三角板的毕业设计文档格式.docx
《三角板的毕业设计文档格式.docx》由会员分享,可在线阅读,更多相关《三角板的毕业设计文档格式.docx(28页珍藏版)》请在冰豆网上搜索。
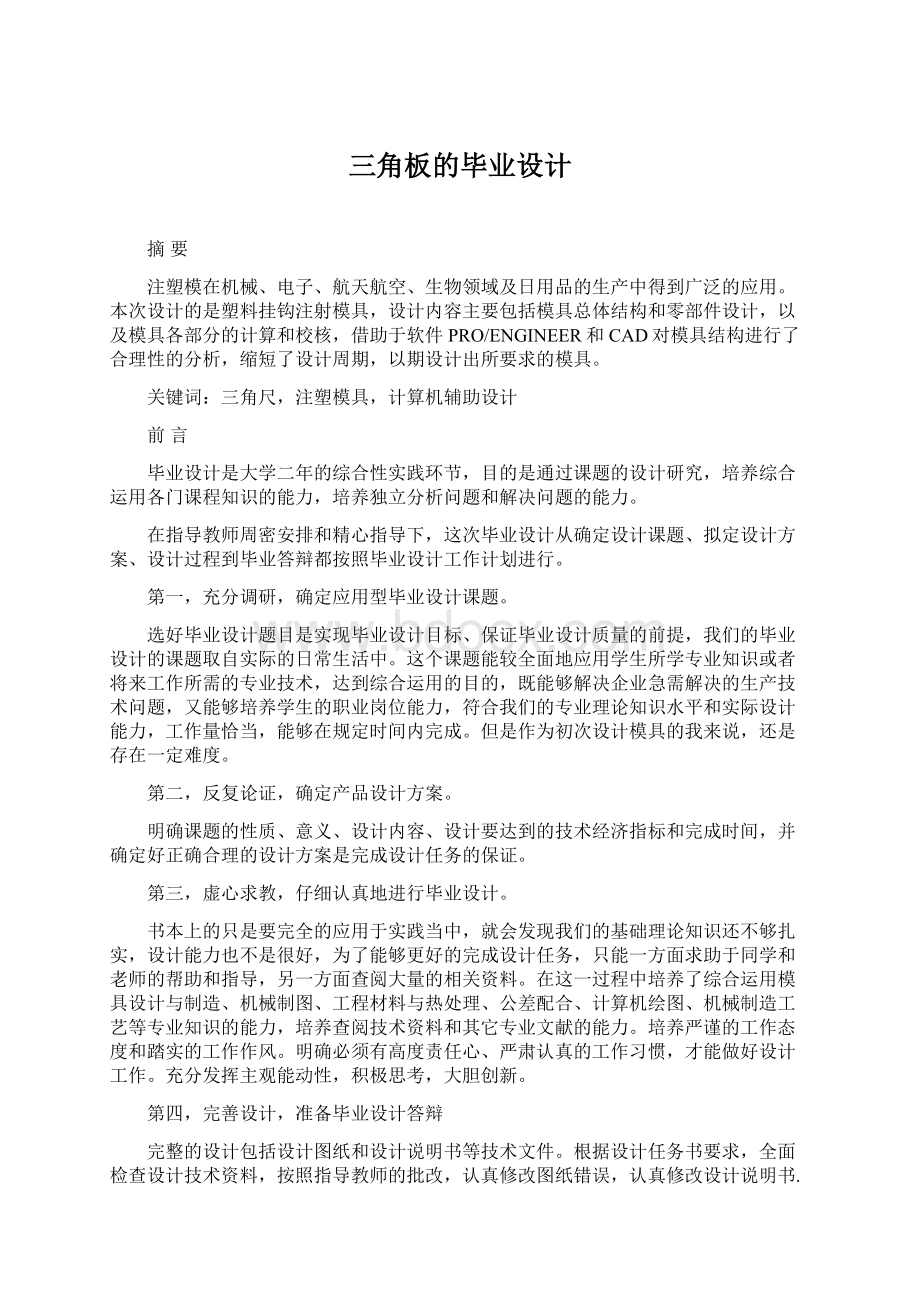
模具在机械,电子,轻工,汽车,纺织,航空,航天等工业领域里,日益成为使用最广泛的主要工艺装备,它承担了这些工业领域中60%~90%的产品的零件,组件和部件的生产加工。
模具制造的重要性主要体现在市场的需求上,仅以汽车,摩托车行业的模具市场为例。
汽车,摩托车行业是模具最大的市场,在工业发达的国家,这一市场占整个模具市场一半左右。
汽车工业是我国国民经济五大支柱产业之一,汽车工业重点是发展零部件,经济型轿车和重型汽车,汽车模具作为发展重点,已在汽车工业产业政策中得到了明确。
汽车基本车型不断增加,2005年将达到170种。
一个型号的汽车所需模具达几千副,价值上亿元。
为了适应市场的需求,汽车将不断换型,汽车换型时约有80%的模具需要更换。
中国摩托车产量位居世界第一,据统计,中国摩托车共有14种排量80多个车型,1000多个型号。
单辆摩托车约有零件2000种,共计5000多个,其中一半以上需要模具生产。
一个型号的摩托车生产需1000副模具,总价值为1000多万元。
其他行业,如电子及通讯,家电,建筑等,也存在巨大的模具市场。
目前世界模具市场供不应求,模具的主要出口国是美国,日本,法国,瑞士等国家。
中国模具出口数量极少,但中国模具钳工技术水平高,劳动成本低,只要配备一些先进的数控制模设备,提高模具加工质量,缩短生产周期,沟通外贸渠道,模具出口将会有很大发展。
研究和发展模具技术,提高模具技术水平,对于促进国民经济的发展有着特别重要的意义。
1.2我国模具工业的现状
自20世纪80年代以来,我国的经济逐渐起飞,也为模具产业的发展提供了巨大的动力。
20世纪90年代以后,大陆的工业发展十分迅速,模具工业的总产值在1990年仅60亿元人民币,1994年增长到130亿元人民币,1999年已达到245亿元人民币,2000年增至260~270亿元人民币。
今后预计每年仍会以10℅~15℅的速度快速增长。
目前,我国17000多个模具生产厂点,从业人数五十多万。
除了国有的专业模具厂外,其他所有制形式的模具厂家,包括集体企业,合资企业,独资企业和私营企业等,都得到了快速发展。
其中,集体和私营的模具企业在广东和浙江等省发展得最为迅速。
例如,浙江宁波和黄岩地区,从事模具制造的集体企业和私营企业多达数千家,成为我国国内知名的“模具之乡”和最具发展活力的地区之一。
在广东,一些大集团公司和迅速崛起的乡镇企业,为了提高其产品的市场竞争能力,纷纷加入了对模具制造的投入。
例如,科龙,美的,康佳和威力等知名集团都建立了自己的模具制造中心。
中外合资和外商独资的模具企业则多集中于沿海工业发达地区,现已有几千家。
1.3我国模具技术的现状
20世纪80年代开始,发达工业国家的模具工业已从机床工业中分离出来,并发展成为独立的工业部门,其产值已超过机床工业的产值。
改革开放以来,我国的模具工业发展也十分迅速。
近年来,每年都以15%的增长速度快速发展。
许多模具企业十分重视技术发展。
加大了用于技术进步的投入力度,将技术进步作为企业发展的重要动力。
此外,许多科研机构和大专院校也开展了模具技术的研究与开发。
模具行业的快速发展是使我国成为世界超级制造大国的重要原因。
今后,我国要发展成为世界制造强国,仍将依赖于模具工业的快速发展,成为模具制造强国。
中国塑料模工业从起步到现在,历经了半个多世纪,有了很大发展,模具水平有了较大提高。
在大型模具方面已能生产48"
(约122CM)大屏幕彩电塑壳注射模具,6.5KG大容量洗衣机全套塑料模具以及汽车保险杠和整体仪表板等塑料模具,精密塑料模方面,以能生产照相机塑料件模具,多形腔小模数齿轮模具及塑封模具。
经过多年的努力,在模具CAD/CAE/CAM技术,模具的电加工和数控加工技术,快速成型与快速制模技术,新型模具材料等方面取得了显著进步;
在提高模具质量和缩短模具设计制造周期等方面作出了贡献。
1.4发展趋势
尽管我国模具工业有了长足的进步,部分模具已达到国际先进水平,但无论是数量还是质量仍满足不了国内市场的需要,每年仍需进口10多亿美元的各类大型,精密,复杂模具。
与发达国家的模具工业相比,在模具技术上仍有不小的差距。
今后,我国模具行业应在以下几方面进行不断的技术创新,以缩小与国际先进水平的距离。
(1)注重开发大型,精密,复杂模具;
随着我国轿车,家电等工业的快速发展,成型零件的大型化和精密化要求越来越高,模具也将日趋大型化和精密化。
(2)加强模具标准件的应用;
使用模具标准件不但能缩短模具制造周期,降低模具制造成本而且能提高模具的制造质量。
因此,模具标准件的应用必将日渐广泛。
(3)推广CAD/CAM/CAE技术;
模具CAD/CAM/CAE技术是模具技术发展的一个重要里程碑。
实践证明,模具CAD/CAM/CAE技术是模具设计制造的发展方向,可显著地提高模具设计制造水平。
(4)重视快速模具制造技术,缩短模具制造周期;
随着先进制造技术的不断出现,模具的制造水平也在不断地提高,基于快速成形的快速制模技术,高速铣削加工技术,以及自动研磨抛光技术将在模具制造中获得更为广泛的应用。
1.5存在的主要问题
我国塑料模具行业与其发展需要和国外先进水平相比,主要存在六个方面的问题。
(1)发展不平衡,产品总体水平较低。
虽然个别企业的产品己达到相当高的水平,个别企业的部分产品已达到或接近国际水平,但总体来看,模具的精度、型腔表面粗糙度、生产周期、寿命等指标与国外先进水平相比尚有较大差距。
包括生产方式和企业管理在内的总体水平与国外工业发达国家相比尚有10年以上的差距。
(2)工艺装备落后,组织协调能力差。
虽然部分企业经过近几年的技术改造,工艺装备水平己比较先进,但大部分企业工艺装备仍比较落后。
更主要的是我们的企业组织协调能力差,难以很好整合或调动社会资源为我所用,从而就难以承接比较大的项目。
(3)大多数企业开发能力弱。
一方面是技术人员比例低、水平不够高,另一方面是科研开发投入少,更重要的是观念落后,对开发不够重视。
(4)管理落后更甚于技术落后。
技术落后往往容易看到,管理落后有时却难以意识到。
国内外模具企业管理上的差距十分明显,管理的差距所带来的问题往往比技术上的差距更为严重。
(5)市场需求旺盛,生产发展一时还难以跟上,供需矛盾一时还难以解决,供不应求的局
面还将持续一段时间,特别是在中高档产品方面矛盾更为突出。
(6)体制和人才问题的解决尚待时日。
在社会主义市场经济中,在经济全球化的过程中,竞争性行业,特别是像模具这样依赖于特殊用户,需单件生产的行业,许多企业目前的体制和经营机制仍旧很难适应多变的市场。
人才的数量和素质水平也跟不上行业的快速发展。
虽然各地都在努力解决这两个问题,但要得到较好解决尚待时日。
展望未来,由于国际、国内宏观环境总体良好,国内塑料模具各主要用户行业仍将持续以较快速度发展,塑料模具也必将持续高速发展。
目前存在的主要问题通过国内外交流与合作,通过全行业的共同努力,通过各方面的共同支持,定会逐渐得到较好的解决。
第二章塑件的分析及塑料的成型工艺性能
图2.1
图2.2
2.1塑件的工艺分析
分析塑胶件的工艺性包括技术和经济两方面,在技术方面,根据产品图纸,主要分析塑胶件的形状特点、尺寸大小、尺寸标注方法、精度要求、表面质量和材料性能等因素,是否符合模塑工艺要求;
在经济方面,主要根据塑胶件的生产批量分析产品成本,阐明采用注射生产可取得的经济效益。
(1).该塑件尺寸较大,一般精度等级,为降低成型费用,采用一模一腔的结构来提高生产率。
塑件壁较薄,对制品不进行后加工。
(2).为满足制品高光亮的要求与提高成型效率采用点浇口。
(3).为了方便加工和热处理,型芯部分采用镶拼结构。
2.2材料的成型工艺性能
该塑件用塑料PVC。
PVC中文名字叫做聚氯乙烯,
英文名字叫做Polyvinylchlorid。
基本特性:
主要成份为聚氯乙烯,色泽鲜艳、耐腐蚀、牢固耐用,由于在制造过程中增加了增塑剂、抗老化剂等一些有毒辅助材料来增强其耐热性,韧性,延展性等,故其产品一般不存放食品和药品。
它是当今世界上深受喜爱、颇为流行并且也被广泛应用的一种合成材料。
它的全球使用量在各种合成材料中高居第二。
据统计,仅仅1995年一年,PVC在欧洲的生产量就有五百万吨左右,而其消费量则为五百三十万吨。
在德国,PVC的生产量和消费量平均为一百四十万吨。
PVC正以4%的增长速度在全世界范围内得到生产和应用。
近年来PVC在东南亚的增长数度尤为显著,这要归功于东南亚各国都有进行基础设施建设的迫切需求。
在可以生产三维表面膜的材料中,PVC是最适合的材料。
PVC(聚氯乙烯),其单体的结构简式为CH2=CHCl
注塑模工艺条件:
干燥处理:
通常不需要干燥处理。
熔化温度:
185~205℃模具温度:
20~50℃
注射压力:
可大到1500bar保压压力:
可大到1000bar注射速度:
为避免材料降解,一般要用相当地的注射速度。
流道和浇口:
所有常规的浇口都可以使用。
如果加工较小的部件,最好使用针尖型浇口或潜入式浇口;
对于较厚的部件,最好使用扇形浇口。
针尖型浇口或潜入式浇口的最小直径应为1mm;
扇形浇口的厚度不能小于1mm。
聚氯乙烯具有阻燃(阻燃值为40以上)、耐化学药品性高(耐浓盐酸、浓度为90%的硫酸、浓度为60%的硝酸和浓度20%的氢氧化钠)、机械强度及电绝缘性良好的优点。
但其耐热性较差,软化点为80℃,于130℃开始分解变色,并析出HCI。
PVC的特点及成型特性
比重:
1.38克/立方厘米,成型收缩率:
0.6-1.5%,成型温度:
160-190℃。
特点:
力学性能,电性能优良,耐酸碱力极强,化学稳定性好,但软化点低.适于制作薄板,电线电缆绝缘层,密封件等.
主要用途:
常见制品:
板材、管材、鞋底、玩具、门窗、电线外皮、文具等。
聚氯乙烯制品形式十分丰富,可分为硬聚氯乙烯、软聚氯乙烯、聚氯乙烯糊三大类。
硬聚氯乙烯主要用于管材、门窗型材、片材等挤出产品,以及管接头、电气零件等注塑件和挤出吹型的瓶类产品,它们约占聚氯乙烯65%以上的消耗。
软聚氯乙烯主要用于压延片、汽车内饰品、手袋、薄膜、标签、电线电缆、医用制品等。
聚氯乙烯糊约占聚氯乙烯制品的10%,主要用产品有搪塑制品等。
塑料品种
成分
结构特点
使用温度
密度
性能特点
成型特点
PVC
聚氯乙烯
对酸碱的抵抗能力极强,化学稳定性好。
-15~55℃
1.15~2.00g/cm3
力学性能,电性能优良,耐酸碱力极强,化学稳定性好,
聚氯乙烯在成型温度下容易分解放出氯化氢,所以必须加入稳定剂和润滑剂,并严格控制温度及熔料的滞留时间。
2.3塑件的注塑机选择
1.注塑量的计算:
通过UG建模分析塑件的体积V=9440.4763mm3
塑件的质量:
m1=ρv=9440.4763mm3*1.35g/cm3=12.74g(ρ=1.35g/cm3)
此时凝料道凝料的体积未知,可按塑件质量的0.6倍进行计算,所以注射量为:
nVS+Vj=(2*12.74)+(0.6*12.74*2)
=40.768g
nVs+Vj=(2*9440.4763)+(0.6*9440.4763*2)
=30209.52416mm3
式中Vs------单个塑件的容积(cm3)或质量g
n------模具的型腔数目
Vj-----浇注系统和飞边所需凝料的容积(cm3)质量g
2.锁模力的计算:
凝流道(包括浇口)在分型面上的投影面积A2,在此时还是个未知数,根据经验公式A2=(0.2~0.5)A1.(A1为每个塑件在分型面上的投影面积)。
用0.35nA1进行计算:
A=nA1+A2=nA1+0.35nA1=1.35nA1=12668.63112mm2
塑件中所需的注射压力为100~150mpa。
型腔平均压力为注射压力的30%~65%因塑件为直浇口,塑件的壁较后,注射压力可以少取些,所以为100*60%=60
Fn=12668.63112*60=760117.8672N
3.选择注塑机:
根据注塑量和锁模力选用注塑机类型为FT90.
有关参数如下:
螺杆型号:
A
螺杆直径mm:
30
螺杆长径比L/D:
23.5
注射压力mpa:
205
理论注射容积cm3:
121
注射重量g:
110
注射速率g/s:
10
螺杆转速r/m:
200
料筒温度调节段速:
3+1
锁模部分:
锁模力K.N:
900
模板最大间距mm:
650
模板最大行程mm:
320
模具厚度mm:
110~330
拉杆内间距mm:
355*355
喷嘴直径:
φ4
SR:
18
注塑机的选用原则
1
计算塑件及浇道凝料的总量(体积或质量)应小于注塑机额定容积(体积或质量)的0.8倍
2
模具成型时需要的注射压力应小于所选注射机的最大注射压力
3
模具型腔注射时所产生的压力必须小于注塑机的锁模力
4
模具的闭模高度因在注塑机最大,最小必合高度之间
5
模具脱模取出塑件所需的距离应小于所选注射机的开模行程
6
模具的外形尺寸及安装尺寸必须与所选的注射机模板相应
4.注塑机有关参数的校核。
a.型腔数量的校核。
由注射机额定注射量校核模具型腔数量
n≤(KmN-m2)/m1
2≤(0.8*110-0.6*12.74*2)/12.74≈5
2≤5
式中n------模具的型腔数目
K----注射剂最大注射量的利用系数,一般取0.8
M----注射机的额定塑化量(cm3/h或g/h)
t-----成型周期(S)
型腔数目校核合格。
b.注射压力的校核。
Nm1+m2≤80%m
40.768g≤110*80%
40.768g≤88g
式中m------注射机允许的最大注射量(g或cm3)
m2-----浇注系统所需塑料质量或体积(g或cm3)
m1------单个塑件的质量或体积(g或cm3)
注射压力校核合格。
C.锁模力校核。
F≤Pm(nAs+Aj)
900KN≤12668.63112mm2*60
900KN≤760117.8672N
900≤760.1178672KN
锁模力校核合格。
式中F---------注射机额定锁模力(合模力)N
As,Aj—塑件和浇注系统在分型面上的垂直投影面积(mm2)
Pm-----塑料熔体在模腔内的平均压力(mpa)
n----型腔个数
第三章模具结构设计分
3.1分型面的分析
如何确定分型面,需要考虑的因素比较复杂。
由于分型面受到塑件在模具中的成型位置、浇注系统设计、塑件的结构工艺性及精度、嵌件位置、形状以及推出方法、模具的制造、排气、操作工艺等多种因素的影响,因此在选择分型面时应综合分析比较,从几种方案中优选出较为合理的方案。
选择分型面应遵循以下几项基本原则:
1.分型面应选在塑件外形最大轮廓处
2.确定有利的流模方式
3.保证塑件的精度要求
4.满足塑件的外观质量
5.便于模具加工制造
6.对成型面积的影响
7.对排气效果
其中最重要的是有利流模方式与便于模具的加工制造,宜选择较大易加工的分型面。
为了方便模具加工,应尽可能的选择较大的面作为分型面如图A-A
3.2型芯的设计
图3.1
图3.2
3.3型腔的设计
图3.3
图3.4
3.4型芯、型腔的位置
图3.5型腔的位置
图3.6型芯的位置
第四章模具总体结构设计
4.1工作原理
合模时,注射机开合模系统带动动模向定模方向移动,在分形面出与定模对合其对合的精度由合模导向机构保证。
动模和定模对合后,定模板上的凹模与固定在动模板上的凸模组合成与塑件形状和尺寸一致的封闭型腔,型腔在注射成型过程中被注射机合模系统所提供的锁模力锁紧,以防止它在塑料熔体充填型腔时被所产生的压力涨开。
注射机从喷嘴中注射出的塑料熔体经由开设在定模的主浇道进入模具,再由分流道及浇口进入型腔,待熔体充满形腔并经过保压,补缩和冷却定型后开模。
开模时,注射机开合模系统便带动动模后退,这时动模和定模在分型面出分开,塑件包在凸模随动模一起后退,拉料杆将主浇道凝料从浇口套拉出。
动模退到一定位置时,安装在动模内的推出机构在注射机顶出装置的作用下,使推杆和拉料杆分别将塑件及浇注系统的凝料从凸模和冷料穴中推出,塑件与浇注系统凝料一起从模具中落下,至此完成一次注射过程。
合模时推出机构靠复位杆复位,从而准备下次的注射。
4.2连杆注塑模总体结构
本模具采用LKMSGA型模架
图4.1总体结构如图
图4.2
图4.4总模架图
第五章浇注系统的形式和浇口的设计
5.1主流道设计
5.1.1主流道的选择
主流道是一端与注射机喷嘴相接触,另一端与分流道相连的一段带有锥度的流动通道。
主流道小端尺寸为3mm。
5.1.2主流道的衬套的形式
主流道小端的入口处与注射机喷嘴反复接触,属易损件,对材料要求较严,因而模具主流道常设计成可拆卸更换的主流道衬套形式(俗称浇口套),以便有效的选用优质钢材单独进行加工和热处理.其型式见图
图5.1
5.1.3主流道衬套的固定
因为采用有拖浇口套,所以用定位圈配合固定在模具的面板上。
定位圈也是标准件。
具体固定形式如图
:
图5.2
5.2分流道设计
在多型腔或单型腔多浇口(塑件尺寸大)时应设置分流道。
分流道是知主流道末端与浇口之间这一段塑料溶体的流动通道。
它是浇注系统中熔融状态的塑料由主流道流入型腔前,通过截面积的变化及流向变换以获得平稳流态的过渡段,因此要求所设计的分流道应能满足良好的压力传递和保持理想的填充状态,使塑料熔体尽快地流经分流道充满型腔,并且流动过程中压力损失及热量损失尽可能小,能将塑料熔体均衡地分配到各个型腔。
5.3.1主分流道的形状及尺寸
为了便于加工及凝料脱模,分流道大多设置在分型面上,分流道截面形状一般为圆形梯形U形半圆形及矩形等,工程设计中常采用梯形截面加工工艺性好,且塑料熔体的热量散失流动阻力均不大,一般采用下面的经验公式可确定其截面尺寸:
式中B―分流道直径(mm)
m―塑件的重量(g)
L―分流道的长度(mm)
已知:
M=7.0gL=24mm得B=6mm即R=2/B=0.8
图5.3.3主分流道的长度及布置形式
a.分流道要尽可能短,且少弯折,便于注射成型过程中最经济地使用原料和注射机的能耗,减少压力损失和热量损失。
将分流道设计成弯曲的,总24mm.
b.分流道在分型面上的布置与前面所述型腔排列密切相关,有多种不同的布置形式,但应遵循两方面原则:
即一方面排列紧凑、缩小模具板面尺寸;
另一方面流程尽量短、锁模力力求平衡。
本模具的流道布置形式,如图
图5.3分流道的布置
5.3.2浇口的设计
浇口亦称进料口,是连接分流道与型腔的通道。
除直接浇口外,它是浇注系统中截面积最小的部分,但却是浇注系统的关键部分。
浇口的位置、形状及尺寸对塑件的性能和质量的影响很大。
5.3.3浇口的选用
浇口可分限制性浇口和非限制性浇口两种。
浇口的作用可以概述为,非限制性浇口起着引料、进料的作用;
限制性浇口一方面通过截面积的突然变化,使分馏道输送来的塑料熔体的流速产生加速度,提高剪切速率,使其成为理想的流动状态,迅速而均衡地充满型腔,另一方面改善塑料熔体进入型腔时的流动特性,调节浇口尺寸,可使多型腔同时充满,可控制填充时间、冷却时间及塑料表面质量,同时还起着封闭型腔防止塑料熔体倒流,并便于浇口凝料与塑件分离的作用。
浇口有点浇口、潜伏式浇口、侧点浇口、直浇口、耳式浇口、扇式浇口、平缝式浇口、环形浇口、轮辐失浇口、爪形浇口、等几类,常用的是前五类浇口,我们采用的是点浇口。
为确保塑件的表面质量,开模时自动拉断,能够实现自动化生产。
5.3.4浇口的位置选择
模具设计时,浇口的位置及尺寸要求比较严格,初步试模之后有时还需修改浇口尺寸。
无论采用什么形式的浇口,其开设的位置对塑件的成型性能及成型质量影响均很大,因此合理选择浇口的开设位置是提高塑件质量的重要环节,同时浇口位置的不同还影响模具结构。
总之,如果要使塑件具有良好的性能与外表,要使塑件的成型在技术上可行、经济上合理,一定要认真考虑浇口位置的选择。
通常需要考虑以下几点:
1)尽量缩短流动距离。