半导体制造工艺流程Word文档格式.docx
《半导体制造工艺流程Word文档格式.docx》由会员分享,可在线阅读,更多相关《半导体制造工艺流程Word文档格式.docx(9页珍藏版)》请在冰豆网上搜索。
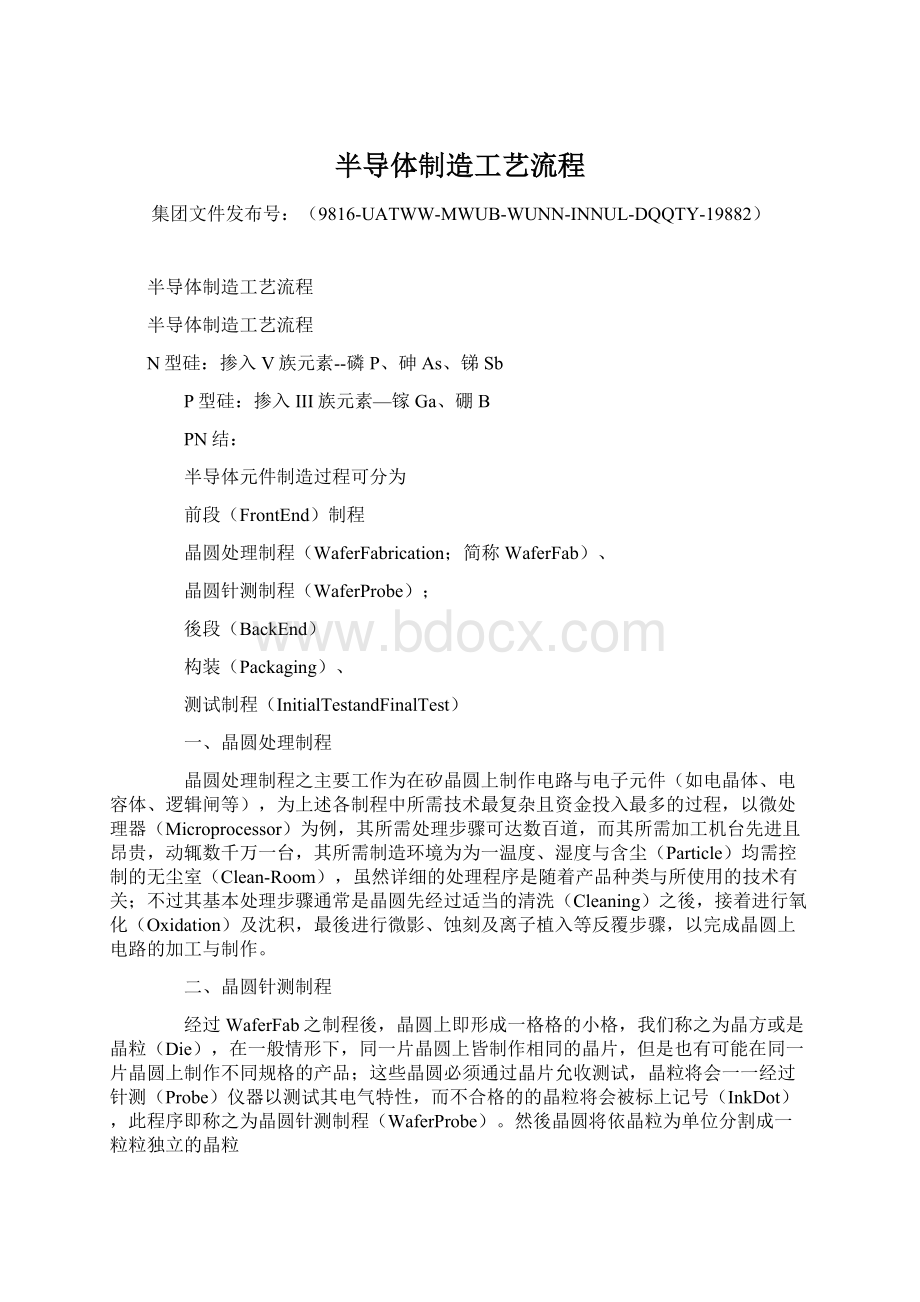
然後晶圆将依晶粒为单位分割成一粒粒独立的晶粒
三、IC构装制程
IC构装制程(Packaging):
利用塑胶或陶瓷包装晶粒与配线以成积体电路
目的:
是为了制造出所生产的电路的保护层,避免电路受到机械性刮伤或是高温破坏。
半导体制造工艺分类
一双极型IC的基本制造工艺:
A在元器件间要做电隔离区(PN结隔离、全介质隔离及PN结介质混合隔离)
ECL(不掺金)(非饱和型)、TTL/DTL(饱和型)、STTL(饱和型)B在元器件间自然隔离
I2L(饱和型)
二MOSIC的基本制造工艺:
根据栅工艺分类
A铝栅工艺
B硅栅工艺
其他分类
1、(根据沟道)PMOS、NMOS、CMOS
2、(根据负载元件)E/R、E/E、E/D
三Bi-CMOS工艺:
A以CMOS工艺为基础
P阱N阱
B以双极型工艺为基础
双极型集成电路和MOS集成电路优缺点
半导体制造环境要求
主要污染源:
微尘颗粒、中金属离子、有机物残留物和钠离子等轻金属例子。
超净间:
洁净等级主要由微尘颗粒数/m3
半导体元件制造过程
前段(FrontEnd)制程---前工序
简称WaferFab)
典型的PN结隔离的掺金TTL电路工艺流程
横向晶体管刨面图
纵向晶体管刨面图
NPN晶体管刨面图
1.衬底选择
10Ω.cm111晶向,偏离2O~5O?
P型Siρ
晶圆(晶片)晶圆(晶片)的生产由砂即(二氧化硅)开始,经由电弧炉的提炼还原成冶炼级的硅,再经由盐酸氯化,产生三氯化硅,经蒸馏纯化后,透过慢速分解过程,制成棒状或粒状的「多晶硅」。
一般晶圆制造厂,将多晶硅融解后,再利用硅晶种慢慢拉出单晶硅晶棒。
一支85公分长,重76.6公斤的8寸硅晶棒,约需2天半时间长成。
经研磨、抛光、切片后,即成半导体之原料晶圆片
第一次光刻—N+埋层扩散孔
1。
减小集电极串联电阻
2。
减小寄生PNP管的影响
外延层淀积
VPE(Vaporousphaseepitaxy)气相外延生长硅
SiCl4+H2→Si+HCl
氧化
Tepi>
Xjc+Xmc+TBL-up+tepi-ox
第二次光刻—P+隔离扩散孔
在衬底上形成孤立的外延层岛,实现元件的隔离.
第三次光刻—P型基区扩散孔
决定NPN管的基区扩散位置范围
第四次光刻—N+发射区扩散孔
集电极和N型电阻的接触孔,以及外延层的反偏孔。
Al—N-Si欧姆接触:
ND≥1019cm-3,
第五次光刻—引线接触孔
第六次光刻—金属化内连线:
反刻铝
CMOS工艺集成电路
CMOS集成电路工艺--以P阱硅栅CMOS为例
光刻I---阱区光刻,刻出阱区注入孔
阱区注入及推进,形成阱区
3。
去除SiO2,长薄氧,长Si3N4
4。
光II---有源区光刻
5。
光III---N管场区光刻,N管场区注入,以提高场开启,减少闩锁效应及改善阱的接触。
6。
光III---N管场区光刻,刻出N管场区注入孔;
N管场区注入。
7。
光Ⅳ---p管场区光刻,p管场区注入,调节PMOS管的开启电压,生长多晶硅。
8。
光Ⅴ---多晶硅光刻,形成多晶硅栅及多晶硅电阻
9。
光ⅤI---P+区光刻,P+区注入。
形成PMOS管的源、漏区及P+保护环。
10。
光Ⅶ---N管场区光刻,N管场区注入,形成NMOS的源、漏区及N+保护环。
11。
长PSG(磷硅玻璃)。
12。
光刻Ⅷ---引线孔光刻。
13。
光刻Ⅸ---引线孔光刻(反刻AL)。
晶圆材料(Wafer)
圆晶是制作矽半导体IC所用之矽晶片,状似圆形,故称晶圆。
材料是「矽」,IC(IntegratedCircuit)厂用的矽晶片即为矽晶体,因为整片的矽晶片是单一完整的晶体,故又称为单晶体。
但在整体固态晶体内,众多小晶体的方向不相,则为复晶体(或多晶体)。
生成单晶体或多晶体与晶体生长时的温度,速率与杂质都有关系。
一般清洗技术
光学显影
光学显影是在感光胶上经过曝光和显影的程序,把光罩上的图形转换到感光胶下面的薄膜层或硅晶上。
光学显影主要包含了感光胶涂布、烘烤、光罩对准、曝光和显影等程序。
曝光方式:
紫外线、X射线、电子束、极紫外
蚀刻技术(EtchingTechnology)
蚀刻技术(EtchingTechnology)是将材料使用化学反应物理撞击作用而移除的技术。
可以分为:
湿蚀刻(wetetching):
湿蚀刻所使用的是化学溶液,在经过化学反应之後达到蚀刻的目的.
乾蚀刻(dryetching):
乾蚀刻则是利用一种电浆蚀刻(plasmaetching)。
电浆蚀刻中蚀刻的作用,可能是电浆中离子撞击晶片表面所产生的物理作用,或者是电浆中活性自由基(Radical)与晶片表面原子间的化学反应,甚至也可能是以上两者的复合作用。
现在主要应用技术:
等离子体刻蚀
常见湿法蚀刻技术
CVD化学气相沉积
是利用热能、电浆放电或紫外光照射等化学反应的方式,在反应器内将反应物(通常为气体)生成固态的生成物,并在晶片表面沉积形成稳定固态薄膜(film)的一种沉积技术。
CVD技术是半导体IC制程中运用极为广泛的薄膜形成方法,如介电材料(dielectrics)、导体或半导体等薄膜材料几乎都能用CVD技术完成。
化学气相沉积CVD
化学气相沉积技术
常用的CVD技术有:
(1)「常压化学气相沈积(APCVD)」;
(2)「低压化学气相沈积(LPCVD)」;
(3)「电浆辅助化学气相沈积(PECVD)」
较为常见的CVD薄膜包括有:
■二气化硅(通常直接称为氧化层)■氮化硅■多晶硅■耐火金属与这类金属之其硅化物
物理气相沈积(PVD)
主要是一种物理制程而非化学制程。
此技术一般使用氩等钝气,藉由在高真空中将氩离子加速以撞击溅镀靶材后,可将靶材原子一个个溅击出来,并使被溅击出来的材质(通常为铝、钛或其合金)如雪片般沉积在晶圆表面。
PVD以真空、测射、离子化或离子束等方法使纯金属挥发,与碳化氢、氮气等气体作用,加热至400~600℃(约1~3小时)後,蒸镀碳化物、氮化物、氧化物及硼化物等1~10μm厚之微细粒状薄膜,PVD可分为三种技术:
(1)蒸镀(Evaporation);
(2)分子束磊晶成长(MolecularBeamEpitaxy;
MBE);
(3)溅镀(Sputter)
解离金属电浆(淘气鬼)物理气相沉积技术
解离金属电浆是最近发展出来的物理气相沉积技术,它是在目标区与晶圆之间,利用电浆,针对从目标区溅击出来的金属原子,在其到达晶圆之前,加以离子化。
离子化这些金属原子的目的是,让这些原子带有电价,进而使其行进方向受到控制,让这些原子得以垂直的方向往晶圆行进,就像电浆蚀刻及化学气相沉积制程。
这样做可以让这些金属原子针对极窄、极深的结构进行沟填,以形成极均匀的表层,尤其是在最底层的部份。
离子植入(IonImplant)
离子植入技术可将掺质以离子型态植入半导体组件的特定区域上,以获得精确的电子特性。
这些离子必须先被加速至具有足够能量与速度,以穿透(植入)薄膜,到达预定的植入深度。
离子植入制程可对植入区内的掺质浓度加以精密控制。
基本上,此掺质浓度(剂量)系由离子束电流(离子束内之总离子数)与扫瞄率(晶圆通过离子束之次数)来控制,而离子植入之深度则由离子束能量之大小来决定。
化学机械研磨技术
化学机械研磨技术(化学机器磨光,CMP)兼具有研磨性物质的机械式研磨与酸碱溶液的化学式研磨两种作用,可以使晶圆表面达到全面性的平坦化,以利后续薄膜沉积之进行。
在CMP制程的硬设备中,研磨头被用来将晶圆压在研磨垫上并带动晶圆旋转,至于研磨垫则以相反的方向旋转。
在进行研磨时,由研磨颗粒所构成的研浆会被置于晶圆与研磨垫间。
影响CMP制程的变量包括有:
研磨头所施的压力与晶圆的平坦度、晶圆与研磨垫的旋转速度、研浆与研磨颗粒的化学成份、温度、以及研磨垫的材质与磨损性等等。
制程监控
量测芯片内次微米电路之微距,以确保制程之正确性。
一般而言,只有在微影图案(照相平版印刷的patterning)与后续之蚀刻制程执行后,才会进行微距的量测。
光罩检测(Retical检查)
光罩是高精密度的石英平板,是用来制作晶圆上电子电路图像,以利集成电路的制作。
光罩必须是完美无缺,才能呈现完整的电路图像,否则不完整的图像会被复制到晶圆上。
光罩检测机台则是结合影像扫描技术与先进的影像处理技术,捕捉图像上的缺失。
当晶圆从一个制程往下个制程进行时,图案晶圆检测系统可用来检测出晶圆上是否有瑕疵包括有微尘粒子、断线、短路、以及其它各式各样的问题。
此外,对已印有电路图案的图案晶圆成品而言,则需要进行深次微米范围之瑕疵检测。
一般来说,图案晶圆检测系统系以白光或雷射光来照射晶圆表面。
再由一或多组侦测器接收自晶圆表面绕射出来的光线,并将该影像交由高功能软件进行底层图案消除,以辨识并发现瑕疵。
铜制程技术
在传统铝金属导线无法突破瓶颈之情况下,经过多年的研究发展,铜导线已经开始成为半导体材料的主流,由于铜的电阻值比铝还小,因此可在较小的面积上承载较大的电流,让厂商得以生产速度更快、电路更密集,且效能可提升约30-40%的芯片。
亦由于铜的抗电子迁移(电版移民)能力比铝好,因此可减轻其电移作用,提高芯片的可靠度。
在半导体制程设备供货商中,只有应用材料公司能提供完整的铜制程全方位解决方案与技术,包括薄膜沉积、蚀刻、电化学电镀及化学机械研磨等。
半导体制造过程
後段(BackEnd)---后工序
构装(Packaging):
IC构装依使用材料可分为陶瓷(ceramic)及塑胶(plastic)两种,而目前商业应用上则以塑胶构装为主。
以塑胶构装中打线接合为例,其步骤依序为晶片切割(diesaw)、黏晶(diemount/diebond)、焊线(wirebond)、封胶(mold)、剪切/成形(trim/form)、印字(mark)、电镀(plating)及检验(inspection)等。
1晶片切割(DieSaw)
2黏晶(DieBond)
黏晶之目的乃将一颗颗之晶粒置於导线架上并以银胶(epoxy)黏着固定。
黏晶完成後之导线架则经由传输设备送至弹匣(magazine)内,以送至下一制程进行焊线。
3焊线(WireBond)
IC构装制程(Packaging)则是利用塑胶或陶瓷包装晶粒与配线以成积体电路(IntegratedCircuit;
简称IC),此制程的目的是为了制造出所生产的电路的保护层,避免电路受到机械性刮伤或是高温破坏。
最後整个积体电路的周围会向外拉出脚架(Pin),称之为打线,作为与外界电路板连接之用。
4封胶(Mold)
封胶之主要目的为防止湿气由外部侵入、以机械方式支持导线、内部产生热量之去除及提供能够手持之形体。
其过程为将导线架置於框架上并预热,再将框架置於压模机上的构装模上,再以树脂充填并待硬化。
5剪切/成形(Trim/Form)
剪切之目的为将导线架上构装完成之晶粒独立分开,并把不需要的连接用材料及部份凸出之树脂切除(dejunk)。
成形之目的则是将外引脚压成各种预先设计好之形状,以便於装置於电路版上使用。
剪切与成形主要由一部冲压机配上多套不同制程之模具,加上进料及出料机构所组成。
6印字(Mark)
印字乃将字体印於构装完的胶体之上,其目的在於注明商品之规格及制造者等资讯。
7检验(Inspection)
晶片切割之目的为将前制程加工完成之晶圆上一颗颗之检验之目的为确定构装完成之产品是否合於使用。
其中项目包括诸如:
外引脚之平整性、共面度、脚距、印字是否清晰及胶体是否有损伤等的外观检验。
8封装
制程处理的最后一道手续,通常还包含了打线的过程。
以金线连接芯片与导线架的线路,再封装绝缘的塑料或陶瓷外壳,并测试集成电路功能是否正常。
硅器件失效机理
1氧化层失效:
针孔、热电子效应
2层间分离:
AL-Si、Cu-Si合金与衬底热膨胀系数不匹配。
3金属互连及应力空洞
4机械应力
5电过应力/静电积累
6LATCH-UP
7离子污染
典型的测试和检验过程
芯片测试(wafersort)
芯片目检(dievisual)
芯片粘贴测试(dieattach)
压焊强度测试(leadbondstrength)
稳定性烘焙(stabilizationbake)
温度循环测试(temperaturecycle)
离心测试(constantacceleration)
渗漏测试(leaktest)
高低温电测试
高温老化(burn-in)
老化后测试(post-burn-inelectricaltest)