精加工余量,为主表面的精加工做准备,如φ45、φ35、φ30、φ30、φ29.295或φ4外圆柱面M*20*1.5和M*33*1.5普通螺纹(3)
精加工阶段:
其任务是确保所有主要表面达到规定的尺寸精度,留有一定的精加工余量,为主要表面的精加工做准备,并精加工一些次要表面如精度和表面粗糙度要求,主要目标是充分保证加工质量
2、
加工该零件时,先加工端面,然后加工左端面和外圆柱面作为参考。
因为左端面和外圆柱面是为后续的精基准面加工而设置的,所以定位基准可以做得更精确,从而保证每个位置的精度要求,然后再加工其余部分。
3,先粗后细
表示先粗加工后精加工。
粗车将在短时间内切断工件表面的大部分多余部分。
一方面提高金属切削效率,另一方面满足精车平衡均匀性的要求。
如果粗车后留下的平衡均匀度不能满足精加工的要求,应安排半精车,为精车做准备。
4和
对于该零件,应先加工平面,然后再加工平头孔。
这种加工顺序的安排,一方面使用加工平面进行定位,这是稳定和可靠的,另一方面,在加工平面上加工孔,这是相对容易的,并且可以提高孔的加工精度。
6.2工艺分工
工艺集中和工艺分散的确定:
工艺集中是指工件在几道工序中加工的集中,以完成每道工序中更多的加工内容,而工艺集中减少了总的工作量,从而减少了安装数量,减少了夹紧时间,减少了夹具数量,并使用了高生产率的机床工艺分散是将工件的加工分散到更多的工序中,每个工序的含量很小。
至少,每个过程只包括一个简单的步骤。
工序分散可以使各工序使用的设备和工具更简单,简化机床的调整,对操作人员的技术水平要求更低。
综上所述,考虑到工件是中批量生产,采用了工艺分散辅助工序的安排:
辅助工序一般包括去毛刺、倒角、清洗、除锈、退磁、检验等。
6.3热处理程序
热处理的目的是提高材料的机械性能,消除残余应力,改善金属的可加工性。
热处理主要包括初步热处理、最终热处理和内应力处理。
该零件CA6140车床的输出轴由45钢制成。
加工过程中的预热是为了消除零件的内应力。
毛坯锻造后最终热处理应在840℃下保持30分钟,以在半精加工后和精加工前根据规范释放应力。
7、工艺路线的确定
根据以上各部分的分析和加工工艺确定的基本原则,可以初步确定加工工艺路线。
具体方案如下:
方案一
1,备料锻造毛坯
2,热处理退火(消除内应力)3,常规粗车右端面各外圆
4,常规粗车左端面各外圆柱倒角5,热处理淬火回火6,数控车床钻扭
7,倒角
8为数控车床的右端精车、数控车床精车精车精车精车精车精车精车精车精车精车精车精车精车精车精车精车精车精车精车精车精车精车精车精车精车精车精车精车精车精车精车精车精车精车精车精车精车精车精车精车精车精车精车精车精车精车精车精车精车精车精车精车精车精车精车精车精车精车精车精车精车精车精车精车检验
方案2
1毛坯锻造毛坯
2热处理退火(消除内应力)4普通车端外筒和倒角5普通车φ456普通车φ357普通车φ30
8数控车床φ29.295数控铣床先加工9数控铣床钻,然后再拧10数控车床退槽11数控车床螺纹12数控铣床键槽
。
从零
零件考虑,由于轴类零件在切削过程中容易产生弯曲变形,如果采用分散加工,零件在加工过程中的位置精度无法保证。
为了同时保证零件图的圆跳动要求,采用方案1。
8、加工路线的确定
刀具进给路线的确定主要是为了提高生产效率和正确的加工工艺。
确定进给路线时,应考虑以下几个方面:
1.零件的加工精度和表面粗糙度应保证在
2,应制定最短的进给路线,并减少刀具的空行程时间。
提高加工效率。
数值计算应简单,程序段数应少,以减少编程工作量
9。
工艺设计
9.1加工余量、工艺尺寸及其公差的确定
各工序的加工余量应根据各数据和制定的零件加工工艺路线,结合计算和查表确定。
根据经济精度选择中间工序的公差,根据进入机体的原则标出上下偏差,并确定每个加工面的加工余量。
工艺尺寸和毛坯尺寸如下:
1)外圆柱面φ35工艺名称精加工半精加工毛坯2)外圆柱面φ30工艺名称精加工半精加工毛坯3)外圆柱面φ45
工艺名称粗车工艺余量2工艺公差IT10工艺尺寸公差φ45表面粗糙度6.3工艺余量1.01.157.1工艺公差IT6IT10IT11工艺尺寸公差φ30φ31φ32.11工艺公差IT5IT10IT11工艺尺寸公差φ35φ36φ37.1φ43+1表面粗糙度0.81.66.3毛坯4螺纹M20*1.5工艺名称攻丝精车半精车粗车毛坯5螺纹M33*1.5工艺名称攻丝精车半精车粗车毛坯工艺名称精车半精车粗车毛坯7加工孔φ8工艺名称铰孔8加工键槽φ10工艺名称精铣粗铣2工艺余量1.01.01.157.5工艺余量1.01.01.157.5工艺余量1.01.157.1操作余量0.27.8操作余量操作余量IT8IT10IT12操作余量IT8IT10IT12操作余量IT6IT10IT11操作余量IT9IT12操作余量IT9IT12φ48+1操作尺寸余量φ20φ20φ21φ22.1φ28+1工艺尺寸公差φ33φ33φ34φ35.1φ43+1工艺尺寸公差φ29.295φ30φ31φ38+1工艺尺寸公差φ8φ7.8工艺尺寸公差φ10φ6表面粗糙度1.61.63.26.3表面粗糙度1.6表面粗糙度3.26.3表面粗糙度1.63.26莫氏锥度4号(基于左锥端面)9加工键槽(φ6)工艺名称精铣粗铣工艺余量工艺公差IT9IT12工艺尺寸公差φ6φ4表面粗糙度1.63.210加工离隙槽(3*1)工艺名称粗车工艺余量2工艺公差IT10工艺尺寸公差φ18表面粗糙度3.211加工离隙槽(2*3*0.5)工艺名称粗车工艺余量2工艺公差IT10工艺尺寸公差φ34表面粗糙度3.212加工凸槽(4*1)工艺名称工艺余量工艺公差工艺尺寸公差表面粗糙度粗车2IT10φ313.210。
基准选择
在加工第一道或前几道工序时,通常选择毛坯上的粗糙表面作为定位基准,这是粗糙基准,零件选择φ20外圆柱面作为粗糙基准来加工φ45外圆柱面和右端面以上选择符合粗基准选择原则中的最小余量和易夹紧原则。
在后续工艺中,加工面作为定位基准,外圆柱面和φ45的右端面作为定位基准。
这个基准是很好的基准。
选择精确基准时,采用基准重合,基准统一。
这种定位相对简单可靠,为重要表面的后续加工做准备。
粗基准
由于该零件是轴类零件,为了保证精度,选择外圆作为粗基准。
首先,选择三爪卡盘自动对准原理进行夹紧外圆是一个粗糙的基准面,外圆、端面和孔都经过加工。
然后将加工后的外圆作为加工另一端面的参照。
精基准
的选择对零件加工后的精度非常重要。
该零件以一端的孔为精度基准,一端夹紧另一端完成外圆加工。
11,切削用量的选择
所谓合理切削用量,是指在保证加工质量的前提下,充分利用刀具的切削性能和机床性能,获得高生产率和低加工成本的切削用量切削参数的制定是根据选择的刀具材料和几何角度合理确定反切削量和进给量。
加工外圆柱面φ45
粗车:
确定进给速度f:
查阅上海
科学出版社金属加工技师手册更新版,表10-8,知道f=0.6~0.9mm/r,取
f=0.71mm/rap=2.5mm结合CA6140手册,检查金属切削手册,知道VC=70~90m/min,取Vc=75m根据CA6140规范,D=341.22r/min被视为n=320r/min,因此实际切割速度Vc=n?
d/1000=320x3.14x45/1000=70.34m/min功率Pc=KCxAPxVCx0.71/60000=2305x
2.5x70.34x0.66/60x1000=4.4Kw,因为在机床指令中发现Pc=7.5Kw,效率为0.8,机床功率pn功率Pc=KCxAPxVCxf/60000=2305x0.3x120/60000=1.24Kw
由于Pc=7.5Kw,在机床规格中,效率为0.75,机床功率pn加工外圆柱面φ35
d=35确定进给速度f:
检查
海洋科学出版社表10-8,f=0.6~0.9mm/r,f=0.6检查金属切削手册,VC=70~90m/min,Vc=75m/min,n=1000Vc/?
根据CA6140规范,D=341.2r/min被视为n=320r/min,因此实际切割速度Vc=n?
d/1000=320×
3.14×
35/1000=70.34m/minAP=2.5mm
检查功率PC=KC×
AP×
VC×
F/60000=2305×
2.5×
70.34×
0.71/60000=4.8Kw,因为PC=7.5Kw,效率为0.8,功率pn半成品车:
检查加工工艺设计手册P433找出:
f=0.4~0.5mm/r=
f=0.45AP=0.9mm,检查外圆切削数据表找出:
VC=1.667~2.17m/s=Vc=1.8m/s,然后n=1000Vc/?
D=546.8r转/分,四舍五入到n=550转/分,Vc=n?
d/1000=510x3.14x62.9/1000=100.7m/min功率
PC=KCxAPxVCxf/60000=2305x0.9x0.45x100.7/60000=1.57KW,由于Pc=7.5Kw,效率0.8,机床功率pn加工外圆柱面30°
d=30确定进给速度f:
海洋科学出版社金属加工技师更新手册中的表10-8,f=0.6~0.9mm/r,f=0.71mm/R检查“金属切削手册”知道VC=70~90m/minVc=75m/min是
n=1根据CA6140规范,D=341.2r/min被视为n=320r/min,因此实际切割速度Vc=n?
d/1000=70.34米/分钟,功率Pc=7.5毫米,功率Pc=KCxApxVCxf/60000=2305x2.5x70.34x0.71/60000=4.8千瓦,因为Pc=7.5Kw,效率为0.8,机床功率pn
半成品车:
f=0.4~0.5mm/r取f=0.45mm/r
再次检查外圆切削数据表找出:
VC=1.667~2.17m/s取Vc=1.8m/s取
9D=506.55r/min四舍五入n=510r/minap=0.9mmVc=n?
d/1000=510x3.14x67.9/1000=108.7m/min功率PC=KCxAPxVCxf/60000=2305x0.9x108.7x0.45/60000=1.7Kw,因为Pc=7.5Kw,效率0.75,机床功率pn粗车:
f=0.7mm/rap=2.5mmn=190r/minVc=n?
d/1000=190x3.14x
181/1000=108m/min功率Pc=KCxAPxVCx0.001/60=2305x2.5x108/60x1000=10.3Kw,因为Pc=7.5Kw,效率为0.75,机器功率pn钻孔:
f=0.2mm/rAP=9mmn=509.5r/minVc=n?
d/1000=509.5×
18/1000=28.8m/min功率Pc=KC×
0.001/60=2305×
9×
28.8/60×
1000=9.9Kw,因为在机床指令中发现Pc=7.5Kw,效率为0.75,机床功率pn铰孔:
f=0.25毫米/rap=0.12毫米n=238.8转/minvc=n?
d/1000=238.8×
20/1000=15m/min功率Pc=KC×
0.1×
15/60×
1000=0.06Kw,因为在机床规格中发现Pc=7.5Kw,效率为0.75,机床功率pn
12。
机床的选择
①工艺3采用CA6140普通车床。
车床的参数如下:
CA6140型,中心距750毫米1000毫米1500毫米,床身上下最大车削直径400毫米,鞍座最大工作车削路径550毫米,水平拖板最大车削直径214毫米,主轴孔径52毫米,主轴锥孔MT6#,主轴速度系列16。
主轴转速范围
20-1800转/分,公制螺纹(30种)0.45-20毫米(30种),英制螺纹(30种)40-0.875吨/分(30种),模数螺纹0.125-5毫米,直径螺距螺纹160-4D。
P、横向刀架行程239毫米小刀架行程150毫米,尾套孔锥度MT5#,套筒行程120毫米,主电机功率4/5.5KW,总尺寸2350×
1020×
1250毫米
②工艺7、8、9采用数控车床CK7150A。
车床参数如下:
8工位电动刀架,可实现自动换刀。
数控装置:
FANUCOI,最大旋转直径590毫米,最大加工直径500毫米,最大加工长度1000毫米,主轴转速范围30-2000转/分,主轴电机功率7.5千瓦,主精度x定位精度≤0.016毫米,Z定位精度≤0.025毫米,x重复定位精度≤0.007毫米Z重复定位精度≤0.01毫米刀具选择
作为刀具材料的切削性能直接影响生产率、工件加工精度、加工表面质量、刀具磨损和加工成本,刀具材料的正确选择是数控加工过程的重要组成部分。
该工具应该具有高刚性、足够的强度和韧性、高耐磨性、良好的导热性、良好的可制造性和经济性、抗粘附性和化学稳定性由于零件CA6140车床的输出轴由45钢制成,建议使用YT15型硬质合金刀具。
由于加工这类零件时摩擦严重,切削温度高,YT型硬质合金具有较高的硬度和耐磨性,特别是高耐热性,高速切削钢时刀具磨损小,使用寿命长,所以加工45钢这类材料时使用硬质合金刀具。
(1),粗车外圆柱面:
刀具编号T0101,90度可转位车刀,圆弧半径1,刀片
型号VCUM160408R-A4,刀具型号PVJCR2525-16Q
(2)半精车,精车外圆柱面:
刀具编号T0202,75度可转位车刀,圆弧半径1,
刀片型号WNUM00
加工工具表
加工表面粗车外圆柱面半成品,精车外圆柱面切削坡口车削螺纹粗铣键槽钻孔铰孔刀具编号t0101t0202t0303t0404t0505t0606t0707刀具名称可转位车刀车削坡口车削螺纹刀具钻孔铰刀刀具参数90r=175r=19060r=3刀片类型VCUM160408R-A4刀具型号pvjcr2525-16qwnum080304El-a2pcrc2020-16qphi=1199湖南铁路职业技术学院材料名称45工艺编号工艺名称机械加工工艺卡数量材料规格产品类型零件名称传动轴产品名称设备工艺设备工艺内容图纸编号文件编号操作时间名称型号12345678材料准备热处理普通车普通车削、普通车削、热处理、铣削、数控车削、数控车削、锻造毛坯退火(消除内应力)、粗车削、各圆柱面上的半精车削、精车余量及左端面粗车右端面及外圆柱面倒角名称编号车床CA6140车床CA6140三爪卡盘三爪卡盘分度头粗车左端面φ45外圆柱面车床CA6140倒角调质先钻和铰各圆柱面右端的半精车及倒角铣床X51车床CK7150A三爪卡盘车床CK7150A三爪卡盘109121415标记
数控车削粗加工车床M33*1.5车床CK7150A三爪卡盘数控铣床钻头和铰刀φ8深9平孔数控铣床键槽去毛刺检查编号签名验证日期汇编车床CK7150A三爪卡盘铣床X51分度头日期第1页共1页增林玉
加工工艺卡
产品型号传动轴