涡轮轴制造方案及加工余量汇总Word格式.docx
《涡轮轴制造方案及加工余量汇总Word格式.docx》由会员分享,可在线阅读,更多相关《涡轮轴制造方案及加工余量汇总Word格式.docx(14页珍藏版)》请在冰豆网上搜索。
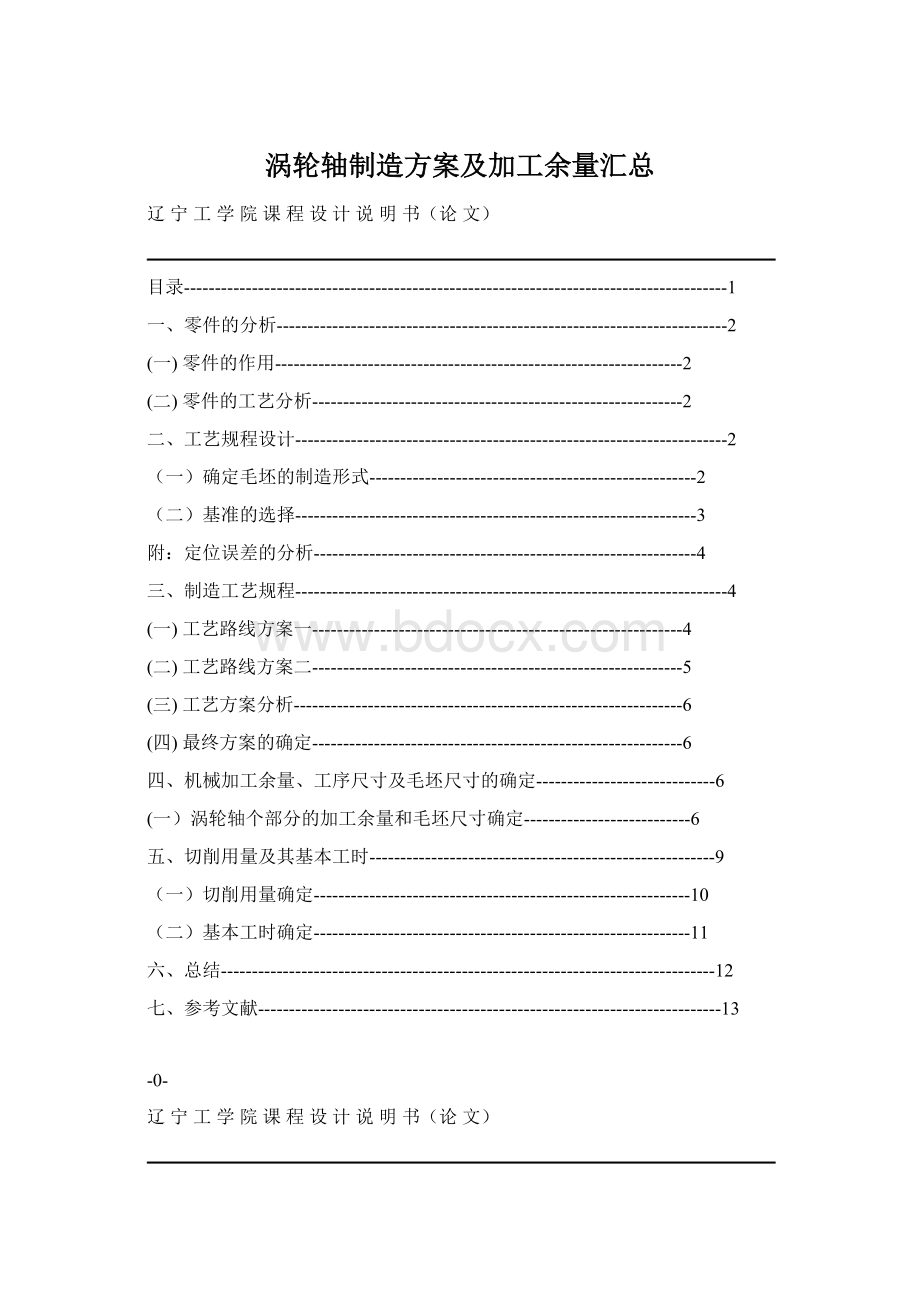
45
钢并调制,且蜗轮
轴上装有滚动轴承、蜗轮、轴套、密封圈、键。
号钢是一般轴类零件常用的
材料,竞购调质可以得到较高的切削性能,而且获得较好的强度和人性等综合
力学性能,重要表面经过局部淬火后再回火,表面硬度可以达到
HRC45-52。
定位精基准面中心孔应在组加工之前加工,在调制之后和磨削之前各需安
排一次修研中心孔的工序。
调质之后修研中心孔为消除中心孔的热处理变形和
氧化皮,磨削之前修研中心孔是为提高定位精基准面的精度和减小锥面的表面
组糙度值。
拟定轴的工艺过程时,在考虑主要表面加工的同时,还要考虑次要
表面的加工。
在半精加工外圆时,应车到图样规定的尺寸,同时加工出各退刀
槽、倒角和螺纹;
两个键槽应在半精车后以及磨削之前铣削加工出来,这样可保
证铣键槽时有较精确的定位基准,又可避免在精磨后铣键槽是破坏已精加工的
外圆表面。
二、工艺规程设计
(一)确定毛坯的制造形式
涡轮材料为
钢,由于该工件比较简单所以选择铸造,以使金属纤维尽量
不被切断,保证零件工作可靠。
此外考虑到选择各种已标准化、系列化的通用
刀具、通用量检具及辅助工具加工及检验工件。
其中,影响毛坯选择的因素通
常包括:
零件材料的工艺和对材料组织要求
零件的结构形状和外形尺寸
-1-
零件对毛坯精度、表面粗糙度和表面层性能的要求
现有的生产条件和充分考虑利用新工艺、新技术和新材料的可能
而轴常用材料主要是优质碳素钢和合金钢,优质碳素钢价格低廉,对应力
集中的敏感性小、并能通过热处理改善综合性能。
根据工作条件的采用热处理
工艺(如正火、调质、淬火等)以及一些表面处理(渗碳、渗氮及碳氮共渗等)。
经调质和表面淬火后,具有较高的力学性能。
一般机械的轴常用
钢。
轴的毛
坯一般采用轧制的圆钢或铸造。
锻件的强度较高,重要的轴,阶梯尺寸变化大
的轴。
应采用铸造毛坯。
结论:
本零件要求调质获得良好的综合机械性能,故选用
钢,采用铸件,
调质处理硬度
HB-241-269。
(二)基准的选择
1、粗基准的选择
选择涡轮轴的毛坯外柱圆面及其一个侧面作为定位基准,即遵循“基准重合”
的原则。
合理地选择定位基准,使工件的定位基准与工序基准相重合,使工件
安装稳定,加工中所引起的变形最小,使工件定位方便,夹紧可靠。
对于保证
零件的尺寸和位置精度有着决定性的作用。
而且对于一般的轴类零件而言,以
外表面作为粗基准是合理的。
由于涡轮轴零件全部表面都要加工,因此,粗基
准:
两端端面及中心孔。
端面加工:
采用铣削加工,使所有加工表面有足够的加工余量并且保证相互
位置精度,还要满足方便装夹等要求。
1、对于毛坯是铸件来说,毛坯精度是由铸件来保证的,其精度较高,加工
余量也较小。
毛坯铸件后已经过喷丸处理,表面平整、光洁、无飞边、毛刺等
缺陷
2、对于毛坯是铸件,不仅具有较好的加工性,而且加工余量也较精确,其
毛坯精度比锻件还高,完全能保证定位可靠
3、在涡轮轴加工过程中,选择粗基准还要考虑加工余量的分配均匀、合理。
这对于涡轮轴长径比较大、刚度低的特点来说,不仅有利于减小因切削余量不
均、切削力剧烈变化而使工件产生的弯曲变形,对于保证精加工质量和提高劳
动生产率具有重要的意义。
由于该涡轮轴的几个主要配合表面(Q、P、N、M)及轴肩面(H、G)对基准轴线
A-B
均有径向圆跳动和端面圆跳动的要求,它又是实心轴,所以应选择两端中
-2-
心孔为基准,采用双顶尖装夹方法,以保证零件的技术要求。
2、精基准的选择
对于涡轮轴的精加工及基准是以轴颈作为精基准。
考虑选择精基准时的主
要问题是如何保证设计技术要求的实现以及装夹准确、可靠、方便;
保证零件
的加工精度,满足基准重合、基准统一、互为基准、自为基准和便于装夹的原
则,以粗加工后的端面为主要的定位精基准,外圆表面为辅助的定位精基准。
具体而言,精基准:
Φ30
的外圆表面,轴的最左端面及最右端面,蜗杆齿
的左端面。
轴右端
Φ15
段的右端面。
定位误差的分析
造成定位误差的原因有两个:
一是定位基准与工序基准不重合,由此产生
基准不重合误差△b;
二是定位基准与限制位基准不重合,由此产生基准位移误
差△y
。
基准不重合误差△b
是一批工件逐个在夹具上定位时,定位基准与工序基
准
不重合而造成的加工误差,其大小为定位尺寸的公差在加工尺寸方向上的投影。
基准位移误差△y
是一批工件逐个在夹具上定位时,定位基准相对于限位
基
准的最大变化范围在加工尺寸方向上的投影。
三、制造工艺规程
(一)工艺路线方案一
1)
备料;
2)
精密锻造;
3)
粗车两端面,打中心孔;
4)
粗车蜗杆外圆;
-3-
5)
粗车右端
和
17
外圆;
6)
粗车
Φ22
Φ18
的外圆只
的左端面以及
Φ17
的外圆;
7)
车出蜗杆齿轮;
8)
半精车左端
外圆表面及车到
的外圆右端面;
9)
半精车左端各段的外圆表面,车出键槽;
10)
调质热处理;
11)
重新校核两端端面和中心孔;
12)
精车左右端的
的外圆表面和端面及
4x2
的槽沟;
13)
车两端倒角;
14)
砂带打磨左右两端外圆表面,去除蜗杆上的毛刺;
15)
检查
(二)工艺路线方案二
锻造,精密锻造毛坯;
热处理,正火
粗车两端面,保持总长
154mm;
钻中心孔;
粗车圆柱面
,φ15,φ17,φ
22,φ30
;
粗车圆柱面φ15,φ17,
M20,φ
22
半精车φ15
外圆柱面,车1⨯
45︒
倒角;
半精车外圆柱面φ17
,车削
2
⨯
φ15
半精车圆柱面φ30
,φ
精车蜗杆齿;
10)半精车外圆柱面φ15
,车1⨯
倒角
11)半精车外圆柱面φ17
φ14
12)半精车外圆柱面
M20
φ18
13)半精车外圆柱面φ
φ
20
退刀槽,车
0.5
-4-
14)正火
修研中心孔
16)精车外圆φ15,φ17
17)精车外圆φ17,φ15
18)车
1.5
-
6
h
的螺纹
19)铣
5
16,6
25
的键槽
20)终检
(三)工艺方案分析
通过对比方案一和方案二,两者都是通过锻造的方法得到毛坯件,都遵循
了基准先行的原则。
两个方案的共同点是以轴的中心线为基准,一次对各个部
分的外圆进行加工,通过粗车——半精车——精车的路线来是零件达到规定的
几何参数和无力性质。
蜗杆齿是通过车削的方式得到的,,热处理方法是调质,
精度也不容易满足要求,增加了制造的成本。
而又因为这个蜗杆齿的头数为一,
使用车削完全可以满足要求,也比较合理。
经过了粗车和半精车后在用淬火和
回火的方法对我干进行热处理加强齿面的强度。
这种方法也可以降低制造的成
本。
(四)最终方案的确定
经过以上的仔细分析后来看,使用方案二更加合理、可靠。
所以最终决定
采用方案二。
四、
机械加工余量、工序尺寸及毛坯尺寸的确定
-5-
加工对象
最左端的
外圆表面
工序名称
工序间余量
/mm
工序
工序基本
尺寸/mm
标注工序尺
寸/mm
经济精度
IT
表面粗糙度
Ra/µ
m
精磨
0.3
6
0.16
30.6
Φ30.6
精车
0.6
7
1.6
31.8
Φ31.8
半精车
0.9
10
5
33.6
Φ33.6
粗车
4.2
13
15
42
Φ42
蜗杆齿
工序基
本尺寸
0.8
5.5
1.1
8
2.5
4.4
12
左端的
Φ36
1
12.5
38
Φ38
2
蜗杆齿部分的前加工
(一)涡轮轴个部分的加工余量和毛坯尺寸确定
-6-
工对象
轴右端的
3.2
62.2
Φ62.2
66.2
Φ66.2
Φ28
-7-
23.8
Φ23.8
5.9
蜗杆轴段的两端面
6.4
82
62
3
88
68
轴两端面
324
330
39.8
Φ29.8
5.1
-8-
加工类型
切削速度
υ(m/min)
进给量
f
(mm/r)
切削深度
αp(mm
)
132
因为由前面的已经算
出的一次性最大加工
量为
5.1mm,小于车
刀的最大加工量,因
而可以一次加工完成。
所以切削深度按照之
前每次计算的加工量
为切削深度
189
0.15
210
0.1
钻螺纹孔
36
粗铣
半精铣
180
五、切削用量及其基本工时
(一)切削用量确定
切削用量主要包括三个要素,其分别是:
切削速度
υ(m/min);
f
(mm/r);
)。
1
vc
是指刀具切削刃上选定点相对于工件待加工表面在主运动方
向的瞬时速度。
在主运动每转一转或每一行程时(或单位时间内),刀具与工件
之间沿进给运动方向的相对位移。
3
背吃刀量(切削深度)ap
待加工表面与已加工表面之间的垂直距离。
本次加工的的各种加工方法的切削用量入下表所示
-9-
(二)基本工时确定
基本加工工时按照以下公式计算
t
基
=
l
+
l1
l2
i
fn
i
=
z
a
p
n
1000υ
πD
式中
;
——加工长度(mm);
——刀具的切入长度(mm);
——道具切出长度(mm);
——进给次数;
Z——加工余量(mm);
p
——背吃刀量(mm)
——进给量(mm);
10
-
——机床主轴转速(r/min0
υ
——切削速度(m/min);
D
——加工直径(mm0.
6、总结
通过这次汽车制造工艺关于凸轮轴的课程程设计,我学到了更多关于
设计的思维,关于怎么设计零件的毛坯,以及机械加工余量以及切削用量等知
识。
因此,这次设计使我对制造工艺这门学科有了进一步的了解,更重的是,
我学到了一些关于加工工艺的步骤及措施。
在制图方面,我更加懂得零件粗糙
度以及平行度对零件的加工实际要求,另外,我还更加熟悉了绘制毛坯这一绘
图流程。
在制作工艺卡片方面,在我们看似简单的一张张工艺卡片,它却在一
定意义上反映了每一个加工工艺所对应的加工要求以及最终这一工艺能对该零
件起到一个什么样的效果。
最后,这次设计能够顺利完成绝非一人的能力,我要感谢我们这一组
同学的互相讨论以及大家一起的分工合作。
11
七、参考文献
[1]
李益民主编.《机械制造工艺设计简明手册》.北京:
机械工业出版社,
1994.7
[2]
王先逵主编.《机械制造工艺学》.清华大学:
机械工业出版社,2006.1
[3]
赵家齐主编.《机械制造技术基础课程设计指导书》.北京:
机械工业出
版社,2000
[4]郑修本、冯冠大主编.《机械制造工艺学》.北京:
机械工业出版社.
1992
[5]
李洪主编.《机械加工工艺手册》.北京:
北京出版社.1990
[6]
李云主编.《机械制造工艺学》.北京:
机械工业出版社.1990
[7]
王恒杰主编
《机械原理与机械零件》
陕西科学技术出版社.2000.3
[8]
郭勇军
康勇
汪哲能
主编《机械制造工艺基础与技能训练》
.北京.
电子工业出版社。
2013.1
12
[9]王先逵
主编
《机械制造工艺学》第三版
机械工艺出版社
2013
年
月
13